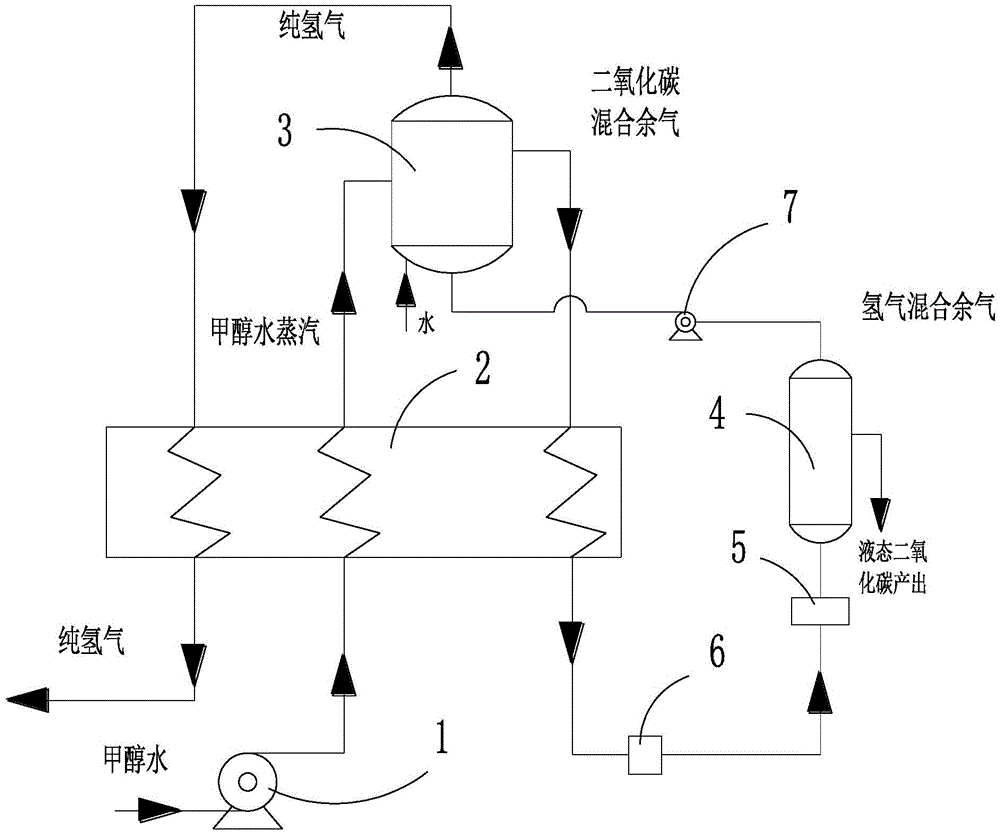
本实用新型涉及一种重整、分离一体式高压制氢系统。
背景技术:
:氢能源作为21世纪最理想的能源,作为汽车燃料,在低温下容易发动,而且对发动机的腐蚀作用小,可延长发动机的使用寿命。由于氢气与空气能够均匀混合,完全可省去一般汽车上所用的汽化器,从而可简化现有汽车的构造。更令人感兴趣的是,只要在汽油中加入4%的氢气。用它作为汽车发动机燃料,就可节油40%,而且无需对汽油发动机做多大的改进。氢燃料电池作为发电系统。无污染,燃料电池对环境无污染。它是通过电化学反应,而不是采用燃烧(汽、柴油)或储能(蓄电池)方式--最典型的传统后备电源方案。燃烧会释放像cox、nox、sox气体和粉尘等污染物。如上所述,燃料电池只会产生水和热。如果氢是通过可再生能源产生的(光伏电池板、风能发电等),整个循环就是彻底的不产生有害物质排放的过程。无噪声,燃料电池运行安静,噪声大约只有55db,相当于人们正常交谈的水平。这使得燃料电池适合范围更广,包括室内安装,或是在室外对噪声有限制的地方。高效率,燃料电池的发电效率可以达到50%以上,这是由燃料电池的转换性质决定的,直接将化学能转换为电能,不需要经过热能和机械能(发电机)的中间变换,因为多一次能源转化,效率就减少一次。目前氢能源加氢站的氢气的主要来源是用储能罐由外地运回,整个加氢站需要存储大量的氢气;研究发现,氢能源产业中的氢气包括四个环节,氢气制备、氢气储存、氢气运输、氢气添加(往氢能源车中加氢气),其中,氢气制备和氢气添加这两个环节目前比较安全,而氢气储存环节比较容易发生事故,氢气运输环节成本较高,这跟氢气的特性有关;目前新闻中经常会出现加氢站发生爆炸的问题和加氢费用高的原因。因此,为降低现在加氢站大量储存氢气的问题,缩短或者精简掉氢气运输环节的高成本,需要去重新设计一种加氢站系统。技术实现要素:本实用新型要解决的技术问题是:克服现有技术的不足,提供一种重整、分离一体式高压制氢系统,解决以往甲醇水蒸气的重整器、氢气分离、水煤气重整是三个独立的设备,致使制氢系统庞杂的问题。本实用新型解决其技术问题所采用的技术方案是:一种重整、分离一体式高压制氢系统,包括重整分离装置、三相换热装置、疏水器、水冷换热器以及二氧化碳液化装置;所述重整分离装置包括上反应腔和下反应腔,所述上反应腔和下反应腔连通,所述上反应腔填充第一催化填料,所述下反应腔内填充第二催化填料;所述上反应腔开设用于输入甲醇水蒸气的第一进口以及用于输出二氧化碳混合余气的第一出口,所述上反应腔内插入吸氢管,所述吸氢管对于上反应腔内的混合气体进行吸氢分离,并将吸附的氢气从吸氢管输出;所述下反应腔开设有用于输入氢气混合余气的第二进口;所述第一进口连接甲醇水蒸气进管,所述吸氢管出口连接纯氢气出管,第一出口连接二氧化碳混合余气出管,所述甲醇水蒸气进管、纯氢气出管以及二氧化碳混合余气出管均连接三相换热装置,所述二氧化碳混合余气出管依次连接疏水器、水冷换热器以及二氧化碳液化装置,所述二氧化碳液化装置连接氢气混合余气出管,所述氢气混合余气出管连接重整分离装置的第二进口,所述氢气混合余气出管上设置有用于提升管内氢气混合余气输送压力的气泵;所述甲醇水蒸气进管连接液态泵,所述液态泵的泵压为18~50mpa,所述水冷换热器连接水冷塔,所述水冷换热器作业温度在18~30.8℃。进一步的,所述吸氢管为铌管,第一催化填料为铜基填料或者锆基填料,第二催化填料为铜基填料或者锆基填料,所述上反应腔和下反应腔作业的温度为200~500℃。进一步的,所述吸氢管为钯膜管或钯合金膜管,第一催化填料为铜基填料或者锆基填料,第二催化填料为铜基填料或者锆基填料,所述上反应腔和下反应腔作业的温度为250~550℃。进一步的,所述纯氢气出管连接储氢罐,纯氢气在液态泵的泵压下送入储氢罐内,所述储氢罐连接加氢机,所述储氢罐连接加氢机。又一方面,一种高压制氢方法,采用上述的重整、分离一体式高压制氢系统,包括以下步骤:s1、液态泵将甲醇水送入甲醇水蒸气管进管,泵压为18~50mpa,甲醇水受热汽化成为甲醇水蒸气进入重整分离装置的上反应腔内,甲醇水蒸气在上反应腔进行重整反应生成氢气、二氧化碳和一氧化碳的混合气体,然后吸氢管对生成的氢气、二氧化碳和一氧化碳的混合气体行氢气分离;所述氢气、二氧化碳和一氧化碳的混合气体的气相组分为氢气65~75%、二氧化碳20~26%、0.3~3%一氧化碳;s2、吸氢管对氢气、二氧化碳和一氧化碳的混合气体进行分离,分离到的纯氢气从吸氢管输出被采集;剩余的二氧化碳混合余气从二氧化碳混合余气出管输出,二氧化碳混合余气经液态泵控制压力,水冷换热器控制二氧化碳混合余气的温度,然后将二氧化碳混合余气送入二氧化碳分离装置内进行二氧化碳液化分离;所述二氧化碳混合余气的气相组分为氢气25~45%、二氧化碳55~75%、水0~3%、0.3~3%一氧化碳;所述液态泵控制的压力为18~50mpa,水冷换热器控制的温度为18~30.8℃;s3、所述二氧化碳混合余气在二氧化碳分离器内制成液态二氧化碳和氢气混合余气,液态二氧化碳输出收集;所述氢气混合余气的组分为氢气65~75%、二氧化碳20~26%、一氧化碳3~9%;s4、将氢气混合余气送入重整分离装置的下反应腔内,配水制成重整混合气,根据一氧化碳的含量进行配水,配水比(一氧化碳:水)为1:1~20;将送入的氢气混合余气在下反应腔内配水重整成重整混合气,所述重整混合气的气相组分为氢气62~77%、二氧化碳22~27%、一氧化碳0.5~1.5%;以使所述重整混合气中氢气、二氧化碳、一氧化碳的比例,与氢气、二氧化碳和一氧化碳的混合气体中氢气、二氧化碳、一氧化碳的比例相接近;s5、重整混合气进入上反应腔内,与氢气、二氧化碳和一氧化碳的混合气体相混合,吸氢管对重整混合气与氢气、二氧化碳和一氧化碳的混合气体进行氢分离作业。进一步的,输出的纯氢气和二氧化碳混合余气均经过三相换热装置换热降温之后输出,所述甲醇水经过三相换热装置换热汽化为甲醇水蒸气。进一步的,所述甲醇水由天然气替换。本实用新型的有益效果是:本实用新型的高压制氢系统,将甲醇水蒸气重整、混合气体进行吸氢分离、氢气混合余气重整都集成在一个反应腔、同一个作业温度下进行,使实现甲醇水重整装置、氢分离装置、水煤气重整器一体化,优化整个制氢系统的布局结构,从而依靠该制氢系统可以做成小型的制氢设备。本实用新型制氢系统中,通过液态泵提供高压(18~50mpa)的制氢压力,使整个制氢系统在针对处理二氧化碳混合余气的时候,只需配置一个水冷换热器来控制二氧化碳混合余气在二氧化碳液化装置内的温度,二氧化碳混合余气在二氧化碳液化装置内的压力直接由液态泵从源头进行控制,使高压制氢系统相比低压制氢,可以省去一个空压机(低压制氢需要单独配置一个空压机来为二氧化碳混合余气提供液化工作的压力),相比中压制氢系统,可以由传统制冷机改为现在的水冷换热器来进行温度控制,通过水冷换热器和水冷塔来控制二氧化碳混合余气在进入二氧化碳分离器的作业温度,温度控制在18~30.8℃,水冷换热器和水冷塔控温的优点在于成本低、运行稳定可靠,适合将该制氢系统安装在常年室外温度在18~30.8℃的地区。本实用新型高压制氢方法,甲醇水蒸气重整分离与吸氢管的吸氢分离都在上反应腔内进行,分离的氢气被采集收集,分离出的二氧化碳混合余气进行回收处理,通过液态泵和制冷机控制针对二氧化碳混合余气进行分离液态二氧化碳的压力和温度,将二氧化碳混合余气通过二氧化碳液化装置分离出氢气混合余气和液态二氧化碳,液态二氧化碳可以存储起来,二氧化碳液化装置在分离的时候,通过控制压力和温度,控制了氢气混合余气中气相组分,使氢气混合余气中的二氧化碳摩尔比低于26%,使氢气混合余气为后道的重整混合气做好准备;氢气混合余气最后下反应腔内通过水煤气配水重整,将氢气混合余气中的将一氧化碳由原本的3~9%降为0.5~1.5%,重整混合气的气相组分:氢气62~77%、二氧化碳22~27%、一氧化碳0.5~1.5%;使重整混合气的气相组分与重整器制备的氢气、二氧化碳和一氧化碳的混合气体组分接近,使两者可以进行混合再次进入上反应腔内,与氢气、二氧化碳和一氧化碳的混合气体相混合,吸氢管再次进行氢气纯化分离制氢作业,实现对系统内的气体进行循环纯化,理论收率可达到100%,实现氢气收率≥95%。同时利用甲醇制氢的加氢站系统,由于氢针对的是直接消费客户,售价比工厂氢气节省了运费,所以对二氧化碳余气中的氢气进行回收,可实现理论100%的收率,实际大于90-99%,同时回收co2理论收率100%,实际收率90-99%。该工艺和加氢站结合,即可实现氢的高收率,同时更多回收co2,并且获得经济效益,真正实现既安全(减少高压储氢),又经济(由于甲醇运费比氢气低很多),还回收了co2,实现零排放。一方面,制氢是无害的,零态排放;另一方面,把二氧化碳减排做成甲醇,温室气体变成有用的甲醇液态燃料,拿甲醇液态燃料来做加氢站,太阳燃料的来源非常丰富,光、风、水、核能都可以,二氧化碳加氢制甲醇,甲醇可以运输,储存与运输都不是问题。整体来看就解决了制、储、运、装等问题,第一,液态阳光加氢站解决了高压加氢站的安全问题;第二,解决了氢的储存、运输、安全问题;第三,氢可以作为再生能源,实现全流程清洁的目标;第四,液态阳光加氢站可以回收二氧化碳,实现二氧化碳减排,不再进一步产生二氧化碳,二氧化碳就一直在那里边循环;五,液态阳光加氢站技术还可以扩展到其他的化学合成领域,也可以用在化学加氢上;第六,可以与加油站、加甲醇站多元共站。特别适合社区分布式热电联用的能源供给和现行的加油站。附图说明下面结合附图对本实用新型进一步说明。图1是重整、分离一体式高压制氢系统;图2是重整分离装置示意图;其中,1、液态泵,2、三相换热装置,3、重整分离装置,31、上反应腔,32、下反应腔,33、加热腔,34、吸氢管,4、二氧化碳液化装置,5、水冷换热器,6、疏水器,7、气泵。具体实施方式现在结合具体实施例对本实用新型作进一步的说明。这些附图均为简化的示意图仅以示意方式说明本实用新型的基本结构,因此其仅显示与本实用新型有关的构成。实施例一如图1图2所示,一种重整、分离一体式高压制氢系统,包括重整分离装置3、三相换热装置2、疏水器6、水冷换热器5以及二氧化碳液化装置4;所述重整分离装置3包括上反应腔31和下反应腔32,所述上反应腔31和下反应腔32连通,所述上反应腔31填充第一催化填料,所述下反应腔32内填充第二催化填料;所述上反应腔31开设用于输入甲醇水蒸气的第一进口以及用于输出二氧化碳混合余气的第一出口,所述上反应腔31内插入吸氢管34,所述吸氢管34对于上反应腔31内的混合气体进行吸氢分离,并将吸附的氢气从吸氢管34输出;所述下反应腔32开设有用于输入氢气混合余气的第二进口;所述第一进口连接甲醇水蒸气进管,所述吸氢管34出口连接纯氢气出管,第一出口连接二氧化碳混合余气出管,所述甲醇水蒸气进管、纯氢气出管以及二氧化碳混合余气出管均连接三相换热装置2,所述二氧化碳混合余气出管依次连接疏水器6、水冷换热器5以及二氧化碳液化装置4,所述二氧化碳液化装置4连接氢气混合余气出管,所述氢气混合余气出管连接重整分离装置3的第二进口,所述氢气混合余气出管上设置有用于提升管内氢气混合余气输送压力的气泵7;疏水器6用于去除二氧化碳混合余气中的水份,二氧化碳混合余气在控制水份之后在进行二氧化碳液化。所述甲醇水蒸气进管连接液态泵1,所述液态泵1的泵压为18~50mpa,所述水冷换热器5连接水冷塔,所述水冷换热器5作业温度在18~30.8℃。具体的,所述吸氢管34为铌管,第一催化填料为铜基填料或者锆基填料,第二催化填料为铜基填料或者锆基填料,所述上反应腔31和下反应腔32作业的温度为200~500℃。吸氢管34也可以采用钯膜管或钯合金膜管,第一催化填料为铜基填料或者锆基填料,第二催化填料为铜基填料或者锆基填料,所述上反应腔31和下反应腔32作业的温度为250~550℃。不管是采用铌管或钯膜管、钯合金膜管,其作用都是一样,都将反应腔内生成的氢气、二氧化碳和一氧化碳的混合气体进行吸氢分离,将纯氢气输出被采集,剩余的二氧化碳混合余气另外输出进行回收作业。所述纯氢气出管连接储氢罐,纯氢气在液态泵1的泵压下送入储氢罐内,所述储氢罐连接加氢机,所述储氢罐连接加氢机。该制氢系统,实现现场制氢,将制得的氢气直接存入储氢罐内,然后直接通过加氢机将制备出来的纯氢气加入氢气车内。作业时,甲醇水经过三相换热装置2汽化为甲醇水蒸气,甲醇水蒸气进入重整分离装置3的上反应腔31内,加热腔33加热控制上反应腔31内的温度,甲醇水蒸气在对应的温度和催化剂填料下进行催化反应,这是一个多组份、多反应的气固催化反应系统;反应方程为:ch3oh→co+2h2;(可逆反应)h2o+co→co2+h2;(可逆反应)ch3oh+h2o→co2+3h2;(可逆反应)2ch3oh→ch3och3+h2o;(副反应)co+3h2→ch4+h2o;(副反应);重整反应生成得氢气、二氧化碳和一氧化碳的混合气体。上反应腔31内的吸氢管34对氢气、二氧化碳和一氧化碳的混合气体进行吸氢作业,吸氢管34将混合气体中的氢气进行分离,纯氢气经吸氢管34输出之后被采集至储氢罐内,剩余的二氧化碳混合余气从上反应腔31的二氧化碳混合余气出管输出,二氧化碳混合余气然后经过三相换热装置2进行降温,在经过液压泵和水冷换热器5控制进入二氧化碳分离装置的压力和温度,然后二氧化碳混合余气二氧化碳分离装置进行液化分离,分离的液态二氧化碳被采集,分离的氢气混合余气送入重整分离装置3的下反应腔32内进行水煤气配水重整,氢气混合余气经过水煤气重整之后变为重整混合气,重整混合气的气相组分与重整反应生成得氢气、二氧化碳和一氧化碳的混合气体组分比例接近,重整混合气从下反应腔32内进入上反应腔31内,与氢气、二氧化碳和一氧化碳的混合气体进行混合,吸氢管34继续对这部分混合之后的气体进行吸氢分离,从而提升整个高压制氢系统的氢气收率。本实用新型的高压制氢系统,重整分离装置3集成甲醇水蒸气重整、氢气分离、水煤气重整三者功能,优化制氢系统,依靠该制氢系统可以做成小型的制氢设备。液态泵1提供的压力为2~5mpa,整个制氢系统处于高压状态下运行,制氢作业比较安全。本实用新型制氢系统中,通过液态泵1提供高压(18~50mpa)的制氢压力,使整个制氢系统在针对处理二氧化碳混合余气的时候,只需配置一个水冷换热器5来控制二氧化碳混合余气在二氧化碳液化装置4内的温度,二氧化碳混合余气在二氧化碳液化装置4内的压力直接由液态泵1从源头进行控制,使高压制氢系统相比低压制氢,可以省去一个空压机(低压制氢需要单独配置一个空压机来为二氧化碳混合余气提供液化二氧化碳工作的压力),相比中压制氢系统,可以由传统制冷机改为现在的水冷换热器5来进行温度控制,通过水冷换热器5和水冷塔来控制二氧化碳混合余气在进入二氧化碳分离器的作业温度,温度控制在18~30.8℃,水冷换热器5和水冷塔控温的优点在于成本低、运行稳定可靠,适合将该制氢系统安装在常年室外温度在18~30.8℃的地区。实施例二一种高压制氢方法,采用上述的重整、分离一体式高压制氢系统,包括以下步骤:s1、液态泵1将甲醇水送入甲醇水蒸气管进管,泵压为18~50mpa,甲醇水受热汽化成为甲醇水蒸气进入重整分离装置3的上反应腔31内,甲醇水蒸气在上反应腔31进行重整反应生成氢气、二氧化碳和一氧化碳的混合气体,这是一个多组份、多反应的气固催化反应系统;反应方程为:ch3oh→co+2h2;(可逆反应)h2o+co→co2+h2;(可逆反应)ch3oh+h2o→co2+3h2;(可逆反应)2ch3oh→ch3och3+h2o;(副反应)co+3h2→ch4+h2o;(副反应);然后吸氢管34对生成的氢气、二氧化碳和一氧化碳的混合气体行氢气分离;所述氢气、二氧化碳和一氧化碳的混合气体的气相组分为氢气65~75%、二氧化碳20~26%、0.3~3%一氧化碳;s2、吸氢管34对氢气、二氧化碳和一氧化碳的混合气体进行分离,分离到的纯氢气从吸氢管34输出被采集;剩余的二氧化碳混合余气从二氧化碳混合余气出管输出,二氧化碳混合余气经液态泵1控制压力,水冷换热器5控制二氧化碳混合余气的温度,然后将二氧化碳混合余气送入二氧化碳分离装置内进行二氧化碳液化分离;所述二氧化碳混合余气的气相组分为氢气25~45%、二氧化碳55~75%、水0~3%、0.3~3%一氧化碳;所述液态泵1控制的压力为18~50mpa,水冷换热器5控制的温度为18~30.8℃;s3、所述二氧化碳混合余气在二氧化碳分离器内制成液态二氧化碳和氢气混合余气,液态二氧化碳输出收集;所述氢气混合余气的组分为氢气65~75%、二氧化碳20~26%、一氧化碳3~9%;使氢气混合余气气相组分中的二氧化碳摩尔比控制在20~26%,二氧化碳液化装置4在工作时压力与温度的选择参见下表:方案压力(mpa)温度(℃)方案11818方案22525方案35030.8s4、将氢气混合余气送入重整分离装置3的下反应腔32内,配水制成重整混合气,根据一氧化碳的含量进行配水,配水比(一氧化碳:水)为1:1~20;水煤气重整反应公式为:co+h2o→co2+h2;将送入的氢气混合余气在下反应腔32内配水重整成重整混合气,所述重整混合气的气相组分为氢气62~77%、二氧化碳22~27%、一氧化碳0.5~1.5%;以使所述重整混合气中氢气、二氧化碳、一氧化碳的比例,与氢气、二氧化碳和一氧化碳的混合气体中氢气、二氧化碳、一氧化碳的比例相接近;s5、重整混合气进入上反应腔31内,与氢气、二氧化碳和一氧化碳的混合气体相混合,吸氢管34对重整混合气与氢气、二氧化碳和一氧化碳的混合气体进行氢分离作业。具体的,输出的纯氢气和二氧化碳混合余气均经过三相换热装置2换热降温之后输出,所述甲醇水经过三相换热装置2换热汽化为甲醇水蒸气。本实施例中甲醇水也可以有天然气替换,通过天然气制氢得到氢气、二氧化碳和一氧化碳的混合气体。实用新型的高压制氢方法,依托实施例一中的重整、分离一体式高压制氢系统,将甲醇水作为制氢原料,液态泵1在源头提供高压(18~50mpa)将甲醇水泵入重整分离装置3的上反应腔31内,反应生成氢气、二氧化碳和一氧化碳的混合气体,然后吸氢管34对氢气、二氧化碳和一氧化碳的混合气反应吸氢,纯氢气可以直接输出采集,制氢效率大大提高。然后将产生的二氧化碳混合余气输送,经液态泵1和水冷换热器5控制二氧化碳混合余气在二氧化碳分离装置内的压力和温度,使其中的二氧化碳液化分离,控制分离出来的氢气混合余气的组分,使氢气混合余气中的二氧化碳摩尔比低于26%,使氢气混合余气为后道的重整混合气做好准备;氢气混合余气再送入重整分离装置3的下反应腔32内,下反应腔32和上反应腔31的工作温度以及吸氢管34作业温度由加热腔33统一控制,氢气混合余气通过水煤气配水重整,将氢气混合余气中的一氧化碳由原本的3~9%降为0.5~1.5%,重整混合气的气相组分:氢气62~77%、二氧化碳22~27%、一氧化碳0.5~1.5%;使重整混合气的气相组分与重整器制备的氢气、二氧化碳和一氧化碳的混合气体组分接近,重整混合气在从下反应腔32直接进入上反应腔31内,与氢气、二氧化碳和一氧化碳的混合气体一起混合,再次经吸氢管34进行循环吸氢分离,实现对系统内的气体进行循环纯化,理论收率可达到100%,实现氢气收率≥95%。以上述依据本实用新型的理想实施例为启示,通过上述的说明内容,相关工作人员完全可以在不偏离本项实用新型技术思想的范围内,进行多样的变更以及修改。本项实用新型的技术性范围并不局限于说明书上的内容,必须要根据权利要求范围来确定其技术性范围。当前第1页12