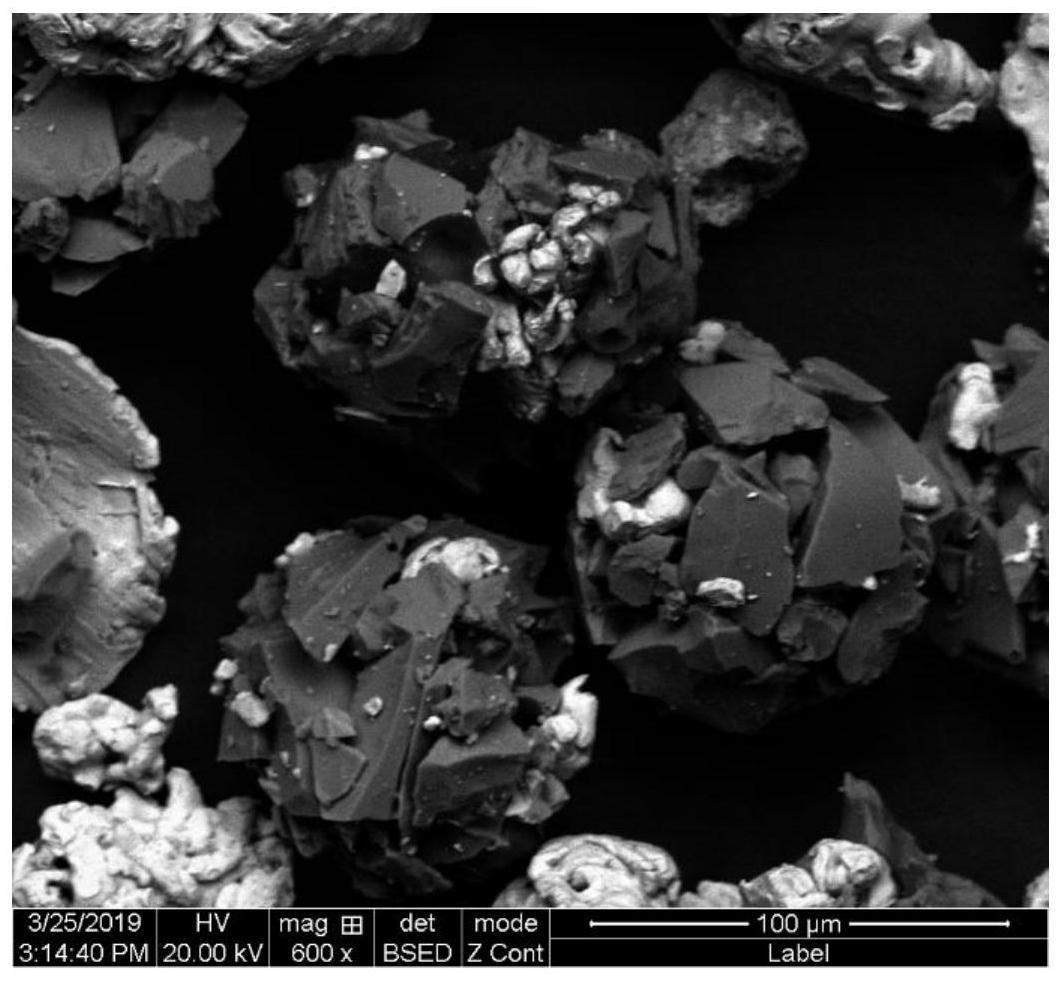
[0001]
本发明属于磁性磨料制备技术领域,尤其涉及一种球形磁性磨料及其制备方法。
背景技术:[0002]
磁力研磨加工技术是利用磁场将磁性磨料吸引到一起,形成磁力研磨刷,通过磁力研磨刷对工件表面进行滑擦、翻滚、磨削等运动形式,来实现对工件表面的抛光加工。磁性磨料作为磁力研磨加工技术的重要磨具,其研磨性能直接制约着磁力研磨加工技术的推广和应用。
[0003]
目前已报道的磁力磨料的制备工艺主要有:粘结法、机械混合法、复合镀层法和烧结法。其中,烧结法是对磁性基体和陶瓷的混合物料依次进行压制、等静压、烧结和破碎等处理,制备得到的磁性磨料的磁性基体与陶瓷相界面结合力较强,使用寿命长,但该制备工艺制备得到的磁性磨料存在形状不规则的问题,导致磁性磨料的加工效率低。
技术实现要素:[0004]
鉴于此,本发明的目的在于提供一种球形磁性磨料的制备方法,本发明提供的制备方法制得的磁性磨料形状规则为球形,加工效率高。
[0005]
为了实现上述发明目的,本发明提供了以下技术方案:
[0006]
本发明提供了一种球形磁性磨料的制备方法,包括以下步骤:
[0007]
将硬质相、铁磁相和水混合,得到混合浆料;
[0008]
将所述混合浆料进行造粒,得到球形磁性磨料,所述球形磁性磨料包括铁磁相核芯和包裹在所述铁磁相核芯表面的硬质相壳层;
[0009]
所述硬质相和铁磁相的质量比为1:(3~5)。
[0010]
优选地,所述造粒的方式为喷雾造粒,所述喷雾造粒的入口温度为230~270℃,出口温度为100~130℃。
[0011]
优选地,所述喷雾造粒的离心雾化器的转速为8000~24000r/min,混合浆料的进料速率为4~6kg/h。
[0012]
优选地,所述硬质相的粒径为10~40μm,所述铁磁相的粒径为50~200μm。
[0013]
优选地,所述硬质相包括氧化铝、金刚石、立方氮化硼、四碳化硼、碳化硅、氧化锆、碳化钛或碳化钨。
[0014]
优选地,所述铁磁相包括羰基铁、铁硅合金、铁铝合金或铁镍合金。
[0015]
优选地,所述混合浆料还包括粘结剂和分散剂,所述分散剂包括四甲基氢氧化铵和聚乙二醇。
[0016]
优选地,所述四甲基氢氧化铵和聚乙二醇的质量比为(1~5):(5~25)。
[0017]
本发明还提供了上述技术方案所述制备方法制得的球形磁性磨料,包括铁磁相核芯和包裹在所述铁磁相核芯表面的硬质相壳层,所述球形磁性磨料的球形度为0.8~1.2;粒径为50~200μm;ζ电位为40~50mv。
[0018]
本发明提供的球形磁性磨料的制备方法,包括以下步骤:将硬质相、铁磁相和水混合,得到混合浆料;将所述混合浆料进行造粒,得到球形磁性磨料,所述球形磁性磨料包括铁磁相核芯和包裹在所述铁磁相核芯表面的硬质相壳层;所述硬质相和铁磁相的质量比为1:(3~5)。本发明通过造粒,得到具有核壳结构的球形磁性磨料,球形磁性磨料中硬质相均匀的覆盖在铁磁相表面,使硬质相不易发生团聚现象,有利于提高磁性磨料的相对磁导率,增大磁性磨料达到饱和磁感应强度值,使磁性磨料在加工工件时受到的磁场力增大,产生的切削力增大,进而提高球形磁性磨料的加工效率和加工性能,延长球形磁性磨料的使用寿命。且本发明制备得到的球形磁性磨料的硬质相的微切削刃分布具有均匀一致的特征,具有良好的加工效率。因此,本发明提供的制备方法解决了现有技术中存在的得到的磁性磨料存在形状不规则,导致磁性磨料加工效率低的问题。
[0019]
且本发明制备得到的球形磁性磨料的粒度均匀、流动性好,易于成型。
附图说明
[0020]
图1~2为实施例1制备得到的球形磁性磨料的sem图;
[0021]
图3~4为对比例1制备得到的磁性磨料的sem图;
[0022]
图5为实施例1所得球形磁性磨料、对比例1所得球形磁性磨料和羰基铁的磁导率曲线。
具体实施方式
[0023]
本发明提供了一种球形磁性磨料的制备方法,包括以下步骤:
[0024]
将硬质相、铁磁相和水混合,得到混合浆料;
[0025]
将所述混合浆料进行造粒,得到球形磁性磨料。
[0026]
在本发明中,若无特殊说明,所采用的原料均为本领域常规市售产品。
[0027]
本发明将硬质相、铁磁相和水混合,得到混合浆料。
[0028]
在本发明中,所述硬质相、铁磁相和水混合的方式优选为将硬质相和铁磁相第一混合后,与水第二混合,得到悬浮液;将所述悬浮液进行球磨,得到混合浆料。
[0029]
在本发明中,所述第一混合的方式优选为搅拌,所述搅拌的速率优选为200~250r/min,进一步优选为230~240r/min;所述搅拌的时间优选为4~6h,进一步优选为4h。在本发明中,所述第二混合的方式优选为搅拌,所述搅拌的速率优选为80~120r/min,进一步优选为100r/min;所述搅拌的时间优选为0.5~1h。
[0030]
在本发明中,所述硬质相和铁磁相的质量比为1:(3~5),优选为1:4。在本发明中,若铁磁相的质量过多时,制备得到的球形磁性磨料中硬质相包覆不完全,球形磁性磨料的相对磁导率低,从而影响球形磁性磨料的切削加工性能;若铁磁相的质量过少时,多余的硬质相无法包覆在铁磁相表面,会发生自身团聚现象,在磁力研磨过程中发生飞散,同时会影响球形磁性磨料在磁场中的受力,降低加工效率。
[0031]
在本发明中,所述悬浮液的固含量优选为40~60wt%。
[0032]
在本发明中,所述硬质相优选包括氧化铝、金刚石、立方氮化硼、四碳化硼、碳化硅、氧化锆、碳化钛或碳化钨,在本发明具体实施例中进一步优选为氧化铝;所述硬质相的粒径为10~40μm,优选为15~20μm。在本发明中,所述铁磁相优选包括羰基铁、铁硅合金、铁
铝合金或铁镍合金,在本发明具体实施例中进一步优选为羰基铁;所述铁磁相的粒径为50~200μm,优选为80~180μm,进一步优选为140μm。
[0033]
在本发明中,所述球磨优选在球磨机中进行,所述球磨的介质优选为氧化铝,所述氧化铝的粒径优选为4~9mm,进一步优选为粒径为4mm的氧化铝和粒径为9mm的氧化铝的混合物,所述粒径为4mm的氧化铝和粒径为9mm的氧化铝的质量比优选为3:2;所述球磨的球料比优选为1:1,即所述硬质相和铁磁相的混合物的质量和氧化铝的质量比优选为1:1。在本发明中,所述球磨的转速优选为120~230r/min。
[0034]
在本发明中,所述混合浆料优选还包括粘结剂和分散剂,所述粘结剂和分散剂优选在所述球磨的过程中加入。本发明优选球磨0.5h后,加入粘结剂和分散剂。在本发明中,加入所述粘结剂和分散剂后,优选继续球磨0.5~1.5h,所述球磨的方式与上述球磨的方式一致,不再一一赘述。
[0035]
在本发明中,所述粘结剂优选为聚乙烯醇(pva),所述pva的醇解度优选为88%;所述pva的平均分子量优选为1700。在本发明中,所述粘结剂和硬质相的质量比优选为(1~5):25。在本发明中,所述分散剂优选包括四甲基氢氧化铵(tmah)和聚乙二醇(peg),所述tmah和peg的质量比优选为(1~5):(5~25),进一步优选为(2~4):(10~20)。在本发明中,所述分散剂和硬质相的质量比优选为(0.6~3):25。在本发明中,加入所述粘结剂和分散剂后,得到的混合浆料的固含量优选为40~60%。在本发明中,tmah为强碱有机物,能够提高是硬质相在混合浆料中的分散性;peg为聚合物高分子,通过位阻型分散机制起作用,一端吸附在硬质相的颗粒表面,另一端可以在水介质中充分伸展,形成位阻层,阻碍硬质相颗粒的碰撞聚集和重力沉降,有利于硬质相颗粒通过静电稳定机理达到稳定分散。
[0036]
在本发明中,所述水优选为去离子水。
[0037]
得到混合浆料后,本发明将所述混合浆料进行造粒,得到球形磁性磨料。
[0038]
在本发明中,所述造粒的方式优选为喷雾造粒,所述喷雾造粒优选在喷雾造粒机中进行。在本发明中,所述喷雾造粒的入口温度优选为230~270℃,进一步优选为240~260℃,更优选为250℃;所述喷雾造粒的出口温度优选为100~130℃,进一步优选为110~120℃;所述喷雾造粒的离心雾化器的转速优选为8000~24000r/min,进一步优选为20000r/min;所述喷雾造粒的混合浆料的进料速率优选为4~6kg/h,进一步优选为5kg/h。
[0039]
在本发明中,喷雾造粒过程中,粘合剂过多或进口热风温度过高,会增强颗粒的团聚强度;进料速度过快,雾化过程雾滴水分蒸发不及时影响收缩成形,进料速度过慢影响制备速率。
[0040]
本发明还提供了上述技术方案所述制备方法制得的球形磁性磨料,包括铁磁相和包裹在所述铁磁相表面的硬质相,所述球形磁性磨料的球形度为0.8~1.2;粒径为50~200μm;ζ电位为40~50mv。
[0041]
在本发明中,所述球形磁性磨料中铁磁相的质量百分含量优选为60~80%,所述球形磁性磨料中硬质相的质量百分含量优选为20~40%。
[0042]
下面结合实施例对本发明提供的球形磁性磨料及其制备方法进行详细的说明,但是不能把它们理解为对本发明保护范围的限定。
[0043]
实施例1
[0044]
按质量比为1:4的比例,将200gal2o3(粒径为15μm)和800g羰基铁(粒径为80μm)混
合,搅拌4h,转速为200r/min,得到混合物料;
[0045]
将得到的混合物料和1500g水混合,得到悬浮液,悬浮液的固含量为40wt%,搅拌0.5h后,转速为120r/min,在球磨机中进行球磨,球磨介质为氧化铝(粒径为4mm的氧化铝和粒径为9mm的氧化铝的混合物,粒径为4mm的氧化铝和粒径为9mm的氧化铝的质量比为3:2),球料比为1:1,球磨的转速为120r/min,球磨0.5h后,与40g pva、5g tmah和19g peg混合,继续球磨0.5h,得到混合浆料;
[0046]
将得到的混合浆料进行喷雾造粒,喷雾造粒的入口温度为240℃,出口温度为120℃,离心雾化器的转速为24000r/min,混合浆料的进料速率为6kg/h,得到球形磁性磨料。
[0047]
本实施例得到的球形磁性磨料以羰基铁为核,以al2o3为壳层,球形磁性磨料中al2o3的质量百分含量为25%,羰基铁的质量百分含量为75%,粒径为100μm,球形度为0.8~1,ζ电位为40mv。
[0048]
在下述研磨条件下测试所得磁性磨料的性能:磨料为本实施例所得球形磁性磨料;球形磁性磨料的填充量为3g;被加工工件为直径为10mm、壁厚为1mm的tc4钛管;研磨参数包括:转速为1500r/min,加工间隙为2mm,进给速度为100mm/min。
[0049]
通过测试所得球形磁性磨料的最佳研磨时间来确定球形磁性磨料中羰基铁基体和表面氧化碳化硅层之间的结合强度,所得结果为:本实施例所得球形磁性磨料的最佳研磨时间为20min;即所得磁性磨料在上述研磨条件下的使用寿命。
[0050]
通过测试所得球形磁性磨料在上述研磨条件下对被加工工件的表面粗糙度变化情况来测试球形磁性磨料的加工效率,测试结果为:在加工5min后,tc4钛管外壁初始粗糙度ra=0.365
±
0.01μm下降至ra=0.089
±
0.01μm。
[0051]
对比例1
[0052]
采用本领域熟知的常压烧结法制备的磁性磨料:
[0053]
按质量比为1:4的比例,将200gal2o3(粒径为38μm)和800g羰基铁(粒径为150μm)混合,机械混合4h后,加入30g pva搅拌均匀,压制成块;
[0054]
将压制后的样品放入真空干燥箱中进行干燥,10h后取出,在真空管式炉中进行烧结,烧结温度为1200℃,保温时间为2h,随炉冷却后机械破碎,破碎后的粒径为110μm。
[0055]
采用与实施例1相同的研磨条件测试本对比例所得球形磁性磨料的性能,所得结果为:本对比例所得球形磁性磨料的最佳研磨时间为20min;在加工5min后,tc4钛管外壁初始粗糙度ra=0.365
±
0.01μm下降至ra=0.297
±
0.01μm。
[0056]
图1~2为实施例1制备得到的球形磁性磨料的sem图,图中磨料黑色部分为硬质相,白色部分为铁磁相,从图中可以看出,本发明制备得到的球形磁性磨料硬质相在铁磁相表面分布均匀,棱角分明,没有出现硬质相钝化的现象,且硬质相未发生团聚现象,能够保证相对一致的切削深度,因而具有较高的加工效率。
[0057]
图3~4为对比例1制备得到的磁性磨料的sem图,图中磨料黑色部分为硬质相,白色部分为铁磁相,从图中可以看出,传统烧结法制备的磁性磨料硬质相在烧结过程中钝化,且分布不均,硬质相发生团聚现象,出现铁磁相与硬质相分离的情况,没有形成良好的包覆核壳结构,影响加工效果。
[0058]
对比例2
[0059]
将400gal2o3(粒径为10μm)和400g羰基铁(粒径为90μm)混合,搅拌1h,转速为250r/
min,得到混合物料;
[0060]
将得到的混合物料和800g水混合,得到悬浮液,悬浮液的固含量为50wt%,搅拌1h后,转速为80r/min,在球磨机中进行球磨,球磨介质为氧化铝(粒径为4mm的氧化铝和粒径为9mm的氧化铝的混合物,粒径为4mm的氧化铝和粒径为9mm的氧化铝的质量比为3:2),球料比为1:1,球磨的转速为80r/min,球磨1h后,与30g pva、10g tmah和20g peg混合,继续球磨0.5h,得到混合浆料;
[0061]
将得到的混合浆料进行喷雾造粒,喷雾造粒的入口温度为250℃,出口温度为100℃,离心雾化器的转速为20000r/min,混合浆料的进料速率为5kg/h,得到球形磁性磨料。
[0062]
本实施例得到的球形磁性磨料以羰基铁为核,以为al2o3壳层,球形磁性磨料中al2o3的质量百分含量为33%,羰基铁的质量百分含量为67%,粒径为110μm,球形度为0.6,ζ电位为45mv。
[0063]
采用与实施例1相同的研磨条件测试本对比例所得球形磁性磨料的性能,所得结果为:本对比例所得球形磁性磨料的最佳研磨时间为25min;在加工5min后,tc4钛管外壁初始粗糙度ra=0.365
±
0.01μm下降至ra=0.167
±
0.01μm。
[0064]
实施例2
[0065]
将200gal2o3(粒径为40μm)和600g羰基铁(粒径为180μm)混合,搅拌4h,转速为230r/min,得到混合物料;
[0066]
将得到的混合物料和800g水混合,得到悬浮液,悬浮液的固含量为50wt%,搅拌0.5h后,转速为100r/min,在球磨机中进行球磨,球磨介质为氧化铝(粒径为4mm的氧化铝和粒径为9mm的氧化铝的混合物,粒径为4mm的氧化铝和粒径为9mm的氧化铝的质量比为3:2),球料比为1:1,球磨的转速为230r/min,球磨0.5h后,与40g pva、5g tmah和15g peg混合,继续球磨0.5h,得到混合浆料;
[0067]
将得到的混合浆料进行喷雾造粒,喷雾造粒的入口温度为260℃,出口温度为120℃,离心雾化器的转速为24000r/min,混合浆料的进料速率为6kg/h,得到球形磁性磨料。
[0068]
本实施例得到的球形磁性磨料以羰基铁为核,以为al2o3壳层,球形磁性磨料中al2o3的质量百分含量为33%,羰基铁的质量百分含量为67%,粒径为220μm,球形度为0.9,ζ电位为43mv。
[0069]
采用与实施例1相同的研磨条件测试本实施例所得球形磁性磨料的性能,所得结果为:本实施例所得球形磁性磨料的最佳研磨时间为22min;在加工5min后,tc4钛管外壁初始粗糙度ra=0.365
±
0.01μm下降至ra=0.139
±
0.01μm。
[0070]
实施例3
[0071]
将200gal2o3(粒径为20μm)和1000g羰基铁(粒径为140μm)混合,搅拌4h,转速为240r/min,得到混合物料;
[0072]
将得到的混合物料和800g水混合,得到悬浮液,悬浮液的固含量为60wt%,搅拌0.5h后,转速为120rpm,在球磨机中进行球磨,球磨介质为氧化铝(粒径为4mm的氧化铝和粒径为9mm的氧化铝的混合物,粒径为4mm的氧化铝和粒径为9mm的氧化铝的质量比为3:2),球料比为1:1,球磨的转速为230r/min,球磨0.5h后,与30g pva、3g tmah和20g peg混合,继续球磨0.5h,得到混合浆料;
[0073]
将得到的混合浆料进行喷雾造粒,喷雾造粒的入口温度为250℃,出口温度为120
℃,离心雾化器的转速为24000r/min,混合浆料的进料速率为6kg/h,得到球形磁性磨料。
[0074]
本实施例得到的球形磁性磨料以羰基铁为核,以为al2o3壳层,球形磁性磨料中al2o3的质量百分含量为20wt%,羰基铁的质量百分含量为80wt%,粒径为165μm,球形度为1,ζ电位为46mv。
[0075]
采用与实施例1相同的研磨条件测试本实施例所得球形磁性磨料的性能,所得结果为:本实施例所得球形磁性磨料的最佳研磨时间为22min;在加工5min后,tc4钛管外壁初始粗糙度ra=0.365
±
0.01μm下降至ra=0.102
±
0.01μm。
[0076]
对比例3
[0077]
将400gal2o3(粒径为30μm)和800g羰基铁(粒径为100μm)混合,搅拌4h,转速为220r/min,得到混合物料;
[0078]
将得到的混合物料和2000g水混合,得到悬浮液,悬浮液的固含量为60wt%,搅拌0.5h后,转速为120r/min,在球磨机中进行球磨,球磨介质为氧化铝(粒径为4mm的氧化铝和粒径为9mm的氧化铝的混合物,粒径为4mm的氧化铝和粒径为9mm的氧化铝的质量比为3:2),球料比为1:1,球磨的转速为120r/min,球磨0.5h后,与40g pva、5g tmah和20g peg混合,继续球磨0.5h,得到混合浆料;
[0079]
将得到的混合浆料进行喷雾造粒,喷雾造粒的入口温度为330℃,出口温度为120℃,离心雾化器的转速为24000r/min,混合浆料的进料速率为6kg/h,得到球形磁性磨料。
[0080]
本对比例得到的球形磁性磨料以羰基铁为核,以为al2o3壳层,球形磁性磨料中al2o3的质量百分含量为50wt%,羰基铁的质量百分含量为50wt%,粒径为130μm,球形度为0.6,ζ电位为42mv。
[0081]
采用与实施例1相同的研磨条件测试本对比例所得球形磁性磨料的性能,所得结果为:本对比例所得球形磁性磨料的最佳研磨时间为24min;在加工5min后,tc4钛管外壁初始粗糙度ra=0.365
±
0.01μm下降至ra=0.292
±
0.01μm。
[0082]
对比例4
[0083]
按质量比为1:6的比例,将300gal2o3(粒径为20μm)和1800g羰基铁(粒径为120μm)混合,搅拌4h,转速为230r/min,得到混合物料;
[0084]
将得到的混合物料和1400g水混合,得到悬浮液,悬浮液的固含量为60wt%,搅拌0.5h后,转速为120r/min,在球磨机中进行球磨,球磨介质为氧化铝(粒径为4mm的氧化铝和粒径为9mm的氧化铝的混合物,粒径为4mm的氧化铝和粒径为9mm的氧化铝的质量比为3:2),球料比为1:1,球磨的转速为120r/min,球磨0.5h后,与45g pva、5g tmah和25g peg混合,继续球磨0.5h,得到混合浆料;
[0085]
将得到的混合浆料进行喷雾造粒,喷雾造粒的入口温度为330℃,出口温度为120℃,离心雾化器的转速为18000r/min,混合浆料的进料速率为5kg/h,得到球形磁性磨料。
[0086]
本对比例得到的球形磁性磨料以羰基铁为核,以为al2o3壳层,球形磁性磨料中al2o3的质量百分含量为17wt%,羰基铁的质量百分含量为83wt%,粒径为140μm,球形度为0.9,ζ电位为48mv。
[0087]
采用与实施例1相同的研磨条件测试本对比例所得球形磁性磨料的性能,所得结果为:本对比例所得球形磁性磨料的最佳研磨时间为20min;在加工5min后,tc4钛管外壁初始粗糙度ra=0.365
±
0.01μm下降至ra=0.227
±
0.01μm。
[0088]
应用例
[0089]
对于初始粗糙度为ra=0.365
±
0.01μm的钛合金管壁,分别采用实施例1和对比例1~4制备的磁性磨料进行磁力研磨加工,研磨加工的参数包括:转速1000r/min,加工间隙:2mm,磁性磨料填充量:5g;进给速度:100mm/min,加工样品分别标记为r1(实施例1样品)、r2(对比例1样品)、r3(对比例2样品)、r4(对比例3样品)和r5(对比例4样品)加工时间8min,加工长度30mm,分别对上述磁力研磨加工后的钛合金管壁的粗糙度进行测试,测试结果分别为:r1样品的粗糙度为ra=0.089
±
0.01μm、r2样品的粗糙度为ra=0.297
±
0.01μm、r3样品的粗糙度为ra=0.167
±
0.01μm、r4样品的粗糙度为ra=0.292
±
0.01μm、r5样品的粗糙度为ra=0.227
±
0.01μm。说明本发明提供的制备方法制得的磁性磨料具有良好的加工性能。
[0090]
测试实施例1所得球形磁性磨料、对比例1所得球形磁性磨料和羰基铁的磁导率,结果如图5所示,图5中壳核磨料代表实施例1所得球形磁性磨料,烧结磨料代表对比例1所得磁性磨料,fe代表羰基铁;从图5可以看出:实施例1所得球形磁性磨料的磁导率更高,这是由于实施例1所得球形磁性磨料是壳核球形结构,硬质相均匀分布在铁磁相表面,球形磁性磨料在磁场中达到饱和磁感应强度值大,而烧结法制备的磁性磨料由于烧结成块再破碎,出现硬质相贯穿铁磁相的现象,从而磨料在磁场中达到饱和磁感应强度值较小,磁场力小加工效率低。
[0091]
以上所述仅是本发明的优选实施方式,应当指出,对于本技术领域的普通技术人员来说,在不脱离本发明原理的前提下,还可以做出若干改进和润饰,这些改进和润饰也应视为本发明的保护范围。