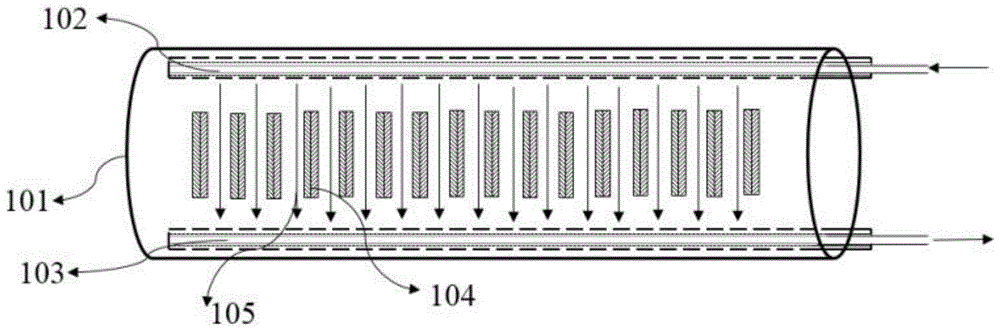
本发明涉及技术太阳能电池
技术领域:
,特别是涉及适用于高温扩散管的管用进气排气装置。
背景技术:
:目前,perc+se技术是最为成熟高效电池技术路线之一,并且已经实现大规模量产,其中扩散是激光选择性发射极(selectiveemitterse)技术的核心工序之一。激光se技术,利用硅片表面沉积磷硅玻璃或硼硅玻璃中掺杂源,在激光热效应作用下,实现掺杂源再分布。当前,晶硅电池扩散均采用管式扩散方式,其扩散均匀性通过调整工艺时间、气体流量和温度三个因素调整,同时与炉管进气、排气方式、位置也有很大关系。传统的高温扩散管,单纯采用炉口进气炉尾抽气、炉尾进气炉口抽气或者喷淋方式进气炉中抽气等方式,其进气排气管均为单层管,此类设计,进气或者排气气流方向均垂直于硅片在炉管中放置,在扩散工艺过程中炉内会产生横向气流,上述横向气流造成炉管内不同空间位置掺杂气体气流速度不稳定,产生气流扰动。在此情况下,硅片表面掺杂气体反应分布不均匀,对整个炉管片内和片间方阻均匀性产生不利影响,同时也会影响硅片表面磷硅玻璃或硼硅玻璃厚度和掺杂源浓度的分布均匀性,进而影响下一步激光se后方阻。此外传统高温扩散管还存在其他问题,其表现为(1)仅单纯关注进气管,而排气管依然单层管的方式,但这种方式也会造成横向气流扰动;(2)上述单层进气管对掺杂气体无法混合均匀,影响扩散气体均匀分布;(3)进气管开孔不规则导致进气管、排气管不通用,造成成本增加。技术实现要素:针对上述现有技术的缺点,本发明的目的是提供一种能保证扩散气体在炉管内均匀和稳定分布的管用进气排气装置。为实现上述目的,本发明的技术方案如下:管用进气排气装置,包括进气管和排气管,所述进气管和排气管分布在炉管内并紧靠炉内壁,所述进气管和排气管以布置在炉管内部的硅片为中心对称分布;所述进气管和排气管均为结构相同的多层套管结构,所述多层套管结构由至少两根气管由内向外同轴心套接构成;在每层气管上开设若干气孔。优选的,每层气管上的若干气孔均沿气管轴向或周向并排布置成一排或一排以上。优选的,相邻层间气管上的若干气孔互为错位布置。优选的,在多层套管结构中相邻气管的气孔孔径自内层向外层呈逐渐递减。优选的,在多层套管结构中每层气管上各相邻气孔的孔间距自内层向外层呈逐渐递减。优选的,在多层套管结构中相邻气管中气孔的开孔位置互为相反。优选的,在多层套管结构位于最外层气管上的若干气孔在周向面沿轴向并排布置成1~3排。优选的,若最外层气管上气孔沿周向并排布置成3排,在左右最外侧两排气孔中,位于左右相邻的两个气孔的中心相交线之间形成夹角ɑ,所述夹角ɑ为50°~100°。本发明的有益效果如下:与现有技术相比,本发明重新设计了进气管和排气管,进气管和排气管采用多层套管结构,多层套管结构的内部空间使扩散源气体和反应残留废气可在多层套管结构中充分混合均匀后进入或排出炉管。另一方面各层气管中气孔的位置、角度、孔径、孔距、孔向均调整,从而实现进入炉管的气流方向稳定性和均匀性。进气管、排气管对称式设计保证保证气体为垂直于硅片排列方向流动,防止产生横向气体流影响整个炉管空间内硅片表面磷硅玻璃或硼硅玻璃厚度均匀性和浓度分布。确保工艺气体(磷源或硼源)在硅片表面沉积反应的更均匀,利于后续se激光工序的稳定性附图说明图1示出了本发明实施例一种管用进气排气装置的应用图。图2示出了图1的剖面示意图。图3示出了本发明实施例一种管用进气排气装置中进气管或排气管的示意图。图4示出了图3的剖面示意图。图5示出了本发明实施例一种管用进气排气装置中进气管或排气管最外层气孔分布图。其中:101、炉管;102、进气管;103、排气管;104、硅片;201、第一气孔;202、第二气孔;203、第三气孔;204、第一孔间距;205、第二孔间距;206、第三孔间距;208、夹角;208、外层管;209、中层管;2010、内层管。具体实施方式为了使本发明的目的、技术方案及优点更加清楚明白,以下结合附图及实施例,对本发明进行进一步详细说明。应当理解,此处所描述的具体实施例仅仅用以解释本发明,并不用于限定本发明。下面结合附图对本发明请求保护的管用进气排气装置,以用于为例进行详细介绍说明。如图1和图2所示的一种管用进气排气装置,包括进气管102和排气管103,进气管102和排气管103分布在炉管101内并紧靠炉内壁,进气管102和排气管103以布置在炉管101内部的硅片104为中心对称分布。如图1所述,上述进气管102和排气管103对称式设计保证气体如图1箭头所示方向垂直于硅片104排列方向流动,防止产生横向气体流影响整个炉管空间内硅片表面磷硅玻璃或硼硅玻璃厚度均匀性和浓度分布。进气管102和排气管103均为结构相同的多层套管结构,多层套管结构由至少两根以上的气管由内向外同轴心套接构成;优选的,如图3、图4所示,本实施例中进气管102或排气管103均采用三层套管方式,在每层气管上开设若干气孔,每一层气管上的若干气孔均沿气管轴向或周向并排布置成一排或一排以上,如图3所示,相邻层间气管上的若干气孔互为错位布置。如图3所示,在多层套管结构中相邻气管的气孔孔径自内层向外层呈逐渐递减。在多层套管结构中每层气管上各相邻气孔的孔间距自内层向外层呈逐渐递减。如图3所示,优选的,本实施例三层套管中内层管2010的第一气孔201的孔径为4~5mm,内层管2010中各第一气孔201之间的第一孔间距204为40~50mm,内层管2010中第一气孔201的孔径优选为5mm,第一孔间距优选为45mm;中层管209中的第二气孔202的孔径为2~4mm,中层管209中各第二气孔202之间的第二孔间距205为30~40mm,中间管209中第二气孔202的孔径优选为3.5mm,第二孔间距优选为35mm,外层管208中各第三气孔203的孔径为0.5~1mm,外层管208中各第三气孔203之间的第三孔间距206为10~20mm,外层管208中第二气孔203的孔径优选为0.8mm,第三孔间距206优选为15mm。(理论上内层管和中层管可以选择相同孔直径)。如图4所示,在多层套管结构中相邻气管中气孔的开孔位置互为相反。优选的,在本实施例三层套管结构中,外层管208上的各第三气孔203位于外层管208的下半部分;中层管209上的各第二气孔202位于中层管209的上半部分;内层管2010中第一气孔201位于内层管2010的下半部分。优选的,在本实施例的外层管208中,如图4、图5所示,外层管208上的第三气孔203在周向面沿轴向分布成三排,如图4所示,在左右最外侧两排第三气孔203中,在左右相邻的两个第三气孔203的中心相交线之间形成夹角ɑ,夹角ɑ为50°~100°,本实施例中优选的角度为85°。单晶硅片经过清洗制绒后,进入炉管101,按照设定扩散工艺进行扩散工序处理。待扩散完毕后,将放置于炉管内五个不同位置的硅片(炉口、炉中左、炉中、炉中右、炉尾)取出测试硅片扩散方阻,然后进行se激光扫描加工,测试其方阻变化。表1和表2均为采用同样的高温扩散管和工艺参数进行扩散后的方阻测试结果。区别在于表1采用常规炉口进气炉尾排气扩散管,表2采用本实施例中管用进气排气装置,由表1和表2可以得出,采用本实施例中管用进气排气装置的整体扩散方阻均匀性更佳,不同炉管位置扩散片激光处理前后方阻差值更为稳定,即实现了表面磷硅玻璃或硼硅玻璃沉积的均匀性,便于后续激光se方阻的稳定性监控。表1常规炉口进气炉尾排气扩散管进行扩散和激光后方阻变化炉尾炉中左炉中炉中右炉口扩散后124.00125.52124.78120.86122.14激光后85.1683.1679.7473.673.24差值38.8442.3645.0447.2648.90表2本发明设计进气排气装置扩散管进行扩散和激光后方阻变化炉尾炉中左炉中炉中右炉口扩散后127.3129.16127.78129.16128.54激光后84.0483.783.8484.4884.11差值43.2645.4643.9444.6844.43以上所述实施例的各技术特征可以进行任意的组合,为使描述简洁,未对上述实施例中的各个技术特征所有可能的组合都进行描述,然而,只要这些技术特征的组合不存在矛盾,都应当认为是本说明书记载的范围。以上所述实施例仅表达了本发明的几种实施方式,其描述较为具体和详细,但并不能因此而理解为对发明专利范围的限制。应当指出的是,对于本领域的普通技术人员来说,在不脱离本发明构思的前提下,还可以做出若干变形和改进,这些都属于本发明的保护范围。因此,本发明专利的保护范围应以所附权利要求为准。当前第1页12