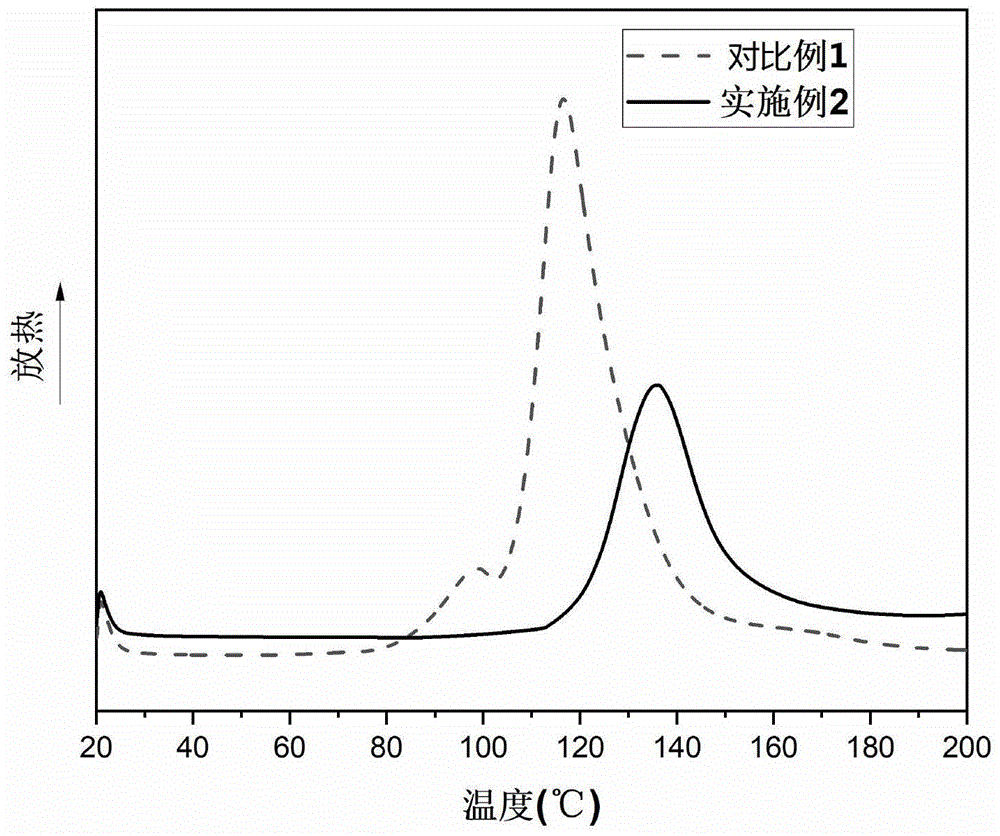
本发明属于有机合成固化剂
技术领域:
,涉及一种环氧树脂固化剂及其制备方法,更具体的说是涉及一种含金属有机框架mofs-咪唑类化合物复合体系的新型环氧树脂潜伏性固化剂及其制备方法。
背景技术:
:环氧树脂是一种应用广泛的热固性树脂,具有良好的电绝缘性、耐化学性、耐磨性、耐高温等优点,现在它已成为涂料、胶粘剂、电气绝缘材料以及复合材料重要的树脂基体。环氧树脂在固化之前为液态或低软化点的物质,其状态随着分子骨架种类和聚合度的大小而不同,使用价值有限。环氧树脂只有经过固化之后,才能形成坚韧的、不溶不熔的聚合物,满足各类应用的需求。环氧树脂中的环氧基团,容易与固化剂发生化学反应,形成三维网状结构,因此环氧树脂的固化过程尤为重要,而固化剂是环氧树脂固化过程中最重要的核心成分,固化剂在固化反应中充当交联点的作用,不同的固化剂对固化工艺和固化产品性能的影响是不同的。环氧树脂固化剂通常可以分为显在性固化剂和潜伏性固化剂,传统的显在性固化剂与环氧树脂组成的是双组分固化体系,存在操作工艺性能差、混合不均匀的缺点,储存稳定性差,混合后会迅速固化,所以固化剂与环氧树脂需要分开储存,使用时现配现用。而潜伏性固化剂在与环氧树脂混合后,组成物储存期长,在一般条件下,不会发生或者很难发生固化反应,但一旦受热、光、湿气或压力等外界条件作用下能迅速固化,具有很好的可控性和稳定性。因此,研发一种含金属有机框架mofs-咪唑类化合物复合体系的新型环氧树脂潜伏性固化剂及其制备方法是本领域技术人员亟需解决的问题。技术实现要素:有鉴于此,本发明提供了一种含金属有机框架mofs-咪唑类化合物复合体系的新型环氧树脂潜伏性固化剂及其制备方法。为了实现上述目的,本发明采用如下技术方案:一种环氧树脂固化剂,由含过渡金属的盐与咪唑类化合物以摩尔比为1:(2-5)制得。本发明的有益效果:1.本发明固化剂中的部分咪唑类化合物被填充在mofs材料的多孔结构内,可以在热量的作用下释放出来,在常温下为粘稠态胶体,粘度大,不易流动,储存运输方便;需要使用时只需要在70-130℃下持续加热至液体,即可在环氧树脂中充分分散,混合固化使用,而且与粉末状固化剂相比,胶状液体的固化剂在环氧树脂中分散更为均匀,固化效果更加优异。2.本发明的新型潜伏性固化剂可以改变金属盐与咪唑类化合物的比例,调整其固化环氧树脂的温度与速率。也就是说,这种含mofs-咪唑类化合物复合体系的新型潜伏性固化剂适用于各个温度,应用范围广,制备简单。进一步,上述含过渡金属的盐为醋酸锌或氯化钴。进一步,上述咪唑类化合物为2-甲基咪唑或2-乙基咪唑。采用上述进一步的有益效果:本发明选择上述过渡金属离子较为活泼,容易与咪唑类化合物中的氮原子形成稳定的配位化合物,在室温下具有很长的适用期。咪唑类化合物分子结构中含有仲胺活泼氢原子,本身可以作环氧树脂中温固化剂,其分子中同时存在叔胺氮原子,也可以作为环氧树脂体系中的促进剂。本发明还提供一种环氧树脂固化剂的制备方法,包括以下步骤:(1)按照上述环氧树脂固化剂称取各原料;(2)将含过渡金属的盐与咪唑类化合物研磨成粉末;(3)将含过渡金属的盐与咪唑类化合物搅拌混合,得混合物;(4)将所得混合物加热反应,得到上述环氧树脂固化剂。本发明的有益效果:本发明制备方法为固相反应加热法,该合成方法工艺简单、条件温和且对环境友好,绿色环保。最重要的是,制备过程中没有产生废液,不需要进行废液处理,成本低。进一步,步骤(2)中,上述粉末粒径为22-28μm。采用上述进一步的有益效果:粒径合适的粉末能更加迅速的发生反应,减少反应时间,降低生产成本。进一步,步骤(3)中,上述搅拌转速为400-800r/min,搅拌时间为20-40min。采用上述进一步的有益效果:合适的搅拌速度能使两种粉末均匀混合,且粉末又不会飞溅。进一步,步骤(4)中,上述加热温度为70-130℃,加热反应时间为40-90min。采用上述进一步的有益效果:合适的温度和加热反应时间,能使反应物反应充分,没有原料残留且不会因为温度过高发生副反应。附图说明图1是以实施例2制得的固化剂与环氧树脂混合固化后得到的环氧树脂和以对比例1制得的固化剂与环氧树脂混合固化后得到的环氧树脂的dsc曲线,升温速率为10℃/min。图2是以实施例1-3制得的固化剂与环氧树脂混合固化后得到的环氧树脂测得的dsc曲线1-3。图3以实施例1-3和对比例1制得的固化剂与环氧树脂混合固化后得到的环氧树脂测得的tga曲线。图4以实施例1、实施例6和对比例1制得的固化剂与环氧树脂混合固化后得到的环氧树脂测得的tga曲线。具体实施方式下面将对本发明实施例中的技术方案进行清楚、完整地描述,显然,所描述的实施例仅仅是本发明一部分实施例,而不是全部的实施例。基于本发明中的实施例,本领域普通技术人员在没有做出创造性劳动前提下所获得的所有其他实施例,都属于本发明保护的范围。请补充以下内容:实施例1环氧树脂固化剂的制备方法,包括以下步骤:(1)称取醋酸锌18.3g,2-甲基咪唑20.5g;(2)将醋酸锌与2-甲基咪唑研磨成粒径为25μm的粉末;(3)将醋酸锌与2-甲基咪唑搅拌混合,搅拌转速为700r/min,搅拌时间为30min,得混合物;(4)将所得混合物加热反应,加热温度为130℃,加热反应时间为60min,得到环氧树脂固化剂;(5)将所得环氧树脂固化剂与环氧树脂进行搅拌混合,两者质量比为1:6,搅拌转速为900r/min,搅拌时间为30min。实施例2环氧树脂固化剂的制备方法,包括以下步骤:(1)称取醋酸锌18.3g,2-甲基咪唑24.6g;(2)将醋酸锌与2-甲基咪唑研磨成粒径为25μm的粉末;(3)将醋酸锌与2-甲基咪唑搅拌混合,搅拌转速为700r/min,搅拌时间为30min,得混合物;(4)将所得混合物加热反应,加热温度为130℃,加热反应时间为60min,得到环氧树脂固化剂;(5)将所得环氧树脂固化剂与环氧树脂进行搅拌混合,两者质量比为1:6,搅拌转速为900r/min,搅拌时间为30min。实施例3环氧树脂固化剂的制备方法,包括以下步骤:(1)称取醋酸锌18.3g,2-甲基咪唑28.7g;(2)将醋酸锌与2-甲基咪唑研磨成粒径为25μm的粉末;(3)将醋酸锌与2-甲基咪唑搅拌混合,搅拌转速为700r/min,搅拌时间为30min,得混合物;(4)将所得混合物加热反应,加热温度为130℃,加热反应时间为60min,得到环氧树脂固化剂;(5)将所得环氧树脂固化剂与环氧树脂进行搅拌混合,两者质量比为1:6,搅拌转速为900r/min,搅拌时间为30min。实施例4环氧树脂固化剂的制备方法,包括以下步骤:(1)称取醋酸锌18.3g,2-甲基咪唑41.0g;(2)将醋酸锌与2-甲基咪唑研磨成粒径为22μm的粉末;(3)将醋酸锌与2-甲基咪唑搅拌混合,搅拌转速为400r/min,搅拌时间为20min,得混合物;(4)将所得混合物加热反应,加热温度为70℃,加热反应时间为40min,得到环氧树脂固化剂。实施例5环氧树脂固化剂的制备方法,包括以下步骤:(1)称取醋酸锌18.3g,2-乙基咪唑28.8g;(2)将醋酸锌与2-乙基咪唑研磨成粒径为23μm的粉末;(3)将醋酸锌与2-乙基咪唑搅拌混合,搅拌转速为500r/min,搅拌时间为25min,得混合物;(4)将所得混合物加热反应,加热温度为80℃,加热反应时间为50min,得到环氧树脂固化剂。实施例6环氧树脂固化剂的制备方法,包括以下步骤:(1)称取氯化钴13.0g,2-甲基咪唑24.6g;(2)将氯化钴与2-甲基咪唑研磨成粒径为25μm的粉末;(3)将氯化钴与2-甲基咪唑搅拌混合,搅拌转速为600r/min,搅拌时间为30min,得混合物;(4)将所得混合物加热反应,加热温度为90℃,加热反应时间为60min,得到环氧树脂固化剂。实施例7环氧树脂固化剂的制备方法,包括以下步骤:(1)称取氯化钴13.0g,2-乙基咪唑28.8g;(2)将氯化钴与2-乙基咪唑研磨成粒径为26μm的粉末;(3)将氯化钴与2-乙基咪唑搅拌混合,搅拌转速为800r/min,搅拌时间为40min,得混合物;(4)将所得混合物加热反应,加热温度为130℃,加热反应时间为90min,得到环氧树脂固化剂。对比例1(1)称取2-甲基咪唑4.1g;(2)将2-甲基咪唑研磨成粒径为25μm的粉末,得到环氧树脂固化剂;(3)将2-甲基咪唑粉末与环氧树脂进行搅拌混合,两者质量比为1:6,搅拌转速为900r/min,搅拌时间为30min。图1是以实施例2制得的固化剂与环氧树脂混合固化后得到的环氧树脂和以对比例1制得的固化剂与环氧树脂混合固化后得到的环氧树脂的dsc曲线,升温速率为10℃/min。由图1可知,对比例1的固化温度虽然较低,但是在制备过程中,其固化剂与环氧树脂没有充分混合,还有2-甲基咪唑颗粒残留,分散不均匀;而本发明的固化剂与环氧树脂混合充分,不存在明显分层,固化温度明显。图2是以实施例1-3制得的固化剂与环氧树脂混合固化后得到的环氧树脂测得的dsc曲线1-3。由图2可知,三条曲线的固化温度各不相同,原因是环氧树脂混合物中的固化剂不同,即醋酸锌与2-甲基咪唑比例不同,同时也体现了本发明的固化剂可以调整固化温度。图3以实施例1-3和对比例1制得的固化剂与环氧树脂混合固化后得到的环氧树脂测得的tga曲线。由图3可知,本发明固化剂的环氧树脂体系和咪唑化合物固化剂的环氧树脂体系的分解曲线相似。但是,测试结束后剩余的残留物质表明:本发明的固化剂中存在金属-有机框架(mofs)。图4以实施例1、实施例6和对比例1制得的固化剂与环氧树脂混合固化后得到的环氧树脂测得的tga曲线。由图4可知,过渡金属钴盐也适用于本发明的环氧树脂固化剂制备方法。表1是对比了实施例1-3,对比例1制得的固化剂与环氧树脂制得混合物的dsc测试中的起始温度(ti)、峰值温度(tp)、终止温度(tf)。表1由表1可知,在相同温度、湿度、压力等外部条件下,咪唑类化合物固化剂的反应起始温度ti低,表明在低温下的固化反应活性高,导致储存稳定性差;而本发明的反应起始温度ti较高,在高温下的固化反应活性高,在室温下的储存稳定性良好。表2为实施例1-3,对比例1固化剂与环氧树脂混合后在各个温度下的凝胶时间。表2凝胶化温度(℃)4050608090100实施例1凝胶时间(h)85.548.613.44.52.40.9实施例2凝胶时间(h)80.345.412.13.72.20.7实施例3凝胶时间(h)73.237.67.91.81.20.5对比例1凝胶时间(min)230.0120.060.020.09.05.0表3为实施例1-3,对比例1固化剂与环氧树脂混合后在各个温度下的固化时间。表3固化温度(℃)110120130140150实施例1固化时间(min)140100805535实施例2固化时间(min)11587684525实施例3固化时间(min)10076573420对比例1固化时间(min)6855342515由表2-3可知,在相同温度、湿度、压力等外部条件下,咪唑类化合物固化剂的稳定性较差,反应活性高,容易发生凝胶化现象,固化时间短。而本发明的固化剂的稳定性较好,适应性强,固化时间相对较长。对所公开的实施例的说明,使本领域专业技术人员能够实现或使用本发明。对这些实施例的多种修改对本领域的专业技术人员来说将是显而易见的,本文中所定义的一般原理可以在不脱离本发明的精神或范围的情况下,在其它实施例中实现。因此,本发明将不会被限制于本文所示的这些实施例,而是要符合与本文所公开的原理和新颖特点相一致的最宽的范围。当前第1页12