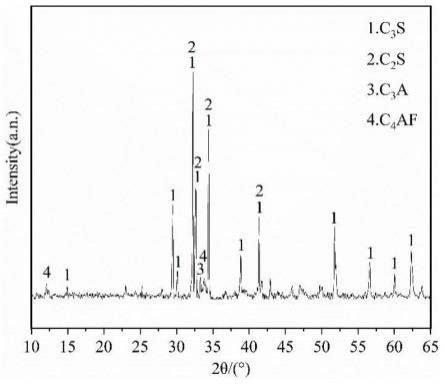
1.本发明属于混凝土材料技术领域,特别涉及一种绿泥石英片岩硅酸盐水泥熟料及其制备方法。
背景技术:2.绿泥石英片岩是一种矿山废石,其主要氧化物为sio2和al2o3,以鞍山各大矿区为例,绿泥石英片岩的sio2含量平均60%,al2o3含量平均11%,目前对绿泥石英片岩的资源化利用较少。
3.硅铝质原料是水泥熟料中酸性氧化物(sio2、al2o3)的主要来源。现如今生产水泥的天然硅铝质原料一般是黄土、黏土、页岩、泥岩、粉砂岩等。随着水泥用量的迅速增加以及石灰石和黏土等不可再生资源的减少,从化学组成上看,绿泥石英片岩能够替代传统硅铝质原料为水泥熟料提供稳定的酸性氧化物。这能够缓解传统硅铝资源减少的危机,也能实现矿山固体废弃物资源化利用。
4.有学者将矿山废石应用到水泥熟料制备中,并且取得了一定的成果。
5.张存仁,杨建康,李新于2017年在《中国水泥》第4期发表的“矿山剥离废石在水泥生产中的综合利用”中对武家河大理岩矿山剥离废石进行分析,发现剥离废石中含有凝灰岩,由于凝灰岩中含铁比较稳定,且铁和铝比例符合生产低碱水泥的要求,因此,用其代替了硫酸渣和黏土产出水泥,并取得良好的效果。覃爱平,程海平,徐合林于2016年在《水泥》第12期发表的“高镁废石在白水泥生产中的应用”中将石灰矿山中的高镁废石进行分级处理,将其与石灰石按一定比例搭配,然后以一定比例煤炭和石油焦作为燃料进行熟料快烧,得到白度达87%以上的熟料;最后,将其与精选的高镁废石、方解石和石灰等进行混合研磨,制备出各项指标均符合国家标准的水泥。
6.刘连成于2007年在《new building materials》第5期发表的“coal gangue cement synthesized at low temperature”中以煤矸石作为原料,经过低温活化,形成矸石渣,然后将其与生石灰和晶种按比例混合后研磨,将研磨产品经过水热合成—低温焙烧—加入石膏后制得水泥。
7.杨兆祺,王振芳,曹文霞于2008年在《水泥技术》第2期发表的“绿泥石石英片岩用作硅铝铁质原料的试验与生产”中将新疆拉他加依绿泥石英片岩作为硅铝铁质原料生产水泥,取得了一定的效果。需要注意的是,新疆地区的绿泥石英片岩位于远古界地层,属于低硅高镁高铁型岩石,sio2含量平均只有44.55%,mgo平均含量为6.98%,fe2o3平均含量为13.51%;而鞍山地区的绿泥石英片岩大多位于太古界地层,年代更为久远,属于高硅高镁低铁型岩石,sio2平均含量达到60%,mgo平均含量达到9%,fe2o3平均含量为6%;可以看出,两个地区的绿泥石英片岩在化学成分上存在较大差异,文献“绿泥石石英片岩用作硅铝铁质原料的试验与生产”的研究仅适用于新疆地区的绿泥石英片岩,且并未给出具体的实施方案,对于鞍山地区的绿泥石英片岩难以推广使用。
技术实现要素:8.本发明的目的是为了寻找水泥替代原料,提供一种绿泥石英片岩硅酸盐水泥熟料及其制备方法。该方法制备的生料易磨性好,生产的熟料强度高,能实现矿山固体废弃资源化综合利用,有效缓解水泥企业原材料短缺问题。
9.本发明技术方案具体内容如下:
10.一种绿泥石英片岩硅酸盐水泥熟料,所述的硅酸盐水泥熟料以绿泥石英片岩、石灰石、钢渣、砂岩和粉煤灰为原料,经破碎、球磨、成型、高温煅烧后冷却制备而成。
11.其中,所述原料的质量百分比含量为:石灰石83%-84%,绿泥石英片岩4%-6%,砂岩5%-6%,粉煤灰2%-3%,钢渣3%-4.5%。
12.所述原料的化学成分要求如下:
13.绿泥石英片岩二氧化硅含量>57%;三氧化二铝含量>10%;三氧化二铁含量>5%;氧化镁含量<10%;
14.石灰石为中钙石灰石,其氧化钙含量>48%;二氧化硅含量<7%;氧化镁含量<2%;
15.砂岩二氧化硅含量>80%;氧化镁含量<1%;
16.粉煤灰三氧化二铝含量>30%;
17.钢渣三氧化二铁含量>25%;
18.所述的硅酸盐水泥熟料率值控制范围为:石灰饱和系数kh=0.91
±
0.02、硅率sm=2.40
±
0.10、铝率im=1.40
±
0.10。
19.所述的硅酸盐水泥熟料主要矿物组成为:c3s 52%~55%,c2s 18%~22%,c3a8%~11%,c4af 10%~13%。
20.上述绿泥石英片岩硅酸盐水泥熟料的制备方法,包括以下步骤:
21.(1)球磨:将粒径<2mm绿泥石英片岩、石灰石、砂岩、粉煤灰、钢渣烘干后,分别放入球磨机中球磨60min-70min,得到细粉原料,然后将细粉原料按照生料配比混合均匀后放入球磨机中混匀20min以上,将球磨混匀得到的原料用0.08mm方孔筛筛分,控制生料细度为0.08mm方孔筛的筛余量<10%,制得生料;
22.(2)生料成型:在生料中加入质量为生料10%~15%的水和2~5%的粘结剂(如聚乙烯醇、液体硅酸钠等),将充分搅拌均匀后的含水生料放入生料成型模具内压制成型,然后将成型生料块放入烘干箱中烘干;
23.(3)熟料煅烧:将干燥后的生料块置于已升温至700~800℃的炉内,并且继续以8~10℃/min的速率升温至1350℃~1400℃,然后恒温30~40min;煅烧完成后将炉温降至1250℃~1300℃时取出试样,置于空气中风冷至室温,得到硅酸盐水泥熟料。
24.进一步的,上述绿泥石英片岩硅酸盐水泥熟料的制备方法,所述步骤(2)中的干燥为以恒温105~115℃干燥1h以上。
25.本发明具有以下的优点和技术效果:
26.(1)本发明利用矿山采剥废石-绿泥石英片岩作为水泥硅铝质原料煅烧硅酸盐水泥熟料,可以降低煅烧热耗及水泥生产成本,为矿山废石处理提供了一个新的途径。
27.(2)本发明用绿泥石英片岩作为水泥硅铝质原料煅烧硅酸盐水泥熟料,为水泥企业提供了一个新的水泥硅铝质原料来源。
28.(3)本发明用矿山采剥废石-绿泥石英片岩作为水泥硅铝质原料煅烧出的硅酸盐水泥熟料游离氧化钙含量达标、主要矿物组成为:c3s 52%~55%,c2s 18%~22%,c3a 8%~11%,c4af 10%~13%,硅酸盐水泥熟料阿利特晶体、贝利特晶体发育良好,说明绿泥石英片岩作为硅铝质原料煅烧出的水泥熟料表现良好。
29.(4)本发明通过对制得的硅酸盐水泥熟料进行性能试验,结果表明,水泥熟料的安定性良好;初凝时间>120min,终凝时间<260min,3d抗压强度>21.0mpa、抗折强度>5.0mpa,28d抗压强度>40.0mpa、抗折强度>7.5mpa。
附图说明
30.图1、实例1熟料xrd图谱。
31.图2、实例2熟料xrd图谱。
32.图3、实例3熟料xrd图谱。
具体实施方式
33.为了阐述本发明的方法,使技术方案清晰明了,结合以下实施例,对本发明进一步详细描述。应当说明,此处所描述的仅是本发明的一部分实施例,而不是全部的实施例。基于本发明中的实施例,本领域普通技术人员在没有做出创造性劳动的前提下所获得的所有其它实施例,都属于本发明保护的范围。
34.原料处理要求:各原料经破碎机破碎后须烘干后按配比称料,球磨机内混匀时间不得低于20min。
35.实施例1
36.(1)原料预处理:将绿泥石英片岩、石灰石、砂岩、粉煤灰、钢渣用破碎机进行破碎处理,取通过2mm方孔筛的原料并进行预均化处理。
37.(2)生料配比:生料按以下重量百分比原料称取:石灰石83.23%、绿泥石英片岩4%、砂岩5.83%、粉煤灰2.83%、钢渣4.11%;
38.(3)球磨:将破碎后的绿泥石英片岩、石灰石、砂岩、粉煤灰、钢渣烘干后分别放入球磨机中球磨60min,得到细粉原料,然后将细粉原料按照生料配比混合均匀后放入球磨机中混匀20min,将球磨混匀得到的原料用0.08mm方孔筛筛分,控制生料细度为0.08mm方孔筛的筛余量<10%,制得生料。
39.(4)生料成型:在生料中加入生料质量10%的蒸馏水和生料质量2%的聚乙烯醇,将充分搅拌均匀后的含水生料放入生料成型模具内压制成型,然后将成型生料试块放入烘干箱中以恒温105℃干燥1h。
40.(5)熟料煅烧:将干燥后的生料试样置于已升温至800℃的高温煅烧炉内,并且继续以10℃/min的速率升温至1400℃,然后恒温35min;煅烧完成后将高温煅烧炉温度降至1250℃时取出试样,置于空气中用电吹风急冷至室温,得到硅酸盐水泥熟料。
41.熟料率值范围及矿物含量详见表1,熟料的物理性能参数详见表2,熟料矿物组成见图1。
42.实施例2
43.(1)原料预处理:将绿泥石英片岩、石灰石、砂岩、粉煤灰、钢渣用破碎机进行破碎
处理,取通过2mm方孔筛的原料并进行预均化处理。
44.(2)生料配比:生料按以下重量百分比原料称取:石灰石83.17%、绿泥石英片岩5%、砂岩5.61%、粉煤灰2.42%、钢渣3.8%;
45.(3)球磨:将破碎后的绿泥石英片岩、石灰石、砂岩、粉煤灰、钢渣烘干后分别放入球磨机中球磨65min,得到细粉原料,然后将细粉原料按照生料配比混合均匀后放入球磨机中混匀22min,将球磨混匀得到的原料用0.08mm方孔筛筛分,控制生料细度为0.08mm方孔筛的筛余量<10%,制得生料。
46.(4)生料成型:在生料中加入11%的蒸馏水和3%的聚乙烯醇,将充分搅拌均匀后的含水生料放入生料成型模具内压制成型,然后将成型生料试块放入烘干箱中以恒温105℃干燥70min。
47.(5)熟料煅烧:将干燥后的生料试样置于已升温至800℃的高温煅烧炉内,并且继续以10℃/min的速率升温至1390℃,然后恒温30min;煅烧完成后将高温煅烧炉温度降至1270℃时取出试样,置于空气中用电风扇急冷至室温,得到硅酸盐水泥熟料。
48.熟料率值范围及矿物含量详见表1,熟料的物理性能参数详见表2,熟料矿物组成见图2。
49.实施例3
50.(1)原料预处理:将绿泥石英片岩、石灰石、砂岩、粉煤灰、钢渣用破碎机进行破碎处理,取通过2mm方孔筛的原料并进行预均化处理。
51.(2)生料配比:生料按以下重量百分比原料称取:石灰石83.17%、绿泥石英片岩6%、砂岩5.2%、粉煤灰2.24%、钢渣3.39%;
52.(3)球磨:将破碎后的绿泥石英片岩、石灰石、砂岩、粉煤灰、钢渣烘干后分别放入球磨机中球磨67min,得到细粉原料,然后将细粉原料按照生料配比混合均匀后放入球磨机中混匀21min,将球磨混匀得到的原料用0.08mm方孔筛筛分,控制生料细度为0.08mm方孔筛的筛余量<10%,制得生料。
53.(4)生料成型:在生料中加入13%的蒸馏水和5%的聚乙烯醇,将充分搅拌均匀后的含水生料放入生料成型模具内压制成型,然后将成型生料试块放入烘干箱中以恒温105℃干燥75min。
54.(5)熟料制成:将干燥后的生料试样置于已升温至800℃的高温煅烧炉内,并且继续以10℃/min的速率升温至1350℃,然后恒温40min;煅烧完成后将高温煅烧炉温度降至1300℃时取出试样,置于空气中用电风扇急冷至室温,得到硅酸盐水泥熟料。
55.熟料率值范围及矿物含量详见表1,熟料的物理性能参数详见表2,熟料矿物组成见图3。
56.表1熟料率值范围及矿物组成
57.58.表2熟料物理性能
59.