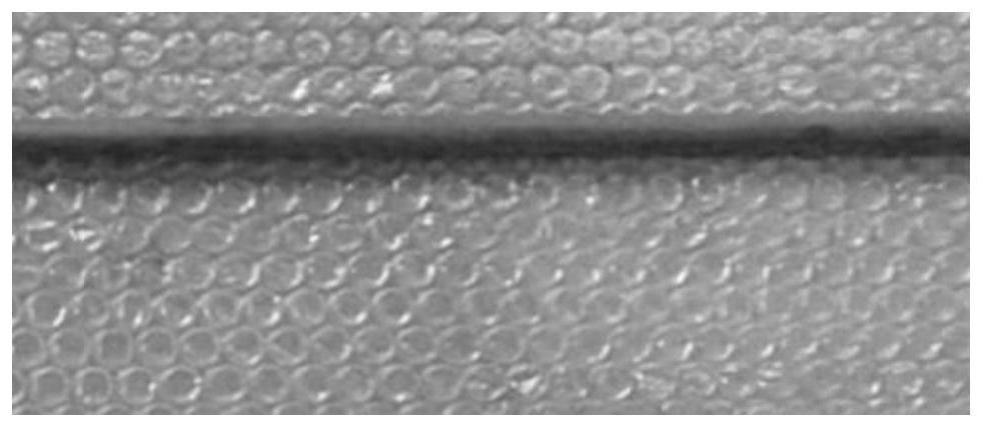
1.本发明提供一种陶瓷基复合材料细长薄壁管件及其制备方法,尤其涉及一种三层复合结构的cf/sic或sicf/sic陶瓷基复合材料管件及其制备方法与应用。
背景技术:2.在多种核反应堆型中,模块式高温气冷堆因为具有安全性好,效率高,多用途的特点,在中小型机组规模下具有极高经济竞争力。一般情况下,模块式高温气冷堆冷却剂(如:氦气)出口温度直接决定了高温气冷堆的效率,反应堆的冷却剂温度越高,就可以获得更高的发电效率。模块式高温气冷堆的堆芯类型分为柱状芯和球床芯,其中,柱状芯是将直径约为0.5mm的包覆燃料颗粒置入包壳管内,冷却剂从平行放置的包壳管阵列之间的空间流动完成换热。若包壳管采用镍基高温合金等耐高温金属材料,氦气出口温度被限制到1000℃以下,气冷堆发电绝对能效低于50%。未来若要将气冷堆应用于特种飞行器小型核动力系统、空间站及深空探测器的能源系统时,耐高温金属材料包壳管不仅存在重量大,而且存在高温机械性能下降等问题,严重影响气冷堆系统的比效率,使得气冷堆潜力不能完全发挥。采用耐温性更好、高温性能不下降、低密度的cf/sic或sicf/sic陶瓷基复合材料作为高温气冷堆柱状堆芯包壳管,可以将气冷堆的冷却剂出口温度至1000℃以上,提升发电绝对能效的同时,可将气冷堆系统减重30~50%,提高气冷堆系统比效率。
3.除了气冷堆,现行压水堆用核燃料锆合金包壳管存在断电事故中锆材与冷却水之间的锆水反应引发爆炸的风险,以及锆合金在事故中脆断造成核燃料泄漏的风险。近年来,sicf/sic陶瓷基复合材料因其高温性能稳定,不发生脆断、耐中子辐照,高温下不与水发生反应等优点成为耐事故燃料包壳管的优选材料。
4.然而,气冷堆燃料包壳管长度大于等于800mm,直径小于等于30mm,壁厚在1~2mm之间,压水堆燃料包壳管长度约4000mm,直径小于105mm,壁厚在0.8~1mm之间,目前无法实现如此超长径比,超薄壁厚cf/sic或sicf/sic陶瓷基复合材料纤维预制体的成型;而且,燃料包壳管对气密性要求极高,现行的化学气相渗透法制备cf/sic或sicf/sic陶瓷基复合材料的残余气孔率一般在10%~15%左右,气密性较低,无法达到堆外考核要求,且入堆考核要求更高,难度更大。
技术实现要素:5.本发明的目的是:克服现有方法无法实现超长径比、超薄壁厚cf/sic或sicf/sic陶瓷基复合材料纤维预制体成型以及现有方法制备的cf/sic或sicf/sic陶瓷基复合材料因残余气孔率较大,无法达到堆外及入堆考核要求的问题,提供一种超长径比、超薄壁厚的陶瓷基复合材料管件的制备方法,还相应提供一种基于上述方法制备的陶瓷基复合材料细长薄壁管件,满足气冷堆用燃料包壳管和压水堆用燃料包壳管相关考核要求和应用要求。
6.为解决上述技术问题,本发明所采用以下技术方案:
7.一种陶瓷基复合材料细长薄壁管件的制备方法,其特殊之处在于,包括如下步骤:
8.步骤1、制备cf/sic或sicf/sic复材管件,作为陶瓷基复合材料细长薄壁管件的中间层;
9.步骤1.1、在管状或棒状芯模上后缠卷1~1.5mm厚的纸层;
10.步骤1.2、在纸层上缠卷c纤维布或sic纤维布,缠卷厚度为中间层设计厚度的1.2~1.5倍,形成管状纤维预制体;
11.步骤1.3、将管状纤维预制体置于模壁上开孔的石墨外模中,随后将芯模抽出,采用化学气相渗透法在管状纤维预制体上制备热解碳界面,形成含热解碳界面的管状纤维预制体;
12.步骤1.4、清除含热解碳界面的管状纤维预制体内芯部已经碳化的纸屑,以三氯甲基硅烷为先驱体,利用化学气相渗透法制备sic基体,至管件孔隙率降低至15%以内,去除石墨外模,形成陶瓷基复合材料细长薄壁管件的中间层;
13.步骤2、陶瓷基复合材料细长薄壁管件的中间层加工;
14.采用无心磨对陶瓷基复合材料细长薄壁管件的中间层外表面进行加工,采用纱线、磨棒等对陶瓷基复合材料细长薄壁管件的中间层内表面进行加工;
15.步骤3、配制sic晶须浆料,将加工后的陶瓷基复合材料细长薄壁管件的中间层浸渍到sic晶须浆料中,进行致密化;
16.步骤4、在致密后的陶瓷基复合材料细长薄壁管件的中间层内壁和外壁分别制备sic陶瓷内层及sic陶瓷外层;
17.将涂有sic晶须的陶瓷基复合材料细长薄壁管件的中间层置于化学气相炉中,化学气相渗透法,以三氯甲基硅烷为陶瓷先驱体,在中间层内外表面沉积sic,形成管件sic陶瓷内层及sic陶瓷外层;
18.步骤5、对步骤4制备完成的管件内层及外层进行抛光。
19.进一步地,为保证sic基体在细长管件中的渗透均匀性,步骤1.4中,化学气相渗透法制备sic基体的条件为:气压2.5
±
0.5kpa,温度1000
±
20℃,鼓泡氢气和氩气流量1.7
±
0.2l/min,稀释氢气1.0
±
0.2l/min。
20.进一步地,为封堵化学气相过程中无法填封纤维预制体孔洞,提高cf/sic或sicf/sic复材中间层的致密度,步骤3中所述的sic晶须直径为0.2~1.5μm,所述sic晶须浆料黏度为1.8~2.4pa
·
s。
21.进一步地,步骤3中,进行致密化的步骤具体为:
22.步骤3.1、将加工后的陶瓷基复合材料细长薄壁管件的中间层浸渍到sic晶须浆料中2~3min,进行致密化,然后烘干;
23.步骤3.2、再次重复步骤3.12~3次。
24.进一步地,步骤4中,化学气相渗透法制备sic陶瓷内层或sic陶瓷外层的条件为:气压2.0
±
0.5kpa,温度1200
±
20℃,时间120h,鼓泡氢气和氩气流量1.7
±
0.2l/min,稀释氢气1.0
±
0.2l/min。
25.进一步地,为避免细长芯模在使用过程中意外折断,影响预制体成型,步骤1.1中所述的管状或棒状芯模为不锈钢或铝合金。
26.本发明还提供一种陶瓷基复合材料细长薄壁管件,其特殊之处在于:采用上述制
备方法制备,管壁由内到外依次为sic陶瓷内层、cf/sic或sicf/sic复材中间层和sic陶瓷外层;所述sic陶瓷内层厚度为50
±
10μm,cf/sic或sicf/sic复材中间层厚度为0.7mm~2mm,sic陶瓷外层厚度为50
±
10μm;所述管件的长度为300~4000mm,外径为9.5~29mm。
27.本发明还提供一种上述陶瓷基复合材料细长薄壁管件作为气冷堆燃料包壳管及压水堆燃料包壳管的应用。
28.本发明的优点是:
29.1、本发明中“sic陶瓷内层+cf/sic或sicf/sic复材中间层+sic陶瓷外层”的三层结构,以及内、外壁加工后进行sic晶须浸渍的工序可极大提高陶瓷基复合材料细长薄壁管件的气密性;
30.2、本发明中cf/sic或sicf/sic复材中间层、sic陶瓷内层、外层都采用化学气相沉积法制备,使用的设备都为化学气相炉,仅通过调节设备进气参数和气压等参数就可互换使用,过程简单、经济高效;
31.3、本发明中,“采用不锈钢或铝合金管材和棒材作为芯模,并在芯模上首先缠卷1~1.5mm后的纸层,后缠卷碳纤维布或碳化硅纤维布,且在复材中间层界面沉积前使用外模固型,并抽出芯模,保留纸层在芯部”的成型方案,首先1)不锈钢或铝合金材质的芯模不会像石墨材质的芯模一样因为管件过长而折断;2)在芯模上缠卷纸层有利于退除芯模,并且会在芯模退除后,纤维预制体内型仍可以保证;3)采用纤维布缠卷成型管件预制体,工艺难度低,而且相比编织成型,成本极低。
附图说明
32.图1 300mm sicf/sic陶瓷基复合材料细长薄壁管件实物图;
33.图2 1200mm sicf/sic陶瓷基复合材料细长薄壁管件实物图;
具体实施方式
34.以下结合具体实施例对本发明进行详细说明。
35.实施例一
36.本实施例针对sicf/sic复材中间层厚度为0.7mm,sic陶瓷内层厚度为50
±
10μm,sic陶瓷外层厚度为50
±
10μm,长为300mm,外径为9.50mm的sicf/sic管件制备。
37.选择外径合适,300mm长的不锈钢管状或棒状芯模上先后缠卷1mm厚的纸层(离心纸或牛皮纸等)和1.05mm厚度的sic纤维布,形成300mm长管状纤维预制体;将管状纤维预制体至于石墨外模中(该石墨外模的模壁上均布直径为2-3mm的孔),随后将芯模抽出,采用化学气相渗透法在管状纤维预制体上制备150
±
20nm厚度的热解碳界面,形成含界面的管状纤维预制体;清除纤维预制体内芯部已经碳化的纸屑,以三氯甲基硅烷为先驱体,利用化学气相渗透法制备sic基体,化学气相渗透法制备sic基体的条件为:气压2.5
±
0.5kpa,温度1000
±
20℃,鼓泡氢气和氩气流量1.7
±
0.2l/min,稀释氢气1.0
±
0.2l/min。管件孔隙率降低至15%以内后,去除石墨外模,形成管件sicf/sic复材中间层。
38.采用无心磨对管件sicf/sic复材中间层将外径加工至9.40mm,采用纱线、磨棒等对管件sicf/sic复材中间层内径加工至8.00mm。
39.用sic晶须直径为1.5μm,配制黏度为2.4pa
·
ssic晶须浆料,将管件sicf/sic复材
中间层浸渍到sic晶须浆料中3min,然后烘干,反复3次,进行致密化。
40.将涂有sic晶须的sicf/sic复材中间层管件置于化学气相炉中,以三氯甲基硅烷为陶瓷先驱体,沉积条件为:气压2.0
±
0.5kpa,温度1200
±
20℃,时间120h,鼓泡氢气和氩气流量1.7
±
0.2l/min,稀释氢气1.0
±
0.2l/min,在中间层内外表面沉积sic,形成管件sic陶瓷内层及sic陶瓷外层。
41.将管件sic陶瓷内径抛光至7.9mm,sic陶瓷外层抛光至9.50mm。
42.如图1所示,为制备完成的300mm sicf/sic陶瓷基复合材料细长薄壁管件实物图;所制备sicf/sic管件的气密性采用氦检泄漏率进行表征,经检测,氦检泄漏率小于1
×
10-8
pa
·
m3/s,比原技术提高一个数量级。
43.实施例二
44.本实施例针对cf/sic复材中间层厚度为2mm,sic陶瓷内层厚度为50
±
10μm,sic陶瓷外层厚度为50
±
10μm,长为950mm,外径为29.00mm的cf/sic管件制备。
45.选择外径合适,950mm长的铝合金管状芯模上先后缠卷1.5mm厚的离心纸和2.5mm厚度的sic纤维布,形成950mm长管状纤维预制体;将管状纤维预制体至于石墨外模中(该石墨外模的模壁上均布直径为2-3mm的孔),随后将芯模抽出,采用化学气相渗透法在管状纤维预制体上制备150
±
20nm厚度的热解碳界面,形成含界面的管状纤维预制体;清除纤维预制体内芯部已经碳化的离心纸,以三氯甲基硅烷为先驱体,利用化学气相渗透法制备sic基体,化学气相渗透法制备sic基体的条件为:气压2.5
±
0.5kpa,温度1000
±
20℃,鼓泡氢气和氩气流量1.7
±
0.2l/min,稀释氢气1.0
±
0.2l/min。管件孔隙率降低至15%以内后,去除石墨外模,形成管件sicf/sic复材中间层。
46.采用无心磨对管件cf/sic复材中间层将外径加工至28.90mm,采用纱线、磨棒等对管件cf/sic复材中间层内径加工至24.90mm。
47.用sic晶须直径为0.2μm,配制黏度为1.8pa
·
ssic晶须浆料,将管件cf/sic复材中间层浸渍到sic晶须浆料中2min,然后烘干,反复2次,进行致密化。
48.将涂有sic晶须的cf/sic复材中间层管件置于化学气相炉中,以三氯甲基硅烷为陶瓷先驱体,沉积条件为:气压2.0
±
0.5kpa,温度1200
±
20℃,鼓泡氢气和氩气流量1.7
±
0.2l/min,稀释氢气1.0
±
0.2l/min,在中间层内外表面沉积sic,形成管件sic陶瓷内层及sic陶瓷外层。
49.将管件sic陶瓷内径抛光至24.80mm,sic陶瓷外层抛光至29.00mm。
50.所制备cf/sic管件的气密性采用氦检泄漏率进行表征,经检测,氦检泄漏率小于1
×
10-8
pa
·
m3/s,比原技术提高一个数量级。
51.实施例三
52.sicf/sic复材中间层厚度为0.7mm,sic陶瓷内层厚度为50
±
10μm,sic陶瓷外层厚度为50
±
10μm,长为1200mm,外径为9.50mm的sicf/sic管件制备。。
53.选择外径合适,1200mm长的铝合金棒状芯模上先后缠卷1mm厚的离心纸和1.05mm厚度的sic纤维布,形成1200mm长管状纤维预制体;将管状纤维预制体至于石墨外模中(该石墨外模的模壁上均布直径为2-3mm的孔),随后将芯模抽出,采用化学气相渗透法在管状纤维预制体上制备150
±
20nm厚度的热解碳界面,形成含界面的管状纤维预制体;清除纤维预制体内芯部已经碳化的离心纸,以三氯甲基硅烷为先驱体,利用化学气相渗透法制备sic
基体,化学气相渗透法制备sic基体的条件为:气压2.5
±
0.5kpa,温度1000
±
20℃,鼓泡氢气和氩气流量1.7
±
0.2l/min,稀释氢气1.0
±
0.2l/min。管件孔隙率降低至15%以内后,去除石墨外模,形成管件sicf/sic复材中间层。
54.采用无心磨对管件sicf/sic复材中间层将外径加工至9.4mm,采用纱线、磨棒等对管件sicf/sic复材中间层内径加工至7.6mm。
55.用sic晶须直径为1.5μm,配制黏度为2.4pa
·
ssic晶须浆料,将管件sicf/sic复材中间层浸渍到sic晶须浆料中2min,然后烘干,反复3次,进行致密化。
56.将涂有sic晶须的sicf/sic复材中间层管件置于化学气相炉中,以三氯甲基硅烷为陶瓷先驱体,沉积条件为:气压2.0
±
0.5kpa,温度1200
±
20℃,时间120h,鼓泡氢气和氩气流量1.7
±
0.2l/min,稀释氢气1.0
±
0.2l/min,在中间层内外表面沉积sic,形成管件sic陶瓷内层及sic陶瓷外层。
57.将管件sic陶瓷内径抛光至7.50mm,sic陶瓷外层抛光至9.50mm。
58.如图2所示,为制备完成的1200mm sicf/sic陶瓷基复合材料细长薄壁管件实物图;所制备sicf/sic管件的气密性采用氦检泄漏率进行表征,经检测,氦检泄漏率小于1
×
10-8
pa
·
m3/s,比原技术提高一个数量级。
59.实施例四
60.sicf/sic复材中间层厚度为0.7mm,sic陶瓷内层厚度为50
±
10μm,sic陶瓷外层厚度为50
±
10μm,长为4000mm,外径为9.50mm的sicf/sic管件制备。。
61.选择外径合适,4000mm长的铝合金棒状芯模上先后缠卷1mm厚的离心纸和1.05mm厚度的sic纤维布,形成4000mm长管状纤维预制体;将管状纤维预制体至于石墨外模中(该石墨外模的模壁上均布直径为2-3mm的孔),随后将芯模抽出,采用化学气相渗透法在管状纤维预制体上制备150
±
20nm厚度的热解碳界面,形成含界面的管状纤维预制体;清除纤维预制体内芯部已经碳化的离心纸,以三氯甲基硅烷为先驱体,利用化学气相渗透法制备sic基体,化学气相渗透法制备sic基体的条件为:气压2.5
±
0.5kpa,温度1000
±
20℃,鼓泡氢气和氩气流量1.7
±
0.2l/min,稀释氢气1.0
±
0.2l/min。管件孔隙率降低至15%以内后,去除石墨外模,形成管件sicf/sic复材中间层。
62.采用无心磨对管件sicf/sic复材中间层将外径加工至9.40mm,采用纱线、磨棒等对管件sicf/sic复材中间层内径加工至8.00mm。
63.用sic晶须直径为1.5μm,配制黏度为2.4pa
·
ssic晶须浆料,将管件sicf/sic复材中间层浸渍到sic晶须浆料中3min,然后烘干,反复3次,进行致密化。
64.将涂有sic晶须的sicf/sic复材中间层管件置于化学气相炉中,以三氯甲基硅烷为陶瓷先驱体,沉积条件为:气压2.0
±
0.5kpa,温度1200
±
20℃,时间120h,鼓泡氢气和氩气流量1.7
±
0.2l/min,稀释氢气1.0
±
0.2l/min,在中间层内外表面沉积sic,形成管件sic陶瓷内层及sic陶瓷外层。
65.将管件sic陶瓷内径抛光至7.90mm,sic陶瓷外层抛光至9.50mm。
66.所制备sicf/sic管件的气密性采用氦检泄漏率进行表征,经检测,氦检泄漏率小于1
×
10-8
pa
·
m3/s,比原技术提高一个数量级。