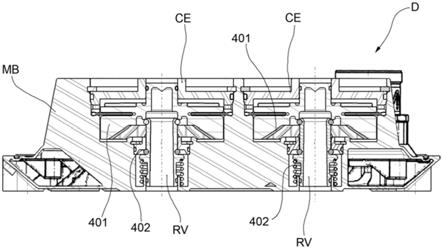
1.本发明总体上属于铁路制动系统领域;特别地,本发明涉及一种铁路制动装置和一种铁路制动装置的制造方法。
背景技术:2.应用于通用铁路车辆的已知的铁路制动系统通常由安装在称为气路板的面板上的多个气动部件组成,该面板既充当物理支撑又充当气动部件之间的气动连接接口。此外,该面板还充当气动制动系统和车辆之间的连接接口。
3.在典型的制动系统中,例如气动制动系统,使用传统技术制造,金属面板100支撑各种气动部件和电动气动部件。面板100除了用作上述气动部件的支撑法兰之外,还通过在同一面板内获得的连接通道102用作气动部件之间的气动接口。如果待支撑和待接合的部件数量有限且所述面板的尺寸有限,例如但不排他地小于500mm
×
500mm
×
30mm,则通道可通过钻孔104获得的通道交叉而形成,如图2所示。如果面板的尺寸更大或连接的数量需要多个不可能构建的交叉点,则面板100改为通过在内表面上加工的两个或多个金属层106的分层来获得通道102。然后,将金属层粘合在一起或通过如图1所示的螺钉装置108拧紧在一起。
4.不利的是,如上所描述的解决方案具有多种缺点。首先,它们需要很长的加工时间,这通常使用计算机数控机床进行。在钻头不能在加工过程中拐弯并错过交叉点或不正确地拦截其他通道的情况下,上述最简单的解决方案,即钻出可能交叉的通道104会受到可钻的最大尺寸的限制。另一方面,多层的解决方案需要多个处理步骤,从获得通道的工序开始,到通过特殊胶水和高温处理的方式使得胶水干燥而获得的粘合。如果由通道表示的等效表面积明显大于可用于粘合的剩余表面积,则存在操作压力,例如大约10巴(bar)会产生致使通道断开的作用力的风险。在这种情况下可以使用拧紧组件,但它需要围绕每个通道的密封垫圈。这个过程通常是手动的,很费力,并且在生产过程中由于垫圈安装不当而容易出现高故障率。
5.迄今为止所描述的所有解决方案的另一个共同的缺点表现为,对于构成火车的每辆车来说,面板100的最终重量(加上部件的重量)可能是从50kg到100kg。该重量导致操作员大量且持续的能量浪费,因为列车必须不断地加速和减速该质量块。
6.ep1588913中描述的解决方案呈现了一个重要的集成步骤。所述专利要求通过如图3所示的三个金属层302、304、306的方式制造高度复杂的电动气动制动系统300,三个金属层中的两个外层承载了通过在内表面机加工而获得的通道308以及穿孔的中间层,该穿孔的中间层用于使得外层的内表面上的通道互连。此外,关于上述的多层解决方案,外层是通过机械加工获得的并且集成了如图所示的气动部件的外部主体的一部分或全部。通过这种方式,实现了进一步集成、减少空间需求和减轻重量。然而,该解决方案并未解决上述的一些缺点。
技术实现要素:7.因此,本发明的一个目的是提供一种解决方案,其能够获得一种铁路制动装置,该铁路致动装置相对于已知的解决方案重量减轻、加工时间减少,并且该铁路致动装置简化了铁路制动装置中的通道构造。
8.根据本发明的一个方面,通过具有由方案1中所限定的特征的铁路制动装置的制造方法和具有由方案5中所限定的特征的制动装置来实现上述和其他目的和优点。本发明的优选实施方式在从属方案中定义,其内容旨在作为本说明书的组成部分。
附图说明
9.现在将描述根据本发明的铁路制动系统的制造方法以及铁路制动装置的一些优选实施例的功能和结构特征。参考附图,其中:
10.‑
图1示出了根据现有技术构造的制动系统的面板;
11.‑
图2示出了根据现有技术构造的制动系统的面板层的通道;
12.‑
图3示出了根据现有技术制造的制动系统;
13.‑
图4a是根据现有技术构成有三个金属层的示例性制动装置的第一视图;
14.‑
图4b示出了图4a中的示例性制动装置的第二视图;
15.‑
图5a是在使用本发明的方法构造的情况下的示例性制动装置的第一视图;
16.‑
图5b示出了图5a中的示例性制动装置的第二视图;
17.‑
图6是当以增材制造的方式构造时的铁路制动装置的示例性主体的立体图。
具体实施方式
18.在详细解释本发明的多个实施例之前,应该阐明的是,本发明的应用不限于结构细节以及以下描述中所呈现的或附图中所示出的部件的配置。本发明可以采用其他实施例并且可以在实践中以不同方式实施或实现。还应当理解的是,措辞和术语具有描述性目的并且不应被解释为限制性的。“包括”和“包含”的使用及其变体应被理解为涵盖下文所述的要素及其等效物,以及附加要素及其等效物。
19.在下文中描述了铁路制动装置的制造方法的一些实施例,该铁路制动装置包括主体mb,该主体mb被布置成至少部分地容纳至少两个不同的气动构件或电动气动构件rv 414、416,连接至少两个气动构件或电动气动构件rv、414、416。
20.不同的气动构件或电动气动构件rv、414、416可以意味着具有结构差异或功能差异的两个元件。
21.这种制造方法包括以下步骤:通过整体块的增材制造(additive manufacturing)实现铁路制动装置的主体mb,所述整体块设置有所述通道以及用于至少两个气动构件或电动气动构件rv、414、416的至少两个座600、602。
22.在本文中,“增材制造”意指在英文中也称为“additive manufacturing(增材制造)”的工序。
23.以此方式,有利地,不再需要以待组装在一起的多个层来实现主体。
24.增材制造在英语中被称为“additive manufacturing(添加剂制造)”或“3dprinting(3d打印)”。
25.铁路制动装置的制造方法还可以包括以下步骤:在铁路制动装置的主体mb的实现完成之后,将至少两个气动构件或电动气动构件rv、414、416的构成部分安置在主体中;以及以下步骤:连接到主体mb,封闭构件ce布置成保持至少两个气动构件或电动气动构件rv、414、416的构成部分在铁路制动装置中的位置。
26.例如,至少两个气动构件或电动气动构件rv、414、416的构成部分是杆和/或膜和/或o形圈和/或弹簧等。
27.封闭构件ce可以是由塑料或金属制成的简单的盖,该盖可以通过钩住/互锁的方式或通过诸如胶水、螺钉等固定装置连接于主体mb。封闭构件可以但不是必须地也通过增材制造来制造。
28.在另一方面,用于实现所述主体mb的步骤中增材制造的材料是金属类型的,和/或,用于实现所述封闭构件ce的步骤中增材制造的材料是金属类型的。
29.铁路制动装置的气动构件或电动气动构件rv、414、416中的至少一个可以是气动继动阀rv。此外,或替代地,铁路制动装置的气动构件或电动气动构件rv、414、416中的至少一个可以是减压阀414、416。
30.图6示出了当通过增材制造的方式实现时的铁路制动装置d的示例性主体mb的立体图。
31.用600、602表示座/隔室,至少两个气动构件或电动气动构件rv、414、416待放置在其中。特别地,用600示出其中将放置气动继动阀rv的座/隔室,并且在602处的座/隔室将放置减压阀414、416在其中。
32.气动构件或电动气动构件rv、414、416可具有它们各自的气动端口,它们各自的气动端口布置成将所述铁路制动装置(d)与包括相应气动端口的支撑法兰接合。在这种情况下,制造方法可以包括以下步骤:通过增材制造的方式实现铁路制动装置d的主体mb,使得所述气动构件或电动气动构件rv、414、416的气动端口布置在主体mb中,以便于从铁路制动装置d的主体mb的单个面露出。
33.优选地,在一个示例中,气动端口是用于功能接口的气动端口而不是用于诊断接口的气动端口。
34.本发明还涉及一种根据上述任一实施例构造的铁路制动装置d。
35.此外,铁路制动装置的主体mb可以包括其中的功能容积(functional volume)。例如,功能容积可以布置成在其中包含气体或液体,气动构件可以从中抽出或引入所述气体或液体。
36.铁路制动装置d的气动构件或电动气动构件可具有它们各自的气动端口,它们各自的气动端口布置成将铁路制动装置与包括相应气动端口的支撑法兰接合。气动构件或电动气动构件rv、414、416的气动端口因此可以布置在主体中,以便于从铁路制动装置的主体的单个面露出。优选地,在一个示例中,气动端口是用于功能接口的气动端口而不是用于诊断接口的气动端口。
37.参考图4a和图4b,示出了根据现有技术的构造有三个金属层的制动装置d的示例的两个视图。在这个示例中,主体是使用传统的机械加工技术实现的。
38.制动装置d包括呈继动阀rv形式的气动构件或电动气动构件。继动阀rv的运动部件由部件401、402分别形成。构成座和任何气动连接通道的所述继动阀rv的主体由层407、
408分别构成。盖403、404形成额外的穿孔通道,在图中不可见,以分别供应和清空先导室(pilot chamber)。膜409、410由两个环411、412分别支撑,这两个环分别需要o形圈以确保气动密封。
39.此外,主体由拧紧在一起的两个面板407和408组成,执行支撑面板、气动连接和其他用于电动气动功能的集成的功能。
40.简而言之,制动装置d的主体包括层/面板403、404、407和408。
41.由于两个面板407和408的连接,可以在面板407、408的未被连接通道占据的体积部分中获得功能容积。将通道彼此隔离并产生功能容积所需的两个面板407、408的气动密封由垫圈保证。
42.图4b示出了泄压阀414、416。金属块418形成两个泄压阀414、416的支撑基座。该支撑与面板407分开制成,以便于能够构造连接泄压阀414、416以及电动气动阀和压力传感器的通道。
43.在现有技术中,由于交叉的数量和复杂性,不能在面板407上直接地获得通道。因此,金属块418随后通过螺钉的方式连接于面板407,并且两个部件之间的密封由o形圈确保。
44.图5a和图5b示出了制动装置的示例的两个视图,类似于图4a和图4b的两个视图,其中主体是通过本发明的方法制造的。
45.如图5a中所见,制动装置的主体,即图4a的层/面板403、404、407和408,通过增材制造的方式被构造在整体块中。
46.制动装置的主体mb通过增材制造构造在整体块中。主体mb还形成通向先导室的供应通道(在图中不可见),以及将继动阀rv连接到制动装置的其他部件所必需的通道。在用增材制造工艺做出的等效解决方案中去除了金属块418。实际上,安全阀414、416之间的所有互连通道c都是在单个主体mb中直接获得的。图5a还示出了到主体mb的封闭构件ce,其布置成保持至少两个气动构件在铁路制动装置d中的位置。
47.因此,本发明的方法具有以下优点:
48.‑
减少构成制动装置的部件数量;
49.‑
减少制动装置的人工组装工作量,从而减少生产时间和减少故障;
50.‑
去除任何的o形圈和垫圈,从而改进完美的气动密封,减少组装时间,减少生产故障;
51.‑
优化气动构件或电动气动构件之间的连接通道的长度,例如优化电动气动阀和继动阀的先导室之间的连接通道的长度,减少所述继动阀的实施延迟;
52.‑
气动构件或电动气动构件的主体与构成各种气动构件或电动气动构件之间连接系统的面板之间的直接集成;
53.‑
优化各种气动构件或电动气动构件之间的通道路径,例如避免通过钻孔获得的解决方案中典型的直角连接,这种直角连接导致涡流和随之而来的空气传播延迟;以及
54.‑
减少制动装置的主体的壁的厚度,这是通过机床或砂铸加工无法获得的,从而减轻整个系统的重量。
55.已经描述了根据本发明的铁路制动装置的制造方法和铁路制动装置的各个方面和实施例。应当理解的是,每个实施例可以与任何其他实施例组合。此外,本发明不限于所
描述的实施例,而是可以在所附权利要求限定的范围内变形。