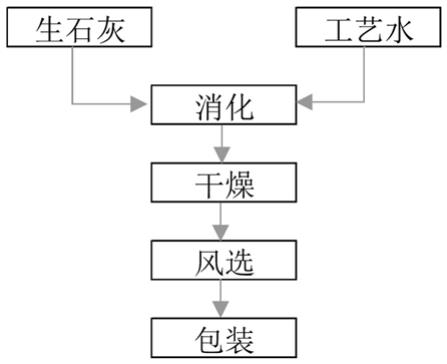
1.本发明涉及一种高比表面积、高白度氢氧化钙的制备方法,尤其涉及高比表面积、高白度、高纯度氢氧化钙的制备方法。
背景技术:2.高比表面积氢氧化钙在电厂烟气脱硫、玻璃工业及化工尾气脱硫等方面,能发挥出非常明显的作用。
3.氢氧化钙作为常用脱硫剂,具有脱硫效率高、技术成熟的特点。但普通氢氧化钙多采用干法风选生产,灰水比低、杂质多、有效氢氧化钙含量低,存在比表面积低(≤20m2/g)、反应活性差、使用成本高的问题。在此背景下,研究高比表面积氢氧化钙,特别是比表面积达到40m2/g以上的,具有纯度高、反应活性好、吸附率高的特点,市场需求越来越大。根据工艺要求进行计算,每焚烧处理1吨垃圾,需要使用至少13千克高比表面积氢氧化钙粉末,全国垃圾处理能力达到1亿吨/年,需要高比表面积氢氧化钙产品100万吨/年。
4.另外,在玻璃制造、石油化工等行业,工业炉产生的烟气中往往含有hcl、hf、二恶英、呋喃和重金属等污染物,高比表面积氢氧化钙产品是吸收这些污染物的最佳选择,可以部分替代活性炭。
技术实现要素:5.针对已有技术存在的不足,本发明的目的在于提供高比表面积、高白度氢氧化钙的制备方法。
6.本发明的是通过如下技术方案实现的:一种高比表面积、高白度氢氧化钙的制备方法,该方法依次包括如下步骤:(1)选取活性大于350ml/4molhcl的生石灰,破碎至15
‑
20mm粒径范围;(2)生石灰与水在60
‑
70℃条件下消化反应,反应初期添加一定量的晶型控制剂,制成氢氧化钙料浆,消化过程反应放热,控制消化结束后温度在95
‑
98℃范围内,出料;(3)将消化结束的ca(oh)2料浆经震动筛、旋流器除杂,去除料浆中的盐酸不溶物、未反应的碳酸钙;(4)除杂后料浆离心浓缩;(5)浓缩料浆进行干燥、并粉碎分级制成高比表面积氢氧化钙。
7.所述步骤(1)中生石灰活性大于350ml/4molhcl,有效氧化钙含量≥92%,t60≤45s。
8.所述步骤(2)中消化水温严格控制在60
‑
70℃。反应温度过低,消化速度慢;反应温度过高,反应剧烈在生石灰表面形成致密氢氧化钙膜,阻止化学反应深入进行。二者最终影响生产效率、成品白度、成品比表面积。
9.所述步骤(2)中的晶型控制剂以生石灰重量的0.5
‑
1.0%,种类为葡萄糖、柠檬酸钠、焦磷酸钠、蔗糖中的一种或几种的混合物。
10.所述步骤(2)中消化过程可在带搅拌反应釜、滚筒消化机、槽式消化机、笼式消化机中的任意一种中反应。
11.所述步骤(2)中消化结束温度指消化机尾部温度,严格控制在95
‑
98℃。
12.所述步骤(3)中,氢氧化钙料浆现后经100目、200目、8um旋流器除杂,除去包含盐酸不溶物、生石灰中所含的碳酸钙、铁铝氧化物。
13.所述步骤(4)中,离心后的氢氧化钙料浆浓缩至质量浓度30%及以上。
14.所述步骤(5)中的干燥采用闪蒸干燥,干燥温度为105
‑
120℃,粉碎后粒径控制在5
‑
8μm。
15.本发明的创新点在步骤(2),通过晶型控制剂调整氢氧化钙乳液的溶解度,提高过饱和度,从而使消化过程中形成的氢氧化钙粒子更小,比表面积更大。
附图说明
16.图1比较例1得到的碳酸钙生产工艺流程图。
17.图2本发明工艺流程图。
18.图3实施例1、比较例1、比较例2的碳酸钙的比表面积检测数据。
具体实施方式
19.实施例1消化:在2立方米的反应釜中加入360公斤温度为65℃工艺水,加入0.28公斤蔗糖,搅拌均匀后,加入56公斤生石灰,生石灰活性355ml/4molhcl,粒度15mm。消化反应30min,制成氢氧化钙料浆,因反应为放热反应,控制消化反应的结束温度至98℃,出料。
20.除杂:消化料浆依次过200目筛网,8μm底流旋流器,除去杂质,除杂后产物的性质为进一步提高白度和纯度。
21.离心:除杂后料浆经离心机浓缩至质量浓度为30%。
22.干燥:使用闪蒸干燥机,控制干燥温度115℃,同时风力粉碎,制品即为高比表面积、高白度氢氧化钙,白度92.8%;含量93.4%;比表面积43.5m2/g;气孔容量0.26cm3/g;分布粒度(d50)5.15um。
23.实施例1
‑
1实施步骤同实施例1,仅补充消化反应温度为60℃,所得到的产品的白度92.4%;含量93.1%;比表面积41.5m2/g;气孔容量0.22cm3/g;分布粒度(d50)5.45um。
24.实施例1
‑
2实施步骤同实施例1,仅补充消化反应温度为55℃,所得到的产品的白度91.3%;含量90.4%;比表面积37.5m2/g;气孔容量0.21cm3/g;分布粒度(d50)7.15um。
25.实施例1
‑
3实施步骤同实施例1,仅补充消化反应温度为58℃,所得到的产品的白度91.8%;含量90.5%;比表面积38.5m2/g;气孔容量0.22cm3/g;分布粒度(d50)7.15um。
26.实施例1
‑
4实施步骤同实施例1,仅补充消化反应温度为70℃,所得到的产品的白度93.0%;含量93.2%;比表面积40.8m2/g;气孔容量0.22cm3/g;分布粒度(d50)7.80um。
27.实施例1
‑
5实施步骤同实施例1,仅补充消化反应温度为75℃,所得到的产品的白度89.9%;含量90.4%;比表面积34.5m2/g;气孔容量0.11cm3/g;分布粒度(d50)9.15um。
28.实施例1
‑
6实施步骤同实施例1,仅补充消化反应温度为80℃,所得到的产品的白度88.4%;含量89.4%;比表面积32.5m2/g;气孔容量0.11cm3/g;分布粒度(d50)10.12um。
29.实施例2消化:在2立方米的反应釜中加入360公斤温度为65℃工艺水,加入0.28公斤蔗糖。搅拌均匀后,加入56公斤生石灰,生石灰活性355ml/4molhcl,粒度20mm。消化反应30min,结束温度95℃,出料。
30.除杂: 消化料浆依次过200目筛网,8μm底流旋流器,除去杂质。
31.离心:除杂后料浆经离心机浓缩至质量浓度为30%。
32.干燥:使用闪蒸干燥机,控制干燥温度115℃,同时风力粉碎,制品即为高比表面积、高白度氢氧化钙,白度92.4%;含量93.7%;比表面积40.2m2/g;气孔容量0.21cm3/g;分布粒度(d50)6.88um。
33.实施例2
‑
1实施步骤同实施例1,仅消化反应结束后温度为94℃,所得到的产品的白度92.4%;含量91,7%;比表面积40.2m2/g;气孔容量0.21cm3/g;分布粒度(d50)6.58um。
34.实施例2
‑
2实施步骤同实施例1,仅消化反应结束后温度为92℃,所得到的产品的白度92.1%;含量90.2%;比表面积40.1m2/g;气孔容量0.20cm3/g;分布粒度(d50)7.04um。
35.实施例2
‑
3实施步骤同实施例1,仅消化反应结束后温度为90℃,所得到的产品的白度91.8%;含量88.7%;比表面积37.7m2/g;气孔容量0.18cm3/g;分布粒度(d50)8.26um。
36.实施例2
‑
4实施步骤同实施例1,仅消化反应结束后温度为98℃,所得到的产品的白度92.4%;含量93.7%;比表面积40.4m2/g;气孔容量0.21cm3/g;分布粒度(d50)7.18um。
37.实施例2
‑
5实施步骤同实施例1,仅消化反应结束后温度为102℃,所得到的产品的白度88.4%;含量89.7%;比表面积31.6m2/g;气孔容量0.11cm3/g;分布粒度(d50)10.34um。
38.实施例2
‑
6实施步骤同实施例1,仅消化反应结束后温度为104℃,所得到的产品的白度86.1%;含量84.6%;比表面积29.1m2/g;气孔容量0.08cm3/g;分布粒度(d50)12.10um。
39.实施例3消化:在2立方米的反应釜中加入360公斤温度为65℃工艺水,加入0.56公斤葡萄糖。搅拌均匀后,加入56公斤生石灰,生石灰活性350ml/4molhcl,粒度20mm。消化反应30min,结束温度95℃。
40.除杂: 消化料浆依次过200目筛网,8μm底流旋流器,除去杂质。
41.离心:除杂后料浆经离心机浓缩至质量浓度为30%。
42.干燥:使用闪蒸干燥机,控制干燥温度120℃,同时风力粉碎,制品即为高比表面积、高白度氢氧化钙。白度92.6%;含量93.3%;比表面积41.3m2/g;气孔容量0.23cm3/g;分布粒度(d50)4.19um。
43.实施例4消化:在2立方米的反应釜中加入360公斤温度为70℃工艺水,加入0.28公斤葡萄糖。搅拌均匀后,加入56公斤生石灰,生石灰活性350ml/4molhcl,粒度20mm。消化反应30min,结束温度98℃。
44.除杂: 消化料浆依次过200目筛网,8um底流旋流器,除去杂质。
45.离心:除杂后料浆经离心机浓缩至质量浓度为30%。
46.干燥:使用闪蒸干燥机,控制干燥温度115℃,同时风力粉碎,制品即为高比表面积、高白度氢氧化钙。白度92.7%;含量93.4%;比表面积40.1m2/g;气孔容量0.22cm3/g;分布粒度(d50)7.89um。
47.实施例5消化:在2立方米的反应釜中加入360公斤温度为65℃工艺水,加入0.28公斤焦磷酸钠。搅拌均匀后,加入56公斤生石灰,生石灰活性350ml/4molhcl,粒度20mm。消化反应30min,结束温度95℃。
48.除杂: 消化料浆依次过200目筛网,8μm底流旋流器,除去杂质。
49.离心:除杂后料浆经离心机浓缩至质量浓度为30%。
50.干燥:使用闪蒸干燥机,控制干燥温度120℃,同时风力粉碎,制品即为高比表面积、高白度氢氧化钙。白度92.1%;含量93.1%;比表面积41.8m2/g;气孔容量0.22cm3/g;分布粒度(d50)6.91um。
51.实施例6方法及步骤同实施例1,仅消化步骤中所用生石灰活性为300 ml/4molhcl。则得到的氢氧化钙。白度91.1%;含量93%;比表面积37.1m2/g;气孔容量0.2cm3/g;分布粒度(d50)5.35um。
52.实施例7方法及步骤同实施例1,仅除杂步骤中所用筛网为100目。则得到的氢氧化钙。白度90.2%;含量92.1%;比表面积36.1m2/g;气孔容量0.19cm3/g;分布粒度(d50)8.31um。
53.实施例8方法及步骤同实施例1,仅除杂步骤中所用旋流器底流为10μm。则得到的氢氧化钙。白度89.1%;含量90.4%;比表面积32.9m2/g;气孔容量0.14cm3/g;分布粒度(d50)10.03um。
54.实施例9方法及步骤同实施例1,仅干燥步骤中控制温度为125℃。则得到的氢氧化钙。白度88.1%;含量93.1%;比表面积40.4m2/g;气孔容量0.19cm3/g;分布粒度(d50)9.18um。
55.实施例10方法及步骤同实施例1,仅干燥步骤中控制温度为110℃。则得到的氢氧化钙。白度89.7%;含量91.2%;比表面积39.6m2/g;气孔容量0.28cm3/g;分布粒度(d50)7.19um。
56.实施例11
方法及步骤同实施例1,仅消化步骤中不添加任何晶型控制剂。则得到的氢氧化钙。白度92.1%;含量93.5%;比表面积30.1m2/g;气孔容量0.11cm3/g;分布粒度(d50)6.18um。
57.实施例11
‑
1方法及步骤同实施例1,消化步骤中添加晶型控制剂为焦磷酸钠,添加量未0.28公斤,则得到的氢氧化钙白度89.1%;含量93.5%;比表面积38.1m2/g;气孔容量0.14cm3/g;分布粒度(d50)9.18um。
58.比较例1在1立方米的反应釜中加入18公斤温度为50℃工艺水,加入56公斤生石灰,生石灰活性200ml/4molhcl,粒度15mm。消化反应30min,结束温度90℃,使用导热油升温至100℃干燥,产物经风选除去超径颗粒,即制的干粉状氢氧化钙产品,白度85.1%;含量90.1%;比表面积20.1m2/g;气孔容量0.08cm3/g;分布粒度(d50)10.45um。
59.比较例2在1立方米的反应釜中加入27公斤温度为50℃工艺水,加入56公斤生石灰,生石灰活性185ml/4molhcl,粒度15mm。消化反应40min,结束温度95℃,使用导热油升温至100℃干燥,产物经风选除去超径颗粒,即制的干粉状氢氧化钙产品,白度86.1%;含量89.8%;比表面积21.5m2/g;气孔容量0.09cm3/g;分布粒度(d50)11.45um。