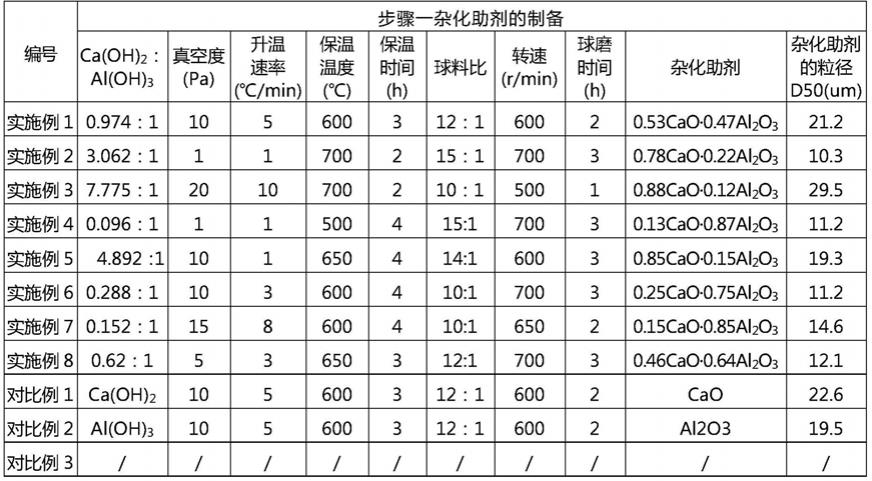
1.本发明涉及氮化锂颗粒以及其制备方法和制备设备,具体涉及一种纳米级氮化锂颗粒、利用气相反应法合成氮化锂颗粒的制备方法和制备设备。
背景技术:2.氮化锂(li3n)是一种金属氮化物,也是碱金属与氮气形成的唯一稳定的二元化合物,它属于六方晶系,晶格结构中存在锂、氮原子共同组成的锂
‑
氮层,且在每两个锂
‑
氮层之间有一个锂层。在氮化锂晶胞中,li
‑
n之间的距离为213pm,接近锂离子与氮负离子的离子半径之和,每个锂
‑
氮层与相邻的锂层间距为194pm,这表明氮化锂是一种离子化合物。li3n具有的这些特殊的物理特性赋予它优异的性能,广泛应用于储能、催化及储氢领域。li3n作为一种具有优异电导率的快离子导体,可用作固态电解质及正极补锂添加剂。除此之外,氮化锂还可以用作催化剂,有效地将六方氮化硼转化为立方氮化硼。近年来,研究者发现氮化锂用作储氢材料具有一定的优势,相比于传统储氢材料,li3n的储氢质量分数可以达到10.4%,储氢性能得到大大的提升。
3.常温下,金属锂暴露在空气中可缓慢生成氮化锂,但在充满氮气的空间内,氮化锂的生成速率要比在空气中快10
‑
15倍。因此,无论工业上还是实验室生产氮化锂,通常将金属锂在熔融状态下通入氮气气流,使得金属锂与氮气反应生成氮化锂。但是,工业上制备氮化锂的这种工艺造成金属锂的利用率比较低,生产效率不佳;并且利用该工艺制备的氮化锂为块状固体或毫米级尺寸的颗粒,严重影响使用性能。目前,市面上销售的氮化锂颗粒粒径过大,如上海麦克林生化科技有限公司在售的150目、粒径83.4μm的氮化锂颗粒;如北京百灵威科技有限公司在售的60目、粒径208.4μm的氮化锂,可见,目前大规模生产粒径为纳米级至几微米级别的氮化锂仍然处于市场空白区。
4.兰州理工大学学报发表了题为《li3n的合成及吸放氢性能研究》,其中li3n的制备步骤如下:将纯度大于99.99%的金属锂放置于空气隔绝、温度可控的密闭容器中,加热电阻丝升温至200℃,使得金属锂变成熔融态,此时通入0.1mpa压力的高纯氮气,保温12h,获得氮化锂单质。该工艺有如下不足:首先,锂源来源于金属锂,对于工业化生产而言,极大的增加了生产成本;其次,金属锂在熔融状态下通入高纯氮气制备氮化锂,存在气液相状态的化学反应面积有限的问题,这导致氮气与金属锂液的反应不充分,从而使锂金属的利用率不高;最后,该工艺生产的氮化锂颗粒的粒径大,影响使用性能。
5.中国专利公开号cn1258239c公开了一种新型锂离子电池负极材料制备方法,该工艺包括纯相氮化锂的制备方法,将金属锂放在经过脱水、脱氧、脱二氧化碳的纯化处理的氮气流中,升高温度至200
‑
700℃,金属锂发生熔融,形成金属锂液,通过气液相化学反应,合成粒度为300目、粒径41.7μm的纯相氮化锂。该工艺有如下不足:使用高纯金属锂作为锂源,成本高;利用高纯氮气与熔融的金属锂液进行气液相反应,极大的降低了生产效率,锂源也得不到充分利用。
6.中国专利公开号cn1300871c公开了一种用于锂离子电池负极的可逆脱嵌锂材料
及制备方法,该工艺包括氮化锂的制备方法,将金属锂片在高纯氮气气氛下,通过升高温度促进氮气与金属锂的反应,银白色锂片逐渐转变成暗红色,然后对反应后的产物进行粉碎,获得氮化锂颗粒。该工艺制备氮化锂存在金属锂反应不充分、获得的氮化锂颗粒纯度低的问题。
技术实现要素:7.针对现有技术中氮化锂的制备成本高、生产效率低、颗粒粒度大的问题,本发明提供一种氮化锂颗粒的制备方法和制备设备。
8.本发明采用的技术方案如下:
9.[1]一种氮化锂颗粒的制备方法,其特征在于,包括以下步骤:
[0010]
(1)杂化助剂制备步骤,其中,将氢氧化钙与氢氧化铝加热后冷却,进行球磨后得到化学式为xcao
·
yal2o3的杂化助剂,其中x、y为质量分数,满足0<x<1、0<y<1、x+y=1;
[0011]
(2)锂原料热分解步骤,其中,将所述杂化助剂与锂原料均匀混合并进行压制,然后进行加热分解而获得熟料;
[0012]
(3)真空热还原步骤,其中,将所述熟料与还原剂混合均匀并压制成团,在真空还原炉中进行真空热还原,生成金属锂蒸气;
[0013]
(4)氮化锂颗粒合成步骤,其中,将所述金属锂蒸气通入反应仓内,氮气与金属锂蒸气接触反应,生成氮化锂颗粒。
[0014]
[2]根据[1]所述的氮化锂颗粒的制备方法,其特征在于,在步骤(1)中,将氢氧化钙与氢氧化铝混合均匀,在真空度1
‑
20pa下以升温速率1
‑
10℃/min升高到500
‑
700℃,保温时间为2
‑
4h,待冷却后,进行球磨而获得杂化助剂xcao
·
yal2o3,其中x、y优选为0.1≤x≤0.9、0.1≤y≤0.9、x+y=1;
[0015]
其中,所述杂化助剂xcao
·
yal2o3的粒径d50为10.0μm≤d50≤80.0μm,优选为10.0μm≤d50≤30.0μm,更优选为10.3μm≤d50≤29.5μm。
[0016]
[3]根据[1]所述的氮化锂颗粒的制备方法,其特征在于,在步骤(2)中,将所述杂化助剂与锂原料混合均匀,以30
‑
100mpa的压力压制成团,在真空度0.1
‑
10pa下以升温速率1
‑
10℃/min升高到500
‑
900℃进行热分解,保温时间为4
‑
10h,待反应结束后,进行球磨,获得熟料;
[0017]
其中,所述锂原料为氢氧化锂、碳酸锂、碳酸氢锂、过氧化锂、硝酸锂中的一种或两种以上,优选为碳酸锂、氢氧化锂;
[0018]
其中,球磨后的熟料粒径d50为10.0μm≤d50≤45.0μm,优选为10.0μm≤d50≤20.0μm,更优选为10.2μm≤d50≤19.8μm;所述杂化助剂与锂原料的质量比为(0.5
‑
1.0):1,优选为(0.75
‑
0.95):1。
[0019]
[4]根据[1]所述的氮化锂颗粒的制备方法,其特征在于,在步骤(3)中,将所述熟料与还原剂混合均匀,以30
‑
100mpa的压力制成团块,在真空度为0.1
‑
10pa下以升温速率1
‑
10℃/min升高到700
‑
1000℃之后,保温4
‑
8h,在真空还原炉中进行真空热还原,生成金属锂蒸气;
[0020]
其中,所述团块的直径为20mm
‑
30mm,质量为40
‑
80g/个。
[0021]
[5]根据[1]所述的氮化锂颗粒的制备方法,其特征在于,在步骤(3)中,所述还原
剂为铝粉、硅粉、铁粉、硅铁、碳粉、硅铝粉、碳化钙、硅铁、镁粉中的一种或两种以上,优选为铝粉、硅粉、硅铝粉;其中,所述熟料与还原剂的质量比为1:(0.1
‑
0.5),优选为1:(0.2
‑
0.3)。
[0022]
[6]根据[1]所述的氮化锂颗粒的制备方法,其特征在于,在步骤(4)中,所述金属锂蒸气进入反应仓,调整氮气流量,氮气与金属锂蒸气充分接触进行气相反应,生成氮化锂颗粒,所述氮化锂颗粒在惰性气体下进行包装、封袋;
[0023]
其中,所述氮气流量为0.10
‑
0.60l/min,优选为0.18
‑
0.58l/min;所述反应仓内部温度为300
‑
500℃,所述氮气的纯度为99.0%
‑
99.99%;所述惰性气体为氮气或者氩气。
[0024]
[7]根据[1]所述的氮化锂颗粒的制备方法,其特征在于,所述氮化锂颗粒的粒径为0.05
‑
0.50μm,优选为0.10
‑
0.30μm,纯度为99.0%
‑
99.4%,产率为68.7%
‑
78.2%。
[0025]
[8]一种氮化锂颗粒,其由[1]~[7]中任一项所述的氮化锂颗粒的制备方法制到。
[0026]
[9]一种制备氮化锂颗粒的设备,其用于实施[1]~[7]中任一项所述的氮化锂颗粒的制备方法,其特征在于,所述设备包括真空还原炉(1)、坩埚(2)、真空泵(3)、微米陶瓷过滤器(4)、流量控制阀(5)、氮气供应装置(6)、反应仓(7);
[0027]
所述氮气供应装置(6)连通反应仓(7),通过流量控制阀(5)调节氮气进气量,所述反应仓内部设置加热单元;
[0028]
在所述真空还原炉(1)的下方设置有真空泵(3);
[0029]
在所述真空还原炉(1)的正中央放置坩埚(2),所述坩埚(2)采用电阻加热方式。
[0030]
[10]根据[9]所述的制备氮化锂颗粒的设备,其特征在于,所述真空还原炉的材质为镍铬合金。
[0031]
与现有技术相比,本发明中的锂原料来源广泛,不局限于金属锂单质,极大地降低了氮化锂颗粒的生产成本;通过采用真空热还原方法制备金属锂蒸气,通入高纯氮气与高温金属锂蒸气混合,进行气相反应,制备氮化锂颗粒,提高了反应速率,提升了生产效率,提高了产品质量,有利于工业化生产,气相反应有助于氮化锂颗粒粒径的纳米化;本发明的杂化助剂的独特配方一方面可以促进锂原料更充分的分解,另一方面,有利于热还原反应的进行,使得氮化锂的产率更高。
附图说明
[0032]
图1是实施例1制备的氮化锂颗粒的扫描电子显微镜(sem)图;
[0033]
图2是实施例1制备的氮化锂颗粒的xrd图;
[0034]
图3是实施例1的杂化助剂的xrd图;
[0035]
图4是实施例2的杂化助剂的xrd图;
[0036]
图5是实施例3的杂化助剂的xrd图;
[0037]
图6是实施例4的杂化助剂的xrd图;
[0038]
图7是实施例5的杂化助剂的xrd图;
[0039]
图8是实施例6的杂化助剂的xrd图;
[0040]
图9是实施例7的杂化助剂的xrd图;
[0041]
图10是实施例8的杂化助剂的xrd图;
[0042]
图11是本发明的设备示意图。
具体实施方式
[0043]
在本说明书中,使用了
‑
表示了数值范围的情况下,它们包含两方的端点,单位是共通的。例如,1
‑
20pa表示真空度为1pa及以上且在20pa及以下。
[0044]
下面结合附图和具体实施例对本发明做进一步详细说明。
[0045]
本发明提供一种以含锂化合物为原料,在真空条件下利用氮气与高温金属锂蒸气发生气相化学反应制备氮化锂颗粒的工艺,具体包括如下步骤:
[0046]
步骤一,制备杂化助剂
[0047]
将氢氧化钙与氢氧化铝按照质量比(0.1
‑
8.0):1,优选按照质量比(0.152
‑
7.775):1,利用高效混合机(vch
‑
5)混合均匀,然后在真空度1
‑
20pa下,以升温速率1
‑
10℃/min升高到500
‑
700℃,保温时间为2
‑
4h,待冷却至室温后,将取出的样品采用直径为5mm的锆球进行磨碎,其中,球料质量比为(10
‑
15):1,球磨机的转速为500
‑
700r/min,球磨时间为1
‑
3h,球磨后得到杂化助剂xcao
·
yal2o3,其中x、y为质量分数,加热过程中持续抽真空,排出产生的水蒸气。采用激光粒度分析仪测定该杂化助剂xcao
·
yal2o3的粒径d50,所制备的杂化助剂xcao
·
yal2o3的粒径d50为10.0μm≤d50≤80.0μm,优选为10.0μm≤d50≤30.0μm,更优选为10.3μm≤d50≤29.5μm。利用xrd测试及gsas软件对杂化助剂进行物相定量分析,从而确定x、y的数值。通过如上地调控氢氧化钙和氢氧化铝的配比、升温速率、保温时间以及球磨条件,x、y的数值可能有变动,但只要x、y满足0<x<1、0<y<1、x+y=1,优选为0.1≤x≤0.9、0.1≤y≤0.9、x+y=1;则可以达到本发明的杂化助剂的有益效果。
[0048]
锂原料的熔点较低,高温条件下溶解为液态时,锂原料的挥发性会增强,如果采用真空热分解的工艺,则锂原料的挥发就会更加严重。因此,本发明中,杂化助剂的添加一方面有利于促进锂原料的分解,另一方面也有效地抑制锂原料的挥发,显著提升了生产产率。杂化助剂的作用机理如下:氧化钙的熔点高达2580℃,在锂原料分解的过程中,氧化钙不会熔化,它起到骨料的作用,局部形成包裹,可以防止锂原料球团的融化与流失,从而抑制锂原料的挥发。其次,氧化钙的另一个重要作用是在真空热还原过程中,能够与还原剂的氧化物形成稳定复合物,从而降低还原反应温度,促进还原过程的进行。氧化铝可以与锂原料的分解产物氧化锂形成复合物li2o
·
al2o3,该过程降低了热解反应温度,促进了锂原料的热分解。通过使用氧化钙和氧化铝这两者作为杂化助剂,一方面可以抑制锂原料的挥发,降低还原反应温度,并且促进锂原料的热分解,另一方面,更容易压制成块和磨粉。然而单独使用氧化钙作为助剂时,虽然锂原料很容易形成熔体,抑制锂原料的挥发,但锂原料热分解率不高,并且磨粉困难;然而单独使用氧化铝作为杂化助剂时,其与锂原料难以压制成块,难以抑制锂原料的挥发,难以降低还原反应温度,导致锂原料的利用率低。
[0049]
步骤二,锂原料热分解
[0050]
将杂化助剂与锂原料(氢氧化锂、碳酸锂、碳酸氢锂、过氧化锂、硝酸锂的至少一种,优选为氢氧化锂或碳酸锂或氢氧化锂和碳酸锂的混合物)按质量比(0.5
‑
1.0):1,优选按质量比(0.75
‑
0.95):1,利用高效混合机(vch
‑
5)混合均匀,利用嵌样机以30
‑
100mpa的压力压制成团块,在真空度0.1
‑
10pa下以升温速率1
‑
10℃/min升高到500
‑
900℃,保温时间为4
‑
10h,待反应结束后,取出熟料。将熟料采用5mm的锆球进行球磨,球料质量比为(10
‑
15):1,球磨机的转速为500
‑
700r/min,球磨时间为1
‑
3h,球磨后熟料的粒径d50为10.0μm≤d50≤45.0μm,优选为10.0μm≤d50≤20.0μm。
[0051]
步骤三,真空热还原
[0052]
将熟料与还原剂按质量比1:(0.1
‑
0.5),优选为1:(0.2
‑
0.3),混合均匀,利用嵌样机以30
‑
100mpa的压力压制成直径为20mm
‑
30mm、质量为40
‑
80g/个的团块,在真空度为0.1
‑
10pa下以升温速率1
‑
10℃/min升高到700
‑
1000℃之后,保温4
‑
8h,在真空还原炉中进行真空热还原,生成金属锂蒸气。所述还原剂为铝粉、硅粉、铁粉、硅铁、碳粉、硅铝粉、碳化钙、硅铁、镁粉中的一种或两种以上,优选为铝粉、硅粉、硅铝粉。
[0053]
需要说明的是,只要能达到预期的效果,团块的大小和直径并无限定,优选制成直径为20mm
‑
30mm,质量为40
‑
80g/个。通过将熟料与还原剂压制成团块,一方面,可以使各反应原料之间能有一个相对稳定的配比,以便于热还原反应的进行;另一方面,还可以减少锂原料中携带粉尘的量,提高产物的品质。熟料中的氧化钙、氧化铝通过与氧化锂形成cao
·
li2o和al2o3·
li2o,可以显著降低氧化锂的熔点,使得氧化锂在较低的还原温度下呈现熔融状态,这种状态具有一定的电阻,可以使坩埚产生足够的热量。
[0054]
步骤四,合成氮化锂颗粒
[0055]
步骤三中的金属锂蒸气首先通过孔径为1.0μm的微米陶瓷过滤器,此过程将金属锂蒸气中的粉尘有效除去;然后金属锂蒸气进入反应仓内,通过加热单元,将反应仓加热至300
‑
500℃;此时打开氮气供应装置的流量控制阀,控制氮气流量为0.10
‑
0.60l/min,优选为0.18
‑
0.58l/min,氮气进入反应仓内与高温金属锂蒸气充分接触,发生气相反应,生成氮化锂颗粒。需要说明的是,只要能使得所提供的氮气迅速与锂蒸气发生反应即可,氮气流量没有特别限定,优选按照化学反应计量摩尔比使得锂蒸气相对于氮气而言过量。反应结束后,待设备冷却至室温,然后在氩气气氛或氮气气氛下收集氮化锂颗粒,并进行包装。利用icp测试仪对氮化锂颗粒的纯度进行测定,结果分析其纯度为99.0%
‑
99.4%;利用公式z=i/q=im/(11.61ma)
×
100%,计算得出氮化锂颗粒的产率为68.7%
‑
78.2%;利用激光粒度分析仪测定分析可知,氮化锂颗粒的粒径为0.05
‑
0.50μm,优选为0.1
‑
0.3μm。这是目前气液相反应制备氮化锂工艺很难生产出的粒径范围。
[0056]
气相反应相比气液相或气固相反应更加充分,一方面,加快了反应速率,提升了生产效率,有利于工业化生产;另一方面,气相反应有助于氮化锂颗粒纳米化,降低氮化锂颗粒的粒径。
[0057]
另外,本发明提供了一种制备氮化锂颗粒的设备,其用于实施权利要求1所述的氮化锂颗粒的制备方法,其特征在于,所述设备包括如下部件:真空还原炉1、坩埚2、真空泵3、微米陶瓷过滤器4、流量控制阀5、氮气供应装置6、反应仓7等;所述氮气供应装置6连通反应仓7,通过流量控制阀5调节氮气进气量,所述反应仓内部设置加热单元;
[0058]
在所述真空还原炉1的下方设置有真空泵3;
[0059]
在所述真空还原炉1的正中央放置坩埚2,所述坩埚2采用电阻加热方式。
[0060]
附图11示出了本发明的设备示意图,图中的尺寸、构型和位置关系等仅仅用于示意,并非限定本发明。
[0061]
在实施例中使用的原料、设备、测试条件以及检测方法等如下:
[0062]
锂原料为氢氧化锂、碳酸锂、碳酸氢锂、过氧化锂、硝酸锂中的一种或两种以上,质量纯度>99.0%,购买于江西赣锋锂业股份有限公司。
[0063]
真空还原炉购买于上海钜晶精密仪器制造有限公司,用于真空热还原反应。
[0064]
三温区管式炉购买于上海翰军实验设备有限公司,用于金属锂制备氮化锂。
[0065]
xrd设备厂家为德国布鲁克(bruker),型号为bruker d8,xrd测试条件为:电压40kv、电流40ma、cu靶、扫描范围10
°‑
90
°
、步距0.02、扫描速度10
°
/min,用于杂化助剂的定性与定量分析。
[0066]
激光粒度分析仪购自珠海真理光学仪器有限公司,型号为lt3600,用于杂化助剂、熟料、氮化锂的粒径测试。
[0067]
高效混合机(vch
‑
5)购自无锡泰贤粉体科技有限公司,用于生产过程中粉体物料的混合。
[0068]
嵌样机购自永安兴业山水探矿机械有限公司,用于粉体的压块成型。
[0069]
icp检测仪购买于江苏天瑞仪器股份有限公司,按常规方法对氮化锂颗粒进行元素成分检测,即,进行icp测试,测定收集产品中氮化锂的纯度。
[0070]
氮化锂颗粒产率的计算步骤如下:
[0071]
称取锂原料质量为m,其相对分子质量为m,锂原料的化学分子式中含有a个锂原子,则原料中锂原子的物质的量为n=ma/m,则氮化锂的理论产量:
[0072]
q=n/3
×
(6.941
×
3+14.007)=11.61ma/m
[0073]
反应结束后获得的产物中的氮化锂的实际产量为i,则有:氮化锂的产率为z=i/q
×
100%=im/(11.61ma)
×
100%。
[0074]
实施例1
[0075]
步骤一,制备杂化助剂
[0076]
在室温下,利用高效混合机(vch
‑
5),将ca(oh)2与al(oh)3按照质量比0.974:1均匀混合后,在真空度为10pa下,以升温速率5℃/min升高到温度600℃,保温时间为3h,冷却至室温后取出,利用球磨机,采用直径为5mm的锆球将取出的样品进行磨碎,其中,球料质量比为12:1,球磨机的转速为600r/min,球磨时间为2h,球磨后得到杂化助剂。采用激光粒度分析仪测定该杂化助剂的粒径d50,所制备的杂化助剂的粒径d50为21.2μm。经xrd测试及gsas软件对杂化助剂进行物相定量分析,杂化助剂为0.53cao
·
0.47al2o3。
[0077]
如图3所示,经xrd测试,杂化助剂中出现了cao与al2o3的物相。
[0078]
步骤二,锂原料热分解
[0079]
在室温下,利用高效混合机(vch
‑
5),将杂化助剂与锂原料碳酸锂按质量比0.85:1,称取0.898kg的杂化助剂和1.056kg的碳酸锂利用粉体混合机混合均匀,利用嵌样机以压力60mpa进行压制成团,然后在真空度5pa下,以升温速率5℃/min升高至700℃进行热分解反应,保温时间为8h,待反应结束后取出。取出的物料利用球磨机,采用直径为5mm的锆球进行球磨,球料质量比为12:1,球磨机的转数为600r/min,球磨时间为2h,球磨后得到熟料,采用激光粒度分析仪测定,熟料的粒径d50为15.6μm。
[0080]
步骤三,真空热还原
[0081]
按熟料与还原剂铝粉的质量比1:0.24,称量熟料质量为1.327kg,称取铝粉质量为0.319kg,将所述熟料与还原剂混合均匀,利用嵌样机以压力为80mpa进行压制成团,团块的直径约为20mm,单个团块的质量约为40g,在坩埚中将团块在真空度5pa下,以升温速率5℃/min升高到还原温度为850℃之后,在850℃保温,保温时间为6h,在真空热还原炉中进行真空热还原,生成金属锂蒸气。
[0082]
步骤四,合成氮化锂颗粒
[0083]
使金属锂蒸气首先通过孔径为1.0μm的微米陶瓷过滤器,此过程将金属锂蒸气中的粉尘有效除去;然后金属锂蒸气进入反应仓内,将反应仓温度设为400℃。此时打开氮气供应装置上的流量控制阀,氮气摩尔体积为22.4l/mol,控制氮气流量为0.24l/min,氮气供应时间对应于真空热还原步骤中的保温时间;需要说明的是,只要能使得所提供的氮气迅速与锂蒸气发生反应即可,氮气流量没有特别限定,优选按照化学反应计量摩尔比使得锂蒸气相对于氮气而言过量。所述氮气的纯度为99.0%
‑
99.99%。氮气进入反应仓内与高温金属锂蒸气充分接触反应,生成氮化锂颗粒,反应结束后,待设备冷却至室温,然后在氮气气氛下收集棕红色的反应产物255.66g,并用热封袋进行真空包装。对氮化锂颗粒进行表征测试,图1是实施例1制备的氮化锂颗粒的扫描电子显微镜(sem)图;图2是实施例1制备产物的xrd图,通过对比标准卡片可知,该产物为氮化锂。
[0084]
实施例1~8所使用的设备示意图如图11所示,示意图是以示意方式,而不是以实际的尺寸和比例显示本技术的设备,只要能达到预期效果,并无特别限定,例如图11中所述坩埚(2)中心与微米陶瓷过滤器(4)之间的距离可以为30
‑
80cm。
[0085]
利用icp测试仪对氮化锂颗粒的纯度进行测定,根据锂元素和氮元素的分析结果,测得实施例1中制备的氮化锂颗粒的纯度为99.2%,由此计算出反应产物中氮化锂颗粒的实际产量i为253.61g;
[0086]
利用公式z=i/q=im/(11.61ma)
×
100%计算得出氮化锂颗粒的产率,测得实施例1中制备的氮化锂颗粒的产率为76.4%;
[0087]
利用球磨机以500rpm进行研磨分散2h,利用激光粒度分析仪测定分析氮化锂颗粒的粒径d50,颗粒粒径d50为0.22μm。
[0088]
实施例2~8
[0089]
制备方法的步骤基本上与实施例1相同,不同点在于相关的成分以及参数等,具体如表1~4所示。
[0090]
对比例1和2
[0091]
制备方法的步骤基本上与实施例1相同,不同点在于相关的成分以及参数等,具体如表1~4所示。
[0092]
对比例3
[0093]
在室温条件下,在氮气氛围保护下,在手套箱中称取金属锂5.0g,并将金属锂放置在坩埚中一起置于三温区管式炉,此时向三温区管式炉中通入氮气气流,氮气流量为0.40l/min。随后三温区管式炉以升温速率5℃/min,升高到350℃,保温8h,然后在氮气气氛下收集6.51g暗红色的产物,计算出氮化锂的实际产量为3.76g,产率为45%;利用球磨机以500rpm进行研磨分散2h,利用激光粒度分析仪测定分析氮化锂颗粒的粒径d50,粒径d50为55.0μm。
[0094]
表1
[0095][0096]
表2
[0097][0098]
表3
[0099][0100]
表4
[0101][0102]
如表4所示,分析实施例1~8和对比例1~2的测试结果可知,相比于实施例1~8的杂化助剂xcao
·
yal2o3而言,对比例1~2的助剂分别单独为氧化钙或者氧化铝,导致锂原料的热解率低或者挥发率高,造成氮化锂颗粒的产率明显低于实施例1~8。在实施例1~8中,氮化锂颗粒的产率为68.7%
‑
78.2%,纯度为99.0wt%以上,颗粒粒径为0.05
‑
0.50μm,远远优于对比例1~2,这再次说明本发明的复合型杂化助剂显著提升了锂原料的分解率和还原率。
[0103]
其原理可能在于,锂原料的熔点较低,在溶解为液态时,其挥发性变强,采用真空分解的办法,则锂原料的挥发就会更加严重。因此,在实施例1~8采用包含特定比例范围的氧化钙和氧化铝的复合型杂化助剂,该杂化助剂的添加有利于促进锂原料的分解,同时也有效抑制锂原料的挥发,提升整个工艺的产率。氧化钙的熔点高达2580℃,在锂原料分解的过程中,氧化钙不会熔化,它起到骨料的作用,局部形成包裹,可以防止锂原料球团的融化与流失,从而抑制锂原料的挥发。其次,氧化钙的另一个重要作用是在真空热还原过程中,能够与还原剂的氧化物形成稳定复合物,从而降低还原反应温度,促进还原过程的进行。氧化铝可以与锂原料的分解产物氧化锂形成化合物li2o
·
al2o3,该过程降低了热解反应温
度,促进了锂原料的热分解。本发明通过使用氧化钙和氧化铝这两者作为杂化助剂,一方面能够抑制锂原料的挥发,降低还原反应温度,并且促进锂原料的热分解,另一方面,更容易压制成块和磨粉。然而单独使用氧化钙作为助剂时,虽然锂原料很容易形成熔体,锂原料的挥发得到明显抑制,但锂原料热分解率不高,并且磨粉困难,导致氮化锂的产率低;然而单独使用氧化铝作为杂化助剂时,al2o3与锂原料难以压制成块,难以抑制锂原料的挥发,难以降低还原反应温度,导致锂原料的利用率低。
[0104]
如表4所示,分析实施例1~8和对比例3的测试结果可知,相比于目前在工业上通常使用固态锂制备氮化锂的情况而言,根据测试结果分析可知,以气相反应制备的氮化锂颗粒在纯度、粒径大小、产率上均优于气液相制备氮化锂。本发明的气相法制备的氮化锂颗粒的产率、纯度、粒径还存在进一步提高的空间,但是与现有技术相比取得了显著的实质性进步。
[0105]
分析对比例3的测试结果可知,在对比例3中,向熔融金属锂中通入高纯氮气而制备氮化锂,所制备的氮化锂的粒径相比于实施例1~8和对比例1~2中制备的氮化锂的粒径要大很多;氮化锂的产率为45.0%,远低于实施例1~8与对比例1~2,这再次说明气相反应制备氮化锂颗粒的生产效率更高。
[0106]
总结本发明的有益效果如下:
[0107]
1、本发明通过精密地调控杂化助剂的比例、热还原反应温度、真空度、物料、还原剂、氮气流量等条件,可将由真空热还原反应制备的金属锂蒸气直接用于与高纯氮气进行气相反应,从而能够连续地进行锂蒸气制备和氮化锂颗粒制备,提升氮化锂颗粒的生产效率。另外,在成本和原料方面,由于没有使用固态锂作为原料,因而大大地降低了生产成本,同时简化了制备工艺。
[0108]
2、本发明中的复合型杂化助剂通过在500
‑
700℃烧结的方法而制备,能够精密地调控杂化助剂中的cao与al2o3的配混比例,能够促进锂原料的热分解反应,促进锂原料分解为氧化锂。锂原料的熔点较低,当变成熔液时,其挥发性变强。本发明的杂化助剂在高温下起到骨料的作用,局部形成包裹,防止锂原料球团的融化与流失,从而起到抑制锂原料挥发的作用;其次,杂化助剂可与氧化锂形成复合物li2o
·
al2o3和li2o
·
cao,能够降低真空热还原的反应温度,促进还原反应的进行,显著提升氮化锂颗粒的产率。
[0109]
3、不同于在现有工艺中采用氮气与熔融的金属锂反应制备氮化锂,本发明首创地采用气相反应,将高纯氮气与由真空热还原制备的金属锂蒸气进行反应而制备氮化锂颗粒,使得本工艺的反应更加充分,提高反应速率和产率,所制备的氮化锂颗粒的纯度更高,粒径更小。本发明的气相反应法成功地获得粒径为0.05
‑
0.50μm、纯度为99wt%以上的氮化锂颗粒。
[0110]
对所有公开的实施例的上述说明,仅为本发明的最佳实施例及所运用技术原理,并不用于限制本发明。本领域技术人员会理解,且对这些实施例的多种修改对本领域的专业人员来说是显而易见的。显然,本领域的技术人员对实施例进行的各种改动和变型不脱离本发明的精神和范围,这些改动与变型均应包含在本发明的保护范围之内。
[0111]
附图标记说明
[0112]
1、真空还原炉,2、坩埚,3、真空泵,4、微米陶瓷过滤器,5、流量控制阀,6、氮气供应装置,7、反应仓。