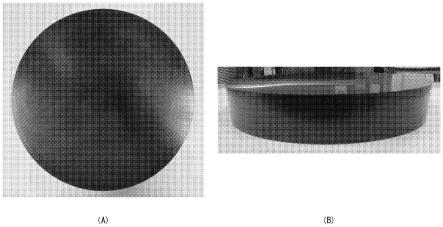
1.本发明涉及一种聚酰亚胺树脂成型体及其制造方法,更详细而言,涉及一种没有表面缺陷、内部空隙的厚的聚酰亚胺树脂成型体及其制造方法。
背景技术:2.由在末端具有加成反应基团的芳香族聚酰亚胺低聚物形成的加成反应型聚酰亚胺树脂的熔融粘度低、对纤维的浸含性优异,能通过传递成型(rtm)、树脂注入(ri)良好地成型,因此广泛用作碳纤维强化复合材料的基质。通过这些方法得到的复合材料构成材料的耐热性、耐候性、机械强度、耐久性等特性优异,因此广泛用于汽车、航空器等运输设备;土木/建筑材料;体育用品等用途。该复合材料构成材料在航空航天领域等中利用(专利文献1等)。
3.如上所述的加成反应型聚酰亚胺树脂通常配合碳纤维等功能性纤维而用作碳纤维强化复合材料的基质,但用作不含有碳纤维等的纯树脂(neat resin)成型品的需求也提高,特别是具有5mm以上的厚度的厚的纯树脂成型品的需求较大。现有技术文献专利文献
4.专利文献1:日本特表2003-526704号公报
技术实现要素:发明要解决的问题
5.在关于加成反应型聚酰亚胺树脂的专利文献1中也记载了,通过使用加成反应型聚酰亚胺树脂,在350~371℃下加热1小时,能成型直径1.5英寸、厚度25毫英寸的纯树脂成型品,但上述专利文献1中记载的纯树脂成型品是厚度约0.6mm的极薄的成型体。此外,如上述专利文献1所述,若将加成反应型聚酰亚胺树脂的预聚物在成型模具内直接加热来赋形,则成型模具内的粘度无法均匀,无法调整为适合于在成型模具内的所有位置上成型的粘度,因此会产生树脂的泄漏、气泡、膨胀等,无法成型没有缺陷的厚的成型品。
6.因此本发明的目的在于,提供一种成型体及其制造方法,所述成型体是厚的由加成反应型聚酰亚胺树脂形成的成型体,其空隙、裂纹等表面缺陷显著减少,由具有5mm以上的厚度。本发明的另一目的在于,提供一种成型体及其制造方法,所述成型体由加成反应型聚酰亚胺树脂形成,其即使是具有15mm以上的厚度的厚的成型体,内部空隙的产生也得到了有效防止,机械强度优异。本发明的又一目的在于,提供一种成型前体,所述成型前体能成型具有5mm以上的厚度的加成反应型聚酰亚胺树脂成型体。技术方案
7.根据本发明,提供一种第一加成反应型聚酰亚胺树脂成型体,其特征在于,是具有
5mm以上的厚度的加成反应型聚酰亚胺树脂成型体,其中,存在于成型体表面的0.5mm以上的缺陷数量为1个/100cm2以下。此外,根据本发明,提供一种第二加成反应型聚酰亚胺树脂成型体,其特征在于,是具有15mm以上的厚度的加成反应型聚酰亚胺树脂成型体,其中,弯曲强度为60mpa以上。
8.在本发明的加成反应型聚酰亚胺树脂成型体中,优选如下内容。1.第一加成反应型聚酰亚胺树脂成型体中的所述缺陷是最大直径为0.5mm以上的凹部或气泡、或者长度为0.5mm以上的裂纹。2.在第一加成反应型聚酰亚胺树脂成型体中,厚度为15mm以上,弯曲强度为60mpa以上。3.所述加成反应型聚酰亚胺树脂是具有苯乙炔基作为加成反应基团的聚酰亚胺树脂。4.成型体的形状是厚度为5~30mm的盘状或矩形的平板状。5.在温度357℃下加热6小时的情况下,不产生变形,或者产生高度小于1mm的凸状变形。
9.此外,根据本发明,提供一种加成反应型聚酰亚胺树脂成型体的制造方法,其特征在于,包括:增粘工序,将加成反应型聚酰亚胺树脂的预聚物在该加成反应型聚酰亚胺树脂的增粘开始温度以上的温度下保持,使比增粘开始温度低10℃的温度条件下的熔融粘度上升至70~900kpa
·
s;粉碎混合工序,将经过该增粘工序的加成反应型聚酰亚胺树脂粉体化并混合;以及赋形工序,将该进行了粉体化的加成反应型聚酰亚胺树脂在加成反应型聚酰亚胺树脂的热固化温度以上的温度下赋形。
10.在本发明的加成反应型聚酰亚胺树脂成型体的制造方法中,优选如下内容。1.在所述增粘工序中,将所述加成反应型聚酰亚胺树脂在比增粘开始温度高15~45℃的温度范围内保持50~200分钟。2.所述赋形工序通过压缩成型来进行。
11.根据本发明,还提供一种成型前体,其特征在于,由加成反应型聚酰亚胺树脂形成,所述成型前体的比该加成反应型聚酰亚胺树脂的增粘开始温度低10℃的温度条件下的熔融粘度为70~900kpa
·
s。
12.需要说明的是,在本说明书中,弯曲强度和增粘开始温度如下所述地定义。(1)弯曲强度依据jis k 7171(塑料-弯曲特性的试验方法),将成型体的厚度方向(成型模具的移动方向)设为试验片(长度50mm
×
宽度10mm
×
厚度3mm)的厚度,切出具有如下的各位置处的厚度的、长度50mm
×
宽度10mm的试验片:距成型体的上表面向厚度方向下方3mm、将成型体的厚度(t)中心(t/2的位置)设为厚度中心(中立面)的3mm、距成型体的下表面向厚度方向上方3mm。使用该试验片进行弯曲试验,将所得到的各试验片的弯曲应力的最小值作为成型体的弯曲强度。测定条件在后文中叙述。
13.(2)增粘开始温度在流变仪中使用平行板,在角频率100rad/s下,以4℃/min升温,达到规定的目标温度后,在该目标温度下保持一定时间的条件下,对未反应状态的加成反应型聚酰亚胺树脂的粘度进行测定。由于升温而熔融,粘度降低。将测定中最低的粘度作为最低熔融粘度,
求出达到目标温度后直至经过120分钟为止的熔融粘度。以5的倍数的温度将目标温度从低温向高温设定,分别进行熔融粘度的计测。将示出最低熔融粘度的时间设为0分钟,标示出以时间(min)为横轴、以熔融粘度(pa
·
s)为纵轴的半对数曲线,通过表格软件计算出指数近似值。将下述式(1)所示的近似式的b的值首次超过0.014的温度作为增粘开始温度。y=aexp(bx)
……
(1)式中,y:熔融粘度(pa
·
s)、x:时间(min)、a和b:常数。发明效果
14.本发明的树脂成型体是耐热性、耐久性以及机械强度优异的、由加成反应型聚酰亚胺树脂形成的,具有5mm以上的厚度的树脂成型体,能作为0.5mm以上的大小的表面缺陷显著减少的厚的成型体来提供。需要说明的是,在本说明书中表面缺陷不限于此,是指:因树脂中内包的空气、因源自树脂的逸出气体等引起的在表面形成的气泡;由该气泡破碎、压缩时的变形而在表面产生的凹状缺陷(也称为空隙、凹陷);或者裂纹等。此外,本发明的树脂成型体即使在具有15mm以上的厚度的情况下,成型体内部也不形成空隙,因此具有60mpa以上的弯曲强度,具有优异的机械强度。而且,根据本发明的树脂成型体的制造方法,通过在比加成反应型聚酰亚胺树脂的增粘开始温度高15~45℃的温度条件下预先进行粘度调整,将其粉碎混合,能有效防止赋形时由于成型模具内的位置而产生的粘度差,能不产生空隙、裂纹等缺陷而成型具有5mm以上,特别是具有5~30mm的厚度的成型体。而且,本发明的成型前体被均匀地调整为适合于在对于树脂成型体的成型温度下的熔融粘度,因此无需进行即将赋形前的粘度调整,不存在像进行即将赋形前的加热、粘度调整的情况那样的气泡的产生和破碎的可能性,能高效成型没有表面缺陷和内部空隙的厚的树脂成型体。
附图说明
15.图1是表示本发明的树脂成型体的一个例子的图。图2是表示在实施例11中得到的成型品的表面的照片,分别是,图2的(a)表示压缩面,图2的(b)表示侧面。图3的(a)表示在实施例11中得到的成型品的后加热后的表面的照片、图3的(b)表示在实施例12中得到的成型品的后加热后的表面的照片。图4是表示在比较例7中得到的成型品的表面(侧面)的放大照片。图5是表示对在比较例7中得到的成型品的后加热后的表面的照片,分别是,图5的(a)表示压缩面,图5的(b)表示侧面。图6是表示在比较例5中得到的成型品的厚度方向剖面的照片。图7是表示在比较例7中得到的成型品的厚度方向剖面的照片。
具体实施方式
16.(树脂成型体)如上所述,在由加成反应型聚酰亚胺树脂形成的纯树脂成型体中,难以在成型体表面不产生缺陷的情况下成型具有5mm以上的厚度的树脂成型体,但本发明的树脂成型体
具有5mm以上的厚度,并且0.5mm以上的表面缺陷减少至1个/100cm2以下。本发明中的树脂成型体只要具有5mm以上的厚度,特别是具有5~30mm的厚度,其形状就没有限定。具体而言,根据后述的本发明的树脂成型体的成型方法明显可知,只要是能通过压缩成型、传递成型来成型的形状就没有特别限定。此外,厚度是指所得到的成型体中的最大厚度,在利用压缩成型、传递成型的情况下,成型模具的移动方向成为树脂成型体的厚度方向。作为本发明的树脂成型体的优选的形状,可举例示出除了盘状、方形等平板状;圆柱状、棱柱状等以外,还可举例示出具有曲面的形状、如图1所示的盘状等所述形状的成型体形成多个而成的树脂成型体。
17.理想的是,本发明的树脂成型体在其表面没有0.5mm以上的缺陷,特别是没有0.5~50mm范围的缺陷,即尽可能为零,即使存在缺陷,该缺陷在成型体的整个表面也减少至1个/100cm2以下。上述缺陷不限定于此,是最大直径为0.5mm以上的凹状缺陷、气泡;或者最大长度为0.5mm以上的裂纹等,例如可以特别举例示出如图4所示的缺陷。
18.本发明的加成反应型聚酰亚胺树脂成型体即使在357℃的温度下加热6小时的情况下,也不产生变形,或即使产生变形也是产生高度小于1mm的凸状变形的程度,具有优异的热稳定性。即,本发明的树脂成型体的成型模具内的成型前体的熔融粘度均匀,如后所述在赋形工序中充分且均匀地热固化,因此未反应的加成反应型聚酰亚胺树脂的预聚物的含量尽可能减少。因此,即使对树脂成型体进一步在上述加热条件下进行加热处理,基于加成反应型聚酰亚胺树脂的预聚物的反应的因气泡的产生、膨胀等而产生的凸状变形也尽可能减少,热稳定性优异。需要说明的是,在本说明书中,凸状变形定义为在357℃的温度下加热6小时前后的加成反应型聚酰亚胺树脂成型体的最大厚度之差。
19.此外,由加成反应型聚酰亚胺树脂形成的成型体通常在制成厚度15mm以上的厚成型体时容易在内部形成空隙,因此存在机械强度降低的倾向,但在本发明的树脂成型体中,如上所述,气泡的产生、膨胀等得以减少,因此即使是厚度为15mm的厚成型体,成型体内部的空隙的形成也得到抑制。其结果是,弯曲强度大至60mpa以上,具有优异的机械强度。需要说明的是,在本发明的第二加成反应型聚酰亚胺树脂成型体中,其是15mm以上的厚成型体,因此也可以通过对表面进行研磨等处理来去除表面缺陷,表面的缺陷也可以未必如关于第一加成反应型聚酰亚胺树脂成型体所规定的那样显著减少。
20.(加成反应型聚酰亚胺树脂)构成本发明的树脂成型体的加成反应型聚酰亚胺树脂由在末端具有加成反应基团的芳香族聚酰亚胺低聚物构成,可以使用通过以往公知的制法制备出的物质。例如,所述加成反应型聚酰亚胺树脂可以通过如下方方式而容易地得到:以使各酸基的当量的合计与各氨基的合计成为大致等量的方式使用芳香族四羧酸二酐、芳香族二胺以及在分子内一并具有加成反应基团和酸酐基或氨基的化合物,优选在溶剂中反应。作为反应的方法,可举例示出如下方法:在100℃以下,优选在80℃以下的温度下聚合0.1~50小时,生成具有酰胺酸键的低聚物,接着利用酰亚胺化剂进行化学酰亚胺化的方法;由在140~270℃左右的高温下加热,进行热酰亚胺化这两道工序构成的方法;或者由从最初开始在140~270℃的高温下进行0.1~50小时聚合/酰亚胺化反应这一道工序构成的方法。
在这些反应中使用的溶剂不限定于此,可以优选使用n-甲基-2-吡咯烷酮、n,n-二甲基甲酰胺、n,n-二甲基乙酰胺、n,n-二乙基乙酰胺、γ-丁内酯、n-甲基己内酰胺等有机极性溶剂。
21.在本发明中,芳香族酰亚胺低聚物的末端的加成反应基团只要是在制造树脂成型体时通过加热而进行固化反应(加成聚合反应)的基团就没有特别限定,若考虑能适当地进行固化反应、以及所得到的固化物的耐热性良好,优选为选自由苯乙炔基、乙炔基、纳迪克酸基以及马来酰亚胺基构成的组中的任意种反应基团,特别是,从没有由固化反应引起的气体成分的产生,而且所得到的树脂成型体的耐热性优异并且机械强度也优异的方面考虑,优选苯乙炔基。这些加成反应基团通过在分子内一并具有加成反应基团和酸酐基或氨基的化合物与芳香族酰亚胺低聚物的末端的氨基或酸酐基优选进行形成酰亚胺环的反应而引入至芳香族酰亚胺低聚物的末端。在分子内一并具有加成反应基团和酸酐基或氨基的化合物例如可以优选使用4-(2-苯乙炔基)苯二甲酸酐、4-(2-苯乙炔基)苯胺、4-乙炔基-苯二甲酸酐、4-乙炔基苯胺、纳迪克酸酐、马来酸酐等。
22.作为形成在末端具有加成反应基团的芳香族酰亚胺低聚物的四羧酸成分,可举例示出选自由2,3,3’,4
’‑
联苯四羧酸二酐、2,2’,3,3
’‑
联苯四羧酸二酐、3,3’,4,4
’‑
联苯四羧酸二酐以及3,3’,4,4
’‑
二苯甲酮四羧酸二酐构成的组中的至少一种四羧酸二酐,特别是,可以优选使用2,3,3’,4
’‑
联苯四羧酸二酐。
23.作为形成在末端具有加成反应基团的芳香族酰亚胺低聚物的二胺成分,不限定于此,可以单独使用或混合多种使用如下二胺:1,4-二氨基苯、1,3-二氨基苯、1,2-二氨基苯、2,6-二乙基-1,3-二氨基苯、4,6-二乙基-2-甲基-1,3-二氨基苯、3,5-二乙基甲苯-2,4-二胺、3,5-二乙基甲苯-2,6-二胺等具有一个苯环的二胺;4,4
’‑
二氨基二苯醚、3,4
’‑
二氨基二苯醚、3,3
’‑
二氨基二苯醚、3,3
’‑
二氨基二苯甲酮、4,4
’‑
二氨基二苯甲酮、4,4
’‑
二氨基二苯基甲烷、3,3
’‑
二氨基二苯基甲烷、双(2,6-二乙基-4-氨基苯氧基)甲烷、双(2-乙基-6-甲基-4-氨基苯基)甲烷、4,4
’‑
亚甲基-双(2,6-二乙基苯胺)、4,4
’‑
亚甲基-双(2-乙基-6-甲基苯胺)、2,2-双(3-氨基苯基)丙烷、2,2-双(4-氨基苯基)丙烷联苯胺、2,2
’‑
双(三氟甲基)联苯胺、3,3
’‑
二甲基联苯胺、2,2-双(4-氨基苯基)丙烷、2,2-双(3-氨基苯基)丙烷联苯胺等具有两个苯环的二胺;1,3-双(4-氨基苯氧基)苯、1,3-双(3-氨基苯氧基)苯、1,4-双(4-氨基苯氧基)苯、1,4-双(3-氨基苯氧基)苯等具有三个苯环的二胺;2,2-双[4-[4-氨基苯氧基]苯基]丙烷、2,2-双[4-[4-氨基苯氧基]苯基]六氟丙烷等具有四个苯环的二胺。
[0024]
其中,优选使用由选自由1,3-二氨基苯、1,3-双(4-氨基苯氧基)苯、3,4
’‑
二氨基二苯醚、4,4
’‑
二氨基二苯醚以及2,2
’‑
双(三氟甲基)联苯胺构成的组中的至少两种芳香族二胺构成的混合二胺,特别是,从耐热性和成型性的方面考虑,优选使用由1,3-二氨基苯与1,3-双(4-氨基苯氧基)苯的组合构成的混合二胺、由3,4
’‑
二氨基二苯醚与4,4
’‑
二氨基二苯醚的组合构成的混合二胺、由3,4
’‑
二氨基二苯醚与1,3-双(4-氨基苯氧基)苯的组合构成的混合二胺、由4,4
’‑
二氨基二苯醚与1,3-双(4-氨基苯氧基)苯的组合构成的混合二胺、以及由2,2
’‑
双(三氟甲基)联苯胺与1,3-双(4-氨基苯氧基)苯的组合构成的混合二胺。
[0025]
就在本发明中使用的、在末端具有加成反应基团的芳香族酰亚胺低聚物而言,酰
亚胺低聚物的重复单元的重复优选为0~20、特别是1~5,利用gpc的苯乙烯换算的数均分子量优选为10000以下,特别是3000以下。通过重复单元的重复数量在上述范围内,能将熔融粘度调整至适当的范围,将功能性纤维混合。此外能提供一种树脂成型体,其无需在高温下成型,成型性优异,并且耐热性和机械强度优异。重复单元的重复数量的调整可以通过改变芳香族四羧酸二酐、芳香族二胺以及在分子内一并具有加成反应基团和酸酐基或氨基的化合物的比例来进行,通过提高在分子内一并具有加成反应基团和具有酸酐基或氨基的化合物的比例,低分子量化而重复单元的重复数量变小,当减少该化合物的比例时,高分子量化而重复单元的重复数量变大。
[0026]
在加成反应型聚酰亚胺树脂中,也可以根据目标的树脂成型体的用途,依照公知的配方配合阻燃剂、着色剂、润滑剂、热稳定剂、光稳定剂、紫外线吸收剂、填充剂等树脂添加剂。
[0027]
(树脂成型体的制造方法)本发明的树脂成型体的制造方法包括:增粘工序,将加成反应型聚酰亚胺树脂的预聚物在该加成反应型聚酰亚胺树脂的增粘开始温度以上的温度下保持,使比增粘开始温度低10℃的温度条件下的熔融粘度上升至70~900kpa
·
s;粉碎混合工序,将经过该增粘工序的加成反应型聚酰亚胺树脂粉体化并混合;以及赋形工序,将该进行了粉体化的加成反应型聚酰亚胺树脂在加成反应型聚酰亚胺树脂的热固化温度以上的温度下赋形。
[0028]
在本发明的树脂成型体的制造中使用的加成反应型聚酰亚胺树脂在交联固化前的预聚物的状态下是低粘度的,因此在树脂成型体的赋形工序中,当使供给至成型模具的预聚物增粘时,成型模具内的中央附近处粘度上升少,成型模具内的中央附近处粘度上升大,存在预聚物的粘度无法均匀的问题。若以成型模具中央部分为基准进行粘度调整,则成型模具的器壁附近的预聚物热分解而发泡/膨胀,产生如下问题:由于由之后的压缩成型带来的加压而气泡破碎、产生空隙。另一方面,若以成型模具的器壁附近的预聚物的粘度为基准,则产生如下问题:粘度过低而无法成型,熔融树脂从成型模具中泄漏。
[0029]
在本发明中,在赋形工序之前,通过上述增粘工序使预聚物的、比增粘开始温度低10℃的温度条件下的熔融粘度上升至70~900kpa
·
s,并且,通过接着进行的粉碎混合工序,将熔融粘度调整至上述范围的加成反应型聚酰亚胺树脂粉体化并混合,制备具有均匀熔融粘度的粉体状的成型前体。由此,无需赋形工序中的增粘,其结果是,如上所述,能成型没有0.5mm以上的缺陷,或即使存在,表面缺陷也显著减少至1个/100cm2以下的、具有5mm以上的厚度的树脂成型体。
[0030]
[增粘工序]在增粘工序中,首先使用电炉等将加成反应型聚酰亚胺树脂的预聚物(酰亚胺低聚物)在加成反应型聚酰亚胺树脂的增粘开始温度以上的温度下保持一定时间,由此使熔融粘度上升至70~900kpa
·
s,优选在比增粘开始温度高15~45℃的温度范围内保持50~200分钟,特别是保持65~110分钟,由此使比增粘开始温度低10℃的温度条件下的预聚物的熔融粘度上升至70~900kpa
·
s。将预聚物在上述温度条件下保持一定时间,由此预聚物逐渐开始交联,因此粘度上升。此外,通过设为上述范围的加热温度和保持时间,能不使预聚物完全地交联固化而仅使粘度上升至上述范围。因此,增粘工序在预聚物的增粘开始温度以上且低于完全地交联
固化的温度下进行。需要说明的是,在加成反应型聚酰亚胺树脂中,反应开始温度依赖于加成反应基团,在本发明中,在具有优选的苯乙炔基作为加成反应基团的聚酰亚胺树脂中,理想的是,通过在作为增粘开始温度附近的320
±
15℃的温度下保持一定时间,使熔融粘度上升至70~900kpa
·
s。
[0031]
在经过增粘工序后,通过冷却(包括放冷)固化而得到的加成反应型聚酰亚胺树脂块也能进行经时保管,操作性优异,但粘度在块的位置,例如在块表面与块中心部分产生差异。因此,本发明的成型前体优选通过后述的粉碎混合工序制成进行了粉体化并且混合的状态的粉体。
[0032]
[粉碎混合工序]在经过增粘工序而得到的、比增粘开始温度低10℃的温度条件下的熔融粘度调整为70~900kpa
·
s的加成反应型聚酰亚胺树脂块如上所述,根据块的位置的不同而粘度有差异,因此在本发明中将其粉碎混合而制成粉体状的成型前体。粉碎混合也可以使用亨舍尔混合机、转鼓混合机、带式混合机、喷射式粉碎机、辊磨机、球磨机、钉碎机(spike mill)、振动研磨机等以往公知的粉碎混合机,从能同时高效进行粉碎和混合的方面考虑,特别优选使用亨舍尔混合机。粉体状成型前体的粒度优选为通过激光散射衍射法测定出的平均粒径(d50)在1~1000μm的范围内。
[0033]
[赋形工序]如上所述,在本发明的成型前体中,在比加成反应型聚酰亚胺树脂的增粘开始温度低10℃的温度条件下具有70~900kpa
·
s的熔融粘度,因此在树脂成型体的成型时,可以将进行了粉碎混合的粉体状的成型前体直接在加成反应型聚酰亚胺的热固化温度以上的温度下赋形。此外,为了使被粉碎的成型前体的温度均匀化,也可以根据需要设置:预热工序,将粉体状的成型前体导入成型模具后,在成型模具内在熔融温度以上且增粘开始温度以下的温度下保持规定时间,优选在比增粘开始温度低5~20℃的温度下保持10~30分钟。
[0034]
导入至成型模具内的粉体状的成型前体、或者在成型模具内经过预热工序而有些熔融的状态的成型前体在所使用的加成反应型聚酰亚胺树脂的热固化温度以上的温度条件下,具体而言在具有苯乙炔基作为加成反应基团的聚酰亚胺树脂中,在360~390℃的温度下赋形,由此成型为所希望的树脂成型体。在本发明的粉体状成型前体中,通过粉碎混合而作为成型前体具有均匀的熔融粘度。其结果是,若在热固化温度以上的温度下加热,则不在成型模具内由于位置而产生粘度差,而在成型模具内均匀地熔融。其结果是,即使通过压缩成型等进行加压压缩,树脂的流动也降低,并且也不产生气泡、膨胀,因此如上所述,能成型具有5mm以上,特别是具有5~30mm的厚度,不产生0.5mm以上的缺陷的、或即使产生缺陷也为1个/100cm2以下的树脂成型体。需要说明的是,从成型5mm以上的厚度的成型体的观点考虑,赋形优选通过对导入至成型模具的混合物进行加压压缩而成型的压缩成型、传递成型来进行,也可以通过注塑成型、挤出成型来成型。实施例
[0035]
(增粘开始温度的测定)通过流变仪对所使用的加成反应型聚酰亚胺树脂的增粘开始温度进行了计测。将向目标温度的达到速度设为4℃/min,在达到目标达到温度后保持120分钟的温度条件下,使用平行板,以角频率100rad/s、应变10%的形式对熔融粘度进行测定,将示出最低熔融粘度的时间设为0分钟,标示出以时间(min)为横轴、以熔融粘度(pa
·
s)为纵轴的半对数曲线,根据指数近似式求出式(1)的系数b。在加成聚合聚酰亚胺(宇部兴产公司制peti-330)中,目标温度为285℃时的b值为0.0092,目标温度为290℃时的b值为0.0141,将增粘开始温度设为290℃。
[0036]
(熔融粘度的测定)通过流变仪(ta instrument公司制ares-g2)对所使用的加成反应型聚酰亚胺树脂的比增粘开始温度低10℃的温度下的熔融粘度进行了测定。使用平行板,将(测定间隙设为1mm)应变设为1%、角频率范围设为0.1~100rad/s,将测定熔融粘度时的0.1rad/s下的熔融粘度作为测定值。需要说明的是,测定时,利用热压将粉体状的成型前体在比增粘开始温度低10℃~40℃的温度下加热加压,制成平滑的板状。
[0037]
(弯曲强度的测定)依据jis k 7171(塑料-弯曲特性的试验方法),使用autograph(岛津制作所制ag-1/50n-10kn),以试验速度1mm/min对从树脂成型体切出的试验片(长度50mm
×
宽度10mm
×
厚度3mm)进行弯曲试验,测定出弯曲强度。需要说明的是,在从距树脂成型体上表面在厚度方向上3mm、距中立面
±
1.5mm、距成型体下表面3mm的位置切出试验片。
[0038]
(表面缺陷的评价)通过目视对缺陷的有无、个数进行了确认,利用尺子、游标卡尺等计测器具对尺寸进行了测定。只要存在于成型体的整个表面的0.5mm以上的缺陷数量为1个/100cm2以下就设为(〇),将比1个/100cm2多的情况设为(
×
)。
[0039]
(成型品的后加热评价)利用游标卡尺、测高计等计测器具对在357℃的温度下加热6小时前后的加成反应型聚酰亚胺树脂成型体的最大厚度进行了测定。只要厚度差小于1mm就设为良(〇),将1mm以上的情况设为(
×
)。
[0040]
(实施例1)将加成反应型聚酰亚胺(宇部兴产公司制peti-330)在电炉内的树脂温度330℃下保持65分钟,将熔融粘度调整为作为比加成反应型聚酰亚胺的增粘开始温度低10℃的温度的280℃下的熔融粘度126.6kpa
·
s。然后,进行骤冷,得到冷却至室温的加成反应型聚酰亚胺树脂的块。将所得到的树脂块通过粉碎混合机粉碎混合后,供给至压缩成型模具,在280℃下预热90分钟后,一边加压至11.0mpa一边以升温速度0.3℃/min升温至320℃,保持60分钟,进而以升温速度0.43℃/min升温至371℃,保持120分钟后,缓慢冷却而得到了厚度5mm的盘状的板。
[0041]
(实施例2)在电炉内的树脂温度330℃下将保持时间变更为95分钟,将熔融粘度调整为作为比加成反应型聚酰亚胺的增粘开始温度低10℃的温度的280℃下的熔融粘度642.9kpa
·
s,
除此以外,与实施例1相同。
[0042]
(实施例3、5、7、9、11)将成型品的厚度设为表1所示的厚度,除此以外,与实施例1同样。
[0043]
(实施例4、6、8、10、12)将成型品的厚度设为表1所示的厚度,除此以外,与实施例2同样。
[0044]
(实施例13)在电炉内的树脂温度330℃下将保持时间变更为110分钟进行了粘度调整,除此以外,与实施例11同样。需要说明的是,无法测定粘度调整后的加成反应型聚酰亚胺树脂的、作为比增粘开始温度低10℃的280℃的温度下的熔融粘度,因此在流变仪内再现了增粘工序。在流变仪内从280℃起以3.1℃/min升温,将达到330℃的时间点设为0分钟,将经过110分钟的时间点的复粘度的值896.3kpa
·
s作为熔融粘度。在测定中使用的平行板,将角频率设定为10rad/s。
[0045]
(实施例14)在电炉内的树脂温度330℃下将保持时间变更为120分钟进行了粘度调整,除此以外,与实施例11同样。需要说明的是,无法测定粘度调整后的加成反应型聚酰亚胺树脂的、作为比增粘开始温度低10℃的280℃的温度下的熔融粘度,因此在流变仪内再现了增粘工序。在流变仪内从280℃起以3.1℃/min升温,将达到330℃的时间点设为0分钟,将经过120分钟的时间点的复粘度的值1151.1kpa
·
s作为熔融粘度。在测定中使用的平行板,将角频率设定为10rad/s。
[0046]
〔比较例1〕将加成反应型聚酰亚胺(宇部兴产公司制peti-330)供给至压缩成型模具,在模具温度280℃下预热90分钟后,以3.3℃/min升温至320℃,在模具温度320℃下保持45分钟,使其上升至压缩成型时不产生树脂漏出的粘度后,一边加压至11.0mpa一边以升温速度0.85℃/min升温至371℃为止,保持120分钟后,缓慢冷却而得到了厚度3mm的盘状的板。
[0047]
(比较例2)将成型品的厚度设为5mm,除此以外,与比较例1同样。
[0048]
(比较例3~7)将模具温度变更为320℃,将保持时间变更为40分钟,将成型品的厚度设为表2所示的厚度,除此以外,与比较例1同样。
[0049]
(比较例8)在电炉内的树脂温度330℃下将保持时间变更为60分钟,将熔融粘度调整为作为比加成反应型聚酰亚胺的增粘开始温度低10℃的280℃下的熔融粘度60.4kpa
·
s,除此以外,与实施例11同样。
[0050]
将在实施例1~14、比较例1~8中得到的、经过增粘工序而得到的加成反应型聚酰亚胺树脂的熔融粘度、成型品的表面缺陷的评价、以及成型品的后加热评价的结果示于表1和表2。需要说明的是,关于比较例1~7,熔融粘度根据模具内的位置而不同,因此未进行计测。
将在实施例5~14、比较例1、4~7中得到的成型品的弯曲强度示于表1和表2。
[0051]
将在实施例11中得到的成型品的表面示于图2。分别是,图2的(a)表示压缩面,图2的(b)表示侧面。此外,将上述后加热评价后的表面放大照片示于图3的(a)。将在比较例7中得到的成型品的侧面的放大照片示于图4。由图4明显可知,产生了许多2~3mm的空隙,也存在着空隙之间连接而形成如裂缝一样的部位。此外,将上述后加热评价后的表面照片示于图5。分别是,图5的(a)表示压缩面,图5的(b)表示侧面。由图5明显可知,存在凸状变形的部位。而且,分别将在比较例5和比较例7中得到的成型品的厚度方向的剖面示于图6和图7。由图6明显可知,在作为15mm的成型品的比较例5中,局部形成了多个内部空隙。此外,由图7明显可知,在作为厚度30mm的成型品的比较例7中,整体存在许多内部空隙。
[0052][0053]
[表2]
工业上的可利用性
[0054]
本发明的树脂成型体是具有5mm以上的厚度的厚的成型体,同时表面缺陷显著减少,并且树脂成型体内部的空隙的产生得到抑制,耐热性、耐久性、机械强度优异,能作为汽车、电气/电子领域等的构件用于各种用途。