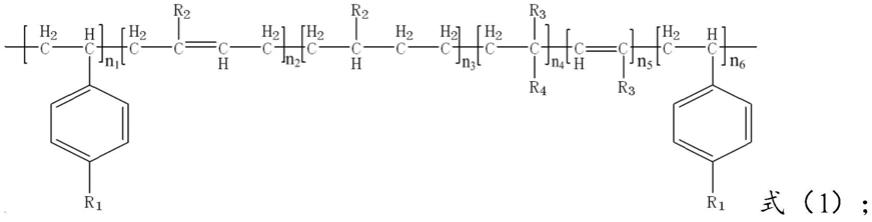
[0001]
本发明涉及橡胶领域,特别涉及一种丁基橡胶的制备方法。
背景技术:[0002]
丁基橡胶是合成橡胶的一种,主要是以异丁烯和少量异戊二烯为反应原料,在引发体系下,于低温(-100℃左右)下通过阳离子聚合制得的。丁基橡胶具有良好的化学稳定性和热稳定性,最突出的是气密性和水密性,由于其独特性能,被广泛用于制造内胎、防振橡胶、工业胶板、医用橡胶等许多方面。
[0003]
目前,丁基橡胶聚合工艺采用淤浆聚合法,以氯甲烷作溶剂,路易斯酸作主催化剂,质子酸作助催化剂,是典型的阳离子聚合。该反应具有反应速度快,放热集中,产物易挂胶、结团的特点。聚合温度升高会导致聚合物分子量急剧下降,难以获得高分子量产物,且产物分子量分布较窄;反应器挂胶会导致传热效果变差,影响撤热效率从而导致聚合温升加快,进而影响产品质量;胶粒结团严重导致溢流管堵塞,聚合反应周期缩短。因此如何迅速排出聚合热以控制反应在恒定的低温下进行,是生产上的主要问题。生产装置频繁开停车会导致生产成本增加,且导致产品质量大幅度波动。因此,丁基橡胶聚合体系传质传热问题成为本领域亟待解决的难题。
技术实现要素:[0004]
有鉴于此,本发明的目的在于提供一种丁基橡胶的制备方法。本发明提供的制备方法能够有效降低阳离子活性聚合的聚合物速度和温升、抑制产物结团、改善丁基橡胶在聚合体系的分散状态,从而提高产物分子量及拓宽分子量分布,以及提高产品质量。
[0005]
本发明提供了一种丁基橡胶的制备方法,包括以下步骤:
[0006]
a)将单烯烃与溶剂混合,得到混合液;
[0007]
b)将淤浆稳定剂溶于二烯烃中,得到淤浆稳定剂溶液;
[0008]
c)将所述混合液、淤浆稳定剂溶液与催化剂溶液混合反应,形成丁基橡胶;
[0009]
所述淤浆稳定剂具有式(1)所示结构:
[0010][0011]
其中,
[0012]
r1、r2、r3和r4各自独立地选自h、c1~c15的烷基、乙烯基、卤素、羟基、卤代甲基、卤代乙基或α-甲基乙烯基;
[0013]
聚合度n1为4~2000,n2为0~2000,n3为0~2000,n4为0~2000,n5为0~2000,n6为0
~2000。
[0014]
优选的,所述淤浆稳定剂与所述单烯烃的质量比为(0.01~5)∶100;
[0015]
所述淤浆稳定剂溶液的质量分数为1wt%~20wt%;
[0016]
所述单烯烃在所述混合液中的质量分数为5wt%~45wt%。
[0017]
优选的,所述单烯烃选自c4~c16的异单烯烃中的一种或几种;
[0018]
所述二烯烃选自c4~c14的共轭二烯烃中的一种或几种。
[0019]
优选的,所述二烯烃与单烯烃的摩尔比为(0.01~0.1)∶1。
[0020]
优选的,所述催化剂溶液包括:主催化剂、助催化剂和溶剂;
[0021]
所述主催化剂为路易斯酸催化剂;
[0022]
所述助催化剂为h2o或hcl。
[0023]
优选的,所述主催化剂与单烯烃的摩尔比为(0.0001~0.005)∶1;
[0024]
所述主催化剂与助催化剂的摩尔比为(1~20)∶1。
[0025]
优选的,所述催化剂溶液为经陈化处理后的催化剂溶液;
[0026]
所述陈化的温度为-80~-95℃,时间为1~45min。
[0027]
优选的,所述步骤c)中,反应的温度为-80~-98℃,时间为1~20min。
[0028]
优选的,所述步骤c)中,在所述反应后还包括:加入终止剂来终止反应;
[0029]
所述终止剂选自甲醇、乙醇、二甘醇中的一种或几种。
[0030]
优选的,所述步骤c)中,在所述反应后还包括:将反应所得产物浆料干燥,从而得到丁基橡胶。
[0031]
本发明提供了一种丁基橡胶的制备方法,在制备过程中引入式(1)所示淤浆稳定剂,能够有效降低阳离子活性聚合的聚合速度,改善丁基橡胶在聚合体系分散状态,抑制产物结团,从而增强聚合体系的传质传热,减轻反应釜堵塞,延长反应周期,最终提高产物分子量及拓宽分子量分布,以及提高产品质量。
[0032]
试验结果表明,本发明的制备方法能够有效降低阳离子活性聚合的聚合速度,改善丁基橡胶在聚合体系分散状态,抑制产物结团,减轻反应釜堵塞。同时,所得丁基橡胶产品的重均分子量在514000以上,分子量分数指数在3.2以上;丁基橡胶不饱和度在1.50mol%以上,门尼粘度(ml(1+8)125℃在43以上;300%定伸在8.0mpa以上,拉伸强度在16.6mpa以上。
附图说明
[0033]
为了更清楚地说明本发明实施例或现有技术中的技术方案,下面将对实施例或现有技术描述中所需要使用的附图作简单地介绍,显而易见地,下面描述中的附图仅仅是本发明的实施例,对于本领域普通技术人员来讲,在不付出创造性劳动的前提下,还可以根据提供的附图获得其他的附图。
[0034]
图1为实施例1~2及对比例1的聚合温升曲线图。
具体实施方式
[0035]
本发明提供了一种丁基橡胶的制备方法,包括以下步骤:
[0036]
a)将单烯烃与溶剂混合,得到混合液;
[0037]
b)将淤浆稳定剂溶于二烯烃中,得到淤浆稳定剂溶液;
[0038]
c)将所述混合液、淤浆稳定剂溶液与催化剂溶液混合反应,形成丁基橡胶;
[0039]
所述淤浆稳定剂具有式(1)所示结构:
[0040][0041]
其中,
[0042]
r1、r2、r3和r4各自独立地选自h、c1~c15的烷基、乙烯基、卤素、羟基、卤代甲基、卤代乙基或α-甲基乙烯基;
[0043]
聚合度n1为4~2000,n2为0~2000,n3为0~2000,n4为0~2000,n5为0~2000,n6为0~2000。
[0044]
本发明在制备过程中引入式(1)所示淤浆稳定剂,能够有效降低阳离子活性聚合的聚合速度,改善丁基橡胶在聚合体系分散状态,抑制产物结团,从而增强聚合体系的传质传热,减轻反应釜堵塞,延长反应周期,最终提高产物分子量及拓宽分子量分布,以及提高产品质量。
[0045]
关于步骤a):将单烯烃与溶剂混合,得到混合液。
[0046]
本发明中,所述单烯烃优选为c4~c16的异单烯烃中的一种或几种;更优选为c4~c10的异单烯烃中的一种或几种;最优选为c4~c6的异单烯烃中的一种或几种;在本发明的一些实施例中,所述单烯烃为异丁烯。
[0047]
本发明中,所述溶剂优选为氯甲烷;在本发明的一些实施例中,所述溶剂为一氯甲烷。
[0048]
本发明对单烯烃与溶剂的混合方式没有特殊限制,能够将二者混匀即可。本发明中,所述混合的温度优选为-60~-95℃。经混合后,得到混合液。
[0049]
本发明中,所述单烯烃在所述混合液中的质量分数优选为5wt%~45wt%;在本发明的一些实施例中,所述质量分数为10wt%、15wt%或27wt%。
[0050]
关于步骤b):将淤浆稳定剂溶于二烯烃中,得到淤浆稳定剂溶液。
[0051]
本发明中,所述淤浆稳定剂具有式(1)所示结构:
[0052][0053]
其中,
[0054]
r1、r2、r3和r4各自独立地选自h、c1~c15的烷基、乙烯基、卤素、羟基、卤代甲基、卤
代乙基或α-甲基乙烯基;
[0055]
聚合度n1为4~2000,n2为0~2000,n3为0~2000,n4为0~2000,n5为0~2000,n6为0~2000。
[0056]
在本发明的一些实施例中,所述淤浆稳定剂分别为式(1-1)~式(1-5)所示化合物:
[0057]
式(1-1):商品型号为asahi kasei p2000,ps(即聚苯乙烯)含量67wt%;
[0058][0059]
其中,n2和n4不为0。
[0060]
式(1-2):商品型号为kuraray 2006,ps含量35wt%;
[0061][0062]
其中,n3不为0。
[0063]
式(1-3):商品型号为kuraray 1020,ps含量36wt%;
[0064][0065]
其中,n3不为0。
[0066]
式(1-4):商品型号为jsr tr2250,ps含量52wt%;
[0067][0068]
其中,n2、n5不为0。
[0069]
式(1-5):商品型号为jsrtr1086,ps含量45wt%;
90~-97℃;所述反应的时间优选为1~20min,更优选为2~15min,最优选为5~10min。
[0085]
本发明中,在所述反应后,优选还包括:加入终止剂来终止反应。本发明中,所述终止剂优选为甲醇、乙醇和二甘醇中的一种或几种。本发明对所述终止剂的用量没有特殊限制,按照本领域常规终止操作所需用量执行即可。
[0086]
本发明中,经上述反应及终止操作后,得到丁基橡胶浆料。本发明还包括:对所述浆料干燥。本发明中,所述干燥优选为真空干燥;所述干燥的温度优选为25~50℃。经上述干燥脱除溶剂,得到丁基橡胶产品。
[0087]
本发明提供的丁基橡胶的制备方法中,在反应中引入特定的式(1)稳定剂,能够有效降低阳离子活性聚合的聚合速度,改善丁基橡胶在聚合体系分散状态,抑制产物结团,从而增强聚合体系的传质传热,减轻反应釜堵塞,延长反应周期,最终提高产物分子量及拓宽分子量分布,以及提高产品质量(包括获得较高的门尼粘度和较好的拉伸性能)。
[0088]
为了进一步理解本发明,下面结合实施例对本发明优选实施方案进行描述,但是应当理解,这些描述只是为进一步说明本发明的特征和优点,而不是对本发明权利要求的限制。以下实施例中,所用的稳定剂式(1-1)~(1-5)为前文中所述的商业产品。
[0089]
实施例1
[0090]
s1、在-70℃下,称取22.5g异丁烯加入到127.5g一氯甲烷中,得到混合液。
[0091]
s2、将式(1-1)所示聚合物加入异戊二烯中,得到6.3wt%的淤浆稳定剂溶液。
[0092]
s3、取1.07g步骤s2的淤浆稳定剂溶液加入到步骤s1的混合液中,降至-97.5℃,得到反应物溶液。
[0093]
s4、称取0.2g乙基倍半氯化铝的正己烷溶液(质量分数为10%)、加入到10ghcl的一氯甲烷溶液(质量分数为0.025wt%)中,混合均匀,并于-97.5℃下陈化30min,得到催化剂溶液。
[0094]
s5、将步骤s4的催化剂溶液加入步骤s3的反应物溶液中,于-97.5℃反应20min。聚合过程中温升缓慢,得到的浆料呈颗粒状分散均匀。
[0095]
s6、加入2g乙醇终止反应,将浆料移至真空干燥箱中除去溶剂,得到丁基橡胶。
[0096]
实施例2
[0097]
s1、在-70℃下,称取20g异丁烯加入到113.5g一氯甲烷中,得到混合液。
[0098]
s2、将式(1-2)所示聚合物加入异戊二烯中,得到4.4wt%的淤浆稳定剂溶液。
[0099]
s3、取1.36g步骤s2的淤浆稳定剂溶液加入到步骤s1的混合液中,降至-97.5℃,得到反应物溶液。
[0100]
s4、称取0.15g一氯二乙基铝的正己烷溶液(质量分数为20%)、加入到6ghcl的一氯甲烷溶液(质量分数为0.020wt%)中,混合均匀,并于-97.5℃下陈化20min,得到催化剂溶液。
[0101]
s5、将步骤s4的催化剂溶液加入步骤s3的反应物溶液中,于-97.5℃反应10min。聚合过程中温升缓慢,得到的浆料呈颗粒状分散均匀。
[0102]
s6、加入2g乙醇终止反应,将浆料移至真空干燥箱中除去溶剂,得到丁基橡胶。
[0103]
实施例3
[0104]
s1、在-85℃下,称取40g异丁烯加入到110g一氯甲烷中,得到混合液。
[0105]
s2、将式(1-3)所示聚合物加入异戊二烯中,得到5.66wt%的淤浆稳定剂溶液。
[0106]
s3、取2.12g步骤s2的淤浆稳定剂溶液加入到步骤s1的混合液中,降至-97.5℃,得到反应物溶液。
[0107]
s4、称取0.3g二氯乙基铝的正己烷溶液(质量分数为20%)、加入到12ghcl的一氯甲烷溶液(质量分数为0.020wt%)中,混合均匀,并于-97.5℃下陈化30min,得到催化剂溶液。
[0108]
s5、将步骤s4的催化剂溶液加入步骤s3的反应物溶液中,于-97.5℃反应20min。聚合过程中温升缓慢,得到的浆料呈颗粒状分散均匀。
[0109]
s6、加入2g乙醇终止反应,将浆料移至真空干燥箱中除去溶剂,得到丁基橡胶。
[0110]
实施例4
[0111]
s1、在-80℃下,称取15g异丁烯加入到135g一氯甲烷中,得到混合液。
[0112]
s2、将式(1-4)所示聚合物加入异戊二烯中,得到4.8wt%的淤浆稳定剂溶液。
[0113]
s3、取1.58g步骤s2的淤浆稳定剂溶液加入到步骤s1的混合液中,降至-97.5℃,得到反应物溶液。
[0114]
s4、称取0.15g二氯乙基铝的正己烷溶液(质量分数为20%)、加入到8ghcl的一氯甲烷溶液(质量分数为0.020wt%)中,混合均匀,并于-97.5℃下陈化15min,得到催化剂溶液。
[0115]
s5、将步骤s4的催化剂溶液加入步骤s3的反应物溶液中,于-97.5℃反应10min。聚合过程中温升缓慢,得到的浆料呈颗粒状分散均匀。
[0116]
s6、加入2g乙醇终止反应,将浆料移至真空干燥箱中除去溶剂,得到丁基橡胶。
[0117]
实施例5
[0118]
s1、在-80℃下,称取15g异丁烯加入到135g一氯甲烷中,得到混合液。
[0119]
s2、将式(1-5)所示聚合物加入异戊二烯中,得到4.8wt%的淤浆稳定剂溶液。
[0120]
s3、取1.58g步骤s2的淤浆稳定剂溶液加入到步骤s1的混合液中,降至-97.5℃,得到反应物溶液。
[0121]
s4、称取0.15g二氯乙基铝的正己烷溶液(质量分数为20%)、加入到8ghcl的一氯甲烷溶液(质量分数为0.020wt%)中,混合均匀,并于-97.5℃下陈化10min,得到催化剂溶液。
[0122]
s5、将步骤s4的催化剂溶液加入步骤s3的反应物溶液中,于-97.5℃反应15min。聚合过程中温升缓慢,得到的浆料呈颗粒状分散均匀。
[0123]
s6、加入2g乙醇终止反应,将浆料移至真空干燥箱中除去溶剂,得到丁基橡胶。
[0124]
对比例1
[0125]
按照实施例1的制备过程进行,不同的是,不添加淤浆稳定剂。
[0126]
聚合过程中温升迅速,且产物结团黏在反应釜的搅拌桨及釜壁上。
[0127]
实施例6
[0128]
(1)温升测试
[0129]
对实施例1~2及对比例1聚合过程中的温升进行监测,结果参见图1,图1为实施例1~2及对比例1的聚合温升曲线图。可以看出,对比例1聚合过程的温升较快,相比之下,实施例1~2的聚合温升明显降低。证明,本发明的制备方法能够有效降低阳离子活性聚合的聚合速度,改善丁基橡胶在聚合体系分散状态,抑制产物结团,从而增强聚合体系的传质传
热,减轻反应釜堵塞。
[0130]
(2)丁基橡胶产品性能测试
[0131]
对实施例1~5及对比例1所得丁基橡胶产品进行核磁分析、门尼粘度分析、gpc测试,结果参见表1。
[0132]
表1实施例1~5及对比例1所得产品的测试结果
[0133][0134][0135]
由表1测试结果可以看出,与对比例1相比,实施例1~5所得丁基橡胶产品的分子量明显提升,分子量分布明显拓宽。同时,丁基橡胶的拉伸性能明显提高,门尼粘度和不饱和度也明显提升,使产品性能得到明显改善。
[0136]
以上实施例的说明只是用于帮助理解本发明的方法及其核心思想。对这些实施例的多种修改对本领域的专业技术人员来说将是显而易见的,本文中所定义的一般原理可以在不脱离本发明的精神或范围的情况下,在其它实施例中实现。因此,本发明将不会被限制于本文所示的这些实施例,而是要符合与本文所公开的原理和新颖特点相一致的最宽的范围。