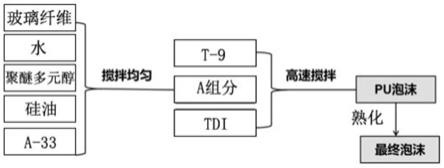
1.本发明属于生物除臭领域,更具体地,涉及一种复合聚氨酯填料及制备方法和应用。
背景技术:2.生物除臭填料的开发在一定程度上决定着常用除臭技术的升级换代。生物除臭滤池所用填料一般选取含纤维物质如树皮、干草、炭质等填料,从而形成一种有利于透气的疏松结构,为微生物提供适当的生存环境。但是,此类单一填料的生物滤池在运行一段时间后常产生透气性变差、填料堵塞等问题,其一般使用寿命仅为3
‑
5年。多数生物滤池除臭技术的研究主要集中于混合填料的开发,如屈艳芬等采用以混合肥料、沸石、有机料聚成的复合有机填料进行除臭试验,取得了良好的效果。除了传统天然填料外,聚氨酯泡沫以其成本低廉、密度小、开孔率高、泡孔尺寸可调、比表面积大等优势,引起了学术界的关注。daniel dobslaw等将聚氨酯填料应用在生物滴滤器中去除高挥发性有机物(voc)。张颖等利用其高吸附性能对大气进行吸附性研究。胡永彪等利用聚氨酯泡沫大气被动采样技术对北京部分区域进行气体采集。
3.因此,针对目前在生物除臭滤池中,树皮、干草等填料在运行一段时间后常产生透气性变差、填料堵塞、其一般使用寿命仅为3
‑
5年等问题,以及针对炭质填料存在成本高昂(约2000
‑
3000元/m3)、可燃烧、废炭处理困难等问题,亟待开发出新型的生物除臭用填料。
技术实现要素:4.本发明的目的是针对现有技术的不足,提出一种复合聚氨酯填料及制备方法和应用。本发明的复合聚氨酯填料开发成本低廉、泡孔尺寸可调、比表面积大。
5.为了实现上述目的,本发明第一方面提供了一种复合聚氨酯填料,该复合聚氨酯填料包括以重量份计的以下组分:a组分300
‑
400份、催化剂t
‑
9 0.3
‑
0.5份和甲苯二异氰酸酯150
‑
180份;其中,所述a组分包括以重量份计的以下组分:结构增强型填料10
‑
15份、水15
‑
20份、聚醚多元醇200
‑
400份、硅油2
‑
5份和催化剂三乙醇胺a
‑
33 0.3
‑
0.5份。
6.在本发明中,作为优选方案,所述水为去离子水。
7.根据本发明,优选地,所述结构增强型填料为玻璃纤维、甘蔗纤维和木质纤维中的至少一种,优选为玻璃纤维,进一步优选地,所述玻璃纤维的长度为1.5
‑
9mm。
8.在本发明中,所述催化剂三乙醇胺a
‑
33为本领域技术人员公知的用于制备聚氨酯的催化剂。
9.根据本发明,优选地,所述复合聚氨酯填料的孔隙率大于等于95%。
10.根据本发明,优选地,所述复合聚氨酯填料的泡孔直径为1
‑
1.3mm。
11.根据本发明,优选地,所述复合聚氨酯填料的压缩强度大于等于4.5kpa。
12.根据本发明,优选地,所述复合聚氨酯填料的泡沫密度为20
‑
40kg/m3。
13.本发明第二方面提供了所述的复合聚氨酯填料的制备方法,该方法包括如下步
骤:
14.s1:将所述结构增强型填料、水、聚醚多元醇、硅油和催化剂三乙醇胺a
‑
33混合搅拌均匀,得到所述a组分;
15.s2:将所述a组分、所述催化剂t
‑
9和所述甲苯二异氰酸酯混合搅拌均匀,并依次进行发泡和熟化处理,得到所述复合聚氨酯填料。
16.在本发明中,经过熟化处理得到的所述复合聚氨酯填料为聚氨酯软泡。
17.在本发明中,所述发泡处理所用的设备为本领域技术人员公知的用于使聚氨酯发泡的设备。
18.根据本发明,优选地,步骤s1的混合搅拌的速率为300
‑
400r/min。
19.根据本发明,优选地,步骤s2的混合搅拌的速率为600
‑
1000r/min。
20.根据本发明,优选地,所述熟化处理的条件包括:熟化温度为70
‑
90℃,熟化时间为10
‑
20min。
21.本发明第三方面提供了所述的复合聚氨酯填料在生物除臭中的应用。
22.根据本发明,优选地,进行所述生物除臭的设备包括生物滴滤塔。
23.本发明的技术方案具有如下有益效果:
24.(1)本发明的复合聚氨酯填料具有表面亲水性和表面正电性,可放在生物滴滤塔中进行生物除臭,本发明的复合聚氨酯填料的除臭效率随着臭气中硫化氢和氨的浓度的增加而提高,在高负荷区平均去除率可达94%和77%以上。
25.(2)本发明的复合聚氨酯填料与炭质填料相比,在硫化氢进气浓度高(高负荷区)时,本发明的复合聚氨酯填料具有较明显的除臭效果。且与炭质填料对比,本发明的复合聚氨酯填料成本降低25%
‑
35%,密度降低90%,减少了反应器内部结构强度要求。
26.本发明的其它特征和优点将在随后具体实施方式部分予以详细说明。
附图说明
27.通过结合附图对本发明示例性实施方式进行更详细的描述,本发明的上述以及其它目的、特征和优势将变得更加明显。
28.图1示出了本发明的一种复合聚氨酯填料的制备方法的工艺流程示意图。
具体实施方式
29.下面将更详细地描述本发明的优选实施方式。虽然以下描述了本发明的优选实施方式,然而应该理解,可以以各种形式实现本发明而不应被这里阐述的实施方式所限制。相反,提供这些实施方式是为了使本发明更加透彻和完整,并且能够将本发明的范围完整地传达给本领域的技术人员。
30.实施例1
31.本实施例提供一种复合聚氨酯填料,该复合聚氨酯填料包括以重量份计的以下组分:a组分400份、催化剂t
‑
9 0.45份和甲苯二异氰酸酯170份;其中,所述a组分包括以重量份计的以下组分:3mm玻璃纤维15份、去离子水18份、聚醚多元醇300份、硅油3份、催化剂三乙醇胺a
‑
330.45份。
32.如图1所示,所述的复合聚氨酯填料的制备方法包括如下步骤:
33.s1:将所述玻璃纤维、去离子水、聚醚多元醇、硅油、催化剂三乙醇胺a
‑
33混合搅拌均匀,得到所述a组分;混合搅拌的速率为400r/min;
34.s2:将所述a组分、所述催化剂t
‑
9和所述甲苯二异氰酸酯混合搅拌均匀,并依次进行发泡和熟化处理,得到所述复合聚氨酯填料。混合搅拌的速率为1000r/min;熟化温度为80℃,熟化时间为15min。
35.实施例2
36.本实施例提供一种复合聚氨酯填料,本实施例与实施例1的区别仅在于玻璃纤维的长度为4.5mm。
37.实施例3
38.本实施例提供一种复合聚氨酯填料,本实施例与实施例1的区别仅在于玻璃纤维的长度为9mm。
39.测试例1
40.将实施例1
‑
3的复合聚氨酯填料进行压缩强度性能表征,测定方法如下:
41.采用cmt 6104微机控制电子万能试验机装置进行压缩测试,测试标准为gb/t 8813
‑
2008。将泡沫切成50mm
×
50mm
×
50mm的立方体,压缩实验速率为厚度的10%(5mm/min),压缩强度为泡沫相对形变为10%时的压缩力除以横截面的初始面积所得到的商。每组测量的泡沫试样个数不少于5个,取其平均值为复合聚氨酯填料的压缩强度。
42.测试结果如下:
43.玻璃纤维长度在3mm、4.5mm和9mm时复合聚氨酯填料的压缩强度分别为4.8kpa、3kpa和3.1kpa;随着玻璃纤维长度的增加,在发泡过程中容易刺穿泡孔壁,泡坏了泡孔结构造成压缩强度下降;当玻璃纤维长度继续增大时,在搅拌发泡过程中发生缠结,使得发泡倍率降低,压缩强度增大。
44.玻璃纤维长度为3.0mm时对应的压缩强度较高;玻璃纤维长度过长会刺破泡孔壁而影响泡孔结构,而且极易发生缠结现象影响发泡。因此,选择玻璃纤维最佳长度为3.0mm。
45.测试例2
46.将实施例1
‑
3的复合聚氨酯填料进行挂膜量测定,测定方法如下:取6个边长为2cm的复合聚氨酯填料置于60℃的烘箱中干燥0.5h,称重并记为m0。然后将复合聚氨酯填料浸入到生化池进行挂膜培养,挂膜周期为1个月,最后将复合聚氨酯填料干燥,并称重记为m1。每组实验平行做3次,取平均值。挂膜质量m可由式(1)计算。
47.m=m1‑
m0ꢀꢀꢀꢀꢀꢀꢀꢀꢀꢀꢀꢀꢀꢀꢀꢀꢀꢀꢀꢀꢀꢀꢀꢀꢀꢀ
(1)
48.式中:m为挂膜质量,g;m0为初始复合聚氨酯填料质量,g;m1为挂膜后的复合聚氨酯填料,g。
49.测试结果如下:
50.复合聚氨酯填料的主要作用是为除臭微生物提供适宜生长的环境。在实施例1
‑
3的复合聚氨酯填料中,3mm、4.5mm和9mm玻璃纤维的挂膜质量m分别达到了0.90g/g、0.75g/g和0.80g/g,即玻璃纤维长度为3mm时的复合聚氨酯填料的挂膜性能最佳,其挂膜性能相对于传统炭质填料(0.43g/g传统炭质填料)较优异,可以承载更多的微生物,能充分发挥生物除臭的特性。
51.测试例3
52.将实施例1的复合聚氨酯填料分别切割为边长为2cm的多个正方体,放入内径为0.2m,柱高为2m的生物滴滤塔内。在所述生物滴滤塔内的复合聚氨酯填料的有效高度为0.6m。以热水解污泥臭气和标气混合作为生物滴滤塔恶臭气体的气源,并设置气体在生物滴滤塔内的停留时间为15s。利用微生物分解吸收特性来去除恶臭气体,活性污泥微生物的接种量为0.3m3活性污泥/m3复合聚氨酯填料,接种3次。
53.进行典型恶臭气体的硫化氢和氨的检测,硫化氢检测采用gb 11742
‑
1989进行检测,氨检测采用hj 533
‑
2009进行检测;
54.测试结果如下:
55.在硫化氢进气浓度低负荷区、中负荷区和高负荷区的硫化氢去除率分别平均达到70%、81%和94%以上;硫磺在低负荷区、中负荷区和高负荷区的去除负荷量(单位为:g硫
·
kg
‑1填料
·
d
‑1)分别平均达到0.004、0.017和0.582;而传统炭质填料在高负荷区的硫磺去除负荷量(单位为:g硫
·
kg
‑1填料
·
d
‑1)为0.25。
56.在氨进气浓度低负荷区(2.84mg
·
m
‑3~10.26mg
·
m
‑3)、中负荷区(25.78mg
·
m
‑3~39.76mg
·
m
‑3)和高负荷区(61.26mg
·
m
‑3~88.89mg
·
m
‑3)的氨去除率分别平均达到45%、71%和77%以上。
57.以上已经描述了本发明的各实施例,上述说明是示例性的,并非穷尽性的,并且也不限于所披露的各实施例。在不偏离所说明的各实施例的范围和精神的情况下,对于本技术领域的普通技术人员来说许多修改和变更都是显而易见的。