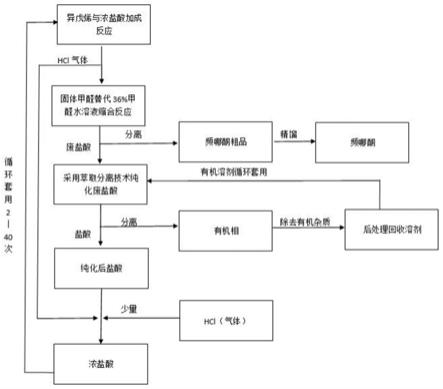
1.本发明属于化工技术领域,具体涉及一种频哪酮制备方法。
背景技术:2.频哪酮是生产农药、医药、染料及生物抑制剂的重要中间体,尤其是在三唑类农药、抗艾滋病毒新药atazanavir、抗真菌药物特比萘芬和抗癫痫药物司替戊醇等产品的生产中发挥巨大作用,应用广泛。目前频哪酮的生产方法主要以异戊烯法为主,以异戊烯为原料与工业盐酸加成反应制备氯代特戊烷,分离后再与甲醛水溶液经过成环、开环、重排三步反应,再经过多次精馏得到频哪酮产品。该方法生产工艺路线长、反应收率低,生产过程中产生大量的焦油杂质和大量危废酸,环境污染严重,造成生产成本较高,且生产的频哪酮产品纯度只有95%左右(gc),难以满足医药产品生产需求;并且目前工业上通常的频哪酮收率只有77%左右,焦油产生量高达19%以上,焦油产生量高既代表了反应选择性差,也造成了前述的各种环保和工艺控制问题(具体参数参见本发明实施例2)。因此,现有技术严重制约了频哪酮产能扩大和行业发展。本专利申请人研究了大量的现有技术,发现目前公开的各类文献仅是表面上生成绿色工艺,但实际上并不能真正解决上述问题。如:
3.发明专利cn109809972a公开了一种绿色制备频哪酮的方法,此发明专利采取的是连续生产法,但是没有从根本上解决杂质焦油的产生,酸水相中会带有大量的褐色杂质焦油,套用后严重影响频哪酮的生产,杂质产品质量下降,杂质焦油不断累加变成精馏釜残,形成危险废物,废酸也会杂质越来越多,无法套用,不能解决废酸排放和杂质焦油排放问题,在实际生产中难以进一步推广。
4.发明专利cn103240094a公开了一种制备频哪酮的工艺及复合性催化剂,所述工艺以氯代特戊烷为原料,选用zn/co/sb复合催化剂,制备频哪酮,该工艺是将频哪酮中间体氯代特戊烷分离后进行的缩合反应,中间体的分离步骤不可避免,且该技术反应时间为4-5h,并未明显缩短反应时间,且产品收率没有明显提高,另外也没有解决频哪酮生产过程产生大量杂质焦油和废弃酸液的环保问题,环保效益并不明显。
5.发明专利cn105503550a公开了一种频哪酮合成的绿色制备方法,所述制备方法采用异戊烯与盐酸反应得到叔戊基氯经分离后,以甲醇或者频哪酮为溶剂与三聚甲醛反应生成频哪酮。以甲醇或者频哪酮为溶剂与三聚甲醛反应避免了盐酸作为溶剂,减少了废酸产生量,但是经研究发现叔戊基氯与甲醛的缩合、成环及重排反应需在酸性溶剂中才可进行,因此采用甲醇或者频哪酮为溶剂反应收率很低,实际应用价值不大,同时甲醇等溶剂额外引入也增加了废弃有机溶剂的排放,频哪酮精馏后反应生成的杂质焦油变成釜残成为有机危废,同时第一步产生的废酸也不能表明无废液产生,仍有废液排放,面临较高的环保成本,没有从根本上解决环保问题。
技术实现要素:6.因此,针对上述问题,有必要对频哪酮现有生产方法进行改进和优化,以提高频哪
酮生产的反应选择性和收率,减少焦油杂质和废酸产生量,提高产品质量,真正做到清洁和绿色生产频哪酮。
7.本发明的一个方面,
8.本发明研发团队在大量的实验研究基础上意外发现在传统异戊烯反应体系中添加一种镧系路易斯酸类催化剂能够或多或少解决焦油杂质的问题,但相较于传统工艺中不添加催化剂或者添加其他种类的催化剂,焦油含量能够显著减少。本发明实施例附图中给出了实验中焦油含量的对比图。
9.本发明研发团队首先选择了单质氯化镧作为催化剂,发现焦油量能够从不添加该催化剂时的19.75%降低至8.23%,该焦油降低效果已经非常惊人;推断可能是因为催化剂大大加快了反应速度,提高了反应选择性,使得聚合物大幅减少;并且,在降低焦油杂质的同时,产物频哪酮的收率和纯度还能同时有所增加,这些都是意料不到的效果。基于此,本发明进行了各种催化剂的选择实验,发现如下几种组配的催化剂均能显著降低焦油杂质含量,并同时能得到优于现有工业应用的高收率和高纯度的频哪酮产品。
10.具体的催化剂组配如下:
11.通常的,催化剂为单用或复配的镧系路易斯酸;所述镧系路易斯酸原则上可以为溴代镧系金属盐,也可以为氯代镧系金属盐,但是因为本发明的频哪酮反应体系选择盐酸为溶剂体系,因此优选氯代镧系金属盐。具体的优选氯化镧,氯化铈,氯化镨,氯化钕,氯化铒,氯化钬,氯化镝或氯化铥。
12.另外,因为镧系氧化物溶于盐酸也形成镧系氯化物,如果在实际工业中更易得到镧系氧化物,其也是可以优选的催化剂。
13.优选的,所述单用的镧系路易斯酸为氯化镧、氯化铈、氯化镨或氯化铷。
14.可选的,复配的镧系路易斯酸为任意两种或多种镧系路易斯酸组合。
15.优选的,所述复配的镧系路易斯酸为氯化镧或氯化铈或氯化镨或氯化铷与其他任一种或多种镧系路易斯酸组合。
16.进一步的,针对复配型催化剂,还需要在大量实验基础上调整其复配比例,不同的复配比例其最终反应效果还是有一定差异。
17.如本发明实施例中给出了复配的镧系路易斯酸中,氯化镧或氯化铈或氯化镨或氯化铷的物质的量与其他任一种复配成分物质的量之和之比为1:10~10:1的范围内反应结果较优,当扩大到1:50~50:1,某些区间反应结果稍差,但均在工业应用的可接受范围内。优选1:5~10:1,或1:3~10:1,或3:1~10:1,或5:1~10:1,更优选的3:1。本发明实施例中给出了各种复配催化剂在不同配比情况下的反应结果。
18.当催化剂选择三种成分的复配镧系路易斯酸时,三种成分的复配摩尔比范围为:1~5:1~3:1~3,更优选的为1~3:1:1,或3:1:1。
19.进一步的,还需要控制催化剂与异戊烯原料的用料比,如催化剂与异戊烯的物质的量的比为5~50:1000是比较优选的范围,具体可优选10~50:1000,20~50:1000,30~50:1000,40~50:1000,20:1000,50:1000。本发明实施例给出了各种优选的催化剂与异戊烯的用料比参数的反应结果。
20.本发明实施例中给出了各种代表性的催化剂组配及配比,从反应结果数据可以明显看出,焦油杂质含量,产物频哪酮收率,纯度等均较现有工艺大大提高。如焦油产生量控
制在12%以下,优选的能控制在10%以下,9%以下,8%以下,7%以下,6%以下,5%以下,4%以下,同时频哪酮产物的收率能控制在80%以上,优选的85%以上,90%以上,频哪酮产物均能达到目前医药品中对频哪酮产品纯度要求的98.50%以上。
21.本发明的另一方面,
22.本发明的频哪酮制备方法,包括异戊烯和盐酸的第一步反应,以及之后的加入催化剂和甲醛进行第二步反应,两步反应为连续反应,实现了一锅式操作,大大提高了工业效率(反应原理如图1所示)。该反应在使用上述催化剂的基础上,焦油量大幅减少;并且因为反应转化率比较高,产物频哪酮的纯度高,一次精馏就能得到理想的反应产物。
23.为了优化反应各种指标,并同时基于各反应物料的特性,如异戊烯的沸点较低,本发明还优化了各项主要反应参数。
24.具体的,第一步反应中,反应温度为0~10℃,反应时间为60~90分钟。
25.具体的,第二步反应中,温度为60~90℃,第二步反应时间为1~6小时。优选的反应温度为80~90℃,优选的反应时间为4~6小时,最优参数为反应温度为83℃,反应时间为4小时。
26.具体的,第二步反应中,甲醛的加入时间为0.5~3小时,优选的加料时间为2~3小时,并且为缓慢滴加。
27.基于上述反应得到的良好效果,本发明为进一步满足实际工业应用中对绿色生产的要求,对反应原料进行了进一步优化,如将甲醛水溶液替换为固体甲醛盐酸溶液。并且经过实验研究,发现固体甲醛与盐酸的质量比为1:5~1:20的浓度范围最优,具体可优选1:5,或1:10。
28.本发明实施例给出了各种优选的固体甲醛盐酸溶液配比参数的反应结果。
29.本发明的另一方面,
30.基于上述各项优化工艺条件,本发明的产物中盐酸溶液中不再含有难以除去的焦油杂质,能够便捷的进行回收利用,如可以直接在原反应体系中循环利用,还能同时减少废酸废水的排放。具体的,在第二步反应后,将反应液冷却至室温,静置分层,上层得到频哪酮产品,下层为盐酸层,下层盐酸可循环套用;循环套用最高可达60次,优选2-40次,当超过60次后,盐酸的纯度已经不能够满足反应的需要,可以做废酸处理。具体的,下层盐酸层采用二氯甲烷或二氯乙烷有机溶剂萃取,经补充氯化氢后循环套用。
31.综上,本发明涉及的一种频哪酮的制备方法,反应过程大大减小了杂质焦油的产生量,使频哪酮收率和纯度大幅提高,显著降低了生产成本,提高了产品质量;并且反应操作步骤简化,工艺相对简单合理。整体上实现了频哪酮的清洁生产,不仅绿色环保,而且经济效益非常可观。
附图说明
32.图1为本发明的频哪酮制备方法的反应原理图;
33.图2为本发明的频哪酮制备方法的工艺流程图;
34.图3为传统工艺技术制备频哪酮过程中的反应液状态图,其中上层透明液为频哪酮溶液,下层为焦油与盐酸的混合液,焦油含量为19%以上;
35.图4为添加本发明某些催化剂制备频哪酮过程中的反应液状态图,焦油含量在5%
以下。(图中的上下层溶液均非常澄清,焦油杂质几乎没有,阴影部分为玻璃瓶反光)
36.图5为实施例2.15中频哪酮产物气相色谱图。
具体实施方式
37.下面将结合本发明实施例中的附图,对本发明实施例中的技术方案进行清楚、完整地描述,显然,所描述的实施例仅是本发明一部分实施例,而不是全部的实施例。基于本发明中的实施例,本领域普通技术人员在没有作出创造性劳动前提下所获得的所有其他实施例,都属于本发明保护的范围。
38.下列实施例中的试剂来源:
39.异戊烯:淄博联碳化学有限公司
40.固体甲醛:淄博齐星化学科技有限公司
41.催化剂:山东德胜新材料有限公司
42.盐酸来源于为本发明申请人工厂的其他产品线副产物,也可以直接外购。
43.下列实施例中的焦油产生量的测定方式:将反应完成之后的液体过滤,离心,对焦油杂质进行称重。
44.实施例1
45.本实施例结合图1,对本发明的一种频哪酮制备方法进行详细描述。
46.在反应釜中投入500kg30%浓度的工业盐酸,降温至0~10℃,搅拌下将160kg预冷至-5℃的异戊烯缓慢滴加进反应釜,0~10℃反应60~90分钟,升温至50℃,加入催化剂,缓慢滴加140kg固体甲醛的盐酸溶液,升温至60~90℃反应1~6小时,冷却至室温,静置分层,上层有机相经过一次精馏得到频哪酮产品;下层盐酸层采用二氯甲烷或二氯乙烷有机溶剂萃取,经补充氯化氢后循环套用(本发明实施例的套用次数为40次)。具体反应原理和反应过程详见附图1和附图2。
47.实施例2
48.按照实施例1的制备方法分别采用无催化剂、单质或复配镧系路易斯酸、其他路易斯酸催化剂制备频哪酮,其中,限定条件为:催化剂(复配催化剂为复配后的催化剂总量)物质的量为异戊烯物质的量的2%,第二步反应时间为4h,反应温度为83℃,固体甲醛的盐酸溶液质量比例为1:5,实验结果如表1。
49.表1
50.51.[0052][0053]
从表2中可以看出,
[0054]
不添加催化剂时,焦油含量高达19.75%,取出部分反应后的溶液在分液瓶中静置,具体状态见图3所示。大量焦油溶于盐酸中造成盐酸循环回收利用的障碍,大量的废酸废水都无法解决,带来非常高的工业环保成本。
[0055]
添加单独镧系金属氯化物作为反应催化剂时,不仅杂质焦油产生量大幅减少,而且频哪酮产品纯度和收率都有了大幅提高。综合考虑焦油产生量及频哪酮的收率,单用时尤以氯化镧、氯化铈效果最优。
[0056]
采用镧系路易斯酸两种复合或三种复合使用制备频哪酮,限定条件为复合使用时两个镧系金属氯化物组分的摩尔比为3:1,或者三种复配成分的摩尔比范围为3:1:1,效果也均好于现有技术。并且根据数据结果可以看出,氯化镧或氯化铈或氯化镨或氯化铷与其他一种或两种镧系氯化物复配时,其技术效果会好于单一成分的镧系氯化物催化剂。可以进一步说明,两种或多种镧系氯化物复配其催化作用产生了一定的协同促进效果。如实施例2.15,2.20,2.22,2.25,2.29,2.30的反应后的焦油含量均不超过5%,整个反应液呈现非常澄清的状态,见图5所示。
[0057]
当选择氯化锌,或氯化钙,或三氯化铝,或氯化锌与氯化钙的混合物,或氯化锌、氯化钙与镧系金属氯化物的混合物作为催化剂时,效果均不太理想,焦油溶于盐酸中造成盐酸循环回收利用的障碍,并不能实现真正意义上的清洁绿色生产频哪酮。
[0058]
实施例2.15的频哪酮产物的气相色谱图见附图5所示,纯度为98.68%。
[0059]
实施例3
[0060]
实验过程同实施例1,限定条件:催化剂为氯化镧,反应时间为4h,反应温度为83℃,固体甲醛的盐酸溶液质量比例为1:5,氯化镧与异戊烯物质的量比分别为5:1000、10:1000、20:1000、30:1000、40:1000、50:1000制备频哪酮,具体结果如表3。
[0061]
表3
[0062][0063]
由表3可以看出,氯化镧作为反应催化剂,当n(氯化镧):n(异戊烯)=20:1000,反应温度为83℃,反应时间为4h时,杂质焦油产生量为8.23%(减少了58.31%),频哪酮产品纯度都在98.50%以上,频哪酮收率在88%以上,效果改善明显。
[0064]
实施例4
[0065]
按照实施例1所述的制备方法,采用氯化镧和氯化铈作为催化剂,两个镧系金属氯化物组分的摩尔比为3:1,反应时间为4h,反应温度为83℃,固体甲醛的盐酸溶液质量比例为1:5,氯化镧和氯化铈混合物与异戊烯物质的量比分别为5:1000、10:1000、20:1000、30:1000、40:1000、50:1000,具体结果如表4。
[0066]
表4
[0067][0068]
由表4可以看出,以氯化镧和氯化铈作为复合催化剂,n(氯化镧):n(氯化铈)=3:1,n(氯化镧和氯化铈):n(异戊烯)=20:1000时,反应温度为83℃,反应时间为4h时,杂质焦油产生量为3.17%(减少了83.94%),频哪酮产品纯度都在98.50%以上,频哪酮收率在91%以上(提高了17.70%)。
[0069]
实施例5
[0070]
实验过程同实施例1,限定条件为催化剂为氯化镧和氯化铈两者复配使用,复合催化剂物质的量之和为异戊烯物质的量的2%,反应时间为4h,反应温度为83℃,固体甲醛的盐酸溶液质量比例为1:5,分别采用氯化镧和氯化铈物质的量比1:10、1:5、1:3、3:1、5:1、10:1、1:20、1:50、20:1、50:1制备频哪酮,具体结果如表6。
[0071]
表5
[0072][0073]
由表5可以看出,以氯化镧和氯化铈作为复合催化剂,n(氯化镧):n(氯化铈)=1:10~10:1时,杂质焦油产生量均低于10%,频哪酮产品纯度都在98.50%以上,频哪酮收率在86.94%以上。当n(氯化镧):n(氯化铈)在1:10~10:1的范围之外时,杂质焦油产生量明显升高,且频哪酮产品纯度和收率都降低了。
[0074]
实施例6
[0075]
实验过程同实施例1,限定条件为催化剂为氯化镧、氯化铈、氯化镨三者复配使用,复合催化剂物质的量之和为异戊烯物质的量的2%,反应时间为4h,反应温度为83℃,固体甲醛的盐酸溶液质量比例为1:5,分别采用氯化镧、氯化铈、氯化镨物质的量比3:1:1、5:1:1、5:3:3、5:2:2、1:1:1、6:1:1、5:4:4制备频哪酮,具体结果如表6。
[0076]
表6
[0077][0078]
由表6可以看出,氯化镧、氯化铈、氯化镨三者复配使用时,较优的比例范围为:1~5:1~3:1~3,优选的为1~3:1:1,或3:1:1。
[0079]
实施例7
[0080]
实验过程同实施例1,催化剂为氯化镧和氯化铈,两个镧系金属氯化物组分的摩尔比为3:1,催化剂物质的量之和为异戊烯物质的量的2%,采用固体甲醛与工业盐酸的质量比为1:5,固体甲醛盐酸溶液的加料时间为0.5h,反应时间为1h,反应温度为60℃,对频哪酮杂质焦油产生量、产品纯度(gc)、收率(以异戊烯计)进行分析,实验结果见表7。
[0081]
实施例8
[0082]
实验过程同实施例1,催化剂为氯化镧和氯化铈,两个镧系金属氯化物组分的摩尔比为3:1,催化剂物质的量之和为异戊烯物质的量的2%,采用固体甲醛与工业盐酸的质量比为1:10,固体甲醛盐酸溶液的加料时间为1h,反应时间为3h,反应温度为70℃,对频哪酮杂质焦油产生量、产品纯度(gc)、收率(以异戊烯计)进行分析,实验结果见表7。
[0083]
实施例9
[0084]
实验过程同实施例1,催化剂为氯化镧和氯化铈,两个镧系金属氯化物组分的摩尔比为3:1,催化剂物质的量之和为异戊烯物质的量的2%,采用固体甲醛与工业盐酸的质量比为1:10,固体甲醛盐酸溶液的加料时间为2h,反应时间为4h,反应温度为83℃,对频哪酮杂质焦油产生量、产品纯度(gc)、收率(以异戊烯计)进行分析,实验结果见表7。
[0085]
实施例10
[0086]
实验过程同实施例1,催化剂为氯化镧和氯化铈,两个镧系金属氯化物组分的摩尔比为3:1,催化剂物质的量之和为异戊烯物质的量的2%,采用固体甲醛与工业盐酸的质量比为1:15,固体甲醛盐酸溶液的加料时间为3h,反应时间为6h,反应温度为90℃,对频哪酮杂质焦油产生量、产品纯度(gc)、收率(以异戊烯计)进行分析,实验结果见表7。
[0087]
实施例11
[0088]
实验过程同实施例1,催化剂为氯化镧和氯化铈,两个镧系金属氯化物组分的摩尔比为3:1,催化剂物质的量之和为异戊烯物质的量的2%,采用固体甲醛与工业盐酸的质量比为1:20,固体甲醛盐酸溶液的加料时间为2h,反应时间为5h,反应温度为80℃,对频哪酮杂质焦油产生量、产品纯度(gc)、收率(以异戊烯计)进行分析,实验结果见表7。
[0089]
实施例12
[0090]
实验过程同实施例1,催化剂为氯化镧和氯化铈,两个镧系金属氯化物组分的摩尔比为3:1,催化剂物质的量之和为异戊烯物质的量的2%,采用固体甲醛与工业盐酸的质量比为1:5,固体甲醛盐酸溶液的加料时间为2h,反应时间为4h,反应温度为83℃,对频哪酮杂质焦油产生量、产品纯度(gc)、收率(以异戊烯计)进行分析,实验结果见表7。
[0091]
表7
[0092][0093][0094]
由表7可以看出,第二步反应中的固体甲醛与工业盐酸的质量比、固体甲醛盐酸溶液的加料时间,反应时间对反应结果的影响差异比较大,较优的组配范围是固体甲醛与工业盐酸的质量比最优为1:5或1:10,且固体甲醛盐酸溶液的加料时间不少于2小时,反应时间大于4小时,反应温度在83度左右。
[0095]
实施例13
[0096]
在本技术人的工厂中开展年产8000吨的频哪酮实际生产,具体核算数据为:每年减少废酸排放48000吨,一年节约成本1200万余元,实现了频哪酮的绿色清洁生产,实为一项重大工艺改革。
[0097]
以上所述仅为本发明创造的较佳实施例而已,并不用以限制本发明创造,凡在本发明创造的精神和原则之内,所作的任何修改、等同替换等,均应包含在本发明创造的保护范围之内。