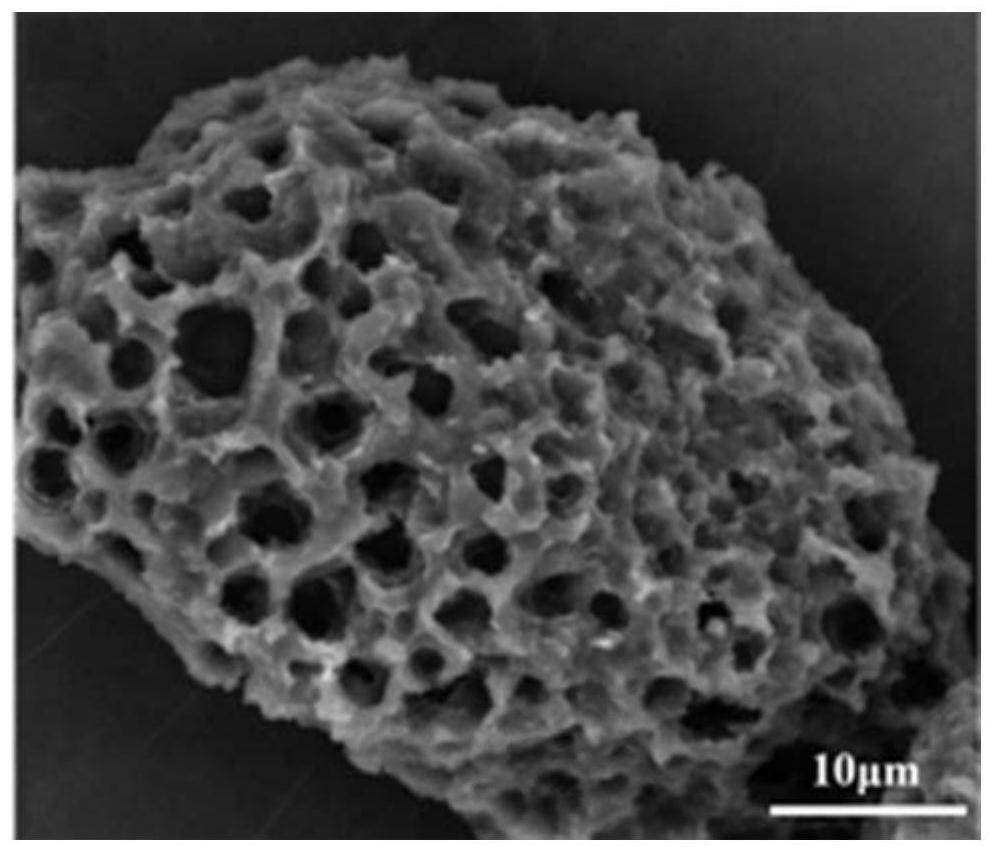
1.本发明涉及一种金刚石颗粒表面腐蚀方法,尤其涉及一种可以在金刚石颗粒表面形成多孔结构,提高其自锐性和磨削性能的金刚石颗粒腐蚀工艺,属于新型超硬材料制备领域。
背景技术:2.金刚石单晶因其具有高硬度、高导热率和高化学稳定性而被作为磨削材料广泛应用于单晶硅、铁磁铁氧体、蓝宝石基片、sic结构件等无机材料的磨削加工。
3.随着科学技术的发展,制造业对磨削加工后的材料的表面质量要求越来越高,甚至要求应力损伤层厚度及表面粗糙度都达到纳米级别。但是传统的单颗金刚石磨粒上只有一个粗大切削刃参与磨削,磨削刃锋利时材料去除效率较高,但磨削应力集中,磨削纹理深且粗,高质量的工件表面难以创成。当前解决这一问题的方法,都是采用更细粒度的金刚石来进行磨削加工,但是细粒度金刚石在实现高质量的加工表面同时会使磨削效率大幅度降低,大幅度增加了材料的加工成本。
4.为了提高金刚石的磨削效率,目前大量的工作都集中在金刚石颗粒的表面改性或增加金刚石内部缺陷方面:如采用镍磷包覆法制备改性金刚石颗粒,改性后金刚石颗粒表面含有更多的凸起和凹坑,磨削过程中,凸起发挥切割刃作用,能有效提高金刚石颗粒的磨削效率;或使用feni作为催化剂,在高温高压下合成的金刚石单晶过程中通过工艺控制,使生长的金刚石晶体中形成过饱和的空位和夹杂物等缺陷,磨削过程中缺陷提高了金刚石的自锐性。但是以上两种方法都存在工艺复杂,难以精确调控处理后的金刚石颗粒的磨削性能的缺点,所以并没有在工业上大范围推广应用。
技术实现要素:5.基于此,本发明的目的是,从金刚石颗粒结构设计方面考虑,提供一种可实现金刚石颗粒表面的定向可控腐蚀,从而在金刚石颗粒表面产生多孔结构的金刚石颗粒表面的腐蚀方法。
6.为实现上述目的,本发明采用以下技术手段:
7.一种金刚石颗粒表面的腐蚀方法,包括如下步骤:
8.将玻璃原料球磨ⅰ后熔融并水淬,得到玻璃碎块;所述玻璃原料按重量百分比计,包括硼酸40-45%、碳酸钠9%、碳酸钾5%、三氧化二铬2-3%、三氧化二锑3-4%、五氧化二钒2-3%和二氧化硅31%-38%;
9.将所述玻璃碎块与硅烷偶联剂和醇溶性酚醛树脂于醇中混合并球磨ⅱ,得到悬浊液;
10.将金刚石颗粒表面羟基化后浸渍于所述悬浊液中,然后加热所述金刚石颗粒,使所述醇溶性酚醛树脂固化;
11.对所述金刚石颗粒进行热处理,使所述金刚石颗粒表面包覆多孔玻璃膜层;
12.采用氢氧化铁溶胶填充所述多孔玻璃膜层中的孔;
13.所述金刚石颗粒表面的腐蚀方法,还包括加热所述金刚石颗粒,使氢氧化铁溶胶分解得到的氧化铁腐蚀金刚石。
14.所述熔融的温度为1200-1250℃;
15.所述熔融的升温速率为3-5℃/min;
16.所述球磨ⅰ的球料重量比为1.2:1;
17.所述球磨ⅰ的速度为30-40r/min;
18.所述球磨ⅰ的时间为30-60min。
19.所述悬浊液的液相中,所述硅烷偶联剂的含量为3wt%,所述醇溶性酚醛树脂的含量为5-6wt%;
20.所述硅烷偶联剂包括kh560;
21.所述醇包括乙醇;
22.所述悬浊液的固相中包括所述玻璃碎块经球磨ⅱ得到的玻璃微粉;
23.所述玻璃微粉的含量为55.6wt%。。
24.所述羟基化采用的无机碱包括氢氧化钠或氢氧化钾;
25.所述固化的温度为160-180℃。
26.所述金刚石颗粒的粒径为80-250μm;
27.所述多孔玻璃膜层的厚度为5-20μm;
28.所述多孔玻璃膜层中的孔的孔径1-10μm。
29.所述热处理的温度为650-750℃;
30.所述热处理的升温速率为为5-8℃/min;
31.所述热处理的真空度为1-10pa。
32.所述悬浊液的制备方法包括向醇中加入硅烷偶联剂和醇溶性酚醛树脂,搅拌后,加入所述玻璃碎块,再进行球磨的步骤;
33.所述搅拌的速度为2000-3000r/min;
34.所述搅拌的时间为1-1.5h,
35.所述球磨ⅱ的介质包括氧化锆;
36.所述玻璃碎块,醇溶液和氧化锆球的重量比为1:0.8:2;
37.所述球磨ⅱ的转速为50r/min;
38.所述球磨ⅱ的时间为12h。
39.所述氢氧化铁溶胶的制备方法包括调节铁盐溶液的ph使铁盐水解的步骤;或者
40.所述氢氧化铁溶胶的制备方法包括在搅拌的条件下向铁盐溶液中滴加ph调节剂调节铁盐溶液的ph使铁盐水解的步骤;
41.所述搅拌的速度为800r/min;
42.所述铁盐包括氯化铁;
43.所述铁盐溶液的浓度为0.1mol/l;
44.所述ph调节剂包括乙酸钠溶液;
45.所述ph调节剂的加入量为铁盐溶液质量的8-10%;
46.所述乙酸钠溶液的浓度为0.1mol/l。
47.包括加热所述金刚石颗粒到700-800℃,使氢氧化铁溶胶分解得到的氧化铁腐蚀金刚石的步骤。
48.包括以4-5℃/min的速率加热所述金刚石颗粒到700-800℃,使氢氧化铁溶胶分解得到的氧化铁腐蚀金刚石的步骤。
49.所述金刚石颗粒表面的腐蚀方法,还包括将所述金刚石颗粒浸泡于hf溶液中,然后烘干的步骤;
50.所述hf溶液的浓度为10%;
51.所述烘干的温度为120℃。
52.相比于现有技术,本发明带来以下技术效果:
53.本发明提供的方法能制备出表面呈现为多孔结构的金刚石颗粒(参见图6),并且可以方便的通过改变工艺参数来控制金刚石颗粒表面腐蚀孔的深度,从而改变腐蚀后的金刚石颗粒的自锐性和磨削性能。
54.本发明提供的方法腐蚀金刚石后得到的金刚石颗粒在磨削过程中,其工作方式为微纳尺度的多磨削刃。相比于传统金刚石的单刃磨削,其磨削刃尺寸变小,但数量增多,磨削热和应力得以分散,有利于提高加工表面质量;同时金刚石的多孔结构会使金刚石的抗压强度大幅度降低,自锐性明显提高,能有效的提高磨削效率。
附图说明
55.为了更清楚地说明本发明实施例的技术方案,下面将对实施例中所需要使用的附图作简单地介绍,应当理解,以下附图仅示出了本发明的某些实施例,因此不应被看作是对范围的限定,对于本领域普通技术人员来讲,在不付出创造性劳动的前提下,还可以根据这些附图获得其他相关的附图。
56.图1示出了实施例5中,1pa下650℃保温20min后金刚石表面玻璃膜层的显微照片;从图中可以看出在1pa下650℃保温20min后致密的玻璃膜层表面产生了1-4μm的气孔;
57.图2示出了实施例10中,1pa下750℃保温20min后金刚石表面玻璃微粉的显微照片;从图中可以看出在1pa下750℃保温20min后致密的玻璃膜层表面产生了2-10μm的气孔;
58.图1和图2表明金刚石表面表面玻璃膜层中的气孔直径会随保温温度的提高而增加;
59.图3示出了fe2o3腐蚀金刚石的过程原理图;
60.图4示出了实施例7中,在750℃空气气氛下保温1h后获得的多孔金刚石颗粒的显微照片;从图中可以看出金刚石表面形成较浅的腐蚀坑
61.图5示出了实施例7中,在750℃空气气氛下保温3h后获得的多孔金刚石颗粒的显微照片;从图中可以看出金刚石表面腐蚀坑较深,形成联通的多孔结构;
62.图4、图5表明通过控制保温时间,可以精确地控制腐蚀坑深度,从而调控金刚石的显微结构。
63.图6示出了实施例7制备得到的表面多孔的金刚石颗粒的显微照片;从图中可以看出该方法可高效制备多孔的金刚石颗粒;
64.图7示出了采用实施7制备得到的表面多孔的金刚石颗粒磨削得到碳化硅的表面显微照片;从图中可以看出工件表面磨削纹路均匀细密,工件表面质量较好;
65.图8示出了传统单晶金刚石磨削的碳化硅片表面。从图中可以看出工件表面磨削纹路粗大不均匀,工件表面质量较差;传统单晶金刚石的来源为工业合成金刚石。
具体实施方式
66.下面详细描述本发明的实施例,所述实施例的示例在附图中示出,其中自始至终相同或类似的标号表示相同或类似的元件或具有相同或类似功能的元件。下面通过参考附图描述的实施例是示例性的,仅用于解释本发明,而不能理解为对本发明的限制。
67.本发明提供了一种金刚石颗粒的腐蚀方法,该方法首先在金刚石颗粒表面包覆多孔玻璃膜层;然后采用氢氧化铁溶胶填充所述多孔玻璃膜层中的孔;最后加热所述金刚石颗粒,使氢氧化铁溶胶分解得到的氧化铁腐蚀金刚石。这样,氧化铁在腐蚀金刚石时,只会腐蚀氧化铁填充处的金刚石的表面,而未填充的部分则不会被腐蚀。这种腐蚀方法,会在金刚石表面形成孔洞,而这些孔洞的孔壁外沿可作为磨削刃,而提高磨削效率和磨削效果。
68.优选的,金刚石颗粒的表面是经过了预处理的。所述预处理包括如下步骤:
69.首先,对金刚石颗粒进行清洗。即,将一定粒度的金刚石颗粒放入无水乙醇中,在2000-4000hz的频率下超声清洗20-40分钟,捞出金刚石颗粒,在室温下干燥后,然后将金刚石颗粒浸入到3-5wt%的naoh水溶液中,浸泡20-40分钟,金刚石颗粒捞出后用去离子水冲洗至中性,在120度烘箱中烘干,完成金刚石颗粒的表面预处理。超声清洗可去除金刚石颗粒表面的污染物,然后浸泡在naoh水溶液中,可增加金刚石颗粒表面的oh-含量,活化金刚石颗粒表面。
70.优选的,在金刚石颗粒表面包覆多孔玻璃膜层可采用如下方法。
71.首先配置玻璃原料,具体配方如下:
[0072][0073]
然后采用用所述玻璃原料制备玻璃碎块。具体的,将称好的上述玻璃原料倒入刚玉球磨坛中,球磨坛直径600mm,按球料重量比1.2:1的比例加入直径为30mm氧化锆球,球磨坛自转速度为30-40r/min。原料球磨30-60min后取出。然后对玻璃原料进行熔融处理。具体的,将坩埚炉以3-5℃/min的速度,升温到1200-1250℃,塞上堵料杆,倒入混好的玻璃原料,倒入原料的体积为坩埚体积的2/3,在坩埚炉出料口处放一装满水的耐热钢容器。待炉温再次升到1200℃时,保温半小时,提起堵料杆让熔化的原料流入水中进行水淬,将水淬后得到的玻璃碎块收集,烘干待用。
[0074]
在所述玻璃原料中,二氧化硅为玻璃微粉的网络形成体。硼酸、碳酸钠和碳酸钾在玻璃原料熔炼过程中转变为三氧化二硼、氧化钠和氧化钾,其在玻璃原料中作为促熔成分,
使玻璃原料的软化点降低到550℃以下。玻璃原料中引入三氧化二铬,以降低熔融玻璃原料的表面张力,使熔融其易于在金刚石颗粒表面铺展;玻璃原料中引入五氧化二钒可以改善熔融玻璃原料与金刚石颗粒的润湿性,使熔融玻璃原料更容易包裹金刚石颗粒,三氧化二锑则作为后期金刚石表面玻璃膜层的发泡剂引入。各原料按比例混合后在1200℃熔炼后,形成均匀的玻璃熔融体,然后水淬获得玻璃碎块。
[0075]
然后,需将玻璃碎块磨细然后包覆在金刚石颗粒表面。具体的,在无水乙醇溶液中加入3wt%的kh560硅烷偶联剂和5-6wt%的醇溶性酚醛树脂,在2000-3000r/min的条件下搅拌1h,获得kh560乙醇溶液。以kh560乙醇溶液为分散介质,10mm的氧化锆球为球磨介质,向kh560乙醇溶液中加入玻璃碎块。玻璃碎块,kh560乙醇溶液和氧化锆球质量比为1:0.8:2,转速为50r/min,球磨12h后,用400#筛网过滤研磨后的浆料,获得悬浊液。kh560硅烷偶联剂分子结构中,一端为疏水的环氧基团,另一端为可水解甲氧基团。在球磨过种中,kh560与乙醇发生复分解反应,甲氧基团会与脱去羟基的乙醇分子结合,形成甲乙醚,kh560中则会引入si-oh官能团。在玻璃碎块球磨过程中,kh560与乙醇反应形成的si-oh键能与玻璃粉体表面的si原子形成si-o-si键,在玻璃粉体表面形成有机层,提高玻璃粉体在乙醇溶液中的悬浮稳定性。酚醛树脂则作为临时粘接剂加入,可使磨细后得到的玻璃微粉粘结在金刚石颗粒表面。玻璃碎块在kh560和酚醛树脂的乙醇溶液中球磨12h后,用400#筛网过滤后,获得悬浊液。
[0076]
然后,将表面处理过的金刚石颗粒,浸渍在悬浊液中,浸渍1-2分钟后用不锈钢筛网将金刚石颗粒从悬浊液中捞出,浸渍后金刚石颗粒在筛网上沥干1-2h,将沥干的金刚石颗粒平摊在表面垫有bn的耐热钢板上,然后将金刚石颗粒连同钢板一起放入烘箱中,在160-180℃保温1-2小时,自然冷却,完成金刚石颗粒的表面包覆处理。此时金刚石表面的酚醛树脂固化将玻璃微粉牢固的粘接在金刚石表面,自然冷却后完成金刚石颗粒的表面包覆处理。
[0077]
接着,对金刚石颗粒进行热处理。具体的,将金刚石包覆颗粒连同耐热钢板一起放入电热丝加热的真空炉中,先以5-8℃/min的速度升温至650-750℃,到温后抽真空,真空度控制在1-10pa,保温20-60min后,关炉,随炉冷却,完成金刚石包覆颗粒的热处理。在热处理过程中,当温度升高至300℃时树脂开始裂解,当温度升高到600℃以上时,树脂氧化完全,同时到金刚石表面的玻璃微粉开始软化熔融,在金刚石表面形成致密的粘流层,当温度达到650-750℃时抽真空,真空度控制在1-10pa。此时因为玻璃微粉中含有大量的三氧化二硼和少量的三氧化二锑,在真空下保温时,它们会以气体的形式挥发,在金刚石颗粒表面熔融的玻璃膜层中产生气孔,可以通过控制保温温度调整玻璃膜层中气孔的大小,温度越高玻璃膜层中的气孔越大(参见图1、图2),从而进一步控制氧化腐蚀处理获得的金刚石颗粒的表面腐蚀坑的直径。
[0078]
至此,完成在金刚石表面包覆多孔玻璃膜层。
[0079]
可同步进行的,是氢氧化铁溶胶的配置。具体的,在800r/min的搅拌条件下向浓度为0.1mol/l的fecl3溶液中滴加浓度为0.1mol/l的乙酸钠水溶液,乙酸钠溶液的加入量为fecl3溶液质量的8-10%,乙酸钠溶液滴加完成后再搅拌20-30min,获得稳定的氢氧化铁溶胶。乙酸钠溶液的加入会提高fecl3溶液中oh-的含量,促进fecl3溶液中fe
3+
的水解形成氢氧化铁溶胶。乙酸钠水溶液通过滴加的方式,是为了控制fe
3+
的水解速度,获得稳定的氢氧化
铁溶胶。
[0080]
对金刚石颗粒进行氧化处理后,对金刚石颗粒的腐蚀即完成。
[0081]
具体的,将金刚石包覆颗粒浸渍氢氧化铁溶胶中,浸渍1-2分钟后用不锈钢筛网将金刚石包覆颗粒从氢氧化铁溶胶中捞出,浸渍后金刚石颗粒在筛网上沥干1-2h,再将沥干的金刚石包覆颗粒平摊在表面垫有bn的陶瓷板上,放入马弗炉中,在空气气氛下,以4-5℃/min的速率升温至700-800℃保温1-3h后随炉冷却,完成金刚石包覆颗粒的氧化处理。再将氧化处理后的金刚石包覆颗粒浸泡于过量的10wt%的hf溶液中2-3h后捞出,用去离子水冲洗至中性,再120℃烘箱中烘干后,获得表面腐蚀处理的金刚石颗粒。热处理后的金刚石颗粒,表面的多孔玻璃膜层中存在大量气孔,气孔处的金刚石颗粒基体表面裸露在外,将金刚石包覆颗粒浸渍氢氧化铁溶胶后,气孔下裸露的金刚石表面会附着一层氢氧化铁溶胶层。氧化处理过程中,当温度超过500℃时,氢氧化铁凝胶层完全分解为fe2o3,玻璃包覆层气孔下的金刚石表面直接与fe2o3相接触,温度超过700℃时,fe2o3开始氧化金刚石表面的碳原子,使fe-o键断裂,生成co和feo,随着金刚石还原fe2o3反应的进行,在金刚石与fe2o3的界面处会生成feo产物层。由于feo中fe-o键的键能大,在腐蚀温度下不与金刚石产生化学反应,腐蚀剂fe2o3中的氧需要通过在feo产物层中进行扩散,才能与金刚石发生化学反应(参见图3)。使fe2o3腐蚀金刚石的反应速率变慢,从而便于进行控制腐蚀速率,能够方便的通过控制保温时间来控制金刚石表面腐蚀坑的深度(参见图4、图5)。
[0082]
去除金刚石颗粒表面的多孔玻璃微粉,而得到腐蚀后的金刚石颗粒
[0083]
氧化处理后的金刚石颗粒浸泡于过量的10wt%的hf溶液中2-3h后捞出,去除金刚石颗粒表面的多孔玻璃膜层,用去离子水冲洗至中性然后再120℃烘箱中烘干后,即得。
[0084]
由此可见,
[0085]
实施例1
[0086]
金刚石颗粒的表面预处理
[0087]
将一定粒度的金刚石颗粒放入无水乙醇中,在2000hz的频率下超声清洗20分钟,捞出金刚石颗粒,在室温下干燥后,然后将金刚石颗粒浸入到5wt%的naoh水溶液中,浸泡20分钟,金刚石颗粒捞出后用去离子水冲洗至中性,在120度烘箱中烘干,完成金刚石颗粒的表面预处理。
[0088]
实施例2
[0089]
金刚石颗粒表面包覆玻璃的熔炼
[0090]
采用高温熔炼法制备金刚石表面包覆玻璃微粉,玻璃微粉的重量百分比配方如下:
[0091][0092]
将称好的各种原料倒入刚玉球磨坛中,球磨坛直径600mm,按球料质量比1.2:1的比例加入直径为30mm氧化锆球,球磨坛自转速度为40r/min。原料球磨60min后取出,获得包覆玻璃熔炼原料。
[0093]
将坩埚炉以5℃/min的速度,升温到1250℃,塞上堵料杆,倒入混好的熔炼原料粉,倒入料粉的体积为坩埚体积的2/3,在坩埚炉出料口处放一装满水的耐热钢容器。待炉温再次升到1200℃时,保温半小时,提起堵料杆让熔化的玻璃流入水中进行水淬,将水淬后的玻璃碎块收集,烘干待用。
[0094]
实施例3
[0095]
金刚石颗粒表面包覆剂的制备
[0096]
在无水乙醇溶液中加入3wt%的kh560硅烷偶联剂和6wt%的醇溶性酚醛树脂,在3000r/min的条件下搅拌1h,获得kh560乙醇溶液。以kh560乙醇溶液为分散介质,10mm的氧化锆球为研磨介质。玻璃碎块:kh560乙醇溶液:氧化锆球质量比为1:0.8:2,转速为50r/min,球磨12h后,用400#筛网过滤研磨后的浆料,获得悬浊液。
[0097]
实施例4
[0098]
金刚石颗粒表面的包覆处理
[0099]
将实施例1获得的表面处理过的金刚石颗粒,浸渍在步骤3制备的悬浊液中,浸渍2分钟后用不锈钢筛网将金刚石颗粒从包覆剂中捞出,浸渍后金刚石颗粒在筛网上沥干2h,将沥干的金刚石颗粒平摊在表面垫有bn的耐热钢板上,然后将金刚石颗粒连同钢板一起放入烘箱中,在160℃保温1小时,自然冷却,完成金刚石颗粒的表面包覆处理。
[0100]
实施例5
[0101]
金刚石包覆颗粒的热处理
[0102]
将实施例4获得的金刚石包覆颗粒连同耐热钢板一起放入电热丝加热的真空炉中,先以8℃/min的速度升温至650℃,到温后抽真空,真空度控制在1pa,保温60min后,关炉,随炉冷却,完成金刚石包覆颗粒的热处理。
[0103]
实施例6
[0104]
氢氧化铁溶胶的配置
[0105]
在800r/min的搅拌条件下向浓度为0.1mol/l的fecl3溶液中滴加浓度为0.1mol/l的乙酸钠水溶液,乙酸钠溶液的加入量为fecl3溶液质量的8%,乙酸钠溶液滴加完成后再搅拌30min,获得稳定的氢氧化铁溶胶。
[0106]
实施例7
[0107]
金刚石包覆颗粒的氧化处理
[0108]
将金刚石包覆颗粒浸渍在步骤6制备的氢氧化铁溶胶中,浸渍2分钟后用不锈钢筛网将金刚石包覆颗粒从氢氧化铁溶胶中捞出,浸渍后金刚石颗粒在筛网上沥干2h,再将沥干的金刚石包覆颗粒平摊在表面垫有bn的陶瓷板上,放入马弗炉中,在空气气氛下,以5℃/min的速率升温至750℃保温2h后随炉冷却,完成金刚石包覆颗粒的氧化处理。再将氧化处理后的金刚石包覆颗粒浸泡于过量的10wt%的hf溶液中2h后捞出,用去离子水冲洗至中性,再120℃烘箱中烘干后,获得表面腐蚀处理的金刚石颗粒。
[0109]
用本发明实施例1-7制备得到的的金刚石颗粒制备的树脂金刚石磨盘在对碳化硅密封环表面进行平面磨削时,与相同粒度的传统金刚石制备的磨盘相比,由于金刚石颗粒呈现为表面多孔结构,金刚石颗粒与sic相接触磨削时,多孔金刚石颗粒更容易破碎,自锐性更好,磨削效率更高。采用用本发明提供的方法制备得到的粒度为70/80的金刚石颗粒制备的树脂金刚石磨盘对8英寸sic密封环进行磨削加工时,磨削加工量可达到0.9mm/分钟,而传统粒度为70/80的单晶金刚石颗粒制备的树脂金刚石磨盘对8英寸sic密封环进行加工时,其磨削加工量为0.6mm/分钟,其磨削效率能提高约50%。同时多孔金刚石磨削刃数量增多,使得单个刃口的磨削深度减小,工件表面单位面积上加工的刻痕数目增加,深度降低。其加工的碳化硅的表面的磨削纹路更加细腻,磨削质量更好(参见图7、图8)。
[0110]
实施例8
[0111]
金刚石颗粒的表面预处理
[0112]
将一定粒度的金刚石颗粒放入无水乙醇中,在4000hz的频率下超声清洗40分钟,捞出金刚石颗粒,在室温下干燥后,然后将金刚石颗粒浸入到3wt%的naoh水溶液中,浸泡40分钟,金刚石颗粒捞出后用去离子水冲洗至中性,在120度烘箱中烘干,完成金刚石颗粒的表面预处理。
[0113]
实施例9
[0114]
金刚石颗粒表面包覆玻璃的熔炼
[0115]
采用高温熔炼法制备金刚石表面包覆玻璃微粉,玻璃微粉的重量百分比配方如下:
[0116][0117]
将称好的各种原料倒入刚玉球磨坛中,球磨坛直径600mm,按球料质量比1.2:1的比例加入直径为30mm氧化锆球,球磨坛自转速度为30r/min。原料球磨30min后取出,获得包覆玻璃熔炼原料。
[0118]
将坩埚炉以3℃/min的速度,升温到1200℃,塞上堵料杆,倒入混好的熔炼原料粉,
倒入料粉的体积为坩埚体积的2/3,在坩埚炉出料口处放一装满水的耐热钢容器。待炉温再次升到1200℃时,保温半小时,提起堵料杆让熔化的玻璃流入水中进行水淬,将水淬后的玻璃碎块收集,烘干待用。
[0119]
实施例10
[0120]
金刚石颗粒表面包覆剂的制备
[0121]
在无水乙醇溶液中加入3wt%的kh560硅烷偶联剂和5wt%的醇溶性酚醛树脂,在3000r/min的条件下搅拌1h,获得kh560乙醇溶液。以kh560乙醇溶液为分散介质,10mm的氧化锆球为研磨介质。玻璃碎块:kh560乙醇溶液:氧化锆球质量比为1:0.8:2,转速为50r/min,球磨12h后,用400#筛网过滤研磨后的浆料,获得悬浊液。
[0122]
实施例11
[0123]
金刚石颗粒表面的包覆处理
[0124]
将实施例1获得的表面处理过的金刚石颗粒,浸渍在步骤3制备的悬浊液中,浸渍2分钟后用不锈钢筛网将金刚石颗粒从包覆剂中捞出,浸渍后金刚石颗粒在筛网上沥干2h,将沥干的金刚石颗粒平摊在表面垫有bn的耐热钢板上,然后将金刚石颗粒连同钢板一起放入烘箱中,在180℃保温1小时,自然冷却,完成金刚石颗粒的表面包覆处理。
[0125]
实施例12
[0126]
金刚石包覆颗粒的热处理
[0127]
将实施例4获得的金刚石包覆颗粒连同耐热钢板一起放入电热丝加热的真空炉中,先以5℃/min的速度升温至750℃,到温后抽真空,真空度控制在10pa,保温20min后,关炉,随炉冷却,完成金刚石包覆颗粒的热处理。
[0128]
实施例13
[0129]
氢氧化铁溶胶的配置
[0130]
在800r/min的搅拌条件下向浓度为0.1mol/l的fecl3溶液中滴加浓度为0.1mol/l的乙酸钠水溶液,乙酸钠溶液的加入量为fecl3溶液质量的10%,乙酸钠溶液滴加完成后再搅拌30min,获得稳定的氢氧化铁溶胶。
[0131]
实施例14
[0132]
金刚石包覆颗粒的氧化处理
[0133]
将金刚石包覆颗粒浸渍在步骤6制备的氢氧化铁溶胶中,浸渍2分钟后用不锈钢筛网将金刚石包覆颗粒从氢氧化铁溶胶中捞出,浸渍后金刚石颗粒在筛网上沥干2h,再将沥干的金刚石包覆颗粒平摊在表面垫有bn的陶瓷板上,放入马弗炉中,在空气气氛下,以4℃/min的速率升温至800℃保温2h后随炉冷却,完成金刚石包覆颗粒的氧化处理。再将氧化处理后的金刚石包覆颗粒浸泡于过量的10wt%的hf溶液中2h后捞出,用去离子水冲洗至中性,再120℃烘箱中烘干后,获得表面腐蚀处理的金刚石颗粒。
[0134]
用本发明实施例8-14制备得到的的金刚石颗粒制备的树脂金刚石磨盘在对碳化硅密封环表面进行平面磨削时,与相同粒度的传统金刚石制备的磨盘相比,由于金刚石颗粒呈现为表面多孔结构,金刚石颗粒与sic相接触磨削时,多孔金刚石颗粒更容易破碎,自锐性更好,磨削效率更高。采用用本发明提供的方法制备得到的粒度为70/80的金刚石颗粒制备的树脂金刚石磨盘对8英寸sic密封环进行磨削加工时,磨削加工量可达到1.0mm/分钟,而传统粒度为70/80的单晶金刚石颗粒制备的树脂金刚石磨盘对8英寸sic密封环进行
加工时,其磨削加工量为0.6mm/分钟,其磨削效率能提高约50%。同时多孔金刚石磨削刃数量增多,使得单个刃口的磨削深度减小,工件表面单位面积上加工的刻痕数目增加,深度降低。其加工的碳化硅的表面的磨削纹路更加细腻,磨削质量更好。
[0135]
尽管上面已经示出和描述了本发明的实施例,可以理解的是,上述实施例是示例性的,不能理解为对本发明的限制,本领域的普通技术人员在本发明的范围内可以对上述实施例进行变化、修改、替换和变型。