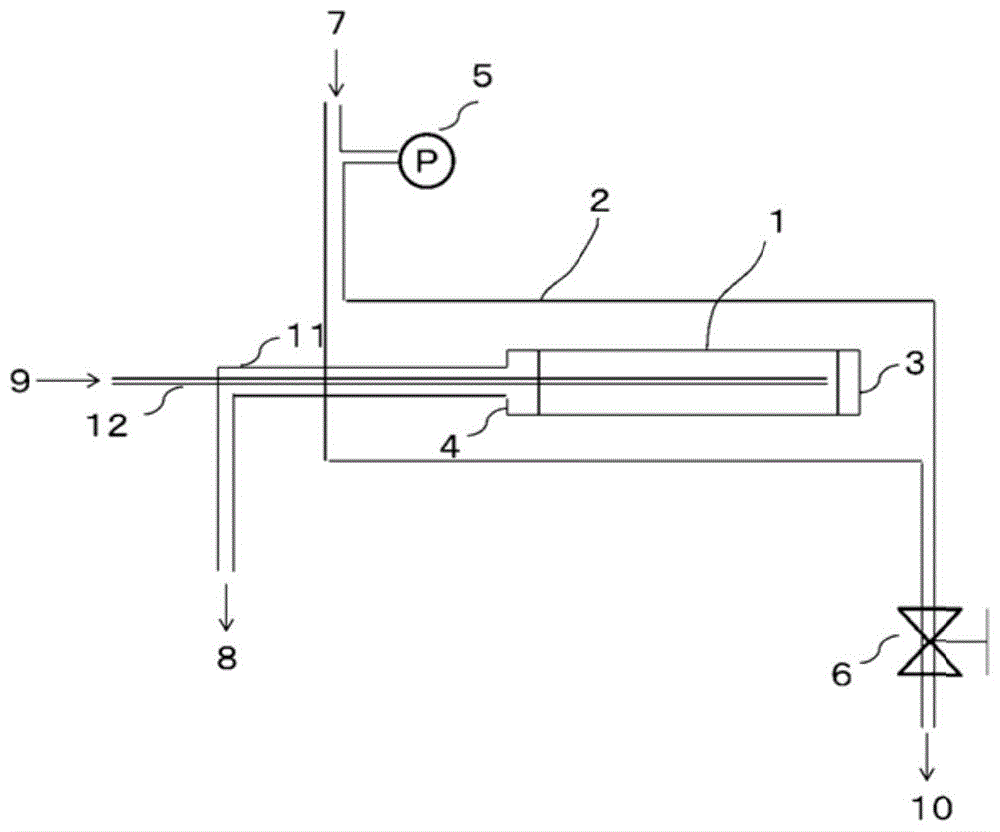
本发明涉及一种方法,其从由包含氨气且包含氢气和/或氮气的多种成分构成的混合气体中,使用沸石膜使氨气选择性透过而分离氨。此外,本发明涉及一种沸石膜,其即使在高温条件下,也可以从由包含氨气且包含氢气和/或氮气的多种成分构成的混合气体中有效地分离氨。
背景技术:
:近年来,作为气体(gas)混合物的分离方法,提出有使用高分子膜、沸石膜等膜的膜分离、浓缩方法。高分子膜具有例如加工为平板膜、中空纤维膜等的加工性优异的特征,然而仍存在有易于膨润、耐热性低的技术问题。此外,高分子膜仍存在有对于反应性化学品的耐性低,易于产生硫化物等吸附性成分所引起的劣化等技术问题。进一步地,高分子膜易于因压力而变形,由此导致分离性能降低,因此,特别是在作为本发明的课题之一的高温条件下的氨分离中,并不实用。对此,近年来,提出有耐化学品性、耐氧化性、耐热稳定性、耐压性良好的各种无机膜。其中,沸石膜具有亚纳米级有序孔,具有作为分子筛的功能,因此不仅可以选择性地使特定分子透过,也被期待用作能比高分子膜在更广温度范围中分离、浓缩的高耐久性分离膜。像这样的沸石膜,通常作为在由无机材料构成的支撑体上将沸石形成为膜状而成的沸石膜复合物进行使用。例如,已经发现:采用水热合成在多孔支撑体上形成沸石膜时,如果使用特定组成的反应混合物,则可提高支撑体上晶化的沸石的晶体取向性,形成在有机化合物与水的混合物的分离中,兼具实用的充分处理量和分离性能的致密沸石膜(专利文献1~3)。一般而言,作为气体分离用沸石膜,已知有a型膜、fau膜、mfi膜、sapo-34膜、ddr膜等沸石膜,提出了显示高处理量和分离性能的气体分离用沸石膜复合物,其适于火力发电站、石油化学工业等排放的气体的分离,例如,二氧化碳与氮、二氧化碳与甲烷、氢与烃、氢与氧、氢与二氧化碳、氮与氧、链烷烃与烯烃等的分离(例如,专利文献4)。另一方面,还关于本发明的从氢气和氮气中分离氨气,膜分离适用,例如对采用工业上重要工艺之一的哈伯-博施法的氨制造工艺的膜分离适用近年来颇受期待。作为哈伯-博施法的工艺特征,可举出的点有:该氨生成反应为平衡反应,热力学上优选为在高压、低温条件下进行反应,然而为了确保催化反应速度,通常强行采用高压、高温的制造条件。此外,由于生成的混合气体中未反应的氢气、氮气与氨气共存,从生成的混合气体中回收作为生成物的氨气的工序中,有必要将混合气体冷却至-20℃~-5℃左右,进行氨的冷凝分离(非专利文献1、2)。特别地,涉及后者,由于上述的反应平衡的制约,生成混合气体中所含的氨气浓度总会是低浓度,因此基于生成混合气体的氨冷却分离工序具有冷却效率差,消耗大量能源的特征。此外,事实上,该工艺中必须从生成混合气体分离大量的氢气和氮气的混合气体,将其作为原料气体再循环至反应器中,因而必须将经冷却的大量未反应的混合气体在升压至规定压力的同时,升温至反应温度,因此制造时的能源消耗进一步猛增。为了避免像这样的高能耗的工艺,提出有将纯化工序时的冷却冷凝分离法替换为使用无机膜的分离方法,高效地回收高浓度的氨气的工艺(专利文献7、8)。作为从氢气、氮气和氨气的混合气体分离含有高浓度氨气的混合气体的方法,可举出:1)使用分离膜,从该混合气体中使氢气和/或氮气选择性透过的方法,2)使用分离膜,从该混合气体中使氨气选择性透过的方法。作为前者使氢气和/或氮气选择性透过的方法,提出有使用各种沸石的多晶层的方法(专利文献5)、使用分子筛膜的方法(专利文献6)。此外,专利文献7中,记载有使氢气和/或氮气选择性透过的方法以及使氨气选择性透过的方法,提出有使用在陶瓷基材上层叠含二氧化硅的层而成的分离膜,从生成气体即氢气、氮气和氨气的混合物中分离氢气、氮气和氨气中的至少一种成分的分离方法。具体地,专利文献7中,作为将分离膜适用于氨制造的简要流程图,显示了由于在高温条件下氢气选择性地透过二氧化硅膜,设置有两个分离膜阶段,以第1阶段的分离膜将氢气分离至透过侧,而从未透过第1阶段的分离膜的氮气和氨气中,以第2阶段的分离膜将氨气分离至透过侧。另一方面,显示了作为从氢气和氨气的混合气体中分离氨气的条件,必须使之为在50℃这样的低温条件下,并且该混合气体中的氨气浓度必须大于60摩尔%。另一方面,作为后者的使氨气选择性透过的方法,除专利文献7外,还提出有使用具有氧8元环的特定沸石,从氨气以及氢气和/或氮气的混合气体中分离氨气的高效的氨分离方法(专利文献8)。此处,提出的是通过设计特定的沸石膜复合物,利用沸石孔径的分子筛作用,分离氨气的手法。一般而言,氨可作为在测定沸石的酸量的升温脱附法中的吸附于酸性位点的探针分子使用,其峰顶温度可达480℃左右,但吸附的氨有通过升温而脱附性质(非专利文献3),然而,专利文献8中公开了通过沸石的离子交换,控制氨在沸石上的吸附能,由此可控制氨气的透过性能。专利文献8中提出了该氨气透过时氨导致的沸石孔的堵塞的问题,在实施例中公开了避免该问题的技术。因此,在专利文献8的分离技术中,提出了:使用可抑制氨的吸附这样的沸石,在抑制氨在孔内阻塞的同时,通过利用沸石的孔径的分子筛作用,使氨气透过的手法是有效的。另一方面,在氨合成手法中,近年来,开发了划时代的制造工艺,具体地报道有使用负载有钌金属的电子盐(electride)催化剂的、在低温(340~400℃)条件下也显示出极高催化活性的制造工艺(专利文献9)。【现有技术文献】【专利文献】【专利文献1】日本特开2011-121040号公报【专利文献2】日本特开2011-121045号公报【专利文献3】日本特开2011-121854号公报【专利文献4】日本特开2012-066242号公报【专利文献5】特表平10-506363号公报【专利文献6】特表2000-507909号公报【专利文献7】日本特开2008-247654号公报【专利文献8】日本特开2014-058433号公报【专利文献9】国际公开第2015/129471号【非专利文献】【非专利文献1】日本化学会编,第6版化学便览应用化学编i,丸善株式会社(2003),p581【非专利文献2】社团法人化学工学协会,化学工艺(process)集成第1版,东京化学同人,p153【非专利文献3】片田直伸,丹羽干,沸石vol.21no.2,沸石学会(2004),p45-52技术实现要素:【发明所要解决的课题】然而,在从含有氢气、氮气、氨气的混合气体中使氢气和/或氮气选择性透过的方法中,介由分离膜而回收的是氢气和/或氮气,本手法的本质课题在于,采用从含有比较高浓度氨气的该混合气体中,首先分离氢气和/或氮气的手法这一点。即,存在课题:该分离氢气和/或氮气的工序中,伴随透过的氢气和/或氮气,大量的氨气也会透过,因此但凡不能回收透过的大量的氨,则不可能达成具有经济性的工艺。例如,采用专利文献7的技术的情况下,为完成具有经济性的工艺,必须有从由第1阶段的分离膜透过的含有氨气的高浓度的氢混合气体,以及未透过的氮气和氨气的混合气体中,分离氨气的工序。即,该方法不仅是至少要以两个阶段来从氢气、氮气和氨气的混合气体中分离氨气的繁杂工艺,而且为完成具有经济性的工艺,还需要从在第1阶段透过的混合气体以及未透过的混合气体的两者中回收氨的工序,以致变为更为繁杂的工艺。为从本质上解决这些课题,就有必要从包含相对高浓度的氢气和氮气的混合气体和/或含有相对低浓度的氨气的混合气体中,分离氢气和氮气,但像这样的工艺中,难以实现生产性高的氨制造工艺,并不现实。进一步地,专利文献7中所提出的将在高温条件下以第1阶段的膜分离至透过侧的氢气再循环的工艺中,存在需要将氢气升压的能源的课题,此外第2阶段的膜的氮气与氨气的分离中,氨气的透过度不充分,存在膜面积增大的担忧。进一步地,在高温条件下,从氢气、氮气、氨气的混合气体中,分离作为原料气体的氢气的专利文献7的手法中,例如,在作为本发明一种实施方式的将分离膜直接安装于氨合成反应器而进行氨合成时,原料气体产生透过,因而由于上述反应平衡的限制,对反应不利,不能生成高浓度的氨气。出于以上观点,使用像这样的分离膜,从氢气、氮气、氨气的混合气体中,使氢气和/或氮气选择性透过的手法不仅制造时的能源成本猛增,且工艺也变得繁杂,而且难以体现出特意将分离膜导入氨制造工艺的优越性。与之相对地,使用分离膜从氢气、氮气、氨气的混合气体中使氨气选择性透过的手法,作为解决上述各种课题的手法是有效的。然而,公知文献7中提出的使用层叠含二氧化硅的层而成的分离膜的氨气分离方法中,记载了使用大于60摩尔%的氨气浓度的混合气体,且为了表现出氨引起的阻塞效应(blockingeffect),必须将该混合气体冷却至50℃,此外,氨气分离能也要为氨气相比氢气或多或少更易于透过的程度。像这样的工艺中,本来就存在如何供给大于60摩尔%的氨气浓度的混合气体这一课题,即使能够供给像这样混合气体也需要大量能源来进行冷却,因此难以完成具有经济性的工艺。另一方面,专利文献8中提出的使用具有氧8元环的特定沸石,从氨气以及氢气和/或氮气的混合气体中分离氨气的手法,由于是使氨气透过,不存在如上所述的制约,可作为适用于工业工艺的有效手法实现。然而,专利文献8中提出的通过利用沸石孔径的分子筛作用的氨分离方法中,氨气与氮气的渗透通量比(理想分离系数)最高仅能达到14左右,其透过性能并不充分。此外,专利文献8中,分别求得氢气和氨气相对于氮气的渗透通量比,比较这些比值,可知虽然提出了从氢气、氮气、氨气的混合气体中,基本选择性透过氨气,但特别是从氨气相对于氢气的渗透通量比来看,其透过性能并不充分,通过利用上述沸石孔径的分子筛作用的氨气分离的有效性是有限的。进一步地,专利文献8中,在140℃下进行从氮和氨气的混合气体中的氨气分离,然而比较氨气透过前后的各种气体的渗透通量时,透过后各个气体的渗透通量值均上升,仍存在有在140℃这一较低温条件下,沸石膜的耐久性也会受损这一课题。对于这些课题,为了使用沸石膜而使氨气高效地透过,由于氨本质上具有在沸石上的吸附能,因而也必须恰当组合供给混合气体的组成、使其分离时的温度。然而,专利文献8中,并未记载该合适的分离条件,既没有提出也没有证实从氢气、氮气和氨气的混合气体、氢气和氨气的混合气体中分离氨的手法。另一方面,氨制造工艺中,如专利文献9所述,近年来报道了在低温、低压条件下也为高活性的氨制造催化工艺,其作为使制造时所消耗的能源减少的工艺颇受期待。然而,仅以该开创性的制造工艺,则如上所述,出于氨的生成反应为平衡反应的理由,由于反应平衡的限制,无法生成含有大于平衡组成的高浓度氨气的混合气体,不能本质上解决包括上述生成氨的回收、原料气体的再循环工序的制造时的减少能源消耗量这一课题。本发明是鉴于上述现有的实际情形而完成的,其课题为提供一种氨分离方法,其可从由包含氨气且包含氢气和/或氮气的多种成分构成的混合气体中,使氨气高选择性且高透过度地透过沸石膜,由此分离氨,并且高温分离稳定性以及长期运行稳定性优异。用于解决课题的方法本发明人等为解决上述课题,对使用沸石膜的氨分离进行进一步研究时,发现若使氢气、氮气和氨气的混合气体中的氨气浓度为规定量以上时,透过沸石膜的氨气的透过选择性明显提高。此外,发现使用本发明的一个方式时,即使在大于200℃的温度条件下,也可稳定地维持氨气分离性能。更令人吃惊地,发现同样的效果在具有相对于氢分子、氮分子、氨分子的分子尺寸而言大孔径的mfi等沸石中也得以表现。即,专利文献8中,提出了由于透过的氨气成为沸石的孔径阻塞的原因,设计了避免该阻塞的氨气分离透过膜,进行氨的分离的手法;相对于此,本发明中,发现反而若使用主动地进行氨在沸石上的吸附的手法时,可显著提高氨气分离性能,此外分离稳定性也提高,以至完成了本发明。此外,发现与专利文献7中提出的二氧化硅膜不同,使用沸石膜时,在大于50℃、进一步大于200℃的高温条件下,也可稳定地维持氨分离性能,以至完成了本发明。本发明的第一实施方式(发明a)基于像这样的发现而达成,提供如下发明。[a1]一种氨分离方法,其为从至少含有氨气、氢气和氮气的混合气体中,使用沸石膜使氨气选择性透过而分离氨的方法,所述混合气体中的氨气浓度为1.0体积%以上。[a2]根据[a1]所述的氨分离方法,所述混合气体中的氢气/氮气的体积比为0.2以上、3以下。[a3]根据[a1]或[a2]所述的氨分离方法,分离氨时的温度为高于50℃且500℃以下。[a4]根据[a1]~[a3]中任一项所述的氨分离方法,构成所述沸石膜的沸石为rho型沸石或mfi型沸石。[a5]一种氨分离方法,其包括由氢气和氮气制造氨的工序,从该制造工序中所得的含有氨气的混合气体中,通过[a1]~[a4]中任一项所述的分离方法分离氨。此外,本发明人等为解决上述课题,对于使用沸石膜的氨气分离进行进一步研究时,发现:相比现有的二氧化硅膜,虽然现有的氨气分离用沸石膜能高选择性、高效地分离氨气,然而其分离性能的氨气与氮气的渗透通量比(理想分离系数)最高仅为14左右;与之相对地,若使用具有以x射线光电子能谱法(xps)确定的氮原子相对于al原子的摩尔比在规定范围的表面的沸石膜时,可显著提高氨气分离性能。此外,发现若使用本发明时,即使在高温条件下也可稳定地维持氨气分离性能。即,发现为了即使在高温条件下,也可从由包含氨气且包含氢气和/或氮气的多种成分构成的混合气体中,高选择性且高透过性地分离氨气,有必要在各种沸石膜中,使用具有相对于al原子含有规定的摩尔比的氮原子的表面的沸石膜,以至完成本发明。本发明的第二实施方式(发明b)基于像这样的发现而达成,提供如下发明。[b1]一种沸石膜,其特征在于,相对于al原子,氮原子的摩尔比为0.01以上、4以下,所述摩尔比通过x射线光电子能谱法以下述测定条件求得。(测定条件)测定时的x射线源:单色化al-kα射线,功率16kv-34w定量计算时的确定本底的方法:shirley法[b2]根据[b1]所述的沸石膜,其特征在于,所述沸石膜为以铵盐处理过的沸石膜。[b3]根据[b2]所述的沸石膜,其特征在于,所述沸石膜为进一步以硝酸铝处理过的沸石膜。[b4]根据[b1]~[b3]中任一项所述的沸石膜,所述沸石为rho型沸石。[b5]根据[b1]~[b4]中任一项所述的沸石膜,其特征在于,所述沸石膜为氨气分离用。[b6]一种氨分离方法,其从至少包含氨气且包含氢气和/或氮气的混合气体中,使用[b1]~[b5]中任一项所述的沸石膜,使氨气透过而进行分离。[b7]一种氨分离方法,其将由氢气和氮气制造氨的工序中所得的氨通过[b6]所述的分离方法进行分离。此外,本发明人等为解决上述课题,对于使用沸石膜的氨气分离进行进一步研究时,发现:相比现有的二氧化硅膜,虽然现有的氨气分离用沸石膜能高选择性、高效地分离氨气,然而其分离性能的氨气与氮气的渗透通量比(理想分离系数)最高仅为14左右,此外,存在甚至在140℃这一较低温条件下,沸石膜的耐久性也产生损失这一课题;与之相对地,若使用具有以x射线光电子能谱法(xps)确定的si原子相对于al原子的摩尔比在规定范围的表面的沸石膜时,可展现显著的氨气分离性能,同时提高高温条件下的分离稳定性。即,发现为了即使在高温条件下,也可从由包含氨气且包含氢气和/或氮气的多种成分构成的混合气体中,高选择性且高透过性地分离氨气,有必要在各种沸石膜中,使用具有相对于al原子含有规定的摩尔比的si原子的表面的沸石膜,以至完成本发明。本发明的第三实施方式(发明c)基于像这样的发现而达成,提供如下发明。[c1]一种沸石膜,其特征在于,si原子相对于al原子的摩尔比为2.0以上、10以下,所述摩尔比使用x射线光电子能谱法以下述测定条件确定。(测定条件)测定时的x射线源:单色化al-kα射线,输出功率16kv-34w定量计算时的确定本底的方法:shirley法[c2]根据[c1]所述的沸石膜,其特征在于,所述沸石膜的氮原子相对于al原子的摩尔比为0.01以上、4以下,所述摩尔比使用x射线光电子能谱法以下述测定条件求得而确定。(测定条件)测定时的x射线源:单色化al-kα射线,输出功率16kv-34w定量计算时的确定本底的方法:shirley法[c3]根据[c1]或[c2]所述的沸石膜,其特征在于,所述沸石膜为以铝盐处理过的沸石膜。[c4]根据[c1]~[c3]中任一项所述的沸石膜,其特征在于,所述沸石膜为以铵盐处理过的沸石膜。[c5]根据[c1]~[c4]中任一项所述的沸石膜,其特征在于,所述沸石膜为以铵盐处理后,以铝盐处理过的沸石膜。[c6]根据[c1]~[c5]中任一项所述的沸石膜,所述沸石为rho型沸石。[c7]根据[c1]~[c6]中任一项所述的沸石膜,其特征在于,所述沸石膜为氨分离用。[c8]一种氨分离方法,其从至少包含氨气且包含氢气和/或氮气的混合气体中,使用[c1]~[c7]中任一项所述的沸石膜,使氨气透过而进行分离。[c9]一种氨分离方法,其将由氢气和氮气制造氨的工序中所得的氨通过[c8]所述的分离方法进行分离。此外,本发明人等为解决上述课题,对于使用沸石膜的氨气分离进行进一步研究时,发现:若使用具有以x射线光电子能谱法(xps)所确定的碱金属原子相对于al原子的摩尔比为规定范围的表面的沸石膜时,可在保持高氨气分离选择性的情况下,提高透过性能。此外,发现采用本发明时,即使在高温条件下,也可稳定地维持氨气分离性能。即,发现为了即使在高温条件下,也可从由包含氨气且包含氢气和/或氮气的多种成分构成的混合气体中,高选择性且高透过性地分离氨气,有必要在各种沸石膜中,使用具有相对于al原子含有规定的摩尔比的碱金属原子的表面的沸石膜,以至完成本发明。本发明的第四实施方式(发明d)基于像这样的发现而达成,提供如下发明。[d1]一种沸石膜,其特征在于,碱金属原子相对于al原子的摩尔比为0.01以上、0.070以下,所述摩尔比通过x射线光电子能谱法以下述测定条件确定。(测定条件)测定时的x射线源:单色化al-kα射线,输出功率16kv-34w定量计算时的确定本底的方法:shirley法[d2]根据[d1]所述的沸石膜,其特征在于,所述沸石膜的氮原子相对于al原子的摩尔比为0.01以上、4以下,所述摩尔比通过x射线光电子能谱法以下述测定条件确定。(测定条件)测定时的x射线源:单色化al-kα射线,输出功率16kv-34w定量计算时的确定本底的方法:shirley法[d3]根据[d1]或[d2]所述的沸石膜,其特征在于,所述沸石膜为以碱金属盐处理过的沸石膜。[d4]根据[d1]~[d3]中任一项所述的沸石膜,其特征在于,所述沸石膜为以铵盐处理过的沸石膜。[d5]根据[d1]~[d4]中任一项所述的沸石膜,其特征在于,所述沸石膜为以铵盐处理后,以碱金属盐处理过的沸石膜。[d6]根据[d1]~[d5]中任一项所述的沸石膜,所述沸石为rho型沸石。[d7]根据[d1]~[d6]中任一项所述的沸石膜,其特征在于,所述沸石膜为氨气分离用。[d8]一种氨分离方法,其从至少包含氨气且包含氢气和/或氮气的混合气体中,使用[d1]~[d7]中任一项所述的沸石膜,使氨气透过而进行分离。[d9]一种氨分离方法,其将由氢气和氮气制造氨的工序中所得的氨通过[d8]所述的分离方法进行分离。此外,本发明人等为解决上述课题,对于使用沸石膜复合物的氨气分离进行进一步研究时,发现:相比现有的二氧化硅膜,虽然沸石膜能高选择性、高效地分离氨气,然而如本发明的参考例e1所述地,在使用200℃和300℃相对于30℃的热收缩率的变化率为0.13%、0.30%(c轴向)的单调变化的、如专利文献8中提出的将cha型沸石成膜化而成的沸石膜复合物的情况下,在特别是大于200℃的温度范围中,氨气的分离性能降低,尚有改善的余地。推测这是因为沸石的热收缩引起沸石晶界上产生裂纹,气体介由该裂纹透过;与之相对地,发现:如本发明的实施例e所述的rho型沸石,即使在200℃相对于30℃的热收缩率的变化率为1.55%时,相比cha型沸石收缩显著,表现为相对于温度非线形的热膨胀/收缩的行为的沸石中,若300℃的热膨胀率的变化率为0.02%左右时,则在大于200℃的高温条件下,也可高选择性、高效地分离氨。即发现,为了本发明的课题之一即在高温条件下,从由包含氨气且包含氢气和/或氮气的多种成分构成的气体混合物中,高选择性且高透过性地分离氨气,在各种沸石膜复合物中,也有必要适用将显示在规定温度范围中的热膨胀变化率的沸石成膜化而成的沸石膜复合物,以至完成本发明。另外,本说明书中,热膨胀率的变化率是指热膨胀率的变化率最大的轴向中的热膨胀率的变化率。例如,cha型沸石具有在a轴和c轴方向上不同的热膨胀/收缩率,其变化率为c轴较大。因此,cha的热膨胀率的变化率为c轴方向的热膨胀率的变化率。同样地,mfi型沸石具有a轴、b轴、c轴方向上不同的热膨胀/收缩率,其变化率为c轴较大。因此,本说明书中的mfi型的热膨胀率的变化率为c轴方向的热膨胀率的变化率。另一方面,rho型沸石为立方晶系,其晶轴全部等价,因此与轴向无关,热膨胀率的变化率固定。本发明的第五实施方式(发明e)基于像这样的发现而达成,提供如下发明。[e1]一种氨分离用沸石膜复合物,其为包含沸石的氨分离用沸石膜复合物,所述沸石的300℃的热膨胀率相对于30℃的热膨胀率的变化率为±0.25%以内,400℃的热膨胀率的相对于30℃的热膨胀率的变化率为±0.35%以内。[e2]根据[e1]所述的氨分离用沸石膜复合物,400℃的该热膨胀率相对于30℃的热膨胀率的变化率,与所述沸石的300℃的该热膨胀率相对于30℃的热膨胀率的变化率的比为±120%以内。[e3]根据[e1]或[e2]所述的氨分离用沸石膜复合物,所述沸石为rho型沸石或mfi型沸石。[e4]根据[e1]~[e3]中任一项所述的氨分离用沸石膜复合物,所述沸石的sio2/al2o3摩尔比为6以上500以下。[e5]一种氨分离方法,其为从至少包含氨气且包含氢气和/或氮气的气体混合物中,使用[e1]~[e4]中任一项所述的氨气分离用沸石膜复合物分离氨。[e6]一种氨分离方法,其将由氢气和氮气制造氨的工序中所得的氨通过[e5]所述的分离方法进行分离。特别地,第二至第五的实施方式为涉及有助于氨的节能型制造工艺的完成的氨气分离膜的技术,此外,为可期待用于作为本发明的方式之一的反应分离型氨制造工艺的技术。【发明效果】依据本发明的第一实施方式,可以从由包含氨气及氢气和氮气的多种成分构成的混合气体中,以高选择性且高效地将氨气连续地分离至透过侧。此外,依据本发明,即使在大于50℃、进一步大于200℃的高温条件下,也可稳定地使用,因此氨气的透过度高,其结果是可以减小分离所必要的膜面积,使得用小规模的设备在低成本下的氨分离成为可能。作为本发明的沸石膜的具体适用例,在哈伯-博施工艺所代表的氨制造工艺等中,从回收自反应器的、由包含氨气及氢气和氮气的多种成分构成的混合气体中回收氨时,相比以往的冷却冷凝分离法,可更高效地进行氨分离,可减少用于氨冷凝的冷却能源。此外,作为其他方式,本发明的沸石膜即使在高温条件下也可稳定地从由包含氨气及氢气和氮气的多种成分构成的混合气体中,高透过度且高效地将氨气分离至透过侧,因此可以设计反应分离型氨制造工艺,将本发明的沸石膜设置于反应器内,在生成氨气的同时回收生成的氨气。依据本发明的第二至第五的实施方式,即使在高温条件下也可稳定地从由包含氨气且包含氢气和/或氮气的多种成分构成的混合气体中,高选择性且高效地将氨气连续地分离至透过侧。此外,本发明的沸石膜即使在更高温条件下也可稳定地使用,因此氨气的透过度高,其结果是可以减小分离所必要的膜面积,使得用小规模的设备在低成本下的氨气分离成为可能。作为本发明的沸石膜的具体适用例,在哈伯-博施工艺所代表的氨制造工艺等中,从反应器所回收的由包含氨气且包含氢气和/或氮气的多种成分构成的混合气体中回收氨时,相比以往的冷却冷凝分离法,可更高效地进行氨分离,因而可减少用于氨冷凝的冷却能源。此外,作为其他方式,本发明的沸石膜即使在高温条件下也可稳定地从由包含氨气且包含氢气和/或氮气的多种成分构成的混合气体中,高透过度且高效地将氨气分离至透过侧,因此可以设计反应分离型氨制造工艺,将本发明的沸石膜设置于反应器内,在生成氨气的同时回收生成的氨气。特别地,第一至第五实施方式在反应分离型氨制造工艺中的适用,不仅可以期待将氨制造时的反应压的低压化,还可期待显著提高原料气体向氨气的转化率,降低制造时的回收气体向反应器的再循环量。即,通过采用本发明的沸石膜的反应分离型氨制造工艺,可抑制制造时的能源消耗量,使经济性优异的节能型氨制造成为可能。【附图说明】【图1】显示实施例中用于氨气分离试验的装置的结构的示意图。【图2】实施例e4涉及的沸石的与温度对应的热膨胀率的测定结果。【符号说明】1沸石膜复合物2耐压容器3支撑体前端的密封部4沸石膜复合物与透过气体回收管的接合部5压力计6背压阀7供给气体(试样气体)8透过气体9吹扫气体10非透过气体11透过气体回收管12吹扫气体供给管具体实施方式下文中,对于本发明的实施方式进行更为详细的说明,但以下所记载的构成要件的说明为本发明的实施方式的一例,本发明不受这些内容所限定,在其要旨范围内可进行各种变形而实施。另外,本说明书中的沸石是指国际沸石协会(internationalzeoliteassociation,iza)所规定的沸石。其结构以x射线衍射数据表征。此外,本说明书中,可将“沸石膜在多孔支撑体上所形成的多孔支撑体-沸石膜复合物”称为“沸石膜复合物”或“膜复合物”。此外,可将“多孔支撑体”简称为“支撑体”,将“铝硅酸盐的沸石”简称为“沸石”。进一步地,本说明书中,可分别将“氢气”、“氮气”以及“氨气”简称为“氢”、“氮”、“氨”。另一方面,本发明中的氨分离是指从含有氨气的混合气体中,获得含有更高浓度的氨气的混合气体。本发明的氨分离方法的第一实施方式(发明a)为从由至少包含氨、氢和氮的多种成分构成的混合气体中,使用沸石膜,高透过度且高选择性地进行将氨稳定连续地向透过侧进行分离的方法,其特征在于,从含有规定量以上的氨的氢和氮的混合气体中,使氨选择性透过而分离。此外,本发明的氨分离方法的其他实施方式的特征在于,使由包含氨且包含氢和/或氮的多种成分构成的混合气体与规定的沸石膜接触,从该混合气体中,使氨选择性透过而分离。下文中,说明详细内容。<氨的制造方法>本实施方式所涉及的氨分离方法在从至少包含氨、氢和氮的混合气体中,高效地分离氨时可有效使用,因此与获得像这样的混合气体的氨制造方法组合使用是有效的。即,在包括由氢和氮制造氨的第一工序以及将第一工序中所得的氨通过后述的氨分离方法进行分离的第二工序的、将第一工序中所得的氨以第二工序进行氨分离的氨制造方法以外,使上述第一工序以及上述第二工序在一个反应器内进行的氨的制造方法也是本发明的优选方式之一。第一工序以及第二工序在一个反应器内进行是指使第一工序以及第二工序同时进行。即,本发明的一个实施方式中,可在容器内由氢气和氮气制造氨气,在该容器内,边从含有所制造的氨气的混合气体中分离氨,边高效地制造氨。作为氨的工业制造方法,没有特别的限制,可举出哈伯-博施法。该方法中,基本上采用如下工艺:以氧化铁作为催化剂,在300℃~500℃、10~40mpa这样的高温高压下,使氮和氢气在催化剂上进行反应生成氨,在冷却反应器出口气体中所含的生成氨而进行冷凝分离,将其作为制品回收的同时,分离未反应的氮和氢气作为原料气体进行再循环。此外,作为哈伯-博施法的改良方法,1980年代开发出可在更低压条件下制造氨的ru系负载催化剂,与上述哈伯-博施工艺组合而成的工艺也实现了工业化,但其基本制造工艺跨越100年而没有改变。像这样地,一般而言氨制造工业催化剂可大致分为铁系催化剂和ru系催化剂。用于氨制造时的原料气体的摩尔比优选作为理论比的氢/氮=3,但ru系催化剂中容易产生氢导致的催化剂中毒,因此优选使用低于该摩尔比的制造条件。若考虑该点时,虽然没有特别的限制,作为与本发明的氨分离技术相组合的氨制造催化工艺,由于接近后述的氨分离中的供给气体中所含有的氢气/氮气的优选体积比,优选使用ru系催化剂的工艺,通过该组合,可降低生成的氨分离中氢的透过量。<氨分离方法>本发明的氨分离方法的第一实施方式的特征在于,使用沸石膜,使由包含氨及氢和氮的多种成分构成的混合气体与该沸石膜接触,从该混合气体中使氨选择性透过而分离。此外,本发明的氨分离方法的特征在于,使用规定的沸石膜,使由包含氨且包含氢和/或氮的多种成分构成的混合气体与该沸石膜接触,从该混合气体中使氨选择性透过而分离。另外,如上所述地,依据本发明,在反应器内由氢气和氮气制造氨气,上述反应器内中,可使用沸石膜边使所制造的氨气透过,边高效地制造/回收氨。本发明中的通过沸石膜的氨分离主要为基于沸石孔内的氨的跳跃机制(hoppingmechanism)的分离,但也通过基于吸附氨、铵离子等的沸石膜的孔径控制而利用了作为分子筛的分离。通过前者的作用,能够使与沸石膜亲和性高的氨高选择性地透过沸石膜;此外,通过后者的作用,由于可高效地分离具有吸附氨的沸石膜的有效孔径以上尺寸的气体分子与其以下尺寸的气体分子,可更有效地分离氨。由于沸石孔内的氨的跳跃机制,氨的透过选择性显著提高的原因尚未详知,但因为像这样的沸石膜中,由于沸石中所含有的吸附氨、铵离子,沸石膜内的孔径变窄,从而特别是可以降低分子尺寸小的氢气的透过速度。由于使用孔径大于氢气、氮气、氨气的分子尺寸的沸石时,该作用也同样地使沸石膜的孔变窄,因而表现出对氮气、氢气的透过的阻碍。另一方面,通过沸石孔内所含的吸附氨、铵离子,孔内可产生氨的吸附/脱附引起的跳跃移动,通过该行为表现出氨气的选择性分离。在本发明的第一实施方式(发明a)中,如上所述地,其特征在于利用氨在沸石上的吸附,基于沸石孔内的氨的跳跃机制的氨分离,因而有必要将含有氢气、氮气和氨气的供给气体中的氨气浓度控制为规定量以上。作为供给气体中的氨气的浓度,该浓度为1.0体积%以上是重要的。这是因为吸附在沸石上的氨与气相中的氨气存在吸附平衡的关系,氨的在沸石上的吸附能很大程度上依存于供给气体中的氨气浓度。如本发明的比较例所示,在小于1.0体积%氨气浓度中,也可以表现出若干氨的透过选择性,但该效果并不显著。因此,本发明中,使用1.0体积%以上的氨气浓度的供给气体是重要的,在使像这样气体在加压条件下与沸石膜接触时,可有效引发氨在沸石上的吸附,因而可提高从供给气体中的氨分离选择性。此外,使用1.0体积%以上的氨气浓度的供给气体时,由于供给气体中的氨气浓度提高,透过速度也提高。另外,要使混合气体中的氨气浓度为1.0体积%以上时,只要制造氨时以使所得的混合气体中的氨气浓度为1.0体积%以上的条件进行氨的制造即可。上述之中,供给气体中的氨气浓度优选为2.0体积%以上,更优选为3.0体积%以上,特别优选为5.0体积%以上。另一方面,上限没有特别限制,供给气体中的氨气浓度越高则分离性能越提高,因而通常小于100体积%,基于分离氨的必要性的理由,一般而言为80体积%以下,优选为60体积%以下,更优选为40体积%以下。另外,供给气体中的氨的浓度为采取供给气体,分析其成分,获取氨的摩尔分数,将其视为与体积%相同。其他气体的体积%也同样获取摩尔分数,将其视为体积%。另一方面,在与氨制造工艺组合分离氨的情况下,为该制造工艺条件下生成的氨平衡浓度以下。相对于公知的从氢、氮和氨的混合气体中使氢气和/或氮气选择性透过的方法,使用本发明的氨分离技术由于是从供给气体中分离氨的工艺,从含有高浓度氨的混合气体中的氨分离是有利的。此外,即使在之后根据需要采用从未透过膜的非透过侧的混合气体中回收氢气的工序的情况下,也为从氨气浓度充分降低的该混合气体中回收氢的设计,因而具有不易产生从公知的供给气体中分离氢和/或氮而进行氨浓缩的工艺中的上述课题的特征。此外,例如,其还有以下特征,相比专利文献7,氨分离性能显著提高,且高温下运行时、长期运行时的分离稳定性也高。像这样地,若氢、氮和氨的混合气体中的氨气浓度为规定量以上时,透过沸石膜的氨的透过选择性明显提高的原因尚未详知,但若提高该混合气体中的氨气浓度时,出于上述的氨气与沸石的吸附平衡的理由,易于产生在沸石上的吸附,首先生成了氨吸附于孔内的沸石膜。像这样生成的吸附有氨的沸石膜由于沸石膜内的孔径变窄,可降低分子尺寸小的氢的透过速度。由于使用孔径大于氢、氮、氨的分子尺寸的沸石时,该作用也同样地使沸石膜的孔变窄,因而明显表现出对氢气透过的阻碍。另一方面,沸石孔内所吸附的氨可产生由于膜内外的压力差的孔内的氨的吸附/脱附引起的跳跃移动,通过该行为表现出氨气的选择性分离。即,本发明是一种在首先主动进行氨在沸石上的吸附,控制沸石膜的孔径,提高氨分离选择性的同时,另一方面,使用孔内的氨吸附/脱附引起的跳跃移动,使氨选择性透过的技术。与之相对地,专利文献8中提出,像这样的氨吸附沸石膜在氨透过中成为阻塞的原因,因而设计不产生像这样的吸附的沸石,通过利用沸石的孔径的分子筛来分离氨的技术,在这点上两者大为不同。另一方面,如专利文献7中所提出的二氧化硅膜中,不易产生氨吸附,此外,即使氨被吸附,热稳定性也低,因而不能表现出如本发明的效果。另一方面,在主要利用伴随氨在沸石上的吸附/脱附的孔内跳跃机制而进行氨分离的本发明中,氨分离时的温度对使用的沸石膜的长期耐久性、沸石膜的氨分离性能以及与氨制造设备组合时的工艺整体的制造能源收支有很大的影响,因此成为重要的设计因素之一。出于这些角度,本发明中,在分离氨合成中的生成气体的情况下,氨分离时的温度通常为与氨的合成温度相同或为其以下的温度,氨分离时的温度为进行氨分离的分离器内的温度,即,供给至分离的混合气体的温度、所分离氨气的温度。此外,分离膜的温度可视为大致与分离器内的温度相同。基于氨的制造工艺设计,在与合成温度相同的温度下进行分离时,不需要进行再循环至反应器的氢、氮的升温,因而优选。由此,氨分离时的优选温度也与氨合成反应中反应温度相关,但通常为500℃以下,优选为450℃以下,更优选400℃以下。使用本发明的沸石膜,在这些温度条件下进行氨分离时,该沸石膜不仅稳定性高,可长期间连续运行,而且可表现出高氨透过选择性。另一方面,其下限通常为大于50℃的温度,优选为100℃以上,更优选为150℃以上,特别优选为200℃以上,其中优选为250℃以上,尤其优选为300℃以上。在这些温度条件下进行氨分离时,吸附于沸石孔内的氨的脱附速度提高,其结果是沸石膜的氨透过速度提高。此外,作为氨制造工艺,进行原料气体的再循环时,为降低氢、氮的升温所消耗的能源,优选在更高温条件下的氨分离,出于该角度,其下限优选为250℃以上,更优选为300℃以上。在如本发明的基于孔内跳跃移动的氨分离方法中,通过控制沸石孔内的碱金属原子相对于al原子的摩尔比为小于饱和量比而控制其速度,因而该摩尔比的控制很重要,存在若与如本发明的第四实施方式的将该摩尔比控制为0.01以上、0.070以下的手法相组合时则优选的情况。供给气体(混合气体)中的其他气体组成没有特别的限制,供给气体中所含有的氢气/氮气的体积比通常为3以下,更优选为2以下。通过调整该体积比,可降低氨分离时的氢的透过量,氨分离选择性提高。出于像这样的理由,在从氨制造工艺获得本发明的氨分离工艺的供给气体的情况下,没有特别限制,但优选与降低原料气体中的氢气/氮气的体积比的ru系氨制造催化工艺组合。另一方面,由于其下限越低则氨分离选择性提高,因而没有特别限制,通常为0.2以上、优选为0.3以上,更优选为0.5以上。此处,上限以及下限的记载值为在有效数字的范围内有效,即,上限3以下是指2.5以上小于3.5,另一方面0.2以上是指0.15以上小于0.25,1.0以上是指0.95以上小于1.05。本发明中供给气体(混合气体)的压力越高则沸石膜的分离性能越高,越可降低使用的沸石膜的面积,因而为优选方式,但只要为大气压以上的压力时就没有特别限制,可适当减压调整压力至期望的压力而使用。分离对象的气体低于分离使用的压力的情况下,可用压缩机等增压使用。供给气体的压力通常为大气压或大于大气压,优选为0.1mpa以上,更优选为0.2mpa以上。此外,上限值通常为20mpa以下,优选为10mpa以下,更优选为5mpa以下,也可为3mpa以下。透过侧的压力只要比供给侧的气体压力低时就没有特别限制,通常为10mpa以下,优选为5mpa以下,更优选为1mpa以下,进一步优选0.5mpa以下,根据情况不同也可为降低至大气压以下的压力。在分离达到供给气体中的氨的浓度为低值的情况下,优选透过侧为低压力,若降低至大气压以下的压力时,则能分离氨至供给气体中的氨气浓度为更低浓度。供给侧的气体与透过侧的气体的压差没有特别限制,通常为20mpa以下,优选为10mpa以下,更优选为5mpa以下,进一步优选1mpa以下。此外,通常为0.001mpa以上,优选为0.01mpa以上,更优选为0.02mpa以上。这里,压差是指该气体的供给侧的分压与透过侧的分压的差。此外,压力[pa]在没有特别限定的情况下,则指绝对压力。供给气体的流速为以可补充透过气体的减少的程度的流速,或为使供给气体中透过性小的气体在膜的极近处的浓度与气体全体中的浓度一致而尽量混合供给气体的流速即可,也与沸石膜复合物的管径、膜的分离性能相关,但以线速度计通常为0.001mm/sec以上,优选为0.01mm/sec以上,更优选为0.1mm/sec以上,其中,优选为0.5mm/sec以上,更优选为1mm/sec以上,上限没有特别限制,通常为1m/sec以下,优选为0.5m/sec以下。本发明的从混合气体中的氨分离方法中,也可使用吹扫气体。吹扫气体是指为了高效回收从分离膜所透过的氨而供给的气体,并非导入分离透过前的供给气体侧的气体,而是供给至分离膜的透过侧的气体。即,吹扫气体为与分离透过前的供给气体分别供给的气体,在透过侧使与供给气体不同种类的气体流动,回收透过膜的气体。本发明在使用的吹扫气体是指例如图1所示的从管路12供给的气体9。吹扫气体的压力通常为大气压,但并不特别限于大气压,优选为20mpa以下,更优选为10mpa以下,进一步优选1mpa以下,下限优选为0.09mpa以上,更优选为0.1mpa以上。根据情况,也可进行减压而使用。吹扫气体的流速没有特别限制,以线速度计通常为0.5mm/sec以上,优选为1mm/sec以上,上限没有特别限制,通常为1m/sec以下,优选为0.5m/sec以下。用于气体分离装置没有特别限制,通常将沸石膜复合物做成膜组件进行使用(下文,有时也将“使用沸石膜复合物和/或使用沸石膜复合物的分离装置”简称为“膜组件”)。膜组件例如可为如图1所示意性显示的装置,也可使用例如《气体分离·纯化技术》((株)东丽研究中心、2007年出版)22页等所例示的膜组件。对于图1的装置中的混合气体的分离操作,在实施例一项中进行说明。进行从混合气体中的氨的膜分离时,可使膜组件为多段而使用。该情况下,向第1阶段的膜组件供给进行分离的气体,可将未透过膜的非透过侧的气体进一步供给至第2阶段的膜组件,也可将透过的气体供给至第2阶段的膜组件。在前者的方法中,可进一步提高非透过侧的透过性低的成分的浓度,在后者的方法中,可进一步提高透过的气体中的透过性高的成分的浓度。此外,可恰当使用将这些方法组合而成的方法。以设置为多段的膜组件进行分离的情况下,在向后一阶段的膜组件供给气体时,可根据需要以升压器等调整供给气体的压力。此外,在以多段使用膜组件的情况下,各阶段可设置性能不同的膜。通常,作为膜的性能,存在透过性能高的膜的分离性能低,另一方面,分离性能高的膜的透过性能低的倾向。由此,在将希望分离或浓缩的气体成分处理至规定浓度为止时,透过性高的膜所必要的膜面积减小,另一方面,透过性低的成分也易于透过到透过侧,由此,透过侧气体中的透过性高的成分的浓度趋于降低。反之,分离性能高的膜中,难以产生透过性低的成分向透过侧的透过,由此,透过侧气体中透过性高的成分的浓度高,然而必要的膜面积趋于增大。通过1种膜的分离中,难以控制必要膜面积与浓缩或分离目标气体的透过、非透过量的关系,而通过使用不同性能的膜,控制则变得容易。根据膜成本与分离·回收的气体的价格,设置膜以优化膜面积与浓缩、分离目标气体的透过、非透过量的关系,可使整体的收益最大化。例如,用1段的膜分离不能充分分离氨的情况下,可进一步用多段膜使非透过侧的气体分离。此外,用1段的膜分离,膜的氨/氢的分离不充分,在透过侧含有氨的同时较多含有氢的情况下,也可将透过气体用氨与氢的分离性能高的膜进行分离。本发明中使用的沸石膜的耐化学品性、耐氧化性、耐热稳定性、耐压性优异,且可发挥对氨的高透过性能、分离性能,具有耐久性优异的性能。这里所谓高透过性能是指显示出充分的处理量,例如,透过膜的气体成分的渗透通量(permeance)[mol/(m2·s·pa)],例如在温度200℃、压差0.3mpa下使氨透过的情况下,其通常为1×10-9以上、优选为5×10-9以上,更优选为1×10-8以上,进一步优选为2×10-8以上,尤其优选为5×10-8以上,特别优选为1×10-7以上,最优选为2×10-7以上。上限没有特别限制,通常为3×10-4以下。此外,本发明中使用的沸石膜复合物的渗透通量[mol/(m2·s·pa)],例如在以相同的条件使氮透过的情况下,其通常为5×10-8以下,优选为3×10-8以下,更优选为1×10-8以下,尤其优选为5×10-9以下,最优选为1×10-9以下,理想的是渗透通量为0,实用上有时要求1×10-10~1×10-14左右。这里,渗透通量(permeance,也称为“透过度”)是指用透过物质的量,除以膜面积、时间和透过物质的供给侧与透过侧间的分压差的积的值,单位为[mol/(m2·s·pa)],其为通过实施例一项中所述方法算出的值。此外,沸石膜的选择性由理想分离系数、分离系数表示。理想分离系数、分离系数为在膜分离中通常采用的表示选择性的指标,理想分离系数为通过实施例一项中所述方法算出的值,分离系数为如下述算出的值。求分离系数α时,通过下述式算出。α=(q’1/q’2)/(p’1/p’2)〔上述式中,q’1和q’2分别表示透过性高的气体和透过性低的气体的透过量[mol/(m2·s·pa)],、p’1和p’2分别表示供给气体中的透过性高的气体和透过性低的气体的分压[pa]。〕分离系数α也可为如下所述而求得。α=(c’1/c’2)/(c1/c2)〔上述式中,c’1和c’2分别表示透过气体中透过性高的气体和透过性低的气体的浓度[体积%],c1和c2分别表示供给气体中透过性高的气体和透过性低的气体的浓度[体积%]。〕理想分离系数,例如在温度200℃、压差0.3mpa下,使氨和氮透过时,其通常为15以上,优选为20以上,更优选为25以上,最优选为30以上。此外,在温度200℃、压差0.3mpa下,使氨和氢透过时,其通常为2以上,优选为3以上,更优选为5以上,进一步优选为7以上、尤其优选为8以上,特别优选为10以上,最优选为15以上。理想分离系数的上限是完全仅透过氨的情况,此时为无限大,实用上分离系数有时为10万左右以下。本发明中所使用的沸石膜的分离系数,例如,在温度50℃、压差0.1mpa下,使氨和氮的体积比1:1的混合气体透过时,其通常为2以上、优选为3以上,更优选为4以上、更优选为5以上。分离系数的上限是完全仅透过氨的情况,此时为无限大,实用上分离系数有时为10万程度以下。本发明中所使用的沸石膜,如上所述,耐化学品性、耐氧化性、耐热稳定性、耐压性优异,且可发挥高透过性能、分离性能,耐久性优异,使用像这样的沸石膜的本发明的氨分离方法,可适用于从氨合成的生成物中的氨分离。此外,本发明的氨分离方法也可通过在氨合成反应器内设置沸石膜,在反应器内使氨选择性透过而进行分离,使反应器内的氢气和氮气与氨气的平衡发生转移,作为高转化率且高效地合成氨的膜反应器进行利用。(沸石)本发明中,构成沸石膜的沸石为铝硅酸盐。铝硅酸盐以si和al的氧化物为主成分,在不损伤本发明的效果的情况下,也可含有其以外的元素。作为本发明的沸石中所含的阳离子种,理想的是易于配位于沸石的离子交换位点的阳离子种,例如,选自周期表的第1列、第2列、第8列、第9列、第10列、第11列和第12列的元素群的阳离子种,nh4+,以及它们中的两种以上的阳离子种,更优选为选自周期表的第1列、第2列的元素群的阳离子种,nh4+,以及它们中的两种以上的阳离子种。本发明中所使用的沸石为铝硅酸盐。铝硅酸盐的sio2/al2o3摩尔比没有特别的限制,通常为6以上、优选为7以上,更优选为8以上,另一方面,其通常为500以下,优选为100以下,更优选为80以下,进一步优选50以下,尤其优选为45以下,更进一步优选30以下,最优选为25以下。通过使用像这样的规定的范围的sio2/al2o3摩尔比的沸石,可提高沸石膜的致密性以及耐化学反应性、耐热性等的耐久性,因而优选。此外,出于从由包含氨且包含氢和氮的多种成分构成的混合气体中使氨透过的分离性能的角度,出于上述的al元素的酸性位点成为氨的吸附位点的理由,优选使用含有较多al的沸石,通过使用显示上述的sio2/al2o3摩尔比的沸石,可高透过度且高选择性地分离氨。沸石的sio2/al2o3摩尔比可通过后述的水热合成的反应条件而进行调整。另外,本说明书中,sio2/al2o3摩尔比为扫描型电子显微镜-能量色散x射线光谱法(sem-edx)所确定的数值。该情况下,为获得仅膜厚数微米的膜的信息,通常将x射线的加速电压设为10kv而进行测定。作为本发明中使用的沸石的结构,以国际沸石协会(iza)规定的代码进行表示时,可举例如abw、aco、aei、aen、afi、aft、afx、ana、atn、att、atv、awo、aww、bik、cha、ddr、dft、eab、epi、eri、esv、gis、goo、ite、jbw、kfi、lev、lta、mer、mon、mtf、owe、pau、phi、rho、rte、rwr、sas、sat、sav、siv、tsc、ufi、vni、yug、ael、afo、aht、dac、fer、heu、imf、ith、mel、mfs、mww、obw、rro、sfg、sti、szr、ter、ton、tun、wei、mfi、mon、pau、phi、mor、fau等。其中优选骨架密度为18.0t/nm3以下的沸石,更优选为aei、afx、cha、ddr、eri、lev、rho、mor、mfi、fau,进一步优选为aei、cha、ddr、rho、mor、mfi、fau,特别优选为cha、rho或mfi,最优选为rho或mfi。通过使用骨架密度低的沸石,在含有氨的混合气体中存在除氨以外的透过成分时,可降低这些透过成分透过时的阻力,易于增大氨的透过量。此外,本发明的第五实施方式(沸石膜复合物e)中,优选骨架密度为18.0t/nm3以下的沸石,更优选为afx、ddr、eri、lev、rho、mor、mfi、fau,进一步优选ddr、rho、mor、mfi、fau,最优选为rho、mfi。这里,骨架密度(单位:t/nm3)是指沸石的每单位体积(1nm3)中存在的t原子(构成沸石骨格的原子中,氧以外的原子)的个数,该值由沸石的结构所确定。另外,骨架密度与沸石的结构上的关系如《沸石骨架类型图集(atlasofzeoliteframeworktypes)》(第6次修订版,2007爱思唯尔出版社)中所示。本发明的氨与氢和氮的膜分离中,特征在于其为利用氨在沸石上的吸附,基于沸石孔内的氨的跳跃机制的氨分离,然而没有特别限制,其中,有时由于具有接近氨分子直径的孔径的沸石会提高氨分离选择性而优选,出于该角度,作为沸石结构,优选具有氧8元环孔的沸石。另一方面,具有大于氧8元环的尺寸的孔在提高氨的透过度的方面优选,但存在降低其与氢和/或氮的分离性能的情况。然而,即使在使用具有大于氧8元环的尺寸的孔的沸石时,使用所述降低sio2/al2o3摩尔比的沸石时,也可通过吸附于al位点的氨控制沸石膜的孔径,因而可高透过度且高选择性地分离氨。因此,用于膜分离的沸石的有效孔径,由于对吸附有氨的沸石膜的孔径存在很大影响,是重要的设计因素之一。沸石的有效孔径可通过导入沸石的金属种、离子交换、酸处理、甲硅烷化处理等进行控制。此外,通过以其他手法控制有效孔径,也可提高分离性能。例如,由于导入沸石骨格的金属种的原子直径,沸石的孔径受到少量影响。在导入原子直径小于硅的金属,具体地例如硼(b)等时,孔径变小;导入原子直径大于硅的金属,具体地例如锡(sn)等时,孔径变大。此外,存在可通过用酸处理使导入沸石骨格中的金属发生脱附,从而影响孔径的情况。通过离子交换,以离子半径大的1价离子交换沸石中的离子时,有效孔径减小,另一方面,以离子半径小的1价离子进行离子交换时,有效孔径为接近沸石结构所具有的孔径的值。通过甲硅烷化处理,可降低沸石的有效孔径。例如,通过将沸石膜的外表面的末端硅烷醇甲硅烷化,进一步地,通过层叠甲硅烷化层,朝向沸石的外表面的孔的有效孔径减小。本发明中所使用的沸石膜复合物的分离功能没有特别限制,可通过控制沸石的表面物性,通过控制气体分子对沸石膜的亲和性、吸附性来体现。即,通过控制沸石的极性来控制氨在沸石上的吸附性,使其易于透过。例如,如本发明的第二实施方式,通过使氮原子存在而控制沸石的极性,可控制氨在沸石上的亲和性,使其易于透过。此外,通过以al原子取代沸石骨格的si原子,可增大极性,由此,可使像氨这样的极性大的气体分子主动地在沸石孔中吸附、透过。此外,可将ga、fe、b、ti、zr、sn、zn等al原子源以外的其他原子源添加在水热合成的水性反应混合物中,控制所得的沸石的极性。此外,通过离子交换,不仅控制沸石的孔径,还可控制分子的吸附性能,控制透过速度。(沸石膜)本发明中的沸石膜是指由沸石构成的膜状物,优选为在多孔支撑体的表面上使沸石晶化而形成。作为构成膜的成分,在沸石以外可根据需要含有二氧化硅、氧化铝等无机粘合剂,聚合物等有机物或者修饰沸石表面的甲硅烷化剂等。本发明中所使用的沸石膜所含的优选沸石如上所述,沸石膜所含的沸石可为1种,也可含有多种。此外,如ana、gis、mer的易于生成混相的沸石,在晶体之外,也可含有非晶成分等。本发明的其他方式之一(沸石膜b)为含有沸石的沸石膜,其特征在于,x射线光电子能谱法所确定的相对于al元素的氮元素的摩尔比为0.01以上、4以下。沸石膜b特别优选用于第一实施方式的氨分离法。沸石膜b优选为具有x射线光电子能谱法(xps)所确定的氮原子相对于al原子的摩尔比在规定范围的表面的沸石膜。这里,本说明书中的沸石膜的表面是指为分离氨而供给由包含氨且包含氢和/或氮的多种成分构成的混合气体的一侧的沸石膜的表面,在以在多孔支撑体上成膜化的形态使用沸石膜复合物时,其意味着不与多孔支撑体接触的面。另外,本说明书中,沸石膜中所含的氮原子相对于al原子的摩尔比是指通过在以下的测定条件下的x射线光电子能谱法(xps)所确定的数值。(测定条件)测定时的x射线源:单色化al-kα射线,输出功率16kv-34w定量计算时的确定本底的方法:shirley法本发明的第二实施方式中,上述xps测定所确定的沸石膜表面所含的氮原子的含量,相对于沸石膜表面的al原子,以摩尔比计通常为0.01以上,优选为0.05以上,更优选为0.10以上,进一步优选为0.20以上,特别优选为0.30以上,尤其优选为0.50以上,其上限由于与沸石膜所含的沸石中的含有氮原子的阳离子种的结构、根据需要进行沸石膜的硝酸盐处理时残留的硝酸离子的量相关,没有特别限制,但通常为4以下,优选为3以下,更优选为1以下。通过使用具有像这样的规定的氮原子/al原子比的表面组成的沸石,在提高沸石膜的致密性以及耐化学反应性、耐热性等的耐久性的同时,可从由包含氨且包含氢和/或氮的多种成分构成的混合气体中,以高透过度且高选择性地分离氨。这里,上限以及下限的记载值在有效数字范围内有效。即,上限4以下意味着小于4.5,另一方面0.01以上意味着0.005以上。本发明的第二实施方式中沸石膜所含的氮原子可举出后述的沸石中所含的铵离子(nh4+)、来源于将甲胺、二甲胺、三甲胺、乙胺、二乙胺、三乙胺、乙二胺、二甲基乙二胺、四甲基乙二胺、二亚乙基三胺、三亚乙基四胺、苯胺、甲基苯胺、苄胺、甲基苄胺、六亚甲基二胺、n,n-二异丙基乙胺、n,n,n-三甲基-1-金刚烷胺、吡啶以及哌啶等碳原子数1~20的有机胺质子化而成的阳离子种的氮原子、来源于制造沸石膜时使用含有氮原子的有机模板(结构导向剂)时的有机模板的氮原子、来源于后述根据需要而实施的沸石膜的硝酸盐处理时残留的硝酸离子的氮原子等。本实施方式中尚未详知,没有特别限制,但如下文所述地其特征在于,利用氨在沸石上的吸附,在控制用于膜分离的沸石的有效孔径的同时,基于沸石孔内的氨的跳跃机制而分离氨。在像这样主要利用伴随氨在沸石上的吸附/脱附的孔内跳跃机制进行氨分离的本发明中,首先,如何使包含氨的供给混合气体中的氨与沸石膜表面的吸附亲和性高于该混合气体中所含的其他氢、氮等气体是重要的设计因素。出于该角度,使如上述形态的氮原子存在于沸石膜表面时,通过与供给气体中的氨的氢键等相互作用,可提高氨在沸石膜上的吸附亲和性,因而氨分离性能趋于提高。此外,本发明的其他方式之一(沸石膜c)为含有沸石的沸石膜,其特征在于,x射线光电子能谱法所确定的si元素相对于al元素的摩尔比为2.0以上、10以下。沸石膜c优选用于第一实施方式的氨分离法。本发明中所使用的沸石膜c的特征在于,其为具有x射线光电子能谱法(xps)所确定的si原子相对于al原子的摩尔比在规定范围的表面的沸石膜。另外,本说明书中,沸石膜中所含的si原子相对于al原子的摩尔比是指在以下的测定条件下通过x射线光电子能谱法(xps)所确定的数值。(测定条件)测定时的x射线源:单色化al-kα射线,输出功率16kv-34w定量计算时的确定本底的方法:shirley法本实施方式中,上述的xps测定所确定的沸石膜表面所含的si原子含量,相对于沸石膜表面的al原子,以摩尔比计为2.0以上,优选为2.5以上,更优选为3.0以上,其上限通常为10以下,优选为8.0以下,更优选为7.0以下,特别优选为6.7以下。本发明中,沸石膜中的si原子相对于al原子的摩尔比,如下文所述地,可通过控制沸石膜中的沸石sio2/al2o3比的方法、用铝盐处理沸石膜的方法等进行控制。通过使用像这样规定的si原子/al原子摩尔比的沸石膜,在从由包含氨且包含氢和/或氮的多种成分构成的混合气体中分离氨时,如基于本实施例可知地,在可提高沸石膜的致密性以及耐化学反应性、耐热性等的耐久性的同时,可表现出高透过选择性以及高透过度,且提高高温时的分离热稳定性。此外,本实施方式中,在控制上述的沸石膜表面的si原子含量的同时,若根据需要将xps测定所确定的沸石膜表面所含的氮原子的含量控制在规定范围时,可趋于显著提高从由沸石膜表面所含的多种成分构成的混合气体中进行氨分离时的分离选择性,因此优选使氮原子在沸石膜表面共存,且恰当控制它们的含量。像这样地根据需要使氮原子存在于沸石膜表面时,该氮原子的含量,相对于沸石膜表面的al原子,以摩尔比计通常为0.01以上,优选为0.05以上,更优选为0.10以上,进一步优选为0.20以上,特别优选为0.30以上,尤其优选为0.50以上,其上限与沸石膜所含的沸石中的含有氮原子的阳离子种的结构、根据需要进行沸石膜的硝酸盐处理时残留的硝酸离子量相关,因而没有特别限制,通常为4以下,优选为3以下,更优选为1以下。使用具有像这样规定的氮原子/al原子比的表面组成的沸石时,在提高沸石膜的致密性以及耐化学反应性、耐热性等耐久性的同时,可从由包含氨且包含氢和/或氮的多种成分构成的混合气体中高选择性地分离氨,因而优选。另外,上述上限以及下限的记载值在有效数字范围内有效。即,上限4以下意味着小于4.5,另一方面0.01以上意味着0.005以上。。本实施方式中使沸石膜含有氮原子时的氮原子可为后述的沸石中所含的铵离子(nh4+)、来源于将甲胺、二甲胺、三甲胺、乙胺、二乙胺、三乙胺、乙二胺、二甲基乙二胺、四甲基乙二胺、二亚乙基三胺、三亚乙基四胺、苯胺、甲基苯胺、苄胺以及甲基苄胺、六亚甲基二胺、n,n-二异丙基乙胺、n,n,n-三甲基-1-金刚烷胺、吡啶以及哌啶等碳原子数1~20的有机胺质子化而成的阳离子种的氮原子、来源于制造沸石膜时使用含有氮原子的有机模板(结构导向剂)时的有机模板的氮原子、来源于后述根据需要而实施的沸石膜的硝酸盐处理时残留的硝酸离子的氮原子等。本实施方式中,进一步地,在将xps测定所确定的沸石膜表面所含的碱金属原子的含量控制在规定范围时,从由包含氨且包含氢和/或氮的多种成分构成的混合气体中进行氨分离时的氨透过度趋于提高。因此,根据需要控制它们的含量是优选方式之一。作为像这样地在沸石膜表面上根据需要而使碱金属原子存在的情况下的碱金属原子,可举例为li、na、k、rb、cs以及它们的两种以上的金属原子,其中优选li、na、cs,出于氨分离性能优异且为广泛使用的碱金属的理由,更优选na。另外,这些碱金属原子作为构成沸石膜的沸石中的al位点的离子对,以阳离子的形态存在,通常如下文所述地,通过所合成的沸石膜的离子交换处理导入沸石中。根据需要,使沸石膜表面存在碱金属原子时的碱金属原子的含量,相对于沸石膜表面的al原子,以摩尔比计为0.01以上,优选为0.02以上,更优选为0.03以上,进一步优选为0.04以上,特别优选为0.05以上,其上限通常为0.10摩尔当量以下,优选为0.070摩尔当量以下,更优选为0.065摩尔当量以下,进一步优选为0.060摩尔当量以下,特别优选为055摩尔当量以下。将碱金属原子的含量控制为上述范围时,在提高氨分离选择性的同时,趋于可提高氨的透过度,是优选的。另外,沸石膜中碱金属原子相对于al原子的摩尔比,如下文所述地,可通过调整沸石的离子交换处理时的离子交换量而进行控制。本实施方式中尚未详知,没有特别限制,但如下文所述地其特征在于,利用氨在沸石上的吸附,在控制用于膜分离的沸石的有效孔径的同时,基于沸石孔内的氨的跳跃机制而分离氨。在像这样地主要利用伴随氨在沸石上的吸附/脱附的孔内跳跃机制进行氨分离的本发明中,首先,如何使包含氨的供给混合气体中的氨与沸石膜表面的吸附亲和性高于该混合气体中所含的其他氢、氮等气体是重要的设计因素。出于该角度,使较多al原子在沸石膜表面存在时,沸石膜表面的极性改变,与供给气体中的氨的吸附亲和性提高,因而氨分离性能提高。此外,本实施方式中,沸石膜表面的al原子含量可通过构成沸石膜的沸石的sio2/al2o3比、沸石膜形成后的铝盐处理等进行控制,特别是后者铝盐处理还具有密封沸石膜表面上存在的微细的缺陷的效果,在可提高沸石膜的致密性以及耐化学反应性、耐热性等耐久性的同时,非常有助于本发明的课题之一的沸石膜的高温时的分离热稳定性的提高。此外,本发明的其他方式之一(沸石膜d)为含有沸石的沸石膜,其特征在于x射线光电子能谱法所确定的碱金属元素相对于al元素的摩尔比为0.01以上、0.070以下。沸石膜d特别优选用于第一实施方式的氨分离法。本发明的第四实施方式中所使用的沸石膜d优选为具有x射线光电子能谱法(xps)所确定的碱金属原子相对于al原子的摩尔比在规定范围的表面的沸石膜。另外,本说明书中,沸石膜中所含的碱金属原子相对于al原子的摩尔比是指在以下的测定条件下通过x射线光电子能谱法(xps)所确定的数值。(测定条件)测定时的x射线源:单色化al-kα射线,输出功率16kv-34w定量计算时的确定本底的方法:shirley法本实施方式中,作为通过上述xps测定所确定的沸石膜表面所含的碱金属原子,可举例li、na、k、rb、cs以及它们中的两种以上的金属原子,其中优选li、na、cs,出于氨分离性能优异且为广泛使用的碱金属的理由,更优选na。另外,这些碱金属原子作为构成沸石膜的沸石中的al位点的离子对,以阳离子的形态存在,通常如下文所述地,可通过所合成的沸石膜的离子交换处理导入沸石中。本实施方式中,控制通过上述xps测定所确定的沸石膜表面所含的碱金属原子的含量是重要的,相对于沸石膜表面的al原子,其含量以摩尔比计为0.01以上,优选为0.02以上,更优选为0.03以上,进一步优选为0.04以上,特别优选为0.05以上,其上限通常为0.10摩尔当量以下,优选为0.070摩尔当量以下,更优选为0.065摩尔当量以下,进一步优选为0.060摩尔当量以下,特别优选为055摩尔当量以下。基于本实施例以及参考例可知,通过将碱金属元素的含量控制在上述范围,可在提高氨分离选择性的同时,提高氨的透过度。本实施方式中,沸石膜中的碱金属原子相对于al原子的摩尔比,如下文所述地,可通过调整沸石的离子交换处理时的离子交换量而进行控制。通过使用像这样的规定的碱金属原子/al原子比的沸石膜,从由包含氨且包含氢和/或氮的多种成分构成的混合气体中分离氨时,在表现出高透过选择性的同时,相比不含该碱金属原子的沸石膜,可提高氨的透过度。此外,本实施方式中,在控制上述的沸石膜表面的碱金属原子的含量的同时,若根据需要将通过xps测定所确定的沸石膜表面所含的氮原子的含量控制在规定范围时,趋于显著提高从由包含氨且包含氢和/或氮的多种成分构成的混合气体中进行氨分离时的分离选择性,因此优选使碱金属原子和氮原子在沸石膜表面共存,且恰当控制它们的含量。像这样地根据需要使氮原子存在于沸石膜表面时,该氮原子的含量,相对于沸石膜表面的al原子,以摩尔比计通常为0.01以上,优选为0.05以上,更优选为0.10以上,进一步优选为0.20以上,特别优选为0.30以上,尤其优选为0.50以上,其上限与沸石膜所含的沸石中的含有氮原子的阳离子种的结构、根据需要进行沸石膜的硝酸盐处理时残留的硝酸离子量相关,因而没有特别限制,通常为4以下,优选为3以下,更优选为1以下。使用具有像这样规定的氮原子/al原子比的表面组成的沸石时,在可提高沸石膜的致密性以及耐化学反应性、耐热性等耐久性的同时,可从由包含氨且包含氢和/或氮的多种成分构成的混合气体中高选择性地分离氨,因而优选。另外,上述上限以及下限的记载值在有效数字范围内有效。即,上限4以下意味着小于4.5,另一方面0.01以上意味着0.005以上。本实施方式中使沸石膜含有氮原子时的氮原子可为后述的沸石中所含的铵离子(nh4+)、来源于将甲胺、二甲胺、三甲胺、乙胺、二乙胺、三乙胺、乙二胺、二甲基乙二胺、四甲基乙二胺、二亚乙基三胺、三亚乙基四胺、苯胺、甲基苯胺、苄胺以及甲基苄胺、六亚甲基二胺、n,n-二异丙基乙胺、n,n,n-三甲基-1-金刚烷胺、吡啶以及哌啶等碳原子数1~20的有机胺质子化而成的阳离子种的氮原子、来源于制造沸石膜时使用含有氮原子的有机模板(结构导向剂)时的有机模板的氮原子、来源于后述根据需要而实施的沸石膜的硝酸盐处理时残留的硝酸离子的氮原子等。本实施方式中尚未详知,没有特别限制,但如下文所述地其特征在于,利用氨在沸石上的吸附,在控制用于膜分离的沸石的有效孔径的同时,基于沸石孔内的氨的跳跃机制而分离氨。在像这样地主要利用伴随氨在沸石上的吸附/脱附的孔内跳跃机制进行氨分离的本发明中,从由包含氨且包含氢和/或氮的多种成分构成的混合气体中的氨分离选择性,虽然通过沸石孔内的氨在al位点上的吸附引起的堵塞效应而提高,但另一方面,由于氨在al位点上的吸附力高,因而趋于损害透过性能(透过度)。与之相对地,在使本发明的碱金属原子作为构成沸石膜的沸石中的al位点的离子对,以阳离子的形态以规定量存在时,可控制氨在al位点上的吸附量,另一方面,可通过碱金属阳离子的尺寸保持氨分离选择性。出于这些机制,可在保持氨分离选择性的同时,提高透过性能。即,可认为将沸石中的碱金属原子相对于al原子的含量控制在以摩尔比计为0.01以上、0.070以下是重要的,在其小于0.01时,由于氨在al位点上的吸附,氨的透过度降低,另一方面,以大于0.20的量含有时,氨在al位点上的吸附引起的堵塞效应弱,氨分离选择性降低。此外,本发明的其他方式之一(沸石膜复合物e)为具备多孔支撑体以及其表面上的含有沸石的沸石膜的氨分离用沸石膜复合物,其特征在于,上述沸石的300℃以及400℃的热膨胀率相对于30℃的热膨胀率的变化率在规定范围内。沸石膜复合物e优选用于第一实施方式的氨分离法。具体地,沸石的300℃的热膨胀率相对于30℃的热膨胀率的变化率为±0.25%以内,400℃的热膨胀率相对于30℃的热膨胀率的变化率为±0.35%以内。本实施方式的沸石所定义的热膨胀率是指在以下条件下算出的数值。另外,本说明书中,热膨胀率的数值为正数时,表示沸石膨胀,其为负数时,表示沸石收缩。(热膨胀率的变化率的测定方法)本发明中,沸石的规定温度下的热膨胀率相对于30℃的热膨胀率的变化率可通过在以下条件下的升温xrd测定法,求出在30℃和规定温度下测定的晶格常数,通过下述式(1)而求得。(升温xrd测定装置规格)【表1】表1(测定条件)【表2】表2测定氛围:大气升温条件:20℃/min测定方法:在测定温度下保持5分钟后实施xrd测定。测定数据中使用可变狭缝,进行固定狭缝校正。热膨胀率的变化率=(规定温度下测定的晶格常数)÷(30℃下测定的晶格常数)-1…(1)本发明的沸石的300℃的热膨胀率相对于30℃的热膨胀率的变化率,以其绝对值计为0.25%以下,优选为0.20%以下,更优选为0.15%以下,尤其优选为0.10%以下,最优选为0.05%以下。即,沸石的300℃的热膨胀率相对于30℃的热膨胀率的变化率为±0.25%以内,优选为±0.20%以内,更优选为±0.15%以内,尤其优选为±0.10%以内,最优选为±0.05%以内。另一方面,沸石的400℃的热膨胀率相对于30℃的热膨胀率的变化率,以其绝对值计为0.35%以下,优选为0.30%以下,更优选为0.25%以下,尤其优选为0.20%以下,特别优选为0.15%以下,最优选为0.10%以下。即,沸石的400℃的热膨胀率相对于30℃的热膨胀率的变化率为±0.35%以内,优选为±0.30%以内,更优选为±0.25%以内,尤其优选为±0.20%以内,特别优选为±0.15%以内,最优选为±0.10%以内。将像这样的显示出低热膨胀率的变化率的沸石在多孔支撑体上成膜而成的沸石膜复合物,从由包含氨且包含氢和/或氮的多种成分构成的气体混合物中使氨透过时,在将该复合物升温至大于200℃的温度条件,特别是大于250℃的温度条件,进一步大于300℃的温度时,不易产生由沸石的热膨胀(收缩)引起的沸石晶界的裂纹,因而即使在高温条件下,也可高透过度且高效地将氨稳定地分离至透过侧。使用表现出像这样的热膨胀率的沸石的沸石膜复合物,特别地如本实施例的rho型沸石所记载地,即使表现出相对于温度的非线性的热膨胀/收缩的行为,在高温条件下作为膜,也可稳定地表现出高分离性能。这里,相对于温度的非线性的热膨胀/收缩的行为是指不相对于温度单调地热膨胀或收缩的行为,即,例如是指以下行为,在某一温度范围中表现出热膨胀或热收缩行为,但在此外的温度范围中表现出相反行为,即前者的情况下热收缩,后者的情况下热膨胀。这尚未详知,没有特别限制,但可认为是由于形成了致密的沸石膜复合物,其升温过程中,即使沸石热收缩、热膨胀,沸石也可在支撑体上适当移动,不生成裂纹,表现出适应高温条件下的高分离性能。因此,在高温条件下稳定地分离氨时,也可以使用在升温过程中表现出非线性的热膨胀/收缩行为的沸石。作为本发明中使用的沸石没有特别限制,已知有例如,rho(d.r.corbin.etal.j.am.chem.soc,112,4821-4830)、mfi、afi、ddr(parks.h.etal.stud.surf.sci.catal.1997,105,1989-1994)等。此外,本实施方式的沸石的、相对于30℃的热膨胀率的400℃的该热膨胀率的变化率与相对于30℃的热膨胀率的300℃的热膨胀率的变化率的比,以绝对值计通常为120%以下,优选为115%以下,更优选为110%以下,尤其优选为105%以下,最优选为103%以下。使用表现出像这样的规定温度间的规定热膨胀率的变化率比的沸石,在多孔支撑体上成膜而成的沸石膜复合物,例如,即使在开始氨制造时其反应初期在反应器内产生不均匀发热时,也可抑制局部沸石的热膨胀(收缩)引起的晶界裂纹的产生,因而可高透过度且高效地将氨稳定地分离至透过侧。本实施方式的沸石膜复合物若在合成膜时,经由将热膨胀率的变化率在规定范围内的沸石作为晶种附着在多孔支撑体上的工序而制备时,在很多情况下,即使在高温条件下也可稳定地以高选择性分离氨,是优选的。在像这样的沸石膜复合物的制备中,作为晶种而使用的沸石的热膨胀率的变化率,以300℃的热膨胀率相对于30℃的热膨胀率的变化率的绝对值计,为0.25%以下,优选为0.20%以下,更优选为0.15%以下,尤其优选为0.10%以下,最优选为0.05%以下。另一方面,400℃的热膨胀率相对于30℃的热膨胀率的变化率以其绝对值计通常为0.30%以下,优选为0.25%以下,更优选为0.20%以下,尤其优选为0.15%以下,最优选为0.10%以下。作为本实施方式的特征的沸石的规定温度下的热膨胀率的变化率,如后文所述地,可通过恰当选择使用的沸石的阳离子种而进行控制。例如,关于rho型沸石的阳离子种与热膨胀率的关系,如化学通讯(chemical,communications),2000,2221-2222.所记载地,已知由于沸石中所含的阳离子种,热膨胀率有所变化。因此,为获得本实施方式的即使在高温条件下也可稳定地以高选择性分离氨的沸石膜复合物,在rho型沸石之中,选定规定的阳离子种是尤为重要的。另一方面,关于本实施方式的实施例所述的mfi沸石的热膨胀率,与上述rho型沸石的情况同样地,通过选择恰当的沸石中的阳离子种,可制造表现出本实施方式特性的沸石膜复合物。作为本实施方式的沸石中所含的阳离子种,理想的是易于配位于沸石的离子交换位点的阳离子种,例如,选自周期表的第1列、第2列、第8列、第9列、第10列、第11列和第12列的元素群的阳离子种,nh4+,以及它们中的两种以上的阳离子种,更优选为选自周期表的第1列、第2列的元素群的阳离子种,nh4+,以及它们中的两种以上的阳离子种。本实施方式中所使用的沸石为铝硅酸盐。铝硅酸盐的sio2/al2o3摩尔比没有特别限制,但通常为6以上,优选为7以上,更优选为8以上,进一步优选10以上,尤其优选为11以上,特别优选为12以上,最优选为13以上。上限是通常al为杂质程度的量,以sio2/al2o3摩尔比计,通常为500以下,优选为100以下,更优选为90以下,进一步优选为80以下,尤其优选为70以下,更优选为50以下,最优选为30以下。通过使用像这样的规定范围的sio2/al2o3摩尔比的沸石,可提高沸石膜的致密性以及耐化学反应性、耐热性等耐久性。此外,出于从由包含氨且包含氢和/或氮的多种成分构成的气体混合物中使氨透过的分离性能的角度,基于如上述地al元素的酸性位点成为氨吸附位点的理由,优选使用含有规定量al的沸石,通过使用显示出上述sio2/al2o3摩尔比的沸石,能高透过度且高选择性地分离氨。沸石的sio2/al2o3摩尔比可通过后述的水热合成的反应条件进行调整。本发明中所使用的沸石膜的厚度没有特别限制,但通常为0.1μm以上,优选为0.3μm以上,更优选为0.5μm以上,进一步优选为0.7μm以上,更进一步优选为1.0μm以上,特别优选为1.5μm以上。此外,通常为100μm以下,优选为60μm以下,更优选为20μm以下,进一步优选为15μm以下,更进一步优选为10μm以下,特别优选为5μm以下的范围。若沸石膜的厚度为上述下限值以上,则趋于不易产生缺陷,分离性能改善。此外,若沸石膜的厚度为上述上限值以下,则透过性能趋于提高,进一步地,高温区域中,不易因升温而在沸石膜上产生裂纹,因而趋于可抑制高温时的透过选择性的降低。形成沸石膜的沸石的平均一次粒径没有特别限制,通常为30nm以上,优选为50nm以上,更优选为100nm以上,其上限为膜的厚度以下。若沸石的平均一次粒径为上述下限值以上,则可减小沸石的晶界,因而可获得良好的透过选择性。因此,最优选沸石的平均一次粒径与沸石膜的厚度相同的情况。此时,可将沸石的晶界降至最小。后述的水热合成中所得的沸石膜由于可使沸石的粒径与膜的厚度相同,因而优选。另外,本发明中,平均一次粒径是在用扫描型电子显微镜对本发明的沸石膜复合物的表面或断裂面的观察中,对于任意选择的30个以上的颗粒测定一次粒径,作为平均值而求得。沸石膜的形状没有特别限制,可采用管状、中空纤维状、整体(monolith)型、蜂窝型等所有形状。此外,沸石膜的尺寸也没有特别限定,例如,可作为形成于后述尺寸的多孔支撑体上的沸石膜复合物而形成。(多孔支撑体)本发明中,沸石膜优选在多孔支撑体的表面等上形成。优选沸石在多孔支撑体上晶化为膜状。本发明中所使用的多孔支撑体优选具有可使沸石在其表面晶化为膜状的化学的稳定性。作为合适的多孔支撑体,可举出聚砜、乙酸纤维素、芳香族聚酰胺、偏二氟乙烯、聚醚砜、聚丙烯腈、聚乙烯、聚丙烯、聚四氟乙烯和聚酰亚胺等气体透过性的多孔质高分子;二氧化硅、α-氧化铝、γ-氧化铝、莫来石、氧化锆、二氧化钛、氧化钇、氮化硅、碳化硅等陶瓷烧结体;铁、青铜、不锈钢等烧结金属、网状的成形体;玻璃、碳成型体等无机多孔质。其中,作为高温区域下的氨分离用的多孔支撑体,出于该支撑体的高温时的机械强度、耐变形性、热稳定性、耐反应性优异的理由,这些之中优选陶瓷烧结体和金属烧结体、玻璃、碳成型体等无机多孔支撑体。无机多孔支撑体优选烧结陶瓷即基本成分或其大部分由无机非金属物质构成的固体材料而成的支撑体。作为优选的陶瓷烧结体,如上所述地,可举出包括α-氧化铝、γ-氧化铝、二氧化硅、莫来石、氧化锆、二氧化钛、氧化钇、氮化硅、碳化硅等的陶瓷烧结体,它们可为单独的烧结体,也可将多种混合烧结。这些陶瓷烧结体因为其一部分表面在沸石膜合成中会沸石化,由此,多孔支撑体和沸石膜的密着性提高,因而可提高沸石膜复合物的耐久性。特别地,包含氧化铝、二氧化硅、莫来石中的至少一种的无机多孔支撑体易于产生无机多孔支撑体的部分沸石化,因而无机多孔支撑体与沸石的结合变牢固,易于形成致密且分离性能高的沸石膜,因而更优选。本发明中所使用的多孔支撑体优选其表面(下文中也称为“多孔支撑体表面”)上,具有使形成于多孔支撑体上的沸石晶化的作用。上述多孔支撑体表面优选对孔径进行控制。多孔支撑体表面附近的多孔支撑体的平均孔径通常为0.02μm以上,优选为0.05μm以上,更优选为0.1μm以上,进一步优选为0.15μm以上,进一步更优选为0.5μm以上,尤其优选为0.7μm以上,最优选为1.0μm以上,通常为20μm以下,优选为10μm以下,更优选为5μm以下,特别优选为2μm以下。通过使用具有像这样的范围的孔径的多孔支撑体,可形成提高氨的透过选择性的致密沸石膜。优选多孔支撑体的表面平滑,可根据需要通过打磨表面等进行研磨。本发明中所使用的多孔支撑体的多孔支撑体表面附近以外的部分的孔径不受限制,此外没有特别控制的必要,但该其他部分的气孔率通常为20%以上,更优选为30%以上,通常为60%以下,优选为50%以下。多孔支撑体表面附近以外的部分的气孔率影响分离气体、液体时的透过流量,通过为上述下限以上,透过物趋于易于扩散,为上述上限值以下则趋于易于防止多孔支撑体的强度降低。此外,作为控制透过流量的方法,可使用将气孔率不同的多孔质体组合为层状而成的多孔支撑体。本发明中所使用的多孔支撑体的形状若为可有效分离混合气体、液体混合物的形状则没有特别限制,具体地可举出平板状、管状、圆筒状、具有大量贯通孔的蜂窝状的支撑体、整体状等。此外,多孔支撑体的尺寸等为任意,适当选择调整以获得期望的沸石膜复合物即可。其中,存在多孔支撑体的形状优选为管状的情况。管状多孔支撑体的长度没有特别的限制,通常为2cm以上,优选为4cm以上,更优选为5cm以上,特别优选为10cm以上,尤其优选为40cm以上,最优选为50cm以上,另一方面,通常为200cm以下,优选为150cm以下,更优选为100cm以下。多孔支撑体的长度为上述下限值以上时,可增加每一根的混合气体的分离处理量,因而可降低设备成本。此外,其为上述上限值以下时,可简化沸石膜复合物的制造,进一步地可防止由于使用时的振动等而易于折断等问题的产生。管状多孔支撑体的内径通常为0.1cm以上,优选为0.2cm以上,更优选为0.3cm以上,特别优选为0.4cm以上,通常为2cm以下,优选为1.5cm以下,更优选为1.2cm以下,特别优选为1.0cm以下。外径通常为0.2cm以上,优选为0.3cm以上,更优选为0.6cm以上,特别优选为1.0cm以上,通常为2.5cm以下,优选为1.7cm以下,更优选为1.3cm以下。管状多孔支撑体的壁厚通常为0.1mm以上,优选为0.3mm以上,更优选为0.5mm以上,进一步优选0.7mm以上,更优选为1.0mm以上,特别优选为1.2mm以上,通常为4mm以下,优选为3mm以下,更优选为2mm以下。若管状多孔支撑体的内径、外径和壁厚分别为上述下限值以上,则可提高支撑体的强度,使其不易折断。此外,若管状支撑体的内径和外径分别为上限值以下,则可减小伴随氨分离的设备的尺寸,因而在经济上有利。此外,若管状支撑体的壁厚为上述上限值以下,则趋于提高透过性能。第五实施方式中所使用的多孔支撑体的300℃的热膨胀率相对于30℃的热膨胀率的变化率,以其绝对值计为0.25%以下,优选为0.20%以下,更优选为0.15%以下,尤其优选为0.10%以下,最优选为0.05%以下。即,沸石膜复合物e的多孔支撑体的300℃的热膨胀率相对于30℃的热膨胀率的变化率为±0.25%以内,优选为±0.20%以内,更优选为±0.15%以内,尤其优选为±0.10%以内、最优选为±0.05%以内。另一方面,沸石膜复合物e的多孔支撑体的400℃的热膨胀率相对于30℃的热膨胀率的变化率,以其绝对值计通常为0.30%以下,优选为0.25%以下,更优选为0.20%以下,尤其优选为0.15%以下,最优选为0.10%以下。即,多孔支撑体的400℃的热膨胀率相对于30℃的热膨胀率的变化率为±0.30%以内,优选为±0.25%以内,更优选为±0.20%以内,尤其优选为±0.15%以内,最优选为±0.10%以内。在表现出像这样的低热膨胀率的多孔支撑体上成膜而成的沸石膜复合物,例如,即使在大于200℃的温度条件下,进一步地大于300℃的温度条件下,出于从由包含氨且包含氢和/或氮的多种成分构成的气体混合物中使氨透过的目的,升温该复合物时,伴随多孔支撑体的热膨胀(收缩)也难以产生沸石膜的裂纹,因而即使在高温条件下,也可高透过度且高效地将氨稳定地分离至透过侧。此外,第五实施方式中所使用的多孔支撑体的相对于30℃的热膨胀率的400℃的该热膨胀率的变化率与相对于30℃的热膨胀率的300℃的热膨胀率的变化率的比,以绝对值计通常为120%以下,优选为115%以下,更优选为110%以下,尤其优选为105%以下,最优选为103%以下。在表现出像这样的规定的温度间的规定热膨胀率比的多孔支撑体上成膜而成的沸石膜复合物,例如,即使在氨制造中反应器内产生不均匀的发热时,也可抑制伴随局部的多孔支撑体的热膨胀(收缩)的沸石膜裂纹的产生,因而即使在高温条件下,也可高透过度且高效地将氨稳定地分离至透过侧。(沸石膜复合物)本发明中,沸石膜优选作为至少包含沸石和支撑体而构成的沸石膜复合物进行使用。本发明中,沸石膜复合物是指在上述多孔支撑体的表面等上,使上述沸石固着为膜状,优选晶化固着,根据情况,优选一部分沸石固着到支撑体的内部的状态。作为沸石膜复合物,例如,优选在多孔支撑体的表面等通过水热合成使沸石晶化为膜状。沸石膜在多孔支撑体上的位置没有特别限制,在使用管状支撑体时,可在外表面形成沸石膜,也可在内表面形成,进一步地可根据适用的体系,在两面形成。此外,可在支撑体的表面上层叠而形成,也可使其晶化以填入支撑体的表面层的孔内。该情况下,晶化的膜层的内部没有裂纹、连续微孔是重要的,出于提高分离性的方面,优选形成所谓致密的膜。此外,构成沸石膜复合物的沸石和支撑体没有特别的限制,优选任意组合上述沸石和支撑体而使用,但其中,特别优选的沸石和多孔支撑体的组合可具体举出mfi型沸石-多孔质氧化铝支撑体、rho型沸石-多孔质氧化铝支撑体、ddr型沸石-多孔质氧化铝支撑体、afi型沸石-多孔质氧化铝支撑体、cha型沸石-多孔质氧化铝支撑体、aei型沸石-多孔质氧化铝支撑体,优选为cha型沸石-多孔质氧化铝支撑体、mfi型沸石-多孔质氧化铝支撑体、rho型沸石-多孔质氧化铝支撑体,更优选为mfi型沸石-多孔质氧化铝支撑体、rho型沸石-多孔质氧化铝支撑体。本发明的一种实施方式(沸石膜b~e)中,优选为mfi型沸石-多孔质氧化铝支撑体、rho型沸石-多孔质氧化铝支撑体,更优选为rho型沸石-多孔质氧化铝支撑体。<沸石膜复合物的制造方法>本发明中,沸石膜复合物的形成方法若为可将上述的沸石膜在多孔支撑体上形成的方法则没有特别限制,可通过公知的方法制造。例如,可使用以下等任意的方法:(1)使沸石在支撑体上晶化为膜状的方法、(2)在支撑体上以无机粘合剂或有机粘合剂等使沸石固着的方法、(3)将分散有沸石的聚合物在支撑体上固着的方法、(4)通过将沸石浆料含浸入支撑体中,根据情况进行抽吸,使沸石固着在支撑体上的方法。其中,特别优选使沸石在多孔支撑体上晶化为膜状的方法。晶化的方法没有特别限制,但优选将支撑体投入用于沸石制造的水热合成用的反应混合物(下文中可将其称为“水性反应混合物”)中,直接通过水热合成,使沸石在支撑体表面等上晶化的方法。该情况下,可通过例如,将调整组成均匀化的水性反应混合物投入内部装有多孔支撑体的高压釜等耐热耐压容器,密闭、加热一定时间,制造沸石膜复合物。水性反应混合物含有si原子源、al原子源、碱源和水,进一步地根据需要含有有机模板(结构导向剂)。为对沸石膜复合物的制造方法有更为深入的理解,下文作为代表例,对于rho型沸石膜复合物以及mfi型沸石膜复合物的制造方法进行详细说明,然而本发明的沸石膜及其制造方法不受这些说明的限定。(rho型沸石膜)本发明中所使用的rho型沸石是指以国际沸石协会(iza)所确定的规定沸石结构的代码为rho结构的沸石。rho型沸石的结构特征为具有由直径的氧8元环构成的三维孔。本发明中所使用的rho型沸石的骨架密度为骨架密度是指沸石的每中的氧以外的构成骨架的原子数,该值由沸石的结构所确定。另外,骨架密度与沸石的结构的关系如《沸石骨架类型图集》(第5次修订版,2007爱思唯尔出版社)所示。(mfi型沸石膜)本发明中所使用的mfi型沸石是指以国际沸石协会(iza)所确定的规定沸石结构的代码为mfi结构的沸石。mfi型沸石的结构特征为具有由或直径的氧10元环构成的三维孔,其结构可通过x射线衍射数据表征。本发明中所使用的mfi型沸石的骨架密度为骨架密度是指沸石的每中的氧以外的构成骨架的原子数,该值由沸石的结构所确定。另外,骨架密度与沸石的结构上的关系如《沸石骨架类型图集》(第5次修订版,2007爱思唯尔出版社)所示。<rho型沸石膜的制造方法>(硅原子源)用于水性反应混合物的硅(si)原子源没有特别限制,可举出例如,铝硅酸盐沸石、气相法二氧化硅、胶体二氧化硅、无定形二氧化硅、硅酸钠、硅酸甲酯、硅酸乙酯、三甲基乙氧基硅烷等硅醇盐(siliconalkoxides)、原硅酸四乙酯、铝硅酸盐凝胶等,优选为铝硅酸盐沸石、气相法二氧化硅、胶体二氧化硅、无定形二氧化硅、硅酸钠、硅酸甲酯、硅酸乙酯、硅醇盐、铝硅酸盐凝胶。它们可单独使用一种,也可混合两种以上使用。以使相对于si原子源的其他原料的使用量分别为前述或后述的适当范围的方式使用si原子源。(铝原子源)多孔支撑体-rho型沸石膜复合物的制造中所使用的铝(al)原子源没有特别限制,可举出铝硅酸盐沸石、非晶态氢氧化铝、三水铝石结构的氢氧化铝、三羟铝石结构的氢氧化铝、硝酸铝、硫酸铝、氧化铝、铝酸钠、勃姆石、假勃姆石、铝醇盐、铝硅酸盐凝胶等,优选为铝硅酸盐沸石、非晶态氢氧化铝、铝酸钠、勃姆石、假勃姆石、铝醇盐、铝硅酸盐凝胶,特别优选铝硅酸盐沸石、非晶态氢氧化铝、铝酸钠、铝硅酸盐凝胶。它们可单独使用一种,也可混合两种以上使用。铝硅酸盐沸石可单独使用一种,也可混合两种以上使用。在使用铝硅酸盐沸石作为al原子源的情况下,优选全al原子源的50质量%以上、特别是70~100质量%、尤其是90~100质量%为上述铝硅酸盐沸石。此外,在使用铝硅酸盐沸石作为si原子源的情况下,优选全si原子源的50质量%以上、特别是70~100质量%、尤其是90~100质量%为上述铝硅酸盐沸石。铝硅酸盐沸石的比例在该范围时,rho型沸石膜的si原子/al原子摩尔比提高,可成为耐酸性、耐水性优异、适用范围广的沸石膜。晶种以外的原料混合物所含的al原子源(包括前述的铝硅酸盐沸石和其他al原子源)相对于硅(si原子)的使用量(al原子/si原子比)的优选范围通常为0.01以上,优选为0.02以上,更优选为0.04以上,进一步优选为0.06以上,通常为1.0以下,优选为0.5以下,更优选为0.2以下,进一步优选为0.1以下。通过控制在该使用量的范围,易于将沸石中的氮原子、碱金属元素的含量控制在本发明的优选范围。此外,为增大al原子/si原子比率,则减少硅原子源相对于铝原子源的用量即可,另一方面,为减小该比率,则增加硅原子源相对于铝原子源的使用量即可。另外,本发明的一些实施方式(例如,发明b~e)中,若al原子/si原子比大于1.0,则所得的rho型沸石膜的耐水性、耐酸性降低,作为沸石膜的用途受到限制。若al原子/si原子比小于0.01,则难以获得rho型沸石膜。另外,水性反应混合物中也可含有硅原子源、铝原子源以外的其他原子源,例如镓(ga)、铁(fe)、硼(b)、钛(ti)、锆(zr)、锡(sn)、锌(zn)等原子源。作为碱源使用的碱的种类没有特别限制,可使用碱金属氢氧化物、碱土金属氢氧化物。这些金属氢氧化物的金属种通常为钠(na)、钾(k)、锂(li)、铷(rb)、铯(cs)、钙(ca)、镁(mg)、锶(sr)、钡(ba),优选为na、k、cs,更优选为na、cs。此外,金属氧化物的金属种可并用两种以上,具体地,优选并用na和cs。作为金属氢氧化物,具体地,例如可使用氢氧化钠、氢氧化钾、氢氧化锂、氢氧化铷、氢氧化铯等碱金属氢氧化物;氢氧化钙、氢氧化镁、氢氧化锶、氢氧化钡等碱土金属氢氧化物等。此外,作为用于水性反应混合物的碱源,可使用下述的有机模板的抗衡阴离子的氢氧根离子。另外,本发明所涉及的沸石的晶化中,有机模板(结构导向剂)并非必须,但通过使用与各结构对应的种类的有机模板,由于晶化而成的沸石的硅原子相对于铝原子的比例提高,结晶性提高,优选使用有机模板。作为有机模板,只要能形成期望的沸石膜,则不论种类,任何模板均可。此外,模板可使用一种,也可组合两种以上使用。适于反应的有机模板的种类根据合成的沸石结构而不同,有机模板若使用可获得期望的沸石结构的模板即可。具体地,例如,若为rho结构,则可使用18-冠-6-醚等。有机模板为阳离子时,可伴随不损害沸石形成的阴离子。作为代表像这样的阴离子的离子,可含有cl-、br-、i-等卤离子、氢氧根离子、乙酸盐、硫酸盐和羧酸盐。其中,特别适合使用氢氧根离子,氢氧根离子的情况可起到作为上述碱源的功能。水性反应混合物中的si原子源与有机模板的比,以有机模板相对于sio2的摩尔比(有机模板/sio2比)计,通常为0.005以上,优选为0.01以上,更优选为0.02以上,进一步优选为0.05以上,特别优选为0.08以上,最优选为0.1以上,通常为1以下,优选为0.5以下,更优选为0.4以下,进一步优选为0.35以下,特别优选为0.30以下,最优选为0.25以下。水性反应混合物的有机模板/sio2比在该范围内时,在可生成致密的沸石膜之余,可获得耐酸性优异、al原子不易脱附的沸石。此外,该条件中,特别的是可形成致密且耐酸性优异的rho型的铝硅酸盐的沸石。关于碱金属原子源,通过使用其合适量,后述的有机结构导向剂易于以合适的状态配位于铝,因而易于制成晶体结构。碱金属原子源(r)和晶种以外的水热合成用原料混合物所含的硅(si原子)的摩尔比(r/si原子)通常为0.1以上,优选为0.15以上,更优选为0.20以上,进一步优选为0.25以上,尤其优选为0.30以上,特别优选为0.35以上,通常为2.0以下,优选为1.5以下,更优选为1.0以下,进一步优选为0.8以下,特别优选为0.6以下,最优选为0.5以下。碱金属原子源相对于硅的摩尔比(r/si原子)大于上述上限值时,存在生成的沸石易于溶解,不能获得沸石或收率明显降低的情况。r/si原子小于上述下限值时,存在原料的al原子源、si原子源不能充分溶解,不能获得均匀的水热合成用原料混合物,变得难以生成rho型沸石的情况。(水的量)水热合成用原料混合物中的水的量相对于晶种以外的原料混合物所含的硅(si原子)的摩尔比通常为10以上,优选为20以上,更优选为30以上,进一步优选为40以上,特别优选为50以上,通常为200摩尔以下,优选为150以下,更优选为100以下,进一步优选80以下,特别优选为60以下。大于上述上限时,反应混合物过稀,会变得难以形成无缺陷的致密膜。小于10时,反应混合物浓,因而会易于形成自发核,阻碍rho型沸石从支撑体的生长,变得难以形成致密的膜。(晶种)本发明中,作为“沸石”制造原料(原料化合物)的成分之一,也可使用晶种。水热合成时,并非必须使反应系内存在晶种,但通过存在晶种,可促进多孔支撑体上的沸石的晶化。作为使反应系内存在晶种的方法没有特别限制,可使用如合成粉末沸石时的向水性反应混合物中加入晶种的方法,在支撑体上附着有晶种的方法等,本发明中,优选在支撑体上附着有晶种。通过在支撑体上预先附着有晶种,易于生成致密且分离性能高的沸石膜。作为使用的晶种,若为能促进晶化的沸石则与种类无关,但为高效地使其晶化,优选与形成的沸石膜相同的晶型。例如,形成rho型铝硅酸盐的沸石膜时,优选使用rho型沸石的晶种。理想的是晶种的粒径与支撑体的孔径接近,可根据需要粉碎使用。粒径通常为20nm以上,优选为50nm以上,更优选为100nm以上,进一步优选0.15μm以上,特别优选为0.5μm以上,最优选为0.7μm以上,通常为5μm以下,优选为3μm以下,更优选为2μm以下,特别优选为1.5μm以下。根据支撑体的孔径,存在晶种的粒径越小越理想的情况,可根据需要粉碎使用。晶种的粒径通常为5nm以上,优选为10nm以上,更优选为20nm以上,通常为5μm以下,优选为3μm以下,更优选为2μm以下。在支撑体上附着晶种的方法没有特别限制,例如,可使用将晶种分散于水等溶剂中,将支撑体浸入该分散液中,在表面附着晶种的浸涂法;通过将晶种分散在水等溶剂中,将一端密封支撑体浸渍于分散液中后,从支撑体的另一端抽吸,在支撑体表面牢固地附着晶种的抽吸法;将晶种与水等溶剂混合为浆料状的物质涂布于支撑体上的方法等。为了控制晶种的附着量,再现性良好地制造沸石膜,优选浸涂法和抽吸法;出于使晶种在支撑体上密着的角度,优选涂布浆料状的晶种的方法和抽吸法。此外,出于使晶种在支撑体上密着的目的和/或去除过剩晶种的目的,在浸涂法、抽吸法之后,也可适宜地用戴着乳胶手套的手指等对附着有晶种的支撑体进行擦拭推挤。使晶种分散的溶剂没有特别限制,但特别优选水、碱性水溶液。碱性水溶液的种类没有特别限制,但优选氢氧化钠水溶液、氢氧化钾水溶液。此外,这些碱种也可混合。碱性水溶液的碱浓度没有特别限制,通常为0.0001mol%以上,优选为0.0002mol%以上,更优选为0.001mol%以上,进一步优选0.002mol%以上。此外,通常为1mol%以下,优选为0.8mol%以下,更优选为0.5mol%以下,进一步优选为0.2mol%以下。使晶种的溶剂没有特别限制,但特别优选水。所分散的晶种的量没有特别限制,相对分散液的总重量,通常为0.05质量%以上,优选为0.1质量%以上,更优选为0.5质量%以上,进一步优选1质量%以上,特别优选为2质量%以上,最优选为3.0质量%以上。此外,通常为20质量%以下,优选为10质量%以下,更优选为5质量%以下,进一步优选为4质量%以下。所分散的晶种的量过少时,支撑体上附着的晶种的量少,因而水热合成时支撑体上部分存在未生成沸石的部位,可能变为有缺陷的膜。另一方面,在分散液中的晶种的量在某一程度以上时,通过例如浸涂法在多孔支撑体上附着的晶种的量近乎恒定,分散液中的晶种的量过多时,晶种的浪费增加,在成本方面不利。在支撑体上通过浸涂法、抽吸法或浆料的涂布附着晶种之后,理想的是在干燥后进行沸石膜的形成。干燥温度通常为50℃以上,优选为80℃以上,更优选为100℃以上,通常为200℃以下,优选为180℃以下,更优选为150℃以下。关于干燥时间,若可充分地干燥则没有问题,通常为10分钟以上,优选为30分钟以上,上限没有特别限定,但出于经济上的角度,通常为5小时以下。对于干燥后的附着有晶种的支撑体,出于使晶种在支撑体上密着的目的和/或去除过剩晶种的目的,也可适宜地用戴着乳胶手套的手指等对附着有晶种的支撑体进行擦拭推挤。在多孔支撑体上预先附着的晶种的量没有特别限制,以多孔支撑体的每1m2膜形成面的质量计通常为0.1g以上,优选为0.3g以上,更优选为0.5g以上,进一步优选为0.80g以上,最优选为1.0g以上,通常为100g以下,优选为50g以下,更优选为10g以下,进一步优选为8g以下,最优选为5g以下。晶种的附着量在小于上述下限时,趋于难以形成晶体,膜的生长变得不充分,膜的生长变得不均匀。此外,晶种的量在大于上述上限时,存在表面的凹凸因晶种而增长,或由于从支撑体掉落的晶种,自发核易于生长,阻碍支撑体上的膜生长的情况。任一情况下,均趋于难以生成致密的沸石膜。通过水热合成在多孔支撑体上形成沸石膜时,支撑体的固定化方法没有特别限制,可为竖放、横放等所有形态。此时,可采用静置法形成沸石膜,也可在水性反应混合物的搅拌下形成沸石膜。水热合成通过将如上述负载有晶种的支撑体和配制的水热合成用混合物或将其熟成而获得的水性凝胶加入耐压容器,在自身产生压力下或在不阻碍晶化程度的气体加压下,搅拌下或使容器旋转或振摇的同时,或在静置状态,保持规定温度而进行。出于不阻碍从支撑体上的晶种的晶体生长的角度,理想的是静置状态下的水热合成。通过水热合成形成沸石膜时的反应温度没有特别限制,只要是为了获得目标沸石结构的膜的适宜温度即可,通常为100℃以上,优选为110℃以上,更优选为120℃以上,尤其优选为130℃以上,特别优选为140℃以上,最优选为150℃以上,通常为200℃以下,优选为190℃以下,更优选为180℃以下,进一步优选为170℃以下。反应温度过低时,沸石会变得难以晶化。此外,反应温度过高时,易于生成与作为目标的沸石不同类型的沸石。通过水热合成形成沸石膜时的加热(反应)时间没有特别限制,只要是为了获得目标沸石结构的膜的适宜时间即可,通常为3小时以上,优选为8小时以上,更优选为12小时以上,尤其优选为15小时以上,通常为10天以下,优选为5天以下,更优选为3天以下,进一步优选2天以下,尤其优选为1.5天以下。反应时间过短时,沸石会变得难以晶化。反应时间过长时,易于生成与作为目标的沸石不同类型的沸石。水热合成时的压力没有特别限制,在将加入密封容器中的水性反应混合物加热至上述温度范围时所产生的自生压力就足够。进一步地根据需要,加入氮等不活性气体也无妨。通过多次重复水热合成,可提高沸石膜的致密性。多次重复水热合成时,在对第1次水热合成中获得的沸石膜复合物进行水洗、加热干燥后,再次浸渍于重新准备的水性反应混合物中进行水热合成即可。第1次水热合成后获得的沸石膜复合物并非必须进行水洗、干燥,但通过水洗、干燥,可保证水性反应混合物的组成为目标组成。进行多次合成时的合成次数通常为2次以上,通常为10次以下,优选为5次以下,更优选为3次以下。水洗可为一次,也可重复数次。通过水热合成而获得的沸石膜复合物在水洗后,进行加热处理,使其干燥。这里,加热处理是指加热而使沸石膜复合物干燥,此外,使用有机模板时,意味着烧制除去该有机模板。加热处理的温度在以干燥为目的时,通常为50℃以上,优选为80℃以上,更优选为100℃以上,通常为200℃以下,优选为150℃以下。加热处理的温度在以烧制除去有机模板为目的时,通常为250℃以上,优选为300℃以上,更优选为350℃以上,进一步优选为400℃以上,通常为800℃以下,优选为600℃以下,更优选为550℃以下,特别优选为500℃以下。在以烧制除去有机模板为目的时,若加热处理的温度过低,则有机模板的残留比例趋于增多,沸石的孔减少,因而用于氨分离时的透过量可能减少。若加热处理温度过高,则会由于支撑体与沸石的热膨胀率的差增大,沸石膜可能易于产生裂纹,沸石膜的致密性会丧失,分离性能降低。加热处理的时间,若是沸石膜充分干燥,或可烧制除去有机模板的时间,则没有特别限制,在以干燥为目的时,优选为0.5小时以上,更优选为1小时以上,在以烧制除去有机模板为目的时,根据升温速度、降温速度而有所变更,优选为1小时以上,更优选为5小时以上。加热时间的上限没有特别限制,通常为200小时以下,优选为150小时以下,更优选为100小时以下。在以烧制模板为目的时的加热处理在空气气氛下进行即可,也可在氮等不活性气体、添加有氧的气氛下进行。在有机模板的存在下进行水热合成时,将获得的沸石膜复合物进行水洗后,例如,适宜地通过加热处理、萃取等,优选通过上述加热处理,即烧制除去有机模板。以烧制除去有机模板为目的的加热处理时的升温速度,为防止多孔支撑体与沸石的热膨胀率的差引起沸石膜上产生裂纹,理想的是尽可能缓慢。升温速度通常为5℃/分以下,优选为2℃/分以下,更优选为1℃/分以下,进一步优选0.5℃/分以下,特别优选为0.3℃/分以下。升温速度的下限通常考虑操作性为0.1℃/分以上。此外,以烧制除去有机模板为目的的加热处理中,为避免沸石膜中产生裂纹,加热处理后的降温速度也有必要进行控制,降温速度与升温速度同样地,理想的是越缓慢越好。降温速度通常为5℃/分以下,优选为2℃/分以下,更优选为1℃/分以下,更优选为0.5℃/分以下,特别优选为0.3℃/分以下。降温速度的下限通常考虑操作性为0.1℃/分以上。<mfi型沸石膜的制造方法>(硅原子源)用于水性反应混合物的硅(si)原子源没有特别限制,可使用例如,铝硅酸盐沸石、气相法二氧化硅、胶体二氧化硅、无定形二氧化硅、硅酸钠、硅酸甲酯、硅酸乙酯、三甲基乙氧基硅烷等硅醇盐、原硅酸四乙酯、铝硅酸盐凝胶等。优选为气相法二氧化硅、胶体二氧化硅、无定形二氧化硅、硅酸钠、硅酸甲酯、硅酸乙酯、硅醇盐、铝硅酸盐凝胶。它们可单独使用一种,也可混合两种以上使用。以使相对于si原子源的其他原料的使用量分别为前述或后述的适当范围的方式使用si原子源。(铝原子源)多孔支撑体-mfi型沸石膜复合物的制造中所使用的铝(al)原子源没有特别限制,可举出铝硅酸盐沸石、非晶态氢氧化铝、三水铝石结构的氢氧化铝、三羟铝石结构的氢氧化铝、硝酸铝、硫酸铝、氧化铝、铝酸钠、勃姆石、假勃姆石、铝醇盐、铝硅酸盐凝胶等,优选为非晶态氢氧化铝、铝酸钠、勃姆石、假勃姆石、铝醇盐、铝硅酸盐凝胶,特别优选非晶态氢氧化铝、铝酸钠、铝硅酸盐凝胶。它们可单独使用一种,也可混合两种以上使用。晶种以外的原料混合物所含的al原子源(包括前述的铝硅酸盐沸石和其他al原子源)相对于硅(si原子)的使用量(al原子/si原子比)的优选范围以摩尔比计,通常为0.001以上,优选为0.002以上,更优选为0.003以上,进一步优选为0.004以上,通常为1.0以下,优选为0.5以下,更优选为0.2以下,进一步优选为0.1以下。通过控制在该使用量的范围,易于将沸石中的氮原子、碱金属元素的含量控制在本发明的优选范围。此外,为增大al原子/si原子比率,可减少硅原子源相对于铝原子源的用量,另一方面,为减小该比率,可增加硅原子源相对于铝原子源的使用量。另外,水性反应混合物中也可以含有si原子源、al原子源以外的其他原子源,例如ga、fe、b、ti、zr、sn、zn等原子源。作为碱源使用的碱的种类没有特别限制,可使用碱金属氢氧化物、碱土金属氢氧化物。作为金属氢氧化物,具体地,可使用例如氢氧化钠、氢氧化钾、氢氧化锂、氢氧化铷、氢氧化铯等碱金属氢氧化物;氢氧化钙、氢氧化镁、氢氧化锶、氢氧化钡等碱土金属氢氧化物等。此外,作为用于水性反应混合物的碱源,可使用下述的有机模板的抗衡阴离子的氢氧根离子。另外,本发明所涉及的沸石的晶化中,有机模板并非必须,但通过使用与各结构对应的种类的有机模板(结构导向剂),由于晶化而成的沸石的硅原子相对于铝原子的比例提高,结晶性提高,优选使用有机模板。作为有机模板,只要能形成期望的沸石膜,则不论种类,任何模板均可。此外,模板也可使用一种,也可组合两种以上使用。适于反应的有机模板的种类根据合成的沸石结构不同而不同,有机模板使用可获得期望的沸石结构的模板即可。具体地,例如,若为mfi结构,则可使用四丙基氢氧化铵等。有机模板为阳离子时,可伴有不损害沸石形成的阴离子。作为代表像这样的阴离子的离子,可含有cl-、br-、i-等卤离子、氢氧根离子、乙酸盐、硫酸盐和羧酸盐。其中,特别适合使用氢氧根离子,氢氧根离子的情况可起到作为上述碱源的功能。水性反应混合物中的si原子源与有机模板的比,以有机模板相对于sio2的摩尔比(有机模板/sio2比)计,通常为0.005以上,优选为0.01以上,更优选为0.02以上,尤其优选为0.05以上,特别优选为0.1以上,通常为1以下,优选为0.5以下,更优选为0.3以下,尤其优选为0.25以下,特别优选为0.2以下。水性反应混合物的有机模板/sio2比在该范围内时,在可生成致密的沸石膜之余,可获得耐酸性优异、al原子不易脱附的沸石。此外,该条件中,特别的是可形成致密且耐酸性优异的mfi型的铝硅酸盐的沸石。关于碱金属原子源,通过使用其合适量,后述的有机结构导向剂易于以合适的状态配位于铝,因而易于制成晶体结构。碱金属原子源(r)和晶种以外的水热合成用原料混合物所含的硅(si原子)的摩尔比(r/si原子)通常为0.01以上,优选为0.02以上,更优选为0.03以上,进一步优选为0.04以上,特别优选为0.05以上,通常为1.0以下,优选为0.6以下,更优选为0.4以下,进一步优选为0.2以下,特别优选为0.1以下。碱金属原子源相对于硅的摩尔比(r/si原子)大于上述上限值时,存在生成的沸石易于溶解,不能获得沸石或收率明显降低的情况。r/si原子小于上述下限值时,存在原料的al原子源、si原子源不能充分溶解,不能获得均匀的水热合成用原料混合物,变得难以生成mfi型沸石的情况。(水的量)水热合成用原料混合物中的水的量相对于晶种以外的原料混合物所含的硅(si原子)的摩尔比通常为10以上,优选为15以上,更优选为20以上,进一步优选为25以上,特别优选为30以上,通常为500摩尔以下,优选为300以下,更优选为200以下,进一步优选150以下,特别优选为100以下。大于上述上限时,反应混合物过稀,会变得难以形成无缺陷的致密膜。小于10时,反应混合物浓,因而会易于形成自发核,阻碍mfi型沸石从支撑体的生长,变得难以形成致密的膜。(晶种)本发明中,作为“沸石”制造原料(原料化合物)的成分之一,也可使用晶种。水热合成时,并非必须使反应系内存在晶种,但通过存在晶种,可促进多孔支撑体上的沸石的晶化。作为使反应系内存在晶种的方法没有特别限制,可使用如合成粉末沸石时的向水性反应混合物中加入晶种的方法,在支撑体上附着有晶种的方法等,本发明中,优选在支撑体上附着有晶种。通过在支撑体上预先附着有晶种,易于生成致密且分离性能高的沸石膜。作为使用的晶种,若为能促进晶化的沸石则与种类无关,但为高效地使其晶化,优选与形成的沸石膜相同的晶型。例如,形成mfi型铝硅酸盐的沸石膜时,优选使用mfi型沸石的晶种。理想的是晶种的粒径与支撑体的孔径接近,可根据需要粉碎使用。粒径通常为1nm以上,优选为10nm以上,更优选为50nm以上,进一步优选为0.1μm以上,特别优选为0.5μm以上,尤其优选为0.7μm以上,最优选为1μm以上,通常为5μm以下,优选为3μm以下,更优选为2μm以下,最优选为1.5μm以下,特别优选为1.2μm以下。根据支撑体的孔径,存在晶种的粒径越小越理想的情况,可根据需要粉碎使用。晶种的粒径通常为0.5nm以上,优选为1nm以上,更优选为2nm以上,通常为5μm以下,优选为3μm以下,更优选为2μm以下。在支撑体上附着晶种的方法没有特别限制,例如,可使用将晶种分散于水等溶剂,将支撑体浸入该分散液中,在表面附着晶种的浸涂法;将晶种分散在水等溶剂,将一端密封支撑体浸渍于该分散液中后,通过从另一端抽吸支撑体,在支撑体表面牢固地附着晶种的抽吸法;将晶种与水等溶剂混合为浆料状的物质涂布于支撑体上的方法等。为了控制晶种的附着量,再现性良好地制造沸石膜,优选浸涂法和抽吸法;出于使晶种在支撑体上密着的角度,优选涂布浆料状的晶种的方法和抽吸法。此外,出于使晶种在支撑体上密着的目的和/或去除过剩晶种的目的,在浸涂法、抽吸法之后,也可适宜地用戴着乳胶手套的手指等对附着有晶种的支撑体进行擦拭推挤。使晶种分散的溶剂没有特别限制,但特别优选水、碱性水溶液。碱性水溶液的种类没有特别限制,但优选氢氧化钠水溶液、氢氧化钾水溶液。此外,这些碱种也可混合。碱性水溶液的碱浓度没有特别限制,通常为0.0001mol%以上,优选为0.0002mol%以上,更优选为0.001mol%以上,进一步优选为0.002mol%以上。此外,通常为1mol%以下,优选为0.8mol%以下,更优选为0.5mol%以下,进一步优选0.2mol%以下。使晶种分散的溶剂没有特别限制,但特别优选水。所分散的晶种的量没有特别限制,相对分散液的总重量,通常为0.05质量%以上,优选为0.1质量%以上,更优选为0.5质量%以上,进一步优选为1质量%以上,特别优选为2质量%以上,最优选为3质量%以上。此外,通常为20质量%以下,优选为10质量%以下,更优选为5质量%以下,进一步优选为4质量%以下。所分散的晶种的量过少时,支撑体上附着的晶种的量少,因而水热合成时支撑体上存在一部分未生成沸石的部位,可能变为有缺陷的膜。另一方面,在分散液中的晶种的量在某一程度以上时,通过例如浸涂法在多孔支撑体上附着的晶种的量近乎恒定,分散液中的晶种的量过多时,晶种的浪费增加,在成本方面不利。在支撑体上通过浸涂法、抽吸法或浆料的涂布附着晶种之后,理想的是在干燥后进行沸石膜的形成。干燥温度通常为50℃以上,优选为80℃以上,更优选为100℃以上,通常为200℃以下,优选为180℃以下,更优选为150℃以下。对于干燥时间,若可充分地干燥则没有问题,通常为10分钟以上,优选为30分钟以上,上限没有特别限定,但出于经济上的角度,通常为5小时以下。对于干燥后的附着有晶种的支撑体,出于使晶种在支撑体上密着的目的和/或去除过剩晶种的目的,也可适宜地用戴着乳胶手套的手指等对附着有晶种的支撑体进行擦拭推挤。在多孔支撑体上预先附着的晶种的量没有特别限制,以多孔支撑体的每1m2膜形成面的质量计通常为0.1g以上,优选为0.3g以上,更优选为0.5g以上,进一步优选为0.80g以上,最优选为1.0g以上,通常为100g以下,优选为50g以下,更优选为10g以下,进一步优选为8g以下,最优选为5g以下。晶种的附着量在小于上述下限时,趋于难以形成晶体,膜的生长变得不充分,膜的生长变得不均匀。此外,晶种的量在大于上述上限时,存在表面的凹凸因晶种而增长,由于从支撑体掉落的晶种,自发核易于生长,阻碍支撑体上的膜生长的情况。任一情况下,均趋于难以生成致密的沸石膜。通过水热合成在多孔支撑体上形成沸石膜时,支撑体的固定化方法没有特别限制,可为竖放、横放等所有形态。此时,可采用静置法形成沸石膜,也可在水性反应混合物的搅拌下形成沸石膜。水热合成通过将如上述负载有晶种的支撑体和配制成的水热合成用混合物或将其熟成而获得的水性凝胶加入耐压容器,在自身产生压力下或在不阻碍晶化程度的气体加压下,在搅拌下或使容器旋转或振摇的同时,或在静置状态,保持规定温度而进行。出于不阻碍从支撑体上的晶种的晶体生长的角度,理想的是静置状态下的水热合成。通过水热合成形成沸石膜时的反应温度没有特别限制,只要是为了获得目标沸石结构的膜的合适温度即可,通常为100℃以上,优选为120℃以上,更优选为130℃以上,尤其优选为140℃以上,特别优选为150℃以上,最优选为160℃以上,通常为200℃以下,优选为190℃以下,更优选180℃以下,特别优选为170℃以下。反应温度过低时,沸石会变得难以晶化。此外,反应温度过高时,易于生成与作为目标的沸石不同类型的沸石。通过水热合成形成沸石膜时的加热(反应)时间没有特别限制,只要是为了获得目标沸石结构的膜的合适时间即可,通常为1小时以上,优选为5小时以上,更优选为10小时以上,通常为10天以下,优选为5天以下,更优选为3天以下,进一步优选为2天以下,尤其优选为1天以下。反应时间过短时,沸石会变得难以晶化。反应时间过长时,易于生成与作为目标的沸石不同类型的沸石。水热合成时的压力没有特别限制,在将加入密封容器中的水性反应混合物加热至上述温度范围时所产生的自生压力就足够。进一步地根据需要,加入氮等不活性气体也无妨。通过多次重复水热合成,可提高沸石膜的致密性。多次重复水热合成时,在对第1次水热合成中获得的沸石膜复合物进行水洗、加热干燥后,再次浸渍于重新准备的水性反应混合物中进行水热合成即可。第1次水热合成后获得的沸石膜复合物并非必须进行水洗、干燥,但通过水洗、干燥,可保证水性反应混合物的组成为目标组成。进行多次合成时的合成次数通常为2次以上,通常为10次以下,优选为5次以下,更优选为3次以下。水洗可进行一次,也可重复数次。通过水热合成而获得的沸石膜复合物在水洗后,进行加热处理,使其干燥。这里,加热处理是指加热而使沸石膜复合物干燥,此外,使用有机模板时,意味着烧制除去该有机模板。加热处理的温度在以干燥为目的时,通常为50℃以上,优选为80℃以上,更优选为100℃以上,通常为200℃以下,优选为150℃以下。加热处理的温度在以烧制除去有机模板为目的时,通常为350℃以上,优选为400℃以上,更优选为450℃以上,进一步优选为500℃以上,通常为900℃以下,优选为800℃以下,更优选为700℃以下,特别优选为600℃以下。在以烧制除去有机模板为目的时,若加热处理的温度过低,则有机模板的残留比例趋于增多,沸石的孔减少,因而用于氨分离时的透过量可能减少。若加热处理温度过高,则支撑体与沸石的热膨胀率的差增大,因而沸石膜可能易于产生裂纹,沸石膜的致密性会丧失,分离性能降低。作为有机模板,使用四丙基氢氧化铵时,可通过调整该加热处理温度,控制沸石中的氮原子的含量。加热处理的时间,若为使沸石膜充分干燥,或可烧制除去有机模板的时间,则没有特别限制,在以干燥为目的时,优选为0.5小时以上,更优选为1小时以上,在以烧制除去有机模板为目的时,根据升温速度、降温速度而有所变更,优选为1小时以上,更优选为5小时以上。加热时间的上限没有特别限制,通常为200小时以下,优选为150小时以下,更优选为100小时以下。以烧制模板为目的时的加热处理在空气气氛下进行即可,也可在氮等不活性气体、添加有氧的气氛下进行。在有机模板的存在下进行水热合成时,将获得的沸石膜复合物进行水洗后,例如,适宜地通过加热处理、萃取等,优选通过上述加热处理,即烧制除去有机模板。以烧制除去有机模板为目的的加热处理时的升温速度,为防止多孔支撑体与沸石的热膨胀率的差引起沸石膜中产生裂纹,理想的是尽可能缓慢。升温速度通常为5℃/分以下,优选为2℃/分以下,更优选为1℃/分以下,特别优选为0.5℃/分以下,最优选为0.3℃/分以下。升温速度的下限通常考虑操作性为0.1℃/分以上。此外,以烧制除去有机模板为目的的加热处理中,为避免沸石膜上产生裂纹,加热处理后的降温速度也有必要进行控制,降温速度与升温速度同样地,理想的是越缓慢越好。降温速度通常为5℃/分以下,优选为2℃/分以下,更优选为1℃/分以下,特别优选为0.5℃/分以下,最优选为0.3℃/分以下。降温速度的下限通常考虑操作性为0.1℃/分以上。(离子交换)所合成的沸石膜可根据需要进行离子交换。特别地,本发明的某一实施方式(例如,发明b、c、d、e的沸石膜)中,所合成沸石膜进行离子交换处理。本发明的特征之一沸石的热膨胀特性、氨分离热稳定性受到沸石中的阳离子种的很大影响,因而本离子交换为重要的控制方法。此外,如下文所述地,存在通过使用的阳离子种,提高沸石膜的氨透过性能和/或分离性能的情况。即,本发明中使用的阳离子种可在确保上述沸石的热膨胀特性、氨分离热稳定性的同时,考虑氨的透过性能和分离性能而适宜选择。(离子交换)离子交换在使用有机模板合成沸石膜时,通常在除去有机模板后进行。作为离子交换的离子,本发明中,为增加沸石膜表面的氮含量,优选为nh4+、甲胺、二甲胺、三甲胺、乙胺、二乙胺、三乙胺、乙二胺、二甲基乙二胺、四甲基乙二胺、二亚乙基三胺、三亚乙基四胺、苯胺、甲基苯胺、苄胺、甲基苄胺、六亚甲基二胺、n,n-二异丙基乙胺、n,n,n-三甲基-1-金刚烷胺、吡啶以及哌啶等碳原子数1~20的有机胺质子化而成的阳离子种中的任一项,此外,也可与质子;na+、k+、li+、rb+、cs+等碱金属离子;ca2+、mg2+、sr2+、ba2+等碱土金属离子;以及fe、cu、zn、ga、la等过渡金属离子等共存。其中,优选质子、nh4+、na+、li+、cs+、fe离子、ga离子、la离子。这些离子在沸石中可混合存在多种,在平衡上述沸石的热膨胀特性和氨透过性能的情况下,优选采用使上述离子混合存在的手法。通过像这样地控制离子交换的阳离子种以及它们的量,可控制沸石的氨亲和性以及沸石孔内的有效孔径,提高氨的透过选择性,同时提高氨的透过速度。其中,作为提高氨的透过选择性的离子种,优选为nh4+、甲胺、二甲胺、三甲胺、乙胺、二乙胺、三乙胺、乙二胺、二甲基乙二胺、四甲基乙二胺、二亚乙基三胺、三亚乙基四胺、苯胺、甲基苯胺、苄胺、甲基苄胺、六亚甲基二胺、n,n-二异丙基乙胺、n,n,n-三甲基-1-金刚烷胺、吡啶以及哌啶等碳原子数1~20的有机胺质子化而成的阳离子种,其中,nh4+、如碳原子数1~6的有机胺的分子尺寸小的胺质子化而成的阳离子种,出于上述理由更为优选,其中,特别优选nh4+。另一方面,作为提高氨的透过速度的离子种,优选共存有质子、na+、li+、cs+、fe离子、ga离子、la离子,特别优选na+、li+、cs+离子,最优选na+离子。本发明中,通过像这样地调整以含有氮原子的离子种为必须的离子的交换量,可控制沸石膜中的氮原子相对于al原子的摩尔比。另外,本发明的沸石中含有na+离子时,其含量相对于沸石中的al原子,以摩尔比计通常为0.01以上,优选为0.02以上,更优选为0.03以上,进一步优选为0.04以上,特别优选为0.05以上,其上限没有特别限制,通常为0.10摩尔当量以下,优选为0.070摩尔当量以下,更优选为0.065摩尔当量以下,进一步优选为0.060摩尔当量以下,特别优选为055摩尔当量以下。通过使用像这样的规定范围的na+/al原子比的沸石,可从由包含氨且包含氢和/或氮的多种成分构成的混合气体中,以高透过度分离氨。离子交换通过如下的方法等进行即可,将烧制后(使用有机模板的情况等)的沸石膜,用进行离子交换的上述阳离子的硝酸盐、硫酸盐、磷酸盐、有机酸盐、氢氧化物以及cl、br的卤盐、根据情况的盐酸等酸,在通常室温至100℃的温度下处理后,水洗或用40℃至100℃的热水水洗。离子交换处理中使用的溶剂,若可溶解上述离子交换的盐,则可为水,也可为有机溶剂,进行处理的盐的浓度通常为10mol/l以下,下限为0.1mol/l以上,优选为0.5mol/l以上,更优选为1mol/l以上。这些处理条件若根据使用的盐、溶剂种类进行适宜设定即可。使用盐酸等酸时,由于酸会破坏沸石的晶体结构,通常进行处理的酸的浓度为5mol/l以下,根据温度、时间适宜设定即可。此外,离子交换处理通过进行重复处理,离子交换率提高,因而离子交换处理的次数没有特别限制,可重复处理,直到获得作为目标的效果为止。进一步地,离子交换的沸石膜若在离子交换处理后,来源于离子交换处理原料的残存物存在于沸石孔内,则妨碍气体透过性,因而可根据通过需要在200~500℃下进行烧制,除去离子交换处理后的残存物。(硝酸盐处理)本发明的某一实施方式(例如,发明b、c、d、e的沸石膜)中,作为调整沸石膜中的氮原子的含量的方法,优选并用硝酸盐处理,因而下文中对硝酸盐处理进行说明。本发明中,所合成的沸石膜可根据需要实施硝酸盐处理。硝酸盐处理可在包含有机模板的状态下,也可在通过烧制除去有机模板后进行实施。硝酸盐处理是将沸石膜复合物浸渍于例如含有硝酸盐的溶液中进行。由此,有时会由于获得膜表面上存在的微细缺陷被硝酸盐阻塞的效果而优选。进一步地,硝酸盐存在于沸石孔中时,具有提高沸石膜与氨的亲和性的效果,作为提高氨透过性的手法而适当采用。硝酸盐处理中使用的溶剂,若可溶解盐则可为水,也可为有机溶剂;使用的硝酸盐没有特别限制,可举出例如硝酸镁、硝酸钙、硝酸钡、硝酸铝、硝酸镓、硝酸铟、硝酸铁、硝酸钴、硝酸镍、硝酸铜、硝酸锌等。它们可单独使用一种,也可混合使用两种以上。其中优选硝酸镁、硝酸钙、硝酸钡、硝酸铝、硝酸镓、硝酸铟,其中更优选硝酸镁、硝酸钙、硝酸钡、硝酸铝,特别是出于阻塞沸石膜表面上存在的微细缺陷的效果显著,提高氨分离性能的理由,优选硝酸铝。硝酸盐的浓度通常为10mol/l以下,下限为0.1mol/l以上,优选为0.5mol/l以上,更优选为1mol/l以上。处理温度通常为室温至150℃以下,处理进行10分钟至48小时的程度即可,这些处理条件根据使用的硝酸盐、溶剂种类适宜设定即可。硝酸盐处理后的沸石膜也可进行水洗,通过重复进行水洗,可将沸石膜的氮原子含量调整至优选范围。(铝盐处理)本发明中,所合成的沸石膜可根据需要实施铝盐处理。铝盐处理可在包含有机模板的状态下,也可在通过烧制除去有机模板后进行实施。铝盐处理是将沸石膜复合物浸渍于例如含有铝盐的溶液中进行。由此,会有获得膜表面上存在的微细缺陷被铝盐阻塞的效果,因而优选的情况。进一步地,铝盐存在于沸石孔时,存在吸引氨的效果,作为提高氨透过性的手法而适当采用。铝盐处理中使用的溶剂,若可溶解盐则可为水,也可为有机溶剂;使用的铝盐没有特别限制,可举出例如,硝酸铝、硫酸铝、氯化铝、磷酸铝、乙酸铝、碳酸铝、氢氧化铝等。它们可单独使用一种,也可混合使用两种以上。铝盐的浓度通常为10mol/l以下,下限为0.1mol/l以上,优选为0.5mol/l以上,更优选为1mol/l以上。处理温度通常为室温至150℃以下,处理进行10分钟至48小时的程度即可,这些处理条件根据使用的铝盐、溶剂种类适宜设定即可。铝盐处理后的沸石膜也可进行水洗,通过重复进行水洗,可调整沸石膜的al原子含量。为增大本发明的si原子/al原子比率,优选降低进行处理的铝盐的浓度、处理量,或增加铝盐处理后的水洗次数,另一方面,为降低该比率,优选增加进行处理的铝盐的浓度、处理量,或减少铝盐处理后的水洗次数。(甲硅烷化处理)本发明中,所合成的沸石膜,可根据需要实施甲硅烷化处理。甲硅烷化处理是将沸石膜复合物浸渍于含有例如si化合物的溶液中进行。由此,沸石膜表面被si化合物修饰,可成为具有规定的物理化学的性质的沸石膜。例如,通过在沸石膜表面上切实形成含有较多si-oh的层,膜表面的极性提高,可提高极性分子的分离性能。此外,通过以si化合物修饰沸石膜表面,有时可获得阻塞膜表面上存在的微细缺陷的效果。进一步地,通过甲硅烷化处理,可控制沸石的孔径,也可适当采用通过进行该处理提高氨透过选择性的手法。甲硅烷化处理中使用的溶剂可为水,也可为有机溶剂。此外,溶液可为酸性、碱性,此时通过酸、碱催化甲硅烷化反应。使用的甲硅烷化剂没有特别限制,优选烷氧基硅烷。处理温度通常为室温至150℃以下,处理进行10分钟至30小时的程度即可,这些处理条件根据使用的甲硅烷化剂、溶剂种类适宜设定即可。本发明中,本发明的沸石膜表面所含的氮原子的含量,如上所述地,可通过以下方法以及这些方法的适宜组合进行控制:选择沸石膜所含的沸石中的含有氮原子的阳离子种,而调整沸石的al原子/si原子比的方法;调整离子交换法中的离子交换量,而调整氮原子的含量的方法;根据需要在制造沸石膜时,使用含有氮原子的有机模板(结构导向剂),调整其添加量、烧制除去有机模板时的加热温度、加热时间的方法;以硝酸盐处理沸石膜的方法;调整将硝酸处理后的沸石膜进行水洗时的水洗次数的方法。本发明中,此外,本发明的沸石膜表面所含的al原子的含量,如上所述地,可通过以下方法以及这些方法的适宜组合进行控制:调整沸石膜所含的沸石中的al原子/si原子比的方法;以铝盐处理沸石膜的方法;调整对铝盐处理后的沸石膜进行水洗时的水洗次数的方法。本发明中,此外,本发明的沸石膜表面所含的碱金属元素的含量,如上所述地,可通过以下方法以及这些方法的适宜组合进行控制:调整沸石膜所含的沸石中的al原子/si原子比的方法;调整离子交换法中的离子交换量而调整碱金属原子的含量的方法;调整对沸石膜进行水洗时的水洗次数的方法。像这样地制造的沸石膜复合物具有优异的特性,可作为本发明中的从混合气体中的氨的膜分离手段而适当使用。实施例下文中,基于实施例对本发明进行更为具体的说明,然而本发明在不超出其主旨的情况下,不受以下实施例的限制。另外,以下实施例中的各种制造条件、评价结果的值具有作为本发明的实施方式中的上限或下限的优选值的意义,优选范围也可为所述上限或下限值与下述实施例的值的组合,或实施例的值彼此间的组合所规定的范围。另外,下文中,“cha型硅酸盐沸石”可简称为“cha型沸石”,“rho型硅酸盐沸石”可简称为“rho型沸石”,“mfi型硅酸盐沸石”可简称为“mfi型沸石”。[实施例a][分离性能的测定]下文中,沸石膜复合物的分离性能的测定如下进行。(1)氨分离试验在图1所示意性表示的装置中,进行如下的氨分离试验。图1的装置中,作为供给气体,以100sccm的流量,向耐压容器和沸石膜复合物之间,供给包含氨气(nh3)、氮气(n2)、氢(h2)的混合气体,通过背压阀将供给侧气体与透过膜内的气体的压力差调整至恒定0.3mpa,用微型气相色谱分析从配管10排出的排出气体,算出透过气体的浓度和流量。另外,氨分离试验中,为了从耐压容器中除去水分、空气等成分,在测定温度以上干燥和排气,因而在以使用的试样气体进行吹扫处理后,使试样气体温度以及沸石膜复合物的供给气体侧与透过气体侧的压差恒定、透过气体流量稳定后,再测定透过沸石膜复合物的试样气体(透过气体)的流量,算出气体的渗透通量[mol/(m2·s·pa)]。计算渗透通量时的压力,使用供给气体的供给侧与透过侧的压力差(压差)。混合气体的情况下使用分压差。此外,基于该测定结果,通过下述式(1)算出理想分离系数α’。α’=(q1/q2)/(p1/p2)(1)〔式(1)中,q1和q2分别表示透过性高的气体和透过性低的气体的透过量[mol·(m2·s)-1],p1和p2分别表示透过性高的气体和透过性低的气体的、供给侧与透过侧的压力差[pa]。〕该值表示各气体的渗透通量的比率,因此,可算出各气体的渗透通量,由其比率求出。[制造例a1:cha型沸石膜复合物1的制造]通过以下的方法,制造cha型沸石膜复合物1。(水热合成用原料混合物)首先,如下配制水热合成用原料混合物。将1mol/l-naoh水溶液1.45g、1mol/l-koh水溶液5.78g、水114.6g混合,向其加入氢氧化铝(含al2o3-53.5质量%,aldrich公司制)0.19g,搅拌使其溶解成为透明溶液。向其中加入作为有机模板的tmadaoh25质量%水溶液2.43g,进一步加入胶体二氧化硅(日产化学公司制snowtex-40)10.85g,搅拌2小时,将其作为水热合成用原料混合物。该混合物的组成(摩尔比)为sio2/al2o3/naoh/koh/h2o/tmadaoh=1/0.018/0.02/0.08/100/0.04、sio2/al2o3=58。(支撑体)作为多孔支撑体,将株式会社则武制的氧化铝管bn1(外径6mm,内径4mm)切断为80mm的长度后,以超声波清洗机清洗,然后干燥使用。(晶种分散液)作为晶种,以sio2/al2o3/naoh/koh/h2o/tmadaoh=1/0.033/0.1/0.06/20/0.07的凝胶组成(摩尔比)在160℃进行2天水热合成,使其晶化,过滤、水洗、干燥,制造作为晶种的cha型沸石。另外,晶种的粒径为0.3~3μm左右。接着,将该晶种分散在水中,使其为约1质量%,制造晶种分散液(cha型晶种分散液)。(膜复合物的制造)准备上述多孔支撑体,将上述支撑体浸于上述晶种分散液1分钟后,以100℃干燥1小时,在支撑体上附着晶种。附着的晶种质量为约0.001g。将附着有晶种的支撑体沿垂直方向浸渍于加入上述水热合成用原料混合物的teflon(注册商标)制内筒(200ml)中,密封高压釜,在180℃下,以静置状态在自生压力下加热72小时。经过规定时间后,放置冷却后将支撑体-沸石膜复合物从水热合成用原料混合物中取出,清洗后以100℃干燥3小时。接着,将干燥后的膜复合物在空气中用电炉进行450℃下10小时、500℃下5小时的烧制,获得除去沸石中所含的模板的cha型沸石膜复合物1。此时从室温至450度的升温速度和降温速度均为0.5℃/分,从450度至500度的升温速度和降温速度均为0.1℃/分。基于烧制后的膜复合物的质量和支撑体的质量的差求得的、在支撑体上晶化的cha型沸石的质量为约0.279~0.289g。此外,烧制后的膜复合物的空气透过量为2.4~2.9cm3/分。[实施例a1]<膜分离性能的评价>作为前处理,在200℃下,作为供给气体,在耐压容器和制造例a1所述的cha型沸石膜复合物1之间导入50体积%h2/50体积%n2的混合气体,保持压力为约0.4mpa,使cha型沸石膜复合物1的圆筒的内侧为0.098mpa(大气压),进行约120分钟的干燥。使用cha型沸石膜复合物1,在使cha型沸石膜复合物1的温度为100℃、150℃、200℃和250℃的条件下,通过上述方法,进行氨分离试验。另外,作为混合气体,使用12.0体积%nh3/51.0体积%n2/37.0体积%h2的混合气体。获得的透过气体的氨的浓度以及氨/氢(nh3/h2)、氨/氮(nh3/n2)的渗透通量比如表3所示。表3中,透过气体的氨的浓度为将小数点后第1位四舍五入后的值。【表3】表3100℃150℃200℃250℃透过气体的nh3浓度26%25%22%20%nh3/n2的渗透通量比111087nh3/h2的渗透通量比3321[实施例a2]除使用制造例a1所述的cha型沸石膜复合物1,使温度为100℃,混合气体为3.0体积%nh3/24.0体积%n2/73.0体积%h2的混合气体以外,通过与实施例a1相同的手法,进行氨分离评价的结果是,透过气体中的氨气浓度为4.1体积%。从获得的结果可知,可从混合气体中分离氨。[实施例a3]除使用制造例a1所述的cha型沸石膜复合物1,使温度为100℃,混合气体为2.0体积%nh3/19.0体积%n2/79.0体积%h2的混合气体以外,通过与实施例a1相同的手法,进行氨分离评价的结果是,透过气体中的氨气浓度为2.3体积%。从获得的结果可知,可从混合气体中分离氨。[比较例a1]除使制造例a1所述的cha型沸石膜复合物1的温度为100℃,使用0.7体积%nh3/80.0体积%n2/19.3体积%h2的混合气体以外,用与实施例a1相同的手法,进行氨分离的评价。其结果是透过气体的氨气浓度为0.8体积%。[比较例a2]除使制造例a1所述的cha型沸石膜复合物1的温度为100℃,使用0.8体积%nh3/20.1体积%n2/79.1体积%h2的混合气体以外,用与实施例a1相同的手法,进行氨分离的评价。其结果是透过气体的氨气浓度为0.8体积%。从实施例a1、a2、a3和比较例a1、a2可知,即使使用相同的沸石膜复合物,混合气体中的氨气浓度低时,混合气体中的氨分离较困难,与之相对地,通过使混合气体中的氨气浓度为1.0体积%以上,可高效地分离氨。[参考例a1]除使用实施例a1中制作的cha型沸石膜复合物1,使cha型沸石膜复合物1的温度为100℃,将12体积%nh3/50体积%n2/38体积%h2的混合气体以100sccm的流量流通以外,以与实施例a2相同的手法进行氨分离的评价,结果是氢的渗透通量为7.0×10-8[mol/(m2·s·pa)]、氮的渗透通量为2.1×10-8[mol/(m2·s·pa)]、氨的渗透通量为2.4×10-7[mol/(m2·s·pa)]。与之相对地,仅单独流通氢气时的氢的渗透通量为1.6×10-6[mol/(m2·s·pa)],仅单独流通氮气时的氮的渗透通量为3.0×10-7[mol/(m2·s·pa)],基于这些结果可知,供给气体中含有氨气时,氢以及氮的两者的渗透通量均明显降低。可认为基于本结果,通过使混合气体中的氨气浓度为规定量以上,供给气体中的氨吸附于沸石,可表现出阻碍氢、氮的透过的效果。[制造例a2:cha型沸石膜复合物2的制造]将制造例a1中获得的除去模板后的cha型沸石膜复合物1,投入加入有1m的硝酸铵水溶液45g的teflon(注册商标)制内筒(65ml)。密封高压釜,在100℃下以静置状态在自生压力下加热1小时。经过规定时间后,放置冷却后,将该cha型沸石膜从水溶液中取出,以100℃的离子交换水重复进行三次1小时的热水洗后,在100℃下干燥4小时以上,获得作为cha型沸石膜复合物2的nh4+型的cha型沸石膜复合物。[实施例a4]<膜分离性能的评价>除使用制造例a2所述的cha型沸石膜复合物2代替制造例a1所述的cha型沸石膜1以外,通过与实施例a1相同的方法,进行氨的分离评价。获得的透过气体的氨的浓度以及氨/氢、氨/氮的渗透通量比如表4所示。表4中,透过气体的氨的浓度为将小数点后第1位四舍五入后的值。从表4的结果可知,通过使混合气体中的氨气浓度为规定量以上,可高效地分离氨。此外可知,即使在高温条件下,也可高效地分离氨。【表4】表4100℃150℃200℃250℃透过气体的nh3浓度31%27%24%22%nh3/n2的渗透通量比2616119nh3/h2的渗透通量比6422[制造例a3:rho型沸石膜复合物1的制造](水热合成用原料混合物)通过将6.8g的18-冠-6-醚(东京化成公司制)、2.1g的naoh(岸田化学公司制)和4.2g的csoh·h2o(三津和化学公司制)溶解于125.9g的水,在80℃下搅拌3小时,获得冠醚-碱水溶液。然后,向8.9g的y型(fau)沸石(sar=30、zeolyst公司制cbv720)滴加上述冠醚-碱水溶液,配制水热合成用原料混合物。获得的水热合成用原料混合物的凝胶组成(摩尔比)为sio2/al2o3/naoh/csoh/h2o/18-冠-6-醚=1/0.033/0.36/0.18/50/0.18。(支撑体)作为多孔支撑体,将氧化铝管(外径6mm、孔径0.15μm、株式会社则武制)切断为40mm的长度后,用水清洗然后干燥使用。(晶种分散液)通过将23g的18-冠-6-醚(东京化成公司制)和6g的naoh(岸田化学公司制)和5g的csoh·h2o(三津和化学公司制)溶解于84g的水中,在80℃下将获得的溶液搅拌3小时,获得冠醚-碱水溶液。接着,向30g的fau型沸石(sar=30、zeolyst公司制cbv720)滴加上述冠醚-碱水溶液,进一步作为晶种添加根据wo2015020014号单行本合成的rho型沸石0.6g,室温下搅拌2小时,配制混合物。该混合物的组成(摩尔比)为sio2/al2o3/naoh/csoh/h2o/18-冠-6-醚=1/0.033/0.30/0.06/10/0.18。将该混合物在室温下熟成24小时后,加入耐压容器,在150℃的烘箱中静置,进行72小时水热合成。该水热合成反应后,冷却反应液,通过过滤回收生成的晶体。将回收的晶体在100℃下干燥12小时,获得rho型沸石晶体。将获得的rho型沸石用球磨机粉碎,制造晶种分散液。具体地,向500ml的塑料瓶中,加入上述rho型沸石10g和的hd氧化铝珠(nikkato公司制)300g、水90g,以球磨机粉碎6小时,制成10质量%的rho型沸石分散液。向该沸石分散液中添加水以使rho型沸石为3质量%,获得晶种分散液。(膜复合物的制造)向支撑体滴加上述晶种分散液,通过摩擦法使晶种附着在支撑体上。接着,沿垂直方向,将附着有晶种的支撑体浸渍于加入有水热合成用原料混合物的teflon(注册商标)制内筒中,密封高压釜,在150℃下自生压力下加热72小时。经过规定时间后,放置冷却后,将支撑体-沸石膜复合物从高压釜中取出,清洗后在100℃下干燥5小时以上。干燥后,在原始合成(as-made)的状态下的空气透过量为1.5/(m2·分)。接着,为除去模板,在300度下烧制获得的膜复合物,获得rho型沸石膜复合物。基于烧制后的沸石膜复合物的重量与支撑体的重量的差,支撑体上晶化的rho型沸石的重量为78g/m2。接着,将除去模板后的rho型沸石膜复合物投入装有3m的硝酸铵水溶液45g的teflon(注册商标)制内筒(65ml)中,密封高压釜,在110℃下以静置状态在自生压力下加热1小时。经过规定时间后,放置冷却后,将rho型沸石膜从水溶液中取出,通过用水清洗后,在100℃下干燥4小时以上,获得nh4+型的rho型沸石膜复合物。为将获得的nh4+型的rho型沸石膜复合物制成h+型,将该rho型沸石膜复合物用电炉在400℃下烧制2小时。此时至150℃为止的升温速度和降温速度均为2.5℃/分,从150℃至400℃的升温速度和降温速度为0.5℃/分,获得作为rho型沸石膜复合物1的h+型的rho型沸石膜复合物。[实施例a5]<膜分离性能的评价>使用制造例a3所述的rho型沸石膜复合物1,如上所述地,使用图1的装置进行从氨/氢/氮的混合气体中的氨分离试验。作为前处理,在250℃下,在耐压容器和rho型沸石膜复合物1之间,导入50体积%h2/50体积%n2的混合气体作为供给气体,保持压力为约0.3mpa,使rho型沸石膜复合物1的圆筒的内侧为0.098mpa(大气压),干燥约120分钟。然后,以100sccm使12体积%nh3/51体积%n2/37体积%h2的混合气体流通,设定背压为0.4mpa。此时,rho型沸石膜复合物1的供给气体侧与透过气体侧的压差为0.3mpa。将rho型沸石膜复合物1的温度变更为150℃、250℃和300℃,使混合气体流通,算出获得的透过气体的氨的浓度以及氨/氢、氨/氮的渗透通量比。获得的结果如表5所示。表5中,透过气体的氨的浓度为将小数点后第1位四舍五入后的值。另外,250℃下的氨的渗透通量为1.0×10-8[mol/(m2·s·pa)]。基于表5的结果可知,通过使混合气体中的氨气浓度为规定量以上,可高效地分离氨。此外确认到,高温条件下,沸石粒子间不产生空隙、缺陷,可高选择性地分离氨。【表5】表5150℃250℃300℃透过气体的nh3浓度52%54%52%nh3/n2的渗透通量比202524nh3/h2的渗透通量比565[制造例a4:rho沸石膜复合物2的制造]除将附着有晶种的支撑体沿垂直方向浸渍于装有水热合成用原料混合物2的teflon(注册商标)制内筒中,密封高压釜,在150℃下自生压力下加热72小时以外,除不进行nh4+型向h+型的转换以外,以制造例a3中记载的方法获得nh4+型的rho型沸石膜复合物。然后,将nh4+型的rho型沸石膜复合物投入装有1m的硝酸铝水溶液45g的teflon(注册商标)制内筒(65ml)。密封高压釜,在100℃下,以静置状态在自生压力下加热1小时。经过规定时间后,放置冷却后,将rho型沸石膜复合物从水溶液中取出,用水清洗后,在100℃下干燥4小时以上,获得al处理后的nh4+型的rho型沸石膜复合物,进一步地,投入装有1m的硝酸钠水溶液45g的teflon(注册商标)制内筒(65ml)。密封高压釜,在100℃下,以静置状态在自生压力下加热1小时。经过规定时间后,放置冷却后,将rho型膜从水溶液中取出,用水清洗后,在100℃下干燥4小时以上,获得作为rho型沸石膜复合物2的al处理后离子交换为na+型的rho型沸石膜复合物。[实施例a6]<膜分离性能的评价>使用制造例a4所述的rho型沸石膜复合物2,使用图1的装置,通过上述方法,进行从氨/氢/氮的混合气体中的氨分离试验。作为前处理,在250℃下,在耐压容器2和沸石膜复合物1之间导入50体积%h2/50体积%n2的混合气体作为供给气体7,保持压力为约0.3mpa,使rho型沸石膜复合物2的圆筒的内侧为0.098mpa(大气压),干燥约120分钟。然后,以100sccm使12体积%nh3/51体积%n2/37体积%h2的混合气体流通,设定背压为0.4mpa。此时,沸石膜复合物2的供给气体7侧与透过气体8侧的压差为0.3mpa。然后,将rho型沸石膜复合物2的温度变更为100℃和250℃,进行流通,算出获得的透过气体的氨的浓度以及氨/氢、氨/氮的渗透通量比。获得的结果如表6所示。表6中,透过气体的氨的浓度为将小数点后第1位四舍五入后的值。基于表6的结果可知,通过使混合气体中的氨气浓度为规定量以上,可高效地分离氨。此外确认到,即使在高温条件下,rho型沸石膜复合物也可高选择性地分离氨。此外,250℃下的氨的渗透通量为2.0×10-8[mol/(m2·s·pa)]。【表6】表6100℃250℃透过气体的nh3浓度60%56%nh3/n2的渗透通量比2931nh3/h2的渗透通量比76[制造例a5:rho型沸石膜复合物3、4的制造]除添加水以使rho型沸石为1质量%而获得晶种分散液以外,通过与制造例a4相同的方法准备晶种和支撑体,将内侧抽真空的支撑体浸于该晶种分散液中1分钟,然后,在将支撑体的内侧抽真空的状态下,通过摩擦法使晶种附着于支撑体。接着,将附着有晶种的支撑体沿垂直方向浸渍于装有通过与制造例a4相同的方法制作的水热合成用原料混合物的teflon(注册商标)制内筒中,密封高压釜,在160℃下自生压力下加热24小时。经过规定时间后,放置冷却后,将支撑体-沸石膜复合物从高压釜中取出,清洗后在100℃下干燥5小时以上。干燥后,原始合成状态下的空气透过量为0.0/(m2·分)。接着,为除去模板,烧制获得的膜复合物,获得rho型沸石膜复合物。基于烧制后的沸石膜复合物的重量与支撑体的重量的差,支撑体上晶化的rho型沸石的重量为62g/m2。接着,将除去模板后的rho型沸石膜复合物投入装有1m的硝酸铵水溶液50g的teflon(注册商标)制内筒(65ml)。密封高压釜,在100℃下,以静置状态在自生压力下加热1小时。经过规定时间后,放置冷却后,将rho型膜从水溶液中取出,用100℃的离子交换水进行1小时的热水洗。然后,重复5次上述使用1m的硝酸铵水的处理后,在100℃下干燥4小时以上,获得作为rho型沸石膜复合物3的nh4+型的rho型沸石膜复合物。将获得的nh4+型的rho型沸石膜复合物3投入装有1m的硝酸铝水溶液45g的teflon(注册商标)制内筒(65ml)密封高压釜,在100℃下,以静置状态在自生压力下加热1小时。经过规定时间后,放置冷却后,将rho型沸石复合物膜3从水溶液中取出,用水清洗后,在100℃下干燥4小时以上,获得作为rho型沸石膜复合物4的经al处理的nh4+型的rho型沸石膜复合物。[实施例a7]<膜分离性能的评价>使用制造例a5所述的rho型沸石膜复合物4,使用图1的装置,通过上述方法进行从氨(nh3)/氢(h2)/氮(n2)的混合气体中的氨分离试验。作为前处理,250℃下,在耐压容器与rho沸石膜复合物4之间导入10体积%nh3/20体积%h2/60体积%n2的混合气体作为供给气体,保持压力为约0.3mpa,使rho沸石膜复合物4的圆筒的内侧为0.098mpa(大气压),干燥约120分钟。然后,以100sccm使12体积%nh3/51体积%n2/37体积%h2的混合气体流通,设定背压为0.4mpa。此时,rho沸石膜复合物4的供给气体侧与透过气体侧的压差为0.3mpa。此外,作为吹扫气体,从供给气体9供给3.9sccm的氩。将rho型沸石膜复合物4的温度变更为250℃、300℃和325℃而使混合气体流通,获得的透过气体的氨的浓度以及氨/氢、氨/氮的渗透通量比如表7所示。表7中,透过气体的氨的浓度为将小数点后第1位四舍五入后的值。基于这些结果还可确认,在高温条件下,经al处理的nh4+型的rho型沸石膜可高选择性地分离氨。此外,250℃下的氨的渗透通量为1.0×10-8[mol/(m2·s·pa)],325℃下的氨的渗透通量为2.0×10-8[mol/(m2·s·pa)]。基于表7的结果可知,通过使混合气体中的氨气浓度为规定量以上,可高效地分离氨。此外可知,即使在高温条件下,也可高效地分离氨。【表7】表7250℃300℃325℃透过气体的nh3浓度71%70%71%nh3/n2的渗透通量比435963nh3/h2的渗透通量比151313[制造例a6:rho型沸石膜复合物5的制造]通过与制造例a5的rho型沸石膜复合物3相同的方法,将获得的nh4+型的rho型沸石膜复合物投入装有1m的硝酸钠水溶液50g的teflon(注册商标)制内筒(65ml)。密封高压釜,在100℃下,以静置状态在自生压力下加热1小时。经过规定时间后,放置冷却后,将rho型膜从水溶液中取出,用100℃的离子交换水进行1小时的热水洗后,在100℃下干燥4小时以上,获得离子交换成na+型的rho型沸石膜复合物。接着,将获得的na+型的rho型沸石膜投入装有1m的硝酸铝水溶液50g的teflon(注册商标)制内筒(65ml),密封高压釜,在100℃下,以静置状态在自生压力下加热1小时。经过规定时间后,放置冷却后,将rho型膜从水溶液中取出,重复3次用100℃的离子交换水的1小时热水洗后,在100℃下干燥4小时以上,获得作为rho型沸石膜复合物5的经al处理的na+型的rho型沸石膜复合物。[实施例a8]<膜分离性能的评价>除使用制造例a6所述的rho型沸石膜复合物5代替制造例a5所述的rho型沸石膜复合物4,作为吹扫气体供给8.3sccm的氩以外,以与实施例a7相同的方法,进行12.0体积%nh3/51.0体积%n2/37.0体积%h2的混合气体的分离试验。获得的透过气体的氨的浓度以及氨/氢、氨/氮的渗透通量比如表8所示。表8中,透过气体的氨的浓度为将小数点后第1位四舍五入后的值。此外,250℃下的氨的渗透通量为4.4×10-8[mol/(m2·s·pa)],325℃下的氨的渗透通量为1.1×10-7[mol/(m2·s·pa)]。基于这些结果可知,通过使混合气体中的氨气浓度为规定量以上,可高效地分离氨。此外可确认,即使在高温条件下,也可高选择性地分离氨。【表8】表8250℃300℃325℃透过气体的nh3浓度82%77%66%nh3/n2的渗透通量比259237230nh3/h2的渗透通量比443534[实施例a9]除使用制造例a6所述的rho型沸石膜复合物5,使温度为250℃,使混合气体为2.0体积%nh3/20.0体积%n2/78.0体积%h2的混合气体以外,用与实施例a8相同的手法,进行氨分离的评价的结果是,透过气体中的氨气浓度为19.9体积%。基于获得的结果可知,可从混合气体中分离氨。[实施例a10]除使用制造例a6所述的rho型沸石膜复合物5,使温度为250℃,使混合气体为3.0体积%nh3/20.0体积%n2/77.0体积%h2的混合气体以外,用与实施例a8相同的手法,进行氨分离的评价的结果是,透过气体中的氨气浓度为27.6体积%。基于获得的结果可知,可从混合气体中分离氨。[制造例a7:rho型沸石膜复合物6的制造](水热合成用混用物)作为用于水热合成的原料混合物,配制如下。通过将6.8g的18-冠-6-醚(东京化成公司制)、2.1g的naoh(岸田化学公司制)和4.2g的csoh·h2o(三津和化学公司制)溶解于125.9g的水中,在80℃下搅拌3小时,获得冠醚-碱水溶液。然后,向8.9g的y型(fau)沸石(sar=30、zeolyst公司制cbv720)和0.2g的氢氧化铝(al2o353.5质量%、aldrich公司制)滴加上述冠醚-碱水溶液,配制水热合成用原料混合物。获得的水热合成用原料混合物的凝胶组成(摩尔比)为sio2/al2o3/naoh/csoh/h2o/18-冠-6-醚=1/0.040/0.36/0.18/50/0.18。(膜复合物的制造)除添加水以使rho型沸石为1质量%而获得晶种分散液以外,通过与制造例a4相同的方法准备晶种和支撑体,将内侧抽真空的支撑体浸于该晶种分散液1分钟,然后,在支撑体的内侧抽真空的状态下通过摩擦法使晶种附着于支撑体。接着,将附着有晶种的支撑体沿垂直方向浸渍于装有水热合成用原料混合物的teflon(注册商标)制内筒中,密封高压釜,在160℃、自生压力下加热24小时。经过规定时间后,放置冷却后,将支撑体-沸石膜复合物从高压釜中取出,清洗后在100℃下干燥5小时以上。干燥后,原始合成状态下的空气透过量为0.0/(m2·分)。接着,为除去模板,烧制获得的膜复合物,获得rho型沸石膜复合物。基于烧制后的沸石膜复合物的重量与支撑体的重量的差,支撑体上晶化的rho型沸石的重量为56g/m2。接着,将除去模板后的rho型沸石膜复合物投入装有1m的硝酸铵水溶液50g的teflon(注册商标)制内筒(65ml)。密封高压釜,在100℃下,以静置状态在自生压力下加热1小时。经过规定时间后,放置冷却后,将rho型膜从水溶液中取出,用100℃的离子交换水进行1小时的热水洗。接着,重复5次上述使用1m的硝酸铵水的处理后,在100℃下干燥4小时以上,获得nh4+型的rho型沸石膜复合物。将nh4+型的rho型沸石膜复合物投入装有1m的硝酸铝水溶液50g的teflon(注册商标)制内筒(65ml)。密封高压釜,在100℃下,以静置状态在自生压力下加热1小时。经过规定时间后,放置冷却后,将rho型膜从水溶液中取出,用水清洗后,在100℃下干燥4小时以上,获得作为rho型沸石膜复合物6的经al处理的nh4+型的rho型沸石膜复合物。[实施例a11]<膜分离性能的评价>除使用制造例a7所述的rho型沸石膜复合物6代替制造例a5所述的rho型沸石膜复合物4以外,用与实施例a7相同的方法,在rho型沸石膜复合物6的温度为250℃和325℃的条件下,进行12体积%nh3/51体积%n2/37体积%h2的混合气体的分离试验。获得的透过气体的氨的浓度以及氨/氢、氨/氮的渗透通量比如表9所示。表9中,透过气体的氨的浓度为将小数点后第1位四舍五入后的值。基于这些结果可知,通过使混合气体中的氨气浓度为规定量以上,可高效地分离氨。此外确认到,用增加al含量的凝胶组成制造的rho膜,在高温条件下可更高选择性地分离氨。此外,250℃下的氨的渗透通量为1.3×10-8[mol/(m2·s·pa)]、325℃下的氨的渗透通量为2.8×10-8[mol/(m2·s·pa)]。【表9】表9250℃325℃透过气体的nh3浓度85%81%nh3/n2的渗透通量比408368nh3/h2的渗透通量比13269[制造例a8:mfi型沸石膜复合物1的制造](水热合成用原料混合物)水热合成用原料混合物通过下述方法配制。混合50wt%-naoh水溶液13.65g、水101g,向其加入铝酸钠(含有al2o3-62.2质量%)0.15g,室温下搅拌10分钟。向其中加入胶体二氧化硅(日产化学公司制snowtex-40)32.3g,在50度下搅拌5小时,作为水热反应用原料混合物。该反应用原料混合物的组成(摩尔比)为sio2/al2o3/naoh/h2o=3.05/0.013/0.193/100、sio2/al2o3=239。(晶种分散液)准备以研钵粉碎的zsm5沸石(东曹制hsz-800系列822h0a),分散晶种以使该晶种的浓度为约0.4质量%,制作晶种分散液。(膜复合物的制造)在上述晶种分散液中,将进行与制造例a1相同处理的多孔支撑体浸渍1分钟后,在70℃下干燥1小时,再度将其浸于晶种分散液1分钟后,在70℃下干燥1小时,在支撑体上附着晶种。附着的晶种的质量为约0.0016g。此外,通过上述方法准备附着有晶种的多孔支撑体。分别将附着有晶种的三个支撑体沿垂直方向浸渍于上述装有水热合成用原料混合物的teflon(注册商标)制内筒(200ml),密封高压釜,在180℃下,以静置状态在自生压力下加热30小时。经过规定时间后,放置冷却后,将支撑体-沸石膜复合物从反应混合物中取出,清洗后,在100℃下干燥3小时,获得mfi型沸石膜复合物1。另外,支撑体上晶化的mfi型沸石的质量为0.26~0.28g。此外,烧制后的膜复合物的空气透过量为0.0~0.1cm3/分。[实施例a12]<膜分离性能的评价>除使用制造例a8所述的mfi型沸石膜复合物1代替制造例a1所述的cha型沸石膜复合物1以外,用与实施例a1相同的方法进行氨分离评价。获得的透过气体的氨的浓度以及氨/氢、氨/氮的渗透通量比如表10所示。表10中,透过气体的氨的浓度为将小数点后第1位四舍五入后的值。此外,250℃下的氨的渗透通量为7.5×10-8[mol/(m2·s·pa)]。基于这些结果可知,通过使混合气体中的氨气浓度为规定量以上,可高效地分离氨。此外确认到,即使温度从150℃变更为250℃,氨也可高选择性地透过膜内。因此确认到,即使在高温条件下,也可高选择性地分离氨。【表10】表10100℃150℃200℃250℃透过气体的nh3浓度46%44%46%45%nh3/n2的渗透通量比18182323nh3/h2的渗透通量比5455[实施例a13]除使温度为250℃,混合气体为2.0体积%nh3/20.0体积%n2/78.0体积%h2的混合气体以外,用与实施例a12相同的手法,进行氨分离的评价的结果是,透过气体中的氨气浓度为7.0体积%。基于获得的结果可知,可从混合气体中分离氨。[实施例a14]除使温度为250℃,混合气体为3.0体积%nh3/20.0体积%n2/77.0体积%h2的混合气体以外,用与实施例a12相同的手法,进行氨分离的评价的结果是,透过气体中的氨气浓度为10.7体积%。基于获得的结果可知,可从混合气体中分离氨。[参考例a2]除使用制造例a8中制作的mfi型沸石膜复合物1,使mfi型沸石膜复合物1的温度为250℃,以100sccm的流量使12体积%nh3/50体积%n2/38体积%h2的混合气体流通以外,用与实施例a12相同的手法进行氨分离的评价,结果是氢的渗透通量为1.6×10-8[mol/(m2·s·pa)],氮的渗透通量为3.3×10-9[mol/(m2·s·pa)],氨的渗透通量为7.5×10-8[mol/(m2·s·pa)]。与之相对地,仅单独流通氢气时的氢的渗透通量为4.7×10-7[mol/(m2·s·pa)],仅单独流通氮气时的氮的渗透通量为3.0×10-7[mol/(m2·s·pa)],基于这些结果可知,在供给气体中含有氨气时,氢和氮的两者的渗透通量均显著降低。可认为基于本结果,通过使混合气体中的氨气浓度为规定量以上,供给气体中的氨吸附于沸石,可表现出阻碍氢、氮的透过的效果。表11中显示了实施例a1~a3、a8~10、a12~14、比较例a1~a2的数据。另外,实施例a1~a3、比较例a1,a2显示100℃下、实施例a8~10、a12~14显示250℃下的评价结果。基于这些结果也可知,通过使混合气体中的氨气浓度为规定量以上,相对于氢和氮,氨的浓缩度提高。【表11】表11[实施例b][物性和分离性能的测定]下文中,沸石或沸石膜复合物的物性、分离性能等的测定如下进行。(1)x射线回折(xrd)测定xrd测定基于以下条件进行。装置名:bruker公司制newd8advance光学系统:聚焦光学系统光学系统规格入射侧:密封式x射线球管(cukα)索拉狭缝(2.5°)发散狭缝(可变狭缝)样品台:xyz平台受光侧:半导体阵列检测器(lynxeye1dmode)ni-滤片索拉狭缝(2.5°)测角仪半径:280mm测定条件x射线功率(cukα):40kv、40ma扫描轴:θ/2θ扫描范围(2θ):5.0-70.0°测定模式:连续步长:0.01°计数时间:57.0sec(0.3sec×190ch)自动可变狭缝(automatic-ds):1mm(照射宽度)对测定数据进行可变→固定狭缝校正。另外,x射线沿垂直于圆筒管的轴向照射。此外,在置于样品台圆筒管状膜复合物和与平行于样品台表面的面接触的两条线中,相比与样品台表面接触的线,主要对位于样品台表面上方的另一侧的线照射x射线,以尽可能地减少噪音。此外,照射宽度通过自动可变狭缝固定为1mm而测定,使用materialsdata,inc.的xrd解析软件jade+9.4(英语版),进行可变狭缝→固定狭缝变换,获得xrd图像。(2)xps测定(na、si、al、n)xps测定基于以下条件进行。仪器名:ulvac-phi株式会公司制quantum2000测定时的x射线源:单色化al-kα,功率16kv-34w(x射线产生面积)荷电中和:电子枪5μa、离子枪3v分光系统:通能宽谱:187.70ev窄谱(n1s,o1s,na1s,al2p,si2p,cs3d5):58.70ev※检出cs的情况下,由于cs3d5与al2p的峰位置重叠,采用al2s的峰代替al2p。(确认使用不含有cs的样品,采用al2p和al2s中的任一者,表面组成的分析值没有差别。)测定区域:300μm角飞离角:45°(从表面)能量校正;si2p=103.4ev定量采用ulvac-phi株式会社提供的灵敏度校正系数而进行,定量计算时的本底通过shirley法确定。(3)空气透过量密封沸石膜复合物的一端,将另一端以密封状态与5kpa的真空管路连接,用设置于真空管路与沸石膜复合物之间的质量流量仪测定空气流量,作为空气透过量[l/(m2·h)]。作为质量流量仪使用kofloc公司制8300,n2气体用,最大流量500ml/min(20℃,换算为1个大气压)。kofloc公司制8300中,质量流量仪的显示为10ml/min(20℃,换算为1个大气压)以下时,采用lintec公司制mm-2100m,空气用,最大流量20ml/min(0℃,换算为1个大气压)进行测定。图1中,将圆筒形的沸石膜复合物1,以收纳于不锈钢制的耐压容器2的状态,设置于恒温槽(未图示)。恒温槽中附设温度控制装置,从而能够调整供给气体的温度。圆筒形的沸石膜复合物1的一端用截面t字形的尾销3密封。沸石膜复合物1的另一端介由连接部4与透过气体8的排出配管10连接,配管10向耐压容器2的外侧延伸。进一步地,从耐压容器2出来的气体排出配管13上连接有测定从供给配管12出来的供给气体7的供给压力的压力计5,以及用于调整供给压力的背压阀6。各连接部气密性良好地连接。图1的装置中,进行单成分气体透过试验时,以恒定流量将供给气体(试样气体)7供给至耐压容器2与沸石膜复合物1之间,通过背压阀6恒定供给侧的压力,用与配管10连接的流量计,测定透过沸石膜复合物1的透过气体8。圆筒形的沸石膜复合物1的一端用截面t字形的尾销3密封。沸石膜复合物1的另一端介由连接部4与透过气体8的排出配管11连接,配管11向耐压容器2的外侧延伸。流向耐压容器2的供给气体(试样气体)7的供给配管12与测定供给气体7的供给侧的压力的压力计5连接。各连接部气密性良好地连接。(4)氨分离试验在图1中示意显示的装置中,如下所述地,进行氨分离试验。图1的装置中,作为供给气体,以100sccm的流量,将包含氨、氮、氢的混合气体供给至耐压容器与沸石膜复合物之间,通过背压阀调整供给侧的气体与透过膜内的气体的压力差,使之恒定为0.3mpa,作为标准物质,向从配管10排出的排出气体混合的用质量流量控制器控制流量的氦,用微型气相色谱进行分析,算出透过气体的浓度和流量。另外,氨分离试验中,由于为从耐压容器中除去水分、空气等成分,在测定温度以上干燥和排气,通过使用的试样气体进行吹扫处理后,使试样气体温度以及沸石膜复合物的供给气体侧与透过气体侧的压差恒定,透过气体流量稳定后,测定透过沸石膜复合物的试样气体(透过气体)的流量,算出气体的渗透通量[mol/(m2·s·pa)]。使用供给气体的供给侧与透过侧的压力差(压差)计算渗透通量时的压力。混合气体的情况下使用分压差。此外,基于该测定结果,通过下述式(1)算出理想分离系数α’。α’=(q1/q2)/(p1/p2)(1)〔式(1)中,q1和q2分别表示透过性高的气体和透过性低的气体的透过量[mol·(m2·s)-1],p1和p2分别表示透过性高的气体和透过性低的气体的、供给侧与透过侧的压力差[pa]。〕该值表示各气体的渗透通量的比率,因此,可算出各气体的渗透通量,由其比率求得。[制造例b1:rho型沸石膜复合物1、2的制造]通过以下方法制造rho型沸石膜复合物1、2。在制造rho型沸石膜复合物1、2之前,如下所述地,准备水热合成用原料混合物1、支撑体和晶种分散液1。(水热合成用原料混合物1)通过将6.8g的18-冠-6-醚(东京化成公司制)、2.1g的naoh(岸田化学公司制)和4.2g的csoh·h2o(三津和化学公司制)溶解于125.9g的水,在80℃下搅拌3小时,获得冠醚-碱水溶液。然后,向8.9g的y型(fau)沸石(sar=30、zeolyst公司制cbv720)滴加上述冠醚-碱水溶液,配制水热合成用原料混合物。获得的水热合成用原料混合物1的凝胶组成(摩尔比)为sio2/al2o3/naoh/csoh/h2o/18-冠-6-醚=1/0.033/0.36/0.18/50/0.18。(支撑体)作为多孔支撑体,将氧化铝管(外径6mm,内径4mm,孔径0.15μm,株式会社则武制)切断为80mm的长度后,用水清洗后干燥使用。(晶种分散液1)通过将23g的18-冠-6-醚(东京化成公司制)、6g的naoh(岸田化学公司制)和5g的csoh·h2o(三津和化学公司制)溶解于84g的水,将获得的溶液在80℃下搅拌3小时,获得冠醚-碱水溶液。接着,向30g的fau型沸石(sar=30,zeolyst公司制cbv720)滴加上述冠醚-碱水溶液,进一步地作为晶种添加根据wo2015020014号单行本而合成的rho型沸石0.6g,室温下搅拌2小时,配制混合物。该混合物的组成(摩尔比)为sio2/al2o3/naoh/csoh/h2o/18-冠-6-醚=1/0.033/0.30/0.06/10/0.18。将该混合物在室温下熟成24小时后,投入耐压容器,在150℃的烘箱中静置,进行72小时水热合成。该水热合成反应后,冷却反应液,通过过滤回收生成的晶体。将回收的晶体在100℃下干燥12小时,获得rho型沸石的晶体。用球磨机粉碎获得的rho型沸石,制造晶种分散液。具体地,向500ml的塑料瓶投入上述rho型沸石10g、的hd氧化铝珠(nikkato公司制)300g、水90g,用球磨机粉碎6小时,制成10质量%的rho型沸石分散液。向该沸石分散液添加水以使rho型沸石为1质量%,获得晶种分散液1。(沸石膜复合物的制造)接着,在该晶种分散液1中,将内侧抽真空的支撑体浸1分钟,然后,以支撑体的内侧抽真空的状态,通过摩擦法使晶种附着于支撑体。将附着有晶种的支撑体沿垂直方向浸渍于装有水热合成用原料混合物的teflon(注册商标)制内筒中,密封高压釜,在160℃下,在自生压力下加热24小时。经过规定时间后,放置冷却后,将支撑体-沸石膜复合物从高压釜中取出,用离子交换水清洗后,在100℃下干燥5小时以上。干燥后,原始合成状态下的空气透过量为0.0l/(m2·分)。接着,为除去模板,烧制获得的膜复合物,获得rho型沸石膜复合物。将该rho型沸石膜复合物从室温升温2小时至100℃、从100℃升温20小时至300℃,在300℃下烧制5小时后,降温20小时至100℃为止,从100℃降温2小时至室温以。基于烧制后的沸石膜复合物的重量与支撑体的重量的差,支撑体上晶化的rho型沸石的重量为62g/m2。接着,将除去模板后的rho型沸石膜复合物投入装有1m的硝酸铵水溶液50g的teflon容器(注册商标)制内筒(65ml)中。密封高压釜,在100℃下,以静置状态在自生压力下加热1小时。经过规定时间后,放置冷却后,将rho型膜从水溶液中取出,用100℃的离子交换水进行1小时的热水洗。然后,重复5次上述使用1m的硝酸铵水的处理后,在100℃下干燥4小时以上,获得作为rho型沸石膜复合物1的nh4+型的rho型沸石膜复合物。将获得的nh4+型的rho型沸石膜复合物1投入装有1m的硝酸铝水溶液45g的teflon容器(注册商标)制内筒(65ml),密封高压釜,在100℃下,以静置状态在自生压力下加热1小时。经过规定时间后,放置冷却后,将经上述处理的nh4+型的rho型沸石膜复合物1从水溶液中取出,用离子交换水清洗后,在100℃下干燥4小时以上,获得作为rho型沸石膜复合物2的经al处理的nh4+型的rho型沸石膜复合物。此外,通过xps测定该沸石膜复合物的沸石膜的结果是,沸石膜的氮原子/al原子摩尔比为0.42,si原子/al原子摩尔比为3.01。[实施例b1]<膜分离性能的评价>使用制造例b1所述的rho型沸石膜复合物2,使用图1的装置通过上述方法,进行从氨气(nh3)/氢气(h2)/氮气(n2)的混合气体中的氨分离试验,具体地,通过下述方法进行。作为前处理,在250℃下,向耐压容器与rho沸石膜复合物2之间导入10体积%nh3/20体积%h2/60体积%n2的混合气体作为供给气体,保持压力为约0.3mpa,使rho沸石膜复合物2的圆筒的内侧为0.098mpa(大气压),干燥约120分钟。然后,作为供给气体,以100sccm流通12体积%nh3/51体积%n2/37体积%h2的混合气体,设定背压为0.4mpa。此时,rho沸石膜复合物2的供给气体侧与透过气体侧的压差为0.3mpa。此外,从供给气体9供给3.9sccm的氩作为吹扫气体。另外,将rho型沸石膜复合物2的温度变更为250℃、300℃和325℃,使混合气体流通时,获得的透过气体的氨的浓度以及氨/氢、氨/氮的渗透通量比如表12所示。基于表12的结果可知,通过使用以xps测定的氮原子/al原子摩尔比为0.42的nh4+型的rho型沸石膜,可高效地分离氨。此外确认到,高温条件下,以xps测定的氮原子/al原子摩尔比为0.42的本nh4+型的rho型沸石膜可高选择性地分离氨。另外,250℃下的氨的渗透通量为1.0×10-8[mol/(m2·s·pa)],325℃下的氨的渗透通量为2.0×10-8[mol/(m2·s·pa)]。【表12】表12250℃300℃325℃透过气体的nh3浓度71%70%71%nh3/n2的渗透通量比435963nh3/h2的渗透通量比151313[制造例b2:rho型沸石膜复合物3的制造]通过以下方法,制造rho型沸石膜复合物3。另外,支撑体使用与制造例b1相同的支撑体,晶种分散液使用与制造例b1相同的晶种分散液1。(水热合成用混用物2)作为水热合成原料混合物2,配制如下。通过将6.8g的18-冠-6-醚(东京化成公司制)、2.1g的naoh(岸田化学公司制)和4.2g的csoh·h2o(三津和化学公司制)溶解于125.9g的水,在80℃下搅拌3小时,获得冠醚-碱水溶液。然后,向8.9g的y型(fau)沸石(sar=30、zeolyst公司制cbv720)和0.2g的氢氧化铝(al2o353.5质量%、aldrich公司制)滴加上述冠醚-碱水溶液,配制水热合成用原料混合物。获得的水热合成用原料混合物2的凝胶组成(摩尔比)为sio2/al2o3/naoh/csoh/h2o/18-冠-6-醚=1/0.040/0.36/0.18/50/0.18。(膜复合物的制造)在晶种分散液1中,将内侧抽真空的支撑体浸渍1分钟,然后,在支撑体的内侧抽真空的状态下通过摩擦法使晶种附着于支撑体。接着,将附着有晶种的支撑体沿垂直方向浸渍于装有水热合成用原料混合物2的teflon(注册商标)制内筒中,密封高压釜,在160℃下、自生压力下加热24小时。经过规定时间后,放置冷却后,将支撑体-沸石膜复合物从高压釜中取出,用离子交换水清洗后,在100℃下干燥5小时以上。干燥后,原始合成状态下的空气透过量为0.0l/(m2·分)。接着,为除去模板,烧制获得的膜复合物,获得rho型沸石膜复合物。将该rho型沸石膜复合物从室温升温2小时至100℃,从100℃升温20小时至300℃,在300℃下烧制5小时后,降温20小时至100℃为止,从100℃降温2小时至室温。基于烧制后的沸石膜复合物的重量与支撑体的重量的差,支撑体上晶化的rho型沸石的重量为56g/m2。接着,将除去模板后的rho型沸石膜复合物投入装有1m的硝酸铵水溶液50g的teflon容器(注册商标)制内筒(65ml)中。密封高压釜,在100℃下,以静置状态在自生压力下加热1小时。经过规定时间后,放置冷却后,将rho型膜从水溶液中取出,用100℃的离子交换水进行1小时的热水洗。接着,重复5次上述使用1m的硝酸铵水的处理后,在100℃下干燥4小时以上,获得nh4+型的rho型沸石膜复合物。将nh4+型的rho型沸石膜复合物投入装有1m的硝酸铝水溶液50g的teflon容器(注册商标)制内筒(65ml)。密封高压釜,在100℃下,以静置状态在自生压力下加热1小时。经过规定时间后,放置冷却后,将经上述处理的nh4+型的rho型沸石膜复合物从水溶液中取出,用离子交换水清洗后,在100℃下干燥4小时以上,获得作为rho型沸石膜复合物3的经al处理的nh4+型的rho型沸石膜复合物。此外,通过xps测定的沸石膜的氮原子/al原子摩尔比为0.76,si原子/al原子摩尔比为6.65。[实施例b2]<膜分离性能的评价>除使用制造例b2所述的rho型沸石膜复合物3代替制造例b1所述的rho型沸石膜复合物2,将作为吹扫气体的氩的供给量变更为8.3sccm以外,用与实施例b1相同的方法在250℃和325℃的条件下,进行12体积%nh3/51体积%n2/37体积%h2的混合气体的分离试验。获得的透过气体的氨的浓度以及氨/氢、氨/氮的渗透通量比如表13所示。基于表13的结果可知,通过使用xps测定的氮原子/al原子摩尔比为0.76的本nh4+型的rho型沸石膜,可高效地分离氨。此外确认到,以增大al原子含量的凝胶组成制造的rho膜在高温条件下,可更高选择性地分离氨。另外,250℃下的氨的渗透通量为1.3×10-8[mol/(m2·s·pa)]、325℃下的氨的渗透通量为2.8×10-8[mol/(m2·s·pa)]。【表13】表13250℃325℃透过气体的nh3浓度85%81%nh3/n2的渗透通量比408368nh3/h2的渗透通量比13269[制造例b3:rho型沸石膜复合物4的制造]通过以下方法,制造rho型沸石膜复合物4。另外,水热合成用原料混合物和支撑体分别使用与制造例b1相同的水热合成用原料混合物1和支撑体。(晶种分散液2)除制作10质量%的rho型沸石分散液后,添加水以使rho型沸石为3质量%以外,通过与制造例b1的晶种分散液1相同的方法制造晶种分散液2。(膜复合物的制造)向支撑体滴加晶种分散液2,通过摩擦法使晶种附着于支撑体。接着,将附着有晶种的支撑体沿垂直方向浸渍于装有水热合成用原料混合物1的teflon(注册商标)制内筒中,密封高压釜,在150℃下自生压力下加热72小时。经过规定时间后,放置冷却后,将支撑体-沸石膜复合物从高压釜中取出,用离子交换水清洗后,在100℃下干燥5小时以上。干燥后,原始合成状态下的空气透过量为1.5l/(m2·分)。接着,为除去模板,烧制获得的膜复合物,获得rho型沸石膜复合物。将该rho型沸石膜复合物从室温升温2小时至150℃,从150℃升温20小时至400℃,在400℃下烧制5小时,降温20小时至150℃为止,从150℃降温2小时至室温。基于烧制后的沸石膜复合物的重量与支撑体的重量的差,支撑体上晶化的rho型沸石的重量为78g/m2。接着,将除去模板后的rho型沸石膜复合物投入装有3m的硝酸铵水溶液45g的teflon容器(注册商标)制内筒(65ml),密封高压釜,在110℃下,以静置状态在自生压力下加热1小时。经过规定时间后,放置冷却后,将rho型膜从水溶液中取出,用离子交换水清洗后,在100℃下干燥4小时以上,获得nh4+型的rho型沸石膜复合物。为将获得的nh4+型的rho型沸石膜复合物制成h+型,将该rho型沸石膜复合物用电炉在400℃下烧制2小时。此时至150℃为止的升温速度和降温速度均为2.5℃/分,150℃至400℃的升温速度和降温速度为0.5℃/分,获得作为rho型沸石膜复合物4的h+型的rho型沸石膜复合物。此外,通过xps测定的沸石膜的氮原子/al原子摩尔比为0.23,si原子/al原子摩尔比为2.92。[实施例b3]<膜分离性能的评价>使用制造例b3所述的rho型沸石膜复合物4,使用图1的装置进行从氨/氢/氮的混合气体中的氨分离试验。作为前处理,在250℃下,向耐压容器与rho型沸石膜复合物4之间导入50体积%h2/50体积%n2的混合气体作为供给气体,保持压力为约0.3mpa,使rho型沸石膜复合物4的圆筒的内侧为0.098mpa(大气压),干燥约120分钟。然后,以100sccm使12体积%nh3/51体积%n2/37体积%h2的混合气体流通,设定背压为0.4mpa。此时,rho型沸石膜复合物4的供给气体侧与透过气体侧的压差为0.3mpa。此外,从供给气体9供给2.4sccm的氩作为吹扫气体。另外,将rho型沸石膜复合物4的温度变更为150℃、250℃和300℃,使混合气体流通时,算出获得的透过气体的氨的浓度以及氨/氢、氨/氮的渗透通量比,获得的结果如表14所示。基于本结果确认到,将实施例b1以及2的nh4+型的rho型沸石膜复合物的分离结果相比较,虽然以xps测定的氮原子/al原子摩尔比为0.23的本h+型的rho型沸石膜复合物的氨分离性能有一些降低,其分离性能依然较高。另外,250℃下的氨的渗透通量为1.0×10-8[mol/(m2·s·pa)]。【表14】表14150℃250℃300℃透过气体的nh3浓度52%54%52%nh3/n2的渗透通量比202524nh3/h2的渗透通量比565[制造例b4:rho型沸石膜复合物5的制造]通过以下方法,制造rho型沸石膜复合物5。另外,作为水热合成用原料混合物,使用与制造例b2相同的水热合成原料混合物2,支撑体和晶种分散液分别使用与制造例b1相同的支撑体和晶种分散液1。(膜复合物的制造)在晶种分散液1中,将内侧抽真空的支撑体浸渍1分钟,然后,在支撑体的内侧抽真空的状态下,通过摩擦法使晶种附着于支撑体。接着,将附着有晶种的支撑体沿垂直方向浸渍于装有水热合成用原料混合物2的teflon(注册商标)制内筒中,密封高压釜,在160℃下自生压力下加热24小时。经过规定时间后,放置冷却后,将支撑体-沸石膜复合物从高压釜中取出,用离子交换水清洗后,在100℃下干燥5小时以上。干燥后,原始合成状态下的空气透过量为0.0l/(m2·分)。接着,为除去模板,将获得的膜复合物从室温升温2小时至100℃,从100℃升温20小时至300℃,在300℃下烧制5小时后,降温20小时至100℃为止,从100℃降温2小时至室温而烧制,获得cs+型的rho型沸石膜复合物5。本rho型沸石膜复合物5在其配制工序中完全不使用含有氮原子的原料,其含量以氮原子相对于al原子的摩尔比计小于0.01。另外,基于烧制后的沸石膜复合物的重量与支撑体的重量的差,支撑体上晶化的rho型沸石的重量为58g/m2。[参考例b1]<膜分离性能的评价>使用制造例b4所述的rho型沸石膜复合物5,使用图1的装置,通过上述方法进行从氨/氢/氮的混合气体中的氨分离试验。作为前处理,在250℃下,向耐压容器与rho沸石膜复合物5之间导入10体积%nh3/20体积%h2/60体积%n2的混合气体作为供给气体,保持压力为约0.3mpa,使rho沸石膜复合物2的圆筒的内侧为0.098mpa(大气压),干燥约120分钟。然后,以100sccm使12体积%nh3/51体积%n2/37体积%h2的混合气体流通,设定背压为0.4mpa。此时,rho沸石膜复合物5的供给气体侧与透过气体侧的压差为0.3mpa。此外,从供给气体9供给3.9sccm的氩作为吹扫气体,另外,将rho型沸石膜复合物5的温度变更为250℃和300℃,使混合气体流通时,获得的透过气体的氨的浓度以及氨/氢、氨/氮的渗透通量比如表15所示。另外,250℃下的氨的渗透通量为1.9×10-8[mol/(m2·s·pa)],300℃下的氨的渗透通量为2.0×10-8[mol/(m2·s·pa)]。基于表15的结果可知,本质上不含有氮原子的本cs+型的rho型沸石膜,相比含有x射线光电子能谱法所确定的相对于al原子的规定量的氮原子的实施例b1~3中任一项的rho型沸石膜,具有氨分离能降低,还有温度提高时分离性能大幅降低的倾向。因此,通过本结果可知,使用含有x射线光电子能谱法所确定的相对于al原子的规定量的氮原子的沸石膜时,能提高膜与氨的亲和性,优先透过氨,且具有相对于温度的高稳定性。【表15】表15250℃300℃透过气体的nh3浓度49%42%nh3/n2的渗透通量比3022nh3/h2的渗透通量比75[实施例c][物性和分离性能的测定]下文中,沸石或沸石膜复合物的物性、分离性能等的测定与实施例b同样进行。[制造例c1:rho型沸石膜复合物1、2的制造]通过以下方法,制造rho型沸石膜复合物1、2。在制造rho型沸石膜复合物1、2的制造之前,如下所述地,准备水热合成用原料混合物1、支撑体和晶种分散液1。(水热合成用原料混合物1)通过将6.8g的18-冠-6-醚(东京化成公司制)、2.1g的naoh(岸田化学公司制)和4.2g的csoh·h2o(三津和化学公司制)溶解于125.9g的水,在80℃下搅拌3小时,获得冠醚-碱水溶液。然后,向8.9g的y型(fau)沸石(sar=30、zeolyst公司制cbv720)滴加上述冠醚-碱水溶液,配制水热合成用原料混合物。获得的水热合成用原料混合物1的凝胶组成(摩尔比)为sio2/al2o3/naoh/csoh/h2o/18-冠-6-醚=1/0.033/0.36/0.18/50/0.18。(支撑体)作为多孔支撑体,将氧化铝管(外径6mm、内径4mm、孔径0.15μm、株式会社则武制)切断为80mm的长度后,用水清洗后干燥使用。(晶种分散液1)通过将23g的18-冠-6-醚(东京化成公司制)、6g的naoh(岸田化学公司制)和5g的csoh·h2o(三津和化学公司制)溶解于84g的水,在80℃下搅拌获得的溶液3小时,获得冠醚-碱水溶液。接着,向30g的fau型沸石(sar=30、zeolyst公司制cbv720)滴加上述冠醚-碱水溶液,进一步地作为晶种添加根据wo2015020014号单行本合成的rho型沸石0.6g,在室温下搅拌2小时,配制混合物。该混合物的组成(摩尔比)为sio2/al2o3/naoh/csoh/h2o/18-冠-6-醚=1/0.033/0.30/0.06/10/0.18。将该混合物在室温下熟成24小时后,投入耐压容器中,在150℃的烘箱中静置,进行72小时水热合成。该水热合成反应后,冷却反应液,通过过滤回收生成的晶体。将回收的晶体在100℃下干燥12小时,获得作为rho型沸石的晶体。将获得的rho型沸石用球磨机粉碎而制造晶种分散液。具体地,向500ml的塑料瓶中投入上述rho型沸石10g、的hd氧化铝珠(nikkato公司制)300g、水90g,用球磨机粉碎6小时,制成10质量%的rho型沸石分散液。向该沸石分散液中添加水以使rho型沸石为1质量%,获得晶种分散液1。(沸石膜复合物的制造)接着,在该晶种分散液1中,使内侧抽真空的支撑体浸渍1分钟,然后,在支撑体的内侧抽真空的状态下,通过摩擦法使晶种附着于支撑体。将附着有晶种的支撑体沿垂直方向浸渍于装有水热合成用原料混合物的teflon(注册商标)制内筒中,密封高压釜,在160℃下自生压力下加热24小时。经过规定时间后,放置冷却后,将支撑体-沸石膜复合物从高压釜中取出,用离子交换水清洗后100℃下干燥5小时以上。干燥后,原始合成状态下的空气透过量为0.0l/(m2·分)。接着,为除去模板,烧制获得的膜复合物,获得rho型沸石膜复合物。将该rho型沸石膜复合物从室温升温2小时至100℃,从100℃升温20小时至300℃,在300℃下烧制5小时后,降温20小时至100℃为止,从100℃降温2小时至室温。基于烧制后的沸石膜复合物的重量与支撑体的重量的差,支撑体上晶化的rho型沸石的重量为62g/m2。接着,将除去模板后的rho型沸石膜复合物投入装有1m的硝酸铵水溶液50g的teflon容器(注册商标)制内筒(65ml)中。密封高压釜,在100℃下,以静置状态在自生压力下加热1小时。经过规定时间后,放置冷却后,将rho型膜从水溶液中取出,用100℃的离子交换水进行1小时的热水洗。然后,重复5次上述使用1m的硝酸铵水的处理后,在100℃下干燥4小时以上,获得作为rho型沸石膜复合物1的nh4+型的rho型沸石膜复合物。将获得的nh4+型的rho型沸石膜复合物1投入装有1m的硝酸铝水溶液45g的teflon容器(注册商标)制内筒(65ml),密封高压釜,在100℃下,以静置状态在自生压力下加热1小时。经过规定时间后,放置冷却后,将经上述处理的nh4+型的rho型沸石膜复合物1从水溶液中取出,用离子交换水清洗后,在100℃下干燥4小时以上,获得作为rho型沸石膜复合物2的经al处理的nh4+型的rho型沸石膜复合物。此外,通过xps测定的沸石膜的氮原子/al原子摩尔比为0.42,si原子/al原子摩尔比为3.01。[实施例c1]<膜分离性能的评价>使用制造例c1所述的rho型沸石膜复合物2,使用图1的装置,通过上述方法进行从氨/氢/氮的混合气体中的氨分离试验,具体通过下述方法进行。作为前处理,在250℃下,向耐压容器与rho沸石膜复合物2之间导入10体积%nh3/20体积%h2/60体积%n2的混合气体作为供给气体,保持压力为约0.3mpa,使rho沸石膜复合物2的圆筒的内侧为0.098mpa(大气压),干燥约120分钟。然后,作为供给气体,以100sccm使12体积%nh3/51体积%n2/37体积%h2的混合气体流通,设定背压为0.4mpa。此时,rho沸石膜复合物2的供给气体侧与透过气体侧的压差为0.3mpa。此外,从供给气体9供给3.9sccm的氩作为吹扫气体。另外,将rho型沸石膜复合物2的温度变更为250℃、300℃和325℃,使混合气体流通时,获得的透过气体的氨的浓度以及氨/氢、氨/氮的渗透通量比如表16所示。另外,250℃下的氨的渗透通量为1.0×10-8[mol/(m2·s·pa)]、325℃下的氨的渗透通量为2.0×10-8[mol/(m2·s·pa)]。基于表16的结果可知,通过使用以xps测定的si原子/al原子摩尔比为3.01的nh4+型的rho型沸石膜,可高效地分离氨。此外,比较250℃和325℃所获得的透过气体的氨的浓度,可知在以xps测定的si原子/al原子摩尔比为3.01的本nh4+型的rho型沸石膜的情况下,其变化率近乎为0%,本沸石膜为分离热稳定性优异的分离膜。【表16】表16250℃300℃325℃透过气体的nh3浓度71%70%71%nh3/n2的渗透通量比435963nh3/h2的渗透通量比151313[制造例c2:rho型沸石膜复合物3的制造]通过以下方法,制造rho型沸石膜复合物3。另外,支撑体使用与制造例c1相同的支撑体,晶种分散液使用与制造例c1相同的晶种分散液1。(水热合成用混用物2)作为用于水热合成的原料混合物2,配制如下。通过将6.8g的18-冠-6-醚(东京化成公司制)、2.1g的naoh(岸田化学公司制)和4.2g的csoh·h2o(三津和化学公司制)溶解于125.9g的水,在80℃下搅拌3小时,获得冠醚-碱水溶液。然后,向8.9g的y型(fau)沸石(sar=30、zeolyst公司制cbv720)和0.2g的氢氧化铝(al2o353.5质量%、aldrich公司制)滴加上述冠醚-碱水溶液,配制水热合成用原料混合物。获得的水热合成用原料混合物2的凝胶组成(摩尔比)为sio2/al2o3/naoh/csoh/h2o/18-冠-6-醚=1/0.040/0.36/0.18/50/0.18。(膜复合物的制造)通过与制造例c1相同的方法,准备晶种分散液1和支撑体,在该晶种分散液1中,将内侧抽真空的支撑体浸渍1分钟,然后,在支撑体的内侧抽真空的状态下,通过摩擦法使晶种附着于支撑体。接着,将附着有晶种的支撑体沿垂直方向浸渍于装有水热合成用原料混合物的teflon(注册商标)制内筒中,密封高压釜,在160℃下自生压力下加热24小时。经过规定时间后,放置冷却后,将支撑体-沸石膜复合物从高压釜中取出,用离子交换水清洗后,在100℃下干燥5小时以上。干燥后,原始合成状态下的空气透过量为0.0l/(m2·分)。接着,为除去模板,烧制获得的膜复合物,获得rho型沸石膜复合物。将该rho型沸石膜复合物从室温升温2小时至100℃,从100℃升温20小时至300℃,在300℃下烧制5小时后,降温20小时至100℃为止,从100℃降温2小时至室温。基于烧制后的沸石膜复合物的重量与支撑体的重量的差,支撑体上晶化的rho型沸石的重量为56g/m2。接着,将除去模板后的rho型沸石膜复合物投入装有1m的硝酸铵水溶液50g的teflon容器(注册商标)制内筒(65ml)中。密封高压釜,在100℃下,以静置状态在自生压力下加热1小时。经过规定时间后,放置冷却后,将rho型膜从水溶液中取出,用100℃的离子交换水进行1小时的热水洗。接着,重复5次上述使用1m的硝酸铵水的处理后,在100℃下干燥4小时以上,获得nh4+型的rho型沸石膜复合物。将nh4+型的rho型沸石膜复合物投入装有1m的硝酸铝水溶液50g的teflon容器(注册商标)制内筒(65ml)中。密封高压釜,在100℃下,以静置状态自生压力下加热1小时。经过规定时间后,放置冷却后,将rho型膜从水溶液中取出,用离子交换水清洗后,在100℃下干燥4小时以上,获得作为rho型沸石膜复合物3的经al处理的nh4+型的rho型沸石膜复合物。此外,通过xps测定的沸石膜的氮原子/al原子摩尔比为0.76,si原子/al原子摩尔比为6.65。[实施例c2]<膜分离性能的评价>除使用制造例c2所述的rho型沸石膜复合物3代替制造例c1所述的rho型沸石膜复合物2,作为吹扫气体供给8.3sccm的氩以外,用与实施例c1相同的方法,在250℃和325℃的条件下,进行12体积%nh3/51体积%n2/37体积%h2的混合气体的分离试验。获得的透过气体的氨的浓度以及氨/氢、氨/氮的渗透通量比如表17所示。另外,250℃下的氨的渗透通量为1.3×10-8[mol/(m2·s·pa)],325℃下的氨的渗透通量为2.8×10-8[mol/(m2·s·pa)]。基于表17的结果可知,通过使用si原子/al原子摩尔比为6.65的本nh4+型的rho型沸石膜,可高效地分离氨。此外,比较250℃与325℃所获得的透过气体的氨的浓度可知,在以xps测定的si原子/al原子摩尔比为6.65的本nh4+型的rho型沸石膜的情况下,其变化率为5%左右,本沸石膜为分离热稳定性优异的分离膜。【表17】表17250℃325℃透过气体的nh3浓度85%81%nh3/n2的渗透通量比408368nh3/h2的渗透通量比13269[制造例c3:rho型沸石膜复合物4的制造]通过以下方法,制造rho型沸石膜复合物4。将通过与制造例c1的rho型沸石膜复合物1相同的方法获得的nh4+型的rho型沸石膜复合物投入装有1m的硝酸钠水溶液50g的teflon容器(注册商标)制内筒(65ml)。密封高压釜,在100℃下,以静置状态在自生压力下加热1小时。经过规定时间后,放置冷却后,将rho型膜从水溶液中取出,用100℃的离子交换水进行1小时的热水洗后,在100℃下干燥4小时以上,获得离子交换为na+型的rho型沸石膜复合物。接着,将获得的na+型的rho型沸石膜投入装有1m的硝酸铝水溶液50g的teflon容器(注册商标)制内筒(65ml)中,密封高压釜,在100℃下,以静置状态在自生压力下加热1小时。经过规定时间后,放置冷却后,将rho型膜从水溶液中取出,用离子交换水清洗后,在100℃下干燥4小时以上,获得作为rho型沸石膜复合物4的经al处理的na+型的rho型沸石膜复合物。此外,通过xps测定的沸石膜的na/al原子摩尔比为0.05、n原子/al原子摩尔比为1.21,si原子/al原子摩尔比为7.46。[实施例c3]<膜分离性能的评价>使用制造例c3所述的rho型沸石膜复合物4,使用图1的装置,通过上述方法进行从氨/氢/氮的混合气体中的氨分离试验。作为前处理,在250℃的条件下,向耐压容器与rho沸石膜复合物4之间导入10体积%nh3/20体积%h2/60体积%n2的混合气体作为供给气体,保持压力为约0.3mpa,使rho沸石膜复合物4的圆筒的内侧为0.098mpa(大气压),干燥约120分钟。然后,以100sccm使12体积%nh3/51体积%n2/37体积%h2的混合气体流通,设定背压为0.4mpa。此时,rho沸石膜复合物的供给气体侧与透过气体侧的压差为0.3mpa。此外,从供给气体9供给8.3sccm的氩作为吹扫气体。获得的透过气体的氨的浓度以及氨/氢、氨/氮的渗透通量比如表18所示。另外,此外250℃下的氨的渗透通量为4.4×10-8[mol/(m2·s·pa)],325℃下的氨的渗透通量为1.1×10-7[mol/(m2·s·pa)]。从表18的结果可知,通过使用以xps测定的si原子/al原子摩尔比为7.46的na+型的rho型沸石膜,可高效地分离氨。此外,比较250℃和325℃所获得的透过气体的氨的浓度可知,在以xps测定的si原子/al原子摩尔比为7.46的本na+型的rho型沸石膜的情况下,其变化率为20%左右,本沸石膜为分离热稳定性有一些降低的分离膜,但依然表现出高分离热稳定性。【表18】表18250℃300℃325℃透过气体的nh3浓度81%77%66%nh3/n2的渗透通量比259237230nh3/h2的渗透通量比443534[制造例c4:rho型沸石膜复合物5的制造]通过以下方法,制造rho型沸石膜复合物5。另外,水热合成用混合物使用与制造例c1相同的水热合成用原料混合物1,晶种分散液使用与晶种分散液1相同的分散液。(支撑体)作为多孔支撑体,将氧化铝管(外径6mm、内径4mm、孔径0.15μm、株式会社则武制)切断为40mm的长度后,用水清洗之后干燥使用。(膜复合物的制造)在该晶种分散液1中,将内侧抽真空的支撑体浸渍1分钟,然后,在支撑体的内侧抽真空的状态下,通过摩擦法使晶种附着于支撑体。接着,将附着有晶种的支撑体沿垂直方向浸渍于装有水热合成用原料混合物1的teflon(注册商标)制内筒中,密封高压釜,在160℃下自生压力下加热24小时。经过规定时间后,放置冷却后,将支撑体-沸石膜复合物从高压釜中取出,用离子交换水清洗后,在100℃下干燥5小时以上。干燥后,原始合成状态下的空气透过量为0.0l/(m2·分)。接着,为除去模板,烧制获得的膜复合物,获得rho型沸石膜复合物。将该rho型沸石膜复合物从室温升温2小时至100℃,从100℃升温20小时至300℃,在300℃下烧制5小时后,降温20小时至100℃为止,从100℃降温2小时至室温。基于烧制后的沸石膜复合物的重量与支撑体的重量的差,支撑体上晶化的rho型沸石的重量为52g/m2。接着,将除去模板后的rho型沸石膜复合物投入装有1m的硝酸铵水溶液50g的teflon容器(注册商标)制内筒(65ml)中。密封高压釜,在100℃下,以静置状态在自生压力下加热1小时。经过规定时间后,放置冷却后,将rho型膜从水溶液中取出,用100℃的离子交换水进行1小时的热水洗。接着,重复5次上述使用1m的硝酸铵水的处理后,在100℃下干燥4小时以上,获得作为rho型沸石膜复合物5的nh4+型的rho型沸石膜复合物。[参考例c1]<膜分离性能的评价>使用制造例c4所述的rho型沸石膜复合物5,使用图1的装置,通过上述方法进行从氨(nh3)/氢(h2)/氮(n2)的混合气体中的氨分离试验。作为前处理,在250℃的条件下,向耐压容器与rho沸石膜复合物5之间导入10体积%nh3/20体积%h2/60体积%n2的混合气体作为供给气体,保持压力为约0.3mpa,使rho沸石膜复合物5的圆筒的内侧为0.098mpa(大气压),干燥约120分钟。然后,以100sccm使12体积%nh3/51体积%n2/37体积%h2的混合气体流通,设定背压为0.4mpa。此时,rho沸石膜复合物的供给气体侧与透过气体侧的压差为0.3mpa。此外,从供给气体9供给3.9sccm的氩作为吹扫气体。获得的透过气体的氨的浓度以及氨/氢、氨/氮的渗透通量比如表19所示。通过本结果可知,相比经al处理的nh4+型的rho型沸石膜,未进行al处理的本nh4+型的rho型沸石膜的分离性能降低。即,通过本结果可知,通过对nh4+型的rho型沸石膜进行al处理,由于适当控制沸石膜的相对于si原子的al原子,可设计出从由包含氨且包含氢和/或氮的多种成分构成的混合气体中高选择性地分离氨的沸石膜。另外,250℃下的氨的渗透通量为3.0×10-8[mol/(m2·s·pa)],300℃下的氨的渗透通量为2.9×10-8[mol/(m2·s·pa)]。【表19】表19250℃300℃透过气体的nh3浓度41%41%nh3/n2的渗透通量比1518nh3/h2的渗透通量比44[实施例d][物性和分离性能的测定]下文中,沸石或沸石膜复合物的物性、分离性能等的测定与实施例b同样地进行。[制造例d1:rho型沸石膜复合物1、2的制造]通过以下方法,制造rho型沸石膜复合物1、2。在制造rho型沸石膜复合物1、2的制造之前,如下所述地,准备水热合成用原料混合物1、支撑体和晶种分散液1。(水热合成用原料混合物1)通过将6.8g的18-冠-6-醚(东京化成公司制)、2.1g的naoh(岸田化学公司制)和4.2g的csoh·h2o(三津和化学公司制)溶解于125.9g的水,在80℃下搅拌3小时,获得冠醚-碱水溶液。然后,向8.9g的y型(fau)沸石(sar=30、zeolyst公司制cbv720)滴加上述冠醚-碱水溶液,配制水热合成用原料混合物。获得的水热合成用原料混合物1的凝胶组成(摩尔比)为sio2/al2o3/naoh/csoh/h2o/18-冠-6-醚=1/0.033/0.36/0.18/50/0.18。(支撑体)作为多孔支撑体,将氧化铝管(外径6mm、内径4mm、孔径0.15μm、株式会社则武制)切断为80mm的长度后,用水清洗后干燥使用。(晶种分散液1)通过将23g的18-冠-6-醚(东京化成公司制)、6g的naoh(岸田化学公司制)和5g的csoh·h2o(三津和化学公司制)溶解于84g的水,在80℃下将获得的溶液搅拌3小时,获得冠醚-碱水溶液。接着,向30g的fau型沸石(sar=30、zeolyst公司制cbv720)滴加上述冠醚-碱水溶液,进一步地作为晶种添加根据wo2015020014号单行本合成的rho型沸石0.6g,在室温下搅拌2小时,配制混合物。该混合物的组成(摩尔比)为sio2/al2o3/naoh/csoh/h2o/18-冠-6-醚=1/0.033/0.30/0.06/10/0.18。将该混合物在室温下熟成24小时后,投入耐压容器中,在150℃的烘箱中静置,进行72小时水热合成。该水热合成反应后,冷却反应液,回收通过过滤生成的晶体。将回收的晶体在100℃下干燥12小时,获得作为rho型沸石的晶体。将获得的rho型沸石用球磨机粉碎而制造晶种分散液。具体地,向500ml的塑料瓶,投入上述rho型沸石10g、的hd氧化铝珠(nikkato公司制)300g、水90g,用球磨机粉碎6小时制成10质量%的rho型沸石分散液。向该沸石分散液中添加水以使rho型沸石为1质量%,获得晶种分散液1。(沸石膜复合物的制造)接着,在该晶种分散液1中,将内侧抽真空的支撑体浸渍1分钟,然后,在支撑体的内侧抽真空的状态下,通过摩擦法使晶种附着于支撑体。将附着有晶种的支撑体沿垂直方向浸渍于装有水热合成用原料混合物的teflon(注册商标)制内筒中,密封高压釜,在160℃下自生压力下加热24小时。经过规定时间后,放置冷却后,将支撑体-沸石膜复合物从高压釜中取出,用离子交换水清洗后,在100℃下干燥5小时以上。干燥后,原始合成状态下的空气透过量为0.0l/(m2·分)。接着,为除去模板,烧制获得的膜复合物,获得rho型沸石膜复合物。将该rho型沸石膜复合物从室温升温2小时至100℃,从100℃升温20小时至300℃,在300℃下烧制5小时后,降温20小时至100℃为止,从100℃降温2小时至室温。基于烧制后的沸石膜复合物的重量与支撑体的重量的差,支撑体上晶化的rho型沸石的重量为62g/m2。接着,将除去模板后的rho型沸石膜复合物投入装有1m的硝酸铵水溶液50g的teflon容器(注册商标)制内筒(65ml)中。密封高压釜,在100℃下,以静置状态在自生压力下加热1小时。经过规定时间后,放置冷却后,进行上述处理,将经上述处理的rho型沸石膜复合物从水溶液中取出,用100℃的离子交换水进行1小时的热水洗。然后,重复5次上述使用1m的硝酸铵水的处理后,在100℃下干燥4小时以上,获得作为rho型沸石膜复合物1的nh4+型的rho型沸石膜复合物。将获得的nh4+型的rho型沸石膜复合物1投入装有1m的硝酸钠水溶液50g的teflon容器(注册商标)制内筒(65ml)中。密封高压釜,在100℃下,以静置状态在自生压力下加热1小时。经过规定时间后,放置冷却后,将rho型膜从水溶液中取出,用100℃的离子交换水进行1小时的热水洗后,在100℃下干燥4小时以上,获得离子交换为na+型的rho型沸石膜复合物。接着,将获得的na+型的rho型沸石膜投入装有1m的硝酸铝水溶液50g的teflon容器(注册商标)制内筒(65ml)中,密封高压釜,在100℃下,以静置状态在自生压力下加热1小时。经过规定时间后,放置冷却后,将rho型膜从水溶液中取出,用离子交换水清洗后,在100℃下干燥4小时以上,获得作为rho型沸石膜复合物2的经al处理的na+型的rho型沸石膜复合物。此外,通过xps测定的沸石复合物膜的沸石膜的碱金属/al原子摩尔比为0.05、n原子/al原子摩尔比为1.21,si原子/al原子摩尔比为7.46。[实施例d1]<膜分离性能的评价>使用制造例d1所述的rho型沸石膜复合物2,使用图1的装置通过上述方法进行从氨/氢/氮的混合气体中的氨分离试验,具体通过下述方法进行。作为前处理,在250℃的条件下,向耐压容器与rho沸石膜复合物2之间导入10体积%nh3/20体积%h2/60体积%n2的混合气体作为供给气体,保持压力为约0.3mpa,使rho沸石膜复合物2的圆筒的内侧为0.098mpa(大气压),干燥约120分钟。然后,作为供给气体,以100sccm使12体积%nh3/51体积%n2/37体积%h2的混合气体流通,设定背压为0.4mpa。此时,rho沸石膜复合物的供给气体侧与透过气体侧的压差为0.3mpa。此外,从供给气体9供给8.3sccm的氩作为吹扫气体。获得的透过气体的氨的浓度以及氨/氢、氨/氮的渗透通量比如表20所示。从表20的结果可知,通过使用na+型的rho型沸石膜,可高效地分离氨。此外确认到,高温条件下,经al处理的na+型的rho型沸石膜可高选择性地分离氨。此外,250℃下的氨的渗透通量为4.4×10-8[mol/(m2·s·pa)],基于与表现出与本参考例d1的相同的n原子/al原子摩尔比和si原子/al原子摩尔比、不含有碱金属的rho型沸石膜复合物3的比较可知,含有碱金属原子时,可高透过性地回收相同高浓度的氨。【表20】表20250℃透过气体的nh3浓度82%nh3/n2的渗透通量比259nh3/h2的渗透通量比44[制造例d2:rho型沸石膜复合物3的制造]通过以下方法,制造rho型沸石膜复合物3。另外,支撑体使用与制造例d1相同的支撑体,晶种分散液使用与制造例d1相同的晶种分散液1。(水热合成用混用物2)作为用于水热合成的原料混合物2,配制如下。通过将6.8g的18-冠-6-醚(东京化成公司制)、2.1g的naoh(岸田化学公司制)和4.2g的csoh·h2o(三津和化学公司制)溶解于125.9g的水,在80℃下搅拌3小时,获得冠醚-碱水溶液。然后,向8.9g的y型(fau)沸石(sar=30、zeolyst公司制cbv720)和0.2g的氢氧化铝(al2o353.5质量%、aldrich公司制)滴加上述冠醚-碱水溶液,配制水热合成用原料混合物。获得的水热合成用原料混合物2的凝胶组成(摩尔比)为sio2/al2o3/naoh/csoh/h2o/18-冠-6-醚=1/0.040/0.36/0.18/50/0.18。(膜复合物的制造)通过与制造例d1相同的方法准备晶种和支撑体,在该晶种分散液1中,将内侧抽真空的支撑体浸渍1分钟,然后,在支撑体的内侧抽真空的状态下,通过摩擦法使晶种附着于支撑体。接着,将附着有晶种的支撑体沿垂直方向浸渍于装有水热合成用原料混合物2的teflon(注册商标)制内筒中,密封高压釜,在160℃下自生压力下加热24小时。经过规定时间后,放置冷却后,将支撑体-沸石膜复合物从高压釜中取出,用离子交换水清洗后,在100℃下干燥5小时以上。干燥后,原始合成状态下的空气透过量为0.0l/(m2·分)。接着,为除去模板,烧制获得的膜复合物,获得rho型沸石膜复合物。将该rho型沸石膜复合物从室温升温2小时至100℃,从100℃升温20小时至300℃,在300℃下烧制5小时后,降温20小时至100℃为止,从100℃降温2小时至室温。基于烧制后的沸石膜复合物的重量与支撑体的重量的差,支撑体上晶化的rho型沸石的重量为56g/m2。接着,将除去模板后的rho型沸石膜复合物投入装有1m的硝酸铵水溶液50g的teflon容器(注册商标)制内筒(65ml)中。密封高压釜,在100℃下,以静置状态在自生压力下加热1小时。经过规定时间后,放置冷却后,将rho型膜从水溶液中取出,用100℃的离子交换水进行1小时的热水洗。接着,重复5次上述使用1m的硝酸铵水的处理后,在100℃下干燥4小时以上,获得nh4+型的rho型沸石膜复合物。将nh4+型的rho型沸石膜复合物投入装有1m的硝酸铝水溶液50g的teflon容器(注册商标)制内筒(65ml)中。密封高压釜,在100℃下,以静置状态在自生压力下加热1小时。经过规定时间后,放置冷却后,将经上述处理的nh4+型的rho型沸石膜复合物从水溶液中取出,用离子交换水清洗后,在100℃下干燥4小时以上,获得作为rho型沸石膜复合物3的经al处理的nh4+型的rho型沸石膜复合物。此外,通过xps测定的沸石膜的n原子/al原子摩尔比为0.76,si原子/al原子摩尔比为6.65。未检测到碱金属。[参考例d1]<膜分离性能的评价>除使用制造例d2所述的rho型沸石膜复合物3代替制造例d1所述的rho型沸石膜复合物2以外,用与实施例d1相同的方法,在rho型沸石膜复合物3的温度为250℃的条件下,进行12体积%nh3/51体积%n2/37体积%h2的混合气体的分离试验。获得的透过气体的氨的浓度以及氨/氢、氨/氮的渗透通量比如表21所示。基于表21的结果可知,通过使用nh4+型的rho型沸石膜,可高效地分离氨。此外确认到,以增加al含量的凝胶组成来制造的rho膜,在高温条件下,可更高选择性地分离氨。然而可知,250℃下的氨的渗透通量为1.3×10-8[mol/(m2·s·pa)],透过性比含有碱金属的rho型沸石膜复合物2低。【表21】表21250℃透过气体的nh3浓度85%nh3/n2的渗透通量比408nh3/h2的渗透通量比132[制造例d3:rho型沸石膜复合物4的制造]通过以下方法,制造rho型沸石膜复合物4。(水热合成用混用物2)作为用于水热合成的原料混合物,配制如下。通过将6.8g的18-冠-6-醚(东京化成公司制)、2.1g的naoh(岸田化学公司制)和4.2g的csoh·h2o(三津和化学公司制)溶解于125.9g的水,在80℃下搅拌3小时,获得冠醚-碱水溶液。然后,向8.9g的y型(fau)沸石(sar=30、zeolyst公司制cbv720)和0.2g的氢氧化铝(al2o353.5质量%、aldrich公司制)滴加上述冠醚-碱水溶液,配制水热合成用原料混合物。获得的水热合成用原料混合物2的凝胶组成(摩尔比)为sio2/al2o3/naoh/csoh/h2o/18-冠-6-醚=1/0.040/0.36/0.18/50/0.18。(膜复合物的制造)通过与制造例d1相同的方法,准备晶种分散液1和支撑体,在该晶种分散液1中,将内侧抽真空的支撑体浸渍1分钟,然后,在支撑体的内侧抽真空的状态下,通过摩擦法使晶种附着于支撑体。接着,将附着有晶种的支撑体沿垂直方向浸渍于装有水热合成用原料混合物2的teflon(注册商标)制内筒中,密封高压釜,在160℃下自生压力下加热24小时。经过规定时间后,放置冷却后,将支撑体-沸石膜复合物从高压釜中取出,用离子交换水清洗后,在100℃下干燥5小时以上。干燥后,原始合成状态下的空气透过量为0.0l/(m2·分)。接着,为除去模板,将获得的膜复合物从室温升温2小时至100℃,从100℃升温20小时至300℃,在300℃下烧制5小时后,降温20小时至100℃为止,100℃降温2小时至室温烧制,获得cs+型的rho型沸石膜复合物4。像这样地,本cs+型的rho型沸石膜复合物4由于在形成沸石膜后不经过离子交换处理工序,沸石的al位点的离子对本质上为碱金属(cs和na)阳离子。基于本烧制后的沸石膜复合物的重量与支撑体的重量的差,支撑体上晶化的rho型沸石的重量为58g/m2。此外,通过xps测定的沸石复合物膜的沸石膜的碱金属/al原子摩尔比为0.073。[参考例d2]<膜分离性能的评价>使用制造例d3所述的rho型沸石膜复合物4,使用图1的装置,通过上述方法进行从氨/氢/氮的混合气体中的氨分离试验。作为前处理,在250℃下,向耐压容器与rho沸石膜复合物4之间导入10体积%nh3/20体积%h2/60体积%n2的混合气体作为供给气体,保持压力为约0.3mpa,使rho沸石膜复合物4的圆筒的内侧为0.098mpa(大气压),干燥约120分钟。然后,以100sccm使12体积%nh3/51体积%n2/37体积%h2的混合气体流通,设定背压为0.4mpa。此时,rho沸石膜复合物4的供给气体侧与透过气体侧的压差为0.3mpa。使rho型沸石膜复合物4的温度为250℃,使混合气体流通,获得的透过气体的氨的浓度以及氨/氢、氨/氮的渗透通量比如表22所示。此外,250℃下的氨的渗透通量为1.9×10-8[mol/(m2·s·pa)]。基于这些结果可知,由于形成沸石膜后未经离子交换处理工序,沸石的al位点的离子对本质上为碱金属阳离子的本cs+型rho型沸石膜,相比于rho型沸石膜复合物3,氨的透过性有一些提高,然而相比rho型沸石膜复合物2和3,氨分离性能降低。即,通过本结果可知,通过适当控制沸石中的碱金属原子相对于al原子的摩尔比,可设计一种沸石膜,其不仅可从由包含氨且包含氢和/或氮的多种成分构成的混合气体高选择性地分离氨,还可提高氨的透过性。【表22】表22250℃透过气体的nh3浓度49%nh3/n2的渗透通量比30nh3/h2的渗透通量比7[实施例e][物性和分离性能的测定]下文中,沸石或沸石膜复合物的物性的测定之中,xrd测定以与实施例b相同的条件进行,分离性能等测定与实施例b同样地进行。(1)热膨胀率的测定沸石的热膨胀率通过在以下条件下的升温xrd测定法而确定。(升温xrd测定装置规格)【表23】表23(测定条件)【表24】表24测定气氛:大气升温条件:20℃/min测定方法:保持测定温度5分钟后,实施xrd测定。测定数据中,使用可变狭缝,进行固定狭缝校正。热膨胀率的变化率的算出方法:热膨胀率的变化率=(规定温度下测定的晶格常数)÷(30℃下测定的晶格常数)-1……(1)[实施例e1](rho型沸石的制造)rho型沸石如下所述地合成。通过将23g的18-冠-6-醚(东京化成公司制)、6g的naoh(岸田化学公司制)和5g的csoh·h2o(三津和化学公司制)溶解于84g的水中,在80℃下搅拌获得的溶液3小时,获得冠醚-碱水溶液。向30g的fau型沸石(sar=30、zeolyst公司制cbv720)滴加上述冠醚-碱水溶液,进一步地作为晶种添加根据wo2015020014号单行本合成的rho型沸石0.6g,在室温下搅拌2小时,配制水热合成用原料混合物。该混合物的组成(摩尔比)如下。sio2/al2o3/naoh/csoh/h2o/18-冠-6-醚=1/0.033/0.30/0.06/10/0.18将该水热合成用原料混合物在室温下熟成24小时后,投入耐压容器中,在150℃的烘箱中静置,进行72小时水热合成。该水热合成反应后,冷却反应液,通过过滤回收生成的晶体。回收的晶体在100℃下干燥12小时。对获得的rho型沸石测定热膨胀率的结果是200℃的热膨胀率相对于30℃的变化率为-1.55%、300℃的热膨胀率相对于30℃的变化率为0.02%,400℃的热膨胀率相对于30℃的变化率为-0.01%,确认到相比30℃的热膨胀率,近乎未产生热膨胀或热收缩。[实施例e2]<rho型沸石膜复合物1的制作>通过在多孔支撑体上直接水热合成rho型沸石,制作多孔支撑体-rho型沸石膜复合物。另外,作为多孔支撑体,将氧化铝管(外径6mm、孔径0.15μm、株式会社则武制)切断为40mm的长度后,用水清洗后干燥使用。在多孔支撑体上进行水热合成之前,用球磨机粉碎以实施例e1所述的方法合成的rho型沸石,将其作为晶种使用。球磨机的粉碎如下实施。向500ml的塑料瓶中,加入上述晶种用的rho型沸石10g、的hd氧化铝珠(nikkato公司制)300g、水90g,球磨机粉碎6小时,作成10质量%的rho型沸石分散液。向该沸石分散液中,添加水以使rho型沸石为3质量%,获得晶种分散液。向支撑体滴加该晶种分散液,通过摩擦法使晶种附着于支撑体。接着,作为用于水热合成的原料混合物,配制如下。通过将6.8g的18-冠-6-醚(东京化成公司制)、2.1g的naoh(岸田化学公司制)和4.2g的csoh·h2o(三津和化学公司制)溶解于125.9g的水,在80℃下搅拌3小时,获得冠醚-碱水溶液。然后,向8.9g的y型(fau)沸石(sar=30、zeolyst公司制cbv720)滴加上述冠醚-碱水溶液,配制水热合成用原料混合物。获得的水热合成用原料混合物的凝胶组成(摩尔比)为sio2/al2o3/naoh/csoh/h2o/18-冠-6-醚=1/0.033/0.36/0.18/50/0.18。将附着有晶种的支撑体沿垂直方向浸渍于装有水热合成用原料混合物的teflon(注册商标)制内筒中,密封高压釜,在150℃下自生压力下加热72小时。经过规定时间后,放置冷却后,将支撑体-沸石膜复合物从高压釜中取出,清洗后100℃下干燥5小时以上。干燥后,原始合成状态下的空气透过量为1.5/(m2·分)。接着,为除去模板,烧制获得的膜复合物,获得rho型沸石膜复合物。基于烧制后的沸石膜复合物的重量与支撑体的重量的差,支撑体上晶化的rho型沸石的重量为78g/m2。接着,将除去模板后的rho型沸石膜复合物投入装有3m的硝酸铵水溶液45g的teflon(注册商标)容器制内筒(65ml)中。密封高压釜,在110℃下,以静置状态在自生压力下加热1小时。经过规定时间后,放置冷却后,将rho型膜从水溶液中取出,用水清洗后,在100℃下干燥4小时以上,获得nh4+型的rho型沸石膜复合物。为将nh4+型的rho型沸石膜复合物制成h+型,将该rho型沸石膜复合物用电炉在400℃下烧制2小时。此时,使至150℃为止的升温速度和降温速度均为2.5℃/分,从150℃至400℃的升温速度和降温速度为0.5℃/分,获得h+型的rho型沸石膜复合物。下文中,将所制造的rho型沸石膜复合物称为“rho型沸石膜复合物1”。[实施例e3](膜分离性能的评价)使用实施例e2所述的rho型沸石膜复合物1,使用图1的装置,进行从氨/氢/氮的混合气体中的氨分离试验。作为前处理,在250℃下,向耐压容器2和沸石膜复合物1之间导入50%h2/50%n2的混合气体作为供给气体7,保持压力为约0.3mpa,使沸石膜复合物1的圆筒的内侧为0.098mpa(大气压),干燥约120分钟。然后,以100sccm使12%氨/51%氮/37%氮的混合气体流通,设定背压为0.4mpa。此时,rho型沸石膜复合物1的供给气体7侧与透过气体8侧的压差为0.3mpa。将rho型沸石膜复合物1的温度变更为150℃~300℃,流通,获得的透过气体的氨的浓度以及氨/氢、氨/氮的渗透通量比如表25所示。基于这些结果也可确认,在高温条件下,通过减少rho型沸石的热膨胀或收缩,可使沸石粒子间不产生空隙、缺陷,可高选择性地分离氨。此外,250℃下的氨的渗透通量为1.0×10-8[mol/(m2·s·pa)]。因此,本发明的沸石膜复合物通过使用热膨胀率的变化率落入规定的范围内的沸石作为晶种来合成,表现出即使在高温条件下,也可稳定地高选择性地分离氨。【表25】表25150℃250℃300℃透过气体的nh3浓度52%54%52%nh3/n2的渗透通量比202524nh3/h2的渗透通量比565[实施例e4]<na+型rho的合成>关于na+型rho沸石,采用“微孔和介孔材料(microporousandmesoporousmaterials)132(2010)352-356)”所述的方法实施水热合成。水热合成反应后,冷却反应液,通过过滤回收生成的晶体。将回收的晶体在100℃下干燥12小时。对获得的rho型沸石测定热膨胀率的结果如图2所示。确认到na+型rho的热膨胀率相对于温度可拟合为一次直线。基于本拟合式可估算,300℃的热膨胀率相对于30℃的变化率为0.23%,400℃的热膨胀率相对于30℃的变化率为0.33%。[实施例e5]<rho沸石膜复合物2的合成>除将附着有晶种的支撑体沿垂直方向浸渍于装有水热合成用原料混合物的teflon(注册商标)制内筒中,密封高压釜,在150℃下自生压力下加热72小时以外,用与实施例e2所述的方法获得nh4+型的rho型沸石膜复合物。对于nh4+型的rho型沸石膜复合物,将其投入装有1m的硝酸铝水溶液45g的teflon(注册商标)容器制内筒(65ml)中。密封高压釜,在100℃下,以静置状态在自生压力下加热1小时。经过规定时间后,放置冷却后,将rho型膜从水溶液中取出,用水清洗后,在100℃下干燥4小时以上,获得经al处理的nh4+型的rho型沸石膜复合物。进一步地,将其投入装有1m的硝酸钠水溶液45g的teflon(注册商标)容器制内筒(65ml)中。密封高压釜,在100℃下,以静置状态在自生压力下加热1小时。经过规定时间后,放置冷却后,将rho型膜从水溶液中取出,用水清洗后,在100℃下干燥4小时以上,al处理后,获得离子交换为na+型的rho型沸石膜复合物。下文中,将所制造的al处理后离子交换为na+型的rho型沸石膜复合物称为“rho型沸石膜复合物2”。[实施例e6]<膜分离性能的评价>使用实施例e5所述的rho型沸石膜复合物2,使用图1的装置进行从氨/氢/氮的混合气体中的氨分离试验。作为前处理,在250℃下,向耐压容器2和沸石膜复合物1之间导入50%h2/50%n2的混合气体作为供给气体7,保持压力为约0.3mpa,使沸石膜复合物的圆筒的内侧为0.098mpa(大气压),干燥约120分钟。然后,以100sccm使12%氨/51%氮/37%氮的混合气体流通,设定背压为0.4mpa。此时,rho型沸石膜复合物2的供给气体7侧与透过气体8侧的压差为0.3mpa。将rho型沸石膜复合物2的温度变更为50℃和250℃而流通,获得的透过气体的氨的浓度以及氨/氢、氨/氮的渗透通量比如表26所示。基于这些结果也可确认,在高温条件下,通过减小rho型沸石的热膨胀或收缩,可使沸石粒子间不产生空隙、缺陷,可高选择性地分离氨。此外,250℃下的氨的渗透通量为2.0×10-8[mol/(m2·s·pa)]。因此确认到,通过使构成沸石膜复合物的沸石的热膨胀率的变化率在规定的范围内,rho型膜复合物可在高温条件下稳定地分离氨。【表26】表26100℃250℃透过气体的nh3浓度60%56%nh3/n2的渗透通量比2931nh3/h2的渗透通量比76[实施例e7]<mfi型沸石的制造>mfi型沸石如下所述而合成。混合50wt%-naoh水溶液13.65g、水101g,向其中加入铝酸钠(含有al2o3-62.2质量%)0.15g,室温下搅拌10分钟。向其中加入胶体二氧化硅(日产化学公司制snowtex-40)32.3g,在50度下搅拌5小时,将其作为水热反应用原料混合物。该反应用原料混合物的组成(摩尔比)为sio2/al2o3/naoh/h2o=3.05/0.013/0.193/100、sio2/al2o3=239。将该水热合成用原料混合物投入耐压容器中,在180℃的烘箱中,在以15rpm搅拌的同时,进行30小时水热合成。该水热合成反应后,冷却反应液,通过过滤回收生成的晶体。将回收的晶体在100℃下干燥12小时。对于获得的mfi型沸石测定c轴方向的热膨胀率的结果是,200℃的热膨胀率相对于30℃的变化率为0.13%,300℃的热膨胀率相对于30℃的变化率为0.15%,400℃的热膨胀率相对于30℃的变化率为0.13%(均为c轴方向),确认到相比30℃沸石产生了膨胀。[实施例e8]<mfi型沸石膜复合物的制作>首先,通过下述方法配制水热合成用原料混合物。混合50wt%-naoh水溶液13.65g、水101g,向其中加入铝酸钠(含有al2o3-62.2质量%)0.15g,室温下搅拌10分钟。向其中加入胶体二氧化硅(日产化学公司制snowtex-40)32.3g,50度下搅拌5小时,将其作为水热反应用原料混合物。该反应用原料混合物的组成(摩尔比)为sio2/al2o3/naoh/h2o=3.05/0.013/0.193/100、sio2/al2o3=239。用研钵粉碎zsm5沸石(东曹制hsz-800系列822h0a)作为晶种准备,,在使该晶种的浓度为约0.4质量%的水溶液中(zsm5晶种水溶液)中,将多孔支撑体浸渍1分钟后,在70℃下干燥1小时,再度浸渍于zsm5晶种溶液1分钟后,在70℃下干燥1小时,使晶种附着。附着的晶种的质量为约0.0016g。另外,作为多孔支撑体,将株式会社则武制的氧化铝管bn1(外径6mm、内径4mm)切断为80mm的长度后,用超声波清洗机清洗,然后干燥使用。此外,准备3个通过上述方法附着有晶种的多孔支撑体。将附着有晶种的3个支撑体分别沿垂直方向浸渍于装有上述水性反应混合物的teflon(注册商标)制内筒(200ml)中,密封高压釜,在180℃下,以静置状态在自生压力下加热30小时。经过规定时间后,放置冷却后,将支撑体-沸石膜复合物从反应混合物中取出,清洗后,在100℃下干燥3小时,获得mfi型沸石膜复合物2。支撑体上晶化的mfi型沸石的质量为0.26~0.28g。此外,烧制后的膜复合物的空气透过量为0.0~0.1cm3/分。[实施例e9]<膜分离性能的评价>将实施例e8所述的mfi型沸石膜复合物2的温度变更为100℃~250℃,以100sccm的流量使12%氨/51%氮/37%氮的混合气体流通,获得的透过气体的氨的浓度以及氨/氢、氨/氮的渗透通量比如表27所示。确认到即使将温度从150℃变更为250℃,也可使氨高选择性地透过膜内。因此确认到,即使在高温条件下,沸石粒子间不产生空隙、缺陷,可高选择性地分离氨,因而可认为沸石的热膨胀率与rho型沸石膜复合物为相同程度。此外,250℃下的氨的渗透通量为7.5×10-8[mol/(m2·s·pa)]。【表27】表27100℃150℃200℃250℃透过气体的nh3浓度46%44%46%45%nh3/n2的渗透通量比18182323nh3/h2的渗透通量比5455[参考例e1]<cha型沸石的制造>cha型沸石如下所述而合成。混合0.6g的naoh(岸田化学公司制)、1.1g的koh(岸田化学公司制)和水10g,向其中加入氢氧化铝(含有al2o3-53.5质量%、aldrich公司制)0.5g,搅拌使其溶解,制成透明溶液。作为有机模板,向其中加入n,n,n-三甲基-1-金刚烷氢氧化铵(下文中将其称为“tmadaoh”。)的25质量%水溶液5.4g,进一步地加入胶体二氧化硅(日产化学公司制snowtex-40)12g,搅拌2小时,制成水热合成用原料混合物。该混合物的组成(摩尔比)为sio2/al2o3/naoh/koh/h2o/tmadaoh=1/0.033/0.2/0.2/15/0.08,sio2/al2o3为30。将该水热合成用原料混合物加入耐压容器中,在190℃的烘箱中,在以15rpm搅拌的同时,进行15小时水热合成。该水热合成反应后,冷却反应液,通过过滤回收生成的晶体。将回收的晶体在100℃下干燥12小时。对于获得的cha型沸石测定热膨胀率的结果是,200℃的热膨胀率相对于30℃的变化率为-0.13%,300℃的热膨胀率相对于30℃的变化率为-0.30%,400℃的热膨胀率相对于30℃的变化率为-0.40%(均为c轴方向),确认到相比30℃,沸石产生收缩。[参考例e2]<cha型沸石膜复合物的制作>首先,如下所述地,配制水热合成用原料混合物。混合1mol/l-naoh水溶液1.45g、1mol/l-koh水溶液5.78g、水114.6g,向其中加入氢氧化铝(含有al2o3-53.5质量%、aldrich公司制)0.19g,搅拌使其溶解,制成透明溶液。作为有机模板,向其中加入25质量%的tmadaoh水溶液2.43g,进一步地加入胶体二氧化硅(日产化学公司制、snowtex-40)10.85g搅拌2小时,制成水热合成用原料混合物。该混合物的组成(摩尔比)为sio2/al2o3/naoh/koh/h2o/tmadaoh=1/0.018/0.02/0.08/100/0.04,sio2/al2o3=58。作为多孔支撑体,将株式会社则武制的氧化铝管bn1(外径6mm、内径4mm)切断为80mm的长度后,用超声波清洗机清洗,然后干燥使用。作为晶种,使用如下获得cha型沸石:以sio2/al2o3/naoh/koh/h2o/tmadaoh=1/0.033/0.1/0.06/20/0.07的凝胶组成(摩尔比)在160℃下进行2天水热合成晶化,将其过滤、水洗、干燥。晶种的粒径为0.3~3μm程度。将该晶种在水中分散为约1质量%的浓度,在其(cha晶种水溶液)中,将上述支撑体浸渍1分钟后,在100℃下干燥1小时附着晶种。附着的晶种的质量为约0.001g。将3根附着有晶种的支撑体沿垂直方向浸渍于装有上述水性反应混合物的teflon(注册商标)制内筒(200ml)中,密封高压釜,在180℃下,以静置状态在自生压力下加热72小时。经过规定时间后,放置冷却后,将支撑体-沸石膜复合物从反应混合物中取出,清洗后,在100℃下干燥3小时。将干燥后的膜复合物在空气中,用电炉在450℃下烧制10小时,500℃下烧制5小时。此时,从室温至450度的升温速度和降温速度均为0.5℃/分,从450度至500度的升温速度和降温速度均为0.1℃/分。基于烧制后的膜复合物的质量和支撑体的质量的差求得的支撑体上晶化的cha型沸石的质量为约0.279~0.289g。此外,烧制后的膜复合物的空气透过量为2.4~2.9cm3/分。下文中,将所制造的cha型沸石膜复合物称为“cha型沸石膜复合物3”。[参考例e3]<膜分离性能的评价>将参考例e2所述的cha型沸石膜复合物3的温度变更为100℃~250℃,以100sccm的流量流通12%氨/51%氮/37%氮的混合气体,获得的透过气体的氨的浓度以及氨/氢、氨/氮的渗透通量比如表28所示。可知将温度从150℃变为250℃时,温度越高,透过膜内的气体中的氨气浓度越低。此外,250℃下的氨的渗透通量为7.2×10-7[mol/(m2·s·pa)]。可认为这虽然是高于rho型和mfi型沸石膜复合物的渗透通量,但氨/氮或氨/氢的渗透通量比小,因而氨的透过选择性低,气体从沸石粒子间的空隙、缺陷中透过。【表28】表28100℃150℃200℃250℃透过气体的nh3浓度26%25%22%20%nh3/n2的渗透通量比111087nh3/h2的渗透通量比3321由以上结果可知,通过实施例e2和e5获得的本发明的沸石膜复合物,即使在如大于200℃的高温的温度条件下,也可稳定地从由包含氨且包含氢和/或氮的多种成分构成的气体混合物中,高透过度且高效地将氨高选择性地分离至透过侧。另一方面,可认为通过参考例e2获得的沸石膜复合物的情况下,在大于200℃的温度中,由于沸石产生热收缩,沸石粒子间产生空隙、缺陷,氨的透过选择性降低。即,可认为通过参考例e2获得的cha型沸石的300℃的热膨胀率相对于30℃的热收缩率的变化率为-0.30%,热膨胀率大,因而在如大于200℃的高温温度范围中,该沸石的热收缩引起沸石晶界中产生裂纹,气体穿过该裂纹而透过,因而氨分离性能降低。即可知,为了在大于200℃的温度范围中维持沸石膜复合物的高致密性,从由包含氨且包含氢和/或氮的多种成分构成气体混合物中高选择性且高透过性地分离氨,即使300℃的热膨胀率相对于30℃的热膨胀率的变化率仅以0.30%变化,膜性能也降低。相对于此,可知如实施例e2所述的沸石那样,300℃的热收缩率相对于30℃的热膨胀率的变化率为0.02%时,即使200℃的热收缩率的变化率为1.55%,产生明显的热收缩,也令人吃惊地,在大于200℃的温度范围中,氨可高选择性地透过。此外可知,如实施例e5、e8所述的沸石那样,300℃的热膨胀率相对于30℃的热膨胀率的变化率的绝对值为0.25%以内时,在大于200℃的温度范围中,氨可高选择性地透过。当前第1页1 2 3