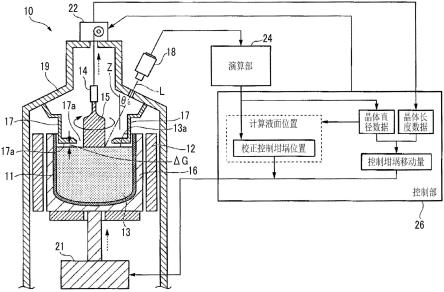
1.本发明涉及一种用于通过柴可拉斯基(czochralski)法(以下,称为cz法)制造单晶的单晶制造装置及单晶的制造方法,尤其涉及一种晶体提拉工序中的单晶的直径测量。
背景技术:2.作为半导体器件的基板材料的硅晶片大多通过cz法制造。在cz法中,通过在石英坩埚内加热多晶硅原料而生成硅熔液,并使籽晶从硅熔液上方下降而浸渍于硅熔液之后,一边使籽晶及石英坩埚旋转一边使籽晶缓缓上升,从而在籽晶下方生长大的单晶。根据cz法,能够以高产率制造大口径的单晶硅。
3.以某直径为目标而制造单晶锭。例如,若最终产品为300mm的晶片,则通常会生长比其直径稍微大的305~320mm的单晶锭。之后,单晶锭的外周被磨削成圆柱状,并切成晶片状之后,经过倒角工序,最终成为目标直径的晶片。如此,单晶锭的目标直径必须大于最终产品的晶片直径,但若太大,则会增加磨削研磨费用而变得不经济。因此,要求一种比晶片大且直径尽量小的单晶锭。
4.在cz法中,一边控制晶体提拉条件一边提拉单晶,以使晶体直径恒定。关于单晶的直径控制,例如专利文献1中记载有如下方法:通过处理单晶与熔液的界面的图像来准确地测量生长的单晶直径。在该方法中,控制坩埚旋转速度、晶体旋转速度、晶体提拉速度、坩埚上升速度及熔液的温度(加热器功率)等,以使单晶直径成为目标的直径。
5.并且,专利文献2关于熔液面位置的测量,记载有如下方法:用设置于腔室外侧的相机拍摄到腔室内的炉内结构物及熔液的液面时,计算显现于拍摄图像中的炉内结构物的实像及镜像的代表尺寸。该方法中,检测拍摄图像中显现的炉内结构物的实像及在熔液的液面上映照的炉内结构物的镜像各自的边缘图案,根据相机的设置角度及焦距,将炉内结构物的实像及镜像各自的边缘图案投影转换至基准平面上,进行对于基准平面上的炉内结构物的实像及镜像各自的边缘图案的图案匹配时,根据匹配率成为最大的基准图案形状来计算炉内结构物的实像及镜像各自的代表尺寸。现有技术文献专利文献
6.专利文献1:日本专利第4253123号公报专利文献2:日本特开第2018-90451号公报
技术实现要素:发明所要解决的技术问题
7.利用cz法的单晶提拉控制中,根据设置在炉外的相机的拍摄图像测量单晶直径,并进行单晶的直径控制,以使直径的测量值与直径轮廓一致,因此要求高精度的直径测量。如图8所示,以往的直径测量方法中,在相机图像中设定水平方向的直径测量用扫描线sl,根据该扫描线sl上的亮度分布与阈值th(切片级别,slice level)的交点来检测熔合环
(fusion ring)fr的边缘。接着,利用扫描线sl与熔合环fr的边缘的两个交点p
l
、pr之间的宽度w以及晶体中心位置c0至扫描线sl的距离h,求出熔合环的直径d=2(w2+4h2)
1/2
。由于如此求出的熔合环的直径d的单位是像素(pixel),因此通过直径d乘以直径换算系数来求出转换成实际单位(mm)的晶体直径值。
8.如此,由于从相机图像获得的晶体直径的信息是像素(pixel),因此需要将其转换成实际的直径单位(mm)。但是,由于单位转换中使用的直径换算系数是根据操作员在单晶提拉工序中用望远镜目测测量而得的晶体直径值来创建的直径换算系数,因此存在单位转换的精度差且直径计算误差大的问题。
9.因此,本发明的目的在于提供一种能够提高晶体直径的测量精度的单晶制造装置及制造方法。用于解决技术问题的方案
10.为了解决上述课题,根据本发明的单晶制造装置的特征在于,包括:单晶提拉部,从熔液提拉单晶;相机,拍摄在所述熔液与所述单晶的边界部产生的熔合环;及演算部,处理所述相机的拍摄图像,所述演算部根据所述相机的设置角度及焦距,将显现于所述相机的拍摄图像中的所述熔合环投影转换至相当于所述熔液的液面的基准平面上,并根据所述基准平面上的所述熔合环的形状来计算所述单晶的直径。
11.根据本发明,无需使用用于单位转换根据相机的拍摄图像求出的直径测量值的直径换算系数,便能够准确地求出单晶的实际直径。因此,能够提高晶体提拉工序中的单晶直径的测量精度。
12.在本发明中,所述演算部优选将基于相对于所述拍摄图像的亮度分布的规定阈值而检测到的所述熔合环的边缘图案投影转换至所述基准平面上。由此,能够准确地掌握熔合环的形状。
13.在本发明中,所述阈值为所述拍摄图像中的亮度峰值乘以小于1的值而获得的值,所述演算部优选在所述拍摄图像中设定与所述熔合环交叉的水平扫描线,并检测所述水平扫描线上的亮度分布与所述阈值的外侧交点(拍摄图像的靠近外周的一点)作为所述熔合环的边缘图案。
14.在本发明中,所述演算部优选根据投影在所述基准平面上的所述熔合环的边缘图案与规定直径测量线的两个交点之间的距离以及所述单晶中心位置至所述直径测量线的距离来计算所述单晶的直径。由此,能够几何计算熔合环的直径,并能够根据熔合环的直径来计算单晶的直径。
15.在本发明中,所述演算部优选对所述熔合环的边缘图案进行圆近似,并根据所述熔合环的近似圆的直径来计算所述单晶的直径。由此,能够提高熔合环直径的测量精度。
16.在本发明中,所述演算部优选通过从所述单晶在提拉工序中的直径减去规定的校正量、或者通过所述单晶在提拉工序中的直径乘以规定的校正系数来计算所述单晶在室温下的直径。由此,能够根据室温下的单晶直径来控制晶体直径。
17.在本发明中,所述演算部优选根据炉内结构、所述液面的位置或所述单晶的长度变化来改变所述校正量或所述校正系数。由此,能够根据单晶的生长状况的变化,准确地测量晶体直径。
18.并且,根据本发明的单晶制造方法,其为利用cz法的单晶的制造方法,其特征在
于,包括:用相机拍摄在熔液与单晶的边界部产生的熔合环的步骤;及处理所述相机的拍摄图像以计算所述单晶的直径的步骤,计算所述单晶的直径的步骤中,根据所述相机的设置角度及焦距,将显现于所述相机的拍摄图像中的所述熔合环投影转换至相当于所述熔液的液面的基准平面上,并根据所述基准平面上的所述熔合环的形状来计算所述单晶的直径。
19.根据本发明,无需使用用于单位转换根据相机的拍摄图像求出的直径测量值的直径换算系数,便能够准确地求出单晶的实际直径。因此,能够提高晶体提拉工序中的单晶直径的测量精度。
20.在本发明中,计算所述单晶的直径的步骤中,优选将基于相对于所述拍摄图像的亮度分布的规定阈值而检测到的所述熔合环的边缘图案投影转换至所述基准平面上。由此,能够准确地掌握熔合环的形状。
21.在本发明中,所述阈值为所述拍摄图像中的亮度峰值乘以小于1的值而获得的值,计算所述单晶的直径的步骤中,优选在所述拍摄图像中设定与所述熔合环交叉的水平扫描线,并检测所述水平扫描线上的亮度分布与所述阈值的外侧交点(拍摄图像的靠近外周的一点)作为所述熔合环的边缘图案。
22.在本发明中,计算所述单晶的直径的步骤中,优选根据投影在所述基准平面上的所述熔合环的边缘图案与规定直径测量线的两个交点之间的距离以及所述单晶中心位置至所述直径测量线的距离来计算所述单晶的直径。由此,能够几何计算熔合环的直径,并能够根据熔合环的直径来计算单晶的直径。
23.在本发明中,计算所述单晶的直径的步骤中,优选对所述熔合环的边缘图案进行圆近似,并根据所述熔合环的近似圆的直径来计算所述单晶的直径。由此,能够提高熔合环直径的测量精度。
24.在本发明中,计算所述单晶的直径的步骤中,优选通过从所述单晶在提拉工序中的直径减去规定的校正量、或者通过所述单晶在提拉工序中的直径乘以规定的校正系数来计算所述单晶在室温下的直径。由此,能够根据室温下的单晶直径来控制晶体直径。
25.在本发明中,计算所述单晶的直径的步骤中,优选根据炉内结构、所述液面的位置或所述单晶的长度变化来改变所述校正量或所述校正系数。由此,能够根据单晶的生长状况的变化,准确地测量晶体直径。发明效果
26.根据本发明,能够提供可以提高晶体直径的测量精度的单晶制造装置及制造方法。
附图说明
27.图1是表示本发明的实施方式的单晶制造装置的结构的概略剖视图。图2是用于说明使用单晶制造装置的单晶硅的制造方法的流程图。图3是表示通过图2的制造方法制造的单晶硅锭的形状的侧视图。图4是相机18的拍摄图像,是用于说明在固液界面产生的熔合环的图。图5是用于说明将拍摄图像的二维坐标投影转换为实际空间的坐标的方法的示意图。图6是用于说明本实施方式的直径计算方法的图。
图7是用于说明根据隔热构件17的实像ma及镜像mb各自的开口半径rf、rm来计算间隙值δg的方法的示意图。图8是用于说明以往的直径计算方法的图。
具体实施方式
28.以下,一边参考附图,一边详细地说明本发明的优选的实施方式。另外,以下所示的实施方式,是为了更充分地理解发明的主旨而具体说明的,除非另有指定,否则并不限定本发明。并且,在以下说明中所使用的附图中,为了易于理解本发明的特征,为了方便,有时放大表示主要部分,各构成要素的尺寸比例等不一定与实际相同。
29.图1是表示本发明的实施方式的单晶制造装置的结构的概略剖视图。
30.如图1所示,单晶制造装置10为用于生长单晶硅的装置,其具备大致圆筒形的腔室19,在腔室19的内部设置有积存硅熔液13的石英坩埚11。腔室19例如只要是在内部形成有一定的间隙的双层壁结构即可,通过使冷却水流过该间隙,可以防止加热石英坩埚11时的腔室19的高温化。
31.从单晶硅提拉开始之前至结束之后,向这样的腔室19的内部,导入氩气等非活性气体。在腔室19的顶部设置有提拉驱动装置22。提拉驱动装置22一边使成为单晶硅锭15的生长核的籽晶14及从籽晶14生长的单晶硅锭15旋转,一边将其向上方提拉。在这样的提拉驱动装置22中,可以形成有根据单晶硅锭15的提拉量传输单晶硅锭15的晶体长度信息的传感器(未图示)。提拉驱动装置22与控制部26连接,晶体长度信息被传送至控制部26。在本实施方式中,石英坩埚11等腔室19内的构成要素及提拉驱动装置22构成单晶提拉部。
32.在腔室19的内部设置有以包围石英坩埚11的方式配置的大致圆筒形加热器12。加热器12加热石英坩埚11。在该加热器12的内侧,收纳有坩埚支撑体(石墨坩埚)16及石英坩埚11。石英坩埚11为其整体由石英一体形成且上方为开放面的大致圆筒形的容器。
33.在石英坩埚11中积存有熔融固体硅而成的硅熔液13。坩埚支撑体16例如其整体由石墨形成,且以包裹石英坩埚11的方式密合支撑。坩埚支撑体16维持硅熔融时软化的石英坩埚11的形状,并起到支撑石英坩埚11的作用。
34.在坩埚支撑体16的下侧设置有坩埚升降装置21。坩埚升降装置21从下侧支撑坩埚支撑体16及石英坩埚11,并且使石英坩埚11上下移动,以使随着单晶硅锭15的提拉而变化的硅熔液13的熔液面13a的液面位置成为适当的位置。由此,控制硅熔液13的熔液面13a的位置。坩埚升降装置21同时在提拉时能够以规定的转速旋转支撑坩埚支撑体16及石英坩埚11。
35.在石英坩埚11的上表面,以覆盖硅熔液13的上表面(即熔液面13a)的方式形成有隔热构件(遮蔽筒)17。隔热构件17例如由形成为研钵状的隔热板构成,在其下端形成有大致圆形的开口17a。并且,隔热构件17的上端的外侧缘部固定在腔室19的内表面侧。
36.这样的隔热构件17防止被提拉的单晶硅锭15从石英坩埚11内的硅熔液13受到辐射热而改变热历史而使品质恶化。并且,这样的隔热构件17通过将导入到腔室19的内部的提拉气氛气体从单晶硅锭15侧引导至硅熔液13侧,控制硅熔液13的熔液面13a附近的残留氧气量、从硅熔液13蒸发的硅蒸气、sio等,从而使单晶硅锭15达到目标品质。认为,这种提拉气氛气体的控制依赖于炉内压力及通过隔热构件17的下端与硅熔液13的熔液面13a的间
隙时的流速。需要准确地设定隔热构件17的下端至硅熔液13的熔液面13a为止的距离(间隙值)δg,以使单晶硅锭15达到目标品质。另外,作为提拉气氛气体,在氩气等非活性气体中,能够含有氢气、氮气或除此以外的规定气体作为掺杂剂气体。
37.在腔室19的外侧设置有相机18。相机18例如是ccd相机,通过形成于腔室19的观察窗拍摄腔室19内。相机18的设置角度θc相对于单晶硅锭15的提拉轴z成为规定角度,相机18具有相对于铅垂方向倾斜的光轴l。换言之,相机18的设置角度θc是指相对于铅垂方向的光轴l的倾斜角。相机18对包括隔热构件17的开口17a及熔液面13a的石英坩埚11的上表面区域从斜上方进行拍摄。相机18与演算部24连接,相机18的拍摄图像在演算部24中用于检测晶体直径及液面位置。
38.演算部24根据包括由相机18拍摄的隔热构件17的实像及在硅熔液13的熔液面13a上映出的隔热构件17的镜像的图像来计算硅熔液13的液面位置。并且,演算部24根据包括由相机18拍摄的硅熔液13与单晶硅锭15的边界部的图像来计算单晶硅锭的直径。演算部24与控制部26连接,由演算部24将演算结果传送至控制部26。
39.控制部26根据从提拉驱动装置22的传感器获得的单晶硅锭15的晶体长度数据及由演算部24计算出的晶体直径数据来控制石英坩埚11的移动量(上升量)。为了进一步控制石英坩埚11的移动量,控制部26根据由演算部24计算出的硅熔液13的液面位置,进行石英坩埚11的位置校正控制。
40.图2是用于说明使用单晶制造装置10的单晶硅的制造方法的流程图。并且,图3是表示通过图2的制造方法制造的单晶硅锭的形状的侧视图。
41.如图2所示,在单晶硅的制造中,首先将作为原料的多晶硅投入到石英坩埚11中,利用加热器12加热并熔融石英坩埚11内的多晶硅,以生成硅熔液13(步骤s11)。
42.接着,使籽晶14下降而着落在硅熔液13上(步骤s12)。之后,实施一边维持与硅熔液13的接触状态一边缓缓提拉籽晶14而使单晶生长的晶体提拉工序(步骤s13~s16)。
43.在晶体提拉工序中,依次实施:缩颈工序s13,为了无位错化而形成晶体直径被缩小的颈部15a;肩部生长工序s14,形成晶体直径缓缓变大的肩部15b;直体部生长工序s15,形成晶体直径维持在规定的直径(例如约300mm)的直体部15c;及尾部生长工序s16,形成晶体缓缓变小的尾部15d,最终单晶从熔液面分离。根据以上,完成具有颈部15a、肩部15b、直体部15c及尾部15d的图3所示的单晶硅锭15。
44.在晶体提拉工序中,根据相机18的拍摄图像来计算硅熔液13的熔液面13a与隔热构件17之间的间隙值δg,并由此计算硅熔液13的液面位置。然后,根据该间隙值δg来控制坩埚的上升量。由此,从单晶硅的提拉开始至提拉结束之间,无论硅熔液13是否减少,使相对于加热器12、隔热构件17等炉内结构物的熔液面13a的位置保持恒定或改变,由此能够控制对硅熔液13的热的辐射分布。
45.并且,在晶体提拉工序中,根据相机18的拍摄图像来计算单晶的直径,并控制晶体提拉条件,以使晶体直径成为与晶体长度对应的规定直径。在肩部生长工序s14中控制为使晶体直径缓缓变大,在直体部生长工序s15中控制为使晶体直径恒定,在尾部生长工序s16中控制为使晶体直径缓缓变小。晶体提拉条件的控制对象是石英坩埚11的高度位置、晶体提拉速度、加热器输出等。关于使用相机18的拍摄图像的提拉条件的控制,将在晶体提拉工序中进行。具体而言,从图2中的缩颈工序s13的开始至尾部生长工序s16的结束之间进行。
46.接着,关于根据相机18的拍摄图像来计算晶体直径的方法,详细地进行说明。
47.图4是相机18的拍摄图像,是用于说明在固液界面产生的熔合环的图。
48.如图4所示,硅熔液13能够通过隔热构件17的开口17a窥视,拍摄图像中映入隔热构件17的一部分。并且,在隔热构件17的开口17a的内侧有单晶硅15,还能够从隔热构件17与单晶硅15之间的微小的间隙窥视硅熔液13。此外,在单晶硅15与硅熔液13的边界部产生熔合环fr。熔合环fr是由来自加热器12等的辐射光在固液界面的弯月面(meniscus)反射而产生的环状的高亮度区域。在拍摄图像中,由于隔热构件17固定在腔室19,因此其位置不变,但熔合环fr的位置或大小根据晶体直径、液面位置的变化而变化。在液面位置为恒定的情况下,晶体直径越大,熔合环fr也变得越大。并且,在晶体直径为恒定的情况下,液面位置越下降,晶体直径变得越小。如此,由于能够从熔合环fr捕捉固液界面附近的单晶轮廓,因此能够计算单晶的直径。
49.在硅熔液13的熔液面13a上映入隔热构件17的镜像mb。隔热构件17的镜像mb根据隔热构件17至熔液面13a的距离而变化。因此,隔热构件17的实像ma与在熔液面13a上映照的镜像mb的间隔,与随着晶体生长的硅熔液13的消耗、石英坩埚11的升降而引起的熔液面13a的上下移动联动,但熔液面13a的位置在该实像ma与镜像mb之间的中间点。因此,例如,若使熔液面13a与隔热构件17的下端一致,则隔热构件17的实像ma与镜像mb的间隔会成为零,若缓缓下降熔液面13a,则隔热构件17的下端至熔液面13a的距离(间隙值)δg也会缓缓扩大。此时的间隙值δg,能够作为隔热构件17的实像ma与镜像mb的间隔d的1/2的值(即,d=δg
×
2)来计算。如此,硅熔液13的液面位置能够作为距隔热构件17的下端的距离而求出。
50.在从熔合环fr测量单晶的直径的情况下,根据用相机18拍摄的图像检测熔合环fr的边缘图案,并根据熔合环fr的边缘图案来计算晶体直径。熔合环fr的直径值能够根据通过最小二乘法对其边缘图案(样本值)进行近似而获得的近似圆求出。通过进一步校正如此求出的熔合环fr的直径,能够计算常温下的单晶直径。
51.测量晶体直径时,必须稳定地检测熔合环fr。作为从图像数据中检测规定的图像位置的方法,通常使用基于其图像的亮度值设定阈值并进行二值化处理的方法。但是根据二值化处理进行了熔合环fr的边缘检测的情况下,由于随着炉内温度变化的亮度变化,检测位置有可能偏离。
52.为了排除该影响,优选从通过求出拍摄图像中的亮度峰值(熔合环fr的峰值亮度)并将该峰值亮度乘以小于1的值而确定的阈值(切片级别)来检测熔合环fr的边缘,而不是通常的二值化方法。即,熔合环fr的边缘图案(轮廓线)检测中,通过根据图像中的熔合环fr的亮度来改变阈值(切片级别),能够减小由亮度变化的影响而引起的测量误差,从而能够稳定地检测和确定熔合环fr的准确的尺寸。具体而言,与图8相同,设定与熔合环fr交叉的水平扫描线sl,检测该水平扫描线sl上的亮度分布与阈值(相当于图8中的th)的外侧交点(拍摄图像的靠近外周的一点)作为熔合环fr的边缘。
53.由于设置于腔室19的外侧的相机18从斜上方拍摄熔液面13a,因此熔合环fr的外观形状不是正圆形而失真。为了准确地计算熔合环fr直径,需要对图像进行失真校正。因此,在本实施方式中,将由相机18拍摄的熔合环fr的边缘图案投影转换至基准平面上,求出从正上方观察时的熔合环fr的直径。另外,基准平面是硅熔液13的液面(水平面),如上述能
够根据隔热构件17的实像ma和镜像mb求出。
54.图5是用于说明将拍摄图像的二维坐标投影转换至实际空间的坐标的方法的示意图。
55.如图5的左侧的图所示,由于相机18从斜上方拍摄腔室19内,因此拍摄图像中的熔合环的形状失真,成为具有远近感的图像。即,离相机18的距离近的下侧图像比上侧图像更宽。因此,为了准确地计算熔合环的尺寸,需要对图像进行失真校正。因此,将相机18的拍摄图像的坐标投影转换至设定在与熔液面13a相同高度位置的基准平面上的坐标而校正失真。
56.图5的右侧的图表示进行图像校正时的坐标系。在该坐标系中,将基准平面作为xy平面。并且,xy坐标的原点c0是从相机18的成像装置18a的中心位置c(0,yc,zc)通过相机18的透镜18b的中心位置f(0,yf,zf)所画的直线(虚线)与基准平面的交点。该直线是相机18的光轴。
57.并且,单晶硅15的提拉方向是作为铅垂轴的z轴正方向,成像装置18a的中心位置c(0,yc,zc)与透镜18b中心位置f(0,yf,zf)在yz平面内。图5的左侧的图所示的图像中的坐标(u,v)由成像装置18a的像素来表示,与下式(1)所示的成像装置18a上的任意一点p(x
p
,y
p
,z
p
)对应。
58.[数式1]
[0059]
在此,αu与αv是成像装置18a在横向和纵向的像素尺寸,yc和zc是成像装置18a在中心位置c的y坐标与z坐标。并且,如图5的右侧的图所示,θc是相机18的光轴与z轴所成的角度,是相机18的设置角度。
[0060]
此外,利用相机18的透镜18b的中心位置f(0,yf,zf)及透镜的焦距f1,由下式(2)来表示成像装置18a的中心位置c(0,yc,zc)。
[0061]
[数式2]
[0062]
在此,若对式(2)进行详细说明,则将基准平面上的坐标原点c0至成像装置18a的中心位置c(0,yc,zc)的距离设为lc时,yc、zc分别如下式(3)。
[0063]
[数式3]
[0064]
将坐标原点c0至相机18的透镜18b的中心位置f的距离设为a、将透镜18b的中心位置f至成像装置18a的中心位置c的距离设为b时,坐标原点c0至成像装置18a的中心位置c的距离lc如下式(4)。
[0065]
[数式4]lc=a+b(4)
[0066]
并且,根据透镜的成像公式,焦距f1利用距离a、b表示为如下式(5)所示。
[0067]
[数式5]
[0068]
根据式(4)及式(5)消除距离b,若由距离a和焦距f1表示lc,则如下式(6)。
[0069]
[数式6]
[0070]
关于坐标原点c0至相机18的透镜18b的中心位置f的距离a的值,利用相机18的透镜18b的中心位置f(0,yf,zf),能够表示为如下式(7)所示。
[0071]
[数式7]
[0072]
因此,可以由式(3)、式(6)及式(7)求出上述式(2)。
[0073]
将透镜18b视为针孔时,成像装置18a上的任意一点p(x
p
,x
p
,x
p
)通过f(0,yf,zf)投影在基准平面上,该投影点p’(x,y,0)能够由下式(8)表示。
[0074]
[数式8]
[0075]
通过使用式(1)、式(2)及式(8),能够求出投影在基准平面上的熔合环的坐标。
[0076]
在透镜18b的中心位置f(0,yf,zf)至成像装置18a的中心位置c(0,yc,zc)的距离b为已知的情况下,关于透镜18b在中心位置f的坐标yf,zf,利用距离b及成像装置18a在中心位置c的坐标yc,zc,能够表示为如以下的式(9)所示。
[0077]
[数式9]
[0078]
如此,在透镜18b的中心位置f(主点)至成像装置18a的中心位置c的距离b(背距(backdistance))为已知的情况下,能够使用背距值来表示投影点p’(x,y,0)。
[0079]
接着,对熔合环半径的计算方法进行说明。作为根据投影在基准平面上的熔合环坐标来计算其中心位置的坐标(xo,yo)及半径r的方法,使用最小二乘法即可。熔合环为圆形,其图像满足下式(10)所示的圆方程式。
[0080]
[数式10](x-x0)2+(y-y0)2=r2(10)
[0081]
在此,计算式(10)中的(x0,y0)及r时,使用最小二乘法。为了简单地进行利用最小二乘法的演算,进行下式(11)所示的变形。
[0082]
[数式11]
[0083]
通过最小二乘法求出该式(11)中的变量a、b、c。其结果会获得式(11)与所测点之差的平方和为最小的条件,并通过求解下式(12)所示的偏微分方程式来获得。
[0084]
[数式12]
[0085]
然后,该式(12)的解能够由下式(13)所示的联立方程式来计算。
[0086]
[数式13]
[0087]
如此通过使用最小二乘法,能够计算投影在基准平面上的熔合环的近似圆。
[0088]
之后,根据熔合环的近似圆来计算其直径。如图6所示,此时的直径计算方法通过设定与投影在基准平面pl0上的熔合环fr(近似圆)上的两个点交叉的直径测量线sl0,并利用熔合环fr与直径测量线的两个交点p
l0
、p
r0
之间的宽度w0及晶体中心位置c0至直径测量线sl0的距离h,求出熔合环fr的直径d=(w2+4h2)
1/2
。由于通过这种几何计算求出的熔合环的直径d的信息不是像素(pixel)而是毫米(mm),因此不需要进行单位转换。
[0089]
由于晶体提拉工序中的单晶硅在高温下热膨胀,因此其直径大于从腔室19取出并冷却时的直径。在根据这种经热膨胀的晶体直径对单晶硅的直径进行控制的情况下,难以将室温下的晶体直径控制为目标直径。
[0090]
因此,在晶体提拉工序中的单晶硅的直径控制中,将相机18的拍摄图像中显现的单晶硅在高温下的直径转换为室温下的直径,根据该室温下的晶体直径来控制晶体提拉速度等晶体生长条件。如此,根据室温时的晶体直径来控制晶体提拉条件的原因在于,对室温时的晶体直径的管理很重要。即,即使在高温下将直径提拉到目标直径,当返回到室温时,若其直径小于目标直径,则有可能无法产品化,因此对直径进行控制以使室温时的晶体直径成为目标直径。
[0091]
通过从根据熔合环求出的单晶在高温下的直径减去规定校正量来能够求出单晶硅在室温下的直径。或者,也可以通过根据熔合环求出的单晶在高温下的直径乘以规定的校正系数来求出单晶硅在室温下的直径。由于此时的校正量或校正系数因炉内结构而异,因此对每个单晶提拉装置单独设定。并且,当炉内结构随着晶体生长而变化时,可以根据晶体生长来改变校正量或校正系数。此外,晶体直径的校正量或校正系数可以根据硅熔液的液面位置的变化而变化,或者也可以根据单晶的提拉长度来设定。因此,例如,可以在晶体提拉工序的前半部分使用某个校正量来校正晶体直径,而在晶体提拉工序的后半部分使用
其它校正量来校正晶体直径。通过如上所述,能够更准确地估计常温下的晶体直径。
[0092]
在通过从相机的晶体直径的测量结果减去规定的校正量来求出室温下的晶体直径的情况下,根据关于相同晶体获得的、由相机测得的提拉工序中的晶体直径的测量结果和在室温下实际测量的晶体直径的测量结果来预先计算所述校正量。并且,在通过相机的晶体直径的测量结果乘以规定的校正系数来求出室温下的晶体直径的情况下,根据关于相同晶体获得的、由相机测得的提拉工序中的晶体直径的测量结果和在室温下实际测量的晶体直径的测量结果来预先计算所述校正系数。上述任一方法中,也考虑到由于晶体提拉工序中的热膨胀而使单晶沿长边方向延伸的量,计算在晶体长边方向上一致的直径测量位置处的校正量或校正系数。
[0093]
接着,对投影转换熔合环时成为基准平面的硅熔液的液面位置的计算方法进行说明。
[0094]
图7是用于说明根据隔热构件17的实像ma及镜像mb各自的开口半径rf、rm来计算间隙值δg的方法的示意图。
[0095]
如图7所示,在隔热构件17被水平设置的情况下,隔热构件17的镜像的中心坐标原本存在于隔着熔液面13a的、与隔热构件17的实像的中心坐标(x
hc
,y
hc
,0)相反的一侧,连结其两个点的直线成为通过隔热构件17的实像的中心坐标(x
hc
,y
hc
,0)的与铅垂轴的z轴平行的直线。
[0096]
另一方面,基准平面上的隔热构件17的镜像的中心坐标(x
mc
,y
mc
,0)由于成为隔热构件17的镜像的中心坐标(x
mc
,y
mc
,z
gap
)投影在基准平面上的坐标,因此镜像的中心坐标(x
hc
,y
hc
,z
gap
)将位于通过基准平面上的隔热构件17的镜像的中心坐标(x
mc
,y
mc
,0)与透镜18b的中心位置f(xf,yf,zf)的直线上。因此,欲计算的间隙δg成为zgap的一半的值,能够由以下所示的式(14)来计算。
[0097]
[数式14]-2δg=z
gap
=z
f-2zf(y
mc-yf)/(y
hc-yf)(14)
[0098]
将成像装置的透镜18b的中心位置f至隔热构件17的实像的开口中心的距离设为lf、将成像装置的透镜18b中心位置f至隔热构件17的镜像的开口中心的距离设为lm时,距离lf、lm如式(15)所示。
[0099]
[数式15]
[0100]
然后根据这些距离lf、lm,间隙值δg能够表示为如式(16)所示。
[0101]
[数式16]2δg=(l
m-lf)cosθc(16)
[0102]
如此,可知,为了计算间隙值δg,只要求出距离lf、lm即可。
[0103]
能够认为,在熔液面13a上映照的隔热构件17的镜像位于比实际的隔热构件17远2δg的位置,因此隔热构件17的镜像半径rm显得比实像半径rf小。此外,已知,在晶体提拉中的炉内温度环境下,由于热膨胀而隔热构件17的开口尺寸大于常温下的尺寸。因此,将考虑到热膨胀的开口半径(理论值)设为r
actual
、将隔热构件17的实像开口的半径测量值设为rf、将隔热构件17的镜像开口的半径测量值设为rm时,距离lf、lm能够由下式(17)来计算。
[0104]
[数式17]
[0105]
根据上述式(16)、(17),间隙值δg能够如下式(18)计算。
[0106]
[数式18]2δg=lc(r
actual
/r
m-r
actual
/rf)cosθc(18)
[0107]
如此,能够根据隔热构件17的实像及镜像各自的开口的半径测量值rf、rm来求出间隙值δg。
[0108]
如上说明,本实施方式的单晶硅的制造方法包括:用相机拍摄在硅熔液与单晶硅的边界部产生的熔合环的拍摄步骤;及处理相机的拍摄图像以计算单晶硅的直径的晶体直径计算步骤,晶体直径计算步骤中,由于根据相机的设置角度θc及焦距f1,将显现于相机的拍摄图像中的熔合环投影转换至相当于熔液的液面位置的基准平面上,并根据所述基准平面上的所述熔合环的形状来计算所述单晶的直径,因此无需使用用于单位转换根据相机的拍摄图像求出的直径测量值的直径转换系数,便能够准确地求出单晶的实际直径。因此,在晶体提拉工序中能够准确地测量并控制晶体直径,由此,能够提高单晶硅的制造成品率。
[0109]
以上,对本发明的优选的实施方式进行了说明,但本发明并不限于上述实施方式,在不脱离本发明的主旨的范围内,能够进行各种变更,当然这些也包括在本发明的范围内。
[0110]
例如,在上述实施方式中,以单晶硅的制造为例进行了说明,但本发明并不限于此,能够应用于利用cz法生长的各种单晶的制造。附图标记说明
[0111]
10-单晶制造装置,11-石英坩埚,12-加热器,13-硅熔液,13a-硅熔液的液面,14-籽晶,15-单晶硅(锭),15a-颈部,15b-肩部,15c-直体部,15d-尾部,16-坩埚支撑体(石墨坩埚),17-隔热构件(遮蔽筒),17a-隔热构件的开口,18-相机,18a-成像装置,18b-透镜,19-腔室,21-坩埚升降装置,22-提拉驱动装置,24-演算部,26-控制部。