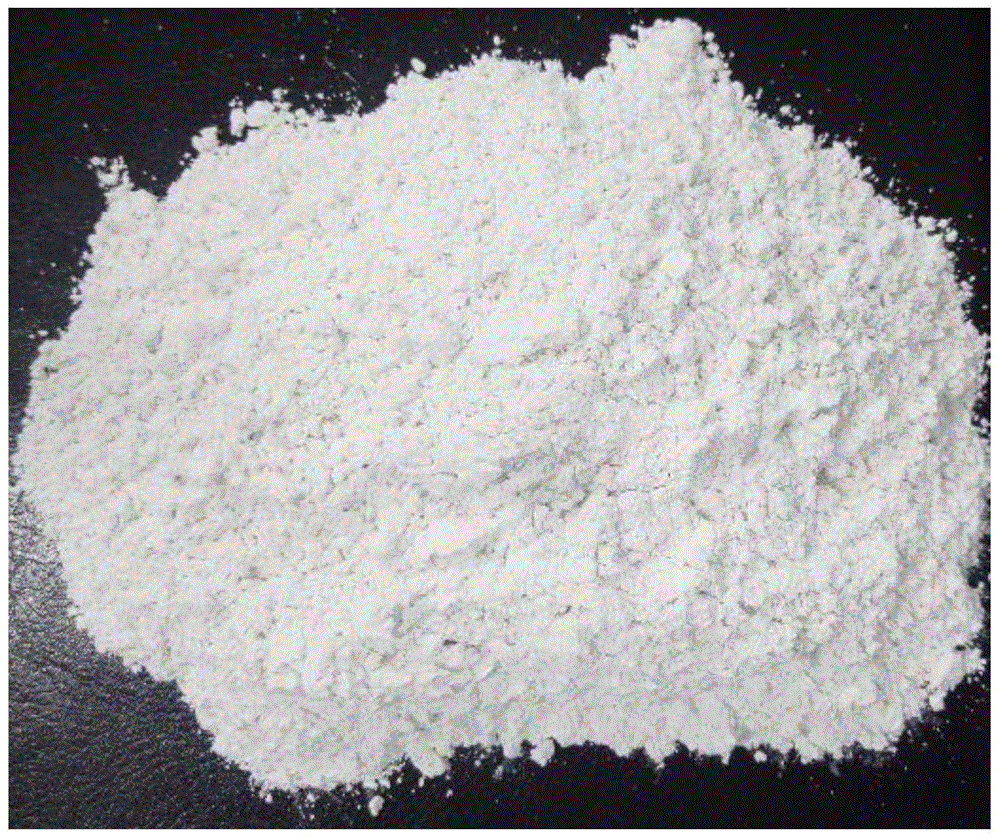
本发明属于建筑材料
技术领域:
,涉及一种具有高耐磨性的水泥混凝土面层材料及其制备方法。
背景技术:
:随着国民经济的不断增长,我国工业化、城镇化和机动化进程不断推进,交通运输行业进入高速发展阶段。与此同时,配套的公共交通基础设施建设也进入蓬勃发展时期,道路网线工程逐步完善。水泥混凝土路面属于刚性路面,与普通沥青混凝土路面相比,具有承载力高、稳定性好、使用寿命长、平整度保持期长、环境污染小以及养护成本低等优点。因此,水泥混凝土路面被广泛应用于高速公路、城市道路、广场、停车场、飞机跑道和车站码头等。水泥混凝土路面不仅要求强度高、脆性低、抗冲击韧性好,同时还应具备优良的耐磨性能。水泥混凝土路面的耐磨性主要取决于其面层材料的耐磨性,而面层材料的耐磨性直接影响到水泥混凝土路面的正常使用、安全性及耐久性。目前,主要通过添加矿物掺合料、增强材料以及改善道路工程的施工工艺来提高水泥混凝土路面的耐磨性能。加入粉煤灰、矿渣、硅粉以及石灰石粉等矿物掺合料,通过形态效应、填充效应以及火山灰活性效应来提高水泥混凝土面层的耐磨性能。此外,将钢纤维、玻璃纤维、玄武岩纤维以及合成纤维等增强材料加入到水泥混凝土中,通过纤维的应力传递和裂缝桥联作用来提高耐磨性,实现水泥混凝土路面优良的路用性能。近年来,伴随纳米技术的快速发展,包括纳米二氧化硅、纳米二氧化钛、纳米二氧化锆等在内的纳米颗粒也被用来提高水泥混凝土路面的性能,这些纳米颗粒通过成核效应和颗粒填充效应改善水泥混凝土的水化作用和耐久性。然而,现有矿物掺合料对提升水泥混凝土面层耐磨性的增强作用有限;纤维原材料成本相对较高,难分散,施工困难,特别地,钢纤维用于道路工程面层中易锈蚀且对车辆轮胎损害大,玻璃纤维有抗碱耐久性问题、以及用于人行道面层对于人体呼吸系统损坏较大的环保问题;而纳米颗粒的成本较高,阻碍其在工程应用中推广。相比上述矿物掺合料、纤维和纳米颗粒来说,碳酸钙晶须机械强度高、耐磨耐热性能好、无毒、原材料来源广泛且生产成本较低,具有较高的性价比。因此,碳酸钙晶须已被广泛应用于塑料、摩擦材料、造纸、涂料以及医药等领域,是当前最具潜力且可大规模应用在水泥混凝土面层中的改性材料。技术实现要素:为了克服现有技术的不足,本发明提出了一种具有高耐磨性的水泥混凝土面层材料及其制备方法,可解决现有水泥混凝土面层易开裂、耐磨性差,导致其使用寿命缩短的问题,同时可有效降低成本。本发明的技术方案是:一种具有高耐磨性的水泥混凝土面层材料,包括碳酸钙晶须和水泥砂浆;其中,水泥砂浆包括水泥、掺合料、水、石英砂、减水剂和工业消泡剂。各组份的重量份数如下:碳酸钙晶须15~30份;水泥381~387份;掺合料(f类粉煤灰)43份;石英砂212~215份;水127~129份;减水剂2~4份、工业消泡剂2份。进一步特征,所述的碳酸钙晶须为针状纤维,长度为20~30μm,直径为1~2μm,长径比为20~30。进一步特征,所述水泥为普通硅酸盐水泥42.5r。进一步特征,所述石英砂的粒径为20~120目。上述的具有高耐磨性的水泥混凝土面层材料的制备方法,步骤如下:s01按水泥混凝土面层材料所含有的组份及各自的重量份数进行配料;s02将碳酸钙晶须加入到1/2的水和减水剂混合液中,通过超声分散5分钟,获取碳酸钙晶须悬浮液;s03首先将水泥、掺合料和石英砂加入到砂浆搅拌机中干拌60~120秒;其后加入碳酸钙晶须悬浮液,继续搅拌60~120秒;之后分2次加入剩余1/2的水和减水剂混合液,继续搅拌120~180秒;最后加入工业消泡剂搅拌60秒,得到新拌混合物;s04将新拌混合物浇筑、振捣、成型及养护。其中,步骤s02中,所述减水剂属聚羧酸类高效减水剂;超声分散采用超声波细胞破碎仪。步骤s03中,所述的工业消泡剂可以为磷酸三丁酯。步骤s04中,所述养护条件为温度不低于5℃,湿度不低于95%,养护时间28天。本发明将碳酸钙晶须加入到水泥基体中,不仅可以发挥其微观尺度上的填充作用,同时具有高抗拉强度、高弹性模量以及大长径比的碳酸钙晶须还能够在水泥基体中起到微纤维作用,通过晶须拔出、晶须拔断、裂纹偏转以及晶须桥联等一系列增强机制,可有效抑制水泥基体中微裂缝的产生,实现对水泥基体的增强增韧。另外,除上述作用之外,碳酸钙晶须在水泥基体中还表现出物理稀释作用,降低水泥的水化热、非蒸发水量和氢氧化钙(ch)晶体量;其次,碳酸钙晶须的加入能体现晶核作用,使水化硅酸钙(c-s-h)凝胶和氢氧化钙(ch)以碳酸钙晶须作为晶核生长;再次,碳酸钙晶须在水泥基体中能够起到化学催化作用,生成单碳铝酸盐,消耗多余的铝相,减少高硫型水化硫铝酸钙(aft)向单硫型水化硫铝酸钙(afm)的转化,改善孔隙结构,进而提高水泥基体的强度。此外,碳酸钙晶须可以优化ch晶体在水泥基体中的取向,缩小ch晶体生长的空间,提高水泥基体的结构密实度。此外,针状的碳酸钙晶须具有较大的比表面积,在拌合过程中,大量的碳酸钙晶须可相互搭接最终形成网状结构,能显著调节水泥基材料拌合物的黏度。特别地,良好的耐摩擦和耐热性能进一步支持碳酸钙晶须作为水泥混凝土面层的耐磨改性材料。最后,碳酸钙晶须的原材料来源广泛,生产技术成熟,成本低廉,本技术可为我国碳酸钙矿产资源的大规模开发利用开辟新途径。附图说明图1(a)为碳酸钙晶须的宏观形貌。图1(b)为碳酸钙晶须的微观形貌。图2为实施例1~3中碳酸钙晶须的xrd图。图3为实施例1~3中样本生产流程图;图4为实施例1~3中样本的单位面积磨损量;图5为实施例1~3中样本的立方体抗压强度。具体实施方式下面结合附图和实施例来说明本发明的具体实施方式,但以下实施例只是用来详细说明本发明,并不以任何方式限制本发明的范围。以下实施例中所涉及的一些步骤或方法,如无特殊说明,均为本领域的常规方法,所涉及的材料、仪器设备,如无特别说明,均为常规材料和仪器设备。实施例1本实施例所用的碳酸钙晶须如图1所示,原材料的组份重量配比为:30份碳酸钙晶须、381份普通硅酸盐水泥、43份掺合料、212份石英砂、127份水以及4份减水剂和2份消泡剂。样本的生产过程如图3所示,选用sj-15型砂浆搅拌机,搅拌叶转速80±4r/min,搅拌筒转速60±2r/min。首先,将127份水和4份聚羧酸类高效减水剂混合搅拌30秒后均匀分成两份;将30份碳酸钙晶须加入到上述1/2减水剂混合溶液中搅拌30秒;对上述混合溶液超声分散5分钟,形成碳酸钙晶须悬浮液;将称量过的原材料,包括381份普通硅酸盐水泥、43份掺合料和212份石英砂加入砂浆搅拌机中,均匀搅拌60秒;接着将碳酸钙晶须悬浮液加入上述干拌混合料中,继续搅拌60秒;之后将剩余的1/2减水剂混合溶液在60秒内分2次加入到上述拌合料中,继续搅拌60秒;最后,加入2份工业消泡剂,搅拌60秒后获取新拌水泥混凝土面层材料。最后,浇筑成150mm×150mm×150mm的立方体样本,在温度为20±3℃的水中养护28天,获得具有高耐磨性的水泥混凝土面层材料。按照《公路工程水泥及水泥混凝土试验规程》jtge30-2005和《水泥胶砂耐磨性试验方法》jc/t421-1991中的规定,采用带有花轮磨头的tms-04型水泥胶砂/混凝土耐磨试验机进行耐磨试验。首先,将实施例1得到的立方体样本表面擦干,并放入空气中自然干燥24小时,在60℃的烘箱中烘干4小时后冷却至室温,进行耐磨试验。然后,将样本固定到耐磨试验机的水平托盘上,并在200n的荷载作用下预磨30转,称量原始质量m1;接着将样本继续固定到耐磨试验机的水平托盘上,在200n的荷载作用下再磨60转,称量样本质量m2。整个试验的过程中采用吸尘器对样本磨损面磨掉的粉尘及时清理。根据下式计算样本单位面积磨损量g:式中:g为样本单位面积上的磨损量,kg/m2;m1为样本经历30转预磨损后的质量,即样本的原始质量,kg;m2为样本经历60转磨损后的质量,kg。实施例2~实施例3与实施例1相比,实施例2~实施例3的区别仅在于各组份的重量份数不同,详见表一。碳酸钙晶须水泥掺合料石英砂水减水剂消泡剂对比样本03934321813122实施例2203854321412832实施例3153874321512932通过实施例2和实施例3制备得到的试验样本单位面积的磨损量结果如图4所示。可以看到,各试验样本的单位面积磨损量均小于对比样本,且明显小于《公路水泥混凝土路面施工技术细则》jtg/tf30-2014中关于一级公路面层磨损量的规定,说明该试验样本具有良好的耐磨性。对经历耐磨试验后的样本进行立方体抗压试验,试验结果如图5所示。可以看出,与对照样本相比,试验样本具有更高的抗压强度。本发明的一种高耐磨性水泥混凝土面层材料由于加入了碳酸钙晶须使其具有很好的填充、抗裂以及增强增韧作用,同时具备高耐磨性能。因此,有很好的市场推广价值。对所公开实施例的上述说明,使本领域技术人员能够实现或使用本发明。对这些实施例的多处修改对本领域技术人员来说是显而易见的,本文中所定义的一般原理可以在不脱离发明的精神或范围的前提下,在其它实施例中实现。因此,本发明将不限制于本文所显示的这些实施例,而是要符合与本文公开原理和新颖特点相一致的最宽范围。当前第1页12