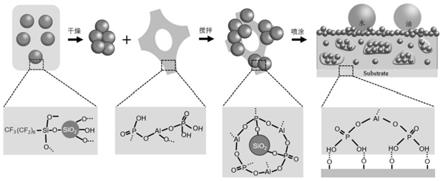
1.本发明涉及一种含改性二氧化硅纳米颗粒聚集体的复合涂料,还涉及上述复合涂料的制备方法及其喷涂在基材上形成超疏液涂层的应用。
背景技术:2.受自然界动植物的启发,例如荷叶、蝴蝶翅膀和沙漠甲虫等,人工构建的超疏液表面也具有多级的微纳复合结构以及低表面能物质,在二者的协同作用下,该表面能够使水滴和不同低表面张力的液滴在表面轻易地发生滚落,因此超疏液表面广泛应用于自清洁、防水防油、减阻、石化运输、防腐防尘、油水分离等多个领域。然而,目前众多超浸润表面均存在结构脆弱、与基底结合力差、表面上低表面能物质易脱落等缺点,严重限制了超浸润表面在实际生活及复杂工况环境下的使用。
3.目前用于提高超疏液涂层表面耐磨性的方法有两类,一是以树脂类有机物作为粘结剂,将功能涂层与基底粘结起来,虽然机械稳定性有一定增强,但是提高程度有限,无法应用于众多需要抵抗磨损的环境。二则是将树脂和功能颗粒混合后进行涂覆,该方法增强了颗粒之间的内聚力以及涂层对基底的附着力,使涂层环境耐久性得到一定提升,但是树脂等高聚物会包裹改性的纳米颗粒,覆盖表面的功能基团,导致疏液效果大大降低。
技术实现要素:4.发明目的:本发明针对现有技术中超疏液涂层存在的问题,提供一种含改性二氧化硅纳米颗粒聚集体的复合涂料;还提供上述复合涂料的制备方法;采用本发明方法制得的涂料可应用于多种基底材料上,在基底材料上形成的涂层使基材表面能够抵抗不同低表面张力液体的污染,同时涂层还具有良好的机械稳定性和环境耐久性,可适用于多种苛刻的工况条件。
5.技术方案:本发明所述的含改性二氧化硅纳米颗粒聚集体的复合涂料,所述纳米复合涂料由如下质量份数的组分混合而成:1~3份陶瓷粘结剂、0.5~0.8份改性二氧化硅纳米颗粒聚集体、0.1~0.2份正硅酸四乙酯、90~110份无水乙醇以及0.1~0.3份氨水。
6.配方中,氨水提供碱性环境,无水乙醇作为溶剂,氨水类似于催化剂促进正硅酸四乙酯水解,水解产生的二氧化硅纳米颗粒填充到改性二氧化硅纳米颗粒聚集体的网状结构中,形成更密实的网状结构,提升形成涂层后的强度;同时正硅酸四乙酯中的硅羟基,与改性二氧化硅纳米颗粒聚集体中剩余的硅羟基发生脱水缩合,形成si
‑
o
‑
si键,正硅酸四乙酯中的硅羟基还能与陶瓷粘结剂中的磷羟基发生脱水缩合,生成p
‑
o
‑
si键,从而一方面降低体系内的羟基含量,提高其疏水性能,另一方面,提高各物料之间的结合力,各物质通过化学键合在一起,提升形成涂层后的内聚力,进而提升机械性能
‑
耐磨性。
7.其中,所述改性二氧化硅纳米颗粒聚集体中聚集体颗粒的粒径为不大于10微米。
8.其中,所述改性二氧化硅纳米聚集体采用如下方法制备而成:先将22~25质量份
碱性硅溶胶水溶液和0.5~0.8质量份正硅酸四乙酯分散于80~100质量份无水乙醇中,然后再往无水乙醇中逐滴加入0.5~0.8质量份改性硅烷,水浴条件下反应,反应后将得到的产物进行干燥、粉碎并用1500目滤网进行筛分,得到聚集体粒径为10微米以下的改性二氧化硅纳米颗粒聚集体;所述改性硅烷为烷基三氯硅烷或/和氟烷基三氯硅烷。
9.生成改性二氧化硅纳米聚集体的反应体系中,链式纳米硅溶胶中的二氧化硅纳米颗粒采用烷基三氯硅烷或/和氟烷基三氯硅烷进行改性,正硅酸四乙酯起到交联剂的作用,具体为:正硅酸四乙酯在碱性环境下发生水解,与硅溶胶发生脱水缩合,使得改性接枝后的二氧化硅纳米颗粒相互交联在一起,形成紧密链式网络结构,利于提高涂层的超疏液性能,同时,更利于形成二氧化硅纳米颗粒聚集体。
10.其中,所述碱性硅溶胶水溶液是将10~15质量份的15wt%链式纳米硅溶胶分散于8~12质量份的10~15wt%氨水溶液中,搅拌均匀后得到碱性硅溶胶水溶液;碱性硅溶胶水溶液的ph值为10~12。
11.其中,所述陶瓷粘结剂采用如下方法制备而成:将20~30质量份的去离子水加入60~78质量份的85wt%磷酸中,室温下搅拌后,再往其中逐滴加入12~15质量份的氢氧化铝,水浴加热条件下持续搅拌,得到陶瓷粘结剂。
12.上述含改性二氧化硅纳米颗粒聚集体的复合涂料的制备方法,所述制备方法为:先制备改性二氧化硅纳米颗粒聚集体,再制备无机陶瓷粘结剂,最后将改性二氧化硅纳米颗粒聚集体与陶瓷粘结剂混合制备出纳米复合涂料;具体为:将1~3质量份的陶瓷粘结剂、0.5~0.8质量份的改性二氧化硅纳米聚集体和0.1~0.2质量份的正硅酸四乙酯分散于90
‑
110质量份的无水乙醇中,室温下混匀后,再加入0.1~0.3质量份的氨水调节ph值为9
‑
10,得到纳米复合涂料。
13.上述含改性二氧化硅纳米颗粒聚集体的复合涂料喷涂在基材上形成超疏液涂层的应用。
14.其中,基材为混凝土、陶瓷、玻璃、钢板、铝片或木材中的一种。
15.其中,具体为:将复合涂料喷涂于清洁后的基材表面,高温固化后,得到超疏液涂层。通过一步法喷涂复合涂料,室温喷涂后固化即可获得稳定的耐磨涂层,有利于大面积整体施工喷涂。
16.本发明超疏液涂料与基材具有良好的结合力,是因为本发明涂料采用无机陶瓷粘结剂,其对任何基板均具有良好的粘结性。
17.本发明涂料中含改性二氧化硅纳米颗粒聚集体采用的改性硅烷是烷基三氯硅烷或氟烷基三氯硅烷,烷基三氯硅烷或氟烷基三氯硅烷能够实现二氧化硅纳米颗粒的充分改性(即提高二氧化硅纳米颗粒的接枝率),原因为:烷基三氯硅烷或氟烷基三氯硅烷能够在碱性条件下发生剧烈反应并充分水解,大幅提高烷基或者氟烷基在二氧化硅表面的接枝率,二氧化硅表面低表面能的基团接枝量越大,其对低表面张力的物质排斥性越好,并且还能最大限度降低硅溶胶中残余硅羟基含量,即采用烷基三氯硅烷或氟烷基三氯硅烷对二氧化硅改性能够降低二氧化硅纳米颗粒的表面张力,提升其疏液性能,同时氯基快速水解后形成的硅羟基还易与二氧化硅上的硅羟基以及与其本身以及二氧化硅和二氧化硅之间硅羟基均发生脱水缩合,从而相互交联,形成三维网络结构,从而形成更多的粒径尺寸在10微米左右的颗粒
‑
聚集体。
18.改性二氧化硅纳米颗粒聚集体加入到陶瓷粘结剂中,增强了改性二氧化硅纳米颗粒聚集体在整个涂层体系中的偏聚效果,涂层受到磨损后,颗粒团聚物起到微胶囊的作用,涂层内的改性二氧化硅纳米颗粒得以释放至表面,使涂层继续保持良好的超疏液性能;采用磷酸二氢铝作为陶瓷粘结剂,与改性二氧化硅纳米颗粒聚集体通过化学键结合在一起,提高了涂层的内聚力,同时,陶瓷粘结剂没有长链的高分子基团,能最大程度将改性二氧化硅纳米颗粒的官能团暴露在涂层表面,提高涂层的超疏液特性;涂料中加入0.1
‑
0.2质量份的正硅酸四乙酯,一方面碱性条件下形成的二氧化硅纳米颗粒可增强涂层的强度,因为生成的二氧化硅纳米颗粒可以填充到网状结构中,形成更密实的网状结构;另一方面,正硅酸四乙酯中的硅羟基,不但可与改性二氧化硅纳米颗粒的剩余硅羟基发生脱水缩合,还能与陶瓷粘结剂中的磷羟基发生脱水缩合,在降低涂层内羟基含量的同时,大大提高了涂层的内聚力,进一步增强涂层的机械性能。
19.有益效果:本发明方法制得的涂料可以应用于多种基底材料上,并与基底材料具有良好的结合力,在基底材料上形成的涂层使基底材料表面能够抵抗不同低表面张力液体的污染,同时涂层还具有良好的机械稳定性和环境耐久性,可适用于多种苛刻的工况条件;本发明制备的涂料涂覆在钢片、陶瓷等基材上,形成的涂层表面对于水、油、十六烷、正癸烷、机油的静态接触角均大于150
°
,滚动角小于滚动角小于10
°
;涂层经过500次负载为1000g磨耗仪摩擦试验后,仍能保持完整的微纳复合结构和超疏液特性,机械稳定性优异。
附图说明
20.图1为本发明超疏液涂料的形成过程以及涂料形成涂层的原理图;
21.图2为实施例1制得的改性纳米颗粒聚集体的透射电子显微镜照片;
22.图3为实施例1制得的改性纳米颗粒聚集体不同放大倍数下的扫描电子显微镜照片;
23.图4为实施例2涂有超疏液涂层的载玻片以及不同低表面张力液体滴在涂层表面的照片;
24.图5为实施例3基材表面超疏液涂层的耐磨性能测试,涂层上油滴滚动角和失重经过不同次数摩擦实验后的变化情况;
25.图6为实施例4基材表面超疏液涂层经过500次负载1000g磨耗仪摩擦试验后不同放大倍数下的扫描电子显微镜照片。
具体实施方式
26.下面结合附图对本发明的技术方案作进一步说明。
27.实施例1
28.本发明含改性二氧化硅纳米颗粒聚集体的复合涂料的制备方法,具体包括如下步骤:
29.(1)制备改性二氧化硅纳米颗粒聚集体:将10质量份的15wt.%链式纳米硅溶胶分散于8质量份的10wt%氨水中,搅拌均匀后获得ph值为10的碱性硅溶胶水溶液;随后将22质量份的碱性硅溶胶水溶液和0.5质量份的正硅酸四乙酯分散于80质量份的无水乙醇中,并逐滴往其中加入0.5质量份的全氟癸基三氯硅烷,混合物料于50℃水浴条件下持续加热
12h,加热后将产物于100℃真空下干燥8h,干燥后粉碎并用1500目滤网进行筛分,获得聚集体粒径在10微米以下的改性二氧化硅纳米颗粒聚集体;
30.(2)制备陶瓷粘结剂:将20质量份的去离子水加入到60质量份的85wt.%磷酸中,室温下搅拌10min后,逐滴加入12质量份的氢氧化铝,于50℃水浴加热条件下持续搅拌3h,得到陶瓷粘结剂;
31.(3)制备超疏液涂料:将1质量份的陶瓷粘结剂、0.5质量份的改性二氧化硅纳米颗粒聚集体和0.1质量份的正硅酸四乙酯分散于90质量份的无水乙醇中,室温下搅拌10min后,加入0.1份氨水调节ph值为9,再持续搅拌30min,得到超疏液涂料。
32.将实施例1制得的超疏液涂料喷涂于清洁后的载玻片表面,将载玻片置于220℃烘箱内固化30min,在载玻片上得到超疏液涂层。通过图2~3可知,实施例1制得的涂料形成的涂层具有典型的微纳复合结构,并且有大量的改性二氧化硅纳米颗粒聚集体填充在涂层中。
33.实施例2
34.本发明含改性二氧化硅纳米颗粒聚集体的复合涂料的制备方法,具体包括如下步骤:
35.(1)制备改性二氧化硅纳米颗粒聚集体:将12质量份的15wt.%链式纳米硅溶胶分散于12质量份的10wt%氨水中,搅拌均匀后获得ph值为10的碱性硅溶胶水溶液;随后将24质量份的碱性硅溶胶水溶液和0.6质量份的正硅酸四乙酯分散于88质量份的无水乙醇中,并逐滴往其中加入0.6质量份的全氟癸基三氯硅烷,混合物料于50℃水浴条件下持续加热16h,加热后将产物于100℃真空下干燥8h,干燥后粉碎并用1500目滤网进行筛分,获得聚集体粒径在10微米以下的改性二氧化硅纳米颗粒聚集体;
36.(2)制备陶瓷粘结剂:将25质量份的去离子水加入到70质量份的85wt.%磷酸中,室温下搅拌10min后,逐滴加入14质量份的氢氧化铝,于50℃水浴加热条件下持续搅拌3h,得到陶瓷粘结剂;
37.(3)制备超疏液涂料:将1.5质量份的陶瓷粘结剂、0.6质量份的改性二氧化硅纳米颗粒聚集体和0.1质量份的正硅酸四乙酯分散于96质量份的无水乙醇中,室温下搅拌10min后,加入0.2份氨水调节ph值为9,再持续搅拌30min,得到超疏液涂料。
38.将实施例2制得的超疏液涂料喷涂于清洁后的载玻片表面,将载玻片置于220℃烘箱内固化30min,在载玻片上得到超疏液涂层。通过图4可知,该涂层具有良好的超疏液性,对水、大豆油、十六烷、正癸烷、机油等液体静态接触角大于150
°
,滚动角小于10
°
。
39.实施例3
40.本发明含改性二氧化硅纳米颗粒聚集体的复合涂料的制备方法,具体包括如下步骤:
41.(1)制备改性二氧化硅纳米颗粒聚集体:将14质量份的15wt.%链式纳米硅溶胶分散于14质量份的10wt%氨水中,搅拌均匀后获得ph值为10的碱性硅溶胶水溶液;随后将25质量份的碱性硅溶胶水溶液和0.6质量份的正硅酸四乙酯分散于90质量份的无水乙醇中,并逐滴往其中加入0.6质量份的全氟癸基三氯硅烷,混合物料于50℃水浴条件下持续加热24h,加热后将产物于100℃真空下干燥8h,干燥后粉碎并用1500目滤网进行筛分,获得聚集体粒径在10微米以下的改性二氧化硅纳米颗粒聚集体;
42.(2)制备陶瓷粘结剂:将26质量份的去离子水加入到72质量份的85wt.%磷酸中,室温下搅拌10min后,逐滴加入14质量份的氢氧化铝,于50℃水浴加热条件下持续搅拌3h,得到陶瓷粘结剂;
43.(3)制备超疏液涂料:将2质量份的陶瓷粘结剂、0.6质量份的改性二氧化硅纳米颗粒聚集体和0.15质量份的正硅酸四乙酯分散于96质量份的无水乙醇中,室温下搅拌10min后,加入0.3份氨水调节ph值为10,再持续搅拌30min,得到超疏液涂料。
44.将实施例3制得的超疏液涂料喷涂于清洁后的不锈钢片表面,将不锈钢片置于220℃烘箱内固化30min,在不锈钢片上得到超疏液涂层。通过图5可知,该涂层经过500次负载为1000g磨耗仪摩擦试验后,油滴滚动角仍低于10
°
,涂层失重小于20%。
45.实施例4
46.本发明含改性二氧化硅纳米颗粒聚集体的复合涂料的制备方法,具体包括如下步骤:
47.(1)制备改性二氧化硅纳米颗粒聚集体:将15质量份的15wt.%链式纳米硅溶胶分散于12质量份的10wt%氨水中,搅拌均匀后获得ph值为10的碱性硅溶胶水溶液;随后将25质量份的碱性硅溶胶水溶液和0.8质量份的正硅酸四乙酯分散于100质量份的无水乙醇中,并逐滴往其中加入0.8质量份的全氟癸基三氯硅烷,混合物料于50℃水浴条件下持续加热24h,加热后将产物于100℃真空下干燥8h,干燥后粉碎并用1500目滤网进行筛分,获得聚集体粒径在10微米以下的改性二氧化硅纳米颗粒聚集体;
48.(2)制备陶瓷粘结剂:将30质量份的去离子水加入到78质量份的85wt.%磷酸中,室温下搅拌10min后,逐滴加入15质量份的氢氧化铝,于50℃水浴加热条件下持续搅拌3h,得到陶瓷粘结剂;
49.(3)制备超疏液涂料:将3质量份的陶瓷粘结剂、0.8质量份的改性二氧化硅纳米颗粒聚集体和0.2质量份的正硅酸四乙酯分散于110质量份的无水乙醇中,室温下搅拌10min后,加入0.3份氨水调节ph值为10,再持续搅拌30min,得到超疏液涂料。
50.将实施例4制得的超疏液涂料喷涂于清洁后的不锈钢片表面,将不锈钢片置于220℃烘箱内固化30min,在不锈钢片上得到超疏液涂层。通过图6涂层的围观表征可知,该涂层经过500次负载为1000g磨耗仪摩擦试验后表面仍保持良好的微纳复合结构。