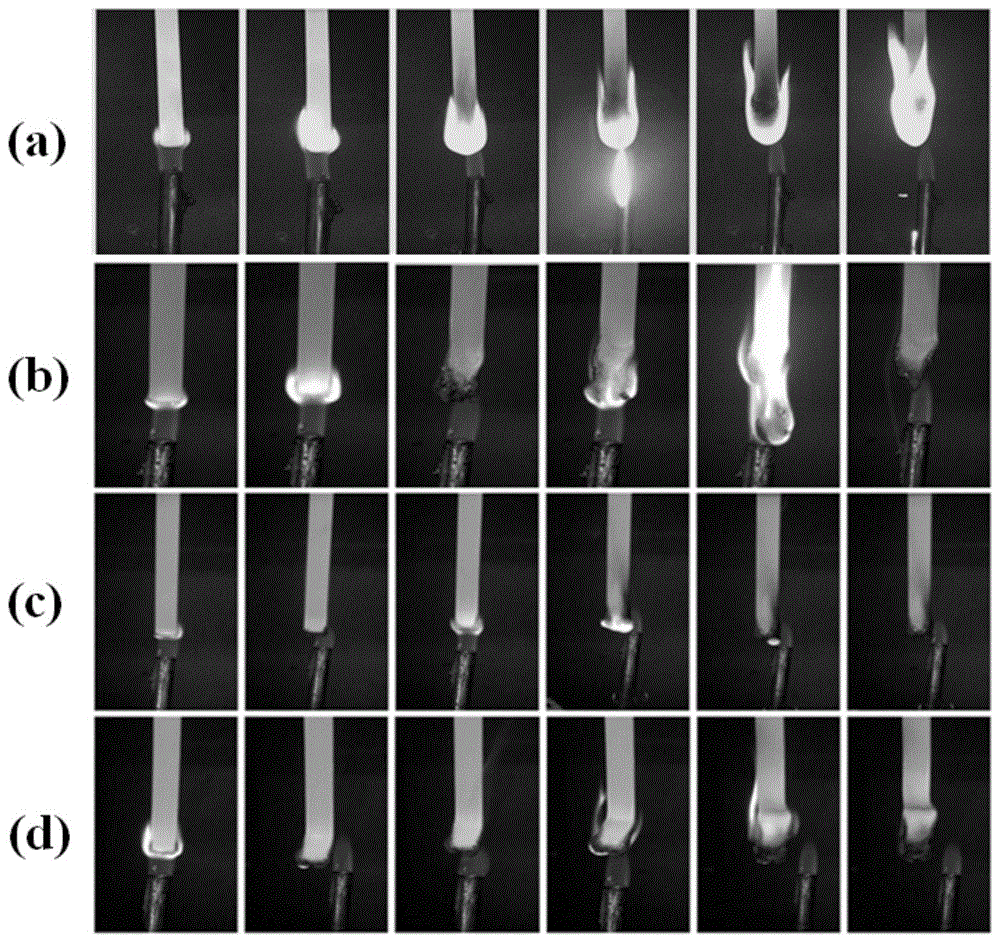
本发明属于无卤阻燃聚合物材料制备领域,具体涉及一种低聚倍半硅氧烷增容及协效无卤阻燃聚丙烯复合材料及其制备方法。
背景技术:
:作为世界第二大通用塑料,聚丙烯(PP)被广泛应用于国民经济各领域。但由于聚丙烯极限氧指数(LOI)低,仅17.4%,极易燃烧而引发火灾,燃烧时发热量大且易产生有焰熔滴,大大限制了其在电子、电器等领域的应用,因此针对聚丙烯材料的阻燃性能研究开发多见于现有技术中。阻燃剂是助剂的一种,添加后可有效的降低易燃聚合物燃烧性能,抑制火焰的传播。其中,膨胀型阻燃剂(IFR)是以磷、氮为主要成分的无卤阻燃剂,此类阻燃剂的优点是燃烧过程发烟量少,不易产生熔滴且无毒气释放。但传统膨胀型阻燃体系存在着许多问题,诸如阻燃剂添加量较卤系阻燃剂大,与聚合物基体相容性差,随添加量增加成品的力学性能下降。在膨胀型阻燃体系中,聚磷酸铵(APP)/季戊四醇(PER)/三聚氰胺(ME)是组成简单且研究较多的传统膨胀阻燃体系,但该体系存在以下问题:(1)在挤出加工过程中,体系中各组分很难混合均匀,难分散;(2)体系中强极性炭源季戊四醇和酸源聚磷酸铵存在与聚合物基体相容性较差,易迁移等问题,导致注塑时聚合物表面起霜严重;而且聚磷酸铵有一定的吸水性,在应用于聚丙烯材料时导致阻燃聚丙烯材料易吸潮的同时阻燃剂也容易从基体中溶出,从而影响到阻燃聚丙烯材料的耐候性以及阻燃耐久性。为了解决上述问题,本发明申请人的在先专利“无卤膨胀阻燃聚甲醛复合材料及其制备方法”(CN201010595733.6)提供了一种聚磷酸铵基复合膨胀型阻燃剂的制备方法,在APP/PER/ME传统体系基础上,采用高温热处理技术先进行ME与APP的高温反应,实现ME在APP大分子链上接枝,再将ME-APP接枝反应产物与PER进行高温反应,从而将传统的三元组分APP、ME和PER在很大程度上集成在一个大分子中,并将其用于阻燃聚甲醛(POM),解决了简单共混膨胀体系中各组分混合不均匀,难分散以及与基体聚甲醛相容性差的难题。但是在将该膨胀型阻燃剂RMAPP应用于非极性聚丙烯材料时,与聚丙烯基体相容性差,因此难以实现在聚合物基体中的均匀分散。同时,在应用于聚丙烯基体时单独使用该膨胀型阻燃剂RMAPP,其阻燃效率较低,阻燃剂添加量较大,导致成品的阻燃材料力学性能下降。为了提高膨胀型阻燃剂的阻燃效率,通常选用阻燃协效剂与阻燃剂共同使用,常用的协效剂包括金属氧化物、硅酸盐、碳纳米管、石墨烯等。但这些协效剂的加入在使材料阻燃性能提高的同时会使其力学性能进一步恶化。技术实现要素:本发明的目的在于克服上述的现有技术问题,提供一种低聚倍半硅氧烷增容及协效无卤阻燃聚丙烯复合材料及其制备方法,所制备的阻燃聚丙烯复合材料阻燃效率高,且对比同类阻燃聚丙烯复合材料力学性能大幅提高。为实现上述目的,本发明是采用由以下技术措施构成的技术方案来实现的:一种低聚倍半硅氧烷增容及协效无卤阻燃聚丙烯复合材料,按重量份数计,其原料组分包括:聚丙烯75~80份,单分子膨胀型阻燃剂RMAPP20~25份,低聚倍半硅氧烷0.5~5份。其中,所述单分子膨胀型阻燃剂RMAPP可选用参照本发明申请人在先专利“无卤膨胀阻燃聚甲醛复合材料及其制备方法”(CN201010595733.6)中关于聚磷酸铵基膨胀型阻燃剂的制备方法所制备得到的膨胀型阻燃剂。进一步地,为了提高所制得阻燃聚丙烯复合材料的成炭效果,所述单分子膨胀型阻燃剂RMAPP为通过下述制备方法得到:将聚磷酸铵、三聚氰胺、季戊四醇先干燥,然后按照聚磷酸铵、三聚氰胺质量比为(1.5~6):1的比例混合均匀后于250~260℃高温下反应3~4小时,反应时间到达后,得到反应后的粉体MAPP;将粉体MAPP与季戊四醇以质量比为7:(0.5~1.5)的比例混合均匀,然后于225~235℃高温下反应1.5~2.5小时后取出,即得单分子膨胀型阻燃剂RMAPP。通常地,为了方便反应制备,所述聚磷酸铵、三聚氰胺、季戊四醇通常选用粉体剂。其中,所述聚磷酸铵优选高聚合度Ⅱ型,聚合度n≥1000;三聚氰胺优选工业级,净含量≥98%;季戊四醇优选工业级,净含量≥98%。其中,所述干燥通常为在80~95℃下真空干燥10~12h。其中,所述低聚倍半硅氧烷(POSS)为聚乙烯基笼型倍半硅氧烷、聚甲基倍半硅氧烷、聚苯基倍半硅氧烷、聚三甲基硅烷基倍半硅氧烷、聚苯基丙基倍半硅氧烷和聚二甲基硅氧烷-苯基倍半硅氧烷共聚物中任一种或其组合物。优选地,所述低聚倍半硅氧烷为聚乙烯基笼型倍半硅氧烷;进一步优选地,所述聚乙烯基笼型倍半硅氧烷为八乙烯基笼型倍半硅氧烷。为了进一步地提高单分子膨胀型阻燃剂RMAPP与聚丙烯基体之间的相容性,所制得阻燃聚丙烯复合材料的垂直燃烧级别(UL-941.6mm)最低达到V-0,极限氧指数达到35%,并提高成品的力学性能,优选地,按重量份数计,所述原料组分包括:聚丙烯75~80份,单分子膨胀型阻燃剂RMAPP23~25份,低聚倍半硅氧烷0.8~2.2份;其中,单分子膨胀型阻燃剂RMAPP和低聚倍半硅氧烷的重量份数之和不低于25份。为了进一步地提高阻燃效率,所制得阻燃聚丙烯复合材料的垂直燃烧级别(UL-941.6mm)最低达到V-0,极限氧指数达到38%,并提高成品的力学性能,优选地,按重量份数计,所述原料组分包括:聚丙烯75份,单分子膨胀型阻燃剂RMAPP23.8~25份,低聚倍半硅氧烷1.2~2.2份。值得说明的是,在实际工业化生产中,还可选择在制备上述无卤阻燃聚丙烯复合材料过程中添加其它现有技术公知的抗氧剂、稳定剂等其它加工助剂。但前提是,这些加工助剂对本发明的目的实现以及对本发明优良效果的取得不得造成不利影响。一种低聚倍半硅氧烷增容及协效无卤阻燃聚丙烯复合材料的制备方法,其包括以下步骤:(1)按重量份数计,备料的原料组分包括:聚丙烯75~80份,单分子膨胀型阻燃剂RMAPP20~25份,低聚倍半硅氧烷0.5~5份;(2)将单分子膨胀型阻燃剂RMAPP与低聚倍半硅氧烷先干燥,然后进行混合,混合均匀后再加入聚丙烯继续混合,至各组分均匀混合,将所得混合物加入至双螺杆挤出机中于温度180~195℃挤出造粒,即得低聚倍半硅氧烷增容及协效无卤阻燃聚丙烯复合材料的料粒。其中,所述干燥通常为在80~95℃环境下干燥。其中,为了使得原料充分混合均匀,并提供一种优选制备方法,所述步骤(2)为:将单分子膨胀型阻燃剂RMAPP与低聚倍半硅氧烷先干燥,然后以25000~28000r/min的转速条件下进行混合,混合2~4分钟后再加入聚丙烯继续混合3~5分钟,混合时间到达后,将所得混合物加入至双螺杆挤出机中于温度180~195℃,螺杆转速100~120r/min条件下挤出造粒,即得低聚倍半硅氧烷增容及协效无卤阻燃聚丙烯复合材料的料粒。值得说明的是,在实际工业化生产中,还可选择在制备上述无卤阻燃聚丙烯复合材料过程中添加其它现有技术公知的抗氧剂、稳定剂等其它加工助剂。但前提是,这些加工助剂对本发明的目的实现以及对本发明优良效果的取得不得造成不利影响。通常地,在制备过程中这些加工助剂可选择与聚丙烯一同加入。本发明选用的低聚倍半硅氧烷对膨胀型阻燃剂同时具有增容和协效的作用。低聚倍半硅氧烷具有增容作用的原因主要包括以下两点:(1)POSS粒子为微纳米级尺寸,具有较大的比表面积,与单分子膨胀型阻燃剂RMAPP颗粒间有静电吸附作用;(2)POSS中Si-O-Si键的氧原子与RMAPP中-NH2基团的氢原子之间存在氢键相互作用。因此POSS粒子能够实现对RMAPP颗粒的包覆,使RMAPP更好地分散在PP基质,提高体系相容性,这也是将POSS作为协效剂使得其成品阻燃性和力学性能优于同类阻燃体系的原因。在优选的技术方案中,POSS选用聚乙烯基笼型倍半硅氧烷,因笼型聚倍半硅氧烷粒子的笼型骨架具有较大刚性,材料在拉伸过程中所承受的负载能够通过界面转移到POSS粒子上,减少因应力集中而造成的材料力学性能的下降。更进一步优选的技术方案中,POSS选用八乙烯基笼型倍半硅氧烷(OV-POSS),OV-POSS所带有的乙烯基团与聚丙烯分子链的相容性更好,进一步提高了增容作用效果。此外,低聚倍半硅氧烷具有的协效阻燃机理如下:RMAPP作为单分子膨胀型阻燃剂,主要在气相和凝聚相发挥阻燃作用,对于气相阻燃,RMAPP受热分解释放不燃气体,稀释可燃气体浓度,从而发挥阻燃作用;对于凝聚相阻燃,RMAPP在酸源部分(APP结构)的作用下,碳源部分(每个结构)通过脱水反应形成炭层,所形成的炭层在加热和燃烧过程中由气源部分(APP和MEL结构)产生的气体作用下膨胀,形成膨胀炭层,阻隔氧气和热量在降解区和燃烧区之间的传递,有效地保护底层的PP基体。而引入的POSS粒子主要在凝聚相发挥阻燃作用:一方面,POSS受热分解形成的SiO2颗粒会覆盖在炭层表面,与膨胀炭层相结合得到强度更高、致密度更好的复合炭层,有效阻隔氧气和热量在降解区与燃烧区之间的传递;另一方面,加入的POSS纳米颗粒在聚合物分解过程中参与聚丙烯大分子链的成炭反应,促进聚丙烯大分子链进入最终的炭层,从而使阻燃复合材料的残炭率及炭层质量大幅提升。综上所述,选用低聚倍半硅氧烷与单分子膨胀型阻燃剂RMAPP组合的聚丙烯基体阻燃复合材料具有优异的阻燃性能和大幅高于同类阻燃复合材料的力学性能。本发明优选技术方案中,所制得阻燃聚丙烯复合材料的极限氧指数达到38.7%,阻燃等级达到UL-V0级别,拉伸强度达到33.6MPa,冲击强度达到3.82kJ/m2。本发明技术方案具有以下有益效果:(1)本发明选用低聚倍半硅氧烷作为协效剂显著改善了膨胀型阻燃剂RMAPP与聚丙烯基体的相容性,在相同垂直燃烧UL-V0级别的条件下,本发明优选方案中,其原料膨胀型阻燃剂的用量相比不添加低聚倍半硅氧烷的同类产品膨胀型阻燃剂的用量减少达17%,拉伸强度提高达78%,冲击强度提高达65%。(2)本发明所得的阻燃复合材料,阻燃性能优异,其中优选方案中,所制得阻燃复合材料能够通过垂直燃烧测试UL-94V-0级别,极限氧指数达到38.7%,热释放速率峰值及热释放总量相比纯的聚丙烯材料分别降低了93%和71%。(3)本发明所选择的单分子膨胀型阻燃剂RMAPP集酸源、气源、碳源为一体,热稳定性高,用与聚合物改性时相容性好,不易吸水析出。(4)本发明所采用的原料无卤环保,且所提出的低聚倍半硅氧烷协效无卤阻燃聚丙烯材料的制备工艺简单,易于实施,成本较低,所制备的阻燃材料综合性能优良,应用前景广阔。附图说明图1为本发明实施例2、实施例5以及对比例2、对比例4所制得复合材料的垂直燃烧测试对比照片,(a)(b)(c)(d)皆为从左到右每间隔5s进行拍摄,其中(a)所使用的样品为对比例2所制得复合材料,(b)所使用的样品为对比例4所制得复合材料,(c)所使用的样品为实施例2所制得复合材料,(d)所使用的样品为实施例5所制得复合材料。图2为本发明实施例2及对比例2、对比例4所制得复合材料断裂表面的电镜对比照片,其中(a)(b)所使用的样品为对比例2所制得复合材料,(c)(d)所使用的样品为对比例4所制得复合材料,(e)(f)所使用的样品为实施例2所制得复合材料,可明显看出,(e)(f)中阻燃颗粒分散性最好,无明显聚团,孔洞较少且孔隙最小。图3为本发明实施例2中单分子膨胀型阻燃剂RMAPP与聚乙烯基笼型倍半硅氧烷混合后复合粉体表面的电镜照片,右边照片为左边照片白框处的进一步放大,明显看出,POSS纳米颗粒粘附并覆盖RMAPP表面。具体实施方式下面通过实施例并结合附图对本发明作进一步说明。值得指出的是,给出的实施例不能理解为对本发明保护范围的限制,该领域的技术人员根据本发明的内容对本发明作出的一些非本质的改进和调整仍应属于本发明保护范围。其中,所述聚磷酸铵选择高聚合度Ⅱ型,聚合度n≥1000,由上海阿拉丁生化科技股份有限公司购入;三聚氰胺选择工业级,净含量≥98%,由成都玉龙化工股份有限公司购入;季戊四醇选择工业级,净含量≥98%,由成都科隆试剂有限公司购入。其中,所述单分子膨胀型阻燃剂RMAPP为通过下述制备方法得到:将聚磷酸铵、三聚氰胺、季戊四醇在90℃下真空干燥12h,然后按照聚磷酸铵、三聚氰胺质量比为6:1的比例混合均匀后于260℃高温下反应4小时,反应时间到达后,得到反应后的粉体MAPP;将粉体MAPP与季戊四醇以质量比为6:1的比例混合均匀,然后于230℃高温下反应2小时后取出,即得单分子膨胀型阻燃剂RMAPP。测试条件如下:氧指数性能按GB/T2406.2-2009标准测试;垂直燃烧性能按GB/T2408-2008标准测试;拉伸性能按GB/T1040.2-2006标准测试;冲击性能按GB/T12670-2008标准测试。实施例1将单分子膨胀型阻燃剂RMAPP与聚乙烯基笼型倍半硅氧烷置于90℃烘箱中干燥半小时,取干燥后的膨胀型阻燃剂RMAPP121g,聚乙烯基笼型倍半硅氧烷4g置于转速26000r/min高混机中混合3分钟,再加入聚丙烯375g继续混合5分钟,混合时间到达后,将所得混合物加入至双螺杆挤出机中于温度190℃,螺杆转速120r/min条件下挤出,挤出物经造粒、干燥,得到低聚倍半硅氧烷增容及协效无卤阻燃聚丙烯复合材料的粒料。将上述料粒经注塑机注塑成标准测试样条,注塑温度为195℃。经检测,样品的垂直燃烧性能达到1.6mmUL94V-0级,极限氧指数(LOI)为35.7%,力学性能拉伸强度达到32.8MPa,简支梁缺口冲击强度达到3.66kJ/m2。实施例2将单分子膨胀型阻燃剂RMAPP与聚乙烯基笼型倍半硅氧烷置于90℃烘箱中干燥半小时,取干燥后的膨胀型阻燃剂RMAPP119g,聚乙烯基笼型倍半硅氧烷6g置于转速26000r/min高混机中混合3分钟,再加入聚丙烯375g继续混合5分钟,混合时间到达后,将所得混合物加入至双螺杆挤出机中于温度190℃,螺杆转速120r/min条件下挤出,挤出物经造粒、干燥,得到低聚倍半硅氧烷增容及协效无卤阻燃聚丙烯复合材料的粒料。将上述料粒经注塑机注塑成标准测试样条,注塑温度为195℃。经检测,样品的垂直燃烧性能达到1.6mmUL94V-0级,极限氧指数(LOI)为38.7%,力学性能拉伸强度达到33.6MPa,简支梁缺口冲击强度达到3.82kJ/m2。实施例3将单分子膨胀型阻燃剂RMAPP与聚乙烯基笼型倍半硅氧烷置于90℃烘箱中干燥半小时,取干燥后的膨胀型阻燃剂RMAPP114g,聚乙烯基笼型倍半硅氧烷11g置于转速26000r/min高混机中混合3分钟,再加入聚丙烯375g继续混合5分钟,混合时间到达后,将所得混合物加入至双螺杆挤出机中于温度190℃,螺杆转速120r/min条件下挤出,挤出物经造粒、干燥,得到低聚倍半硅氧烷增容及协效无卤阻燃聚丙烯复合材料的粒料。将上述料粒经注塑机注塑成标准测试样条,注塑温度为195℃。经检测,样品的垂直燃烧性能达到1.6mmUL94V-0级,极限氧指数(LOI)为37.9%,力学性能拉伸强度达到32.9MPa,简支梁缺口冲击强度达到3.28kJ/m2。实施例4将单分子膨胀型阻燃剂RMAPP与聚乙烯基笼型倍半硅氧烷置于90℃烘箱中干燥半小时,取干燥后的膨胀型阻燃剂RMAPP107.5g,聚乙烯基笼型倍半硅氧烷17.5g置于转速26000r/min高混机中混合3分钟,再加入聚丙烯375g继续混合5分钟,混合时间到达后,将所得混合物加入至双螺杆挤出机中于温度190℃,螺杆转速120r/min条件下挤出,挤出物经造粒、干燥,得到低聚倍半硅氧烷增容及协效无卤阻燃聚丙烯复合材料的粒料。将上述料粒经注塑机注塑成标准测试样条,注塑温度为195℃。经检测,样品的垂直燃烧性能达到1.6mmUL94V-1级,极限氧指数(LOI)为34.4%,力学性能拉伸强度达到30.9MPa,简支梁缺口冲击强度达到3.06kJ/m2。实施例5将单分子膨胀型阻燃剂RMAPP与聚乙烯基笼型倍半硅氧烷置于90℃烘箱中干燥半小时,取干燥后的膨胀型阻燃剂RMAPP102.5g,聚乙烯基笼型倍半硅氧烷22.5g置于转速26000r/min高混机中混合3分钟,再加入聚丙烯375g继续混合5分钟,混合时间到达后,将所得混合物加入至双螺杆挤出机中于温度190℃,螺杆转速120r/min条件下挤出,挤出物经造粒、干燥,得到低聚倍半硅氧烷增容及协效无卤阻燃聚丙烯复合材料的粒料。将上述料粒经注塑机注塑成标准测试样条,注塑温度为195℃。经检测,样品的垂直燃烧性能达到1.6mmUL94V-1级,极限氧指数(LOI)为32.2%,力学性能拉伸强度达到28.9MPa,简支梁缺口冲击强度达到2.83kJ/m2。将实施例1-5的原料配比和性能测试结果进行总结,如下表所示:表1实施例1-5的原料配比组成PP(wt%)RMAPP(wt%)POSS(wt%)实施例17524.20.8实施例27523.81.2实施例37522.82.2实施例47521.53.5实施例57520.54.5表2实施例1-5所得复合材料的性能测试结果实施例6将单分子膨胀型阻燃剂RMAPP与聚甲基倍半硅氧烷置于90℃烘箱中干燥半小时,取干燥后的膨胀型阻燃剂RMAPP100g,聚甲基倍半硅氧烷2g置于转速26000r/min高混机中混合2分钟,再加入聚丙烯300g继续混合3分钟,混合时间到达后,将所得混合物加入至双螺杆挤出机中于温度180℃,螺杆转速100r/min条件下挤出,挤出物经造粒、干燥,得到低聚倍半硅氧烷增容及协效无卤阻燃聚丙烯复合材料的粒料。将上述料粒经注塑机注塑成标准测试样条,注塑温度为195℃。经检测,样品的垂直燃烧性能达到1.6mmUL94V-0级,极限氧指数(LOI)为34.6%,力学性能拉伸强度达到29.2MPa,简支梁缺口冲击强度达到2.85kJ/m2。实施例7将单分子膨胀型阻燃剂RMAPP与聚苯基倍半硅氧烷置于90℃烘箱中干燥半小时,取干燥后的膨胀型阻燃剂RMAPP100g,聚苯基倍半硅氧烷20g置于转速28000r/min高混机中混合4分钟,再加入聚丙烯400g继续混合5分钟,混合时间到达后,将所得混合物加入至双螺杆挤出机中于温度195℃,螺杆转速120r/min条件下挤出,挤出物经造粒、干燥,得到低聚倍半硅氧烷增容及协效无卤阻燃聚丙烯复合材料的粒料。将上述料粒经注塑机注塑成标准测试样条,注塑温度为195℃。经检测,样品的垂直燃烧性能达到1.6mmUL94V-2级,极限氧指数(LOI)为28.9%,力学性能拉伸强度达到30.3MPa,简支梁缺口冲击强度达到2.98kJ/m2。实施例8将单分子膨胀型阻燃剂RMAPP与聚二甲基硅氧烷-苯基倍半硅氧烷共聚物置于90℃烘箱中干燥半小时,取干燥后的膨胀型阻燃剂RMAPP100g,聚二甲基硅氧烷-苯基倍半硅氧烷共聚物10g置于转速26000r/min高混机中混合3分钟,再加入聚丙烯320g继续混合4分钟,混合时间到达后,将所得混合物加入至双螺杆挤出机中于温度190℃,螺杆转速100r/min条件下挤出,挤出物经造粒、干燥,得到低聚倍半硅氧烷增容及协效无卤阻燃聚丙烯复合材料的粒料。将上述料粒经注塑机注塑成标准测试样条,注塑温度为195℃。经检测,样品的垂直燃烧性能达到1.6mmUL94V-1级,极限氧指数(LOI)为32.8%,力学性能拉伸强度达到29.5MPa,简支梁缺口冲击强度达到2.89kJ/m2。实施例9将单分子膨胀型阻燃剂RMAPP、聚乙烯基笼型倍半硅氧烷和聚甲基倍半硅氧烷置于90℃烘箱中干燥半小时,取干燥后的膨胀型阻燃剂RMAPP100g,聚乙烯基笼型倍半硅氧烷10g和聚甲基倍半硅氧烷10g置于转速26000r/min高混机中混合2分钟,再加入聚丙烯300g继续混合3分钟,混合时间到达后,将所得混合物加入至双螺杆挤出机中于温度180℃,螺杆转速100r/min条件下挤出,挤出物经造粒、干燥,得到低聚倍半硅氧烷增容及协效无卤阻燃聚丙烯复合材料的粒料。将上述料粒经注塑机注塑成标准测试样条,注塑温度为195℃。经检测,样品的垂直燃烧性能达到1.6mmUL94V-0级,极限氧指数(LOI)为35.6%,力学性能拉伸强度达到29.1MPa,简支梁缺口冲击强度达到2.89kJ/m2。实施例10将单分子膨胀型阻燃剂RMAPP、聚三甲基硅烷基倍半硅氧烷和聚苯基丙基倍半硅氧烷置于90℃烘箱中干燥半小时,取干燥后的膨胀型阻燃剂RMAPP100g,聚三甲基硅烷基倍半硅氧烷15g和聚苯基丙基倍半硅氧烷10g置于转速26000r/min高混机中混合2分钟,再加入聚丙烯375g继续混合3分钟,混合时间到达后,将所得混合物加入至双螺杆挤出机中于温度180℃,螺杆转速100r/min条件下挤出,挤出物经造粒、干燥,得到低聚倍半硅氧烷增容及协效无卤阻燃聚丙烯复合材料的粒料。将上述料粒经注塑机注塑成标准测试样条,注塑温度为195℃。经检测,样品的垂直燃烧性能达到1.6mmUL94V-2级,极限氧指数(LOI)为30.4%,力学性能拉伸强度达到27.2MPa,简支梁缺口冲击强度达到2.62kJ/m2。对比例1将聚丙烯500g置于转速26000r/min高混机中混合5分钟,混合时间到达后,将所得混合物加入至双螺杆挤出机中于温度190℃,螺杆转速120r/min条件下挤出,挤出物经造粒、干燥,得到聚丙烯材料的粒料。将上述料粒经注塑机注塑成标准测试样条,注塑温度为195℃。经检测,样品的垂直燃烧性能测试未满足评级,极限氧指数(LOI)为18%,力学性能拉伸强度达到34.9MPa,简支梁缺口冲击强度达到3.23kJ/m2。对比例2将聚磷酸铵(APP)/季戊四醇(PER)/三聚氰胺(ME)简单共混的膨胀型阻燃剂(按照现有技术制备)置于90℃烘箱中干燥半小时,取干燥后的膨胀型阻燃剂125g与聚丙烯375g置于转速26000r/min高混机中混合5分钟,混合时间到达后,将所得混合物加入至双螺杆挤出机中于温度190℃,螺杆转速120r/min条件下挤出,挤出物经造粒、干燥,得到膨胀阻燃聚丙烯复合材料的粒料。将上述料粒经注塑机注塑成标准测试样条,注塑温度为195℃。经检测,样品的垂直燃烧性能达到1.6mmUL94V-2级别,极限氧指数(LOI)为27.8%,力学性能拉伸强度达到24.7MPa,简支梁缺口冲击强度达到1.86kJ/m2。对比例3将聚磷酸铵(APP)/季戊四醇(PER)/三聚氰胺(ME)简单共混的膨胀型阻燃剂(按照现有技术制备)置于90℃烘箱中干燥半小时,取干燥后的膨胀型阻燃剂150g与聚丙烯350g置于转速26000r/min高混机中混合5分钟,混合时间到达后,将所得混合物加入至双螺杆挤出机中于温度190℃,螺杆转速120r/min条件下挤出,挤出物经造粒、干燥,得到膨胀阻燃聚丙烯复合材料的粒料。将上述料粒经注塑机注塑成标准测试样条,注塑温度为195℃。经检测,样品的垂直燃烧性能达到1.6mmUL94V-0级别,极限氧指数(LOI)为31.0%,力学性能拉伸强度达到20.4MPa,简支梁缺口冲击强度达到1.35kJ/m2。对比例4将单分子膨胀型阻燃剂RMAPP置于90℃烘箱中干燥半小时,取干燥后的膨胀型阻燃剂RMAPP125g与聚丙烯375g置于转速26000r/min高混机中混合5分钟,混合时间到达后,将所得混合物加入至双螺杆挤出机中于温度190℃,螺杆转速120r/min条件下挤出,挤出物经造粒、干燥,得到膨胀阻燃聚丙烯复合材料的粒料。将上述料粒经注塑机注塑成标准测试样条,注塑温度为195℃。经检测,样品的垂直燃烧性能达到1.6mmUL94V-2级别,极限氧指数(LOI)为30.9%,力学性能拉伸强度达到28.8MPa,简支梁缺口冲击强度达到2.43kJ/m2。将对比例1-4性能测试结果进行总结,如下表所示:表3对照例1-4所得复合材料的性能测试结果对比表2和表3,可明显看出,在相同垂直燃烧级别中,本发明实施例更少添加膨胀型阻燃剂且具有更好的力学性能。如说明书附图2所示,由于对比例2中阻燃剂分散不均匀、相容性差,因此(a)(b)中存在大量团聚的阻燃颗粒和孔洞(白色箭头指向的孔洞)。比较而言,对比例4所制得复合材料中阻燃颗粒分散性明显提高,但仍存在较大孔隙((d)中白色箭头指向的孔洞)。通过(e)(f)明显看出,实施例2所制得复合材料样品中阻燃颗粒的分散性和界面相容性显著提高。其原因是,POSS的存在有利于提高阻燃剂的分散性和相容性,使得阻燃颗粒能够更均匀地分散和嵌入在基体中,从而减少界面表面暴露的阻燃剂颗粒。分析认为,所使用的POSS中含有8个乙烯基,因此POSS与PP分子链有一定的相容性,在一定程度上提高了RMAPP/POSS在PP基体中的分散。如说明书附图3所示,POSS纳米颗粒将粘附并覆盖RMAPP表面,结果表明,POSS纳米粒子包覆RMAPP能够很好地分散于PP基体中,并与PP基体相容。当前第1页1 2 3