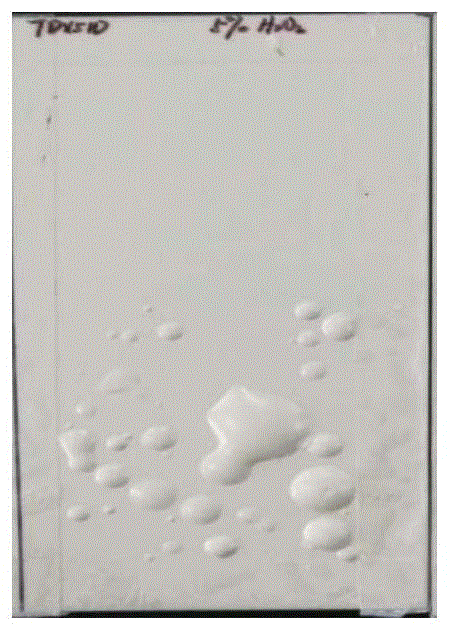
本发明属于金属材料表面处理领域,涉及低碳钢彩色预涂钢板的生产工艺,具体为耐氧化性消毒剂腐蚀的功能彩涂钢板及其制造方法。
背景技术:
:随着彩涂钢板生产、加工应用技术的发展,各类工业厂房围护用彩涂钢板的品种结构也在不断优化升级。在医疗卫生、食品加工等特殊领域,每年都有大量生产车间的新建或改造,对彩涂钢板的需求量超过5万吨/年。但在这些特殊行业,由于对环境细菌滋生、洁净度的控制要求比较高,需要定期使用双氧水、次氯酸钠等消毒剂对车间或办公区域等进行消毒、杀菌,导致其建筑围护系统长期接触强氧化剂,因此对维护系统用材提出了更苛刻的要求。目前大量使用的普通聚酯类彩涂钢板在耐双氧水以及其他消毒剂方面的性能并不能满足实际环境需求,在该情况下,一般使用三至五年彩涂板表面则会出现起泡、粉化破坏,严重影响室内建筑物使用寿命。另外,有些企业为保证产品性能则会选择氟碳涂层甚至不锈钢板用以代替普通聚酯类彩涂钢板,从而带来成本方面的大幅增加。基于此,通过对预涂层中涂料成分进行改良并对生产工艺进行控制,从而制造出一种耐消毒剂用特殊功能彩涂钢板,以满足目前市场所需。经检索,中国专利申请号为201420441214.8,申请公开日为2014年08月06日的专利申请文件公开了一种制药车间用抗vhp氧化彩涂板。该专利主要介绍一种耐雾化双氧水的彩钢板生产工艺。钢板镀层及涂层结构包括:镀锌板、第一钝化层、抗vhp氧化预涂层、抗vhp氧化精涂层、第二钝化层、抗vhp氧化背涂层。方案通过对彩涂板的改进,不仅使钢板自身具有良好的弯曲加工性能,而且还具有抗vhp氧化特性,在气化双氧水环境中涂层附着力好,不失光泽,不粉化开裂,无起泡现象。但对于医疗卫生领域,多数室内消毒除采用双氧水外,仍会以次氯酸钠作为消毒剂主要成分之一。在此情况下,该专利中所提彩钢板并不满足这一特殊需求,而本专利所涉及的彩钢板不仅具有较强抵抗双氧水能力(尤其为30%高浓度双氧水溶液),而且能够有效抵抗次氯酸钠腐蚀破坏。除此之外,该类产品还具有良好的耐酸碱以及高温高湿性能,能够满足更多场所的实际使用需求,属一款竞争力较强的个性化、功能型彩涂产品。再如,中国专利申请号为201710123403.9,申请公开日为2017年06月30日的专利申请文件公开了一种耐腐蚀、耐酸碱彩板制造方法。该专利的制造方法包括如下步骤:步骤1、预处理:以镀锌钢板或者镀铝锌钢板为基板,表面预处理为脱脂清洗;步骤2、初涂:经过预处理之后的带钢进入到化学涂机,在带钢表面涂一层水基铬化物,再进入辊涂机进行初涂:正面底漆高耐蚀聚氨酯底漆,背面底漆高耐蚀环氧底漆;步骤3、精涂:经过初涂后的带钢通过转向辊进入精涂机进行精涂:正面面漆高耐蚀不饱和聚酯漆,背面面漆高耐蚀环氧背漆,该发明方法依托正反面涂层中量产化的纳米颗粒,通过研磨工艺达到纳米状态,超细的纳米颗粒有效的消除大粒径团聚体带来的空隙缺陷,热熔自修复材料消除了常规涂层中溶剂孔道,形成超强封闭能力和耐酸碱能力,延长了彩板的使用寿命。但是,该类产品的优势在于对酸碱的耐受力较强,但是是否耐强氧化剂,如双氧水、次氯酸钠等的耐腐蚀性没有涉及。因此,亟需开发一种耐氧化性消毒剂腐蚀的彩涂钢板及其制造工艺,不仅对氧化性消毒剂类腐蚀性介质有较好的防御性,而且具备耐酸碱及高温高湿性能。技术实现要素:1、要解决的问题针对现有彩涂钢板不能满足耐强氧化剂腐蚀的问题,本发明提供了一种耐氧化性消毒剂腐蚀的环氧底漆以及耐氧化性消毒剂腐蚀的改性聚酯面漆,两者配合使用形成耐氧化性消毒剂腐蚀的彩涂钢板,通过对彩涂钢板上涂层中涂料成分进行改良,从而得到耐氧化性消毒剂腐蚀的彩涂钢板。本发明还提供了一种耐氧化性消毒剂腐蚀的彩涂钢板制造工艺,目的在于对生产工艺进行控制,制造出耐氧化性消毒剂腐蚀的彩涂钢板2、技术方案为解决上述问题,本发明采用如下的技术方案。一种耐氧化性消毒剂腐蚀的环氧底漆,主要包括环氧树脂、着色颜料和防锈颜料、流平剂、润湿剂、消泡剂和成膜助剂,其各组分的质量份数为:进一步地,所述环氧树脂为多元醇树脂,优选建筑环氧树脂,其中,多元醇树脂为采用双酚a、环氧氯丙烷、液碱和添加剂合成而来的,具有附着性好、加工韧性优良特点。进一步地,所述着色颜料的主要成分包括钛白粉,还包括锌白、以及少量红、黄、炭黑颜料。进一步地,所述防锈颜料包括化学性防锈颜料和/或物理性防锈颜料,其中,化学性防锈颜料包括锌粉或锌铬黄,物理性防锈颜料包括铝粉,当化学性防锈颜料和物理性防锈颜料混合使用时,两者的添加质量比为3:2。一种耐氧化性消毒剂腐蚀的改性聚酯面漆,主要包括第一饱和聚酯、第二改性饱和聚酯、着色颜料、流平剂、润湿剂、消泡剂、耐介质腐蚀特殊助剂,其各组分的质量份数为:进一步地,所述第二改性饱和聚酯的主要成分为三聚氰胺、异氰酸酯、微细成膜粒子、位阻胺和普通聚酯,普通聚酯与其他成分相配合形成致密性较强、耐侯性优良的改性聚酯。进一步地,所述着色颜料的主要成分包括钛白粉,还包括锌白、以及少量红、黄、炭黑颜料组成。进一步地,所述耐介质腐蚀特殊助剂主要包括丙二醇苯醚、酯醇、耐氧化性助剂和含氟表面活性剂。一种耐氧化性消毒剂腐蚀的彩涂钢板,包括基板,所述基板的正面由下至上依次涂覆有第一保护膜、环氧底漆层,环氧底漆层上还涂覆改性聚酯面漆层;所述基板的背面由上至下依次涂覆有第二保护膜和环氧背漆层。进一步地,所述基板为热浸镀锌钢板。进一步地,所述热浸镀锌钢板的镀层重量为120g/m2。进一步地,所述热浸镀锌钢板中钢板的主要化学成分重量百分比为:c:≤0.20%;si:≤0.05%;mn:≤1.30%;p:≤0.02%;s:≤0.02%;al:≤0.07%。进一步地,所述第一保护膜和第二保护膜的厚度为一般情况下控制单面膜重为50~100mg/m2。进一步地,所述环氧底漆层的厚度为5~7μm。进一步地,所述改性聚酯面漆层的厚度为15~17μm。进一步地,所述环氧背漆层的厚度为5~12μm。一种耐氧化性消毒剂腐蚀的彩涂钢板制造工艺,步骤为:首先清洗基板的表面,然后将清洗后的基板的表面进行钝化处理,使其表面生成第一保护膜和第二保护膜,用以减缓基板的腐蚀和增强基板与涂层的粘附性,再于第一保护膜上涂覆环氧底漆、第二保护膜上涂覆环氧背漆,固化后分别形成环氧底漆层和环氧背漆层,最后在环氧底漆层上涂覆改性聚酯面漆,固化后形成改性聚酯面漆层。进一步地,耐氧化性消毒剂腐蚀的彩涂钢板制造工艺的步骤为:s1、清洗:将带有油脂的基板进行喷淋碱洗、漂洗,用以去除基板表面的油污以及杂质,使基板具有清洁的表面;s2、前处理:将清洗后的基板送入化学辊涂段对其表面进行钝化处理,其中钝化液主要成分包括三价铬成分、六价铬成分以及二氧化硅等,带钢通过挤干辊挤干和气刀后进人化学辊涂段对带钢表面进行钝化处理,钝化温度为130±10℃,使其表面生成第一保护膜和第二保护膜,目的在于提高和改善基板的防腐性与涂层的粘附性,用以保证基板的耐腐蚀性及与涂层的粘附性;s3、初涂:将经过钝化处理的基板送入化学干燥炉,使得基板最高出炉温度为80℃;然后将基板的正面涂覆环氧底漆、背面涂覆环氧背漆,再进入初涂固化炉进行固化形成环氧底漆层和环氧背漆层,初涂后的基板出炉后将其冷却到50℃以下,再通过挤干辊和气刀去除基板表面水分;s4、精涂:于环氧底漆层上精涂改性聚酯面漆,再进入精涂固化炉进行固化形成改性聚酯面漆层,冷却后得到耐氧化性消毒剂腐蚀的彩涂钢板。进一步地,所述步骤s3~s4的涂覆工艺采用辊涂。进一步地,所述步骤s3~s4的冷却方式采用水淬装置进行冷却。进一步地,所述步骤s4得到的彩涂钢板还需要进行检验、卷取工序,其中检验是指对涂层的常规性能如膜厚、色差、t弯、光泽、mek、铅笔硬度等具体项目进行线上验证。3、有益效果相比于现有技术,本发明的有益效果为:(1)本发明主要通过对彩涂钢板的涂层底漆、面漆成分进行改良从而提高漆膜致密性及耐腐蚀性,并对其进行耐双氧水及次氯酸钠性能、耐酸碱性能、耐高温高湿等性能进行评估,从而获得一种耐消毒剂用特殊功能彩涂钢板,该特殊涂层彩钢板不仅具有良好的机械加工性能,能够满足实际成型需求,还具有良好的耐消毒剂及其他腐蚀性溶液的能力,是一款针对性强、综合性能较高的产品;(2)本发明彩涂钢板的正面初涂涂层为交联密度较大且附着性良好的环氧树脂,能够有效阻止溶液渗透涂层;正面精涂涂层以聚酯树脂为主要成膜物质,通过在其中添加特殊助剂增加漆膜的致密性;背面涂层为环氧树脂,主要用于发泡所需;(3)本发明的正面环氧底漆所具有的优势主要包括以下两个方面:一是与传统聚氨酯底漆相比,其与基板的附着性得到改善;二是能够提高底漆的涂层致密性有效改善其耐化学性介质腐蚀能力;(4)本发明所涉及正面改性聚酯面漆所具有的技术特性主要包括以下几方面:一是第二改性聚酯所具有的成分能够显著提高涂层致密性,与此同时特殊性强化聚酯成分添加能够有效提升漆膜对化学性介质的耐腐蚀性;二是通过第一饱和聚酯与第二改性饱和聚酯的合理匹配使该产品在满足耐氧化性介质等其余腐蚀性介质的前提下仍能够兼顾成本方面的考虑;三是本发明通过在主要成膜物中添加有针对性的耐氧化性介质助剂能够使该产品在耐双氧水以及次氯酸钠等消毒剂方面具备明显优势,与此同时也通过在其中添加丙二醇苯醚、酯醇等成分使漆膜能够均匀稳定成膜,保证漆膜的完整、平滑性;(5)本发明所涉及的背面环氧树脂与常用背面漆的作用有相通性也有区别性,相通性是指两者主要作用在于作为发泡时所需,区别在于该专利的背面环氧漆中添加耐腐蚀性保护成分,使涂层板在不做夹芯板时仍能够具备较好的耐腐蚀性。附图说明图1为对比例中经5%h2o2浸泡144h后的彩涂钢板;图2为实施例1中经5%h2o2浸泡840h后的彩涂钢板;图3为对比例中经30%h2o2浸泡24h后的彩涂钢板;图4为实施例1中经30%h2o2浸泡24h后的彩涂钢板;图5为对比例中经5.2%naclo浸泡72h后的彩涂钢板;图6为实施例1中经5.2%naclo浸泡216h后的彩涂钢板;图7为对比例中经5%hcl浸泡24h后的彩涂钢板;图8为实施例1中经5%hcl浸泡96h后的彩涂钢板;图9为对比例中经5%naoh浸泡48h后的彩涂钢板;图10为实施例1中经5%naoh浸泡216h后的彩涂钢板;图11为实施例1中经70℃,24h耐高温后的彩涂钢板;图12为实施例1中经40℃,98%rh,1000h耐湿热试验后的彩涂钢板后的彩涂钢板;图13为实施例1与对比例在不同浓度双氧水腐蚀后性能对比情况图;图14为本发明彩涂钢板的结构示意图;图15为实施例1起泡剥离部位扫描图;图16为实施例1起泡剥离部位能谱图;图17为对比例起泡剥离部位扫描图;图18为对比例起泡剥离部位能谱图;图中:1、基板;2、第一保护膜;3、环氧底漆层;4、改性聚酯面漆层;5、第二保护膜;6、环氧背漆层。具体实施方式下面结合具体实施例和附图对本发明进一步进行描述。如表1所示为具体实施方式中使用原料的厂家信息及品名。表1使用原料品名及厂家信息实施例各实施例的一种耐氧化性消毒剂腐蚀的环氧底漆、聚酯面漆、环氧背漆的干膜成分如表2所示表2实施例及对比例的配方选取镀层重量为120g/m2(双面)的热浸镀锌钢板作为彩色预涂基板1,进行制备彩涂钢板的工艺流程:镀锌板—脱脂—清洗—钝化—正、背面底漆涂覆—固化—正面面漆涂覆—固化—冷却—检验—卷取,制成实施例1~3及对比例的彩涂钢板,其中,正面底漆的膜厚控制在5~7μm,正面面漆的膜厚控制在15~17μm,背面背漆的膜厚控制在5~12μm。具体的,实施例中耐氧化性消毒剂腐蚀的彩涂钢板制造工艺的步骤为:s1、清洗:将带有油脂的基板1进行喷淋碱洗、漂洗,用以去除基板1表面的油污以及杂质,使基板1具有清洁的表面;其中清洗工艺中前后两段脱脂采用不同浓度的脱脂剂,其中第一段浓度较高,其脱脂力度更强一些;而经过一道脱脂工序后第二道脱脂时采用的脱脂剂浓度相对较低,主要原因为此时钢带表面很大一部分的油污已被清洗干净。脱脂剂的主要成分包括:碱性成分、磷酸盐、硼酸盐、碳酸盐以及一些表面活性剂、络合剂和缓蚀剂,其余为水。其中,碱性成分可以根据实际需求选择氢氧化钠等,此处不作为本发明的发明点进行描述。s2、前处理:将清洗后的基板1送入化学辊涂段对其表面进行钝化处理,带钢通过挤干辊挤干和气刀后进人化学辊涂段对带钢表面进行钝化处理,钝化温度为130±10℃,使其表面生成第一保护膜2和第二保护膜5,目的在于提高和改善基板的防腐性与涂层的粘附性,用以保证基板的耐腐蚀性及与涂层的粘附性;其中钝化液中以铬酸、铬酸盐溶液以及二氧化硅等添加剂作为主要成分,其余为水,钝化液成分作为现有技术,本领域技术人员可以自行选择钝化液,此处不作为本发明的发明点进行描述。s3、初涂:将经过钝化处理的基板1送入化学干燥炉,使得基板1最高出炉温度为80℃;然后将基板1的正面辊涂涂覆环氧底漆、背面涂覆环氧背漆,再进入初涂固化炉进行固化形成环氧底漆层3和环氧背漆层6,初涂后的基板1出炉后将其冷却到50℃以下,再通过挤干辊和气刀去除基板1表面水分;s4、精涂:于环氧底漆层3上辊涂改性聚酯面漆,再进入精涂固化炉进行固化形成改性聚酯面漆层4,于水淬装置中进行冷却后,得到耐氧化性消毒剂腐蚀的彩涂钢板;彩涂钢板的结构如图14所示,包括基板1,所述基板1的正面由下至上依次涂覆有第一保护膜2、环氧底漆层3,环氧底漆层3上还涂覆改性聚酯面漆层4;所述基板1的背面由上至下依次涂覆有第二保护膜5和环氧背漆层6。s5、将步骤s4得到的彩涂钢板还需要进行检验、卷取工序,其中检验是指对涂层的常规性能如膜厚、色差、t弯、光泽、mek、铅笔硬度等具体项目进行线上验证。彩涂钢板的具体检验标准如下表3所示。表3彩涂钢板的检验标准其中工艺流程中各步骤的工艺参数见表4~8所示:表4清洗工艺工序碱液浓度(%)槽液温度(℃)脱脂1.0-1.555-65脱脂0.5-1.550-65漂洗/50-65漂洗/50-65漂洗/45-60表5钝化工艺钝化层固化pmt,℃钝化层涂覆量(单面),mg/m280-9550~100其中,pmt表示的是最高金属板温。表6涂覆工艺参数表7涂层设计涂层结构正面膜厚/μm背面膜厚/μm2/1≥20≥52/2≥20≥10备注:其中2/1指正面两涂,背面单涂;2/2指正面两涂,背面两涂,实施例1是采用2/1背面单涂的方式,根据实际的生产需求,可以采用背面双涂的复合膜形式,只是生产要求不同,在本发明的保护范围内,因此背面单涂还是双涂,实质上还是落在本发明的保护范围内,此处仅做简要说明,本领域技术人员可以依据客户需要选择采用哪种涂层结构。表8固化pmt其中,pmt表示的是最高金属板温。性能测试对实施例1及对比例的彩涂钢板进行性能试验,样板属性如表9所示。表9试验样板属性该类产品常规性能指标如表10所示,耐消毒剂及酸碱性能指标见表11。表10实施例1彩涂钢板常规性能表11实施例1彩涂钢板非常规性能水平(1)具体性能验证方法如下所示:a.耐溶液试验试验方法:备七只玻璃烧杯,分别配置一定量的5%hcl(盐酸)、5%naoh(氢氧化钠)、5.2%次氯酸钠、(5%、10%、20%、30%)双氧水溶液,并倒入烧杯中。提前将试验样板以及配置好的溶液放入温度为23±2℃的实验室。24小时后,将试验样板分别放入烧杯中,使试件的三分之二浸入溶液中,采用保护膜将烧杯口密封,且将蒸发皿倒扣于杯盖处。每隔24小时后取出,冲洗干净,滤纸吸干水份,观察试件表面状态。b.耐高温试验试验方法:70℃恒温放置24小时。75*150mm试样,实验完成后观察试样表面有无变色、起泡等明显变化。要求色差δe≤2.0。试验设备:高温箱c.耐湿热试验试验方案:40℃、98%湿度恒温恒湿箱放置1000小时。75*150mm试样,试验后观察样板表面要求涂层不起泡。试验设备:hs-150高低温湿热试验箱。测试结果:由图1~4所示为实施例1与对比例中的彩涂钢板耐双氧水性能测试结果,图1和图3中对比例的彩图钢板经耐双氧水性能测试后均起泡,而图2和图4显示实施例1的彩涂钢板经耐双氧水性能测试后均未起泡,图13为实施例1与对比例在不同浓度双氧水腐蚀后性能对比情况图,可知在较低浓度(5%h2o2)下实施例1的耐腐蚀时间是对比例的6倍;随着浓度提升两者之间的差距缩小,在浓度为30%h2o2腐蚀时,实施例1达到对比例的2倍,这主要是由于随着双氧水浓度的提升,其作为强氧化剂对涂层的腐蚀穿透力成数量级的增加,从而导致在较高浓度时,涂层很快起泡,以致两者之间的时间差缩小。图5和图6为实施例1与对比例耐次氯酸钠性能测试结果,图5对比例的彩涂钢板在耐次氯酸钠性能测试后起泡,而明显的,图6实施例1的彩涂钢板在耐次氯酸钠性能测试后未起泡;图7~10为实施例1与对比例中的彩涂钢板耐盐酸及氢氧化钠性能结果,图7中对比例的彩图钢板经耐酸测试后起泡,图8中实施例1的彩图钢板经耐酸测试后未起泡,图9中对比例的彩图钢板经耐碱测试后起泡,图10中实施例1的彩图钢板经耐碱测试后未起泡;图11和图12为实施例1彩涂钢板耐高温及湿热性能结果,图11中实施例1彩涂钢板经70℃,24h耐高温后,δe=0.38,图12中实施例1彩涂钢板经40℃,98%rh,1000h耐湿热试验后,δe=0.86。其中δe代表样板试验前后色差变化值大小,具体为δe=[(△l)2+(△a)2+(△b)2]1/2。l代表亮度,a代表红绿,b代表(红绿)。如果δl为正,说明试样比标样浅,如果δl为负,说明试样比标样深。如果δa为正,说明试样比标样红(或者少绿),如果为负,说明试样绿(或者少红)。如果δb为正,说明试样比标样黄(或者少蓝),如果为负,说明试样蓝(或者少黄)。测试结果如表12所示。表12实施例1与对比例耐氧化性消毒剂性能结果汇总(2)试验分析手段:采用浸泡法分别对样板进行耐双氧水、次氯酸钠腐蚀性能评估,并对其破坏部位进行扫描及能谱分析,进而验证其腐蚀路径,如图15~18所示为实施例1和对比例腐蚀破坏后的扫描及能谱分析,可以得知两者在腐蚀破坏后经扫描分析均为典型羁绊成分,无涂层残留。以上述同样的性能测试方法对实施例2和实施例3中制得的彩涂钢板进行测试,测试结果见表13。表13实施例2和3中的彩涂钢板性能测试结果测试项目实施例2实施例35%h2o2824小时内不起泡824小时内不起泡30%h2o248小时内不起泡60小时内不起泡5.2%naclo300小时内不起泡336小时内不起泡5%hcl96小时内不起泡108小时内不起泡5%naoh196小时内不起泡240小时内不起泡70℃耐高温24小时后δe=0.2624小时后δe=0.24湿热(40℃,98%rh)1000小时后δe=0.231000小时后δe=0.23本发明所述实例仅仅是对本发明的优选实施方式进行描述,并非对本发明构思和范围进行限定,在不脱离本发明设计思想的前提下,本领域工程技术人员对本发明的技术方案作出的各种变形和改进,均应落入本发明的保护范围。当前第1页1 2 3