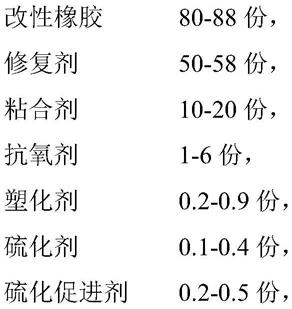
1.本发明属于车辆轮胎制备技术领域,具体涉及一种具有自修补功能防穿刺轮胎及其制备方法。
背景技术:2.车辆的轮胎在运行过程中,轮胎与地面不停地接触摩擦,一旦遭遇滚动石块和碎石割伤,将导致轮胎的使用寿命不断缩短,因此车辆使用一段时间后,大多会依据胎纹上深浅程度来判断轮胎是否应更换,此时需要肉眼检测破损,容易因为疏忽或遗忘检查而错过更换轮胎时机,从而造成因轮胎磨损和刺穿引发的爆胎等交通事故。
3.申请号cn201510357588.0提供了一种聚氨酯弹性体防穿刺轮胎衬垫及其制备方法,主要采用聚氨酯弹性体实现轮胎的韧性和拉伸能力,加强内胎外胎附着,避免了铁质衬垫对内胎咬合造成的爆胎现象;产品一次成型,极大降低了劳动成本。
4.然而,此种技术虽然在一定程度上实现了轮胎衬垫的防穿刺,但是成品存在拉伸强度不强的情形,并且难以适应高温和低冷的恶劣气候。
技术实现要素:5.针对现有技术中的不足,本发明的目的是提供一种具有自修补功能防穿刺轮胎及其制备方法。
6.为达到上述目的,本发明的解决方案是:
7.一种具有自修补功能防穿刺轮胎,其包括原料混合剂和后处理混合剂,其特征在于:所述的原料混合剂包括改性橡胶、修复剂、抗氧剂、塑化剂和防老化剂,所述的后处理混合剂包括粘合剂、硫化剂和硫化促进剂,按照重量份为:
[0008][0009][0010]
其中,橡胶选自天然橡胶、异戊橡胶和丙烯酸橡胶中的至少一类;粘合剂选自苯乙烯-丁二烯-苯乙烯嵌段共聚物和甲基丙烯酸甲酯中的至少一类;塑化剂选自羟基硅油、歧化松香、乙二酸二丁酯和丙烯酸异丙酯中的至少一类;硫化剂选自硫磺、二硫化四甲基秋兰姆和过氧化二苯甲酰中的至少一类;乳化剂选自硬脂酸钠皂和十二烷基苯磺酸钠中的至少
一类;硫化促进剂选自促进剂d、促进剂m和促进剂pz中的至少一类;防老化剂为n-辛基-n
′‑
苯基-β-对苯二胺和防老剂rd的复合物,两者比例为2::3.5。。
[0011]
优选地,修复剂的制备过程:将聚乙烯醇、甲基纤维素和水混合,加热至90-100℃溶解得到;改性橡胶的制备过程:将橡胶和乳化剂在100-120℃下反应10-30min;抗氧剂选自四[β-(3,5-二叔丁基-4-羟基苯基)丙酸]季戊四醇酯(1010)和三[2,4-二叔丁基苯基]亚磷酸酯(168)的复合物,四[β-(3,5-二叔丁基-4-羟基苯基)丙酸]季戊四醇酯和三[2,4-二叔丁基苯基]亚磷酸酯的质量比为(2-3):(1-2)。
[0012]
防老化剂为n-辛基-n
′‑
苯基-β-对苯二胺和防老剂rd的复合物,两者比例为2::3.5。一种上述的具有自修补功能防穿刺轮胎的制备方法,其包括如下步骤:
[0013]
(1)、将改性橡胶、修复剂、抗氧剂、塑化剂和防老化剂在90-120℃下混合10-30min,得到混合物;
[0014]
(2)、在混合物内加入粘合剂、硫化剂和硫化促进剂混合搅拌均匀,倒入模具,加热压膜2-3h,脱模后进行硫化,得到具有自修补功能防穿刺轮胎。
[0015]
具体地,作为优选,步骤(2)中,硫化的温度为160-170℃,压力为5-10mpa,时间为20-40min。
[0016]
由于采用上述方案,本发明的有益效果是:
[0017]
①
增加轮胎韧性。本发明采用改性橡胶、粘合剂和塑化剂的特殊配比复配,可以一定程度减小钉子等尖锐物的刺入,同时又有一定韧性,起到减震的作用;
[0018]
②
增加了轮胎力学强度。本发明采用硫化剂和硫化促进剂的复配,使得轮胎的弹性增加,力学性能增强;
[0019]
③
增强了极限环境适应性。本发明使用改性橡胶作为橡胶基体,使用改性橡胶、修复剂、粘合剂、抗氧剂、塑化剂、硫化剂、硫化促进剂和防老化剂作为胎面胶料,该橡胶基体占胎面胶料总量的50.4-56.5%,具有耐高温(130℃)、耐低温(零下35℃)、耐磨损和稳定性好等特点,从而满足在不同环境中的使用要求;
[0020]
④
增加轮胎使用年限。本发明采用抗氧剂的协同,抗氧剂1010具有良好的相容性,抗氧剂168主要保护轮胎在高温过程不会因光和热氧化而变色及分解,使得形成的轮胎能耐低温和耐高温性能,并延长轮胎的使用寿命;
[0021]
⑤
降低了轮胎的使用成本。采用修复剂,能密封修补轮胎因钉子戳破形成的小孔,不需要另外补胎,从而减少了修理时间和成本。
具体实施方式
[0022]
下面将对本发明实施例中的技术方案进行清楚、完整地描述,显然,所描述的实施例仅仅是本发明一部分实施例,而不是全部实施例。基于本发明中的实施例,本领域普通技术人员在没有做出创造性劳动前提下获得的所有其他实施例,都属于本发明保护的范围。
[0023]
为了验证具有自修补功能防穿刺轮胎及其制备方法中,材料的适用性和工艺的创造性,列举对比例1和实施例1~4的材料种类和工艺流程,实施拉伸强度、硬度(邵-d)、密封性、耐高温和耐低温参数的对比。
[0024]
对比例1:
[0025]
本对比例的轮胎包括如下重量份;
[0026][0027]
其中,橡胶为天然橡胶。
[0028]
粘合剂为苯乙烯-丁二烯-苯乙烯嵌段共聚物。
[0029]
硫化剂为硫磺。
[0030]
硫化促进剂为促进剂pz。
[0031]
防老化剂为n-辛基-n
′‑
苯基-β-对苯二胺和防老剂rd按质量比2:3.5组成的复合物。
[0032]
本对比例的轮胎的制备方法包括如下步骤:
[0033]
(1)、将橡胶和防老化剂在90℃下混合10min,得到混合物;
[0034]
(2)、在混合物内加入粘合剂、硫化剂和硫化促进剂混合搅拌均匀,倒入模具,加热压膜2h;脱模后进行硫化,硫化的温度为160℃,压力为7mpa,时间为20min,得到轮胎。
[0035]
实施例1:
[0036]
本实施例的具有自修补功能防穿刺轮胎包括如下重量份;
[0037][0038][0039]
其中,改性橡胶的制备过程:将天然橡胶和硬脂酸钠皂在100℃下反应10min即可。
[0040]
修复剂的制备过程:将聚乙烯醇、甲基纤维素和水混合,加热至90℃溶解得到。
[0041]
粘合剂为苯乙烯-丁二烯-苯乙烯嵌段共聚物。
[0042]
抗氧剂为四[β-(3,5-二叔丁基-4-羟基苯基)丙酸]季戊四醇酯和三[2,4-二叔丁基苯基]亚磷酸酯的复合物,四[β-(3,5-二叔丁基-4-羟基苯基)丙酸]季戊四醇酯和三[2,4-二叔丁基苯基]亚磷酸酯的质量比为2:1。
[0043]
塑化剂为羟基硅油。
[0044]
硫化剂为二硫化四甲基秋兰姆。
[0045]
硫化促进剂为促进剂d。
[0046]
防老化剂为n-辛基-n
′‑
苯基-β-对苯二胺和防老剂rd按质量比2:3.5组成的复合物。
[0047]
本实施例的具有自修补功能防穿刺轮胎的制备方法包括如下步骤:
[0048]
(1)、将改性橡胶、修复剂、抗氧剂、塑化剂和防老化剂在90℃下混合10min,得到混合物;
[0049]
(2)、在混合物内加入粘合剂、硫化剂和硫化促进剂混合搅拌均匀,倒入模具,加热压膜2h;脱模后进行硫化,硫化的温度为160℃,压力为5mpa,时间为20min,得到具有自修补功能防穿刺轮胎。
[0050]
实施例2:
[0051]
本实施例的具有自修补功能防穿刺轮胎包括如下重量份;
[0052][0053]
其中,改性橡胶的制备过程:将异戊橡胶和十二烷基苯磺酸钠在120℃下反应30min即可。
[0054]
修复剂的制备过程:将聚乙烯醇、甲基纤维素和水混合,加热至100℃溶解得到。
[0055]
粘合剂为甲基丙烯酸甲酯。
[0056]
抗氧剂为四[β-(3,5-二叔丁基-4-羟基苯基)丙酸]季戊四醇酯和三[2,4-二叔丁基苯基]亚磷酸酯的复合物,四[β-(3,5-二叔丁基-4-羟基苯基)丙酸]季戊四醇酯和三[2,4-二叔丁基苯基]亚磷酸酯的质量比为3:2。
[0057]
塑化剂为乙二酸二丁酯。
[0058]
硫化剂为过氧化二苯甲酰。
[0059]
硫化促进剂为促进剂m。
[0060]
防老化剂为n-辛基-n
′‑
苯基-β-对苯二胺和防老剂rd按质量比2:3.5组成的复合物。
[0061]
本实施例的具有自修补功能防穿刺轮胎的制备方法包括如下步骤:
[0062]
(1)、将改性橡胶、修复剂、抗氧剂、塑化剂和防老化剂在120℃下混合30min,得到混合物;
[0063]
(2)、在混合物内加入粘合剂、硫化剂和硫化促进剂混合搅拌均匀,倒入模具,加热压膜3h;脱模后进行硫化,硫化的温度为170℃,压力为10mpa,时间为40min,得到具有自修补功能防穿刺轮胎。
[0064]
实施例3:
[0065]
本实施例的具有自修补功能防穿刺轮胎包括如下重量份;
[0066][0067]
其中,改性橡胶的制备过程:将异戊橡胶、丙烯酸橡胶和十二烷基苯磺酸钠在120℃下反应20min即可。
[0068]
修复剂的制备过程:将聚乙烯醇、甲基纤维素和水混合,加热至95℃溶解得到。
[0069]
粘合剂为苯乙烯-丁二烯-苯乙烯嵌段共聚物。
[0070]
抗氧剂为四[β-(3,5-二叔丁基-4-羟基苯基)丙酸]季戊四醇酯和三[2,4-二叔丁基苯基]亚磷酸酯的复合物,四[β-(3,5-二叔丁基-4-羟基苯基)丙酸]季戊四醇酯和三[2,4-二叔丁基苯基]亚磷酸酯的质量比为2:1。
[0071]
塑化剂为歧化松香。
[0072]
硫化剂为硫磺。
[0073]
硫化促进剂为促进剂pz。
[0074]
防老化剂为n-辛基-n
′‑
苯基-β-对苯二胺和防老剂rd按质量比2:3.5组成的复合物。
[0075]
本实施例的具有自修补功能防穿刺轮胎的制备方法包括如下步骤:
[0076]
(1)、将改性橡胶、修复剂、抗氧剂、塑化剂和防老化剂在100℃下混合20min,得到混合物;
[0077]
(2)、在混合物内加入粘合剂、硫化剂和硫化促进剂混合搅拌均匀,倒入模具,加热压膜2.5h;脱模后进行硫化,硫化的温度为160℃,压力为6mpa,时间为30min,得到具有自修补功能防穿刺轮胎。
[0078]
实施例4:
[0079]
本实施例的具有自修补功能防穿刺轮胎包括如下重量份;
[0080][0081]
其中,改性橡胶的制备过程:将异戊橡胶、丙烯酸橡胶和十二烷基苯磺酸钠在110℃下反应18min即可。
[0082]
修复剂的制备过程:将聚乙烯醇、甲基纤维素和水混合,加热至98℃溶解得到。
[0083]
粘合剂为甲基丙烯酸甲酯。
[0084]
抗氧剂为四[β-(3,5-二叔丁基-4-羟基苯基)丙酸]季戊四醇酯和三[2,4-二叔丁基苯基]亚磷酸酯的复合物,四[β-(3,5-二叔丁基-4-羟基苯基)丙酸]季戊四醇酯和三[2,4-二叔丁基苯基]亚磷酸酯的质量比为3:1。
[0085]
塑化剂为歧化松香和乙二酸二丁酯的复配物。
[0086]
硫化剂为过氧化二苯甲酰。
[0087]
硫化促进剂为促进剂m和促进剂pz的复配物。
[0088]
防老化剂为n-辛基-n
′‑
苯基-β-对苯二胺和防老剂rd按质量比2:3.5组成的复合物。
[0089]
本实施例的具有自修补功能防穿刺轮胎的制备方法包括如下步骤:
[0090]
(1)、将改性橡胶、修复剂、抗氧剂、塑化剂和防老化剂在120℃下混合10min,得到混合物;
[0091]
(2)、在混合物内加入粘合剂、硫化剂和硫化促进剂混合搅拌均匀,倒入模具,加热压膜2h;脱模后进行硫化,硫化的温度为160℃,压力为8mpa,时间为35min,得到具有自修补功能防穿刺轮胎。
[0092]
将上述实施例和对比例的轮胎进行如下性能测试,其结果如表1所示。
[0093]
拉伸强度采用gb/t 528-2009测定进行;轮胎分别穿刺直径5mm的钉子,评价密封性能,拔出钉子后以漏气测试穿刺点是否有漏气现象。
[0094]
硬度(邵-d)测试:
[0095]
针对轮胎获取三片试片,在物理实验室室温23℃、湿度52%条件下静置43h,分别将试片放置在硬度试验机平台上,调整压针头与试片表面距离25mm且针头方向与试片垂直且与四周边界相距15mm,无冲击使压针头压在试件上,记录接触时间为1s,读取硬度(邵-d)参数,重复上述操作,三片试片取最终平均值。
[0096]
耐低温、耐高温性能测试:
[0097]-35℃(或者130℃)下,直径5mm的钢钉,扎孔位置胎面,注入轮胎以后,以30km/h的车速,行驶25km,轮胎修补完成,放置24h,计算轮胎压降。
[0098]
表1
[0099]
测试项目实施例1实施例2实施例3实施例4对比例1拉伸强度(mpa)10310810710965硬度(邵-d)7779777849密封性不漏气不漏气不漏气不漏气漏气低温轮胎压降(bar)0.090.050.070.090.32高温轮胎压降(bar)0.110.100.100.080.67
[0100]
通过表1的分析得出:采用原料混合剂和后处理混合剂的防穿刺轮胎实现的平均拉伸强度是对比例1的1.64倍、平均硬度(邵-d)为对比例1的1.59倍、耐低温为对比例1的1.52倍及耐高温为对比例1的1.30倍,密封性能远好于对比例1。
[0101]
最后应说明的是:以上仅为本发明的优选实施例而已,并不用于限制本发明,尽管参照前述实施例对本发明进行了详细的说明,对于本领域的技术人员来说,其依然可以对前述各实施例所记载的技术方案进行修改,或者对其中部分技术特征进行等同替换。凡在本发明的精神和原则之内,所作的任何修改、等同替换、改进等,均应包含在本发明的保护范围之内。