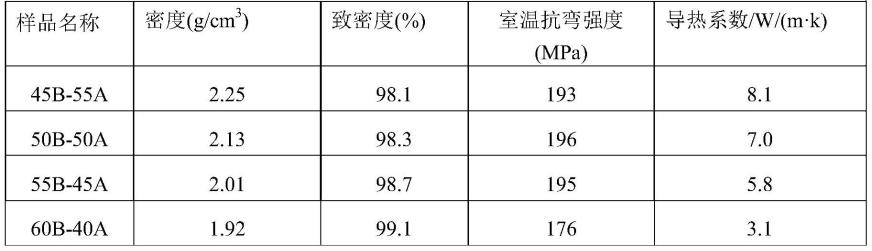
1.本发明属于无机非金属材料领域,涉及一种高导热低温共烧玻璃陶瓷基片及其制备方法。
背景技术:2.低温共烧陶瓷(ltcc)技术是在陶瓷粉末中加入一定量的玻璃粉末,大幅降低陶瓷的烧结温度,从而可以实现和低熔点高电导率的金属材料共烧,该技术不仅集合了高温共烧陶瓷(htcc)的部分优点,并且还有效克服了其烧结温度高的缺点。但是由于玻璃的导热系数低,所以目前制备得到的ltcc共烧陶瓷基板热导率很低,一般为1-3w/(m
·
k),所以此类电子封装材料的散热性能较差。
3.氮化铝陶瓷介电常数低、绝缘性和绝缘耐压性能好、力学性能优异、热膨胀系数低,热导率极高。所以为了改善玻璃陶瓷的导热系数,采用玻璃+aln陶瓷粉末来制备ltcc共烧陶瓷基板。
4.氮化铝陶瓷的导热系数主要受氧杂质含量和显微结构的影响,为了实现氮化铝陶瓷的低温烧结,引入的第二相玻璃相势必会改变氮化铝陶瓷的显微结构,导致其导热系数大幅下降。此外,由于氮化铝粉末的特性,氮化铝粉末在常温下就能发生水解,为了避免在粉末混合和造粒过程中氮化铝粉末发生水解,一般对aln进行热处理,即在一定温度下热处理使aln表面发生氧化,发生氧化后氮化铝粉末表面会生成致密的氧化铝薄膜,从而阻止氮化铝在混料和造粒过程中发生水解。但是在该过程中会在氮化铝粉末表面引入氧杂质,烧结过程中氧原子会扩散进入氮化铝晶格中,同样也会导致氮化铝的导热系数进一步的下降。
技术实现要素:5.针对现有技术的不足,本发明的目的在于提供一种具有优异散热性能、力学性能的高导热低温共烧陶瓷基片及其制备方法。
6.为了实现上述目的,本发明的技术方案如下:
7.本发明一种高导热低温共烧陶瓷基片的制备方法,先将氮化铝粉热处理,然后将热处理后的氮化铝粉与硼酸盐玻璃粉混合,获得混合粉,再将混合粉干燥、造粒获得粒料,粒料经压制成型获得压坯,压坯依次经过除胶、烧结即得共烧陶瓷基片;
8.所述氮化铝粉的粒径为5-10μm,硼酸盐玻璃粉的粒径为1-5μm。
9.本发明的制备方法,先对氮化铝粉进行热处理,使氮化铝粉末表面生成致密的氧化铝薄膜,从而阻止氮化铝在混料和造粒过程中发生水解,同时通过优选出硼酸盐玻璃粉与氮化铝粉共烧,发明人发现,选用硼硅酸盐玻璃粉与和氧化铝在高温下发生反应,可以避免氮化铝表面引入氧化铝,另外,本发明通过控制硼酸盐玻璃粉与氮化铝粉粒径在本发明的范围内,可以使硼硅酸盐玻璃粉均匀的分布在氮化铝颗粒四周,这样不仅有利于烧结致密化,而且有利于控制所得基片中第二相玻璃相形成的玻璃骨架的厚度更薄,而第二相玻
璃相形成的玻璃骨架越薄,其热导率越高。
10.优选的方案,所述氮化铝粉热处理的温度为700-900℃,优选为800℃,所述氮化铝粉热处理的时间为30-90min,优选为60min。
11.通过在上述条件下对氮化铝粉进行热处理,可以在使氮化铝粉末表面生成致密的氧化铝薄膜,从而阻止氮化铝在球磨和造粒过程中发生水解。
12.优选的方案,所述硼酸盐玻璃粉的化学式为sio
2-b2o
3-ro-m2o;其中r选自mg、ca、ba、zn中的至少一种,m选自k、na、li中的至少一种。
13.优选的方案,所述硼酸盐玻璃粉的纯度≧99%,所述氮化铝的纯度≧98%。
14.优选的方案,所述氮化铝粉的粒径为8-10μm,优选为10μm,硼酸盐玻璃粉的粒径为1-5μm,优选为1-3μm,优选为1μm。
15.在本发明中,粒径是指中位粒径d50。
16.优选的方案,所述混合粉中,氮化铝粉的质量分数为25-55wt%,优选为45%,硼酸盐玻璃粉的质量分数为45-75wt%,优选为55%。
17.发明人发现,将硼酸盐玻璃粉与氮化铝粉控制在上述范围内,再协同硼酸盐玻璃粉与氮化铝粉的粒径极配,可以有效的降低氮化铝晶粒之间第二相玻璃相的厚度,并最终获得致密度最高的共烧陶瓷基片,从而提高玻璃陶瓷的热导率。
18.优选的方案,所述混合的方式为球磨,所述球磨的转速为200-300rpm,优选为260rpm,球磨的时间为4-8h,优选为6h。
19.在发明中,需要控制球磨的转速与时间在上述范围内,以保证球磨后物料即能混合均匀,又能保持氮化铝和玻璃粉之间的粒径级配要求,若是转速过快,会导致氮化铝和玻璃粉的粒度变细,不满足所需的粒度级配要求。
20.在实际操作过程中,采用行星式球磨机进行球磨。
21.进一步的优选,所述球磨为湿法球磨,球磨介质为酒精。
22.进一步的优选,所述球磨球为直径为2-8mm的zro2球,球料比为4-6:1。
23.优选的方案,所述干燥的温度为60-100℃,时间为9-15h。
24.优选的方案,干燥后所得粉末过100目筛,取筛下物,然后再对筛下物进行造粒,造粒后,过20目筛,取筛下物,即为粒料。
25.将粒料控制在上述范围内,可以使压坯成型好。
26.优选的方案,所述压制成型的压力为80-120mpa,保压的时间为10-20s。
27.优选的方案,所述除胶的温度为400-600℃,除胶的时间为0.5-2h。
28.在本发明中对除胶的气氛无要求,优选为在保护气氛或真空环境下进行除胶。
29.优选的方案,所述烧结在真空环境下进行,烧结过程为,先以3-7℃/min的升温速率升温至795-825℃,优选为805℃,保温60-120min,优选为90min,然后再以3-7℃/min的升温速率升温至900-1050℃,优选为1000℃,保温90-180min,优选为120min。
30.本发明的烧结过程,先升温至795-825℃进行致密化烧结,致密化烧结完成后,直接升温至晶化温度900-1050℃进行晶化,发明人发现,通过控制致密化烧结与晶化的温度在上述范围内,一方面可以获得致密度高的共烧陶瓷基片,另一方面,可以控制硼硅酸盐玻璃和氮化铝表面的氧化铝的反应从而减少氮化铝表面的氧含量,最终获得具有优异散热性能的共烧陶瓷基片。
31.烧结完成后,对得到的陶瓷基片进行抛光处理,得到陶瓷基片产品。
32.本发明还提供上述制备方法所制备的高导热低温共烧陶瓷基片。
33.原理与优势
34.本发明的制备方法,采用硼硅酸盐玻璃为玻璃相、高导热的氮化铝陶瓷为陶瓷相,先对氮化铝粉进行热处理,使氮化铝粉末表面生成致密的氧化铝薄膜,从而阻止氮化铝在混料和造粒过程中发生水解,同时通过优选出硼酸盐玻璃粉与氮化铝粉共烧,通过控制烧结时的致密化温度和晶化温度,从而控制硼硅酸盐玻璃和氮化铝表面氧化铝的反应来降低氧杂质对氮化铝热导率的影响,同时还可以提高硼硅酸盐玻璃和氮化铝陶瓷之间的润湿性;另一方面,通过控制硼硅酸盐和氮化铝之间的比例、降低氮化铝晶粒之间第二相的厚度,并通过粒度控制来实现玻璃陶瓷的致密化烧结,从而提高玻璃陶瓷的热导率。
35.本发明通过对硼硅酸盐玻璃粉和陶瓷粉末的配比、粒度以及后续致密化和晶化烧结工艺的控制,得到了性能优良,导热系数高(>8w/(m
·
k))的低温共烧陶瓷基片,对低温共烧陶瓷基片来说热导率得到了巨大的提升,可以满足电子封装材料的散热需求。
具体实施方式
36.下面结合实施例对本发明进一步说明:
37.实施例1
38.本实施例所用硼酸盐玻璃粉的化学式为sio
2-b2o
3-mgo-na2o,
39.称取200g氮化铝陶瓷粉末,将粉末放入马弗炉中,10℃/min升温到800℃,保温一个小时后随炉冷却,取出备用;
40.按照表1-1称量不同质量配比的硼硅酸盐玻璃粉(bsg)和氮化铝粉末,硼硅酸盐粉末中值粒度为1μm,氮化铝粉末中值粒度为10μm,称量完毕后,将粉末倒入球磨罐中,球磨珠为直径为5mm的zro2球磨珠,球料质量比为5:1,球磨介质为酒精,球磨转速为260rpm,球磨时间6h,球磨机为行星式球磨机,球磨完毕后。将球磨罐放入干燥箱中70℃烘制12h,烘干后过100目筛备用。
41.表1不同配比的玻璃陶瓷配方
42.样品编号样品名称bsg:aln质量比145b-55a45:55250b-50a50:50355b-45a55:45460b-40a60:40
43.对干燥后的粉末进行造粒,所使用粘接剂为5%的pva溶液,造粒后过20目筛,随后称取20g造粒后的粉末,放置在模具中,将模具放在压机上进行压制,压制压力为100mpa,保压时间为15s,压制完毕后得到压制坯体。
44.将压制坯体放在马弗炉中,以10℃/min从室温升至500℃,保温时间为1h进行除胶,除胶完毕后随炉冷却取出。
45.将除胶后的坯体放在真空烧结炉中,烧结气氛为真空,烧结工艺为以5℃/min升到805℃。保温时间为90min,随后以5℃/min升到1000℃,保温时间为120min。随后对得到的陶瓷基片坯体进行打磨抛光,得到最终的陶瓷基片制品。
46.根据测试标准gb/t 6569-86测试了样品的弯曲强度,根据测试标准gb/t 39862-2021测试了样品的导热系数,采用阿基米德排水法测试了样品的密度和致密度,主要性能结果见表1-2。
47.表1-2不同硼硅酸盐与氮化铝质量比样品性能测试表
[0048][0049]
实施例2:
[0050]
称取200g氮化铝陶瓷粉末,将粉末放入马弗炉中,10℃/min升温到800℃,保温一个小时后随炉冷却,取出备用;
[0051]
按照bsg:aln质量比为55:45分别称取硼硅酸盐玻璃粉和氮化铝粉末,选取不同中值粒径的硼硅酸盐玻璃粉和氮化铝粉末进行对比实验,粉末粒度如表2-1所示,称量完毕后,将粉末倒入球磨罐中,球磨珠为直径为5mm的zro2球磨珠,球料质量比为5:1,球磨介质为酒精,球磨转速为260rpm,球磨时间6h,球磨机为行星式球磨机,球磨完毕后。将球磨罐放入干燥箱中70℃烘制12h,烘干后过100目筛备用。
[0052]
表2-1不同玻璃粉和氮化铝粉的粒度表
[0053]
样品编号样品名称玻璃粉中值粒度氮化铝中值粒度11b-8a1μm8μm21b-9a1μm9μm31b-10a1μm10μm42b-10a2μm10μm53b-10a3μm10μm60.5b-10a0.51071b-15a11580.5b-15a0.515
[0054]
对干燥后的粉末进行造粒,所使用粘接剂为5%的pva溶液,造粒后过20目筛,随后称取20g造粒后的粉末,放置在模具中,将模具放在压机上进行压制,压制压力为100mpa,保压时间为15s,压制完毕后得到压制坯体。
[0055]
将压制坯体放在马弗炉中,以10℃/min从室温升至500℃,保温时间为1h进行除胶,除胶完毕后随炉冷却取出。
[0056]
将除胶后的坯体放在真空烧结炉中,烧结气氛为真空,烧结工艺为以5℃/min升到805℃。保温时间为90min,随后以5℃/min升到1000℃,保温时间为120min。随后对得到的陶瓷基片坯体进行打磨抛光,得到最终的陶瓷基片制品。
[0057]
根据测试标准gb/t 6569-86测试了样品的弯曲强度,根据测试标准gb/t 39862-2021测试了样品的导热系数,采用阿基米德排水法测试了样品的密度和致密度,主要性能
结果见表2-2。
[0058]
表2-2不同粒度玻璃粉和氮化铝粉样品性能测试表
[0059][0060]
实施例3:
[0061]
称取200g氮化铝陶瓷粉末,将粉末放入马弗炉中,10℃/min升温到800℃,保温一个小时后随炉冷却,取出备用;
[0062]
按照bsg:aln质量比为55:45分别称取硼硅酸盐玻璃粉和氮化铝粉末,硼硅酸盐粉末中值粒度为1μm,氮化铝粉末中值粒度为10μm,称量完毕后,将粉末倒入球磨罐中,球磨珠为直径为5mm的zro2球磨珠,球料质量比为5:1,球磨介质为酒精,球磨转速为260rpm,球磨时间6h,球磨机为行星式球磨机,球磨完毕后。将球磨罐放入干燥箱中70℃烘制12h,烘干后过100目筛备用。
[0063]
对干燥后的粉末进行造粒,所使用粘接剂为5%的pva溶液,造粒后过20目筛,随后称取20g造粒后的粉末,放置在模具中,将模具放在压机上进行压制,压制压力为100mpa,保压时间为15s,压制完毕后得到压制坯体。
[0064]
将压制坯体放在马弗炉中,以10℃/min从室温升至500℃,保温时间为1h进行除胶,除胶完毕后随炉冷却取出。
[0065]
将除胶后的坯体放在真空烧结炉中,烧结气氛为真空,对比不同的致密化温度和晶化温度,如表3-1所示,升温速率为5℃/min,致密化温度保温时间为90min,晶化温度保温时间为120min。随后对得到的陶瓷基片坯体进行打磨抛光,得到最终的陶瓷基片制品。
[0066]
表3-1不同致密化温度和晶化温度样品表
[0067]
样品编号样品名称致密化温度晶化温度1ba-795-1000795℃1000℃2ba-805-1000805℃1000℃3ba-815-1000815℃1000℃4ba-825-1000825℃1000℃5ba-805-900805℃900℃6ba-805-950805℃950℃7ba-805-1000805℃1000℃
8ba-805-1050805℃1050℃9ba-750-1000750℃1000℃10ba-805-850805℃850℃11ba-750-850750℃850℃
[0068]
根据测试标准gb/t 6569-86测试了样品的弯曲强度,根据测试标准gb/t 39862-2021测试了样品的导热系数,采用阿基米德排水法测试了样品的密度和致密度,主要性能结果见表3-2。
[0069]
表3-2不同致密化和晶化温度性能测试表
[0070][0071]
从表1-2可知,对比不同bsg:aln配比,玻璃含量越高,样品致密度越高,但导热系数随玻璃含量的身高迅速下降,说明硼硅酸盐玻璃对玻璃陶瓷的导热系数影响很大。aln含量为55%的45b-55a样品导热系数最高,达到8w/(m
·
k)。
[0072]
从表2-2可知,对比不同的硼硅酸盐玻璃粉和氮化铝粉末粒度比,硼硅酸盐玻璃粉中值粒径越大,样品致密度越低,抗弯强度越差,导热系数越低。氮化铝粉末中值粒径越大,样品致密度越高,导热系数越高。当bsg粒径为1μm,aln粒径为10μm时,样品名称为1b-10a的致密度、导热系数最高。
[0073]
从表3-2可知,致密化温度过高或者过低,都会导致复合材料致密度下降,晶化温度越高,样品性能越好,导热性能越好,从表中可知,当致密化温度为805℃,晶化温度为1000℃时,样品有最高的抗弯强度和导热率。
[0074]
所以,当bsg:aln质量配比为45:50,中值粒径为1和10μm,致密化温度和晶化温度为805℃和1000℃时,此时基片的导热率最高,为8w/(m
·
k),且抗弯强度达到193mpa,满足低温共烧陶瓷基片的使用需求。