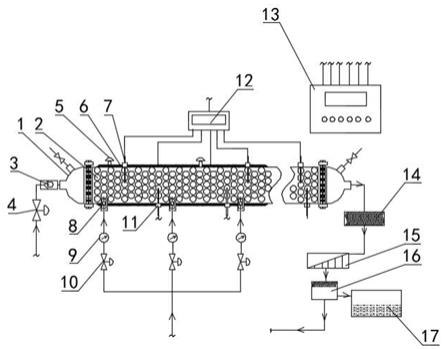
1.本发明涉及化工技术领域,具体为一种催化氧化制备米氏醇的设备及工艺。
背景技术:2.当今的化工产业越来越发达,例如米氏醇是重要的医药、染料中间体,用途广泛。米氏醇作为染料结晶紫内酯(cvl)的主要原料,市场需求量很大。通常以甲烷贝斯(4,4
’-
双二甲氨基二苯基甲烷)和氧气为原料,经过催化氧化过程制备米氏醇。
3.据公开的资料显示,国内使用氧化法生产米氏醇,普遍采用的是反应釜间歇式生产。在实验室模拟该反应,使用负载型多元金属氧化物催化剂,以空气鼓泡法供氧,在球形反应装置中反应时长120min,产品收率和纯度均满意。但间歇釜式反应存在频繁装卸料,反复升降温等诸多重复性操作,生产能力受到制约。为提高生产效率,我司设计并制作了一个小型管式反应器来生产米氏醇。
技术实现要素:4.本发明的目的在于提供一种催化氧化制备米氏醇的设备及工艺,以解决上述背景技术中提出的问题。
5.为实现上述目的,本发明提供如下技术方案:一种催化氧化制备米氏醇的设备,包括壳体,所述壳体内部填装有催化剂,所述壳体入口端通过管道依次连接有入料单向阀和入料电磁阀,所述壳体上端设有安全阀,所述壳体外部缠绕有加热带,所述壳体内部安装有温度传感器(数个测温点),所述壳体上设有氧气接口并且接口上安装有氧气单向阀(防止倒吸和反冲),所述氧气单向阀通过管道连接有氧气电磁阀并且之间的管道上安装有压力表,所述壳体上的氧气接口旁安装有氧气浓度计(作用:可以根据氧传感器数据,调整下游氧气供应量,保证氧化完全,又不至于过度氧化),所述壳体出口端通过管道依次连接有冷凝器、气液分离器、减压蒸馏器和冷却结晶池,所述加热带和温度传感器通过导线连接在温度控制器上,所述入料电磁阀、氧气电磁阀、压力表、氧气浓度计和温度控制器分别通过导线连接在总控制器。
6.优选的:所述壳体材质为304不锈钢,管径d为ф16-50mm,管壁厚2-6mm,长度l为800-2500mm,两侧有封头,通过法兰连接,长径比l/d≥50,所述壳体1内壁上设有导流片并且与管壁呈90
°-
145
°
夹角。
7.优选的:所述催化剂为co-mn-ce多元金属氧化物,载体为活性γ-al2o3微球并且直径d为3-5mm,所述导流片101长度为0.5d-0.86d;所述催化剂填充方式采用径向分层复合堆积方式,装填体积数值为壳体有效长度数值的一半。
8.优选的:所述壳体上的氧气接口成线性分布或者螺旋形分布。
9.优选的:所述加热带外部缠绕保温材料。
10.具体工艺步骤如下:1). 甲烷贝斯用热乙醇溶解,热乙醇含量为20%,溶液从管道进入管式反应设备中,通
过控制入料电磁阀来控制流量;2). 氧气来源于制氧机或气瓶组,氧气经减压阀减压后,压力调至约350 kpa从氧气接口进入反应设备中,通过控制氧气电磁阀控制供氧量;3).打开加热带开始加热并且达到反应温度开始反应,反应温度控制在70℃
±
2℃,由温度控制器设定温度及加热时间,甲烷贝斯在壳体内前进的过程中,被催化氧化,生成四甲基米氏醇;4).壳体出口端接冷凝器和气液分离器,气液分离器气相经冷凝器常压放空,排空压力约为101.3kpa;5).分离出来的液相产物进入减压蒸馏器,蒸出溶剂循环使用,母液在冷却结晶池中冷却后有结晶析出,抽滤后得粗产品;6). 粗产品经乙醇溶解后重结晶,可得产品纯度≥99.5%,母液可作为溶剂循环使用,但反复使用,会影响产品纯度和色泽,可以根据需要进行选择;使用该管式反应器进行催化氧化法制备米氏醇反应的一个优势是可以多点位动态调整氧气供应量,使氧化反应完全进行,同时尽可能避免氧化反应过度。在氧气接口前端的氧传感器探测结果显示游离氧含量≤0.1mol/l时即需要补氧,出料口前端氧传感器探测结果≥0.1mol/l时,即需要降低前一级氧气接口的供氧量。
11.管式反应器为功能完整的单元结构,可独立工作。可根据实际需要,由多根管式反应器组成反应器阵列。可以多根反应器串联,形成有效长度更长的反应器,增加物料在反应器内与催化剂的接触时间。也可以多根反应器并联,组成有效截面通量更大的反应器。也可以根据具体工艺和产能的需求,串并联同时使用。
12.已知提高催化剂床层截面积可以增大单位时间内反应物通量,延长管式反应器长度可以提高反应物在催化剂床层停留时间。因此提高产能更好的办法是设计制造一个直径更大,长度更长的管式反应器。
13.假设以我们制作的这根管式反应器为标准单元,它的产能为e, 用n根同样的管式反应器并联,操作条件不变,则它们的总产能为ne。如果制成一根产能为ne的管式反应器,我们可以根据公式rnew=n^
(1/2)
•
r ,来推算这个新的管式反应器催化剂床层截面半径。我们在增大反应器半径rnew的同时,也会增加反应器长度lnew,以满足恰当的长径比要求,实际产能将比ne更大。
14.综上所述本发明与现有技术相比,本发明的有益效果是:1、本发明涉及的管式反应器取代用反应釜间歇式反应,避免了频繁装卸料,反复升降温等诸多重复性操作。管式反应器可以连续性生产,而且在温度压力流量等参数固定化后可以长期稳定运行。采用管式反应器进行催化氧化反应,比使用间歇釜式反应器效率更高,节能性更好。在运用精确的传感和plc嵌入控制系统控制下,可以实现连续、稳定的自动化生产,转化率和产品纯度都有保证。
15.2、该工艺采用乙醇做溶剂,产物易分离,低温减压蒸馏出溶剂可以循环使用。不需要酸碱中和过程,对设备无腐蚀,不会产生大量三废。
16.3、本发明的管式反应器,本身具备可调整反应平衡的功能。可通过调整氧气供应量,控制反应深度,防止过度氧化发生副反应。
17.4、导流片的独特设计,最大限度的避免了壁效应对流体传质和传热的不利影响。
18.5、催化剂采用径向分层复合堆积结构,是最有效的堆积方式。
19.6、管式反应器是一个多用途反应器,可用于多种催化氧化反应。
20.7、管式反应器的物理参数和催化剂的性能决定了该反应器的氧化效率。可以通过增大反应器截面积、延长催化剂床层长度并提高空速的办法,增大单位时间处理量,实现提高产能的目的。在设计新的管式反应器的时候,公式 rnew=n^
(1/2)
•
r 具有一定的指导意义。
附图说明
21.图1为本发明结构示意图;图2为壳体内壁结构示意图;图3为反应方程式;图4为空速与转化率曲线图。
22.图中:1、壳体,2、催化剂,3、入料单向阀,4、入料电磁阀,5、安全阀,6、加热带,7、温度传感器,8、氧气单向阀,9、压力表,10、氧气电磁阀,11、氧气浓度计,12、温度控制器,13、总控制器,14、冷凝器,15、气液分离器,16、减压蒸馏器,17、冷却结晶池,101、导流片。
具体实施方式
23.下面将结合本发明实施例中的附图,对本发明实施例中的技术方案进行清楚、完整地描述,显然,所描述的实施例仅仅是本发明一部分实施例,而不是全部的实施例。基于本发明中的实施例,本领域普通技术人员在没有做出创造性劳动前提下所获得的所有其他实施例,都属于本发明保护的范围。
24.请参阅图1-图4,本发明提供一种技术方案,包括壳体1,所述壳体1内部填装有催化剂2,所述壳体1入口端通过管道依次连接有入料单向阀3和入料电磁阀4,所述壳体1上端设有安全阀5,所述壳体1外部缠绕有加热带6,所述壳体1内部安装有温度传感器7(数个测温点),所述壳体1上设有氧气接口并且接口上安装有氧气单向阀8(防止倒吸和反冲),所述氧气单向阀8通过管道连接有氧气电磁阀10并且之间的管道上安装有压力表9,所述壳体1上的氧气接口旁安装有氧气浓度计11(作用:可以根据氧传感器数据,调整下游氧气供应量,保证氧化完全,又不至于过度氧化),所述壳体1出口端通过管道依次连接有冷凝器14、气液分离器15、减压蒸馏器16和冷却结晶池17,所述加热带6和温度传感器7通过导线连接在温度控制器12上,所述入料电磁阀4、氧气电磁阀10、压力表9、氧气浓度计11和温度控制器12分别通过导线连接在总控制器13。
25.所述壳体1材质为304不锈钢,管径d为ф16-50mm,管壁厚2-6mm,长度l为800-2500mm,两侧有封头,通过法兰连接,长径比l/d≥50,所述壳体1内壁上设有导流片101并且与管壁呈90
°-
145
°
夹角。
26.所述催化剂2为co-mn-ce多元金属氧化物,载体为活性γ-al2o3微球并且直径d为3-5mm,所述导流片101长度为0.5d-0.86d;所述催化剂2填充方式采用径向分层复合堆积方式,装填体积数值为壳体1有效长度数值的一半。
27.所述壳体1上的氧气接口成线性分布或者螺旋形分布。
28.所述加热带6外部缠绕保温材料。
29.具体步骤如下:
1). 甲烷贝斯用热乙醇溶解,热乙醇含量为20%,溶液从管道进入管式反应设备中,通过控制入料电磁阀4来控制流量;2). 氧气来源于制氧机或气瓶组,氧气经减压阀减压后,压力调至约350 kpa,从氧气接口进入反应设备中,通过控制氧气电磁阀10控制供氧量;3).打开加热带6开始加热并且达到反应温度开始反应,反应温度控制在70℃
±
2℃,由温度控制器12设定温度及加热时间,甲烷贝斯在壳体1内前进的过程中,被催化氧化,生成四甲基米氏醇;4).壳体1出口端接冷凝器14和气液分离器15,气液分离器15气相经冷凝器常压放空,排空压力约为101.3kpa;5).分离出来的液相产物进入减压蒸馏器16,蒸出溶剂循环使用,母液在冷却结晶池17中冷却后有结晶析出,抽滤后得粗产品;6). 粗产品经乙醇溶解后重结晶,可得产品纯度≥99.5%,母液可作为溶剂循环使用,但反复使用,会影响产品纯度和色泽,可以根据需要进行选择;在使用本发明时,首先需要了解空速与转化率的关系,空速反映了装置的处理能力,有体积空速和质量空速两种表达形式。实施例中我们用体积空速来标记这根管式反应器的催化氧化能力。体积空速=原料体积流量(温度20℃,单位m3/h)/催化剂体积(m3),空速的最终单位是h-1
。
30.我们实验了该管式反应器在不同空速下(其他条件相同,管径d为ф50mm,管壁厚6mm,长度l为2500mm,导流片101与管壁呈145
°
夹角,载体微球直径d为5mm,导流片101长度为4.3mm),甲烷贝斯制备四甲基米氏醇的氧化反应。为考察管式反应器本身的催化氧化性能,排除动态供氧对氧化反应的积极作用,本组实验的供氧方式采用从第一氧气接口固定流量足量供氧。实验实施数据例如下所示:实施例1:甲烷贝斯乙醇溶液流量50ml/min,空速为6 h-1
;转化率92.2%。
31.实施例2:甲烷贝斯乙醇溶液流量100ml/min,空速为12 h-1
;转化率为93.0%。
32.实施例3:甲烷贝斯乙醇溶液流量200ml/min,空速为24h-1
;转化率为94.1%实施例4:甲烷贝斯乙醇溶液流量300ml/min,空速为36 h-1
;转化率为94.2%。
33.实施例5:甲烷贝斯乙醇溶液流量500ml/min,空速为60 h-1
;转化率为92.5%。
34.实施例6:甲烷贝斯乙醇溶液流量750ml/min,空速为90h-1
;转化率为72.2%。
35.实施例7:甲烷贝斯乙醇溶液流量1000ml/min,空速为120 h-1
;转化率为45.3%。
36.实施例8:甲烷贝斯乙醇溶液流量1500ml/min,空速为180 h-1
;转化率为22.6%。
37.实施例9:甲烷贝斯乙醇溶液流量2000ml/min,空速为240h-1
;转化率为5.1%。
38.如曲线图4所示空速与转化率关系曲线,随着空速的增大,转化率出现先上升后下降的趋势。这是因为在较低的空速下操作,物料在管式反应器内停留时间太长,氧化过度而发生副反应,从而导致转化率降低。随着空速增大,进入反应器内的原料停留时间缩短,副反应发生的越来越少,表现出转化率逐渐上升的趋势,直到最高点。随着空速继续增大,单位时间里通过催化剂床层的原料增多,反应物在反应器内停留时间缩短,反应不完全即离开,这也是随着空速增大而转化率急剧下降的合理解释。在恰当的操作区间内,可以实现较高的转化率和较大的处理量。这个区间内的某个平衡点,就是寻找的合适的操作条件。
39.在生产中,对化工工艺的要求是稳定和操作简便。追求较高的转化率,可以减少原
材料消耗,也降低产物分离的难度。在保证转化率满足要求的前提下,努力提高单位时间的产量。
40.从图4推算,在空速36h-1
时进行甲烷贝斯催化氧化反应,是该管式反应器最佳操作条件。
41.图4中的实验数据说明,在空速36~72h-1
范围内,启动氧气供应动态调整,可进一步提高该管式反应器的催化氧化效率,在保证较高转化率的基础上,实现更大的产能,如下列实施例所示:实施例11:甲烷贝斯乙醇溶液流量300ml/min,空速为36 h-1
;转化率94.2%;实际产能3.2kg/h。
42.实施例12:甲烷贝斯乙醇溶液流量400ml/min,空速为48 h-1
;转化率94.1%;实际产能4.4kg/h。
43.实施例13:甲烷贝斯乙醇溶液流量500ml/min,空速为60 h-1
;转化率93.9%;实际产能5.3kg/h。
44.实施例14:甲烷贝斯乙醇溶液流量600ml/min,空速为72 h-1
;转化率90.2%;实际产能6.1kg/h。
45.实施例15:甲烷贝斯乙醇溶液流量750ml/min,空速为90h-1
;转化率82.6%;实际产能6.5kg/h。
46.综上经实验验证,在该空速为36 h-1
条件下,每小时可生产约3.2kg四甲基米氏醇,与理论数据基本吻合。
47.尽管已经示出和描述了本发明的实施例,对于本领域的普通技术人员而言,可以理解在不脱离本发明的原理和精神的情况下可以对这些实施例进行多种变化、修改、替换和变型,本发明的范围由所附权利要求及其等同物限定。