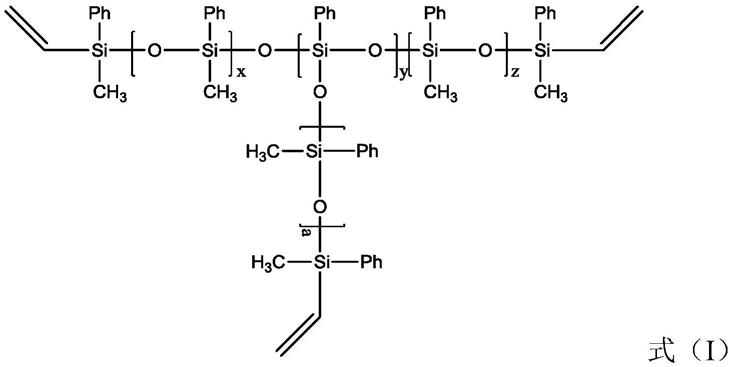
1.本发明涉及有机硅压敏材料技术领域,具体涉及一种可粘结具有抗指纹玻璃、同时具有良好剥离力以及排气性的有机硅压敏胶、制备方法及其应用。
背景技术:2.有机硅压敏胶是一种含硅元素的胶粘剂,它不仅具有压敏胶所必需的压敏性,还有许多特殊的性能,例如:(1)对低表面能材料良好的粘附性;2)突出的耐高低温性能,可在-50~200℃之间长期使用,且在高温和低温下仍然保持其粘接强度和柔韧性;(3)具有良好的化学惰性,具有突出的耐湿性和电性能;(4)良好的耐化学性能,耐溶剂性;(5)介电性能良好。
3.随着手持电子设备的飞速发展,触摸玻璃屏幕更新更是日新月异,对屏幕的保护需求也随之不断增长。目前的玻璃触摸屏幕需要进行表面处理,尤其是抗指纹涂层的处理使得屏幕更耐污,更光滑,使得屏幕的水滴角越来越大,表面能越来越低,传统的保护膜不仅难以粘紧,而且在粘结抗指纹玻璃屏时还存在空气气泡难以排除的问题。
技术实现要素:4.为解决现有技术存在的缺陷,本发明提供一种应用于抗指纹玻璃的有机硅压敏胶,在配方中添加了支化的乙烯基硅油,对抗指纹玻璃具有良好的剥离力和排气泡性能,剥离力稳定性好,不衰减,而且其制备工艺相对简单,便于实现放大规模生产。
5.本发明的另一目的在于提供这种新型的用于抗指纹玻璃的有机硅压敏胶的制备方法。
6.本发明的再一目的在于提供这种用于抗指纹玻璃的有机硅压敏胶的应用。
7.为实现上述目的,本发明的技术方案如下:
8.一种用于抗指纹玻璃的有机硅压敏胶,包括支化乙烯基硅油、乙烯基mq 硅树脂、羟基生胶、羟基mq硅树脂、硅氢交联剂、抑制剂和溶剂;各组份按重量份计为:支化乙烯基硅油10-20份,羟基生胶20~70份,mq硅树脂40~ 70份,硅氢交联剂0.5~1.5份,抑制剂0.4~1.0份,溶剂80-120份;其中,羟基mq硅树脂和乙烯基mq硅树脂的质量比为(10~1):(1~5)。
9.在一个具体的实施方案中,所述支化乙烯基硅油的粘度为200-3000mpa
·
s,优选为500-150 0mpa
·
s;优选地,所述支化乙烯基硅油中乙烯基的质量含量为 0.5~2%。
10.在一个具体的实施方案中,所述羟基生胶的分子量为50~70万。
11.在一个具体的实施方案中,所述羟基mq硅树脂的m/q比值为0.5~0.8,摩尔质量为2700~5000g/mol。
12.在一个具体的实施方案中,所述乙烯基mq硅树脂的m/q比值为0.5~0.8,乙烯基质量分数为0.5~2%,摩尔质量为4000~5000g/mol。
13.在一个具体的实施方案中,所述溶剂选自甲苯、二甲苯、酯类溶剂、酮类溶剂、烷烃类溶剂中的任意一种或几种组合。
14.在一个具体的实施方案中,所述硅氢交联剂的粘度为20~50mpa.s,所述硅氢交联剂为含有端氢基和侧氢基、端氢基和侧氢基的质量百分含量为0.7~1.6wt%的含氢硅油。
15.在一个具体的实施方案中,所述抑制剂选自四甲基四乙烯基环四硅氧烷、二乙烯基四甲基二硅氧烷、甲基乙炔醇、乙炔基环己醇、甲基丁炔醇、3,5-二甲基-1-己炔基-3-醇、3-甲基-1-十二炔-3-醇中的任意一种或几种组合。
16.另一方面,前述的用于抗指纹玻璃的有机硅压敏胶的制备方法,包括以下步骤:
17.1)将一定重量份的支化乙烯基硅油、羟基生胶、羟基mq硅树脂、乙烯基 mq硅树脂、抑制剂和溶剂加入到反应釜中,搅拌使生胶充分溶解分散在溶剂中;
18.2)通入氮气搅拌,搅拌均匀后,缓慢加入羟基生胶重量0.05~1%的催化剂,然后在120-150℃的回流温度下脱水反应3-5h,直至无水产生;优选地,所述催化剂选自醋酸、丙酸、苯甲酸、苯乙酸、三氟苯磺酸或酸性硅藻土中的任意一种。
19.3)冷却至室温,加入硅氢交联剂,搅拌1~3小时,混合均匀得到用于抗指纹玻璃的有机硅压敏胶。
20.再一方面,前述的用于抗指纹玻璃的有机硅压敏胶在抗指纹玻璃的保护膜、电子产品保护膜或排废膜领域中的应用。
21.与现有技术相比,本发明具有以下的有益效果:
22.1)与传统的简单共混工艺对比,在本发明中,通过添加支化乙烯基硅油可使得到的压敏胶具有良好的粘合力稳定性,贴氟塑离型膜保护,老化后对抗指纹屏幕的剥离力没有明显衰减,对钢板的剥离力<1000g/inch。通过mq硅树脂和羟基生胶进行高温缩聚反应,不仅可以提高产品的保质期,改善压敏胶的内聚强度,而且提高产品的耐温和剥离力稳定性,通过控制mq硅树脂的含量和乙烯基含量来调节产品的剥离力,在固化成胶膜时,在催化剂作用下,硅氢交联剂与乙烯基反应,得到的压敏胶不仅对抗指纹玻璃有良好的剥离力,同时对钢板的剥离力不会太高,从而使得压敏胶胶膜的排气性良好。
23.2)本发明配方制得的有机硅压敏胶能涂布在普通50μm pet、100μm pet、 80μm srf以及tpu等基材上,对抗指纹玻璃有较高的剥离力,可达50g/inch,钢板剥离力<1000g/inch。
24.3)本发明制备的抗指纹玻璃有机硅压敏胶强度高,对抗指纹玻璃剥离力稳定性好,不衰减,排气性能好,透光率高。
具体实施方式
25.为了更好的理解本发明的技术方案,下面的实施例将对本发明所提供的方法予以进一步的说明,但本发明不限于所列出的实施例,还应包括在本发明的权利要求范围内其他任何公知的改变。
26.一种用于抗指纹玻璃的有机硅压敏胶,包括基胶组份配方组成和制备方法;
27.所述基胶组份组成包括支化乙烯基硅油、乙烯基mq硅树脂、羟基生胶、羟基mq硅树脂、硅氢交联剂、抑制剂和溶剂,所述配方组份按重量份包括支化乙烯基硅油10-20份,羟基生胶20~70份,mq硅树脂40~70份,硅氢交联剂0.5~1.5份,抑制剂0.4~1.0份,溶剂80-120份;其中,mq硅树脂包括羟基 mq硅树脂和乙烯基mq硅树脂,羟基mq硅树脂和乙烯基mq硅树脂的质量比为(10~1):(1~5)。
28.其中,本发明所述支化乙烯基硅油结构式如下;具体地,所述支化乙烯基硅油的粘度为200-3000mpa
·
s,例如包括但不限于200mpa
·
s、300mpa
·
s、400 mpa
·
s、500mpa
·
s、800mpa
·
s、1000mpa
·
s、1200mpa
·
s、1500mpa
·
s、2000mpa
·
s、2500mpa
·
s、3000mpa
·
s,优选粘度为500-1500mpa
·
s。在所述支化乙烯基硅油中乙烯基的质量含量为0.5~2%。其中,乙烯基的质量含量通过近红外光谱法测试得到。本发明支化乙烯基硅油在铂金催化剂作用下与硅氢交联剂反应,固化后的有机硅压敏胶对抗指纹玻璃剥离力稳定性好,对钢板剥离力低。
[0029][0030]
支化乙烯基硅油的制备方法包括苯基三甲氧基硅烷和甲基苯基二甲氧基硅烷的水解缩合、在酸的催化作用下,苯基三甲氧基硅烷和甲基苯基二甲氧基硅烷发生水解反应,并进一步脱水缩合得到羟基封端的t型聚硅氧烷链段,当链节达到一定数量后加入乙烯基双封头进行封端反应,最终经分离纯化得到具有t 结构的支化乙烯基硅油。
[0031]
上述支化乙烯基硅油的制备过程中,所述酸的催化剂选自浓硫酸、醋酸、丙酸、苯甲酸、苯乙酸、三氟苯磺酸、酸性硅藻土等中的任意一种,优选为浓硫酸。
[0032]
本发明的支化乙烯基硅油的制备步骤具体如下:
[0033]
1)在反应烧瓶中加入一定量的水和浓硫酸,于40℃下搅拌一段时间;
[0034]
2)缓慢滴加适量苯基三甲氧基硅烷和适量甲基苯基二甲氧基硅烷,升温至 50℃后保温1h;
[0035]
3)在80℃温度下蒸出理论量的步骤2)中水解生成的甲醇,加入一定量的甲苯和氢氧化钾水溶液,在130℃下回流5h;
[0036]
4)在低压下蒸除甲苯溶剂,降温至70℃;
[0037]
5)加入一定量四甲基氢氧化铵甲醇溶液及二乙烯基二甲基二硅氧烷进行封端,搅拌30min后升温至90℃,反应5h;
[0038]
6)升温至150℃,30min后结束反应;
[0039]
7)水洗、过滤、旋蒸,得到目标产物。
[0040]
本发明的支化乙烯基硅油的制备步骤涉及到的反应过程如下所示。
[0041][0042]
本发明中的用于抗指纹玻璃的有机硅压敏胶组成中,羟基mq硅树脂分子量为2700~5000,例如包括但不限于2700、3000、3200、3500、3800、4000、 4300、4500、4750、5000;乙烯基mq硅树脂分子量为4000~5000,例如包括但不限于4000、4100、4200、4300、4400、4500、4600、4700、4800、4900、5000,其中乙烯基质量含量为0.5~2%,例如包括但不限于0.5%、0.75%、1%、1.25%、 1.5%、1.75%、2%。通过控制有机硅压敏胶配方中羟基mq硅树脂和乙烯基mq 硅树脂两种mq硅树脂10~30份,其中,羟基mq硅树脂和乙烯基mq硅树脂的质量比为(10~1):(1~5),优选为10:1,可使得压敏胶具有在抗指纹玻璃上获得很好的剥离力,对抗指纹玻璃的剥离力稳定性好,对钢板剥离力低。
[0043]
本发明中的用于抗指纹玻璃的有机硅压敏胶组成中,所述溶剂为甲苯、二甲苯、酯类溶剂、酮类溶剂、烷烃类溶剂中的任意一种或几种组合;其中所述酯类溶剂例如包括但不限于乙酸乙酯,所述酮类溶剂例如包括但不限于丙酮,所述烷烃类溶剂例如包括但不限于庚烷。
[0044]
本发明中的用于抗指纹玻璃的有机硅压敏胶组成中,所述高温缩合反应所用催化剂选自醋酸、丙酸、苯甲酸、苯乙酸、三氟苯磺酸或酸性硅藻土中的任意一种,优选为醋酸。
[0045]
作为本发明中的抑制剂为四甲基四乙烯基环四硅氧烷、二乙烯基四甲基二硅氧烷、甲基乙炔醇、乙炔基环己醇、甲基丁炔醇、3,5-二甲基-1-己炔基-3-醇、 3-甲基-1-十二炔-3-醇中的任意一种或任意几种组合,优选为乙炔基环己醇。
[0046]
本发明中的用于抗指纹玻璃的有机硅压敏胶组成中,所述硅氢交联剂为粘度为20~50mpa
·
s、含氢量为0.7%~1.6%的氢基聚硅氧烷,例如含氢量包括但不限于0.7%、
0.8%、0.9%、1.0%、1.55%。
[0047]
在本发明中,通过羟基mq硅树脂和羟基生胶这种羟基硅橡胶提前进行高温缩合反应,树脂与生胶形成互穿结构可以提高的产品的保质期,粘度变化小,改善固化后压敏胶的内聚强度,提高产品的耐温和剥离力稳定性,通过控制乙烯基mq硅树脂的含量和乙烯基含量调节产品所需的剥离力,在固化成胶膜时,在铂金催化剂作用下,硅氢交联剂与乙烯基反应,在提高对抗指纹玻璃的剥离力的同时钢板剥离力不会太高,从而使得压敏胶胶膜的具有良好的排气性。
[0048]
通过上述配方制得的有机硅压敏胶可在普通50μm pet、100μm pet、80μm srf以及tpu等基材上进行涂布,对抗指纹玻璃有较高的剥离力,可达50g/inch,钢板剥离力<1000g/inch;本发明制备的抗指纹玻璃的有机硅压敏胶强度高,对抗指纹玻璃剥离力稳定性好,不衰减,排气性能好,透光率高。
[0049]
另一方面,本发明的抗指纹玻璃的有机硅压敏胶的制备方法,包括以下步骤:
[0050]
1)将前述的用于抗指纹玻璃压敏胶的支化乙烯基硅油、乙烯基mq硅树脂、羟基生胶、羟基mq硅树脂、抑制剂和溶剂加入反应釜,搅拌使羟基生胶充分溶解分散在溶剂中。
[0051]
2)通入氮气搅拌,搅拌均匀后,缓慢加入生胶总量的0.05~1%铂金催化剂,然后在回流温度120-150℃下脱水反应3-5h,直至无水产生;
[0052]
3)冷却至室温,加入0.5~1.5份硅氢交联剂,搅拌1~3小时,混合均匀得到抗指纹玻璃的有机硅压敏胶。
[0053]
具体地,例如所述基胶组份的制备方法,包括以下步骤:将粘度为200-3000 mpa
·
s的支化乙烯基硅油、乙烯基mq硅树脂、羟基生胶、羟基mq硅树脂和抑制剂,加入到反应釜中,再加入稀释溶剂到反应釜中且生胶充分溶解分散,再加入生胶总量的0.05~1%的催化剂到反应釜中,在氮气保护的条件下在反应釜中高温脱水反应3~5小时;冷却室温后,加入0.5~1.5份硅氢交联剂,搅拌1~3 小时,混合均匀得到抗指纹玻璃的有机硅压敏胶。
[0054]
其中,各配方组份按下述重量份加入:化乙烯基硅油10-20份,羟基生胶 20~70份,mq硅树脂40~70份,硅氢交联剂0.5~1.5份,抑制剂0.4~1.0份,溶剂80-120份;其中,mq硅树脂包括羟基mq硅树脂和乙烯基mq硅树脂,羟基mq硅树脂和乙烯基mq硅树脂的质量比为(10~1):(1~5)。
[0055]
下面结合具体实施例,对本发明中的原理和特征进行描述,所描述的实施例仅用于解释本发明一部分实施例,并非用于限定本发明的范围。
[0056]
以下实施例和对比例所用的主要原料来源如下:
[0057]
mq树脂:晨飞光电cf808;
[0058]
生胶:合盛有机硅;
[0059]
二甲苯:西陇化学,分析纯;
[0060]
乙炔基环己醇:阿拉丁,分析纯;
[0061]
直链乙烯基硅油:合盛有机硅;
[0062]
硅氢交联剂:科幸有机硅;
[0063]
pt催化剂:贺利氏,铂含量为4000ppm。
[0064]
制备的有机硅压敏胶性能测试方法如下:
[0065]
1.粘度检测方法参考gb/t 10247-2008;
[0066]
2.剥离力检测方法参考gb/t 2792-1998;
[0067]
3.水煮性能检测方法:将涂覆在srf膜上且固化完全的压敏胶带(压敏胶干胶厚度为30-40μm)放入煮沸的蒸馏水中,连续煮沸2小时后取出,胶层边缘不脱胶,不掉粉,即为合格。
[0068]
4.放置3天测试对抗指纹玻璃剥离力稳定性,剥离力测试参考 gb/t2792-1998。
[0069]
制备例支化乙烯基硅油的制备
[0070]
1)在反应烧瓶中加入900g的水和100g浓硫酸,于40℃下搅拌1h至温度恒定;
[0071]
2)缓慢滴加100g苯基三甲氧基硅烷和100g甲基苯基二甲氧基硅烷,升温至50℃后保温1h;
[0072]
3)在80℃温度下蒸出理论量的步骤2)中水解生成的甲醇,加入500g的甲苯和100g氢氧化钾水溶液,在130℃下回流5h;
[0073]
4)在低压下蒸除甲苯溶剂,降温至70℃;
[0074]
5)加入10g四甲基氢氧化铵甲醇溶液及10g二乙烯基二甲基二硅氧烷进行封端,搅拌30min后升温至90℃,反应5h;
[0075]
6)升温至150℃,30min后结束反应;
[0076]
7)水洗、过滤、旋蒸,得到目标产物。
[0077]
实施例1
[0078]
1)将20g支化乙烯基硅油、10g乙烯基mq硅树脂、20g羟基生胶、60g 羟基mq硅树脂和80g二甲苯,0.8g乙炔基环己醇加入反应釜,搅拌溶解;其中,羟基生胶分子量为60万;支化乙烯基硅油的粘度为500mpa
·
s,乙烯基质量分数为1.5%;羟基mq硅树脂与乙烯基mq比例为6:1;
[0079]
2)通入氮气搅拌,搅拌均匀后,将0.8g醋酸用20g二甲苯稀释后缓慢加入,然后在150℃回流脱水下反应4h;
[0080]
3)冷却至室温,加入1.5g硅氢交联剂搅拌均匀,得到压敏胶基胶1;
[0081]
4)在100g基胶1中,加入0.5g锚固剂、100g甲苯,搅拌均匀后加入1.5g 铂含量为4000ppm的铂金催化剂,搅拌均匀后涂布在80μm厚的srf基材上,放置烤箱150℃*2min固化以后贴上氟塑离型膜,测试性能,结果如表1所示。
[0082]
实施例2
[0083]
1)将15g支化乙烯基硅油、10g乙烯基mq硅树脂、25g羟基生胶、60g 羟基mq硅树脂和80g二甲苯,0.8g乙炔基环己醇加入反应釜,搅拌溶解;其中,羟基生胶分子量为62万;支化乙烯基硅油的粘度为1000mpa
·
s,乙烯基质量分数为1.5%,羟基mq硅树脂与乙烯基mq比例为6:1;
[0084]
2)通入氮气搅拌,搅拌均匀后,将0.8g醋酸用20g二甲苯稀释后缓慢加入,然后在150℃回流脱水下反应4h;
[0085]
3)冷却至室温,加入1.5g硅氢交联剂搅拌均匀,得到压敏胶基胶2;
[0086]
4)在100g基胶2中,加入0.5g锚固剂、100g乙酸乙酯,搅拌均匀后加入 1.5g铂含量为4000ppm的铂金催化剂,搅拌均匀后涂布在80μm厚的srf基材上,放置烤箱150℃*2min固化以后贴上氟塑离型膜,测试性能,结果如表1所示。
[0087]
实施例3
[0088]
1)将10g支化乙烯基硅油、70g羟基生胶、30g羟基mq硅树脂、10g乙烯基mq硅树脂和80g二甲苯,0.8g二乙烯基四甲基二硅氧烷加入反应釜,搅拌溶解;其中,羟基生胶分子量为70万;支化乙烯基硅油的粘度为1000mpa
·
s,乙烯基质量分数为0.8%;羟基mq硅树脂与乙烯基mq比例为3:1;
[0089]
2)通入氮气搅拌,搅拌均匀后,将0.8g醋酸用20g二甲苯稀释后缓慢加入,然后在150℃回流脱水下反应4h;
[0090]
3)冷却至室温,加入0.5g硅氢交联剂搅拌均匀,得到压敏胶基胶3;
[0091]
4)在100g基胶3中,加入0.5g锚固剂、100g甲苯,搅拌均匀后加入1.5g 铂含量为4000ppm的铂金催化剂,搅拌均匀后涂布在80μm厚的srf基材上,放置烤箱150℃*2min固化以后贴上氟塑离型膜,测试性能,结果如表1所示。
[0092]
实施例4
[0093]
1)将10g支化乙烯基硅油、70g羟基生胶、35g羟基mq硅树脂、5g乙烯基mq硅树脂和80g二甲苯,0.8g乙炔基环己醇加入反应釜,搅拌溶解;其中,羟基生胶分子量为50w,支化乙烯基硅油的粘度为1500mpa
·
s,乙烯基质量分数为1.5%;羟基mq硅树脂与乙烯基mq比例为7:1;
[0094]
2)通入氮气搅拌,搅拌均匀后,将0.8g醋酸用20g二甲苯稀释后缓慢加入,然后在150℃回流脱水下反应4h;
[0095]
3)冷却至室温,加入1.0g硅氢交联剂搅拌均匀,得到压敏胶基胶4;
[0096]
4)在100g基胶4中,加入0.5g锚固剂、100g甲苯,搅拌均匀后加入1.5g 铂含量为4000ppm的铂金催化剂,搅拌均匀后涂布在80μm厚的srf基材上,放置烤箱150℃*2min固化以后贴上氟塑离型膜,测试性能,结果如表1所示。
[0097]
实施例5
[0098]
1)将10g支化乙烯基硅油、70g羟基生胶、8g羟基mq硅树脂、32g乙烯基mq硅树脂和80g二甲苯,0.8g乙炔基环己醇加入反应釜,搅拌溶解;其中,羟基生胶分子量为60w,支化乙烯基硅油的粘度为1500mpa
·
s,乙烯基质量分数为1.5%;羟基mq硅树脂与乙烯基mq比例为1:4;
[0099]
2)通入氮气搅拌,搅拌均匀后,将0.8g醋酸用20g二甲苯稀释后缓慢加入,然后在150℃回流脱水下反应4h;
[0100]
3)冷却至室温,加入1.5g硅氢交联剂搅拌均匀,得到压敏胶基胶5;
[0101]
4)在100g基胶5中,加入0.5g锚固剂、100g甲苯,搅拌均匀后加入1.5g 铂含量为4000ppm的铂金催化剂,搅拌均匀后涂布在80μm厚的srf基材上,放置烤箱150℃*2min固化以后贴上氟塑离型膜,测试性能,结果如表1所示。
[0102]
实施例6
[0103]
1)将20g支化乙烯基硅油、20g羟基生胶、30g羟基mq硅树脂、10g乙烯基mq硅树脂和80g二甲苯,0.8g乙炔基环己醇加入反应釜,搅拌溶解;其中,羟基生胶分子量为60w,支化乙烯基硅油的粘度为500mpa
·
s,乙烯基质量分数为1.5%;羟基mq硅树脂与乙烯基mq比例为3:1;
[0104]
2)通入氮气搅拌,搅拌均匀后,将0.8g醋酸用20g二甲苯稀释后缓慢加入,然后在150℃回流脱水下反应4h;
[0105]
3)冷却至室温,加入1.5g硅氢交联剂搅拌均匀,得到压敏胶基胶6;
[0106]
4)在100g基胶6中,加入0.5g锚固剂、100g甲苯,搅拌均匀后加入1.5g 铂含量为4000ppm的铂金催化剂,搅拌均匀后涂布在80μm厚的srf基材上,放置烤箱150℃*2min固化以后贴上氟塑离型膜,测试性能,结果如表1所示。
[0107]
对比例1传统压敏胶
[0108]
将100g乙烯基硅橡胶生胶、140g甲基mq硅树脂、20g乙烯基mq硅树脂和150g二甲苯,0.8g乙炔基环己醇,1.5g硅氢交联剂加入反应釜,搅拌溶解;其中,乙烯基硅橡胶生胶的分子量为60万,乙烯基质量分数为0.05%,甲基mq硅树脂与乙烯基mq比例为7:1;搅拌4h后得到压敏胶基胶7。
[0109]
在100g压敏胶基胶7中加入0.5份锚固剂、100份甲苯,搅拌均匀后加入 1.5份铂含量为4000ppm的铂金催化剂,涂布在80μm厚的srf基材上,放置烤箱150℃*2min固化以后胶面覆上氟塑离型膜,测试性能,结果如表1所示。
[0110]
对比例2传统压敏胶添加直链乙烯基硅油
[0111]
将20g直链乙烯基硅油、10g乙烯基mq硅树脂、20g羟基生胶、60g羟基 mq硅树脂和80g二甲苯,0.8g乙炔基环己醇,1.5g硅氢交联剂加入反应釜,搅拌溶解;其中,羟基生胶分子量为60万;直链乙烯基硅油的粘度为500mpa
·
s,乙烯基质量分数为1.5%;羟基mq硅树脂与乙烯基mq比例为6:1;搅拌4h后得到压敏胶基胶8。
[0112]
在100g压敏胶基胶8中加入0.5份锚固剂、100份甲苯,搅拌均匀后加入 1.5份铂含量为4000ppm的铂金催化剂,涂布在80μm厚的srf基材上,放置烤箱150℃*2min固化以后胶面覆上氟塑离型膜,测试性能,结果如表1所示。
[0113]
上述实施例与比较例制备的有机硅压敏胶的测试性能数据如下表1所示:
[0114]
表1实施例1-4与比较例1-2的有机硅压敏胶性能
[0115][0116]
从表中可以看出,通过添加支化乙烯基硅油可使得到的压敏胶具有良好的粘合力稳定性,贴氟塑膜保护,老化后对抗指纹屏幕的剥离力没有明显衰减,对钢板的剥离力<1000g/inch。与传统的简单共混工艺对比,在本发明中,通过 mq硅树脂和羟基生胶进行高温缩聚反应,不仅可以提高产品的保质期,改善压敏胶的内聚强度,而且提高产品的耐温和剥离力稳定性,通过控制mq硅树脂的含量和乙烯基含量来调节产品的剥离力,在固化成胶膜时,在铂金催化剂作用下,硅氢交联剂与乙烯基反应,得到的压敏胶不仅对抗指纹玻璃有良好的剥离力,同时对钢板的剥离力不会太高,从而使得压敏胶胶膜的排气性良好。
[0117]
尽管本发明的内容已经通过上述优选实施例作了详细介绍,但应当认识到上述的描述不应被认为是对本发明的限制。本领域技术人员可以理解,在本说明书的教导之下,可对本发明做出一些修改或调整。这些修改或调整也应当在本发明权利要求所限定的范围之内。