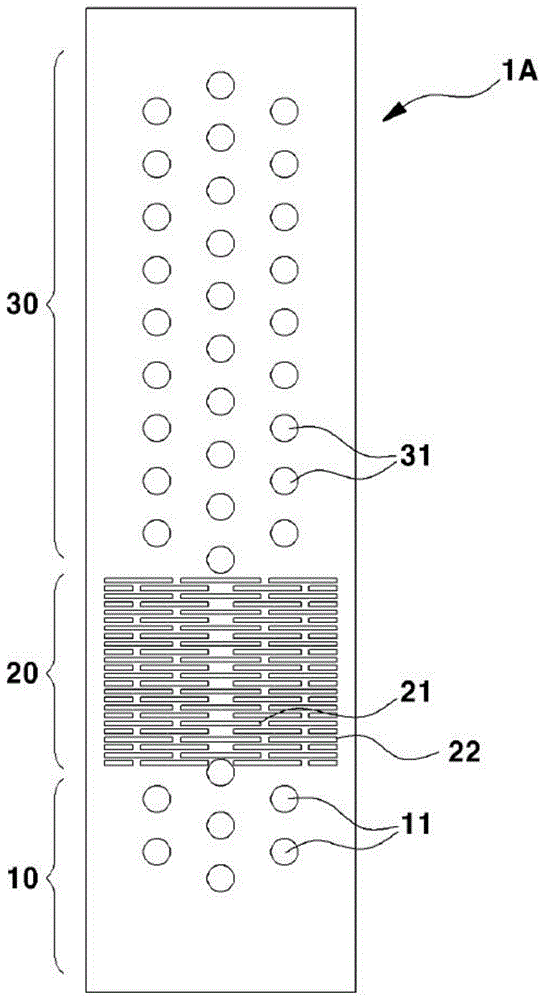
本发明涉及夹板及其成型方法,更详细地涉及可弯曲的夹板及其成型方法。
背景技术:
:通常,夹板用于保护,骨折或骨裂时以及韧带拉伸及破裂时,为了支撑并固定受伤的关节和肌肉组织,通过部分或完全紧密包裹受伤的关节和肌肉组织来防止移动。以往,广泛使用了在患处缠绕并固定涂有石膏的绷带的方法,但是这种施用方法因在石膏硬化过程中发生收缩现象而不能有效地支撑患处,由于不透气,长时间使用可能引起瘙痒,并且在完成患处治疗后必须使用额外的切割器将其除去,因此在切割过程中可能会导致皮肤损伤。为了解决利用上述石膏绷带的夹板的问题,最近,使用浸渍有可固化树脂的弹性纤维,例如,聚酯纤维编织物、玻璃纤维编织物或无纺布等湿固化聚氨酯。浸渍有弹性纤维的固化树脂广泛使用在使用时通过剥离包装纸来使内部的弹性纤维在室温下快速进行自然固化的成型性得以改善的夹板。如上所述的夹板主要是因为在施用时具有优异的成型性或固化性而被使用,但是在治疗完成后使用高速旋转的切割器以从弹性纤维的表面去除夹板。若利用这种高速旋转的切割器来切割固化的弹性纤维,则在切割弹性纤维的过程中产生灰尘,或者通过高速旋转的切割器切割弹性纤维的过程中产生高温,导致烫伤皮肤或一同伤害弹性纤维和皮肤等严重问题。最近,为了解决如上所述的问题,在夹板的一侧沿长度方向单独设置厚度比现有夹板的厚度薄的切开部,并在施用治疗后去除时,使用剪刀或刀来切割去除的方法。但是,在此情况下,虽然根本目的是轻松切割薄的部分,但是由于在整体上均匀地涂敷或覆盖有固化树脂,因此切割不容易,需要用剪刀或刀等切割工具来进行切割,在此情况下,不仅需要很大的力量而且切割也不容易,由此可大大降低施用效率性。并且,在完成治疗后从患处移除夹板的过程中可能引起许多问题,如皮肤损伤等。并且,现有的夹板是使用模具注塑成型的,根据施用夹板的施用人员的身体部位来分别准备各个模具,根据胳膊、腿等施用部位需要各种模具,因此存在基于夹板的成型模具成本增加的问题。并且,通常,合成塑料由于其优异的物性、低廉的价格、轻质特性而在世界各地用于各种用途,作为现代人生活中必不可少的材料,但是合成塑料存在不易分解的问题,其不仅是优点而且也是缺点,因此环境污染问题日益严重。这种合成塑料存在在废弃处理时噪声严重的环境污染问题。为此,尝试用在天然状态下降解的生物降解性树脂代替的技术。生物降解性树脂被土壤中的微生物降解,例如,可列举聚乳酸(polylacticacid,pla)、聚乙醇酸(polyglycolicacid,pga)、聚己内酯(polycaprolactone,pcl)、脂肪族聚酯树脂、聚羟基丁酸(polyhydroxybutyricacid,phba)及d-3-羟基丁酸(d-3-hydroxybutyricacid,hba)等。然而,生物降解性树脂,即,如上所述的聚乳酸、聚乙醇酸、聚己内酯、脂肪族聚酯树脂、聚羟基丁酸及d-3-羟基丁酸等生物降解性树脂的物性低,如尺寸稳定性、抗拉强度及硬度。为了加强这些物性,在生物降解性树脂片材上贴合额外的增强片材,或者尝试在压缩成型片材时,在生物降解性树脂中添加其他普通树脂或无机填料(filler)等来制备的方法。但是,为了将利用以往生物降解性树脂的片材成型成所需的形状,由于需要在高温下加工而可加工性下降,在利用以往生物降解性树脂的片材的情况下,存在不满足生物体接触和食品接触标准的问题。技术实现要素:技术问题本发明所要解决的技术问题在于,提供一种根据夹板的施用部位可自由成型夹板的形状、大小及弯曲程度等的可弯曲的夹板。本发明所要解决的技术问题在于,提供一种使用环境友好的制备方法和产品可用性得以提高的生物降解性复合树脂组合物。并且,本发明所要解决的技术问题在于,提供一种对生物体接触无害且由于生物降解性得以提高而可用于资源的循环的生物降解性复合树脂制备方法及由此制备的片材制备方法。解决问题的方案用于解决上述技术问题的本发明的一实施例的可弯曲的夹板的特征在于,包括:下部夹板部,以规定间距形成有多个第一通气孔;伸张夹板部,以规定间距形成有多个伸张孔;以及上部夹板部,以规定间距形成有多个第二通气孔,通过第一次弯曲将上述下部夹板部、伸张夹板部及上述上部夹板部弯曲成弧形,上述伸张夹板部通过多个伸张孔以不同角度对上述下部夹板部和上述上部夹板部进行第二次弯曲。可弯曲的夹板的特征在于,上述伸张夹板部形成有以规定间距配置的多个伸张孔,以便通过第二次弯曲使上述下部夹板部和上述上部夹板部的弯曲顺利地进行。在一实施例中,可弯曲的夹板的特征在于,包括:第一伸张孔,以规定长度形成于上述伸张夹板部的中间,并通过第二次弯曲以上下隔开的方式伸张;以及第二伸张孔,以规定长度形成于上述第一伸张孔的两侧,并通过第二次弯曲以上下隔开的方式伸张。并且,本发明一实施例的可弯曲的夹板的特征在于,包括:下部夹板部,以规定间隔形成有多个第一通气孔、第二通气孔及第三通气孔;上部夹板部,延伸形成于上述下部夹板部的上部一侧;以及伸张夹板部,延伸形成于上述上部夹板部的一侧,并以规定间隔形成有多个伸张孔,通过第一次弯曲将上述下部夹板部及上述上部夹板部弯曲成弧形,上述伸张夹板部通过多个伸张孔进行第二次弯曲以具有规定直径。并且,可弯曲的夹板的成型方法的特征在于,包括:将夹板部件根据夹板的施用部位切割成规定形状的步骤;为了在弯曲上述夹板部件时使上述夹板部件顺利地变形及伸张而在伸张夹板部冲孔多个伸张孔的步骤;为了使空气通向外部而根据上述夹板部件的施用部位冲孔多个通气孔的步骤;第一弯曲步骤,为了包围上述夹板部件的施用部位的外部面,以规定的弧形对上述夹板部件进行曲面弯曲;以及第二弯曲步骤,以使形成有上述伸张孔的上述伸张夹板部具有不同角度或规定直径的方式进行曲面弯曲。用于解决上述再一技术问题的本发明一实施例的低温可加工性得以提高的生物降解性复合树脂组合物,通过混合聚乳酸、聚己内酯、聚丁二酸丁二醇酯(pbs)、聚己二酸/对苯二甲酸丁二酯(pbat)、聚乙酸乙烯酯(pvac)、交联剂、增容剂来形成。在一实施例中,上述低温可加工性得以提高的生物降解性复合树脂组合物可通过挤出机熔融挤出28~72重量百分比的聚乳酸、5~20重量百分比的聚己内酯、5~10重量百分比的聚丁二酸丁二醇酯、5~15重量百分比的聚己二酸/对苯二甲酸丁二酯、10~20重量百分比的聚乙酸乙烯酯、2~4重量百分比的交联剂、1~3重量百分比的增容剂。上述聚乳酸可以通过将左旋聚乳酸(plla)和作为异构体的右旋聚乳酸(plda)立体络合而成,上述聚乳酸可以是包含左旋聚乳酸、右旋聚乳酸及外消旋聚乳酸的均聚物,或者聚乳酸可以是包含左旋聚乳酸、右旋聚乳酸及外消旋聚乳酸的共聚物。在一实施例中,在上述聚乳酸为包含上述左旋聚乳酸、右旋聚乳酸及外消旋聚乳酸的共聚物的情况下,可立体络合5~10重量百分比地上述右旋聚乳酸。并且,上述聚乙酸乙烯酯可选自由用交联剂接枝的聚乙烯醇(pvoh)及它们的衍生物或混合物组成的组中。在一实施例中,上述聚丁二酸丁二醇酯可用聚丁二酸己二酸丁二醇酯(pbsa)来代替,上述增容剂可以是马来酸酐(mah)。用于解决上述另一技术问题的本发明的一实施例的生物降解性复合树脂制备方法包括:步骤s110,粉末加工28~72重量百分比的聚乳酸、5~20重量百分比的聚己内酯、5~10重量百分比的聚丁二酸丁二醇酯、5~15重量百分比的聚己二酸/对苯二甲酸丁二酯、10~20重量百分比的聚乙酸乙烯酯、2~4重量百分比的交联剂、1~3重量百分比的增容剂;步骤s120,利用双刀片带式搅拌机对加工成上述粉末状态的上述原料进行混合;步骤s130,利用配备有原料供给装置的双螺杆挤出机熔融挤出经混合的上述原料;步骤s140,将经熔融挤出的上述原料投入模具(die)后,冷却并干燥通过模具出来的线材;以及步骤s150,通过切割机将经冷却的线材造粒后进行包装。在一实施例中,上述线材的规格为密度为1.25±0.05(g/cm2)、抗拉强度为50(mpa)、拉伸活动率为3.5~6(gpa)、软化温度为60~70℃、收缩率小于0.5%及水分含量为200ppm以下。在冷却并干燥经熔融挤出的上述线材的步骤s140中,可通过气冷系统来冷却经加工的线材。根据本发明一实施例的利用低温可加工性得以提高的生物降解性复合树脂的片材制备方法包括:步骤s210,粉末加工28~72重量百分比的聚乳酸、5~20重量百分比的聚己内酯、5~10重量百分比的聚丁二酸丁二醇酯、5~15重量百分比的聚己二酸/对苯二甲酸丁二酯、10~20重量百分比的聚乙酸乙烯酯、2~4重量百分比的交联剂、1~3重量百分比的增容剂;步骤s220,利用双刀片带式搅拌机对加工成粉末状态的上述原料进行混合;步骤s230,利用配备有原料供给装置的双螺杆挤出机熔融挤出经混合的上述原料;步骤s240将经熔融挤出的上述原料投入模具后,冷却并干燥通过模具出来的线材;步骤s250,利用片材制备用t型模具挤出机熔融挤出经冷却并干燥的上述线材;步骤s260,压延通过上述t型模具(t-die)挤出机熔融挤出的复合树脂来调节厚度并通过第一次冷却来制备片材;步骤s270,对以上述厚度被调节的状态进行第一次冷却的片材进行第二次冷却;以及步骤s280,按规格切割经第二次冷却的上述片材并进行包装。在一实施例中,在通过压延来调节厚度并进行第一次冷却的步骤s260中,可适用包括冷却辊的三轴辊。发明的效果在本发明的一实施例中,可提供如下的可弯曲的夹板,即,可根据夹板的施用或佩戴部位成型夹板,并可根据使用夹板的身体部位如腿或胳膊等自由成型夹板部件,在弯曲夹板部件时对应于夹板部件的变形的伸张夹板部形成伸张孔,不仅便于基于弯曲的变形,而且可防止夹板部件的损伤或破损。并且,在本发明的一实施例中,可提供如下的可弯曲的夹板的成型方法,即,可通过第一次弯曲及第二次弯曲将夹板部件自由成型成所需的形状及大小,不需要夹板的成型中所需的模具,可大大节俭由模具造成的制备费用,根据伸张夹板部的伸张孔的间距、大小及长度,可通过调节夹板的强度来成型。在本发明的另一实施例中,可通过如下的低温可加工性得以提高的生物降解性复合树脂组合物及其制备方法,即,制备成规定形状的产品可在60~70℃的低温状态下容易地进行后加工,不仅提高使用便利性,而且可制备符合生物体接触无害、食品接触标准的片材。并且,利用上述制备方法,可提供一种通过满足生物降解性条件来可进行资源循环使用的生物降解性复合片材。附图说明图1为示出本发明一实施例的可弯曲的夹板;图2为从一侧示出本发明一实施例的可弯曲的夹板的立体图;图3为从另一侧示出本发明一实施例的可弯曲的夹板的立体图;图4为示出本发明另一实施例的可弯曲的夹板;图5为示出本发明另一实施例的可弯曲的夹板的立体图;图6为示出本发明一实施例的可弯曲的夹板的成型方法的流程图;图7为示出本发明一实施例的低温可加工性得以提高的生物降解性复合树脂制备方法的流程图;图8为示出利用本发明一实施例的低温可加工性得以提高的生物降解性复合树脂片材制备方法的流程图。具体实施方式以下,参照附图详细说明本发明优选的实施例。本发明的实施例是为了向本领域技术人员更完整地说明本发明而提供的,可将下述实施例修改成各种形态,而本发明的范围并不限定于此。反而,这些实施例使本公开更加充实和完整,并且将本发明的范围完整地传达给本领域技术人员而提供的。在附图中,相同的附图标记是指相同的要素。并且,如本说明书中所使用,术语“和/或”包括所列项目中的一个或一个以上的所有组合。使用于本说明书中的术语用于说明实施例,并非限定本发明的范围。并且,在本说明书中,尽管以单数形式描述,但除非上下文清楚地表示单数,否则单数形式包括复数形式。并且,在本说明书中所使用的术语“包含(comprise)”和/或“包括(comprising)”用于特定所提及的形状、数字、步骤、动作、部件、要素和/或它们的组合的存在,而并非排除其他形状、数字、步骤、动作、部件、要素和/或它们的组合的存在或添加。在本说明书中提及的形成于基板或另一层“上(on)”的层是指形成于上述基板或另一层正上方的层,或者也可以是指形成于中间层或多个中间层上的层,上述中间层或多个中间层上的层形成于上述基板或另一层上。并且,对于本
技术领域:
的普通技术人员而言,与其他形状“相邻(adjacent)”配置的结构或形状与上述相邻的形状重叠,或者还可具有配置于下部的部分。在本说明书中,如图所示,“下(below)”、“上(above)”、“上部的(upper)”、“下部的(lower)”、“水平的(horizontal)”或“垂直的(vertical)”等相对术语可用于描述一结构部件、层或区域与另一结构部件、层或领域的关系。应该理解,这些术语不仅包括图中所示的方向还包括元件的其他方向。下面,参照简要示出本发明的理想实施例(和多个中间结构)的剖面图来对本发明的实施例进行说明。在这些附图中,例如,为了说明的便利性和明确性,可夸大多个部件的大小和形状,在实际实现中,可以预期所图示的形状的多个变形。因此,本发明的实施例不应被解释为于本文所示区域的任何特定形状。并且,附图的多个部件的附图标记在整个附图中是指相同的部件。图1为示出本发明一实施例的可弯曲的夹板成型之前的形态。成型之前的夹板1a可通过根据施用部位将夹板部件切割成规定形状及大小来获得。夹板部件由具有规定厚度的合成树脂形成,夹板部件根据夹板的施用部位可呈多种形状。作为本发明的一实施例,夹板1a是佩戴在腿的夹板,可包括支撑脚的下部夹板部10、用于包围脚后跟的伸张夹板部20及紧贴在小腿的上部夹板部30。成型之前的夹板1a由具有规定长度和宽度的合成树脂板的夹板部件形成。下部夹板部10具有规定宽度和长度以用于支撑脚,伸张夹板部20从上述下部夹板部10延伸成一体,以使当弯曲夹板时使其顺利进行,上部夹板部30可具有与上述下部夹板部10相同的宽度。上述下部夹板部10可包括多个第一通气孔11,当佩戴或施用夹板时使空气从外部通向内侧。具有多个一通气孔11,第一通气孔11根据需要可形成为具有规定间隔及互不相同的直径的孔。第一通气孔11可呈各种形状,例如圆形、三角形、四边形、椭圆形、星形、心形等。下部夹板部10的上侧可形成有伸张夹板部20,当进行第二次弯曲时使其顺利进行。伸张夹板部20可形成有以规定间距配置的多个伸张孔21、22,通过第二次弯曲使上述下部夹板部10和上述上部夹板部30的弯曲顺利进行。伸张夹板部20可包括以规定长度形成于伸张夹板部20的中间并通过第二次弯曲以上下隔开的方式伸张的第一伸张孔21,以及以规定长度形成于第一伸张孔21的两侧并通过第二次弯曲以上下隔开的方式伸张的第二伸张孔22。有关伸张夹板部20,当以不同角度弯曲下部夹板部10和上部夹板部30时,伸张夹板部20被伸张并自由变形,并根据夹板的形状及大小成型成所需的形状。伸张夹板部20中形成有以规定宽度形成的第一伸张孔21和以与第一伸张孔21相同的宽度和长度分别形成于上述第一伸张孔21的两侧的第二伸张孔22。第一伸张孔21及第二伸张孔22沿着夹板1a的宽度反向形成,第一伸张孔21和第二伸张孔22以规定高度间隔形成多个。上部夹板部30在伸张夹板部20的上侧形成一体。在上部夹板部30以规定间隔可形成有多个第二通气孔31,使得空气通向外部。第二通气孔31可呈各种形状,例如圆形、三角形、四边形、椭圆形、星形、心形等。图2为在一侧示出本发明一实施例的可弯曲的夹板的成型后的形态的立体图,图3为在另一侧示出本发明一实施例的可弯曲的夹板的成型后的形态的立体图。在图2及图3中示出的成型后的夹板1a是根据作为施用部位的腿形成型的。参照图2及图3,成型后的夹板1a可包括形成有第一通气孔11的下部夹板部10、从下部夹板部10延伸形成的伸张夹板部20及以与下部夹板部10不同的角度形成的上部夹板部30。针对于下部夹板部10、伸张夹板部20、上部夹板部30、第一通气孔11、第一伸张孔21、第二伸张孔22、第二通气孔31,可参照对图1中的该结构的说明。可弯曲的夹板1a可根据施用夹板的部位以适当的大小和形状切割夹板部件后,对切割的夹板部件按规定的圆弧或直径进行第一次弯曲后,根据施用部位可对夹板部件进行第二次弯曲。由此,根据夹板1a的施用部位将夹板1a成型成适当的形状及大小,以对佩戴人员的身体部位合适的大小及形状形成,并可容易地佩戴夹板,而没有因佩戴夹板而产生压力感或紧绷感。图4为示出本发明一实施例的可弯曲的夹板成型之前的形态,图5为示出本发明一实施例的可弯曲的夹板成型后的形态的立体图。作为本发明一实施例,夹板1b表示佩戴或施用于胳膊的夹板,图4中示出的夹板1b表示施用于胳膊之前的成型之前的夹板,图5中示出的夹板1b示出将图4中示出的夹板部件成型成可施用于胳膊的夹板。在一实施例中,夹板1b包括以固定间距形成有多个第一通气孔11、第二通气孔12及第三通气孔13的下部夹板部10、从下部夹板部10的上部一侧延伸形成的上部夹板部30、从上部夹板部30的一侧延伸形成并以规定间距形成有多个伸张孔的伸张夹板部20,下部夹板部10及上部夹板部30通过第一次弯曲被弯曲成弧形,伸张夹板部20可通过多个伸张孔进行第二次弯曲以具有规定直径。参照图4,成型之前的夹板1b的下部夹板部10和上部夹板部30形成一体,在上部夹板部30的一侧可一体形成有伸张夹板部20。并且,下部夹板部10和上部夹板部30形成一体,伸张夹板部20可延伸形成于上部夹板部30的上部一侧。下部夹板部10可形成有多个第一通气孔11、第二通气孔12及第三通气孔13,使得当施用夹板时空气可从外部通向夹板的内侧,上部夹板部30能够以规定长度形成于下部夹板部10的一侧上部。伸张夹板部20延伸形成于上部夹板部30,伸张夹板部20能够以规定长度延伸形成,以便能够夹住手指。在伸张夹板部20中能够以规定间距形成有多个伸张孔21,使得通过弯曲进行变形。参照图5,可弯曲的夹板1b可夹住胳膊和手腕及手指,下部夹板部10以包围胳膊的方式的形状形成,伸张夹板部20以能够夹住手指的方式形成。图6为示出本发明一实施例的可弯曲的夹板的成型方法的流程图。本发明一实施例的可弯曲的夹板的成型方法包括:步骤s10,根据夹板的施用部位,将夹板部件切割成规定形状;步骤s20为了在弯曲上述夹板部件时使上述夹板部件顺利地变形及伸张而在伸张夹板部冲孔多个伸张孔;步骤s30,为了使空气通向外部而根据上述夹板部件的施用部位冲孔多个通气孔;第一弯曲步骤s40,为了包围上述夹板部件的施用部位的外部面,以规定的弧形对上述夹板部件进行曲面弯曲;以及第二弯曲步骤s50,使形成有上述伸张孔的上述伸张夹板部具有不同角度或规定直径的方式进行曲面弯曲。在一实施例中,如图1至图6所示,将夹板部件可弯曲的夹板的成型方法根据施用于腿或胳膊等的夹板切割成规定形状(步骤s10)。在上述夹板部件为施用或佩戴于腿的夹板的情况下,如图1所示,可切割成具有规定长度和宽度的呈大致长方形的夹板部件。并且,在上述夹板为施用或佩戴于胳膊等的夹板的情况下,如图4所示,将具有规定长度和宽度的下部夹板部10形成为大致梯形,并一体形成伸张夹板部20,使得可插入手指。即,夹板部件根据腿或胳膊等佩戴部位形成为适当的形状,并可形成一个以上的伸张夹板部20,使得可插入身体的一部分如手指或脚趾等。在上述夹板部件中可在通过弯曲发生变形的部位形成具有规定长度和宽度的伸张孔21、22(步骤s20)。上述伸张孔20不仅通过弯曲而有利于夹板部件的变形,而且在夹板部件的变形时使夹板部件变形成所需的形状。即,伸张孔21、22形成为直线,通过弯曲而变形时伸张孔21、22的间距隔开,使得弯曲良好并顺利进行,尽管存在弯曲应力,但是也可以弯曲成所需的形状。并且,在夹板部件可形成多个通气孔11、12、13,使得当佩戴或施用夹板时使空气从外部通向夹板的内侧(步骤s30)。上述通气孔11、12、13根据夹板的佩戴可使外部的空气与胳膊或腿接触,并且可为了解决因佩戴夹板而引起的烦闷和不适感而形成多个。像这样,在夹板部件形成伸张夹板部20及通气孔11、12、13的状态下,可通过弯曲器来进行第一次弯曲(步骤s40)。如图2及图3所示,这种第一次弯曲可将下部夹板部10及上部夹板部30弯曲成规定的弧形。即,夹板部件可通过第一次弯曲弯曲成大致半圆形。并且,如图5所示,通过第一次弯曲将下部夹板部10弯曲成规定的弧形。即,如图5所示,对于夹板部件可通过第一次弯曲将下部夹板部10弯曲成规定的弧形。可对进行上述第一次弯曲的夹板部件进行第二次弯曲,使得能够以伸张夹板部20为基准,将下部夹板部10和上部夹板部30弯曲成不同的角度(步骤s50)。如图2及图3所示,可通过弯曲器将佩戴在腿的夹板弯曲成所需的角度。并且,如图5所示,在进行第一次弯曲的状态下,可将佩戴在胳膊的夹板的伸张夹板部20弯曲成具有规定直径的圆形。在本发明的一实施例中,可提供低温可加工性得以提高的生物降解性复合树脂组合物、复合树脂制备方法及由此制备的片材的制备方法。后述的生物降解性复合树脂组合物或片材可用作用于制备可弯曲的夹板的夹板部件。在本发明的一实施例中,可提供低温可加工性得以提高的生物降解性复合树脂组合物,其特征在于,通过混合聚乳酸、聚己内酯、聚丁二酸丁二醇酯、聚己二酸/对苯二甲酸丁二酯、聚乙酸乙烯酯、交联剂、增容剂来形成。在这种复合树脂组合物中,可通过挤出机熔融挤出28~72重量百分比的聚乳酸、5~20重量百分比的聚己内酯、5~10重量百分比的聚丁二酸丁二醇酯、5~15重量百分比的聚己二酸/对苯二甲酸丁二酯、10~20重量百分比的聚乙酸乙烯酯、2~4重量百分比的交联剂、1~3重量百分比的增容剂。上述生物降解性复合树脂包括广义的降解性复合树脂,上述降解性复合树脂由美国材料与试验协会(americansocietyfortestingandmaterials,astm)规定为在特定环境条件下在规定时间内化学结构发生很大变化可通过标准试验方法测定的性质变化的塑料,上述降解性复合树脂分为生物降解性、生物光降解性“分化降解性”、光降解性塑料。并且,在作为国际标准组织的国际标准化组织(internationalstandardorganization,iso)将最终生物降解(ultimatebiodegradation),即,微生物作用下发生有机分解,最终生成二氧化碳、水合无机盐/生物物质的过程规定为生物降解。在根据国际标准化组织472的降解性塑料的定义中,将降解性塑料分为生物降解性塑料和降解性塑料。这种生物降解性塑料是指当用作成型品、包装材料、卫生用品、农业用品等塑料废弃时仅通过简单的填埋来处理而不进行焚烧处理,在几个月到几年的时间内完全分解成水、二氧化碳、甲烷气体、生物质等的塑料。在这种复合树脂组合物中,在上述聚乳酸小于28重量百分比的情况下,用户难以获得所需的物性,在大于72重量百分比的情况下,复合树脂的加工性可能下降。在本复合树脂组合物中,适当地,上述聚乳酸为28~72重量百分比。并且,在聚己内酯小于5重量百分比的情况下,抗拉强度及屈服强度未达到用户所需的水平,在大于20重量百分比的情况下,机械物性可能下降。在本复合树脂组合物中,上述聚己内酯可以合适地为5~20重量百分比。并且,在复合树脂组合物中,在上述聚丁二酸丁二醇酯小于5重量百分比的情况下,获得的树脂的可加工性显著下降,在大于10重量百分比的情况下与现有树脂没有任何差别。另一方面,上述聚丁二酸丁二醇酯可用聚丁二酸己二酸丁二醇酯来代替。此时,上述聚乳酸时通过将左旋聚乳酸和作为异构体的右旋聚乳酸立体络合而成。并且,在一实施例中,上述聚乳酸可以是包含左旋聚乳酸、右旋聚乳酸及外消旋聚乳酸的均聚物,或者聚乳酸还可以是包含左旋聚乳酸、右旋聚乳酸及外消旋聚乳酸的共聚物。此时,在上述聚乳酸为上述左旋聚乳酸、右旋聚乳酸及外消旋聚乳酸的共聚物的情况下,可立体络合5~10重量百分比的上述右旋聚乳酸。并且,在上述聚己二酸/对苯二甲酸丁二酯小于5重量百分比的情况下,机械强度和柔软性下降,在大于15重量百分比的情况下,在机械方向(md)上发生撕裂。若以适当比例混合上述聚己二酸/对苯二甲酸丁二酯,则具有优秀的生物降解性和机械强度并可具有得到提高的柔然性。在本复合树脂组合物中,适当地,上述聚己二酸/对苯二甲酸丁二酯可以为5重量百分比~15重量百分比。并且,在一实施例中,上述聚乙酸乙烯酯可选自由交联剂接枝的聚乙烯醇及它们的衍生物或混合物组成的组中。适当地,上述聚乙酸乙烯酯可以为10~20重量百分比。另一方面,上述增容剂是存在于复合体系中的组分之间的界面并通过帮助混溶性和向同性来形成强烈的界面粘结的物质,在本发明中可适用聚乙二醇(polyethyleneglycol,peg)、马来酸酐(maleicanhydrate,ma)、缩水甘油马来酸酐(glycidilmaleicanhydrade,gam)。上述增容剂可适用马来酸酐。以下,通过下述实施例及比较例进一步具体说明本发明的生物降解性复合树脂组合物。但是仅用于助于理解而例示性记载了本实施例,并非用于限定本发明。实施例1低温可加工性得以提高的生物降解性复合树脂组合物是通过添加50重量百分比的聚乳酸、10重量百分比的聚己内酯、5重量百分比的聚丁二酸丁二醇酯、15重量百分比的聚己二酸/对苯二甲酸丁二酯、15重量百分比的聚乙酸乙烯酯、3重量百分比的交联剂、2重量百分比的增容剂,并用双螺杆挤出机熔融挤出,从而进行颗粒化。然后,根据astmd256在23℃的温度和3.2mm的棒(bar)下对获得的颗粒进行成型后,并根据astmd256测量每个棒的缺口伊佐德冲击强度后,在下述表2中示出。实施例2低温可加工性得以提高的生物降解性复合树脂组合物是通过添加50重量百分比的聚乳酸、15重量百分比的聚己内酯、5重量百分比的聚丁二酸丁二醇酯、15重量百分比的聚己二酸/对苯二甲酸丁二酯、10重量百分比的聚乙酸乙烯酯、4重量百分比的交联剂、1重量百分比的增容剂,并用双螺杆挤出机熔融挤出,从而进行颗粒化。然后,根据astmd256在23℃的温度和3.2mm的棒下对获得的颗粒进行成型后,并根据astmd256测量每个棒的缺口伊佐德冲击强度后,在下述表2中示出。实施例3低温可加工性得以提高的生物降解性复合树脂组合物是通过添加50重量百分比的聚乳酸、20重量百分比的聚己内酯、5重量百分比的聚丁二酸丁二醇酯、10重量百分比的聚己二酸/对苯二甲酸丁二酯、10重量百分比的聚乙酸乙烯酯、2重量百分比的交联剂、3重量百分比的增容剂,并用双螺杆挤出机熔融挤出,从而进行颗粒化。然后,根据astmd256在23℃的温度和3.2mm的棒下对获得的颗粒进行成型后,并根据astmd256测量每个棒的缺口伊佐德冲击强度后,在下述表2中示出。实施例4低温可加工性得以提高的生物降解性复合树脂组合物是通过添加50重量百分比的聚乳酸、15重量百分比的聚己内酯、5重量百分比的聚丁二酸丁二醇酯、5重量百分比的聚己二酸/对苯二甲酸丁二酯、20重量百分比的聚乙酸乙烯酯、4重量百分比的交联剂、1重量百分比的增容剂,并用双螺杆挤出机熔融挤出,从而进行颗粒化。然后,根据astmd256在23℃的温度和3.2mm的棒下对获得的颗粒进行成型后,并根据astmd256测量每个棒的缺口伊佐德冲击强度后,在下述表2中示出。实施例5低温可加工性得以提高的生物降解性复合树脂组合物是通过添加50重量百分比的聚乳酸、5重量百分比的聚己内酯、10重量百分比的聚丁二酸丁二醇酯、15重量百分比的聚己二酸/对苯二甲酸丁二酯、15重量百分比的聚乙酸乙烯酯、4重量百分的交联剂比、1重量百分比的增容剂,并用双螺杆挤出机熔融挤出,从而进行颗粒化。然后,根据astmd256在23℃的温度和3.2mm的棒下对获得的颗粒进行成型后,并根据astmd256测量每个棒的缺口伊佐德冲击强度后,在下述表2中示出。比较例1低温可加工性得以提高的生物降解性复合树脂组合物通过添加100重量百分比的聚乳酸、0重量百分比的聚己内酯、0重量百分比的聚丁二酸丁二醇酯、0重量百分比的聚己二酸/对苯二甲酸丁二酯、0重量百分比的聚乙酸乙烯酯、0重量百分比的交联剂、0重量百分比的增容剂,并用双螺杆挤出机熔融挤出,从而进行颗粒化。然后,根据astmd256在23℃的温度和3.2mm的棒下对获得的颗粒进行成型后,并根据astmd256测量每个棒的缺口伊佐德冲击强度后,在下述表2中示出。比较例2低温可加工性得以提高的生物降解性复合树脂组合物通过添加85重量百分比的聚乳酸、0重量百分比的聚己内酯、5重量百分比的聚丁二酸丁二醇酯、5重量百分比的聚己二酸/对苯二甲酸丁二酯、5重量百分比的聚乙酸乙烯酯、0重量百分比的交联剂、0重量百分比的增容剂,并用双螺杆挤出机熔融挤出,从而进行颗粒化。然后,根据astmd256在23℃的温度和3.2mm的棒下对获得的颗粒进行成型后,并根据astmd256测量每个棒的缺口伊佐德冲击强度后,在下述表2中示出。比较例3低温可加工性得以提高的生物降解性复合树脂组合物通过添加75重量百分比的聚乳酸、5重量百分比的聚己内酯、5重量百分比的聚丁二酸丁二醇酯、5重量百分比的聚己二酸/对苯二甲酸丁二酯、5重量百分比的聚乙酸乙烯酯、4重量百分的交联剂比、1重量百分比的增容剂,并用双螺杆挤出机熔融挤出,从而进行颗粒化。然后,根据astmd256在23℃的温度和3.2mm的棒下对获得的颗粒进行成型后,并根据astmd256测量每个棒的缺口伊佐德冲击强度后,在下述表2中示出。比较例4低温可加工性得以提高的生物降解性复合树脂组合物通过添加65重量百分比的聚乳酸、5重量百分比的聚己内酯、5重量百分比的聚丁二酸丁二醇酯、10重量百分比的聚己二酸/对苯二甲酸丁二酯、12重量百分比的聚乙酸乙烯酯、2重量百分比的交联剂、1重量百分比的增容剂,并用双螺杆挤出机熔融挤出,从而进行颗粒化。然后,根据astmd256在23℃的温度和3.2mm的棒下对获得的颗粒进行成型后,并根据astmd256测量每个棒的缺口伊佐德冲击强度后,在下述表2中示出。比较例5低温可加工性得以提高的生物降解性复合树脂组合物是通过添加55重量百分比的聚乳酸、5重量百分比的聚己内酯、10重量百分比的聚丁二酸丁二醇酯、10重量百分比的聚己二酸/对苯二甲酸丁二酯、15重量百分比的聚乙酸乙烯酯、2重量百分比的交联剂、3重量百分比的增容剂,并用双螺杆挤出机熔融挤出,从而进行颗粒化。然后,根据astmd256在23℃的温度和3.2mm的棒下对获得的颗粒进行成型后,并根据astmd256测量每个棒的缺口伊佐德冲击强度后,在下述表2中示出。表1示出构成实施例1至实施例5及比较例1至比较例5的复合树脂组合物的组合的组成比。表1测定加工成在实施例1~5及比较例1~5中制备的颗粒状的生物降解性复合树脂的棒的冲击强度后,对其进行评价,其结果如表2所示。并且,在170~190℃的温度下利用单轴挤出机(l/d:40,直径为35mm)熔融混练生物降解性复合树脂并加工成3mm的厚度的片材后,按夹板(splint)规格利用激光切割机切割后,用带自动温度调节器的水浴将温度调至70℃并将切割的片材浸泡60秒钟,利用模型成型后,并按时间测量其成型性,分为如下4个等级对低温成型性进行评价。表2冲击强度(j/m)成型性评价实施例1463很好实施例2423很好实施例3342好实施例4368好实施例5512良好比较例163一般比较例293一般比较例3118良好比较例4152良好比较例5321好在上述表2中,由实施例1~5制备的生物降解性复合树脂的冲击强度优于由比较例1~5制备的生物降解性复合树脂,在成型性评价中,由实施例1~5制备的生物降解性复合树脂在成型性评价中也优秀并且,在加工片材后,夹板(splint)的成型等级如下。-成型时间为30~60秒钟:很好-成型时间为60~100秒钟:好-成型时间为100~200秒钟:良好-成型时间为200秒钟以上:一般以下,对利用如上所述的低温可加工性得以提高的生物降解性复合树脂组合物的复合树脂制备方法进行详细说明。图7为示出本发明一实施例的低温可加工性得以提高的生物降解性复合树脂制备方法的流程图。参照图7,低温可加工性得以提高的生物降解性复合树脂制备方法可包括粉末状态加工步骤s110、混合步骤s120、熔融挤出步骤s130、冷却、干燥步骤s140以及包装步骤s150。在粉末状态加工步骤s110中,制备复合树脂时所使用的原料可以为聚乳酸、聚己内酯、聚丁二酸丁二醇酯、聚己二酸/对苯二甲酸丁二酯、聚乙酸乙烯酯、交联剂、增容剂。更具体地,能够以28~72重量百分比的上述聚乳酸、5~20重量百分比的聚己内酯、5~10重量百分比的聚丁二酸丁二醇酯、5~15重量百分比的聚己二酸/对苯二甲酸丁二酯、10~20重量百分比的聚乙酸乙烯酯、2~4重量百分比的交联剂,1~3重量百分比的增容剂的比例混合。在混合步骤s120中,用于粉末原料的混合的设备可使用双刀片带式搅拌机。在本发明的实施例中,用于上述第一次加工物质和剩余原料的混合中的设备例示了双刀片带式搅拌机,但是根据实施例可使用任何设备,只要是用于混合原料的设备即可。在熔融挤出步骤s130中,可利用配备有原料供给装置的双螺杆挤出机熔融挤出上述混合物来进行加工。用于熔融挤出上述混合物的双螺杆挤出机是用于熔融挤出材料时使用的常规的公知技术,并省略其详细说明。在冷却、干燥步骤s140中,将通过上述配备有原料供给装置的双螺杆挤出机挤出的原料投入模具后,可冷却并干燥通过模具处来的线材。此时,线材的冷却、干燥可应用常规的水冷式和气冷式。其中,上述水冷式需要对聚乳酸复合树脂进行第二次干燥。为此在本发明的实施例中可应用作为一体式冷却和干燥的气冷式的冷却干燥方法。通过上述挤出机加工的线材具有规定的温度。为此,在冷却、干燥步骤中,可对线材的温度进行冷却。在上述线材的冷却、干燥步骤中,应用气冷系统是为了通过排除冷却后干燥步骤来减少功率和时间,由此实现环境友好的制备方法。用于冷却上述线材的气冷系统可使用冷却对象时所使用的常规的气冷系统。在本发明的实施例中,将应用于片材冷却的设备具体化为气冷系统,但可应用任何设备,只要是用于冷却对象的设备即可。并且,在水冷式的情况下,由于需要干燥步骤,所以在本发明中可应用气冷式。在包装步骤s150中,对冷却的线材进行造粒后包装。其中,上述线材的规格中密度为1.25±0.05(g/cm2)、抗拉强度为50(mpa)、拉伸活动率为3.5~6(gpa)、软化温度为60~70℃、收缩率小于0.5%及水分含量为200ppm以下。并且,在冷却并干燥上述熔融挤出的线材的步骤s40中,加工的线材可通过气冷系统来冷却。为此,通过本发明的一实施例的低温可加工性得以提高的生物降解性复合树脂及其制备方法制备的复合树脂,通过主要原料成分及利用其的制备方法的改善,将利用上述材料产品化的物品可在60~70℃的低温状态下下易于进行后加工,作为对生物体接触无害,符合食品接触标准的复合树脂,满足生物降解性条件,因此可用于自然循环。以下,对利用如上所述的低温可加工性得以提高的生物降解性复合树脂的片材制备方法进行详细说明。图8为示出利用本发明一实施例的低温可加工性得以提高的生物降解性复合树脂的片材制备方法的流程图。参照图8,上述制备方法可包括:步骤s210,粉末加工28~72重量百分比的聚乳酸、5~20重量百分比的聚己内酯、5~10重量百分比的聚丁二酸丁二醇酯、5~15重量百分比的聚己二酸/对苯二甲酸丁二酯、10~20重量百分比的聚乙酸乙烯酯、2~4重量百分比的交联剂、1~3重量百分比的增容剂;步骤s220,利用双刀片带式搅拌机对加工成粉末状态的上述原料进行混合;步骤s230,利用配备有原料供给装置的双螺杆挤出机熔融挤出经混合的上述原料;步骤s240,将经熔融挤出的上述原料投入模具后,冷却并干燥通过模具出来的线材;步骤s250,利用片材制备用t型模具挤出机熔融挤出经冷却并干燥的上述线材;步骤s260,压延通过上述t型模具挤出机熔融挤出的复合树脂来调节厚度并通过第一次冷却来制备片材;步骤s270,对在上述厚度被调节的状态下进行第一次冷却的片材进行第二次冷却;步骤s280,以及按规格切割经第二次冷却的上述片材并进行包装。上述步骤s210至步骤s240分别对应于参照图7说明的低温可加工性得以提高的生物降解性复合树脂制备方法的步骤s110至步骤s140,有关步骤s210至步骤s240,可参照图7中的步骤s110至步骤s140的说明。在片材制备及进行第一次冷却步骤s260中,对通过上述t型模具挤出机熔融挤出的复合树脂进行压延来调节厚度,并可通过第一次冷却来制备片材。用于本发明实施例的片材制备方法的挤出机可应用任何挤出机,只要是常规的片材制备用挤出机即可。在通过上述压延调节厚度并进行第一次冷却步骤s260中,可应用包括冷却辊的三轴辊。并且,若片材制备中可控制最佳的熔融温度可,则工艺指南(processguide)是通用的,因此省略其详细说明。其中,本发明实施例的片材的规格可设定在密度为1.25±0.05(g/cm2)、抗拉强度为50(mpa)、拉伸活动率为3.5~6(gpa)、软化温度为60~70℃、收缩率小于0.5%及水分含量为200ppm以下的范围之内。在第二次冷却步骤s270中,在调节上述厚度的状态下,对进行第一次冷却的片材进行第二次冷却,在包装的步骤s280中,可按规格切割进行上述第二次冷却的片材来包装。在本发明的实施例中,通过低温可加工性得以提高的生物降解性复合树脂及复合树脂制备方法制备的复合树脂满足主要原料成分及利用其的制备方法在环保型方面得到改善,利用这样制备的复合树脂的产品可在60~70℃的低温状态下易于进行后加工,作为对生物体接触无害,符合食品接触标准,并可通过满足生物降解性条件来使用资源循环。以上,通过上述实施例对由本发明人实施的发明进行了具体说明,但是本发明并不限定于上述实施例,在不脱离本发明主旨的情况下,可进行各种变更。当前第1页1 2 3