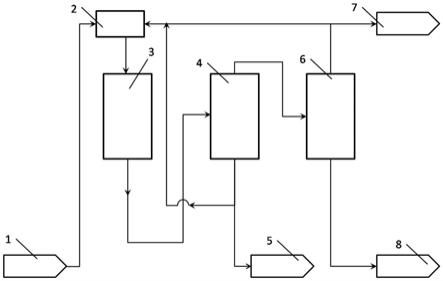
1.本发明涉及一种合成气直接制烯烃的工艺方法,属于化学化工技术领域。
背景技术:2.我国的能源特点是“富煤、缺油、少气”。石油消费对外依存度高,严重制约经济发展,煤、天然气以及生物质等清洁高效的利用一直是可持续发展的重要议题。从原理上讲,煤、天然气和生物质直接转化为化学品的工业化前景比较渺茫,因而选择合适的转化介质作为煤化工和天然气化工的平台实现化学品合成则显得尤为必要。近年来,随着煤气化技术、天然气重整技术、生物质气化技术的日趋成熟,合成气化学被认为是最切实可行的替代石油生产油料和大宗化学品的途径。
3.低碳烯烃,指的是c2-c4烯烃,是非常重要的化工原料。乙烯产量是衡量一个国家化学工业发展水平的标志。目前,我国乙烯、丙烯的生产所面临的突出问题是消费自给率较低、供求矛盾突出。传统工艺生产乙烯主要通过蒸汽裂解技术,该工艺完全依赖并大量消耗不可再生的石油资源。开发非石油路线的低碳烃合成技术,不仅可以对现有的生产技术进行补充,也也对未来新能源的利用提供借鉴。
4.目前,合成气制低碳烃技术的研究尚处于实验室研发阶段,主要集中在催化剂的研发上,工艺过程的研究相对匮乏。催化剂主要分为两种体系,一是采用费托合成催化剂为基础的改性催化剂,主要以铁、钴为活性中心的负载型催化剂,该类催化剂一般具有高的co转化率,烃类产物分布一般满足asf碳数分布规律,c2-c4烃类产物选择性难以突破60%。另一种思路则是采用双功能耦合催化剂的工艺方法。也就是将氧化物和分子筛耦合。science(2016)公布了zncrox与msapo分子筛相结合的催化剂实现了c2-c4烃类选择性达90%(不包括co2)以上。而德国应化(2016)也公布了一种采用znzr氧化物和sapo34相结合催化剂的工艺方法,其c2-c4烃类选择性也达到90%以上(不包括co2)。而德国应化(2016)也公布了一种采用znzr氧化物和sapo34相结合催化剂的工艺方法,其c2-c4烃类选择性也达到90%以上(不包括co2)。该工艺最大的特点就是co2选择性高,约占总产物的45%以上,大量的co2生成,也使反应体系的放热量急剧增加。如何降低反应体系中的co2生成,提高碳的利用率是亟待解决的问题。
技术实现要素:5.本发明的目的在于解决现有技术中co2选择性高,合成气中碳损失大的问题,提供了一种新的合成气制烯烃的工艺方法,该方法利用催化剂的co2加氢活性原位转化一部分co2,一方面增加合成气中的碳利用率,一方面通过co2选择性的降低减少放热量。
6.根据本发明的一个方面,提供了一种用于合成气直接制烯烃的工艺方法,包括:
7.使合成气原料与催化剂接触,反应得到含有机烃、二氧化碳和未反应的合成气的物流;
8.对所述含有机烃、二氧化碳和未反应的合成气的物流进行分离处理,依次分离出
其中的二氧化碳和未反应的合成气;
9.将分离出的二氧化碳和未反应的合成气循环回所述合成气原料中参与反应。
10.根据本发明的一些实施方式,在参与反应的气体中,以摩尔比计,h2/(co+co2)为(4:1)~(1:4),和/或co/co2为(1-10):1。
11.根据本发明的优选实施方式,在参与反应的气体中,以摩尔比计,h2/(co+co2)为(2:1)~(1:2),和/或co/co2为(2-5):1。
12.根据本发明的优选实施方式,所述催化剂包括氧化物和分子筛。
13.根据本发明的优选实施方式,所述氧化物和分子筛的重量比为(1:6)~(6:1);优选为(1:4)~(4:1)。
14.根据本发明的优选实施方式,所述氧化物为具有co和co2转化活性的氧化物,优选包括zn、cr、in、zr、al、ga的氧化物及其复合氧化物中的至少一种。
15.根据本发明的优选实施方式,所述分子筛选自alpo和sapo分子筛;优选包括alpo-18、alpo-17、alpo-34、alpo-14、alpo-11、alpo-5、sapo-18、sapo-17、sapo-11和sapo-5中的至少一种。
16.根据本发明的优选实施方式,所述反应温度为340-460℃;和/或反应压力0.5-8mpa;和/或体积空速为800-8000h-1
。
17.根据本发明的优选实施方式,对所述含有机烃、二氧化碳和未反应的合成气的物流依次进行脱碳处理和烃分离处理,依次分离出其中的二氧化碳和未反应的合成气。
18.根据本发明的优选实施方式,所述脱碳处理包括吸附脱碳处理、溶剂脱碳处理、膜脱碳处理中的至少一种。
19.根据本发明的优选实施方式,所述烃分离处理包括变压吸附处理、深冷分离处理、油吸收分离处理中的至少一种。
20.根据本发明的优选实施方式,所述合成气包括氢气和一氧化碳,氢气和一氧化碳的摩尔比为0.5-3。
21.根据本发明的优选实施方式,反应得到含有机烃、co2和未反应的合成气的物流先与新鲜的合成气换热后再进行脱碳处理,任选的,反应得到含有机烃、co2和未反应的合成气的气流先与新鲜的合成气换热,再与分离得到的二氧化碳再次换热。
22.根据本发明的另一个方面,提供了一种用于合成气直接制烯烃的装置,包括:
23.反应器,用于使合成气原料与催化剂接触发生反应得到含有机烃、二氧化碳和未反应的合成气的物流;
24.脱碳装置,其与所述反应器相连,用于接收来自于所述反应器的含有机烃、二氧化碳和未反应的合成气的物流,并分离其中的二氧化碳;
25.烃分离装置,其与所述脱碳装置相连,用于接收来自于所述脱碳装置的含有机烃和未反应的合成气的物流,并分离其中的未反应的合成气;
26.预混器,其与所述反应器相连,用于接收新鲜合成气、循环的二氧化碳和未反应的合成气,并将其混合输送至反应器。
27.根据本发明的优选实施方式,所述装置还包括:
28.第一换热器,其分别与所述反应器的出口和脱碳装置的入口相连。
29.所述第一换热器设置有物流入口、物流出口、合成气入口和合成气出口,其内部设
置有物流通道和合成气通道;其中物流入口和物流出口为物流通道的入口和出口;合成气入口和合成气出口为合成气通道的入口和出口。
30.根据本发明的优选实施方式,所述物流入口与反应器出口相连,物流出口与脱碳装置的入口相连。合成气入口与新鲜合成气存储装置相连,合成气出口与预混器相连。
31.根据本发明的优选实施方式,所述装置还包括:
32.第二换热器,其分别与所述第一换热器的出口和脱碳装置的入口相连。
33.所述第二换热器设置有物流入口、物流出口、二氧化碳入口和二氧化碳出口,其内部设置有物流通道和二氧化碳通道;其中物流入口和物流出口为物流通道的入口和出口;二氧化碳入口和二氧化碳出口为二氧化碳通道的入口和出口。
34.根据本发明的优选实施方式,所述物流入口与第一换热器的物流出口相连,物流出口与脱碳装置的入口相连。二氧化碳入口与脱碳装置的气体出口相连,二氧化碳出口与预混器相连。
35.根据本发明的优选实施方式,所述反应器为固定床反应器,优选为列管式固定床反应器。
36.根据本发明的优选实施方式,所述脱碳装置选自吸附脱碳装置、溶剂吸收脱碳装置、膜分离脱碳装置中的至少一种。
37.根据本发明的优选实施方式,所述烃分离装置选自变压吸附装置、深冷分离装置、油吸收分离装置中的至少一种。
38.本发明中,co2选择性是指反应生成的co2量除以co转化的量的摩尔百分比。
39.有机烃选择性是指所有有机烃产物的含碳数除以co转化的量的摩尔百分比。
40.c2-c4烯烃选择性是指c2-c4烯烃产物的含碳数占所有有机烃产物的含碳数的摩尔百分比。
41.相比于现有的采用的固定床转化合成气制烯烃的工艺方案,本技术提供了一种co2循环工艺方案,利用催化剂原位转化一部分的co2,可以在保证低碳烃的高选择性的同时,大幅降低co2的选择性,提高合成气中的碳利用率,同时降低放热量,适用于工业生产。
附图说明
42.图1表示根据本发明一个实施例的合成气直接制烯烃的装置和工艺流程示意图;
43.图2表示根据本发明另一个实施例的合成气直接制烯烃的装置和工艺流程示意图。
44.附图标记说明:1为新鲜合成气进口;2为预混器;3为列管式固定床反应器;4为脱碳装置;5为co2排放口;6为烃分离装置;7为驰放口;8;有机烃类产物出口;9为第一换热器;10为第二换热器。
具体实施方式
45.下面通过实施例对本发明作进一步的阐述,但不仅限于本实施例。
46.图1示出了本发明一个实施例的合成气直接制烯烃的装置,包括预混器2、反应器3、脱碳装置4和烃分离装置6。使用本装置的合成气直接制烯烃的工艺流程如下:新鲜合成气1经过预混器预热后,然后进入反应器3与催化剂接触反应,生成含有机烃、二氧化碳和未
反应的合成气的物流;该物流进入脱碳装置4,脱除其中的二氧化碳,得到含有机烃和未反应的合成气的物流,二氧化碳一部分经由二氧化碳排放口5排出,另一部分循环回预混器2与新鲜的合成气混合;含有机烃和未反应的合成气的物流进入烃分离装置6,分离得到有机烃和未反应的合成气,其中有机烃经有机烃类产物出口排出,未反应的合成气大部分循环回预混器2与新鲜的合成气混合,小部分经驰放口7排出。
47.图2示出了本发明一个实施例的合成气直接制烯烃的装置,包括预混器2、反应器3、脱碳装置4、烃分离装置6、第一换热器9和第二换热器10。使用本装置的合成气直接制烯烃的工艺流程如下:新鲜合成气1经过第一换热器9和预混器预热后,然后进入反应器3与催化剂接触反应,生成含有机烃、二氧化碳和未反应的合成气的物流;该物流进入第一换热器9,与新鲜合成气换热后,然后进入第二换热装置10,与脱碳装置分离出的二氧化碳换热,进入脱碳装置4,脱除其中的二氧化碳,得到含有机烃和未反应的合成气的物流,二氧化碳一部分经由二氧化碳排放口5排出,另一部分进入第二换热器10,与含有机烃、二氧化碳和未反应的合成气的物流换热,然后循环回预混器2与新鲜的合成气混合;含有机烃和未反应的合成气的物流进入烃分离装置6,分离得到有机烃和未反应的合成气,其中有机烃经有机烃类产物出口排出,未反应的合成气大部分循环回预混器2与新鲜的合成气混合,小部分经驰放口7排出。
48.【实施例1】
49.采用如图1的工艺流程,固定床中催化剂装填采用氧化物和分子筛1:1装填,氧化物中zncr氧化物占90%,inzr氧化物占10%;分子筛为sapo-34分子筛,在400℃,4.0mpa,4800h-1
的条件下,控制h2:co:co2=4:4:1,反应20小时,反应产物采用气相色谱在线监测,反应结果见表1。
50.【实施例2】
51.采用同实施例1的工艺流程及催化剂装填;在400℃,4.0mpa,4800h-1
的条件下,控制h2:co:co2=8:4:1,反应20小时,反应产物采用气相色谱在线监测,反应结果见表1。
52.【实施例3】
53.采用同实施例1的工艺流程,固定床中催化剂装填采用氧化物和分子筛1:1装填,氧化物中zncr氧化物占90%,inzr氧化物占10%;分子筛为sapo-34分子筛,在400℃,4.0mpa,4800h-1
的条件下,控制h2:co:co2=4:4:0.5,反应20小时,反应产物采用气相色谱在线监测,反应结果见表1。
54.【实施例4】
55.采用同实施例1的工艺流程,固定床中催化剂装填采用氧化物和分子筛1:1装填,氧化物为zncr氧化物;分子筛为sapo-34分子筛,在400℃,4.0mpa,4800h-1
的条件下,控制h2:co:co2=4:4:1,反应20小时,反应产物采用气相色谱在线监测,反应结果见表1。
56.【实施例5】
57.采用如图2的工艺流程,固定床中催化剂装填采用氧化物和分子筛1:1装填,氧化物中zncr氧化物占90%,inzr氧化物占10%;分子筛为sapo-18分子筛,在400℃,4.0mpa,4800h-1
的条件下,控制h2:co:co2=4:4:1,反应20小时,反应产物采用气相色谱在线监测,反应结果见表1。
58.【实施例6】
59.采用如图2的工艺流程,固定床中催化剂装填采用氧化物和分子筛1:1装填,氧化物中zncr氧化物占90%,inzr氧化物占10%;分子筛为sapo-18分子筛,在400℃,5.0mpa,6000h-1
的条件下,控制h2:co:co2=4:4:1,反应20小时,反应产物采用气相色谱在线监测,反应结果见表1。
60.【对比例1】
61.采用固定床直接反应模式(不循环二氧化碳),催化剂装填与实施例1相同;在400℃,4.0mpa,4800h-1
的条件下,控制h2:co:n2=4:4:1,反应20小时,反应产物采用气相色谱在线监测,反应结果见表1。
62.【对比例2】
63.采用固定床直接反应模式(不循环二氧化碳),催化剂装填与实施例4相同;在400℃,4.0mpa,4800h-1
的条件下,控制h2:co:n2=4:4:1,反应20小时,反应产物采用气相色谱在线监测,反应结果见表1。
64.【对比例3】
65.采用固定床直接反应模式(不循环二氧化碳),催化剂装填与实施例5相同;在400℃,4.0mpa,4800h-1
的条件下,控制h2:co:n2=4:4:1,反应20小时,反应产物采用气相色谱在线监测,反应结果见表1。
66.【对比例4】
67.采用固定床直接反应模式(不循环二氧化碳),催化剂装填与实施例6相同;在400℃,5.0mpa,6000h-1
的条件下,控制h2:co:n2=4:4:1,反应20小时,反应产物采用气相色谱在线监测,反应结果见表1。
[0068][0069]
[0070]
在本发明中的提到的任何数值,如果在任何最低值和任何最高值之间只是有两个单位的间隔,则包括从最低值到最高值的每次增加一个单位的所有值。例如,如果声明一种组分的量,或诸如温度、压力、时间等工艺变量的值为50-90,在本说明书中它的意思是具体列举了51-89、52-88
……
以及69-71以及70-71等数值。对于非整数的值,可以适当考虑以0.1、0.01、0.001或0.0001为一单位。这仅是一些特殊指明的例子。在本申请中,以相似方式,所列举的最低值和最高值之间的数值的所有可能组合都被认为已经公开。
[0071]
应当注意的是,以上所述的实施例仅用于解释本发明,并不构成对本发明的任何限制。通过参照典型实施例对本发明进行了描述,但应当理解为其中所用的词语为描述性和解释性词汇,而不是限定性词汇。可以按规定在本发明权利要求的范围内对本发明作出修改,以及在不背离本发明的范围和精神内对本发明进行修订。尽管其中描述的本发明涉及特定的方法、材料和实施例,但是并不意味着本发明限于其中公开的特定例,相反,本发明可扩展至其他所有具有相同功能的方法和应用。