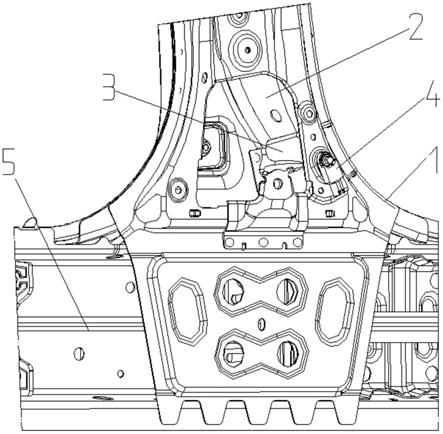
1.本实用新型涉及一种车辆配件技术领域,尤其是涉及一种提高侧碰传感器安装精度的车身结构 。
背景技术:2.侧碰传感器是车辆安全配置中不可或缺的传感器原件,其通过检测受到碰撞引起的加速度变化从而判断是否点爆安全气囊;侧碰传感器安装孔会通过加强板进行加强,安装孔双层板开过孔,由于侧碰传感器的贴合面较小,导致安装过孔较小,制造过程中导致错孔,无法安装,需要铣孔进行安装,一方面压合面破坏,影响侧碰传感器的灵敏性,另一方面需要大量的返工,影响生产效率。
3.例如,一种在中国专利文献上公开的“一种安装螺母板及侧碰传感器装配结构”,其公告号cn209671338u,包括安装顶板以及由所述安装顶板延伸向下形成的第一支腿部、第二支腿部和第三支腿部,所述第一支腿部与所述第二支腿部相对设置,所述安装顶板上设有安装孔。侧碰传感器安装在侧碰传感器安装螺母板上,b柱内板开安装过孔,由于侧碰传感器的贴合面较小,为保证有效焊接,安装过孔孔径较小,制造过程中导致错孔,无法安装,需要铣孔进行安装;返工后安装过孔破坏导致侧碰传感器安装压合面破坏,影响侧碰传感器的灵敏性,另一方面需要大量的返工,影响生产效率。
技术实现要素:4.本实用新型是为了克服现有技术的安装过孔孔径较小,制造过程中导致错孔,无法安装,需要铣孔进行安装;返工后安装过孔破坏导致侧碰传感器安装压合面破坏,影响侧碰传感器的灵敏性及影响生产效率的问题,提供一种提高侧碰传感器安装精度的车身结构,避免错孔的现象出现,降低制造难度,提高生产效率。
5.本实用新型还为了克服现有技术的侧碰传感器安装螺母板与b柱内板通过侧碰传感器安装螺栓进行连接,螺母板与b柱内板间存在间隙,力矩较小无法消除安装点处的间隙,导致侧碰传感器刚度实测值与理论计算值差别较大,影响侧碰传感器后续的信息采集的准确性的问题,提供一种提高侧碰传感器安装精度的车身结构,b柱内板与侧碰传感器加强板通过塞焊连接,消除间隙,保证后续侧碰传感器的信息采集的准确性。
6.为了实现上述目的,本实用新型采用以下技术方案:
7.一种提高侧碰传感器安装精度的车身结构,包括b柱内板、b柱加强板及侧碰传感器,所述b柱内板上设有安装孔,所述安装孔朝向b柱加强板一侧设有连接块,所述侧碰传感器设置在b柱内板远离b柱加强板一侧且侧碰传感器与连接块固定连接,所述b柱加强板上设有侧碰传感器加强板,所述侧碰传感器加强板上设有安装连接块的过孔,所述过孔孔径大于连接块的最大直径,所述侧碰传感器加强板与b柱内板固定连接。
8.b柱加强板位于b柱内板的内侧,侧碰传感器设置在b柱内板的外侧且侧碰传感器通过安装孔与位于b柱内板靠近b柱加强板一侧的连接块固定连接,起到固定侧碰传感器的
作用,侧碰传感器加强板与b柱内板固定连接,起到进一步固定侧碰传感器的作用;相比于传统b柱加强板的过孔,本实用新型通过在b柱加强板上设置侧碰传感器加强板,侧碰传感器加强板上开设有孔径大于连接块的过孔,既降低了制造难度,又避免了过孔孔径过小造成错孔的情况;采用侧碰传感器加强板与b柱内板固定连接,进一步加强b柱内板的稳定性,从而起到进一步固定侧碰传感器的作用;过孔孔径大于连接块的最大直径,起到避让作用,使得侧碰传感器加强板能够与b柱内板贴合。
9.作为优选,所述侧碰传感器加强板的横截面呈l形,所述侧碰传感器加强板的两端与b柱加强板固定连接。呈l形的侧碰传感器加强板两端固定在b柱加强板上,一端与b柱加强板的边缘固定连接,另一端与b柱加强板的内凹部分连接,立体结构使得侧碰传感器加强板有足够的支撑力,提高侧碰传感器加强板的强度,能够更好的支撑b柱内板,从而固定侧碰传感器。
10.作为优选,所述侧碰传感器加强板上过孔的两侧设有与b柱内板焊接的塞焊孔。塞焊孔用于侧碰传感器加强板与b柱内板的塞焊,增强b柱内板与侧碰传感器加强板的连接,消除两者之间的间隙,保证后续侧碰传感器的信息采集的准确性。
11.作为优选,所述侧碰传感器设置在传感器安装支架上,所述传感器安装支架上设有用于安装螺栓的通孔。
12.作为优选,所述连接块为凸焊螺母。侧碰传感器通过螺栓与凸焊螺母的连接固定在b柱内板上,采用螺纹连接便捷、高效、可拆卸。
13.作为优选,所述传感器安装支架上还设有用于与b柱内板连接的卡扣,所述b柱内板上设有与所述卡扣对应的连接孔。传感器安装支架上的卡扣与b柱内板上的连接孔扣接,确定了传感器安装支架的固定位置与固定方向,通过安装孔及连接孔两个固定点,保证了传感器安装支架安装的一致性;通过卡扣与连接孔的扣接实现初步安装,便于下一步固定安装的进行;在螺栓脱落的情况下防止传感器安装支架掉落。
14.作为优选,所述b柱内板上设有凸台,所述安装孔及连接孔设置在所述凸台上。凸台增加了侧碰传感器安装点刚度和安装孔、安装面的精度。
15.因此,本实用新型具有如下有益效果:(1)通过增设侧碰传感器加强板,侧碰传感器加强板与b柱内板固定连接,加强b柱内板的强度,从而进一步的固定侧碰传感器,侧碰传感器固通过螺栓与凸焊螺母的连接固定在b柱内板上,侧碰传感器加强板开较大的过孔,避免了错孔现象的出现,降低了制造难度,提高了生产效率;(2)b柱内板与侧碰传感器加强板通过塞焊固定连接,消除间隙,保证后续侧碰传感器的信息采集的准确性。
附图说明
16.图1是本实用新型的一种结构示意图;
17.图2是本实用新型爆炸图的一种结构示意图;
18.图3是本实用新型b柱加强板的一种结构示意图;
19.图4是本实用新型b柱内板的一种结构示意图;
20.图5是本实用新型侧碰传感器的一种结构示意图。
21.图中:1、b柱内板
ꢀꢀ1‑
1、凸台
ꢀꢀ1‑
2、安装孔
ꢀꢀ1‑
3、凸焊螺母
ꢀꢀ1‑
4、连接孔
ꢀꢀ
2、b柱加强板
ꢀꢀ
3、侧碰传感器加强板
ꢀꢀ3‑
1、过孔
ꢀꢀ3‑
2、塞焊孔
ꢀꢀ
4、侧碰传感器
ꢀꢀ
5、外门槛加强
板
ꢀꢀ
6、传感器安装支架
ꢀꢀ6‑
1、通孔
ꢀꢀ6‑
2、螺栓
ꢀꢀ6‑
3、卡扣。
具体实施方式
22.下面结合附图与具体实施方式对本实用新型做进一步的描述。
23.在图1、图2、图3及图4所示的实施例中,本实用新型的一种提高侧碰传感器安装精度的车身结构 ,包括b柱内板1、b柱加强板2、侧碰传感器4及外门槛加强板5,所述b柱内板上设有安装孔1
‑
2,所述安装孔朝向b柱加强板一侧设有连接块,所述连接块为凸焊螺母1
‑
3,所述侧碰传感器设置在b柱内板远离b柱加强板一侧且侧碰传感器与连接块固定连接,所述b柱加强板上设有侧碰传感器加强板3,所述侧碰传感器加强板上设有安装连接块的过孔3
‑
1,所述过孔孔径大于连接块的最大直径,所述侧碰传感器加强板与b柱内板固定连接。
24.b柱加强板位于b柱内板的内侧,侧碰传感器设置在b柱内板的外侧即b柱内板远离b柱加强板的一侧,且侧碰传感器通过安装孔与位于b柱内板靠近b柱加强板一侧的凸焊螺母固定连接,起到固定侧碰传感器的作用,凸焊螺母通过凸焊固定在b柱内板上,侧碰传感器加强板与b柱内板通过塞焊固定连接,起到进一步固定侧碰传感器的作用;相比于传统b柱加强板的过孔,本实用新型通过在b柱加强板上设置侧碰传感器加强板,侧碰传感器加强板上开设有孔径大于连接块的过孔,既降低了制造难度,又避免了过孔孔径过小造成错孔的情况;采用侧碰传感器加强板与b柱内板焊接,进一步加强b柱内板的稳定性,从而起到进一步固定侧碰传感器的作用;过孔孔径大于连接块的最大直径,起到避让作用,使得侧碰传感器加强板能够与b柱内板贴合,消除侧碰传感器加强板与b柱内板之间的间隙。
25.如图3所示,所述侧碰传感器加强板的横截面呈l形,所述侧碰传感器加强板的两端与b柱加强板固定连接。b柱加强板呈凹字形,侧碰传感器加强板的一端与b柱加强板的边缘固定连接,另一端与b柱加强板的内凹部分连接,构成凸起的支撑结构,立体的支撑结构使得侧碰传感器加强板有足够的支撑力,提高侧碰传感器加强板的强度,能够更好的支撑b柱内板,从而固定侧碰传感器。
26.如图3所示,所述侧碰传感器加强板上过孔的两侧设有与b柱内板焊接的塞焊孔3
‑
2。过孔的两侧各设有一个塞焊孔,通过塞焊孔对侧碰传感器加强板及b柱内板进行塞焊,消除两块板之间的间隙,保证后续侧碰传感器的信息采集的准确性。
27.如图4及图5所示,所述侧碰传感器固定设置在传感器安装支架6上,所述传感器安装支架上设有用于安装螺栓6
‑
2的通孔6
‑
1。传感器安装支架通过螺栓与凸焊螺母的螺纹连接,固定在b柱内板上。所述传感器安装支架上还设有用于与b柱内板连接的卡扣6
‑
3,所述b柱内板上设有与所述卡扣对应的连接孔1
‑
4。所述卡扣为由四片弹性片围成的腰圆形结构,所述连接孔呈腰圆形,腰圆形有效防止传感器安装支架转动。
28.如图4所示,所述b柱内板上设有凸台1
‑
1,所述安装孔及连接孔设置在所述凸台上。侧碰传感器安装处的b柱内板向外凸起即向远离b柱加强板的一侧凸起形成凸台,凸台增加了侧碰传感器安装点刚度和安装孔、安装面的精度。
29.将l形的侧碰传感器加强啊板的两端焊接在b柱加强板上,再将外门槛加强板与b柱加强板焊接,b柱内板与b柱加强板及外门槛加强板焊接固定,此时,焊接螺母位于侧碰传感器加强板的过孔内,将侧碰传感器通过螺栓与b柱内板固定连接,侧碰传感器加强板与b柱内板通过塞焊固定连接消除两者之间的间隙。