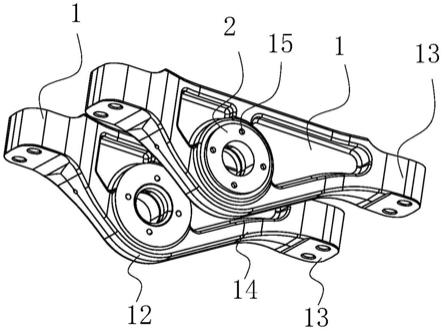
1.本实用新型涉及汽车零部件领域,尤其涉及一种轻量化铝合金油缸支座。
背景技术:2.节能减排的压力加速了汽车轻量化的进程,汽车零部件以铝合金等轻量化材料代替传统的钢铁材料,可实现减重30~50%,整车降低油耗7~13%、减少排放4~6%,成为汽车零部件设计更新换代的必然选择。对于在高油价时代的卡车用户,如果车辆自重降低0.8吨可以多装货物0.8吨,按照每年行驶20万公里、每公里平均运价0.28元计算,一辆轻量化重卡一年可比载重量相同的普通车型增加收入5~6万元。实现轻量化的方法包含优化车辆设计结构及应用轻量化新材料。
3.油缸支座是用于连接油缸和卡车车架的构件,油缸支座一般成对设置在车架上,分别与油缸的耳轴的两端装配。现有技术中的油缸支座基本上采用铸铁件,每个油缸支座的质量约为5kg,对于车辆的底盘的自重有较大影响。另外,油缸顶升翻转车架时,需要油缸的耳轴能相对油缸支座自由转动,且油缸支座是主要的受力机构,承受高载荷。因此,需要提供一种满足高载荷的强度要求、与耳轴的配合位置耐磨性较好、轻量化的油缸支座。
技术实现要素:4.本实用新型所要解决的技术问题是针对现有技术的现状提供一种满足高载荷的强度要求的情况下,与耳轴的配合位置耐磨性较好、具有良好的防滑脱性能、轻量化的铝合金油缸支座。
5.本实用新型解决上述技术问题所采用的技术方案为:该种铝合金油缸支座,包括铝合金材质的支座主体、支座主体上设置有用于与油缸耳轴配合的安装孔,在安装孔内过盈配合有钢材质的衬套,衬套的一端沿径向向外成型有翻边,翻边用于与支座主体固定。
6.支座主体整体呈板状,支座主体包括位于中部呈峰状凸起的衬套安装部,以及向两侧延伸的车架固定部,衬套安装部的厚度小于车架固定部的厚度,自衬套安装部朝车架固定部的过渡位置厚度逐渐增加。
7.为了具有更好的固定效果,支座主体上设有第一固定孔、翻边上设有对应的第二固定孔,第一固定孔与第二固定孔之间通过螺栓组件固定连接。
8.为了防止固定孔外缘位置的应力集中而破坏,第一固定孔沿周向间隔均匀排列有多个,每个第一固定孔的中心点离安装孔外缘的径向距离l1不小于7mm。
9.优选的,径向距离l1为7
‑
15mm。
10.增大衬套外径,从而增大衬套与支座主体的接触面积,有利于分散应力的集中,降低应力,衬套的外直径d1为不小于48mm,且衬套沿径向的壁厚s1不小于4mm。
11.优选的,衬套的外直径d1为49
‑
55mm,且衬套沿径向的壁厚s1为4
‑
8mm。
12.为了同时满足防滑脱摩擦力要求和过盈装配强度要求优选的,衬套与安装孔的过盈量为0.02mm
‑
0.05mm。
13.为了进一步减重的同时对应力集中的径向方向进一步加强,在支座主体的每个板面上均设有第一减重槽、第二减重槽,第一减重槽、第二减重槽分别位于安装孔的两侧,从而在第一减重槽与第二减重槽之间形成加强筋,加强筋沿安装孔的径向方向延伸。
14.优选的,支座主体选用a356铝合金材质,衬套选用45
‑
gb/t699钢材质。选用a356 铝合金材质能兼具良好的减重效果和强度,选用45
‑
gb/t699钢材质价格低廉且具有良好的耐磨性。
15.与现有技术相比,本实用新型的优点在于:
16.1.采用铝合金材质的支座主体,能够大幅度减重,减重率能达到40%以上,强度性能达到要求,疲劳次数超过现有技术的铸铁件;
17.2.与钢材质的衬套配合使用,衬套用于与耳轴配合,从而提高该位置的耐磨性;
18.3.衬套上设置翻边用于与支座主体固定,补充过盈力不足,防滑脱力不足的问题,同时分担油缸耳轴施加在支承座的力,从而降低举升工况的应力值,进一步提高该种油缸支座的使用安全性、使用寿命
19.4.支座主体对衬套安装部位置进行着重加强,从而形成峰状凸起;对车架固定部进行加厚;因为上述位置是应力集中位置,采用该种结构设计可以在保证强度的同时减重;另外,厚度逐渐变化的过渡位置也可以防止该过渡位置的应力集中,增加支座主体的强度。
附图说明
20.图1为本实用新型的实施例的油缸支座的成对设置的示意图;
21.图2为本实用新型的实施例的支座主体和衬套的分解结构示意图;
22.图3为本实用新型的实施例的支座主体的仰视图;
23.图4为本实用新型的实施例的支座主体的左视图;
24.图5为本实用新型的实施例的衬套的结构示意图;
25.图6为本实用新型的实施例的衬套的正视图;
26.图7为本实用新型的实施例的支座主体的立体结构示意图。
具体实施方式
27.下面结合附图和实施例,对本实用新型的具体实施方式作进一步详细描述。
28.如图1所示,该种油缸支座成对设置,对于双油缸的卡车就需要设置两对。
29.该种铝合金油缸支座,包括铝合金材质的支座主体1、支座主体1上设置有用于与油缸耳轴配合的安装孔11,在安装孔11内过盈配合有钢材质的衬套2,衬套2的一端沿径向向外成型有翻边21,翻边21用于与支座主体1固定。
30.支座主体1整体呈板状,支座主体1包括位于中部呈峰状凸起的衬套安装部12,以及向衬套安装部12的两端延伸的车架固定部13,衬套安装部12的厚度小于车架固定部 13的厚度,自衬套安装部12朝车架固定部13的过渡位置14厚度逐渐增加。
31.为了具有更好的固定效果,支座主体1上设有第一固定孔15、翻边21上设有对应的第二固定孔22,第一固定孔15与第二固定孔22之间通过螺栓组件固定连接。
32.为了防止固定孔外缘位置的应力集中而破坏,第一固定孔15沿周向间隔均匀排列有多个,每个第一固定孔15的中心点离安装孔11外缘的径向距离l1不小于7mm。优选的,径
向距离l1为7
‑
15mm。本实施例的径向距离l1为7.5mm,本实施例的第一固定孔设有四个。
33.增大衬套2外径,从而增大衬套2与支座主体1的接触面积,有利于分散应力的集中,降低应力,衬套2的外直径d1为不小于48mm,且衬套2沿径向的壁厚s1不小于 4mm。优选的,衬套2的外直径d1为49
‑
55mm,且衬套2沿径向的壁厚s1为4
‑
8mm。本实施例衬套2的外直径d1为49mm,且衬套2沿径向的壁厚s1为4.25mm。
34.为了同时满足防滑脱摩擦力要求和过盈装配强度要求,衬套2与安装孔11的过盈量为0.02mm
‑
0.05mm。本实施例的过盈量为0.04mm。
35.为了进一步减重的同时对应力集中的径向方向进一步加强,在支座主体1的每个板面上均设有第一减重槽16、第二减重槽17,第一减重槽16、第二减重槽17分别位于安装孔11的两侧,从而在第一减重槽16与第二减重槽17之间形成加强筋18,加强筋18 沿安装孔11的径向方向延伸。为了节约布置空间和进一步减少应力,油缸相对于车架倾斜设置,为了匹配油缸的安装位置,安装孔的位置偏向其中一端的车架固定部13设置,从而第一减重槽16的面积大于第二减重槽17,能够更好减重。
36.优选的,支座主体1选用a356铝合金材质,衬套2选用45
‑
gb/t699钢材质。选用a356铝合金材质能兼具良好的减重效果和强度,选用45
‑
gb/t699钢材质价格低廉且具有良好的耐磨性。
37.该种油缸支座的最大米泽斯应力为181mpa,满足强度要求。总质量为2.648kg,相对常规铸铁件质量5kg减重40%以上。支座主体与衬套的静摩擦力为39.6kn,过盈装配最大米泽斯应力为215mpa,满足防滑脱摩擦力要求和过盈装配强度要求。并且,本发明的油缸支座为分体设计,支座主体为铝合金材质,与油缸耳轴的配合位置设置了钢材质衬套,可以弥补铝合金耐磨性的不足,具有更好的耐磨效果。
38.本实用新型方案所公开的技术手段不仅限于上述实施方式所公开的技术手段,还包括由以上技术特征任意组合所组成的技术方案。应当指出,对于本技术领域的普通技术人员来说,在不脱离本实用新型原理的前提下,还可以做出若干改进和润饰,这些改进和润饰也视为本实用新型的保护范围。