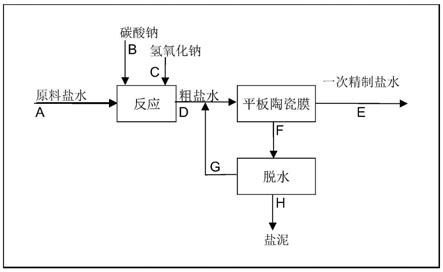
[0001]
本发明涉及一种盐水的精制方法,尤其是涉及一种离子膜烧碱一次精制盐水精制的方法。
背景技术:[0002]
采用饱和氯化钠水溶液生产烧碱是一种成熟的技术,自上世界八十年代中期离子膜制碱技术在中国氯碱行业成功应用以来,中国的氯碱行业无论是技术和设备均进步神速,产能更是高居全球第一。随着技术的不断进步,获得高品质盐水、降低氯化钠原料成本、降低盐水精制成本、降低电解电耗、延长离子膜寿命也就成了氯碱行业各生产厂家的目标。
[0003]
离子膜烧碱对进一次盐水有着严格的要求,如钙镁离子≤1mg/l、悬浮物≤1mg/l等。一次盐水精制主要是除钙镁离子和悬浮物,整个精制过程是在碱性条件下进行,要求氢氧化钠过碱量:0.1~0.3g/l,碳酸钠过碱量:0.3~0.5g/l,目前的一次盐水精制工艺有澄清+砂滤+碳素管过滤器(预涂a纤维素;浮上澄清桶预处理+ptfe膜过滤器;粗过滤+管式陶瓷膜过滤器等。
[0004]
由于原料盐中钙镁杂质、水不溶物的存在,没有预处理的膜过滤盐水精制在中国氯碱一直无法实施,上世纪末推出的浮上澄清桶预处理+ptfe膜过滤工艺对中国氯碱一次盐水品质的提高起到了很好的推动作用,大部分氯碱用户都选择了浮上澄清桶预处理+ptfe膜过滤工艺进行一次盐水精制,但随着时间的推移,浮上澄清预处理器因造价高、防腐难度大等原因已经制约了一次盐水ptfe膜过滤精制的技术进步。
[0005]
曾有企业对氯碱离子膜烧碱一次盐水采用管式陶瓷膜过滤,在经历加入精制剂反应、采用板框压滤机作为管式陶瓷膜预处理的最初应用,逐渐发展为用粗过滤代替板框压滤机,再经过陶瓷膜过滤的一次盐水精制工艺,但由于管式陶瓷膜内径较小,过高的ss进入膜管以造成膜管堵塞,必须降低进膜盐水的含固量,因此采用板框压滤机或其他方式的粗过滤就显得尤为必要。
[0006]
取消预处理,饱和盐水经过化学反应后直接才有膜过滤精制就成了氯碱企业一次盐水精制的目标,但是到目前为止,还没有企业能实现这一点。
技术实现要素:[0007]
本发明的目的就是为了克服上述现有技术存在的缺陷而提供一种离子膜烧碱一次精制盐水精制的方法,适于氯碱现有生产现状、取消预处理、直接膜分离并提高盐水质量。
[0008]
本发明的目的可以通过以下技术方案来实现:一种离子膜烧碱一次精制盐水精制的方法,本方法不采用任何形式的预处理设备,在饱和盐水中通过加入碳酸钠与钙离子反应形成碳酸钙,加入氢氧化钠与镁离子反应形成氢氧化镁,直接采用平板陶瓷膜过滤得到满足离子膜烧碱二次盐水精制要求的一次精盐水,其中钙镁离子≤1mg/l、悬浮物≤1mg/l。
[0009]
所述的方法具体包括以下步骤:
[0010]
(1)将固体盐溶解在配水中配制成原料盐水a,该原料盐水a为饱和盐水,各个组分的浓度如下:氯化钠305
±
5g/l,硫酸钠7.4~15g/l,ca
2+
5~2000mg/l,mg
2+
5~200mg/l;
[0011]
其中采用的固体盐包括摊晒的海盐、内陆地区的湖盐、真空制盐装置生产的精制盐,或其它方式获得的固体盐。
[0012]
配水是将离子膜烧碱生产产生的淡盐水、冷凝水、盐泥滤清液或其他杂水混合在一起,配制成不饱和的氯化钠盐水用于化盐饱和。
[0013]
原料盐水a是饱和的地下卤水,或通过其它方式获得的饱和氯化钠盐水。
[0014]
原料盐水a在化盐池中配制,化盐池采用砼结构、或玻璃鳞片防腐结构。
[0015]
(2)在原料盐水a中加入精制剂碳酸钠溶液b和氢氧化钠溶液c进入反应槽,进行反应除钙镁反应,得到粗盐水d;
[0016]
粗盐水d的各个组分的浓度如下:氯化钠305
±
5g/l,硫酸钠7.4~15g/l,ca(oh)25~4000mg/l,mg(oh)
2 5~500mg/l,ss5~5000mg/l;
[0017]
碳酸钠溶液b采用工业级碳酸钠和工业水配制,其质量浓度为5~15%;,避免因碳酸钠浓度低造成氯化钠浓度降低,也避免因碳酸钠浓度高造成的碳酸钠在管道中结晶堵塞殊荣管道;
[0018]
氢氧化钠溶液c采用离子膜烧碱出电槽的氢氧化钠溶液,其质量浓度为30~32%,避免氢氧化钠浓度过低造成的粗盐水氯化钠浓度降低。
[0019]
碳酸钠的加入量由反应后的碳酸钠残余量控制,碳酸钠过碱量为0.3~0.6g/l;
[0020]
氢氧化钠的加入量由反应后的氢氧化钠的残余量控制,氢氧化钠过碱量为0.1~0.3g/l;
[0021]
所述的除钙镁反应的反应时间由碳酸钠与钙离子的反应时间决定,优选的反应时间≥1小时;
[0022]
反应器为带有顶部加药与机械搅拌的反应器,其结构形式为圆筒式结构,反应器内液体自流进入膜池。优选的采用二个反应器,反应器之间用管道连接,下进上出,粗盐水自反应器1下部进入,自上部流出经管道流入反应器2下部,再自反应器2上部流出经管道流入膜池,避免因盐水进入反应器后钙离子与碳酸钠尚未反应就出反应器的短路问题,机械搅拌,搅拌器安装在反应器顶部。
[0023]
(3)通过除钙镁反应后得到的粗盐水d,自流进入平板陶瓷膜分离膜池,通过抽吸泵负压抽吸,碳酸钙、氢氧化镁、泥沙等水不溶物被截留在平板陶瓷膜的表面,并被气擦洗形成的循环盐水流带离平板陶瓷膜表面,盐水透过平板陶瓷膜得到一次精制盐水e;
[0024]
一次精制盐水e的各个组分的浓度如下:
[0025]
氯化钠305
±
5g/l,硫酸钠7.4~15g/l,钙镁离子≤1mg/l、悬浮物≤1mg/l;
[0026]
所述的平板陶瓷膜的孔径为0.05~0.1微米,材质为球磨α-al2o3,孔隙率>20%,结构形式为平板式;
[0027]
平板陶瓷膜采用负压抽吸、死端过滤,过滤压力0.01~0.1mpa,气擦洗及特殊结构的膜堆可使盐水在膜堆内外循环流动,形成膜表面的错流运动,防止盐泥在膜表面堆积,富集的盐泥与部分盐水进入污泥槽;
[0028]
(4)被气擦洗形成的盐水循环流带离膜表面的碳酸钙、氢氧化镁、盐泥沉积在膜池底部的泥斗中,定期排出盐泥浆f至渣池:
[0029]
盐泥浆f的各个组分的浓度如下:氯化钠305
±
5g/l,硫酸钠7.4~15g/l,ss≤1~5%;
[0030]
(5)盐泥浆f经渣浆泵打入污泥脱水设备脱水,得到滤清液g和盐泥h,盐泥脱水的滤清液g返回平板陶瓷膜膜池;
[0031]
所述的污泥槽的盐泥渣浆液用渣浆泵打入污泥脱水设备,污泥脱水设备为板框压滤机、叠螺机、真空过滤机、带式过滤机等,优选的为板框压滤机。压滤机的底流返回膜池;板框压滤机排出的盐泥多为碳酸钙和氢氧化镁固体;
[0032]
优选的,是进入平板陶瓷膜的盐水过碱量控制,需保持进入膜池的盐水为碱性,氢氧化钠为0.1~0.3g/l;氢氧化钠低于0.1g/l将无法保证镁离子低于1mg/l,氢氧化钠超过0.3g/l将增加运行费用,不经济。
[0033]
优选的碳酸钠为0.3~0.6g/l;碳酸钠低于0.3g/l将无法保证镁离子低于1mg/l,碳酸钠超过0.6g/l将增加运行费用,同样不经济。
[0034]
优选的精制盐水e进入一次盐水精制系统的精盐水槽。
[0035]
与现有技术相比,本发明具有以下有益效果:
[0036]
(1)无论是海盐、湖盐、精制盐还是卤水都存在一定量的钙镁杂质,盐水精制的主要目的就是去除钙镁杂质,钙镁杂质形成的碳酸钙和氢氧化镁为水不溶物,管式陶瓷膜属于內滤方式,粗盐水直接进入膜道,而膜道细小,对进入膜道的水不溶物有浓度要求(一般ss<100mg/l),因而管式陶瓷膜需要采用粗过滤的预处理方式来降低进入膜道的水不溶物浓度,降低膜道堵塞的几率;而ptfe有机膜盐水精制工艺中ptfe膜虽然是外滤,对粗盐水中的水不溶物没有要求,但氢氧化镁会附着在有机膜表面形成致密的滤饼层,影响过滤通量,氢氧化镁密度低难沉降易气浮,浮上澄清预处理兼有气浮和沉降的功能,因此ptfe有机膜盐水精制工艺需要采用浮上澄清的预处理来降低进入膜过滤器的氢氧化镁浓度,提高过滤的通量和稳定性。本方法采用平板陶瓷膜同样采用外滤方式,但膜组件采用了气擦洗,且由于气擦洗使得平板陶瓷膜组件内外盐水循环流动形成错流,流动的盐水将膜表面的氢氧化镁带出膜组件,避免因膜表面氢氧化镁富集形成致密的滤饼层而影响过滤通量和稳定性。因此,本方法不需要采用浮上澄清及其它预处理,加药反应完全的粗盐水直接进入平板陶瓷膜进行固液分离、流程短,设备、仪表、土建、安装成本均大幅度降低。
[0037]
(2)本发明平板陶瓷膜采用负压抽吸、死端过滤,负压抽吸过滤、跨膜压差小、能耗低。传统的管式陶瓷膜采用泵输送盐水的正压过滤且大流量循环,过滤压力甚至达到0.5mpa,其膜压差也为0.5mpa,且反冲洗压力也需要0.5mpa的压力;而平板陶瓷膜采用负压抽吸,抽吸泵的负压<-0.1mpa,膜压差小于泵的负压亦即<0.1mpa,而平板陶瓷膜又属于外滤模式,对进入膜过滤组件的粗盐水中的氢氧化镁、碳酸钙等水不溶物浓度没有特别要求,因此,没有预处理,管式陶瓷膜的过滤通量锐减且波动很大,而平板陶瓷膜仍能维持较高的过滤通量且流量稳定。
[0038]
(3)特殊结构的膜堆,气擦洗形成的盐水循环流动,膜表面类似错流过滤,膜通量大,其工作原理如图3所示:平板陶瓷膜膜堆往往采用六面通透的长方体框架结构,框架底部安装有曝气管,靠曝气产生的气泡对膜表面截留的水不溶物进行气擦洗,膜池中的水流处于紊流状态,将水不溶物从膜表面带走的效率相对较低,气擦洗效果不理想。本发明特殊结构的膜堆同样采用长方体结构,但将除上下两面的其他四面封闭形成筒装,曝气时,筒内
盐水因有大量气泡而密度降低,筒外盐水仍保持原有密度,这样就能形成一个内外的密度差,外部盐水通过底部与曝气的气泡一起进入膜堆并往上部流动,出框架后的盐水,气泡继续上升盐水则沿外筒壁往下部流动,形成一个循环流,在气泡和水流的共同作用下气擦洗效率将明显提高,保证截留的水不溶物被从膜表面带走,且随着循环盐水流从筒外壁加速下沉病沉积在膜池的锥斗内。由于避免了盐泥等水不溶物在膜表面的堆积,膜的过滤的平均通量可以稳定在0.1m3/m2.h以上。
[0039]
(4)本发明由于节省了预处理设备,一次精制因此工艺设备简单,控制方便。
[0040]
(5)为保证精制盐水中钙镁≤1mg/l,ss≤1mg/l且能长期稳定,管式陶瓷膜因高过滤压力(0.5mpa)和高反冲洗压力(0.5mpa)使得膜管极易断裂,且陶瓷膜管有密闭在膜壳内,一旦陶瓷膜管断裂无法发现,即使安装在线监测,等到检测到不合格盐水指标,这些不合格盐水已经进入后续工序。而平板陶瓷膜低压过滤(<0.1mpa)低压反冲洗(<0.1mpa),不会出现膜断裂问题,可以保证盐水质量及其稳定性。且浸没在敞开的膜池内,检修非常方便,无需安装在线监测设备,满足离子膜烧碱进二次盐水精制界区的要求,即钙镁≤1mg/l,ss≤1mg/l。
[0041]
(6)可降低电耗、延长离子膜寿命。烧碱生产的电耗和离子膜寿命是由盐水质量决定的,离子膜烧碱技术自上世纪八十年代在中国使用以来,因盐水质量差,离子膜寿命多在2年左右,交流电耗更是超过2300kwh/吨碱,而ptfe膜自本世纪初推出后已经得到行业用户的认可,其盐水质量大幅度提升,离子膜寿命可延长至5年左右,交流电耗更是降至2200kwh/吨碱以内,但浮上澄清预处理成了制约ptfe膜发展的新的障碍;而平板陶瓷膜因无需浮上澄清预处理、精制盐水质量更是优于ptfe膜和管式陶瓷膜且过滤通量稳定,将更进一步降低电耗、延长离子膜寿命。
附图说明
[0042]
图1为本发明工艺流程图;
[0043]
图2为实施例1中反应流程图;
[0044]
图3为实施例1中膜池的工作原理图。
具体实施方式
[0045]
下面结合附图和具体实施例对本发明进行详细说明。
[0046]
实施例1
[0047]
某氯碱企业一次精制盐水的改进中试
[0048]
现有的离子膜烧碱一次盐水精制系统采用前反应加氢氧化钠除镁、浮上澄清桶作为粗盐水的预处理、后反应加碳酸钠除钙、ptfe有机膜过滤去除反应形成的水不溶物的工艺,除钙镁加药控制氢氧化钠和碳酸钠的过碱量,使得精制盐水呈碱性,ph约10.5~11.5,氢氧化钠约0.1~0.3g/l;碳酸钠约0.3~0.5g/l,这种现有工艺采用预处理是ptfe有机膜过滤精制的需要,没有浮上澄清预处理,ptfe有机膜过滤流量波动很大,无法稳定地保证精制盐水的产量来满足后续工序的需求。
[0049]
由于该企业预处理器建于2008年,内防腐损坏严重,已出现预处理器渗漏现象,为避免因预处理器无法使用造成一次盐水精制系统停产,该企业采用了本发明方法进行工艺
改进的中试,由于平板陶瓷膜采用浸没式负压抽吸的过滤方式,且特殊结构设计的膜堆,通过气擦洗和盐水循环流动可以将膜表面截留的水不溶物带走,保证膜的过滤通量和稳定性,改进后的工艺将取消浮上澄清预处理,将加氢氧化钠反应后盐水短路直接进入后反应槽,加碳酸钠反应后直接进入膜池,采用平板陶瓷膜固液分离。具体方法如下:
[0050]
(1)在化盐池中将待处理的固体盐溶解在配水中配制成原料盐水a,控制原料盐水a各个组分的浓度如下:氯化钠305
±
5g/l,硫酸钠7.4~15g/l,ca
2+
5~2000mg/l,mg
2+
5~200mg/l;
[0051]
化盐池采用砼结构。
[0052]
(2)在原料盐水a中加入精制剂碳酸钠溶液b和氢氧化钠溶液c进入反应槽,进行反应除钙镁反应2h,得到粗盐水d;
[0053]
粗盐水d的各个组分的浓度如下:氯化钠305
±
5g/l,硫酸钠7.4~15g/l,ca(oh)25~4000mg/l,mg(oh)
2 5~500mg/l,ss5~5000mg/l;
[0054]
碳酸钠溶液b采用工业级碳酸钠和工业水配制,其质量浓度为5~15%;,避免因碳酸钠浓度低造成氯化钠浓度降低,也避免因碳酸钠浓度高造成的碳酸钠在管道中结晶堵塞殊荣管道;
[0055]
氢氧化钠溶液c采用离子膜烧碱出电槽的氢氧化钠溶液,其质量浓度为30~32%,避免氢氧化钠浓度过低造成的粗盐水氯化钠浓度降低。
[0056]
碳酸钠的加入量由反应后的碳酸钠残余量控制,碳酸钠过碱量为0.3~0.6g/l;
[0057]
氢氧化钠的加入量由反应后的氢氧化钠的残余量控制,氢氧化钠过碱量为0.1~0.3g/l;
[0058]
反应器为带有顶部加药与机械搅拌的反应器,结构采用圆筒式结构,反应器内液体通过管道自流进入膜池。本实施例中采用二台反应器,反应器之间用管道连接,下进上出,粗盐水自反应器1下部进入,自上部流出经管道流入反应器2下部,再自反应器2上部流出经管道流入膜池,避免因盐水进入反应器后钙离子与碳酸钠尚未反应就出反应器的短路问题,机械搅拌,搅拌器安装在反应器顶部、避免短路;详见附图2。
[0059]
(3)通过除钙镁反应后得到的粗盐水d,自流进入平板陶瓷膜分离膜池3,膜池3的结构如图3所示,包括,长方体结构的膜堆,膜堆内设有除上下两面的其他四面封闭形成筒装的平板陶瓷膜安装筒,该安装筒内安装有平板陶瓷膜,平板陶瓷膜的孔径为0.05~0.1微米,材质为球磨α-al2o3,孔隙率>20%,结构形式为平板式;安装筒底部设有曝气管,该曝气管连接压缩空气输送管,上部设有精制盐水输送管,精制盐水输送管连接抽吸泵,通过抽吸泵负压抽吸,平板陶瓷膜采用负压抽吸、死端过滤,过滤压力0.05mpa,曝气时,筒内盐水因有大量气泡而密度降低,筒外盐水仍保持原有密度,这样就能形成一个内外的密度差,外部盐水通过底部与曝气的气泡一起进入膜堆并往上部流动,出框架后的盐水,气泡继续上升盐水则沿外筒壁往下部流动,形成一个循环流,在气泡和水流的共同作用下气擦洗效率将明显提高,碳酸钙、氢氧化镁、泥沙等水不溶物被截留在平板陶瓷膜的表面,并被气擦洗形成的循环盐水流带离平板陶瓷膜表面,且随着循环盐水流从筒外壁加速下沉病沉积在膜池的锥斗内,富集的盐泥与部分盐水进入污泥槽;盐水透过平板陶瓷膜得到一次精制盐水e;
[0060]
一次精制盐水e的各个组分的浓度如下:
[0061]
精制盐水各个组分的浓度如下:氯化钠约305g/l,硫酸钠7.4g/l,ca
2+
+mg
2+
为
0.78mg/l,ss为0.45mg/l,中试达到预期目标。
[0062]
(4)被气擦洗形成的盐水循环流带离膜表面的碳酸钙、氢氧化镁、盐泥沉积在膜池底部的泥斗中,定期排出盐泥浆f至渣池:
[0063]
盐泥浆f的各个组分的浓度如下:氯化钠305g/l,硫酸钠7.4g/l,ss约3.5%;
[0064]
(5)盐泥浆f经渣浆泵打入污泥脱水设备脱水,得到滤清液g和盐泥h,盐泥脱水的滤清液g返回平板陶瓷膜膜池。
[0065]
实施例2
[0066]
某化工厂在高盐无机废水零排放处理中采用纳滤膜分盐、反渗透膜浓缩、蒸发提盐工艺,废水中氯化钠10g/l,ca
2+
约500mg/l,mg
2+
约100mg/l,硫酸根约5000mg/l。为避免因钙镁离子、硫酸根浓缩富集造成的硫酸钙结垢对纳滤膜、反渗透膜和蒸发设备的影响,决定进行采用加药反应及膜分离氢氧化镁、碳酸钙作为纳滤膜预处理的实验。
[0067]
实验采用在常温条件下加氢氧化钠和碳酸钠反应将钙镁离子反应为氢氧化镁、碳酸钙固体,通过平板陶瓷膜固液分离,得到满足纳滤膜进膜要求的原水。具体方法如下:
[0068]
(1)原水a各个组分的浓度如下:氯化钠10g/l,硫酸钠5000mg/l,ca
2+
500mg/l,mg
2+
100mg/l;
[0069]
(2)在原料水a中加入精制剂碳酸钠溶液b和氢氧化钠溶液c进入反应器,其结构形式为圆筒式结构,顶部装有搅拌器,采用二台反应器串联,反应器之间用管道连接,下进上出,原水自反应器1下部进入,自上部流出经管道流入反应器2下部,再自反应器2上部流出,经管道自流进入膜池,避免因盐水进入反应器后钙离子与碳酸钠尚未反应就出反应器的短路问题,机械搅拌,搅拌器安装在反应器顶部、避免短路进行反应除钙镁反应2h,得到原水d;
[0070]
原水d的各个组分的浓度如下:氯化钠10g/l,硫酸钠5000mg/l,ca(oh)2998mg/l,mg(oh)
2 230mg/l,ss1310mg/l;
[0071]
碳酸钠溶液b采用工业级碳酸钠和工业水配制,其质量浓度为12.5%;
[0072]
氢氧化钠溶液c采用离子膜烧碱出电槽的氢氧化钠溶液,其质量浓度为32%,碳酸钠的加入量由反应后的碳酸钠残余量控制,碳酸钠过碱量为0.47g/l;
[0073]
氢氧化钠的加入量由反应后的氢氧化钠的残余量控制,氢氧化钠过碱量为0.26g/l;
[0074]
(3)通过除钙镁反应后得到的原水d,自流进入平板陶瓷膜分离膜池,通过抽吸泵负压抽吸,碳酸钙、氢氧化镁、泥沙等水不溶物被截留在平板陶瓷膜的表面,并被气擦洗形成的循环盐水流带离平板陶瓷膜表面,盐水透过平板陶瓷膜得到产水e;
[0075]
产水e的各个组分的浓度如下:氯化钠约10g/l,硫酸钠5000mg/l,ca
2+
+mg
2+
为0.75mg/l,ss为0.46mg/l,中试达到预期目标。
[0076]
所述的平板陶瓷膜的孔径为0.05~0.1微米,材质为球磨α-al2o3,孔隙率>20%,结构形式为平板式;
[0077]
平板陶瓷膜采用负压抽吸、死端过滤,过滤压力0.048mpa,气擦洗及特殊结构的膜堆可使盐水在膜堆内外循环流动,形成膜表面的错流运动,防止盐泥在膜表面堆积,富集的盐泥与部分盐水进入污泥槽;
[0078]
(4)被气擦洗形成的水循环流带离膜表面的碳酸钙、氢氧化镁、盐泥沉积在膜池底
部的泥斗中,定期排出盐泥浆f至渣池:
[0079]
盐泥浆f的各个组分的浓度如下:氯化钠10g/l,硫酸钠5g/l,ss≤3.2%;
[0080]
(5)盐泥浆f经渣浆泵打入污泥脱水设备脱水,得到滤清液g和盐泥h,盐泥脱水的滤清液g返回平板陶瓷膜膜池。
[0081]
通过实验,取高盐无机废水,加入氢氧化钠和碳酸钠并控制氢氧化钠约0.26g/l;碳酸钠约0.47g/l,保持原有硫酸根浓度不变,经过平板陶瓷膜过滤,滤清液中ca
2+
+mg
2+
为0.75mg/l,在此条件下,可避免纳滤膜和反渗透膜的结垢隐患,同时蒸发只要定期排老卤至废水调节池,也可以避免蒸发器的硫酸钙结垢,使零排放稳定运行。
[0082]
实施例3
[0083]
氯酸钠生产盐水精制目前多采用道尔澄清桶+砂滤器+碳素管过滤的精制工艺,具有流程长、投资占地大,劳动强度高、不易管理、盐水质量差的特点,其精制盐水中一般ca
2+
+mg
2+
均在10mg/l左右,ss>5mg/l。
[0084]
现有氯酸钠盐水过滤精制,处理量为45m3/h,原料盐水中氯化钠为100g/l,氯酸钠为530g/l,ca
2+
+mg
2+
为100mg/l,含有少量铁屑等。采用加氢氧化钠除镁、碳酸钠除钙、平板陶瓷膜过滤精制工艺,生产要求经过精制后的清液中ca
2+
+mg
2+
不大于1mg/l,水不溶物(ss)含量不大于1mg/l。具体方法如下:
[0085]
(1)氯酸钠盐水a各个组分的浓度如下:氯化钠为100g/l,氯酸钠为530g/l,ca
2+
+mg
2+
为100mg/l,少量铁屑等;
[0086]
(2)在氯酸钠盐水a中加入精制剂碳酸钠溶液b和氢氧化钠溶液c进入反应器,反应器的结构形式为圆筒式结构,顶部装有搅拌器,采用二台反应器串联,反应器之间用管道连接,下进上出,原水自反应器1下部进入,自上部流出经管道流入反应器2下部,再自反应器2上部流出,经管道自流进入膜池,避免因盐水进入反应器后钙离子与碳酸钠尚未反应就出反应器的短路问题,机械搅拌,搅拌器安装在反应器顶部、避免短路进行反应除钙镁反应2h,得到原水d;
[0087]
氯酸钠盐水d的各个组分的浓度如下:氯化钠为100g/l,氯酸钠为530g/l,ca(oh)2195mg/l,mg(oh)
2 45mg/l,ss250mg/l;
[0088]
碳酸钠溶液b采用工业级碳酸钠和工业水配制,其质量浓度为12.5%;
[0089]
氢氧化钠溶液c采用工业级氢氧化钠溶液,其质量浓度为32%,
[0090]
碳酸钠的加入量由反应后的碳酸钠残余量控制,碳酸钠过碱量为0.5g/l;
[0091]
氢氧化钠的加入量由反应后的氢氧化钠的残余量控制,氢氧化钠过碱量为0.2g/l;
[0092]
(3)通过除钙镁反应后得到的氯酸钠盐水d,自流进入平板陶瓷膜分离膜池,通过抽吸泵负压抽吸,碳酸钙、氢氧化镁、铁屑等水不溶物被截留在平板陶瓷膜的表面,并被气擦洗形成的循环盐水流带离平板陶瓷膜表面,盐水透过平板陶瓷膜得到精制氯酸钠盐水e;
[0093]
精制氯酸钠盐水e的各个组分的浓度如下:
[0094]
精制氯酸钠盐水各个组分的浓度如下:氯化钠约100g/l,氯酸钠530g/l,ca
2+
+mg
2+
为0.82mg/l,ss为0.45mg/l,达到预期目标。
[0095]
所述的平板陶瓷膜的孔径为0.05~0.1微米,材质为球磨α-al2o3,孔隙率>20%,结构形式为平板式;
[0096]
平板陶瓷膜采用负压抽吸、死端过滤,过滤压力0.048mpa,气擦洗及特殊结构的膜堆可使盐水在膜堆内外循环流动,形成膜表面的错流运动,防止盐泥在膜表面堆积,富集的盐泥与部分盐水进入污泥槽;
[0097]
(4)被气擦洗形成的盐水循环流带离膜表面的碳酸钙、氢氧化镁、铁屑沉积在膜池底部的泥斗中,定期排出盐泥浆f至渣池:
[0098]
盐泥浆f的各个组分的浓度如下:氯化钠100g/l,氯酸钠530g/l,ss≤3.8%;
[0099]
(5)盐泥浆f经渣浆泵打入污泥脱水设备脱水,得到滤清液g和盐泥h,盐泥脱水的滤清液g返回平板陶瓷膜膜池。