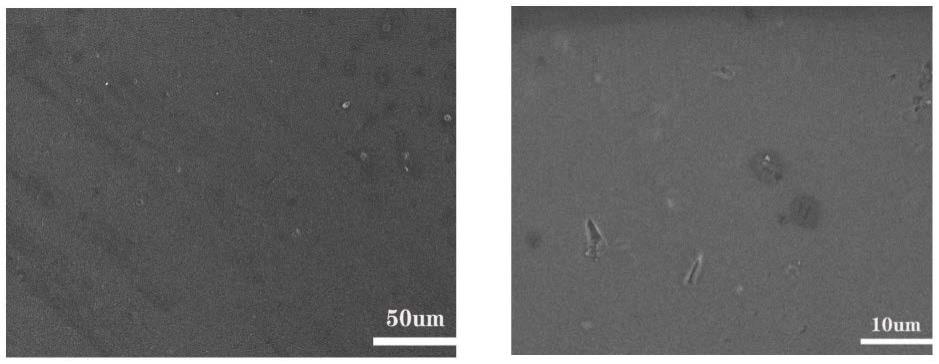
凝胶法在酸性条件下,通过控制硅烷偶联剂的量、搅拌的时间、二乙烯三胺的量获得不同物质的量浓度的硅溶胶,使正硅酸乙酯、γ-(甲基丙烯酰氧)丙基三甲氧基硅烷、十三氟辛基三乙氧基硅烷水解生成纳米氧化硅粒子,通过粒子之间的缩聚反应,交联在一起生成带有含氟基团的硅溶胶,制备获得的硅溶胶在密闭环境下陈化三天,通过浸渍提拉法在预处理好的铝合金基体上涂覆硅溶胶,在室温下即可快速干燥形成均匀完整的有机硅薄膜。
5.本发明技术方案,经过三个步骤实现。
6.(1)纳米有机硅溶胶的制备:
7.室温下将无水乙醇加入到的烧杯中,加热恒温磁力搅拌器,加热温度,紧接着加入正硅酸乙酯,将正硅酸乙酯溶解于无水乙醇中,搅拌均匀,使其充分扩散,滴加去离子水和盐酸到烧杯中,缓慢滴加,使其混合均匀,便于反应,盖上保鲜膜后,继续反应90min,生成的氧化硅粒子粒径大约在5~25nm,然后分别用烧杯加入γ-(甲基丙烯酰氧)丙基三甲氧基硅烷(kh570)和十三氟辛基三乙氧基硅烷(pots),继续搅拌60min,有机前驱体参与水解和缩聚,与正硅酸乙酯生成的氧化硅粒子发生交联,形成三维网状结构,引入疏水基团,最后加入deta,继续搅拌30min,得硅溶胶;
8.如果加入的催化剂量过多或有机溶剂的量过少,会导致硅溶胶发生凝固,对于步骤(1)中的有机溶剂和盐酸要控制其比例。
9.进一步,正硅酸乙酯、无水乙醇、去离子水和盐酸的摩尔比例优选范围为0.073~0.146:0.467~0.934:0.14~0.27:0.00091~0.0062;
10.正硅酸乙酯、二乙烯三胺、γ-(甲基丙烯酰氧)丙基三甲氧基硅烷、十三氟辛基三乙氧基硅烷摩尔质量比为0.073~0.146:0.18~0.94:0.027~0.055:0.014~0.027。进一步优选为:正硅酸乙酯:二乙烯三胺为0.073~0.146:0.37。
11.其中二乙烯三胺加入量对有机硅薄膜的干燥速度、涂层的表面均匀性、硬度及附着力等性能均有影响,用量较低或不含二乙烯三胺涂层容易破裂和脱落,并且疏水性,附着力均难以保证。二乙烯三胺加入量过高会导致在搅拌反应过程中,无水乙醇挥发过快,溶胶会由于无水乙醇的挥发变成凝胶,阻碍实验的进行。正硅酸乙酯、无水乙醇、去离子水、盐酸、二乙烯三胺、γ-(甲基丙烯酰氧)丙基三甲氧基硅烷、十三氟辛基三乙氧基硅烷摩尔质量比为:1~2:6.4~12.8:1.9~3.8:0.0125~0.085:0.18~0.94:0.027~0.055:0.014~0.027。
12.搅拌器加热搅拌为65~70℃,搅拌时间为30~60min。
13.(2)硅溶胶的陈化:
14.搅拌完成后,待其逐步降至室温,密封后放在干燥处静置陈化3天后备用,整个反应过程中,烧杯均需要用保鲜膜封住杯口。
15.硅溶胶的陈化时间越长,硅溶胶中的缩聚就越完全,陈化时间三天(72h)。
16.(3)硅溶胶的涂覆与固化
17.利用浸渍提拉法将步骤(2)中陈化好的硅溶胶涂覆到铝合金基体上,利用镊子将金属基体牢牢夹住,通过人工方式将夹紧的金属基体浸入硅溶胶中浸泡30s,缓慢提拉,速度大概是1~1.5cm/min,上下提拉2~4次,将表面涂有硅溶胶的金属基体在常温下放置1~6h,待其完全固化,得到有机硅薄膜。
18.步骤(3)中的铝合金基体要采用酸洗处理,在用丙酮脱脂,紧接着用去离子水冲
洗,所有的步骤均在超声中进行。
19.与现有技术相比,本发明的优点:
20.(1)本发明制备的硅溶胶无需加热固化,在常温下发生高效率,短时间内固化,并且生成的膜完整均匀,不仅可以降低实验成本,改善制备工艺,而且防止高温下烘干所带来的不均匀内部应力,使得硅溶胶薄膜发生破裂。
21.(2)硅溶胶中引入的有机硅前驱体,可以进一步优化生成单体的分散性和溶胶浓稠度,降低液体表面张力和聚合率及溶胶的流动性。
22.(3)硅溶胶中引入deta,抑制生成的交联体相互干扰,使其产生网状分层,保持涂层密度稳定,增强了涂层的表面疏水性,均匀性和耐磨性能,再者与无水乙醇相容,制备涂层会加速挥发,固化时间由12~24h降至1~6h,涂层固化效率大大提升,并且增强铝合金基体与涂层的结合力。
附图说明
23.图1为实施例1中基体表面涂层sem图;
24.图2(a)和(b)是实施例2;(c)和(d)为实施例3,(e)为实施例4,(f)为对比例1,(g)为对比例2,(h)为对比例3,中的表面涂层sem图;
25.图3为实施例1与对比例1及对比例2的接触角比较;
26.图4为实施例1中硅溶胶的ftir图谱;
27.图5为实施例1的与对比例1以及纯基体的极化曲线图。
具体实施方式
28.下面通过具体的实施方式来进一步说明本发明的技术方案。本领域技术人员应该明了,所述实施例仅仅是帮助理解本发明,不应试位对本发明的具体限制。下面结合附图说明和具体实施案例对本发明进一步详细说明。
29.实施例1
30.(1)溶胶-凝胶法制备纳米有机硅溶胶
31.室温下将0.467mol的无水乙醇加入到200ml的烧杯中,加热恒温磁力搅拌器,使得温度提升到70℃,紧接着加入0.073mol的正硅酸乙酯溶解于无水乙醇中,将正硅酸乙酯搅拌均匀,使其充分扩散,用胶头滴管滴加0.27mol的去离子水和0.0062mol的盐酸(大约2-5滴)到烧杯中,缓慢滴加,使其混合均匀,便于反应,盖上保鲜膜后,继续反应90min,然后分别用烧杯加入在0.055mol范围内的kh570和0.014mol范围内的pots继续搅拌60min,最后加入0.037mol范围内的deta,继续搅拌30min。
32.(2)硅溶胶的陈化
33.搅拌完成后,待其逐步降温,密封后放在干燥处静置陈化3天后备用,整个反应过程中,烧杯均需要用保鲜膜封住杯口。
34.硅溶胶的涂覆与固化
35.本次使用的基体是车载铝合金6000系,al-mg-si合金。准备的规格在15mm
×
15mm
×
2mm的al-mg-si合金基体。将铝合金基体放入酸洗液中,酸洗30s,取出后用丙酮脱脂洗去油污,再用去离子水冲洗,整个过程均在超声中清洗,清洗完成后用滤纸吸干铝合金基体上
的水分,放入烘干箱中干燥后待用;将基体用镊子夹住固定,然后使用浸渍提拉法通过人工方式将夹紧的金属铝合金基体浸入硅溶胶中浸泡30s,缓慢提拉,速度大概是1~1.5cm/min,上下提拉2~4次,将表面涂有硅溶胶的金属基体在常温下放置1h,待其完全固化,使表面得到含氟硅烷的纳米有机硅薄膜(约7微米)。然后对表面处理过后的铝合金进行表征。
36.图1为实施例1中基体表面涂层sem图,从图中可以看出涂层的表面均匀光滑,无破裂。
37.实施例2
38.(1)纳米有机硅溶胶的制备过程中将kh570的物质的量更改为0.001mol或0.1mol,其他参数及步骤同实施例1;
39.(2)硅溶胶的陈化同实施例1;
40.(3)硅溶胶的涂覆和固化同实施例1。
41.图2(a)和(b)为实施例2中分别加入0.001mol或0.1molkh570的基体表面涂层sem图,如下图所示,降低硅烷偶联剂kh570的量涂层表面光滑均匀,但是会发生破裂,增加kh570的量,涂层表面破裂严重,说明kh570的量过少或过多会对涂层表面质量有重要影响,其原因由于过少导致粘结力差,过多导致硅溶胶固含量高,容易团聚,容易产生裂纹。
42.实施例3
43.(1)纳米有机硅溶胶的制备过程中将pots的物质的量更改为0.005mol或0.1mol,其他参数及步骤同实施例1;
44.(2)硅溶胶的陈化同实施例1;
45.(3)硅溶胶的涂覆和固化同实施例1。
46.图2(c)和(d)为实施例3中基体表面涂层sem图,如下图所示,降低硅烷偶联剂pots的量和增加pots的量同样可以在铝合金基体上制备出纳米有机硅薄膜,不会产生破裂,说明pots对涂层表面的质量影响不大。
47.实施例4
48.(1)纳米有机硅溶胶的制备过程中将搅拌温度设定为室温,其他参数及步骤同实施例1;
49.(2)硅溶胶的陈化同实施例1;
50.(3)硅溶胶的涂覆和固化同实施例1。
51.图2(e)为实施例4中基体表面涂层sem图,结果如下图所示,降低反应过程中的搅拌温度,在铝合金基体上生成纳米有机硅薄膜是破裂的。
52.对比例1
53.(1)纳米有机硅溶胶的制备过程中不添加kh570和pots,其他参数及步骤同实施例1;
54.(2)硅溶胶的陈化同实施例1;
55.(3)硅溶胶的涂覆和固化同实施例1。
56.图2(f)为对比例1中基体表面涂层sem图,结果如下图所示,在铝合金基体上生成的纳米有机硅薄破裂严重,与实施例1对比说明前驱体的加入可以有效改善涂层的均匀程度,增大硅溶胶与涂层的表面粘结力。
57.对比例2
58.(1)纳米有机硅溶胶的制备过程中不添加deta,其他参数及步骤同实施例1;
59.(2)硅溶胶的陈化同实施例1;
60.(3)硅溶胶的涂覆和固化同实施例1。
61.图2(g)为对比例2中基体表面涂层sem图,结果如下图所示,未添加deta的硅溶胶通过浸渍提拉法获得的纳米有机硅涂层,局部虽然均匀,可能因为前驱体的官能团与铝合金基体表面游离羟基的结合导致,其余部分破裂严重,而且固固化所需时间在24h,相比较加入的效果严重降低,固化时间变长。
62.因此,不加入deta不仅无法保证高效固化时间,而且涂层的表面均匀性、硬度及附着力也会下降,涂层容易破裂和脱落。
63.对比例3
64.(1)纳米有机硅溶胶的制备同实施例1;
65.(2)硅溶胶的陈化同实施例1;
66.(3)硅溶胶的涂覆和固化过程中,将涂覆硅溶胶的铝合金由常温固化改为100℃烘箱加热固化,其他参数及步骤同实施例1,然后对其进行表征;
67.图2(h)为对比例3中基体表面涂层sem图,结果如下图所示,加热固化的涂层表面结构因内部热应力不均匀导致涂层开裂受损,附着力降低,耐腐蚀性能变差。
68.实施例5
69.(1)样品的形貌观察:
70.对样品表面喷金后,采用扫描电子显微镜(jsm-it100),观察基体的表面形貌,其表面形貌如下图所示。并且实施例1涂层的表面铅笔硬度在h~2h之间,涂层在表面的附着力等级为1~2级。
71.(2)样品的表面涂层的接触角(ca)测量:
72.将带有涂层的铝合金基体放置于接触角测量仪的载物台上,其次将微量进液器固定在载物台上方,打开测试软件,手动推进微量进液器大约5ul,用铝合金基体接住液滴,将摄像机拍摄的画面固定住,利用量角法测量降落的液滴的接触角大小,测量的结果如下图所示。
73.图3为实施例1(左)120
°
,与对比例1(右)45
°
及对比例2(下)100
°
。
74.(3)傅里叶红外光谱仪(ftir)测试样品中的官能团:
75.使用傅里叶红外光谱仪对实施例1进行测量,测得的傅里叶红外光谱图如下图4所示,从各组的红外光谱中可以看出,在3420cm-1
处强而宽的是结构水的-oh键的反对称伸缩振动峰;2880cm-1
处的吸收峰是c-h的反对称伸缩振动峰;971cm-1
处左右的范围的吸收峰是si-oh的键的弯曲振动吸收峰;1330cm-1
附近出现的吸收峰是c-f键的弯曲振动吸收峰;在890-690cm-1
附近出现的峰值是si-c键的伸缩振动吸收峰;在1090cm-1
附近出现的一个很强的吸收峰是si-o-si的反对称伸缩振动吸收峰;说明sio2上成功接枝了-ch3和-cf-基团,形成了si-ch3和si-o-cf键,使得制备的sio2溶胶显示出了良好的疏水性能。
76.(4)电化学工作站测量样品的极化曲线
77.将样品用导电胶与导线连接,再用乳胶固定住,放置于事先模拟海水的3.5wt%的氯化钠溶液中,测得是实例一的极化曲线与镀膜前测得的极化曲线如下图5所示。实施例1的自腐蚀电位优于基体的自腐蚀电位,腐蚀电流密度小,起到了很好的防腐蚀性能。
78.(5)耐摩擦实验
79.借助砂纸砝码进行摩擦实验,旨将样品有涂层的一面与300目砝码的砂纸接触,再在样品上放置一个重300克的砝码,使样品受到2500pa的压强,然后在一测推动样品使之载着砝码一起往一个方向滑动,每滑动20cm取出用水滴测量接触角并记录,至此完成一次摩擦实验。涂层的耐磨性由能够保持疏水的最大摩擦距离来定性表征,
80.实验中,实施例1加入deta的耐摩擦距离为600cm,对比例2未加入deta的耐磨擦距离为200cm,说明加入deta还能使耐磨性大大提高。