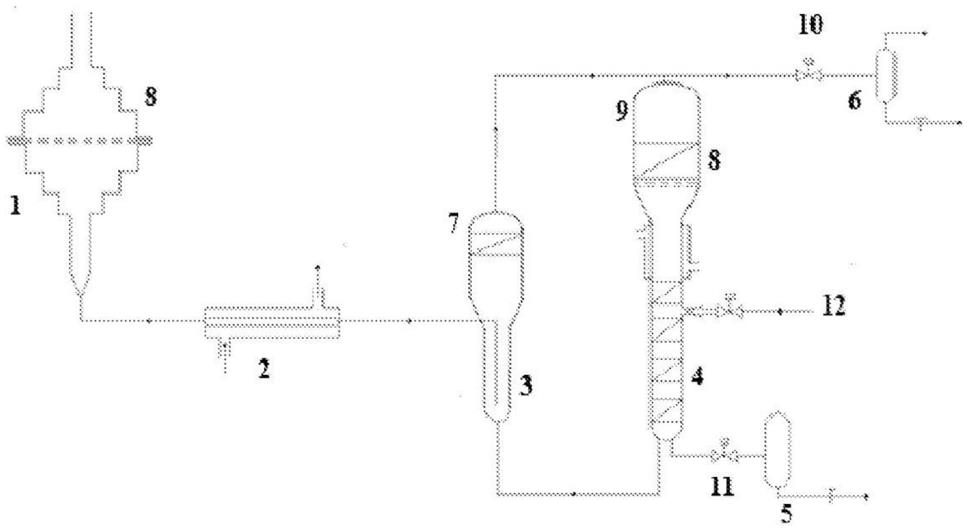
1.本发明涉及使用新方法强化二烷基醚的合成,所述新方法包括与精制反应蒸馏单元偶联的逐级锥形固定床反应器。具体而言,本发明涉及通过使用集成有蒸馏偶联锥形精制反应器的锥形固定床反应器由甲醇脱水合成二甲醚的强化方法。
背景技术:2.目前,空气污染日益严重,需要清洁的替代燃料。近来,正在尝试用有效的化学品和气溶胶推进剂代替氯氟烃(chlorofluorocarbons,cfc)。用于合成这些化学品和气溶胶推进剂的主要原料是二烷基醚,尤其是二甲醚(dimethyl ether,dme),其为lpg替代品用于燃料(非柴油)运输以及发电受到关注。
3.对于大规模基础化学品和中间体的合成,催化固定床反应器是最重要的反应器类型。它主要用于发生在催化剂表面上的非均相催化气体反应,催化剂在这些反应器中布置为所谓的固定床。非均相催化反应器强调催化剂有效性因素和传热传质影响。在固定床反应器中,反应器的圆柱形管中充满反应物和催化剂,这些反应物流过反应器床并转化为所需的产物。催化剂可以有多种配置,包括一个大床、若干水平床、若干平行填充管和多个在其各自壳中的床。根据保持系统内温度控制的需要,可以调整各种配置。
4.甲醇转化为二甲醚的过程是平衡约束反应,高度放热反应,因此应从催化床中导出热量,否则可能导致形成热点,进而导致产品热裂解以及活性反应物的失活,并且由于热量是反应的产物之一,可能会使反应平衡向反应物一侧移动。甲醇脱水得到二甲醚具有限制反应转化率的热力学限制。现有技术中对通过设计该反应的反应器来由甲醇合成二甲醚的所做的努力很少。
5.在期刊“chinese journal of chemical engineering,17(4),630-634,(2009)”发表的作者为m.fazlollahnejad1、m.taghizadeh等的题为《用于甲醇脱水制二甲醚的绝热固定床反应器的实验研究和建模》(experimental study and modeling of an adiabatic fixed-bed reactor for methanol dehydration to dimethyl ether)的文章报道了用于甲醇至二甲醚的催化脱水的一维非均相塞流绝热固定床反应器。该反应器填充有1.5mm-al2o3颗粒作为脱水催化剂,并在大气压下在543-603k的温度范围内运行。
6.2013年8月15日公开的美国专利申请us2013/0211147a1公开了一种非均相催化剂,其允许在较低压力下使合成气有效转化为二甲醚。
7.在期刊“pol.j.chem.tech.,vol.15,no.2,2013”发表的作者为weiyong ying等的题为《通过甲醇气相脱水合成二甲醚的工艺模拟》(“process simulation of dimethyl ether synthesis via methanol vapour phase dehydration”)的文章报道了甲醇在绝热固定床反应器中催化脱水和两塔产品分离的生产过程。二甲醚(dme)合成的这一工艺流程基于甲醇脱水反应的反应动力学模型、改进的液相nrtl模型、气相pr模型的组合参数在pro/ii平台上构建。
8.本领域需要通过设计合适的固定床反应器来解决与选择性、散热、裂解、结焦
(coke formation)以及催化剂失活和反应平衡、流体的高表观速度相关的问题。在传统固定床反应器中,可能难以合适地控制散热,这可能导致低选择性和催化剂失活。
9.需要设计新的方法,使用偶联有后处理单元和精制单元的改进的固定床催化剂用于通过甲醇脱水合成二甲醚,该方法可以提供高催化剂活性、更高的转化率、选择性、催化剂寿命以及原位散热和原位产品移出,这可以节省产品后处理的成本。
10.发明目的
11.本发明的主要目的是提供一种通过使用偶联有精制反蒸馏单元的逐级锥形固定床反应器制备二烷基醚的强化方法。
12.本发明的另一个目的是提供一种锥形固定床反应器,其中反应器直径逐渐增大且具有其他部件如冷凝器、相分离器、蒸馏塔和精制反应器等,从而获得一种制备二烷基醚的强化方法。
13.用于描述本发明的首字母缩略词
14.bpr:背压调节器(back pressure regulator)
15.fbr:固定床反应器(fix bed reactor)
16.whsv:重时空速(weight hourly space velocity)
17.dme:二甲醚(dimethyl ether)
18.gc:气相色谱(gas chromatography)
19.hplc:高效液相色谱(high-performance liquid chromatography)
20.dee:二乙醚(diethyl ether)
技术实现要素:21.因此,本发明提供一种制备二烷基醚的强化方法,所述方法包括以下步骤:
22.在偶联有精制反应器蒸馏单元的逐级锥形固定床反应器中,通过将液体醇注入反应器系统而在如下条件使醇脱水:流速为2.65-8.5ml
·
min-1
且whsv为0.5-1.6h-1
,温度范围为200-260℃,压力为1-10巴;获得二烷基醚,其中所述方法不依赖于于催化剂。
23.在本发明的一个实施方案中,所述二烷基醚为二甲醚或二乙醚。
24.在一个实施方案中,本发明提供一种逐级锥形固定床反应器,包括:
25.i.热交换器(图1,2);
26.ii.相分离器-1(图1,3);
27.iii.反应蒸馏塔(图1,4);
28.iv.液体收集器(图1,5);
29.v.相分离器-2(图1,6);
30.vi.除雾器垫(demister pad)(图1,7);
31.vii.用于催化剂载体的多孔板筛(图1,8);
32.viii.精制催化剂(polishing catalyst)(图1,9);
33.ix.背压调节器(back pressure regulator,bpr)(图1,10);
34.x.液位控制指示器(level control indicator,lcr)(图1,11);和
35.xi.回流入口(图1,12)。
36.在本发明的另一实施方案中,锥形固定床反应器还包括:
37.i.反应物入口(图2,1);
38.ii.冷却水出口(图2,2);和
39.iii.冷却水入口(图2,3)。
40.在本发明的另一个实施方案中,所述逐级锥形固定床反应器包括用于多个反应的多个进料入口。
41.在本发明的另一个实施方案中,所述反应器安装有原位热集成和冷却装置。
42.在本发明的另一个实施方案中,所述反应器提供5-100微米尺寸的催化剂载体筛,以获得期望的背压,从而避免沟流。
43.在本发明的另一个实施方案中,所述反应器以每级从3.3
×
xcm、5.3
×
xcm和7.3
×
xcm分别逐级递增的内径安装,其中x为取决于反应器中装载的催化剂量的比例因子,且所述反应器的逐级锥形布置为10-90
°
的陡角(steep angle)。
44.在本发明的另一个实施方案中,所述反应器提供30-50%更高的反应通量。
45.在本发明的另一个实施方案中,所述反应器用于合成二烷基醚。
附图说明
46.图1描绘反应器设计,其中(1)为反应器;(2)为热交换器;(3)相分离器-1;(4)为反应蒸馏塔;(5)为液体收集器;(6)为相分离器-2;(7)为除雾器垫;(8)为用于催化剂载体的多孔板筛;(9)为精制催化剂;(10)为背压调节器(bpr);(11)为液位控制指示器(lcr);(12)为回流入口。
47.图2示出逐级锥形反应器设计,其中(1)为甲醇入口;(2)为冷却水流出,(3)为冷却水流入。
48.图3示出传统反应器与蒸馏偶联反应器的转化结果比较。
49.图4描绘锥形反应器在不同反应条件下的性能对比图。
50.图5示出锥形反应器与传统反应器性能对比图。
51.图6示出校准气体混合物实际注入gc的情况。
52.图7描绘反应器流出的气体混合物实际注入gc以确认烯烃。
53.图8描绘反应器流出的气体混合物实际注入gc以确认dme的形成和选择性。
54.图9示出逐级锥形反应器的不同视图。
具体实施方式
55.本发明提供一种使用偶联有精制反应蒸馏单元的逐级锥形固定床反应器制备二烷基醚的强化方法。更具体而言,通过甲醇脱水合成二甲醚的方法的强化,其中与传统反应器中的方法相比,该方法的通量提高了至少30-50%,不依赖于催化剂。
56.在本发明中,偶联有精制反应精馏单元的锥形固定床反应器设定为,通过甲醇在脱水剂的存在下脱水进行的二甲醚的高度依赖温度的放热合成。使用锥形固定床分离器进行原位产品分离、加热和加压一体化,解决了平衡约束问题,且反应平衡可以移向产品一侧。传统的反应器工艺存在选择性、散热、裂解、结焦和催化剂失活、流体的高表观速度等问题,这些问题通过锥形固定床反应器的新装置得到解决。
57.本发明提供一种锥形固定床反应器,其中反应器直径逐渐增大,其他部件如冷凝
器、相分离器、蒸馏塔和精制反应器等示于图1。
58.一种制备二烷基醚的强化方法包括,在偶联有精制反应器蒸馏单元的逐级锥形固定床反应器中,通过将液体醇注入反应器系统而在如下条件使醇脱水:流速为2.65-8.5ml
·
min-1
且whsv为0.5-1.6h-1
,温度范围为200-260℃,压力为1-10巴。
59.在本发明的一个实施方案中,所述二烷基醚为二甲醚或二乙醚。
60.二甲醚的制备方法涉及甲醇在脱水剂的存在下脱水,所述脱水剂为二醇,如乙二醇(ethylene glycol,eg)、二甘醇(diethyleneglycol,deg)、三甘醇(triethylene glycol,teg)和四甘醇(tetraethylene glycol,t4eg),和硫酸、用于催化活性的浓磷酸,并且上述方法与选择性、散热、裂解、结焦和催化剂失活等问题相关。通过使用新设计的锥形固定床分离器进行原位产品分离、加热和加压一体化,解决了与平衡约束相关的问题,反应平衡可以移向产品一侧。还可以通过避免裂解来提高催化剂寿命。
61.当催化剂装入固定床反应器时,反应发生在催化剂的初始层。反应过程中会形成水,这会影响催化剂下面的层,使催化剂下面的层无法使用,这是因为水会与甲醇竞争而吸附在催化剂的活性位点上。水限制进入的大量新鲜甲醇在催化剂表面上的为进行反应的吸附,从而通过稀释进入的反应物甲醇而使方法的输出降低。
62.因此,在特别优选的实施方案中,一种制备二烷基醚且特别是二甲醚和二乙醚的方法通过使用锥形固定床反应器得到强化,所述锥形固定床反应器的反应器直径根据反应物/产物特性而以步进角(step angle)10-90
°
逐级增加,如图1所示。
63.在一个实施方案中,本发明提供一种逐级锥形固定床反应器,包括:
64.i.热交换器(图1,2);
65.ii.相分离器-1(图1,3);
66.iii.反应蒸馏塔(图1,4);
67.iv.液体收集器(图1,5);
68.v.相分离器-2(图1,6);
69.vi.除雾器垫(图1,7);
70.vii.用于催化剂载体的多孔板筛(图1,8);
71.viii.精制催化剂(图1,9);
72.ix.背压调节器(bpr)(图1,10);
73.x.液位控制指示器(lcr)(图1,11);和
74.xi.回流入口(图1,12)。
75.在本发明的另一实施方案中,锥形固定床反应器还包括:
76.i.反应物入口(图2,1);
77.ii.冷却水出口(图2,2);和
78.iii.冷却水入口(图2,3)。
79.在本发明的另一个实施方案中,所述逐级锥形固定床反应器包括用于多个反应的多个进料入口。
80.在本发明的另一个实施方案中,所述反应器安装有原位热集成和冷却装置。
81.在本发明的另一个实施方案中,提供用于制备二烷基醚的强化方法的反应器组,包括锥形固定床反应器,所述锥形固定床反应器内径分别以1.3
×
x、3.3
×
x cm、5.3
×
x cm
和7.3
×
x cm每级逐渐增加,其中x为取决于反应器中装载的催化剂量的比例因子。逐级锥形反应器有利于改变各级反应器的直径,这有助于保持反应器内的表观速度并保持陡角10-90
°
,取决于反应类型、反应物性质和产生静压恢复的产物的性质、催化剂床上合适的热量分布、夹带质量通量率,并且有助于最大化反应通量。本文中举例说明的逐级锥形反应器提供的反应器直径范围为1.3厘米(催化剂床入口)至7.3厘米(催化剂床出口),这为新进料提供了最大的催化剂表面,并有助于避免催化剂床中的热点。反应器可以提供多个进料入口,提高了使用多种反应物进入反应器的灵活性。多个进料入口和冷却盘管有助于产品气体的原位冷却,这有助于避免催化剂表面出现热点和裂解,从而延长催化剂寿命。提供5-100微米的筛网尺寸,以提供所需的背压来支撑催化剂,从而避免反应物形成沟流。在一个实施方案中,逐级锥形固定床反应器提供有避免热点形成的冷喷射或骤冷装置。
82.在本发明的另一个实施方案中,该方法提供一组有助于提高脱水/放热反应产率的反应器的新反应器。逐级锥形反应器进一步与相分离器连接,其中通过使用中间冷却器保持相分离器底部的适当温度,使二甲醚从三元反应器出口流中移出,。留在相分离器底部的液体主要含有未反应的反应物(甲醇)和副产物(水),其在此处的反应精馏塔的再沸器中进一步蒸馏,且甲醇在气相中分离出来并在精馏段通过回流新鲜甲醇进一步纯化。甲醇蒸汽在未冷凝的情况下进一步进入精制催化剂区,在精制催化剂区进一步反应形成二甲醚和水,从而节省了冷凝、回收和再次蒸发甲醇的能量。本发明的化学工艺通过使用新的反应器组提供了一些独特的特征,例如产品的原位分离、更高的产率、方法的高通量以及具有能量和成本节约的热集成。
83.在本发明的另一实施方案中,所述反应器用于合成二烷基醚。
84.新的锥形固定床反应器组使二甲醚制备过程的通量提高了30-50%,这是因为所述反应器组允许新鲜甲醇与催化剂最大程度地接触并吸附在催化剂的最大可用表面积上以增加二甲醚的形成。二甲醚是一种蒸气密度非常低的气体,其增加了通过催化剂床流入的流体的超表面速度,从而最大限度地减少了反应物的停留时间。因此,增加反应器的直径以降低速度。一种新的逐级锥形固定床反应器组还减少了放热反应过程中形成的热点,这是因为其借助原位冷却盘管提供了适当的热通量。在蒸馏反应器和冷凝器之后,反应器进一步连接到在10巴下运行的相分离器。二甲醚蒸气、水和甲醇的混合物在原位分离,未转化的甲醇再次通过反应蒸馏塔中的催化剂床以提高通量。
85.在后期分离二甲醚可提供更好的选择性、纯度和能耗降低。同时,甲醇也不会冷凝,这在提供高转化率的情况下节省能源。该方法在260-265℃的反应器中进行,用于选择性合成二甲醚,这与报道和已知的工艺相比非常低,并且反应温度可在常压下提高至400-450℃用于烯烃合成。
86.图1描述反应器设计图,下面给出的不同数字指代不同的部分,图2描述具有用数字编号的逐级锥形模型的锥形反应器。传统反应器与蒸馏偶联反应器的转化率结果的比较如图3所示。性能曲线显示,使用传统固定床反应器(fix bed reactor,fbr),在10巴压力和265℃反应温度下,在重时空速(weight hourly space velocity,whsv)下,转化率为约80%。而在相同反应条件下,蒸馏偶联精制单元的转化率高达88%。
87.锥形反应器在不同反应条件下的性能对比图如图4所示。对比曲线显示,在1巴、1.5的whsv、267℃下,锥形反应器的转化率为约88%,而在1.3的whsv下,使用传统固定床催
化剂实现了相同的转化率。结果表明,通过反应器改进,反应器通量提高了15%。当反应器进一步与蒸馏偶联精制反应器偶联时,在10巴的压力下可以实现相同的转化率,而传统反应器的转化率为约80%。这些结果表明,通过改进反应器,在10巴下反应器通量增加了约30%。
88.锥形反应器与传统反应器的性能对比图如图5所示。转化率图显示,与传统反应器相比,新设计的反应器在各whsv下提供了更高的转化率,这证明锥形反应器的性能优于传统反应器。
89.图6示出校准气体混合物实际注入gc的情况。在使用gc和chromeleon 7软件进行分析后,校准气体混合物的实际注入显示了相同的已知组分。
90.图7描述反应器流出的气体混合物实际注入gc以确认烯烃的过程。反应器出口气体的实际注入符合烯烃(c2、c3)的形成,使用该催化剂,在400-450℃、大气压下,可通过调整催化剂组成和反应条件进一步提高催化剂对烯烃的选择性。
91.图8描述反应器出口气体的实际注入与dme的形成一致,并且没有观察到其他副产物,这表明,使用该催化剂,在260-265℃、大气压下,对dme的选择性为100%。
92.一般信息
93.系统的压力通过施加背压调节器来调节。反应器炉具有表面加热区,且表面加热区的温度由装有pid(比例、积分和微分(proportional,integral,and derivative))控制器的电夹套设定到预定温度,精度为
±
0.5℃。氩气用作载气,以提供所需的压力,并用于产生所需的甲醇分压。氩气的流速由质量流量控制器控制。液态甲醇,其随后在炉的预热区蒸发并以气态与氩气混合,且通过推料泵注入系统。反应器输出流在通过双管换热器后进入两相分离器。
94.反应器流出的气体使用装有tcd检测器、0.53mm
×
30m hp-plot q毛细管柱的在线气相色谱进行每60分钟至180分钟的分析,以氩气作为载气,且冷凝的甲醇-水液体样品还使用hplc分析。为了更好地了解催化剂的性能,将气体样品注入在线气相色谱,并使用chromeleon 7软件分析获得的数据图,其中已注入以下组分的校准气体混合物。
95.气体ppm体积%co3.5235210.4甲醇1.0802882.79氢0.66259627.38dme16.63979329.85co22.5501964.79甲烷0.9467044.89乙烷1.789594.93乙烯1.6736724.94丙烷2.6460284.97丙烯2.5460825.01
96.实施例
97.以下实施例以说明方式给出,因此不应解释为限制本发明的范围。
98.实施例1:在锥形反应器中合成二甲醚
99.将150g合成催化剂样品装入固定床锥形反应器中,并将100g催化剂装入精制反应器单元中。首先,催化剂在氮气和氧气的存在下在50cm3·
min-1
的流速、以3℃/min的升温速率在350-650℃的温度下活化12小时。然后催化剂床冷却至260℃,接着停止氮气和气流。待温度稳定后,将液态甲醇以8.5ml
·
min-1
的流速注入反应器并停止载气流。其中以1ml/min注入甲醇作为反应蒸馏塔中的回流。反应器中的甲醇分压和whsv分别为1个大气压和0.5h-1
。反应温度设定为260℃,压力为10巴,用于选择性dme合成。转化率为88%,且dme的选择性为99.3%。
100.实施例2:在锥形反应器中合成二甲醚
101.将150g合成催化剂样品装入固定床锥形反应器中,并将100g催化剂装入精制反应器单元中。首先,催化剂在氮气和氧气的存在下在50cm3·
min-1
的流速、以3℃/min的升温速率在350-650℃的温度下活化12小时。然后催化剂床冷却至260℃,接着停止氮气和气流。待温度稳定后,将液态甲醇以8.5ml
·
min-1
的流速注入反应器并停止载气流。其中以1ml/min注入甲醇作为反应蒸馏塔中的回流。反应器中的甲醇分压和whsv分别为1个大气压和1.6h-1
。反应温度设定为260℃,压力为10巴,用于选择性dme合成。转化率为85%,且dme的选择性为99.8%。
102.烯烃合成在常压下反应温度可提高到450℃。
103.系统的压力通过施加背压调节器来调节。反应器炉具有表面加热区,表面加热区的温度由配备有pid控制器的电夹套设定到预定温度,精度为
±
0.5℃。氩气用作载气以提供所需的压力并产生所需的甲醇分压。氩气的流速由质量流量控制器控制。液态甲醇随后在炉的预热区蒸发并以气态与氩气混合,且通过推料泵注入系统。反应器输出流通过双管换热器后进入两相分离器。
104.实施例3:在锥形反应器中合成二乙醚
105.将150g合成催化剂样品装入固定床锥形反应器中,并将100g催化剂装入精制反应器单元中。首先,催化剂在氮气和氧气的存在下在50-500cm3·
min-1
的流速、以3℃/min的升温速率在350-650℃的温度下活化12小时。然后催化剂床冷却至275℃,接着停止氮气和气流。待温度稳定后,将液态甲醇以8.5ml
·
min-1
的流速注入反应器并停止载气流。其中以1ml/min注入甲醇作为反应蒸馏塔中的回流。反应器中的甲醇分压和whsv分别为1个大气压和0.5h-1
。反应温度设定为275℃,压力为1巴,用于选择性dee合成。转化率为84%,且dee的选择性为93%。
106.实施例4:在锥形反应器中合成二乙醚
107.将150g合成催化剂样品装入固定床锥形反应器中,并将100g催化剂装入精制反应器单元中。首先,催化剂在氮气和氧气的存在下在50-500cm3·
min-1
的流速、以3℃/min的升温速率在350-650℃的温度下活化12小时。然后催化剂床冷却至275℃,接着停止氮气和气流。待温度稳定后,将液态甲醇以8.5ml
·
min-1
的流速注入反应器并停止载气流。其中以1ml/min注入甲醇作为反应蒸馏塔中的回流。反应器中的甲醇分压和whsv分别为1个大气压和1.6h-1
。反应温度设定为275℃,压力为1巴,用于选择性dee合成。转化率为75%,且dee的选择性为96.0%。
108.实施例5:
109.两相分离器:在分离器中分离液体和气体
110.固定床反应器的流出物进一步送入相分离器,在相分离器,甲醇和水在10巴的压力和120℃下冷凝。二甲醚/二乙醚通过背压调节器(bpr)以未冷凝气体排出。甲醇/乙醇和水的冷凝混合物在分离器底部形成液面。分离器的底部温度保持在120℃,以保持二甲醚/二乙醚处于气相。
111.偶联有精制反应器单元的精馏装置
112.冷凝的甲醇/乙醇和水混合物在u形回路中形成液位,所述u形回路连接相分离器至偶联有精制反应器的蒸馏装置,其中底部温度保持在150-170℃,使得甲醇/乙醇将在此蒸发。气相甲醇/乙醇在催化剂区在260℃和10巴压力下进一步反应,得到二甲醚/二乙醚。部分甲醇/乙醇与水或新鲜甲醇/乙醇的冷凝混合物可用作回流,以确保到达精制催化剂床的甲醇/乙醇蒸气的纯度。
113.本发明的有益效果
114.·
新的反应器组提高了催化剂的活性和持久性,因为该设计有助于消除热点。
115.·
由于反应器组的改进设计,反应器方法提供了更高的转化率(90-92%),这是因为分离单元的设计和布置有助于移除形成的产品。
116.·
反应器和方法的改进设计使二甲醚的选择性为100%,无副产物。
117.·
与传统反应器工艺相比,反应通量增加了30%。由于更多的催化剂表面积与新鲜反应物相互作用,逐级锥形设计为通过催化剂床的反应物和产物提供了最佳的表观速度。
118.·
原位连续产品分离可节省产品后处理成本。