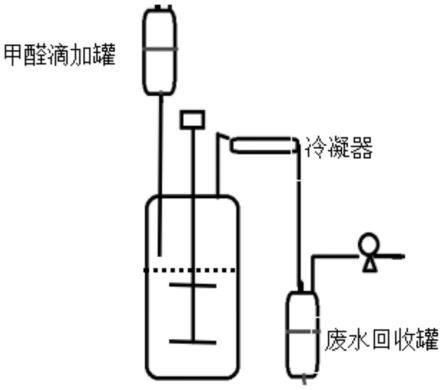
1.本技术涉及高分子材料技术领域,特别是涉及一种热塑性酚醛树脂及其制备工艺。
背景技术:2.热塑性树脂通常由甲醛和过量的苯酚在酸催化剂作用下,经缩合而成的有机高分子化合物。在热塑性树脂的制备过程中,一般采用37wt%的甲醛水溶液,导致引入大量的水分,而且在甲醛和苯酚进行缩合反应过程中会生成水,为获得最终的热塑性树脂,因此,需进行脱水。
3.现有制备工艺中往往是在甲醛和苯酚反应结束后,通过常压或减压方式脱除水分,但需要消耗大量的能量和时间,特别在工业化生产中,反应釜的体积为10~20立方,反应结束后存在大量的水需脱出,而导致脱水时间长的原因主要包括:(1)反应釜的挥发通道小,(2)有水存在的情况下,反应釜内的温度基本在100℃,使得反应釜内的树脂黏粘度大,增加了脱水难度;(3)为避免热塑性树脂变性,生产车间大都采用高压蒸汽加热,且温度160~170℃,影响脱水速率。
技术实现要素:4.鉴于上述问题,本技术提供了一种热塑性酚醛树脂及其制备工艺。
5.本技术中,热塑性酚醛树脂的制备工艺包括:
6.步骤s100、混合酚类化合物和催化剂,并升温至预定值,得到体系a;
7.步骤s200、边向体系a滴加甲醛溶液进行反应,边对反应体系进行脱水,至反应结束后得到体系b;
8.步骤s300、反应结束后,对体系b进行脱水、脱酚;
9.步骤s400、冷却、出料,得到所述热塑性酚醛树脂。
10.与现有制备工艺不同,本技术为边反应边脱水(步骤s200),由于在在催化剂的作用下,酚类化合物和甲醛溶液中的甲醛发生缩合反应,缩合反应为放热过程,且会生产水,本技术充分利用放热过程中的热量使水分蒸发(挥发),当反应结束时,即甲醛基本被反应完时,达到预期的脱水效果。
11.为避免脱水带走大量的甲醛,应控制甲醛和酚类化合物的反应速率以及加入甲醛的方式,步骤s100中,预定值是甲醛和酚类化合物能够快速反应的理想温度,步骤s200中,采用滴加方式,控制单位时间内甲醛的滴加量,保证单位时间内滴加的甲醛能被快速反应掉,防止甲醛被蒸发或被水汽带走。此外,脱水使产物水减少,从而打破反应平衡,有利于缩合反应的进行。
12.经步骤s300得到的体系b继续进行脱水,以进一步脱除体系b残留的水分,然后进行脱酚,冷却,出料得到高纯度的热塑性树脂(步骤s400)。
13.可选的,所述酚类化合物为预热熔融的酚类化合物。
14.可选的,所述催化剂为酸催化剂,优选为强酸催化剂,有利于提升酚类化合物和甲醛的反应速率,使得甲醛滴加到反应釜内可以进行迅速被利用,有效降低甲醛在脱水中的损耗。
15.可选的,所述酸催化剂为草酸、对甲苯磺酸、十二烷基苯磺酸和硫酸中的至少一种。
16.可选的,所述酚类化合物为苯酚,所述甲醛溶液为甲醛水溶液,例如质量浓度为37wt%甲醛水溶液。
17.可选的,所述酚类化合物和甲醛的摩尔比为1:0.5~0.9。
18.可选的,所述催化剂和苯酚的质量比为0.2~5:100。
19.可选的,步骤s200中,所述脱水为:从开始滴加甲醛,至滴加结束后继续保温20~40min。
20.可选的,步骤s200中,所述脱水为:从开始滴加甲醛,至滴加结束后继续保温30min。
21.步骤s300中,保温结束后继续脱水,至160~170℃结束脱水,且脱水的温度大于步骤s200中脱水的温度;
22.步骤200和步骤300中的脱水均为常压脱水。
23.可选的,步骤s100中,所述预定值为110~140℃;
24.步骤s200中,所述甲醛溶液的滴加时间为1~3h,所述脱水的温度为110~140℃。
25.预定值在110~140℃条件下,甲醛滴加到反应釜内迅速与酚类化合物发生缩合反应,根据甲醛与苯酚的反应速度,控制甲醛滴加速度,使得甲醛在单位时间内甲醛的反应速度,滴加速度脱水速度达到平衡,即单位时间内甲醛的滴加量和反应量一致,反应后的甲醛水溶液中的水在常压脱水过程中脱出反应釜。此外,甲醛和苯酚反应过程中会放出大量的热,该热量可以有利于甲醛中的水能被快速脱出,提高能量利用率。此外,在110~140℃条件下,反应釜内含水量低,反应釜粘度低,甲醛中的水可以被快速脱出。
26.以10立方反应釜为例,现有制备工艺中,苯酚和甲醛保温回流需要3h,反应结束后进行常压脱水至120℃需要5h,常压脱水到150℃需要2h,减压脱酚需要2h,总时长12h。而本技术以120℃进行边滴加甲醛边常压脱水为例,滴加甲醛3h,滴加结束后从120到150℃需要2h,减压脱酚2h,总时长7h。反应效率提高近1倍左右。
27.又例如2立方反应釜中,所述热塑性酚醛树脂的制备总时间不大于6.5h,生产效率为大于200kg/h。
28.可选的,步骤s300中,脱酚的方式为真空脱酚。
29.可选的,所述真空脱酚的条件为:真空度小于-0.095mpa,温度为170~180℃。
30.可选的,步骤s200中,所述脱水的方式为蒸馏。
31.可选的,步骤s200中,边滴加甲醛边脱水的方式为:在滴加甲醛的过程中,将反应釜切换成蒸馏状态;参见图1,反应釜至少具有两个通口,其中一通口与甲醛滴加罐连接,用于滴加甲醛;另一通口与冷凝器连接,当在滴加甲醛的过程中,反应釜与冷凝器连接的通口打开,反应釜中蒸发的水从通口脱出,从而实现边滴加甲醛边脱水。
32.本技术还提供了一种热塑性酚醛树脂,采用任一所述热塑性酚醛树脂的制备工艺制得。
33.与现有技术相比,本技术提供的制备工艺通过边反应边脱水,将缩合反应产生的热量用于脱水,不仅缩短了热塑性酚醛树脂的制备时间,而且有效降低生产能耗,达到节能减排效果以及降低生产成本。
附图说明
34.图1为本技术中热塑性酚醛树脂的制备工艺图。
具体实施方式
35.为了便于本领域技术人员更好地理解本发明的技术方案,下面结合具体实施例对本发明作进一步的说明,但本发明不仅限于此。
36.实施例1
37.(1)将预热熔融的苯酚1500kg用专用泵加入高位计量罐,计量加入到2m3反应釜内,接着加入草酸15kg,温度升至130℃,得到体系a;
38.(2)反应釜置于脱水装置状态(常压状态),开始滴加37wt%的甲醛溶液1100kg,并于3小时内滴加完成;滴加甲醛过程中,根据脱水情况,温度控制在130℃,滴加结束后保温30min,保温结束后,得到体系b,其中脱出900kg水;
39.(3)对体系b进行常压脱水,脱水温度为170℃,脱水时间为2小时,再进行真空脱酚,真空脱酚的温度为180℃,真空度小于-0.095mpa,脱酚时间1小时;
40.(4)冷却、出料得到淡黄色透明固体树脂1606kg,反应总时间6.5小时。
41.实施例2
42.(1)将预热熔融的苯酚1500kg用专用泵加入高位计量罐,计量加入到2m3反应釜内,接着加入对甲苯磺酸3kg,温度升至120℃,得到体系a;
43.(2)反应釜置于脱水装置状态(常压状态),开始滴加37%的甲醛溶液788kg,并于1小时内滴加完成。甲醛滴加过程中,根据脱水情况,温度控制在120℃,滴加结束后保温30min,保温结束后,得到体系b,脱出600kg水;
44.(3)对体系b进行常压脱水,至160℃结束脱水,脱水为2.5小时,再进行真空脱酚,温度为180℃,真空度小于-0.095mpa,脱酚时间1小时;
45.(4)冷却、出料得到淡黄色透明固体树脂1436kg,总反应时间5小时。
46.实施例3
47.(1)将预热熔融的苯酚1500kg用专用泵加入高位计量罐,计量加入到2m3反应釜内,接着加入十二烷基苯磺酸5kg,温度升至140℃,得到体系a;
48.(2)反应釜置于脱水装置状态(常压状态),开始滴加37%的甲醛溶液930kg,并于2小时内滴加完成,甲醛滴加过程中,根据脱水情况,温度控制在140℃,滴加结束后保温30min,保温结束后,得到体系b,脱出760kg水;
49.(3)对体系b进行常压脱水,脱水温度为160℃,脱水时间为2.5小时,在进行真空脱酚,温度为180℃,真空度小于-0.095mpa,脱酚时间1小时;
50.(4)放出产品,冷却后得到淡黄色透明固体树脂1596kg,总反应时间为6小时。
51.实施例4
52.(1)将预热熔融的苯酚1500kg用专用泵加入高位计量罐,计量加入到2m3反应釜
内,接着加入硫酸3kg,温度升至130℃后,得到体系a;
53.(2)反应釜置于脱水装置状态(常压状态),开始滴加37%的甲醛溶液1040kg,并于2小时内滴加完成,甲醛滴加过程中,根据脱水情况,温度控制在130℃,滴加结束后保温30min,保温结束后,得到体系b,脱出850kg;
54.(3)对体系b进行常压脱水,脱水温度为170℃,脱水时间为2.5小时,再进行真空脱酚,温度为180℃,真空度小于-0.095mpa,脱酚时间1小时;
55.(4)冷却后得到淡黄色透明固体树脂1577kg,总反应时间6小时。
56.实施例5
57.(1)将预热熔融的苯酚1500kg用专用泵加入高位计量罐,计量加入到2m3反应釜内,接着加入硫酸3kg,温度升至110℃后,得到体系a;
58.(2)反应釜置于脱水装置状态(常压状态),开始滴加37%的甲醛溶液910kg,并于3小时内滴加完成,甲醛滴加过程中,根据脱水情况,温度控制在110℃,滴加结束后保温30min;保温结束后,得到体系b,脱出700kg水;
59.(3)对体系b进行常压脱水,温度为160℃,脱水时间2小时,再进行真空脱酚,温度为180℃,真空度小于-0.095mpa,减压脱酚1小时。
60.(4)冷却、出料得到淡黄色透明固体树脂1550kg,总反应时间6.5小时。
61.对比例1
62.将预热熔融的苯酚1000kg用专用泵加入高位计量罐,计量加入到2m3反应釜内,接着加入草酸10kg,温度升至100℃后,开始滴加37%的甲醛溶液730kg,并于1小时内滴加完成,滴加结束后开始100℃回流保温1.5小时。回流保温结束后,开始常压脱水温度至160℃,脱水时间为5小时,真空脱酚至180℃(真空度小于-0.095mpa),真空脱水时间为1小时。放出产品,冷却后得到淡黄色透明固体树脂1066kg,总反应时间8.5小时。
63.表1实施例1~5和对比例1树脂指标和产量对比
[0064][0065][0066]
对实施例1~5和对比例1制备的酚醛树脂的软化点、游离酚含量、反应釜使用率、生产时间、产量以及生产效率进行比较,由表1可知,实施例1~5的生产效率高于对比例1的。相比于对比例1,实施例1的产生时间短且产量高,生产效率提高了97%,表明大幅度提
高了热塑性酚醛树脂的产量和产能。
[0067]
上述的对实施例的描述是为了便于该技术领域的普通技术人员能理解和使用发明,本技术所属领域的技术人员还可以对上述实施方式进行适当的变更和修改。因此,本技术并不局限于上面揭示和描述的具体实施方式,对本技术的一些修改和变更也应当落入本技术的权利要求的保护范围内。