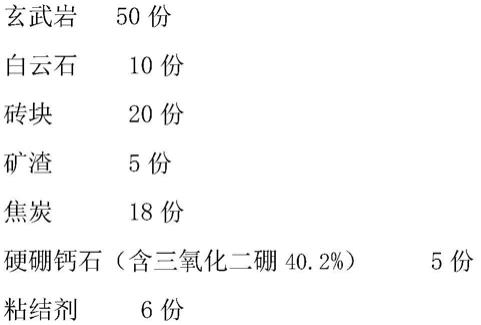
1.本发明涉及岩棉保温材料技术领域,特别是涉及一种含硼成分的岩棉及其制备方法。
背景技术:2.岩棉是性能出众的建筑保温材料,具有保温、吸音、隔热、防火、透气等性能。在已具有成熟应用技术的所有外墙外保温材料中,唯一能够完全满足我国现行国家和行业标准中a级不燃的保温材料。
3.随着岩棉产能的不断扩大,节能降耗成为企业发展的重中之重。传统岩棉产品均采用优质玄武岩、白云石等为主要原材料,经1450℃以上高温熔化后,采用国际先进的四轴离心机高速离心成纤维,同时喷入一定量粘结剂、防尘油、憎水剂,经集棉机收集、通过摆锤法工艺,然后进行固化、切割,形成不同规格和用途的岩棉产品。如何降低冲天炉生产能耗成为节能改造的重点。
4.传统岩棉制备过程中,存在熔体温度高,并且熔体温度范围窄的缺陷,造成能耗较大,同时温度不容易控制。
5.专利申请“采用红土镍矿联产镍生铁和岩棉制品的工艺”(申请号:cn201510119518.1)文件中有如下叙述:为降低熔体的粘度,配料中常掺加一定量的白云石和块状高炉冷却渣,在熔炼过程中,为降低焦炭的消耗量,还需采用加热送风、富氧送风等手段。但是玄武岩等矿石受产地限制,长距离运输会增加成本,不能普遍发展岩棉产业。为了降低能耗,专利申请“用于岩棉熔体温度多点精确控制的纯氧燃烧系统”(申请号:cn201510601219.1)采用温度多点精确控制的纯氧燃烧系统,然而,仍无法彻底解决熔体温度高和范围窄的问题。
6.可见,现有岩棉生产方面存在改进空间。
技术实现要素:7.为解决现有技术的以上缺陷,本发明提出一种含硼成分的岩棉及其制备方法,在作为保温材料的岩棉生产过程中,可有效的降低原材料的熔融温度,降低能耗,本发明采用了如下技术方案:
8.作为本发明的第一个方面,在于提供了一种含硼成分的岩棉,按重量份数计,包括以下组分:玄武岩40
‑
50份、白云石10
‑
20份、砖块20
‑
30份,矿渣5
‑
10份、焦炭10
‑
20份、含硼材料5
‑
10份,粘结剂6
‑
10份。
9.优选的,所述含硼材料为硼镁石、硼砂、硬硼钙石、硼钠解石一种或几种混合而成,含硼量在20
‑
50%。
10.更优选的,所述含硼材料为硬硼钙石。
11.优选的,所述粘结剂为酚醛树脂、氨水、憎水剂、偶联剂、软化水中的任意一种或多种混合物。
12.优选的,所述岩棉包括如下组分:
[0013][0014]
或者,优选的,所述岩棉包括如下组分:
[0015][0016]
或者,优选的,所述岩棉包括如下组分:
[0017][0018][0019]
或者,优选的,所述岩棉包括如下组分:
[0020][0021]
或者,优选的,所述岩棉包括如下组分:
[0022][0023]
优选的,所述玄武岩的的块度为100
‑
300mm,超粒度比例<10%,酸度系数>1.2,密度大于1.6g/cm3。
[0024]
优选的,所述白云石的的块度为60
‑
90mm,超粒度比例<10%。
[0025]
优选的,所述砖块的的块度为100
‑
200mm,超粒度比例<10%。所述的砖块按照如下步骤制得:砖块由回收废岩棉破碎,根据配方加入水泥进行混料,压制成型,然后进入经蒸养窑进行养护。
[0026]
其中,砖块中水泥添加比例为30
‑
45%,废棉添加比例为30
‑
40%,混料含水率在20
‑
30%。
[0027]
优选的,所述矿渣的块度为100
‑
150mm,超粒度比例<10%。
[0028]
优选的,所述焦炭的的块度为200
‑
300mm,超粒度比例<10%,热值大于6500k。
[0029]
作为本发明的第二个方面,在于提供了所述岩棉的制备方法,按照如下步骤:
[0030]
步骤1、将玄武岩、白云石、砖块、矿渣、焦炭和含硼材料按照重量比例分别称重,而后混合;
[0031]
步骤2、将混合后原料加入冲天炉中,保持冲天炉中温度在1300~1400℃范围内,使原料熔化得到熔体;
[0032]
步骤3、熔化的熔体经过四轮高速离心成纤,离心过程中喷洒粘结剂,粘结剂的喷洒量为6
‑
10份;喷洒速率2000
‑
3000l/h、喷洒温度为常温。
[0033]
步骤4、岩棉纤维经打褶加压后进入固化炉固化,而后切割,形成不同规格和用途的岩棉产品。
[0034]
与现有技术相比,本发明的有益效果是:
[0035]
本发明提供的岩棉成分及配比以及制备方法,使得岩棉生产过程中,原料的熔体温度从1450℃降至1350℃,熔体粘度在0.5
‑
2.5pas,最佳成纤温度的范围跨度随着10℃增加到40℃。同时,对含硼材料的岩棉纤维的表征表明,加入了硼材料后纤维的平均直径从5.6
±
0.45μm减至3.4
±
0.27μm,而将其抗拉强度从1700
±
80mpa增加至2100
±
100mpa。
[0036]
另外,本发明所提供的制备方法可使冲天炉的生产能耗降低10%左右,生产控制更加稳定,而且制得的岩棉制品质量提升。
具体实施方式
[0037]
为了充分说明本发明专利的制备思路和构思,在下述实施例中验证本发明说述的制备方法,这些实施例仅供举例说明和特例代表,不应被解释或理解为对本发明保护的限制。
[0038]
在本文中所披露的范围的端点和任何值都不限于该精确的范围或值,这些范围或值应当理解为包含接近这些范围或值的值。对于数值范围来说,各个范围的端点值之间、各个范围的端点值和单独的点值之间,以及单独的点值之间可以彼此组合而得到一个或多个新的数值范围,这些数值范围应被视为在本文中具体公开。
[0039]
本发明中,超粒度比例为大于或小于块度尺寸的部分所占总体的比例。
[0040]
1,本发明采用的原料均为市售产品购买所得,如没有特殊说明,可以采用如下成分的原料:
[0041][0042][0043]
硼镁石含硼量低,使用成本高;硼砂和硼钠解石的含硼成分较高,但价格较高,因此,本发明实施例采用硬硼钙石研究不同添加量的产品性能。
[0044]
憎水剂采用岩棉憎水剂瓦克化学生产的silres bs 1042;偶联剂选自岩棉用硅烷偶联剂。
[0045]
2,本实施例采用的粘结剂为水溶性酚醛树脂,固含量在30
‑
50%,游离醛含量≤0.7%,游离酚含量≤1%。粘结剂采用酚醛树脂加水稀释后使用,含量为5~20%。
[0046]
3,本实施例采用的砖块,按照如下步骤制得:
[0047]
砖块由回收废岩棉破碎,根据配方加入水泥进行混料,压制成型,然后进入经蒸养窑进行养护。
[0048]
其中,砖块中水泥添加比例为30
‑
45%,废棉添加比例为30
‑
40%,混料含水率在20
‑
30%。
[0049]
废棉主要有生产线所产生的废棉,不合格岩棉板,回收的渣球,成分与岩棉板成分
一致;砖块添加主要是解决生产线所产生的的废棉,生产线生产的不合格产品粉碎后也进行制砖,然后再次熔融成棉,废物利用
[0050]
实施例1,一种含硼成分的岩棉保温材料的生产配方
[0051]
包括以下组分:
[0052]
玄武岩50份,块度为100
‑
300mm,超粒度比例8%,酸度系数1.35,密度为1.71g/cm3;
[0053]
白云石10份,块度为60
‑
90mm,超粒度比例8%;
[0054]
砖块20份,块度为100
‑
200mm,超粒度比例3%;水泥添加比例为20%,废棉添加比例为30%,混料含水率为20%;
[0055]
矿渣5份;
[0056]
焦炭18.1份;
[0057]
硬硼钙石5份,含硼量以三氧化二硼计为36.84%;
[0058]
粘结剂6份。
[0059]
实施例2,一种含硼成分的岩棉保温材料的生产配方
[0060]
包括以下组分:
[0061]
玄武岩40份,块度为100
‑
300mm,超粒度比例9%,酸度系数1.35,密度为1.71g/cm3;
[0062]
白云石20份,块度为60
‑
90mm,超粒度比例9%;
[0063]
砖块30份,块度为100
‑
200mm,超粒度比例5%;水泥添加比例为30%,废棉添加比例为20%,混料含水率为10%;
[0064]
矿渣10份;
[0065]
焦炭17.5份;
[0066]
硬硼钙石6份;
[0067]
粘结剂6份。
[0068]
实施例3,一种含硼成分的岩棉保温材料的生产配方
[0069]
包括以下组分:
[0070]
玄武岩45份,块度为100
‑
300mm,超粒度比例6%,酸度系数1.35,密度1.71g/cm3;
[0071]
白云石10份,块度为60
‑
90mm,超粒度比例6%;
[0072]
砖块20份,块度为100
‑
200mm,超粒度比例4%;水泥添加比例为28%,废棉添加比例为15%,混料含水率为15%;
[0073]
矿渣5份;
[0074]
焦炭17.8份;
[0075]
硬硼钙石7份;
[0076]
粘结剂6份。
[0077]
实施例4,一种含硼成分的岩棉保温材料的生产配方
[0078]
包括以下组分:
[0079]
玄武岩45份,块度为100
‑
300mm,超粒度比例10%,酸度系数1.35,密度为1.71g/cm3;
[0080]
白云石10份,块度为60
‑
90mm,超粒度比例10%;
[0081]
砖块20份,块度为100
‑
200mm,超粒度比例8%;水泥添加比例为24%,废棉添加比例为18%,混料含水率为15%;
[0082]
矿渣5份;
[0083]
焦炭17.6份;
[0084]
硬硼钙石8份;
[0085]
粘结剂6份。
[0086]
实施例5,一种含硼成分的岩棉保温材料的生产配方
[0087]
包括以下组分:
[0088]
玄武岩45份,块度为100
‑
300mm,超粒度比例7%,酸度系数1.35,密度为1.71g/cm3;
[0089]
白云石10份,块度为60
‑
90mm,超粒度比例7%;
[0090]
砖块20份,块度为100
‑
200mm,超粒度比例5%;水泥添加比例为26%,废棉添加比例为18%,混料含水率为16%;
[0091]
矿渣5份;
[0092]
焦炭16.9份;
[0093]
硬硼钙石10份;
[0094]
粘结剂6份。
[0095]
对比例1:
[0096]
采用如下组分的岩棉配方为:
[0097][0098]
实施例6:岩棉的制备方法,按照如下步骤:
[0099]
步骤1、将玄武岩、白云石、砖块、矿渣、焦炭和含硼材料按照重量比例分别称重,而后混合;
[0100]
步骤2、将混合后原料加入冲天炉中,保持冲天炉中温度在1300~1500℃范围内,使原料熔化得到熔体;
[0101]
步骤3、熔化的熔体经过四轮高速离心成纤,离心过程中喷洒粘结剂,粘结剂的喷洒量6
‑
10份;喷洒速率2000
‑
3000l/h、喷洒温度为常温。
[0102]
步骤4、岩棉纤维经打褶加压后进入固化炉固化,而后切割,形成不同规格和用途的岩棉产品。
[0103]
将实施例1~5及对比例1分别按照实施例6提供的制备方法制备岩棉产品,并检测岩棉产品的抗拉强度和导热系数,结果汇总如下表所示:
[0104]
其中,岩棉成品抗拉强度检测根据岩棉标准《gb/t25975
‑
2018》。
[0105]
导热系数检测方法或标准为《gb/t25975
‑
2018》
[0106]
平均纤维直径标准为《gb/t5480
‑
2017》
[0107]
表2实施例1~5及对比例1制得的岩棉产品能耗和性能对照表
[0108] 熔体温度焦炭用量岩棉抗拉度平均纤维直径导热系数实施例11400℃
‑
1430℃18.1份197kpa4.55um0.039w/(m
·
k)实施例21390℃
‑
1415℃17.5份224kpa4.38um0.0381w/(m
·
k)实施例31385℃
‑
1412℃17.8份202kpa4.11um0.0363w/(m
·
k)实施例41368℃
‑
1398℃17.6份235kpa3.85um0.0361w/(m
·
k)实施例51350℃
‑
1390℃16.9份252kpa3.37um0.0342w/(m
·
k)对比例11450℃
‑
1460℃18.6份150kpa4.82um0.0410w/(m
·
k)
[0109]
表格中焦炭用量为提供热量的焦炭量,关系生产耗能大小。
[0110]
熔体温度为从冲天炉虹吸口出来的熔体表观温度。
[0111]
通过对比可见,采用本发明提供的含硼成分的岩棉配方和制备方法,冲天炉的生产能耗降低10%左右,生产成本明显降低,生产控制更加稳定,而且制得的岩棉制品强度增加。
[0112]
熔体粘度在0.5
‑
2.5pas时,熔体被离心所产生的岩棉纤维最好,熔体粘度过小过大,均难以成纤;熔体粘度是随着熔体温度的升高而降低的,现有技术,在熔体粘度在0.5
‑
2.5pas时,熔体温度为1450
‑
1460℃,加入适量的含硼材料,熔体粘度在0.5
‑
2.5pas时,熔体温度在1350
‑
1390℃,范围更宽,生产中更容易控制。
[0113]
分析可能的原因如下:在岩棉成分中,二氧化硅的含量占比在45%以上,含硼材料b
‑
o四面体与sio2的s
‑
o四面体直接连接,在连接过程中使原来的正四面体构型发生变化,导致sio2本身稳定性下降,从而降低其熔融温度。
[0114]
现有技术中,熔体需要升温到1450℃左右才有合适的粘度,而且范围较窄;而加入含硼材料后,熔体只需要升温到1350℃,所需要的焦炭量降低,降低能耗。
[0115]
岩棉生产过程中,由于熔体的最佳成纤的温度范围扩大,熔体粘度更稳定,因此产生的岩棉纤维更均匀。岩棉纤维均匀也降低了传热系数,主要是因为纤维均匀后,岩棉材料中空间均匀,有利于热量的散失和辐射。传热系数小,热量传递慢,保温效果好。
[0116]
以上所述仅为本发明的优选实施例而已,并不用于限制本发明,对于本领域的技术人员来说,本发明可以有各种更改和变化。凡在本发明的精神和原则之内,所作的任何修改、等同替换、改进等,均应包含在本发明的保护范围之内。