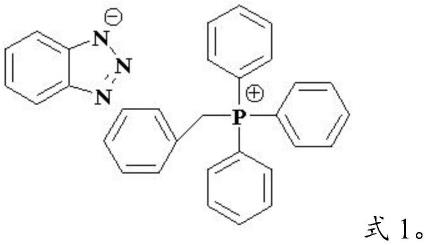
1.本发明涉及酸化缓蚀技术领域,尤其涉及一种耐高温酸化缓蚀剂及其应用。
背景技术:2.在石油勘探开发过程中,随着采矿业的渗入,采矿环境越来越复杂,井底温度随之升高,采矿效率越来越低。石油和天然气井的酸化可以显著提高尤其回收率,是油气田增产的重要措施之一,在石油工业得到了广泛的应用。但酸化过程伴随着碳酸盐的溶解,必然会造成设备及井下油管、套管的严重腐蚀,为减轻酸液腐蚀,较为有效的措施是向酸化液中添加酸性缓蚀剂。
3.随着油气井开发步入中后期,井深不断增大,对油气井酸化作业中使用的缓蚀剂提出了更高的性能要求。目前市面上的酸化缓蚀剂面对高温时(》160℃)时存在易结焦、吸附减弱等缺点,从而使得缓蚀效果不佳。因此,研制一种配方简单、合成条件温和且能满足目前油气井高温(》160℃)酸化作业苛刻要求的新型高温酸化缓蚀剂显得尤为必要。近几年来,关于油井酸化缓蚀剂研究虽然较多,但适用于高温的酸化缓蚀剂品种却很少,且性能不够稳定。部分高温酸化缓蚀剂在高温下存在易焦结、分层、溶解分散性不好,不够稳定的缺点可能会对地层造成进一步的伤害。因此,研制耐高温、效果良好的油井酸化缓蚀剂是油气田酸化增产措施的急需,对于提高酸化效果,减轻设备和管线的腐蚀、增加综合经济效益有重要意义。
技术实现要素:4.本发明的目的在于提供一种耐高温酸化缓蚀剂及其应用,所述耐高温酸化缓蚀剂在高温下稳定性好,同时能够有效提高酸化效果。
5.为了实现上述发明目的,本发明提供以下技术方案:
6.本发明提供了一种耐高温酸化缓蚀剂,包括三苯基苄基溴化膦交换物、增效剂、金属碘化物和溶剂;
7.所述三苯基苄基溴化膦交换物、增效剂、金属碘化物和溶剂的质量比为(0.5~1.0):(1.0~3.5):(0.5~2.0):(3.0~5.0);
8.所述三苯基苄基溴化膦交换物具有式1所示结构:
[0009][0010]
优选的,所述三苯基苄基溴化膦交换物的制备方法,包括以下步骤:
[0011]
将苯骈三氮唑、氢氧化钠水溶液和三苯基苄基溴化膦混合,进行离子交换,得到所述三苯基苄基溴化膦交换物。
[0012]
优选的,所述苯骈三氮唑、氢氧化钠水溶液中的氢氧化钠和三苯基苄基溴化膦的摩尔比为1:1:1。
[0013]
优选的,所述离子交换的温度为60~80℃,时间为24h。
[0014]
优选的,所述增效剂为炔醇类化合物。
[0015]
优选的,所述炔醇类化合物包括炔丙醇。
[0016]
优选的,所述金属碘化物包括碘化亚铜。
[0017]
优选的,所述溶剂包括正丁醇和/或无水乙醇。
[0018]
本发明还提供了上述技术方案所述耐高温酸化缓蚀剂在高温酸液体系中的应用,所述高温酸液体系的温度≤180℃。
[0019]
优选的,所述耐高温酸化缓蚀剂在高温酸液体系中的质量浓度为5.0~15%。
[0020]
本发明提供了一种耐高温酸化缓蚀剂,包括三苯基苄基溴化膦交换物、增效剂、金属碘化物和溶剂;
[0021]
所述三苯基苄基溴化膦交换物、增效剂、金属碘化物和溶剂的质量比为(0.5~1.0):(1.0~3.5):(0.5~2.0):(3.0~5.0);
[0022]
所述三苯基苄基溴化膦交换物具有式1所示结构:
[0023][0024]
本发明所述耐高温酸化缓蚀剂中的三苯基苄基溴化膦交换物可以通过分子中的多个氮原子在金属表面形成多点吸附,增强了所述耐高温酸化缓蚀剂在金属表面的成膜能力,降低了所述耐高温酸化缓蚀剂在高温下从金属表面的脱附速度,从而使缓释效率得到明显提高;同时所述耐高温酸化缓蚀剂在酸液中具有很好的溶解性,所以能够均一、稳定的分散在酸液中,无沉淀和分层现象出现;原料易得。
具体实施方式
[0025]
本发明提供了一种耐高温酸化缓蚀剂,包括三苯基苄基溴化膦交换物、增效剂、金属碘化物和溶剂;
[0026]
所述三苯基苄基溴化膦交换物、增效剂、金属碘化物和溶剂的质量比为(0.5~1.0):(1.0~3.5):(0.5~2.0):(3.0~5.0);
[0027]
所述三苯基苄基溴化膦交换物具有式1所示结构:
[0028][0029]
在本发明中,所述三苯基苄基溴化膦交换物的制备方法优选包括以下步骤:
[0030]
将苯骈三氮唑、氢氧化钠水溶液和三苯基苄基溴化膦混合,进行离子交换,得到所述三苯基苄基溴化膦交换物。
[0031]
在本发明中,所述氢氧化钠水溶液的质量百分数优选为30%~50%,更优选为35%~45%,最优选为40%。
[0032]
在本发明中,所述苯骈三氮唑、氢氧化钠水溶液中的氢氧化钠和三苯基苄基溴化膦的摩尔比优选为1:1:1。
[0033]
在本发明中,所述混合优选为将苯骈三氮唑和氢氧化钠水溶液混合,反应12h后,与三苯基苄基溴化膦混合。
[0034]
在本发明中,所述离子交换的温度优选为60~80℃,更优选为65~75℃,最优选为70℃;时间优选为24h。
[0035]
所述离子交换完成后,本发明还优选包括依次进行的萃取、干燥、过滤和蒸馏;所述萃取优选为采用二氯甲烷萃取3次;所述干燥采用的干燥剂优选为无水硫酸钠;本发明对所述过滤的过程没有任何特殊的限定,采用本领域技术人员熟知的过程保证能够过滤掉干燥剂即可。本发明对所述蒸馏的条件没有任何特殊的限定,采用本领域技术人员熟知的条件能够去除溶剂即可。
[0036]
在本发明中,所述增效剂优选为炔醇类化合物,更优选为炔丙醇。在本发明中,所述增效剂的作用是利用π电子吸附在所述三苯基苄基溴化膦交换物之间的缝隙中,形成完整致密的吸附膜,起到良好的缓蚀效果。
[0037]
在本发明中,所述金属碘化物优选包括碘化亚铜。在本发明中,所述金属碘化物的作用主要是通过与铁原子的特性吸附作用与金属表面配位,提高缓蚀主剂特别是阳离子型缓蚀剂的吸附能力。
[0038]
在本发明中,所述溶剂优选包括正丁醇和/或无水乙醇;当所述溶剂为正丁醇和无水乙醇时,本发明对所述正丁醇和无水乙醇的配比没有任何特殊的限定,按任意配比进行混合即可。
[0039]
在本发明中,所述三苯基苄基溴化膦交换物、增效剂、金属碘化物和溶剂的质量比优选为(0.5~1.0):(1.0~3.5):(0.5~2.0):(3.0~5.0),更优选为(0.6~0.8):(1.5~3.0):(1.0~1.5):(3.5~4.0)。
[0040]
在本发明中,所述耐高温缓蚀剂的制备方法优选包括以下步骤:
[0041]
将三苯基苄基溴化膦交换物、增效剂、金属碘化物和溶剂混合,得到所述耐高温缓蚀剂。
[0042]
在本发明中,所述混合优选在超声的条件下进行,所述超声的温度优选为25℃,时
间优选为30min。本发明对所述超声的频率没有任何特殊的限定,采用本领域技术人员熟知的频率即可。
[0043]
本发明还提供了上述技术方案所述耐高温酸化缓蚀剂在高温酸液体系中的应用。
[0044]
在本发明中,所述耐高温酸化缓蚀剂在高温酸液体系中的质量浓度优选为5.0~15%,更优选为6.0~12.0%,最优选为8.0~10.0%。
[0045]
下面结合实施例对本发明提供的耐高温酸化缓蚀剂及其应用进行详细的说明,但是不能把它们理解为对本发明保护范围的限定。
[0046]
实施例1
[0047]
将0.1mol苯骈三氮唑和7ml质量浓度为40%的氢氧化钠溶液(氢氧化钠的摩尔量为0.1mol)混合,反应12h后,与0.1mol三苯基苄基溴化膦混合,进行离子交换反应24h,用二氯甲烷萃取三次,有机相用无水硫酸钠干燥过夜,过滤去掉干燥剂后,蒸馏除掉溶剂,得到三苯基苄基溴化膦交换物(缓蚀剂主剂);
[0048]
按照0.5:3.0:0.5:3.0的质量比,将所述三苯基苄基溴化膦交换物、炔丙醇、碘化亚铜和无水乙醇置于3ml的离心管中后,在超声波清洗器中25℃,反应30min,得到所述耐高温酸化缓蚀剂,记为a。
[0049]
实施例2
[0050]
参考实施例1,区别在于所述三苯基苄基溴化膦交换物、炔丙醇、碘化亚铜和无水乙醇的质量比为1.0:2.0:1.0:3.0,得到的耐高温酸化缓蚀剂,记为b。
[0051]
实施例3
[0052]
参考实施例1,区别在于所述三苯基苄基溴化膦交换物、炔丙醇、碘化亚铜和无水乙醇的质量比为1.0:1.0:2.0:3.0,得到的耐高温酸化缓蚀剂,记为c。
[0053]
实施例4
[0054]
参考实施例1,区别在于所述三苯基苄基溴化膦交换物、炔丙醇、碘化亚铜和无水乙醇的质量比为1.0:1.5:1.5:3.0,得到的耐高温酸化缓蚀剂,记为d。
[0055]
实施例5
[0056]
参考实施例1,区别在于所述三苯基苄基溴化膦交换物、炔丙醇、碘化亚铜和无水乙醇的质量比为1.0:3.0:0.5:3.0,得到的耐高温酸化缓蚀剂,记为e。
[0057]
实施例6
[0058]
参考实施例1,区别在于所述三苯基苄基溴化膦交换物、炔丙醇、碘化亚铜和无水乙醇的质量比为1.0:3.0:1.0:3.0,得到的耐高温酸化缓蚀剂,记为f。
[0059]
实施例7
[0060]
参考实施例1,区别在于所述三苯基苄基溴化膦交换物、炔丙醇、碘化亚铜和无水乙醇的质量比为1.0:3.5:0.5:3.0,得到的耐高温酸化缓蚀剂,记为g。
[0061]
实施例8
[0062]
参考实施例1,区别在于所述三苯基苄基溴化膦交换物、炔丙醇、碘化亚铜和无水乙醇的质量比为1.0:2.5:1.5:3.0,得到的耐高温酸化缓蚀剂,记为h。
[0063]
测试例
[0064]
对实施例1~8所述耐高温酸化缓蚀剂进行复试速率实验。
[0065]
按照行业标准sy/t 5405-1996《酸化用缓蚀剂性能试验方法及评价指标》进行动
态实验。将钢片用金相砂纸打磨抛光,依次用蒸馏水、无水乙醇、丙酮脱脂去油,用滤纸吸干放在烘箱中干燥2h。用分析天平准确称量其质量。钢片垂直悬挂在高温高压动态腐蚀测定仪中,浸入实验介质。实验后将挂片取出,再用蒸馏水、无水乙醇、丙酮洗净去油,干燥2h后称重。评价实验条件为:
[0066]
工作温度为:180℃,试验压力为16.0mpa,搅拌速度为60r/min,反应时间4h。采用的腐蚀介质为:12wt%浓盐酸+3wt%氢氟酸;采用钢为n80;缓蚀剂用量为5.0~15.0%。对上述8种配方缓蚀剂的腐蚀速率进行了测定。
[0067]
腐蚀速率的计算:
[0068][0069]
其中,vi‑‑‑‑‑‑
单片腐蚀速率,g/(m2·
h);
[0070]
δmi‑‑‑‑‑‑
试片的腐蚀质量,g;
[0071]ai
‑‑‑‑‑
试片表面积,mm2;
[0072]
δt
‑‑‑‑‑‑
反应时间,h。
[0073]
测试结果如表1所示:
[0074]
表1实施例1~8所述耐高温酸化缓蚀剂的缓蚀性能参数
[0075][0076]
由表1可知,以上实施例表明,制备的高温酸化缓蚀剂在特定条件下具有非常优异的缓蚀性能,腐蚀速率远超标准sy/t 5405-1996一级品要求。
[0077]
以上所述仅是本发明的优选实施方式,应当指出,对于本技术领域的普通技术人员来说,在不脱离本发明原理的前提下,还可以做出若干改进和润饰,这些改进和润饰也应视为本发明的保护范围。