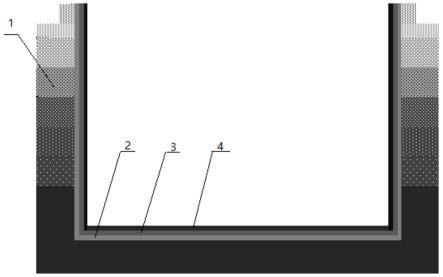
1.本发明涉及炭复合材料领域,具体涉及一种复合材料坩埚及其制备方法。
背景技术:2.随着科学技术的进步,对半导体材料提出了更高的要求,需要耐更高温,大功率,高频率以及其他化学性能的新一代半导体材料,而碳化硅(sic)等第三代半导体材料能满足这些要求,受到了广泛的关注与研究。碳化硅单晶具有良好的高温整流特性和较高的抗幅射性,也具有良好的温差电效应、光电效应、场致发光以及电子发射等珍贵性能。sic晶体材料既可以作为导电型衬底材料也可以作为半绝缘型的衬底材料。sic的宽带隙性能可以应用在抗辐射器件、蓝光led、激光二极管以及超低漏电流器件等;和gan、aln晶格失配低,适合于作为它们的衬底材料;其高击穿电场强度可以应用在高压大功率开关二极管、电力电子器件、ic高密度封装以及空间应用的大功率器件等;其高导热率能提高器件的散热性能,同时也能提高器件的集成密度。
3.目前,物理气相传输法 (physical vapor transport-pvt)是目前较为成熟的大尺寸sic晶体生长技术,即将sic晶片贴在石墨坩埚盖上用作籽晶,石墨坩埚内装有作为生长原料的sic粉末,生长温度控制在2273k到2773k之间,生长原料分解成气相组分后在石墨坩埚内部轴向温度梯度的驱动下输运到籽晶处结晶生长sic晶体。然而,采用pvt法制备sic晶体过程中,微管缺陷、多晶体共生缺陷的存在将严重影响大尺寸sic单晶衬底的性能,温度场的分布在pvt法生长sic晶体的过程中具有至关重要的作用。不同sic多型的形核能很接近,需要对生长条件进行严格的控制,防止出现多型共生缺陷的产生。宋生等[33]通过试验发现,6h-sic晶体更易于生长,生长过程中也更稳定,稳定生长的温度范围较大,相比之下4h-sic的晶体生长则更艰难,温度生长的温度范围很小。在较大的温度梯度条件下,包裹体缺陷更易于形成,因为温度梯度大就质量传输快;而较小的温度梯度则不能满足pvt法质量传输的要求。同时坩埚盖直径方向的温度梯度是晶体向大尺寸发展的关键。所以轴向和直径方向的温度都需要有一个较适宜的取值区间。晶体的生长速率跟温度场有关,每个生长面的生长速率不同,有研究者通过试验发现《11-20》方向的生长速率大于《1-100》方向。pvt法sic晶体生长过程中温度起伏等不稳定因素会引起局部生长条件偏离,因此实现pvt生长室的热场稳定分布、并生长出无微管缺陷的sic单晶是科学研究发展的重点。
[0004]
采用pvt法制备sic晶体过程中,包裹体缺陷也是影响sic衬底性能另一主要缺陷。有研究学者研究表明气相中的si/c元素比的偏离是引起碳包裹体缺陷的主要原因。在生长初期的籽晶石墨化会导致碳包裹物的出现,sic原料的石墨化是不可避免的,因为富si相更易于汽化而离开籽晶,这些富si相会和石墨坩埚或其他石墨元素进行反应,随之而来的结果是相对低的硅分压就会在生长前沿形成。还有其他研究表明碳包裹物的形成不是源于si的缺失,而多余的 si 对石墨坩埚的强烈腐蚀是导致碳包裹物缺陷形成的主要原因,也就是说原料的石墨化以及对坩埚的腐蚀带来的碳颗粒是引起sic单晶中碳包裹物出现的原因。
[0005]
因此,采用pvt法进行零缺陷,大尺寸sic单晶衬底批量生产时,目前急需解决生产过程中sic单晶受横向和轴向温度梯度影响,形成微管缺陷、多晶体共生缺陷问题,解决由于坩埚内部高温气氛与石墨坩埚反应并破坏最佳sic单晶生长元素比,导致sic单晶出现包裹体缺陷等问题。导致上述问题的关键因素之一是目前采用的pvt法制备sic单晶时,制备温度在2000℃以上,现阶段常常采用高纯石墨坩埚作为反应腔体,然而石墨材料属于一种较为均质的耐高温材料,无法通过材料自身的梯度变化来促进反应腔内的温度梯度。此外,在pvt法sic晶体生长过程中,石墨坩埚反应腔内存在大量活性气氛si、sic、si2c以及sic2等。气相在坩埚内部发生复杂反应,包括气相与坩埚壁之间的反应,气相与晶体表面间的反应,气相与原料粉体间的反应以及气相内部的反应。因此石墨坩埚的纯度、坩埚在高温气氛腐蚀后的分解产物均会改变sic晶体生长所需的最佳si和c原子比气氛,从而影响sic晶体的纯度和缺陷控制。
技术实现要素:[0006]
本发明提供了一种复合材料坩埚及其制备方法,用以解决目前现有坩埚难以适应sic单晶生产需求的技术问题。
[0007]
为解决上述技术问题,本发明采用以下技术方案:一种复合材料坩埚,包括碳-碳复合材料基体和设置在所述碳-碳复合材料基体表面的涂层;所述碳-碳复合材料基体的密度从底部至顶部依次递减;所述涂层由内至外依次包括石墨化热解碳-碳纤维层、石墨化热解碳层和高温热解石墨层。
[0008]
上述技术方案的设计思路在于,本技术方案选用比强度高、比模量高、高温力学性能优异、耐蚀性能优良的碳-碳复合材料作为坩埚的基体,替代传统的石墨基体,利用碳-碳复合材料在2000℃以上的高温其力学强度反而增加的优势,以此来避免原有石墨基体在高温下由于石墨颗粒间没有相互作用力,在热膨胀力的作用下容易产生裂纹、在循环使用次数下容易由于抗热震性能较差而开裂的技术问题;同时本方案采用从底部到上部密度呈现梯度递减的结构特征,促使坩埚从下至上形成一种热导率梯度递减的性能分布,并提供坩埚从下至上的一种轴向温度梯度递减、平面温度均质的梯度热场,轴向密度梯度递减可提高轴向温度梯度幅度,从而提高由于温度梯度导致的坩埚内sic分解产物在籽晶处快速生长的效率;平面温度密度一致可保证原料分解速度的一致性和单晶生长速率的一致性,以此来避免单晶生长过程中受温度不均匀而形成的缺陷,最终使得本方案的坩埚对pvt法制备sic单晶具有良好的适应性。另外,本方案还通过对碳-碳复合材料基体表面涂层的设置和设计,一方面利用石墨化热解碳-碳纤维层进一步提高碳-碳复合材料基体表面的致密度,对碳-碳复合材料表面的孔洞和裂纹进行填充和修复,提高坩埚壁面对高温腐蚀性气氛的抵抗力,并利用石墨化热解碳层避免后续高温热解碳涂层制备过程中的因高温造成的碳-碳复合材料基体的纤维损伤,避免材料结构和性能缺陷;另一方面还利用高温热解石墨层的特性避免多孔石墨坩埚在使用过程中孔洞和裂纹处热应力集中而出现的石墨颗粒脱落或孔洞中的碳粉挥发问题,最终避免坩埚内si和c气氛无法实现最佳sic单晶生长的原子比为1:1等影响单晶生长的纯度问题。同时,涂层层的厚度设计思路在于,沉积石墨化热解碳层的成本较低,但是整体涂层密度较低,且裂纹和孔洞缺陷较高,单纯的石墨化热解碳涂层无法满足抵抗腐蚀性气氛的要求,然而通过在其表面添加能接近理论密度的高温热解石
墨时,可以在沉积过程中封填热解碳表面和内部缺陷,也可根据自身优异的抗腐蚀性能,提高涂层整体的性能。但是高温热解石墨的制备成本较高,因此设置该涂层的厚度相比热解碳薄,但又不能过厚,以致失去保护性。
[0009]
作为上述技术方案的进一步优选,所述石墨化热解碳-碳纤维层和石墨化热解碳层的总厚度60~80μm,所述高温热解石墨层的厚度为20~40μm。
[0010]
作为上述技术方案的进一步优选,所述复合材料坩埚从底部至顶部均匀分为三个区域:底部区域、中间区域和上部区域,所述复合材料坩埚的底部区域的密度为1.85~1.99g/cm3;所述复合材料坩埚的中间区域均匀分为三段,从下至上每段的密度分别为1.76~1.89g/cm3、1.68~1.79g/cm3、1.55~1.69g/cm3;所述复合材料坩埚的上部区域均匀分为三段,从下至上每段的密度分别为1.47~1.59g/cm3、1.33~1.49g/cm3、1.35~1.39g/cm3。
[0011]
作为上述技术方案的进一步优选,所述碳-碳复合材料选用碳纤维编制而成,从底部至顶部均匀分为三个区域:底部区域、中间区域和上部区域,所述碳-碳复合材料基体的底部区域的密度为1.2~1.3g/cm3;所述碳-碳复合材料的基体中间区域均匀分为三段,从下至上每段的密度分别为1.1~1.19g/cm3、1.0~1.09g/cm3、0.9~0.99g/cm3;所述碳-碳复合材料基体的上部区域均匀分为三段,从下至上每段的密度分别为0.8~0.89g/cm3、0.7~0.79g/cm3、0.6~0.69g/cm3。设计碳纤维预制体密度时,原则上碳纤维预制体的密度越大越好,这样可以降低后续沉积增密的成本,但是同时碳纤维预制体过大将导致预制体表面开孔率降低,使后续热解碳沉积的气体较难扩散至基体内部进行沉积增密,本技术对碳纤维预制体密度的设计实现了上述两个方面的平衡。
[0012]
基于同一技术构思,本发明还提供一种上述的复合材料坩埚的制备方法,包括以下步骤:s1、制作碳纤维预制体,控制所述碳纤维预制体在垂直方向上由底部向顶部密度依次递减;s2、对所述碳纤维预制体进行增密和定型处理,得到中间体;s3、在所述中间体表面沉积热解碳-碳纤维层,并将带有热解碳-碳纤维层的中间体升温至石墨化温度并保温一段时间,石墨化温度为2000~2400℃,保温时间为3~7h,在热解碳-碳纤维层上原位形成石墨化热解碳层,且热解碳-碳纤维层转变成石墨化热解碳-碳纤维层,得到中间产品;s4、将所述中间产品进行纯化处理,再进行机械加工成所需尺寸,并进行后处理;s5、将经后处理后的中间产品放入高温沉积炉内,将带有石墨化热解碳-碳纤维层和石墨化热解碳层的中间体表面沉积高温热解石墨层,即得到所述复合材料坩埚。
[0013]
作为上述技术方案的进一步优选,步骤s1中采用细编穿刺的方法制作碳纤维预制体,具体方法为:在水平方向以碳纤维布织物,在垂直方向上穿刺纤维束,使纤维束与水平面正交,使用穿刺工具细编穿刺,编织获得从底部至顶部密度梯度递减的碳纤维预制体。长晶坩埚需要在一个平面受热均匀的状态下工作,以此来保证所生成的单晶的纯度和一致性,而本优选方案采用细编穿刺预制体结构,可有效保证在坩埚平面方向上热传导速率的一致性,以及坩埚底部温度场的均匀性,从而保证晶体生长环境,提高晶体生长的均匀性。
[0014]
作为上述技术方案的进一步优选,步骤s2中所述增密和定型处理包括依次进行的化学气相渗透沉积增密定型操作、液相浸渍操作以及高温碳化操作,所述液相浸渍操作和
高温碳化操作重复2~4次。
[0015]
作为上述技术方案的进一步优选,步骤s2中对所述碳纤维预制体进行增密和定型处理前,在所述碳纤维预制体内部放入壁厚为3mm的石墨工装,石墨工装壁面设置有若干直径为20mm的通孔,通孔边间距为5mm。石墨工装可对对预制体起到结构固定的作用,避免碳纤维预制体在增密、定型过程中因为重力作用导致的变形问题,通孔则可保证石墨工装能向其背面均匀输送碳源气体。
[0016]
作为上述技术方案的进一步优选,所述化学气相渗透沉积增密定型操作以丙烯、乙炔和天然气中的至少一种作为碳源、以氢气和氮气中的至少一种作为稀释气体进行沉积,沉积温度为900~1200℃,沉积时间为600~1000h,所述碳源气体流量为5~10l/min,稀释气体流量为2.5~5l/min。
[0017]
作为上述技术方案的进一步优选,所述液相浸渍操作以呋喃树脂、酚醛树脂和环氧树脂中的至少一种为浸渍剂,浸渍温度为60~70℃,浸渍时间为5~10h,浸渍压力为1.5~4mpa。
[0018]
作为上述技术方案的进一步优选,所述高温碳化温度为800~1000℃,升温速率为10~30℃/min,保温时间为3~5h。
[0019]
作为上述技术方案的进一步优选,在沉积热解碳-碳纤维层之前,所述中间体还经石墨化处理,所述石墨化处理的温度为2000~2400℃,升温速率为50~70℃/min,保温时间为5~10h。
[0020]
作为上述技术方案的进一步优选,步骤s3中沉积所述热解碳-碳纤维层时以丙烯为气相碳源、以氮气为稀释气体进行沉积,沉积温度为890~1000℃,升温速率为10~12℃/min,沉积时间为80~100h,碳源通入流量为3~5l/min,稀释气体通入流量为1~1.5l/min。
[0021]
作为上述技术方案的进一步优选,步骤s3中原位形成所述石墨化热解碳层时,升温温度为2000~2400℃,保温时间为3~7h,升温速率为30~50℃/min。
[0022]
作为上述技术方案的进一步优选,步骤s4中通入cl2对所述中间产品进行纯化处理,纯化温度为2000~2400℃,纯化时间为3~5h,cl2流量为3~5l/min。
[0023]
作为上述技术方案的进一步优选,所述后处理包括依次进行的洗涤和干燥操作,洗涤时间为3~5h,干燥时间为10~12h,干燥温度为50-100℃。
[0024]
作为上述技术方案的进一步优选,步骤s5中沉积所述高温热解石墨层时,以甲烷为碳源、以氢气为稀释气体进行沉积,沉积温度为2000~2400℃,沉积时间为5~10h,碳源通入流量为2~3l/min,稀释气体通入流量为1~1.5l/min。
[0025]
与现有技术相比,本发明的优点在于:(1)本发明采用碳-碳复合材料替代石墨坩埚,在碳-碳坩埚力学性能大于石墨材料的优势下,能够提高坩埚的使用寿命;并采用从底部到坩埚上部的碳纤维预制体密度呈现梯度递减的结构特征,能有利于促进坩埚由下至上提供一种梯度温度场,底部的高密度碳纤维预制体,促进底部坩埚的热导率,提高炉体内热源的利用率,实时保证坩埚底部放置sic原料在均匀温度下均匀分解;而其轴向密度梯度递减的作用是提高轴向温度梯度幅度,从而提高由于温度梯度导致的坩埚内sic分解产物在籽晶处快速生长的效率;同时本发明对涂层结构进行了设计,相比现阶段单一石墨坩埚,其涂层接近理论密度,没有任何导致热应力集中的孔洞和裂纹,能有效避免多孔石墨坩埚在使用过程中孔洞和裂纹处热应力集中
而出现的石墨颗粒脱落或孔洞中的碳粉挥发问题,最终避免坩埚内si和c气氛无法实现最佳sic单晶生长的原子比为1:1等影响单晶生长的纯度问题,且涂层与c/c复合材料坩埚属于同质材料,涂层的热稳定较好,其循环使用次数也能得到大幅度提高;(2)本发明的复合材料坩埚的制备方法一方面采用细编穿刺预制体结构能保证碳-碳坩埚纤维束分布的均匀性,保证碳-碳坩埚在使用过程中热传导和保温均匀性,从而保证坩埚底部能拥有一个均匀温度场的晶体生长环境,提高晶体生长的均匀性,能在提高性能的同时,还可降低纤维用量、降低成本;另一方面本发明的方法所形成的涂层的晶型均一性较好,晶界处和晶内缺陷较少,其涂层的耐高温和耐腐蚀性能较好;在一方面,本发明采用梯度超高温热解石墨层的制备方法中,先通过低温化学气相渗透工艺对碳纤维预制体中碳纤维进行热解碳层包覆,有利于避免后续高温化学气相沉积高温热解碳涂层制备过程中的纤维损伤;相比单纯用化学气相沉积沉积高温热解石墨增密法,通过低温化学气相渗透工艺也能大大节约预制体增密的成本;(3)本发明在在石墨化和纯化处理后,能完全保证复合材料坩埚的高纯特性,且能完全适用于对纯度要求极高的sic单晶的生长。
附图说明
[0026]
图1为本发明的复合材料坩埚的结构示意图。
[0027]
图例说明:1、碳-碳复合材料基体;2、石墨化热解碳-碳纤维层;3、石墨化热解碳层;4、高温热解石墨层。
具体实施方式
[0028]
以下结合具体实施例对本发明作进一步详细说明。
[0029]
实施例1如图1所示,本实施例的复合材料坩埚,包括经过热解碳增密的碳纤维增强的碳-碳复合材料基体1和设置在碳-碳复合材料基体1表面的涂层,碳-碳复合材料基体1的密度从底部至顶部依次递减;涂层为由内向外依次叠加的石墨化热解碳-碳纤维层2、石墨化热解碳层3,高温热解石墨层4;其中,复合材料坩埚从底部至顶部均匀分为三个区域:底部区域、中间区域和上部区域,复合材料坩埚底部区域的密度为1.9g/cm3;复合材料坩埚中间区域均匀分为三段,从下至上每段的密度分别为1.8g/cm3、1.7g/cm3、1.6g/cm3;复合材料坩埚上部区域均匀分为三段,从下至上每段的密度分别为1.5g/cm3、1.4g/cm3、1.3/cm3;碳-碳复合材料基体1从底部至顶部同样均匀分为三个区域:底部区域、中间区域和上部区域,碳-碳复合材料基体1底部区域的密度为1.2g/cm3;碳-碳复合材料基体1的中间区域均匀分为三段,从下至上每段的密度分别为1.1g/cm3、1.0g/cm3、0.9g/cm3;碳-碳复合材料基体1的上部区域均匀分为三段,从下至上每段的密度分别为0.8g/cm3、0.7g/cm3、0.6g/cm3;石墨化热解碳-碳纤维层2的石墨化热解碳层3的总厚度70μm,高温热解石墨层4的厚度为30μm。
[0030]
本实施例的复合材料坩埚的制备方法,包括以下步骤:(1)采用细编穿刺梯度编织的方法制备碳纤维预制体:水平方向为碳纤维布,垂直方向为穿刺纤维束,纤维束与水平平面正交的方式,将碳纤维预制体编织成以下端到上端
密度呈梯度递减的梯度结构,通过控制密度从而实现从上至下热导率梯度递减的趋势,解决籽晶与升华源之间的温度梯度难于精确控制的技术问题;(2)采用化学气相渗透法,对碳纤维预制体进行增密和定型处理:a.工装制备和放置:制备出壁厚为3mm的石墨坩埚工装并置于碳纤维预制体坩埚内部,对碳纤维预制体起到结构固定的作用,石墨坩埚工装壁面均匀制备出直径为20mm的通孔,通孔边间距为5mm,保证石墨工装能向其背面均匀输送碳源气体;b.化学气相渗透沉积增密定型:化学气相沉积温度为900℃,升温速率为10℃/min;沉积时间600小时;碳源气氛为丙烯;稀释气体为氮气;碳源气体流量为5l/min;稀释气体流量为2.5l/min;经初步化学气相渗透沉积增密定型后的碳纤维预制体密度分布情况为:从底部到上部的密度分别为:1.6g/cm3,1.49g/cm3,1.39g/cm3,1.29g/cm3,1.19g/cm3,1.09g/cm3,0.99g/cm3(按上文的区域划分,下同);c.采用液相浸渍对碳纤维预制体进一步增密处理:液相浸渍工序需要进行两个步骤,分别为液相浸渍和高温碳化处理;液相浸渍需要循环2次,液相浸渍温度为60℃,液相浸渍时间5h,浸渍压力1.5mpa,浸渗气氛为真空,浸渍剂选用呋喃树脂,浸渍完成后对其进行高温碳化处理2次,碳化温度800℃,升温速率为10℃/min,碳化处理气氛为惰性保护气体;一次液相浸渍和高温碳化处理后,形成低密度碳-碳复合材料,随后对其进行第二次液相浸渍和高温碳化处理得到中间体;二次液相浸渍和高温碳化处理过程中,首先对低密度碳-碳复合材料表面进行凹槽处理,凹槽的宽度为2mm,凹槽的深度为4
㎜
,凹槽边间距为5mm,该凹槽是为了给下一步浸渍提供浸渍所需的开孔孔隙结构,避免第一次液相浸渍封孔导致浸渍料难以浸渗的问题;(3)增密和定型处理完成后,对中间体进行高温石墨化处理,处理温度为2000℃,升温速率为50℃/min,保温时间为5h;经过增密和定型处理和石墨化纯化后,中间体的密度分布情况为:从底部到上部的密度分别为:1.8g/cm3,1.7g/cm3,1.6g/cm3,1.5g/cm3,1.4g/cm3,1.3g/cm3,1.2g/cm3;(4)制备石墨化热解碳层3:先在低温区进行化学气相沉积制备热解碳-碳纤维层。该阶段的沉积温度为890℃;升温速率为10℃/min;气相碳源为丙烯,稀释气体为氮气,两气体的流量分别为3l/min和1.5l/min;沉积时间为80小时,涂层厚度为70μm。沉积该热解碳-碳纤维层的目的是进一步提高碳-碳坩埚表面的致密度,通过低温段的低成本热解碳增密的方法对碳-碳坩埚表面的孔洞和裂纹进行填充和修复,提高坩埚壁面对高温腐蚀性气氛的抵抗力;将沉积了热解碳-碳纤维层的中间体表面再进一步升温至石墨化温度(2000℃),升温速率为30℃/min,保温3小时,制得石墨化热解碳层3;(5)随后通入cl2进行纯化处理,纯化温度与石墨化温度相同,纯化时间为3h,cl2流量为3l/min;(6)纯化处理后,将样品取出,进行机械加工成所需坩埚结构和尺寸,并进行高纯去离子水超声洗涤和真空干燥处理;洗涤时间为3h,干燥时间为10h,干燥温度为50℃;(7)制备高温热解石墨层4:在高温区通入甲烷气相碳源气体,选用氢气作为稀释气体,碳源、稀释气体的流量分别为:2l/min和1l/min,通入气体的时间为5小时,沉积厚度为30μm,最终在中间体表面制备出一层零缺陷、接近理论密度、高温性能稳定的各向异性高温热解石墨层4,即得到本实施例的复合材料坩埚。
[0031]
最终本实施制得的复合材料坩埚的密度分布状态为,从底部到上部的密度分别为:1.9g/cm3,1.8g/cm3,1.7g/cm3,1.6g/cm3,1.5g/cm3,1.4g/cm3,1.3g/cm3。
[0032]
采用分段式取样的方法,对各个密度区域的复合材料坩埚壁材料进行取样,并对其进行热导率测试,结果表明从坩埚底部到上部的密度分别为:1.9g/cm3,1.8g/cm3,1.7g/cm3,1.6g/cm3,1.5g/cm3,1.4g/cm3,1.3g/cm3的各区域(x~y方向)热导率分别为:185/(m
·
k),160w/(m
·
k),142w/(m
·
k),124w/(m
·
k),102w/(m
·
k)。
[0033]
将复合材料坩埚放入高温石墨化炉内进行升温测试,升温速率为20℃/min,升温制700℃,每个密度区间内部设置了热电偶测温棒。结果表明,从坩埚底部到上部的密度分别为:1.9g/cm3,1.8g/cm3,1.7g/cm3,1.6g/cm3,1.5g/cm3,1.4g/cm3,1.3g/cm3的各区域(x~y方向)的坩埚内部的温度为:685℃,550℃,540℃,522℃,500℃,485℃,450℃。在没有装sic单晶生长原料的坩埚不同密度区域的升温速率差异不是很大,这主要是由于在加热时,整个炉腔体内的温度差异较小,在没有温度消耗的情况下,坩埚热导率差异促进温度梯度的效果不那么明显。
[0034]
将复合材料坩埚进行高温生产仿真,结果表明,装有sic单晶生长原料的坩埚加热至2500℃时,放置于坩埚底部的高纯sic粉末需要分解成坩埚顶部籽晶区sic单晶生长所需的气相si源和c源,在这个过程需要吸收坩埚内部的大量热量,因此通过坩埚避免向坩埚内部导热的速率收到影响,因此温度仿真结果,即从坩埚底部到上部的密度分别为:1.9g/cm3,1.8g/cm3,1.7g/cm3,1.6g/cm3,1.5g/cm3,1.4g/cm3,1.3g/cm3的各区域(x~y方向)的坩埚内部的温度分别为:2350℃,2334℃,2318℃,1800℃,1650℃,1435℃,1421℃。这充分体现了梯度碳-碳坩埚能有效提高单晶生长环境的梯温度梯度性,提高单晶生长的环境适用性。
[0035]
将截取的复合材料坩埚一区域(密度为1.9g/cm3的坩埚壁区域)进行抗热震性能测试,测试温度为1200℃到室温,持续时间为10分钟,在氩气保护气氛下进行,循环次数为10次,结果表明涂层未见脱落,通过抗热震性能测试后的样品进行弯曲强度测试,结果表明,抗弯强度为320mpa。
[0036]
实施例2如图1所示,本实施例的复合材料坩埚,包括经过热解碳增密的碳纤维增强的碳-碳复合材料基体1和设置在碳-碳复合材料基体1表面的涂层,碳-碳复合材料基体1的密度从底部至顶部依次递减;涂层为由内向外依次叠加的石墨化热解碳-碳纤维层2、石墨化热解碳层3,高温热解石墨层4;其中,复合材料坩埚从底部至顶部均匀分为三个区域:底部区域、中间区域和上部区域,复合材料坩埚底部区域的密度为1.99g/cm3;复合材料坩埚中间区域均匀分为三段,从下至上每段的密度分别为1.89g/cm3、1.79g/cm3、1.69g/cm3;复合材料坩埚上部区域均匀分为三段,从下至上每段的密度分别为1.59g/cm3、1.49g/cm3、1.39/cm3;碳-碳复合材料基体1从底部至顶部同样均匀分为三个区域:底部区域、中间区域和上部区域,碳-碳复合材料基体1底部区域的密度为1.2g/cm3;碳-碳复合材料基体1的中间区域均匀分为三段,从下至上每段的密度分别为1.1g/cm3、1.0g/cm3、0.9g/cm3;碳-碳复合材料基体1的上部区域均匀分为三段,从下至上每段的密度分别为0.8g/cm3、0.7g/cm3、0.6g/cm3;石墨化热解碳-碳纤维层2的石墨化热解碳层3的总厚度70μm,高温热解石墨层4的厚度为30μm。
[0037]
本实施例的复合材料坩埚的制备方法,包括以下步骤:(1)采用细编穿刺梯度编织的方法制备碳纤维预制体:水平方向为碳纤维布,垂直方向为穿刺纤维束,纤维束与水平平面正交的方式,将碳纤维预制体编织成以下端到上端密度呈梯度递减的梯度结构,通过控制密度从而实现从上至下热导率梯度递减的趋势,解决籽晶与升华源之间的温度梯度难于精确控制的技术问题;(2)采用化学气相渗透法,对碳纤维预制体进行增密和定型处理:a.工装制备和放置:制备出壁厚为3mm的石墨坩埚工装并置于碳纤维预制体坩埚内部,对碳纤维预制体起到结构固定的作用,石墨坩埚工装壁面均匀制备出直径为20mm的通孔,通孔边间距为5mm,保证石墨工装能向其背面均匀输送碳源气体;b.化学气相渗透沉积增密定型:化学气相沉积温度为900℃,升温速率为10℃/min;沉积时间600小时;碳源气氛为丙烯;稀释气体为氮气;碳源气体流量为5l/min;稀释气体流量为2.5l/min;经初步化学气相渗透沉积增密定型后的碳纤维预制体密度分布情况为:从底部到上部的密度分别为:1.5g/cm3,1.4g/cm3,1.3g/cm3,1.2g/cm3,1.1g/cm3,1.0g/cm3,0.9g/cm3;c.采用液相浸渍对碳纤维预制体进一步增密处理:液相浸渍工序需要进行两个步骤,分别为液相浸渍和高温碳化处理;液相浸渍需要循环2次,液相浸渍温度为60℃,液相浸渍时间5h,浸渍压力1.5mpa,浸渗气氛为真空,浸渍剂选用呋喃树脂,浸渍完成后对其进行高温碳化处理2次,碳化温度800℃,升温速率为10℃/min,碳化处理气氛为惰性保护气体;一次液相浸渍和高温碳化处理后,形成低密度碳-碳复合材料,随后对其进行第二次液相浸渍和高温碳化处理得到中间体;二次液相浸渍和高温碳化处理过程中,首先对低密度碳-碳复合材料表面进行凹槽处理,凹槽的宽度为2mm,凹槽的深度为4
㎜
,凹槽边间距为5mm,该凹槽是为了给下一步浸渍提供浸渍所需的开孔孔隙结构,避免第一次液相浸渍封孔导致浸渍料难以浸渗的问题;(3)增密和定型处理完成后,对中间体进行高温石墨化处理,处理温度为2000℃,升温速率为50℃/min,保温时间为5h;经过增密和定型处理和石墨化纯化后,中间体的密度分布情况为:从底部到上部的密度分别为:1.9g/cm3,1.79g/cm3,1.69g/cm3,1.59g/cm3,1.49g/cm3,1.39g/cm3,1.29g/cm3;(4)制备石墨化热解碳层3:先在低温区进行化学气相沉积制备热解碳-碳纤维层。该阶段的沉积温度为890℃;升温速率为10℃/min;气相碳源为丙烯,稀释气体为氮气,两气体的流量分别为3l/min和1.5l/min;沉积时间为80小时,涂层厚度为70μm。沉积该热解碳-碳纤维层的目的是进一步提高碳-碳坩埚表面的致密度,通过低温段的低成本热解碳增密的方法对碳-碳坩埚表面的孔洞和裂纹进行填充和修复,提高坩埚壁面对高温腐蚀性气氛的抵抗力;将沉积了热解碳-碳纤维层的中间体表面再进一步升温至石墨化温度(2000℃),升温速率为30℃/min,保温3小时,制得石墨化热解碳层3;(5)随后通入cl2进行纯化处理,纯化温度与石墨化温度相同,纯化时间为3h,cl2流量为3l/min;(6)纯化处理后,将样品取出,进行机械加工成所需坩埚结构和尺寸,并进行高纯去离子水超声洗涤和真空干燥处理;洗涤时间为3h,干燥时间为10h,干燥温度为50℃;(7)制备高温热解石墨层4:在高温区通入甲烷气相碳源气体,选用氢气作为稀释
气体,气体流量分别为:2l/min,1l/min,通入气体的时间为5小时,沉积厚度为30μm,最终在中间体表面制备出一层零缺陷、接近理论密度、高温性能稳定的各向异性高温热解石墨层4,即得到本实施例的复合材料坩埚。
[0038]
最终,进行梯度高温碳涂层涂覆后的样品密度分布状态为,从底部到上部的密度分别为:1.99g/cm3,1.89g/cm3,1.79g/cm3,1.69g/cm3,1.59g/cm3,1.49g/cm3,1.39g/cm3。
[0039]
采用分段式取样的方法,对各个密度区域的复合材料坩埚壁材料进行取样,并对其进行热导率测试,结果表明从坩埚底部到上部的密度分别为:1.99g/cm3,1.89g/cm3,1.79g/cm3,1.69g/cm3,1.59g/cm3,1.49g/cm3,1.39g/cm3的各区域(x~y方向)热导率分别为:199/(m
·
k),178w/(m
·
k),145w/(m
·
k),134w/(m
·
k),118w/(m
·
k)。相比实施例1,整体密度增加,各区域热导率均增加。
[0040]
将复合材料坩埚放入高温石墨化炉内进行升温测试,升温速率为20℃/min,升温制700℃,每个密度区间内部设置了热电偶测温棒。结果表明,从坩埚底部到上部的密度分别为:1.9g/cm3,1.8g/cm3,1.7g/cm3,1.6g/cm3,1.5g/cm3,1.4g/cm3,1.3g/cm3的各区域(x~y方向)的坩埚内部的温度为:689℃,565℃,554℃,534℃,521℃,513℃,507℃。在没有装sic单晶生长原料的坩埚不同密度区域的升温速率差异不是很大,这主要是由于在加热时,整个炉腔体内的温度差异较小,在没有温度消耗的情况下,坩埚热导率差异促进温度梯度的效果不那么明显。相比实施例1,整体密度增加,材料的热损耗减少。
[0041]
将复合材料坩埚进行高温生产仿真,结果表明,装有sic单晶生长原料的坩埚加热至2500℃时,放置于坩埚底部的高纯sic粉末需要分解成坩埚顶部籽晶区sic单晶生长所需的气相si源和c源,在这个过程需要吸收坩埚内部的大量热量,因此通过坩埚避免向坩埚内部导热的速率收到影响,因此温度仿真结果,即从坩埚底部到上部的密度分别为:1.99g/cm3,1.89g/cm3,1.79g/cm3,1.69g/cm3,1.59g/cm3,1.49g/cm3,1.39g/cm3的各区域(x~y方向)的坩埚内部的温度分别为:2435℃,2418℃,2406℃,2201℃,2001℃,1853℃,1635℃。这充分体现了梯度碳-碳坩埚能有效提高单晶生长环境的梯温度梯度性,提高单晶生长的环境适用性。相比实施例1,各区域温度均有所增加,但梯度性依然保持较好的状态。
[0042]
将截取的复合材料坩埚一区域(密度为1.99g/cm3的坩埚壁区域)进行抗热震性能测试,测试温度为1200℃到室温,持续时间为10分钟,在氩气保护气氛下进行,循环次数为10次,结果表明涂层未见脱落,通过抗热震性能测试后的样品进行弯曲强度测试,结果表明,抗弯强度为350mpa。相比实施例1,密度越高,其力学强度越高。
[0043]
实施例3如图1所示,本实施例的复合材料坩埚,同样包括碳-碳复合材料基体1和设置在碳-碳复合材料基体1表面的涂层,碳-碳复合材料基体1的密度从底部至顶部依次递减,并经过热解碳增密的碳纤维增强的碳-碳复合材料;涂层为由内向外依次叠加的热解碳-碳纤维层、石墨化热解碳层3,高温热解石墨层4;与实施例1和实施例2之间的差别仅在于,复合材料坩埚的密度分布不同,本实施例的复合材料坩埚从底部到上部的密度分别为:1.85g/cm3,1.76g/cm3,1.68g/cm3,1.55g/cm3,1.47g/cm3,1.33g/cm3,1.35g/cm3(顺序与实施例1、实施例2对应)。
[0044]
本实施例的复合材料坩埚的制备方法与实施例1及实施例2相同。
[0045]
采用分段式取样的方法,对各个密度区域的坩埚壁材料进行取样,并对其进行热
导率测试,结果表明从坩埚底部到上部的密度分别为:1.85g/cm3,1.76g/cm3,1.68g/cm3,1.55g/cm3,1.47g/cm3,1.33g/cm3,1.35g/cm3的各区域(x~y方向)热导率分别为:185/(m
·
k),168w/(m
·
k),135w/(m
·
k),124w/(m
·
k),108w/(m
·
k)。相比实施例2,整体密度降低,各区域热导率均降低。
[0046]
将梯度高温碳涂层梯度坩埚放入高温石墨化炉内进行升温测试,升温速率为20℃/min,升温制700℃,每个密度区间内部设置了热电偶测温棒。结果表明,从坩埚底部到上部的密度分别为:1.85g/cm3,1.76g/cm3,1.68g/cm3,1.55g/cm3,1.47g/cm3,1.33g/cm3,1.35g/cm3的各区域(x~y方向)的坩埚内部的温度为:654℃,532℃,521℃,518℃,515℃,511℃,502℃。在没有装sic单晶生长原料的坩埚不同密度区域的升温速率差异不是很大,这主要是由于在加热时,整个炉腔体内的温度差异较小,在没有温度消耗的情况下,坩埚热导率差异促进温度梯度的效果不那么明显。相比实施例2,整体密度降低,材料的热损耗增加。
[0047]
将梯度高温碳涂层涂覆梯度碳-碳坩埚进行高温生产仿真,结果表明,装有sic单晶生长原料的坩埚加热至2500℃时,放置于坩埚底部的高纯sic粉末需要分解成坩埚顶部籽晶区sic单晶生长所需的气相si源和c源,在这个过程需要吸收坩埚内部的大量热量,因此通过坩埚避免向坩埚内部导热的速率收到影响,因此温度仿真结果,即从坩埚底部到上部的密度分别为:1.85g/cm3,1.76g/cm3,1.68g/cm3,1.55g/cm3,1.47g/cm3,1.33g/cm3,1.35g/cm3的各区域(x~y方向)的坩埚内部的温度分别为:2267℃,2258℃,2268℃,1768℃,1578℃,1415℃,1410℃。这充分体现了梯度碳-碳坩埚能有效提高单晶生长环境的梯温度梯度性,提高单晶生长的环境适用性。相比实施例2,各区域温度均降低。
[0048]
将截取的梯度高温碳涂层涂覆梯度碳-碳坩埚一区域(密度为1.85g/cm3的坩埚壁区域)进行抗热震性能测试,测试温度为1200℃到室温,持续时间为10分钟,在氩气保护气氛下进行,循环次数为10次,结果表明涂层未见脱落,通过抗热震性能测试后的样品进行弯曲强度测试,结果表明,抗弯强度为295mpa。相比实施例1和2,密度降低,其力学强度也随之降低。
[0049]
实施例4如图1所示,本实施例的复合材料坩埚,同样包括碳-碳复合材料基体1和设置在碳-碳复合材料基体1表面的涂层,碳-碳复合材料基体1的密度从底部至顶部依次递减,并经过热解碳增密的碳纤维增强的碳-碳复合材料;涂层为由内向外依次叠加的热解碳-碳纤维层、石墨化热解碳层3,高温热解石墨层4;与实施例1和实施例2之间的差别仅在于,复合材料坩埚的密度分布不同,本对比例的复合材料坩埚从底部到上部的密度分别为1.91g/cm3,1.81g/cm3,1.71g/cm3,1.61g/cm3,1.51g/cm3,1.41g/cm3,1.31g/cm3。坩埚密度相比实施例2,有所降低。
[0050]
本实施例的复合材料坩埚的制备方法与实施例1及实施例2相同。
[0051]
采用分段式取样的方法,对各个密度区域的坩埚壁材料进行取样,并对其进行热导率测试,结果表明从坩埚底部到上部的密度分别为:1.91g/cm3,1.81g/cm3,1.71g/cm3,1.61g/cm3,1.51g/cm3,1.41g/cm3,1.31g/cm3的各区域(x~y方向)热导率分别为:191/(m
·
k),171w/(m
·
k),139w/(m
·
k),125w/(m
·
k),110w/(m
·
k)。相比实施例1,整体密度降低,各区域热导率均少量降低。
[0052]
将梯度高温碳涂层梯度坩埚放入高温石墨化炉内进行升温测试,升温速率为20℃/min,升温制700℃,每个密度区间内部设置了热电偶测温棒。结果表明,从坩埚底部到上部的密度分别为:1.91g/cm3,1.81g/cm3,1.71g/cm3,1.61g/cm3,1.51g/cm3,1.41g/cm3,1.31g/cm3的各区域(x~y方向)的坩埚内部的温度为:683℃,561℃,551℃,531℃,518℃,512℃,507℃。在没有装sic单晶生长原料的坩埚不同密度区域的升温速率差异不是很大,这主要是由于在加热时,整个炉腔体内的温度差异较小,在没有温度消耗的情况下,坩埚热导率差异促进温度梯度的效果不那么明显。相比实施例2,整体密度降低,材料的热损耗少量增加。
[0053]
将梯度高温碳涂层涂覆梯度碳-碳坩埚进行高温生产仿真,结果表明,装有sic单晶生长原料的坩埚加热至2500℃时,放置于坩埚底部的高纯sic粉末需要分解成坩埚顶部籽晶区sic单晶生长所需的气相si源和c源,在这个过程需要吸收坩埚内部的大量热量,因此通过坩埚避免向坩埚内部导热的速率收到影响,因此温度仿真结果,即从坩埚底部到上部的密度分别为:1.91g/cm3,1.81g/cm3,1.71g/cm3,1.61g/cm3,1.51g/cm3,1.41g/cm3,1.31g/cm3的各区域(x~y方向)的坩埚内部的温度分别为:2425℃,2408℃,2398℃,2194℃,1988℃,1855℃,1635℃。这充分体现了梯度碳-碳坩埚能有效提高单晶生长环境的梯温度梯度性,提高单晶生长的环境适用性。但相比实施例2,各区域温度均有所降低,但梯度性依然保持较好的状态。
[0054]
将截取的梯度高温碳涂层涂覆梯度碳-碳坩埚一区域(密度为1.91g/cm3的坩埚壁区域)进行抗热震性能测试,测试温度为1200℃到室温,持续时间为10分钟,在氩气保护气氛下进行,循环次数为10次,结果表明涂层出现脱落,这表明均质涂层相比实施例1和2的梯度涂层,其界面结合强度有所降低。
[0055]
通过抗热震性能测试后的样品进行弯曲强度测试,结果表明,抗弯强度为320mpa。相比实施例1,其力学强度有所降低。
[0056]
对比例1本对比例选用均质的等静压石墨作为坩埚原材料(等静压石墨原料的密度为1.9g/cm3),按照实施例1的坩埚尺寸制备同样尺寸大小的坩埚,并采用高温化学气相沉积的方法在坩埚表面制备涂层,得到本对比例的坩埚产品,涂层的结构、厚度进而制备方法均与对比文件1一致。
[0057]
本对比例的坩埚产品的密度分布为均质分布状态,坩埚密度为1.99g/cm3。
[0058]
对本对比例的坩埚产品的热导率进行测试发现,该坩埚各个区域的热导率均为120w/(m
·
k)。
[0059]
将本对比例的坩埚产品放入高温石墨化炉内进行升温测试,升温速率为20℃/min,升温制700℃,每个坩埚高度区间内部设置了热电偶测温棒。结果表明,从坩埚底部到上部温度均约为:678℃,且坩埚内完全没形成一种利于单晶生长的温度梯度。
[0060]
将截取的本对比例的坩埚产品的一区域进行抗热震性能测试,测试温度为1200℃到室温,持续时间为10分钟,在氩气保护气氛下进行,循环次数为10次,结果表明涂层未出现脱落。但是通过抗热震性能测试后的样品进行弯曲强度测试,结果表明,抗弯强度为58mpa。相比实施例1,2,其力学强度非常低,这说明本对比例的坩埚产品的使用寿命将会远短于实施例1的复合材料坩埚。
[0061]
以上所述仅是本发明的优选实施方式,本发明的保护范围并不仅局限于上述实施例。对于本技术领域的技术人员来说,在不脱离本发明技术构思前提下所得到的改进和变换也应视为本发明的保护范围。