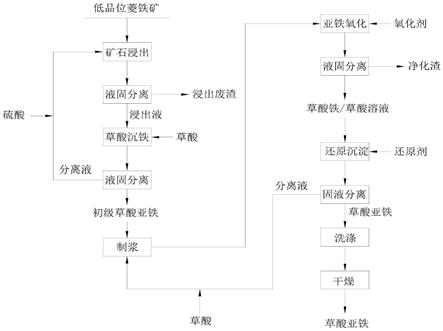
1.本发明涉及锂离子电池正极材料前驱体制备技术领域,具体涉及一种利用菱铁矿制备草酸亚铁的方法。
背景技术:2.锂离子电池具有能量密度高、循环寿命长、对环境污染小和无记忆效应等诸多优点,成为支持当前电动车用电源发展的重要基础,磷酸铁锂电池在安全性和循环寿命等方面表现优异,成为当前电动车市场的主流电池之一。
3.草酸亚铁是制备磷酸铁锂的优质前驱体,目前主要是利用商品化的亚铁盐和草酸盐通过混合沉淀的方式获得,该类技术首先需要将铁锰矿石经过复杂的冶金过程,获得商品化的高纯度亚铁盐和草酸盐,工艺流程长,成本高、副产物和污染物排放量大。菱铁矿是自然界中铁资源的一种重要天然赋存形态,我国菱铁矿资源丰富,但品位低,需要经过焙烧-选矿等一系列的富集过程使铁含量升高,才可用于钢铁冶炼的原料,该过程存在能耗大和污染物排放量大的问题。因此,开发低成本草酸亚铁制备技术和菱铁矿的绿色资源化资源化利用技术,具有重要的现实意义。
技术实现要素:4.为了解决上述技术问题,本发明的目的是提供一种利用菱铁矿制备草酸亚铁的方法,以解决现有技术利用菱铁矿制备草酸亚铁能耗大、纯度低的问题。
5.本发明解决上述技术问题的技术方案如下:提供一种利用菱铁矿制备草酸亚铁的方法,包括以下步骤:
6.(1)矿石浸出:将菱铁矿加入无机酸溶液中进行浸出反应,然后固液分离,得到分离液一;
7.(2)草酸沉铁:在分离液一中加入草酸进行沉淀反应,然后固液分离,得到初级草酸亚铁和分离液二;
8.(3)亚铁氧化:将初级草酸亚铁加至草酸溶液中进行制浆,然后加入氧化剂,再固液分离,得到分离液三;
9.(4)还原沉铁:将分离液三进行还原处理,然后固液分离,得到的沉淀经洗涤、干燥后,得到草酸亚铁。
10.本发明的有益效果为:本发明以菱铁矿为原料,利用草酸亚铁(二价铁固体沉淀)与草酸铁(溶液态三价铁络合物)的物相转化,实现两次除杂,达到去除碱金属(钾钠)、钙镁和重金属的目的,整个过程中无需额外的净化剂加入,制得的草酸亚铁纯度高,副产物少。
11.在上述技术方案中,步骤(1)中矿石浸出过程中,菱铁矿中的碳酸亚铁转化为亚铁离子,其他的金属杂质也转化为金属离子,因此,上述离子经过无机酸浸出后进入分离液一中,其浸出反应的化学式为:
12.feco3+2h
+
→
fe
2+
+h2o+co2↑
13.meco3+2h
+
→
me
2+
+h2o+co2↑
(me:k、na、ca、mg、重金属)
14.步骤(2)中草酸沉铁的过程中,分离液一中的亚铁离子和草酸反应生成沉淀,其沉淀反应的化学式为:
15.fe
2+
+h2c2o4→
fec2o4↓
+2h
+
16.而分离液一中钠、钾离子则不与草酸反应,如此,可以去除分离液一中的钠、钾离子,从而可以得到初级的草酸亚铁沉淀(其含有钙、镁和重金属杂质的草酸盐沉淀)。
17.步骤(3)亚铁氧化过程中,初级草酸亚铁和草酸溶液制浆后,亚铁离子被氧化为三价铁离子,三价铁离子和草酸之间以可溶性络合物的形式存在,络合物的形态与三价铁离子和草酸根离子的比例关系决定,其反应化学式为:
18.fe
3+
+c2o
42-→
fe(c2o4)
+
[0019][0020][0021]
而初级草酸亚铁沉淀中混合的钙、镁和重金属杂质仍然以的草酸盐沉淀的形式存在,从而可以去除初级草酸亚铁中混合的钙、镁和重金属杂质。
[0022]
步骤(4)还原沉铁过程中,通过将三价铁还原为二价铁,进而产生草酸亚铁沉淀,洗涤干燥后得到电池级草酸亚铁。
[0023]
在上述技术方案的基础上,本发明还可以做如下改进:
[0024]
进一步,步骤(1)中无机酸为硫酸、盐酸和硝酸中至少一种。
[0025]
采用上述进一步技术方案的有益效果为:理论上来讲,所有可以与碳酸亚铁反应获得亚铁离子、且不与亚铁离子产生沉淀的酸溶液都可以作为浸出剂,但从从化工生产的角度而言,为了有效降低生产成本,需要在较短时间的反应时间内尽可能的实现亚铁的高效浸出,硫酸、盐酸和硝酸三种无机酸与碳酸亚铁之间的反应速度快,可采用其中的一种或者其中2-3种酸混合溶液作为优选的浸出剂。
[0026]
进一步,步骤(1)中无机酸为硫酸。
[0027]
采用上述进一步技术方案的有益效果为:在实际生产过程中,盐酸对设备腐蚀性较强、高浓度的硝酸盐溶液在高温条件下容易分解,所以硫酸可作为最优化的浸出剂选择。
[0028]
进一步,步骤(1)中菱铁矿的粒度≥100目。
[0029]
采用上述进一步技术方案的有益效果为:矿石浸出过程为液固反应,矿石粒径越小,比表面积越大,与浸出剂的接触面积面大,浸出速率越高;但是矿石粒径越小,其粉碎的能耗越高。因此,综合考虑,菱铁矿的粒度不低于100目即可。
[0030]
进一步,步骤(1)中浸出反应的温度为70-100℃,浸出时间≥3h。
[0031]
采用上述进一步技术方案的有益效果为:浸出反应的反应速率随温度的升高而增大,升高温度可加快亚铁的浸出速率,缩短浸出时间,减小浸出反应器体积,上述温度刚好适中。
[0032]
进一步,步骤(1)中无机酸溶液和菱铁矿的液固比为1-10:1。
[0033]
采用上述进一步技术方案的有益效果为:菱铁矿浸出过程中,生产相同质量的硫酸亚铁,浸出液中亚铁的浓度越高,所需溶液的流通量越小、生产设备也越小,成本越低;但是浸出液中亚铁的浓度越高,溶液的粘稠度越大,浸出效果越差,使亚铁回收率降低。因此,
把浸出液中的亚铁浓度控制在40-100g/l,按照菱铁矿中铁含量为10-40mt%的范围核算,无机酸溶液与菱铁矿配置成的矿浆液固比为1-10:1时为最优。
[0034]
进一步,步骤(1)中无机酸中氢离子和菱铁矿中铁的摩尔比为2.2-3:1。
[0035]
采用上述进一步技术方案的有益效果为:菱铁矿浸出过程中,无机酸溶液浓度浓度越高、浸出后氢离子残留量越大,碳酸亚铁浸出越彻底,亚铁浸出率越高,但残余酸浓度越高,设备腐蚀性越大、杂质浸出率越高,且不利于步骤(2)中初级草酸亚铁的生成。因此,综合考虑,无机酸的用量为理论酸耗量(根据酸与碳酸亚铁之间的化学反应方程式,碳酸亚铁全部浸出时所需的酸的总量)的1.1-1.5倍,即无机酸中氢离子和菱铁矿中铁的摩尔比为2.2-3:1。
[0036]
进一步,步骤(2)中草酸和分离液一中亚铁离子的摩尔比为0.7-0.95:1。
[0037]
采用上述进一步技术方案的有益效果为:为了获得较高的亚铁沉淀率、同时草酸不过量,草酸加入量与分离液中亚铁离子的摩尔比控制在0.7-0.95。若草酸过量,则剩余的草酸会进入分离液二中,如若想循环利用分离液二,将分离液二返回步骤(1)中,在步骤(1)的浸出过程中,草酸会直接和浸出的亚铁反应转化为草酸亚铁沉淀,进入浸出之后的矿渣中,难以以亚铁离子的形式分离出来,导致亚铁回收率降低。
[0038]
进一步,步骤(2)中沉淀反应的温度≥30℃,反应时间≥0.5h。
[0039]
进一步,步骤(2)中分离液二补加无机酸后,返回步骤(1)中重复使用,形成循环工艺。
[0040]
采用上述进一步技术方案的有益效果为:循环工艺能够实现资源的有效利用,减少成本。
[0041]
进一步,步骤(3)中草酸溶液和初级草酸亚铁制得浆液的液固比为3-10:1,草酸和初级草酸亚铁中铁的摩尔比为3-5:1。
[0042]
采用上述进一步技术方案的有益效果为:初级草酸亚铁与草酸溶液制浆所得浆液的液固比越小,所需浆液的流通量越小、生产设备也越小,成本越低;但是草酸溶液的浓度越高,溶液粘度越大,反应效果越差,且容易形成草酸结晶。因此,草酸溶液与初级草酸亚铁配置成的矿浆液固比为3-10:1。当草酸和初级草酸亚铁中铁的摩尔比为3-5:1时,能够将铁离子充分的转化为络合物形式,且溶液中存在游离的草酸根,确保钙、镁和重金属仍以草酸盐沉淀的形式存在。
[0043]
进一步,步骤(3)中氧化剂为氧气、空气或双氧水。
[0044]
采用上述进一步技术方案的有益效果为:使用的氧化剂首选需满足以下两个条件下:
①
可以将亚铁氧化为三价铁离子;
②
不会将草酸氧化分解为二氧化碳。其次,在实际生产过程中,为了提高最终所得草酸亚铁的纯度,还必须尽可能减少氧化剂所引入的其他杂质。因此,综合考虑,优选氧气、空气和双氧水三种氧化剂。
[0045]
进一步,步骤(4)中固液分离后的分离液补加草酸后,返回步骤(3)中重复使用,形成循环工艺。
[0046]
采用上述进一步技术方案的有益效果为:循环工艺能够实现资源的有效利用,减少成本。
[0047]
进一步,步骤(4)中还原处理通过将分离液三进行紫外线照射实现还原。
[0048]
进一步,步骤(4)中还原处理通过在分离液三中加入碳和氢组成的还原剂实现还
原。
[0049]
采用上述进一步技术方案的有益效果为:一切能够将三价铁还原为二价铁的物质都可以用还原剂,但是该工艺为循环工艺,还原剂带入的其他杂质和元素会在循环过程中累积,并最终降低草酸亚铁的品质。因此,首选碳和氢组成的还原剂,反应过程中,还原剂中的碳转化为二氧化碳、氢转化为水,不会残留其他杂质。
[0050]
进一步,还原剂为抗坏血酸、柠檬酸或苹果酸。
[0051]
本发明具有以下有益效果:
[0052]
1、本发明以低品位菱铁矿为原料,直接合成草酸亚铁,缩短了工艺流程,实现了低品位菱铁矿的高效资源化利用,降低草酸亚铁的生产成本。
[0053]
2、本发明采用草酸亚铁(二价铁固体沉淀物)与草酸铁(溶液态三价铁络合物)的物相转化,实现两次除杂,达到去除碱金属(钾钠)、钙镁和重金属的目的,整个过程中无需额外的净化剂加入,草酸亚铁纯度高(电池级),副产物少。
[0054]
3、本发明为闭路循环工艺,溶液循环利用,无废水外排,清洁生产水平高,环保效益显著。
附图说明
[0055]
图1为本发明的工艺流程图。
具体实施方式
[0056]
以下结合附图对本发明的原理和特征进行描述,所举实例只用于解释本发明,并非用于限定本发明的范围。实施例中未注明具体条件者,按照常规条件或制造商建议的条件进行。所用试剂或仪器未注明生产厂商者,均为可以通过市售购买获得的常规产品。
[0057]
实施例1:
[0058]
一种利用菱铁矿制备草酸亚铁的方法,包括以下步骤:
[0059]
(1)矿石浸出:将100kg低品位的菱铁矿研磨成粒度100目的细颗粒,加入稀硫酸溶液中,于80℃条件下,进行浸出反应4h,使菱铁矿中的碳酸铁转化为可溶性的亚铁离子;其中,稀硫酸溶液和菱铁矿的液固比为8:1,硫酸和菱铁矿中铁的摩尔比为1.3:1;
[0060]
(2)液固分离:将步骤(1)所得的浆液进行压滤,得到矿渣和含有硫酸亚铁的分离液一;
[0061]
(3)草酸沉铁(除钾钠):在分离液一中加入草酸,于30℃条件下,进行沉淀反应0.5h,然后固液分离,得到初级草酸亚铁和分离液二;其中,草酸和分离液一中亚铁离子的摩尔比为0.9:1;
[0062]
(4)分离液回用:将分离液二补加硫酸后,返回步骤(1)中重复使用,形成循环工艺;
[0063]
(5)草酸亚铁制浆:将初级草酸亚铁加入到草酸溶液中进行制浆,获得草酸亚铁浆液;其中,草酸溶液和初级草酸亚铁制得浆液的液固比为5:1,草酸和初级草酸亚铁中铁的摩尔比为3.5:1;
[0064]
(6)亚铁氧化:在草酸亚铁浆液中加入双氧水,将亚铁转化为三价铁离子,草酸亚铁溶解变为草酸铁络合物;
[0065]
(7)液固分离(除钙镁、重金属):将步骤(6)所得的溶液进行精密过滤,得到滤渣和分离液三;
[0066]
(8)还原沉铁:将分离液三进行紫外照射,使三价铁离子还原为二价铁离子,产生草酸亚铁沉淀,然后固液分离后,得到草酸亚铁沉淀和含草酸的分离液;
[0067]
(9)草酸亚铁回收:得到的草酸亚铁沉淀经洗涤、干燥后,得到电池级草酸亚铁;
[0068]
(10)溶液循环:向步骤(8)所得的分离液中补加草酸后,返回步骤(5)中,形成循环工艺。
[0069]
实施例2:
[0070]
一种利用菱铁矿制备草酸亚铁的方法,包括以下步骤:
[0071]
(1)矿石浸出:将100kg低品位的菱铁矿研磨成粒度100目的细颗粒,加入稀硫酸溶液中,于70℃条件下,进行浸出反应5h,使菱铁矿中的碳酸铁转化为可溶性的亚铁离子;其中,稀硫酸溶液和菱铁矿的液固比为1:1,硫酸和菱铁矿中铁的摩尔比为1.1:1;
[0072]
(2)液固分离:将步骤(1)所得的浆液进行压滤,得到矿渣和含有硫酸亚铁的分离液一;
[0073]
(3)草酸沉铁(除钾钠):在分离液一中加入草酸,于30℃条件下,进行沉淀反应0.6h,然后固液分离,得到初级草酸亚铁和分离液二;其中,草酸和分离液一中亚铁离子的摩尔比为0.7:1;
[0074]
(4)分离液回用:将分离液二补加硫酸后,返回步骤(1)中重复使用,形成循环工艺;
[0075]
(5)草酸亚铁制浆:将初级草酸亚铁加入到草酸溶液中进行制浆,获得草酸亚铁浆液;其中,草酸溶液和初级草酸亚铁制得浆液的液固比为3:1,草酸和初级草酸亚铁中铁的摩尔比为4:1;
[0076]
(6)亚铁氧化:在草酸亚铁浆液中持续通入空气,将亚铁转化为三价铁离子,草酸亚铁溶解变为草酸铁络合物;
[0077]
(7)液固分离(除钙镁、重金属):将步骤(6)所得的溶液进行精密过滤,得到滤渣和分离液三;
[0078]
(8)还原沉铁:在分离液三中加入抗坏血酸,使三价铁离子还原为二价铁离子,产生草酸亚铁沉淀,然后固液分离后,得到草酸亚铁沉淀和含草酸的分离液;
[0079]
(9)草酸亚铁回收:得到的草酸亚铁沉淀经洗涤、干燥后,得到电池级草酸亚铁;
[0080]
(10)溶液循环:向步骤(8)所得的分离液中补加草酸后,返回步骤(5)中,形成循环工艺。
[0081]
实施例3:
[0082]
一种利用菱铁矿制备草酸亚铁的方法,包括以下步骤:
[0083]
(1)矿石浸出:将100kg低品位的菱铁矿研磨成粒度100目的细颗粒,加入稀硫酸溶液中,于100℃条件下,进行浸出反应3h,使菱铁矿中的碳酸铁转化为可溶性的亚铁离子;其中,稀硫酸溶液和菱铁矿的液固比为10:1,硫酸和菱铁矿中铁的摩尔比为1.5:1;
[0084]
(2)液固分离:将步骤(1)所得的浆液进行压滤,得到矿渣和含有硫酸亚铁的分离液一;
[0085]
(3)草酸沉铁(除钾钠):在分离液一中加入草酸,于30℃条件下,进行沉淀反应
0.5h,然后固液分离,得到初级草酸亚铁和分离液二;其中,草酸和分离液一中亚铁离子的摩尔比为0.95:1;
[0086]
(4)分离液回用:将分离液二补加硫酸后,返回步骤(1)中重复使用,形成循环工艺;
[0087]
(5)草酸亚铁制浆:将初级草酸亚铁加入到草酸溶液中进行制浆,获得草酸亚铁浆液;其中,草酸溶液和初级草酸亚铁制得浆液的液固比为10:1,草酸和初级草酸亚铁中铁的摩尔比为5:1;
[0088]
(6)亚铁氧化:在草酸亚铁浆液中通入氧气,将亚铁转化为三价铁离子,草酸亚铁溶解变为草酸铁络合物;
[0089]
(7)液固分离(除钙镁、重金属):将步骤(6)所得的溶液进行精密过滤,得到滤渣和分离液三;
[0090]
(8)还原沉铁:在分离液三中加入苹果酸,使三价铁离子还原为二价铁离子,产生草酸亚铁沉淀,然后固液分离后,得到草酸亚铁沉淀和含草酸的分离液;
[0091]
(9)草酸亚铁回收:得到的草酸亚铁沉淀经洗涤、干燥后,得到电池级草酸亚铁;
[0092]
(10)溶液循环:向步骤(8)所得的分离液中补加草酸后,返回步骤(5)中,形成循环工艺。
[0093]
对比例1
[0094]
一种利用菱铁矿制备草酸亚铁的方法,包括以下步骤:
[0095]
(1)矿石浸出:将100kg低品位的菱铁矿研磨成粒度100目的细颗粒,加入稀硫酸溶液中,于80℃条件下,进行浸出反应4h,使菱铁矿中的碳酸铁转化为可溶性的亚铁离子;其中,稀硫酸溶液和菱铁矿的液固比为8:1,硫酸和菱铁矿中铁的摩尔比为1.3:1;
[0096]
(2)液固分离:将步骤(1)所得的浆液进行压滤,得到矿渣和含有硫酸亚铁的分离液一;
[0097]
(3)草酸沉铁(除钾钠):在分离液一中加入草酸,于30℃条件下,进行沉淀反应0.5h,然后固液分离,得到草酸亚铁;其中,草酸和分离液一中亚铁离子的摩尔比为0.9:1。
[0098]
试验例
[0099]
一、将实施例1-3制得的草酸亚铁进行铁回收率检测,铁的回收率的检测方法为:将菱铁矿和草酸亚铁中铁含量(质量百分比)通过三氯化钛还原重铬酸钾滴定法测定(gb/t 6730.65-2009铁矿石全铁含量的测定),然后按照下列公式计算铁回收率,结果见表1,由表1可知,用本发明的方法利用菱铁矿制备草酸亚铁,铁回收率高达98%以上。
[0100][0101]
表1铁回收率
[0102]
项目铁回收率实施例198.3%实施例298.5%实施例398.3%
[0103]
二、将实施例1-3和对比例1制得的草酸亚铁进行纯度检测,纯度的检测方法为:将
制得的草酸亚铁通过电感耦合等离子体原子发射光谱法(icp-aes)测定各组分的含量,结果见表2,由表2可知,采用本发明的方法利用菱铁矿制备草酸亚铁,制得的草酸亚铁纯度高,可达到99%以上。
[0104]
表2草酸亚铁纯度
[0105]
草酸亚铁成分(%)实施例1实施例2实施例3对比例1fec2o4·
h2o99.499.699.594.5钾(k)0.00040.00020.00030.134钠(na)0.00020.00040.00030.114钙(ca)0.00070.00040.00050.107镁(mg)0.00080.00050.00050.429铜(cu)0.00040.00030.00030.214锌(zn)0.00050.00050.00020.176镍(ni)0.00050.00040.00050.096铬(cr)0.00050.00030.00020.064
[0106]
以上所述仅为本发明的较佳实施例,并不用以限制本发明,凡在本发明的精神和原则之内,所作的任何修改、等同替换、改进等,均应包含在本发明的保护范围之内。