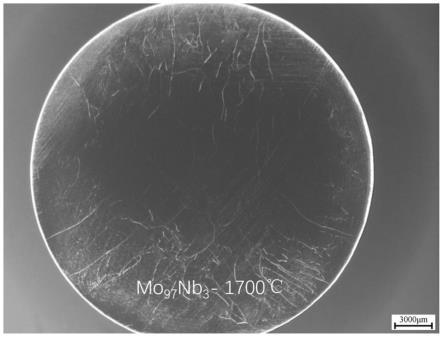
1.本发明属于钼铌单晶室温力学性能优化技术领域,具体涉及一种提升钼铌单晶室温力学性能的方法。
背景技术:2.金属钼是典型的的体心立方金属,具有高熔点(~2610℃)和优异的高温性能,例如高热稳定性,良好的理化性能。此外,在难熔金属中,钼的成本相对较低。考虑到传统的多晶钼中存在大量的大角度晶界,而晶界存在着大量的缺陷。这些缺陷会导致高温下的结构稳定性变差,如蠕变速率增大,合金元素向晶界处偏析等现象。因此,在服役条件苛刻的环境中,通常使用单晶钼及钼合金来取代传统的多晶钼材料。但是纯钼单晶的室温塑性较好,但是强度降低,在实际使用时存在不足。
3.因此,需要提供一种室温力学性能优异的钼铌单晶。
技术实现要素:4.本发明所要解决的技术问题在于针对上述现有技术的不足,提供一种提升钼铌单晶室温力学性能的方法。该方法通过在钼单晶中添加合金元素铌,有效提升纯钼单晶的强度和高温稳定性,并将通过电子束悬浮区域熔炼制备得到的钼铌单晶进行真空退火,有效降低钼铌单晶体系的内应力,从而促进位错滑移,以此提升钼铌单晶的力学性能,尤其是塑性变形能力。
5.为解决上述技术问题,本发明采用的技术方案是:一种提升钼铌单晶室温力学性能的方法,其特征在于,该方法包括以下步骤:
6.步骤一、将钼原料和铌原料混合,然后通过电子束悬浮区域熔炼,得到退火前单晶钼铌合金;
7.步骤二、将步骤一中得到的退火前单晶钼铌合金进行真空退火,得到力学性能提升的单晶钼铌合金。
8.本发明中经电子束区域熔炼得到的钼铌单晶内部的结构缺陷即位错相对较低,但仍存在大量由位错网缠结而成的亚晶界,且由于合金元素的添加,位错线附近因元素的偏聚而产生附加内应力,从而提高位错开动的势垒,因此,通过真空退火,有效降低钼铌单晶体系的内应力,从而促进位错滑移,以此提升钼铌单晶的力学性能,尤其是塑性变形能力。
9.上述的一种提升钼铌单晶室温力学性能的方法,其特征在于,步骤一中所述单晶钼铌合金为直径29mm~31mm、长度98mm~102mm的棒状样品,所述单晶钼铌合金的晶向偏析角不大于3度。本发明采用棒状样品进行退火是为了使样品在加热和冷却的过程中,与单晶生长时的热传导方向一致,即延轴向辐射状向外,尺寸限制在直径29mm~31mm、长度为98mm~102mm是为了考虑实际的使用工况,限定单晶钼铌合金的晶向偏析角不大于3度是为了降低晶粒取向的分散度和缺陷密度,从而提高钼铌单晶的结构稳定性。
10.上述的一种提升钼铌单晶室温力学性能的方法,其特征在于,步骤一中所述单晶
钼铌合金中铌元素的质量含量为3%~6%,余量为钼。
11.上述的一种提升钼铌单晶室温力学性能的方法,其特征在于,所述单晶钼铌合金中铌元素的质量含量为3%,余量为钼,分子式为mo
97
nb3;所述单晶钼铌合金中铌元素的质量含量为6%,余量为钼,分子式为mo
94
nb6。本发明中采用mo
97
nb3单晶和mo
94
nb6单晶具有显著优于纯mo多晶、单晶的高温强度和结构稳定性,可作为核用电源的核心结构件。
12.上述的一种提升钼铌单晶室温力学性能的方法,其特征在于,步骤二中所述真空退火的温度为1100℃~1700℃。本发明通过控制真空退火的温度有效降低钼铌单晶体系的内应力,从而促进位错滑移,以此提升钼铌单晶的力学性能,尤其是塑性变形能力。
13.上述的一种提升钼铌单晶室温力学性能的方法,其特征在于,当单晶钼铌合金的分子式为mo
97
nb3时退火温度为1485℃~1515℃,当单晶钼铌合金的分子式为mo
94
nb6时退火温度为1285℃~1315℃。
14.本发明对于mo
97
nb3单晶而言,在1285℃~1315℃下退火大幅度提升该合金的延伸率,但是会大幅度降低屈服强度,通过综合对比mo
97
nb3单晶最优的退火温度为1485℃~1515℃效果最优;对于mo
94
nb6单晶而言,在1085℃~1115℃和1285℃~1315℃下低温退火,显著提升该合金的屈服强度,在1485℃~1515℃和1685℃~1715℃更高温度下进行退火可有效改善该合金的延伸率,通过综合对比mo
94
nb6单晶最优的退火温度为1285℃~1315℃。
15.上述的一种提升钼铌单晶室温力学性能的方法,其特征在于,步骤二中所述真空退火的升温速率为20℃/min~40℃/min。本发明通过控制升温速率既可保证试样的均匀受热,亦可避免过慢的加热速率导致的升温过程的氧化。
16.上述的一种提升钼铌单晶室温力学性能的方法,其特征在于,步骤二中所述真空退火的时间为110min~130min。本发明通过控制退火时间,既可保证试样在该温度下得到均匀的组织,亦能避免试样在高温环境中出现的严重氧化。
17.本发明与现有技术相比具有以下优点:
18.1、本发明通过在钼单晶中添加合金元素铌,有效提升纯钼单晶的强度和高温稳定性,并将通过电子束悬浮区域熔炼制备得到的钼铌单晶进行真空退火,有效降低钼铌单晶体系的内应力,从而促进位错滑移,以此提升钼铌单晶的力学性能,尤其是塑性变形能力。
19.2、本发明方法提出的退火工艺简便且易于操作,可为改进钼铌合金单晶的室温力学性能提供可能,通过不同条件下的真空退火工艺,可实现钼铌合金单晶中的缺陷调控,有效改善钼铌合金单晶的室温力学性能
20.3、本发明通过控制真空退火的温度,改善钼铌合金单晶内部的微观缺陷,从而改善钼铌单晶的室温力学性能,对于mo
97
nb3单晶而言,在1285℃~1315℃下退火大幅度提升该合金的延伸率,但是会大幅度降低屈服强度,通过综合对比mo
97
nb3单晶最优的退火温度为1485℃~1515℃效果最优;对于mo
94
nb6单晶而言,在1085℃~1115℃和1285℃~1315℃下低温退火,显著提升该合金的屈服强度,在1485℃~1515℃和1685℃~1715℃更高温度下进行退火可有效改善该合金的延伸率,通过综合对比mo
94
nb6单晶最优的退火温度为1285℃~1315℃。
21.下面通过附图和实施例对本发明的技术方案作进一步的详细描述。
附图说明
22.图1为本发明实施例1步骤一中制备的退火前单晶钼铌合金的x射线衍射图。
23.图2为本发明实施例1步骤二中制备的力学性能提升的退火前单晶钼铌合金的x射线衍射图。
24.图3为本发明实施例4步骤二中制备的力学性能提升的退火前单晶钼铌合金的x射线衍射图。
25.图4为本发明实施例4步骤一中制备的退火前单晶钼铌合金的金相图。
26.图5为本发明实施例4步骤二中制备的力学性能提升的单晶钼铌合金的金相图。
27.图6为本发明实施例5步骤一中制备的退火前单晶钼铌合金的x射线衍射图。
28.图7为本发明实施例5步骤二中制备的力学性能提升的单晶钼铌合金的x射线衍射图。
29.图8为本发明实施例8步骤二中制备的力学性能提升的单晶钼铌合金的x射线衍射图。
30.图9为本发明实施例8步骤一中制备的退火前单晶钼铌合金的金相图。
31.图10为本发明实施例8步骤二中制备的力学性能提升的单晶钼铌合金的金相图。
32.图11为本发明实施例1~4制备的力学性能提升的单晶钼铌合金的室温拉伸性能测试结果。
33.图12为本发明实施例5~8制备的力学性能提升的单晶钼铌合金的室温拉伸性能测试结果。
具体实施方式
34.实施例1
35.本实施例包括以下步骤:
36.步骤一、将钼原料和铌原料混合,然后通过电子束悬浮区域熔炼,得到退火前单晶钼铌合金;所述单晶钼铌合金为直径30mm、长度为100mm的棒状样品,所述单晶钼铌合金的晶向偏析角不大于3度;所述单晶钼铌合金中铌元素的质量含量为3%,余量为钼,分子式为mo
97
nb3;
37.步骤二、将步骤一中得到的退火前单晶钼铌合金在真空度不大于5
×
10-3
pa的条件下进行真空退火,得到力学性能提升的单晶钼铌合金;所述真空退火的温度为1085℃~1115℃;所述真空退火的升温速率为30℃/min;所述真空退火的时间为120min;
38.步骤三、将步骤二中得到的退火前单晶钼铌合金和力学性能提升的单晶钼铌合金通过机加工制备为拉伸试样,然后在室温下测试拉伸性能,得到屈服强度和延伸率;所述拉伸试样的直径为3mm,标距段的长度为30mm;所述测试拉伸性能过程中拉伸速度为3mm/min。
39.经检测,本实施例得到的力学性能提升的单晶钼铌合金的屈服强度为408.5mpa,延伸率为9.53%,退火前单晶钼铌合金的屈服强度为380mpa,延伸率约为10.1%。
40.实施例2
41.本实施例包括以下步骤:
42.步骤一、将钼原料和铌原料混合,然后通过电子束悬浮区域熔炼,得到退火前单晶钼铌合金;所述单晶钼铌合金为直径29mm、长度为98mm的棒状样品,所述单晶钼铌合金的晶
向偏析角不大于3度;所述单晶钼铌合金中铌元素的质量含量为3%,余量为钼,分子式为mo
97
nb3;
43.步骤二、将步骤一中得到的退火前单晶钼铌合金在真空度不大于5
×
10-3
pa的条件下进行真空退火,得到力学性能提升的单晶钼铌合金;所述真空退火的温度为1285℃~1315℃;所述真空退火的升温速率为20℃/min;所述真空退火的时间为110min;
44.步骤三、将步骤二中得到的力学性能提升的单晶钼铌合金通过机加工制备为拉伸试样,然后在室温下测试拉伸性能,得到屈服强度和延伸率;所述拉伸试样的直径为3mm,标距段的长度为30mm;所述测试拉伸性能过程中拉伸速度为3mm/min。
45.经检测,本实施例得到的力学性能提升的单晶钼铌合金的屈服强度为382mpa,延伸率为15.45%,退火前单晶钼铌合金的屈服强度为380mpa,延伸率约为10.1%。
46.实施例3
47.本实施例包括以下步骤:
48.步骤一、将钼原料和铌原料混合,然后通过电子束悬浮区域熔炼,得到退火前单晶钼铌合金;所述单晶钼铌合金为直径31mm、长度为102mm的棒状样品,所述单晶钼铌合金的晶向偏析角不大于3度;所述单晶钼铌合金中铌元素的质量含量为3%,余量为钼,分子式为mo
97
nb3;
49.步骤二、将步骤一中得到的退火前单晶钼铌合金在真空度不大于5
×
10-3
pa的条件下进行真空退火,得到力学性能提升的单晶钼铌合金;所述真空退火的温度为1485℃~1515℃;所述真空退火的升温速率为40℃/min;所述真空退火的时间为130min;
50.步骤三、将步骤二中得到的力学性能提升的单晶钼铌合金通过机加工制备为拉伸试样,然后在室温下测试拉伸性能,得到屈服强度和延伸率;所述拉伸试样的直径为3mm,标距段的长度为30mm;所述测试拉伸性能过程中拉伸速度为3mm/min。
51.经检测,本实施例得到的力学性能提升的单晶钼铌合金的屈服强度为403mpa,延伸率为13.17%,退火前单晶钼铌合金的屈服强度为380mpa,延伸率约为10.1%。
52.实施例4
53.本实施例包括以下步骤:
54.步骤一、将钼原料和铌原料混合,然后通过电子束悬浮区域熔炼,得到退火前单晶钼铌合金;所述单晶钼铌合金为直径30mm、长度为101mm的棒状样品,所述单晶钼铌合金的晶向偏析角不大于3度;所述单晶钼铌合金中铌元素的质量含量为3%,余量为钼,分子式为mo
97
nb3;
55.步骤二、将步骤一中得到的退火前单晶钼铌合金在真空度不大于5
×
10-3
pa的条件下进行真空退火,得到力学性能提升的单晶钼铌合金;所述真空退火的温度为1685℃~1715℃;所述真空退火的升温速率为30℃/min;所述真空退火的时间为115min;
56.步骤三、将步骤二中得到的力学性能提升的单晶钼铌合金通过机加工制备为拉伸试样,然后在室温下测试拉伸性能,得到屈服强度和延伸率;所述拉伸试样的直径为3mm,标距段的长度为30mm;所述测试拉伸性能过程中拉伸速度为3mm/min。
57.经检测,本实施例得到的力学性能提升的单晶钼铌合金的屈服强度为400.3mpa,延伸率为12.7%,退火前单晶钼铌合金的屈服强度为380mpa,延伸率约为10.1%。
58.图1为本发明实施例1步骤一中制备的退火前单晶钼铌合金的x射线衍射图,图2为
本发明实施例1步骤二中制备的力学性能提升的单晶钼铌合金的x射线衍射图,图3为本发明实施例4步骤二中制备的力学性能提升的单晶钼铌合金的x射线衍射图,从图1-图3中可以看出,退火前后的单晶钼铌合金均仅在2θ为116.1
°
处出现峰值,代表222晶面的衍射,该结果表明尽管在1700℃下高温退火,单晶钼铌合金均保持单晶结构。
59.图4为本发明实施例4步骤一中制备的退火前单晶钼铌合金的金相图,图5为本发明实施例4步骤二中制备的力学性能提升的单晶钼铌合金的金相图,从图4和图5中可以看出,力学性能提升的单晶钼铌合金中的亚晶界数量与退火前单晶钼铌合金相比明显降低,意味着退火后单晶钼铌合金中的缺陷数量大幅度减少,性能提升。
60.图11为本发明实施例1~4制备的力学性能提升的单晶钼铌合金的室温拉伸性能测试结果,从图11中可以看出,1085℃~1115℃低温退火后的mo
97
nb3屈服强度和延伸率均略有上升,1285℃~1315℃退火后,mo
97
nb3的延伸率得以大幅度上升,进一步提高退火温度至1485℃~1515℃和1685℃~1715℃时,mo
97
nb3单晶的屈服强度和延伸率与退火前相差不大,因此,为了得到延伸率较高mo
97
nb3单晶样品,1285℃~1315℃为最佳真空退火温度。
61.实施例5
62.本实施例包括以下步骤:
63.步骤一、将钼原料和铌原料混合,然后通过电子束悬浮区域熔炼,得到退火前单晶钼铌合金;所述单晶钼铌合金为直径30mm、长度为99mm的棒状样品,所述单晶钼铌合金的晶向偏析角不大于3度;所述单晶钼铌合金中铌元素的质量含量为6%,余量为钼,分子式为mo
94
nb6;
64.步骤二、将步骤一中得到的退火前单晶钼铌合金在真空度不大于5
×
10-3
pa的条件下进行真空退火,得到力学性能提升的单晶钼铌合金;所述真空退火的温度为1085℃~1115℃;所述真空退火的升温速率为20℃/min;所述真空退火的时间为125min;
65.步骤三、将步骤二中得到的力学性能提升的单晶钼铌合金通过机加工制备为拉伸试样,然后在室温下测试拉伸性能,得到屈服强度和延伸率;所述拉伸试样的直径为3mm,标距段的长度为30mm;所述测试拉伸性能过程中拉伸速度为3mm/min。
66.经检测,本实施例得到的力学性能提升的单晶钼铌合金的屈服强度为474.7mpa,延伸率为9.8%,退火前单晶钼铌合金的屈服强度为431mpa,延伸率约为10.3%。
67.实施例6
68.本实施例包括以下步骤:
69.步骤一、将钼原料和铌原料混合,然后通过电子束悬浮区域熔炼,得到退火前单晶钼铌合金;所述单晶钼铌合金为直径29mm、长度为102mm的棒状样品,所述单晶钼铌合金的晶向偏析角不大于3度;所述单晶钼铌合金中铌元素的质量含量为6%,余量为钼,分子式为mo
94
nb6;
70.步骤二、将步骤一中得到的退火前单晶钼铌合金在真空度不大于5
×
10-3
pa的条件下进行真空退火,得到力学性能提升的单晶钼铌合金;所述真空退火的温度为1285℃~1315℃;所述真空退火的升温速率为40℃/min;所述真空退火的时间为120min;
71.步骤三、将步骤二中得到的力学性能提升的单晶钼铌合金通过机加工制备为拉伸试样,然后在室温下测试拉伸性能,得到屈服强度和延伸率;所述拉伸试样的直径为3mm,标距段的长度为30mm;所述测试拉伸性能过程中拉伸速度为3mm/min。
72.经检测,本实施例得到的力学性能提升的单晶钼铌合金的屈服强度为470.3mpa,延伸率为11.8%,退火前单晶钼铌合金的屈服强度为431mpa,延伸率约为10.3%。
73.实施例7
74.本实施例包括以下步骤:
75.步骤一、将钼原料和铌原料混合,然后通过电子束悬浮区域熔炼,得到退火前单晶钼铌合金;所述单晶钼铌合金为直径31mm、长度为98mm的棒状样品,所述单晶钼铌合金的晶向偏析角不大于3度;所述单晶钼铌合金中铌元素的质量含量为6%,余量为钼,分子式为mo
94
nb6;
76.步骤二、将步骤一中得到的退火前单晶钼铌合金在真空度不大于5
×
10-3
pa的条件下进行真空退火,得到力学性能提升的单晶钼铌合金;所述真空退火的温度为1485℃~1515℃;所述真空退火的升温速率为30℃/min;所述真空退火的时间为110min;
77.步骤三、将步骤二中得到的力学性能提升的单晶钼铌合金通过机加工制备为拉伸试样,然后在室温下测试拉伸性能,得到屈服强度和延伸率;所述拉伸试样的直径为3mm,标距段的长度为30mm;所述测试拉伸性能过程中拉伸速度为3mm/min。
78.经检测,本实施例得到的力学性能提升的单晶钼铌合金的屈服强度为439.3mpa,延伸率为16%,退火前单晶钼铌合金的屈服强度为431mpa,延伸率约为10.3%。
79.实施例8
80.本实施例包括以下步骤:
81.步骤一、将钼原料和铌原料混合,然后通过电子束悬浮区域熔炼,得到退火前单晶钼铌合金;所述单晶钼铌合金为直径30mm、长度为100mm的棒状样品,所述单晶钼铌合金的晶向偏析角不大于3度;所述单晶钼铌合金中铌元素的质量含量为6%,余量为钼,分子式为mo
94
nb6;
82.步骤二、将步骤一中得到的退火前单晶钼铌合金在真空度不大于5
×
10-3
pa的条件下进行真空退火,得到力学性能提升的单晶钼铌合金;所述真空退火的温度为1685℃~1715℃;所述真空退火的升温速率为30℃/min;所述真空退火的时间为130min;
83.步骤三、将步骤二中得到的力学性能提升的单晶钼铌合金通过机加工制备为拉伸试样,然后在室温下测试拉伸性能,得到屈服强度和延伸率;所述拉伸试样的直径为3mm,标距段的长度为30mm;所述测试拉伸性能过程中拉伸速度为3mm/min。
84.经检测,本实施例得到的力学性能提升的单晶钼铌合金的屈服强度为425.5mpa,延伸率为16.95%,退火前单晶钼铌合金的屈服强度为431mpa,延伸率约为10.3%。
85.图6为本发明实施例5步骤一中制备的退火前单晶钼铌合金的x射线衍射图,图7为本发明实施例5步骤二中制备的力学性能提升的单晶钼铌合金的x射线衍射图,图8为本发明实施例8步骤二中制备的力学性能提升的单晶钼铌合金的x射线衍射图,从图6-图8中可以看出,退火前后的单晶钼铌合金均仅在2θ为116.1
°
处出现峰值,代表222晶面的衍射,该结果表明尽管在1700℃下高温退火,单晶钼铌合金均保持单晶结构。
86.图9为本发明实施例8步骤一中制备的退火前单晶钼铌合金的金相图,图10为本发明实施例8步骤二中制备的力学性能提升的单晶钼铌合金的金相图,从图9和图10中可以看出,力学性能提升的单晶钼铌合金中的亚晶界数量与退火前单晶钼铌合金相比明显降低,意味着退火后单晶钼铌合金中的缺陷数量大幅度减少,性能提升。
87.图12为本发明实施例5~8制备的力学性能提升的单晶钼铌合金的室温拉伸性能测试结果,从图12中可以看出,对于mo
94
nb6而言退火后该单晶的强度上升,这种上升的趋势随着退火温度的提高而下降,最大值出现在1085℃~1115℃退火后,延伸率在1085℃~1115℃和1285℃~1315℃退火后呈现略微的下降,在1485℃~1515℃和1685℃~1715℃退火后,呈现显著的上升,通过综合对比mo
94
nb6单晶最优的退火温度为1285℃~1315℃。
88.以上所述,仅是本发明的较佳实施例,并非对本发明作任何限制。凡是根据发明技术实质对以上实施例所作的任何简单修改、变更以及等效变化,均仍属于本发明技术方案的保护范围内。