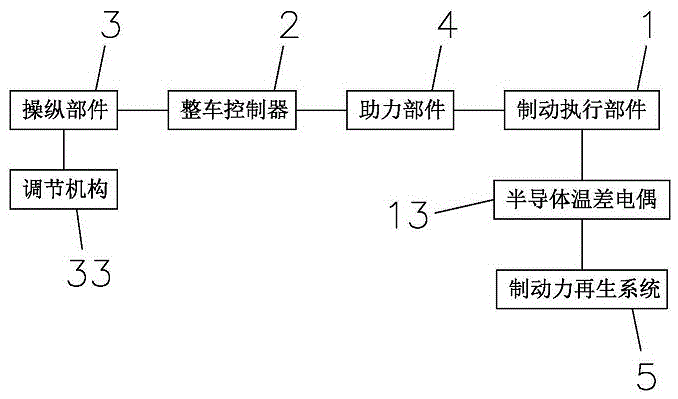
本发明属于新能源汽车
技术领域:
,具体涉及一种新能源汽车制动装置。
背景技术:
:随着社会经济的发展,汽车的保有量越来越多,导致交通事故的发生越来越频繁,调查发现,在交通事故引发因素中,汽车制动失误、故障因素所引发的交通事故占比较高,因此需要针对现有的汽车制动装置进行降低故障率的技术研发。此外,随着新能源汽车的普及,传统汽车的制动装置大多采用真空助力形式。原理就是利用进气歧管里的真空来提供助力的动力。所以在刹车助力过程中不会消耗发动机动力,但是发动机一旦停转就意味着真空助力的消失。在新能源车中,混合动力车会存在大量发动机停转的工况。纯电动车不存在发动机,所以没有可用于助力的发动机歧管真空。因此对于新能源车来说,它的制动系统是通过双回路液压制动+电动真空助力(或电子液压助力)+电机再生制动构成的。双回路液压制动与传统燃油车一致,之所以采用两套回路是为了确保当其中一根液压管漏油的情况下,不会影响另外一套回路的液压建立,主要是确保安全。与燃油车最大的区别在于助力方式和发动机制动方式。新能源车通过电机的反拖发电实现了制动力的再生,取代了燃油车的发动机制动,而助力系统则分为电动真空助力和电子液压助力两种。电动真空助力原理与传统燃油车和相当,只是把发动机进气歧管的真空换成通过电机旋转来产生真空。这种制动系统仍然保留了制动真空泵。优点是由于燃油车时代这种真空泵实现了大规模生产,所以成本很低、技术成熟可靠,制动体验与燃油车没有什么差异。但是缺点就是很难与电机反拖实现的能量回收系统无缝匹配。这就是很多人抱怨的收油后电机再生制动力太强,与刹车踏板产生的制动力完全没有配合。因此现有的新能源汽车大多采用可以与制动力再生系统实现无缝连接的电动液压助力系统,它采用了一整套电传系统,取消了传统制动系统中,制动踏板通过液压与杠杆和制动系统的刚性连接,转而变成了制动踏板仅仅只提供输入信号,所有制动液压的建立都取决于电机旋转产生的液压。简单地说就像电子油门一样,制动踏板与制动系统之间没有任何刚性的机械或液压连接,而仅仅只是通过一个刹车踏板位置传感器给电脑输入一个电信号。电脑通过这个电信号自动控制整个刹车系统的液压建立与制动力分配。也就是说,当刹车踏板输入一个电信号后,电脑可以判断驾驶者希望建立的刹车力度是多少,然后通过计算,这样的刹车力度是仅通过电机反拖就能实现,还是需要电机实现最大程度反拖然后再配合一定力度的刹车系统液压制动。通过这样的精准匹配,在一些高使用频率低使用负荷(如城市走走停停的工况中),可以大量的使用制动力再生制动来给电池充电。而在高速工况需要下,刹车的使用频率很低但每次使用的负荷很大,那么电脑可以控制优先使用电机反拖来实现制动,之后再配合液压刹车系统的介入。这样既可以最大程度的减小刹车盘片的热负荷,又可以最大程度的利用制动能量再生来回收电力、提高续航里程。并且这个过程可以非常平顺,驾驶者几乎无法察觉液压刹车时什么时候介入的。而电动液压助力系统对汽车实施制动动作时需要计算出刹车力度在电机反拖力与刹车系统液压制动力之间进行分配,并由两者分别实施制动动作。由于汽车运行工况多样,刹车制动情况复杂,因此刹车制动信号的处理也是多种多样,至今还没形成一套成熟、可靠性高的新能源汽车制动装置,制动失灵事故时有发生,特别是近期某品牌汽车刹车失灵维权事件受到人民群众的广泛关注,使新能源汽车制动的可靠性问题,成为目前新能源汽车领域的热门研究方向。技术实现要素:为了克服现有技术的不足,本发明提供一种结构简单、制动可靠的新能源汽车制动装置。本发明解决其技术问题所采用的技术方案是:一种新能源汽车制动装置,包括用于与车轮动作实施制动的制动执行部件、用于控制制动执行部件动作的整车控制器和用于为整车控制器输入制动动作信号的操纵部件,所述制动执行部件与整车控制器之间设有用于为制动执行部件提供制动助力的助力部件,所述操纵部件包括踏板机构和用于感应踏板机构动作并将踏板机构的动作信号转换为数字信号传输至整车控制器内的转换器,所述制动执行部件包括相互配合实现汽车制动的制动盘和制动器,所述制动盘和制动器上均设有若干个用于进行制动能量回收的半导体温差电偶,所述半导体温差电偶电连接制动力再生系统。作为本发明进一步的改进,所述踏板机构连接有用于调节踏板机构操纵力的调节机构,整车控制器与调节机构电信号连接,整车控制器向调节机构发送电信号来调节踏板机构操纵力的大小。作为本发明进一步的改进,所述踏板机构包括制动安装座和铰接在制动安装座的制动踏板,所述制动踏板上设有用于与调节机构连接的摆臂,所述调节机构包括连接摆臂的推杆、连接在推杆另一端的第一永磁体、第一复位弹簧和第一电磁体,所述第一复位弹簧设置在第一永磁体与第一电磁体之间使两者间隔开形成用于踩动制动踏板的操纵力反馈区间,所述第一电磁体与整车控制器电信号连接。作为本发明进一步的改进,所述助力部件包括底座、固定安装在底座上的制动液压缸、用于推动制动液压缸进行制动动作控制的主控制部件和辅助控制部件,所述主控制部件与辅助控制部件分别设置在制动液压缸的左右两侧,所述制动液压缸通过管道与制动执行部件连接。作为本发明进一步的改进,所述主控制部件包括与整车控制器电信号连接的制动电机、与制动电机输出轴传动连接的减速箱以及与减速箱输出轴传动连接的移动座,所述移动座通过滑轨安装在底座上,所述移动座与制动液压缸一侧的活塞杆连接。作为本发明进一步的改进,所述辅助控制部件包括第一液压缸和第二液压缸,所述第一液压缸与第二液压缸通过管道连接,所述第一液压缸连接制动液压缸另一侧的活塞杆,所述第一液压缸内设有第二永磁体和第二电磁体,所述第二永磁体与第二电磁体之间设有制动液,所述第二电磁体与整车控制器电信号连接,所述第一液压缸内设有用于驱动制动液回流到第二液压缸内的第二复位弹簧。作为本发明进一步的改进,所述整车控制器还连接有若干个用于采集汽车外周场景信息的视觉传感器,所述视觉传感器安装在汽车的四周。作为本发明进一步的改进,所述制动盘为三层结构,制动盘包括中间的导热层和平铺在导热层两侧的耐磨层,耐磨层与导热层之间设有y型结构的金属连接件进行连接。作为本发明进一步的改进,所述制动器包括制动片,制动片为三层结构,制动片包括中间的导热层和平铺在导热层两侧的耐磨层、防高温氧化层,耐磨层铺设在导热层面向制动盘的一侧,防高温氧化层铺设在导热层背向制动盘的一侧,耐磨层与导热层之间设有y型结构的金属连接件进行连接。本发明的有益效果是:本发明的制动装置通过在制动盘和制动器上设置半导体温差电偶来进行制动能量回收,无需采用电动液压助力系统那样的制动力分配计算原理进行制动力分配,避免了系统计算失误引发安全事故,直接通过操纵部件向整车控制器发送制动信号,整车控制器控制制动执行部件动作来刹车,大大提高了自动装置的可靠性,避免了由于制动工况复杂,系统计算错乱,制动数据不在预设范围等因素,导致的制动失灵现象发生。附图说明下面结合附图和实施方式对本发明进一步说明:图1为本实施例的连接原理图;图2为本实施例的整体结构示意图;图3为本实施例操纵部件的结构示意图;图4为本实施例制动盘的内部结构示意图;图5为本实施例制动片的内部结构示意图。具体实施方式为使本发明实施例的目的、技术方案和优点更加清楚,下面将结合本发明实施例中的附图,对本发明实施例中的技术方案进行清楚、完整地描述。实施例:如图1至图5所示,本实施例公开了一种新能源汽车制动装置,包括用于与车轮动作实施制动的制动执行部件(1)、用于控制制动执行部件(1)动作的整车控制器(2)和用于为整车控制器(2)输入制动动作信号的操纵部件(3),所述制动执行部件(1)与整车控制器(2)之间设有用于为制动执行部件(1)提供制动助力的助力部件(4),所述操纵部件(3)包括踏板机构(31)和用于感应踏板机构(31)动作并将踏板机构(31)的动作信号转换为数字信号传输至整车控制器(2)内的转换器(32),所述制动执行部件(1)包括相互配合实现汽车制动的制动盘(11)和制动器(12),所述制动盘(11)和制动器(12)上均设有若干个用于进行制动能量回收的半导体温差电偶(13),所述半导体温差电偶(13)电连接制动力再生系统(5)。由于现有的新能源汽车制动装置采用电机反拖和液压制动系统协同动作来制动车辆,两者动作和制动力的分配均需要整车控制器(2)根据踏板机构(31)传输的制动信号计算,根据该制动信号的计算结果再发送到电机反拖和液压制动系统中执行制动,但是在实际使用过程中,踏板机构(31)的制动动作是非常多样的,常见的就包括点刹、急刹和长距离制动力反复变化刹车几种。由于在刹车过程中踏板机构(31)传输的信号是连续信号,相应的处理模型也非常复杂,需要精准计算出电机反拖力和液压制动系统的制动力,并即时发送到电机和液压制动系统中进行响应。由于汽车制动的工况非常复杂,处理情况多样,导致整车控制器(2)在计算时容易出现程序错乱,出现制动失灵等现象。最直接的解决方式就是取消电机反拖制动,单独采用液压制动系统进行制动,可以起到制动响应快、结构简单、控制直接、故障率低等特点。但是直接取消电机反拖制动又会导致汽车在制动过程中机械能无法得到回收利用,车辆的续航性能大大降低。因此需要针对液压制动系统提出新的制动能量回收部件来配套。而本实施例的制动装置通过整车控制器(2)单独发送制动信号到制动执行部件(1)中实施制动动作,制动力不需要在电机和液压制动系统中进行分配,大大提高了制动装置动作的时效性和可靠性。作为优选的实施方式,在新能源汽车中,随着电子制动系统的引入,相对于传动汽车的机械制动系统,制动系统的结构得到极大的简化,无需复杂的传动结构来实施制动,因此可以大大降低制动装置的制造成本。但是电子制动系统由于是通过采集踏板机构(31)的角速度和角位移来传输制动信号的,因此就没有了机械制动系统带来的制动反馈力,驾驶体验感较为单一,无法满足不同驾驶模式下需要的不同的制动反馈力,因此本实施例采用以下实施方式来进行制动反馈力调节。所述踏板机构(31)连接有用于调节踏板机构(31)操纵力的调节机构(33),整车控制器(2)与调节机构(33)电信号连接,整车控制器(2)向调节机构(33)发送电信号来调节踏板机构(31)操纵力的大小。所述踏板机构(31)包括制动安装座(311)和铰接在制动安装座(311)的制动踏板(312),所述制动踏板(312)上设有用于与调节机构(33)连接的摆臂(313),所述调节机构(33)包括连接摆臂(313)的推杆(314)、连接在推杆(314)另一端的第一永磁体(315)、第一复位弹簧(316)和第一电磁体(317),所述第一复位弹簧(316)设置在第一永磁体(315)与第一电磁体(317)之间使两者间隔开形成用于踩动制动踏板(312)的操纵力反馈区间,所述第一电磁体(317)与整车控制器(2)电信号连接。本实施例额制动装置可以通过控制第一电磁体(317)的磁通量来调节踏板机构(31)的制动反馈力度,从而与不同驾驶模式所匹配。作为优选的实施方式,所述助力部件(4)包括底座(41)、固定安装在底座(41)上的制动液压缸(42)、用于推动制动液压缸(42)进行制动动作控制的主控制部件(43)和辅助控制部件(44),所述主控制部件(43)与辅助控制部件(44)分别设置在制动液压缸(42)的左右两侧,所述制动液压缸(42)通过管道与制动执行部件(1)连接。所述主控制部件(43)包括与整车控制器(2)电信号连接的制动电机(431)、与制动电机(431)输出轴传动连接的减速箱(432)以及与减速箱(432)输出轴传动连接的移动座(433),所述移动座(433)通过滑轨(434)安装在底座(41)上,所述移动座(433)与制动液压缸(42)一侧的活塞杆连接。所述辅助控制部件(44)包括第一液压缸(441)和第二液压缸(442),所述第一液压缸(441)与第二液压缸(442)通过管道连接,所述第一液压缸(441)连接制动液压缸(42)另一侧的活塞杆,所述第一液压缸(441)内设有第二永磁体(443)和第二电磁体(444),所述第二永磁体(443)与第二电磁体(444)之间设有制动液,所述第二电磁体(444)与整车控制器(2)电信号连接,所述第一液压缸(441)内设有用于驱动制动液回流到第二液压缸(442)内的第二复位弹簧(445)。作为优选的实施方式,所述整车控制器(2)还连接有若干个用于采集汽车外周场景信息的视觉传感器(6),所述视觉传感器(6)安装在汽车的四周。在踏板机构(31)中还设有用于采集推杆(314)动作的移动速度的速度传感器和用于采集推杆(314)动作的移动位移的位移传感器。本实施例新能源汽车制动装置的制动方式如下:驾驶员踩动制动踏板(312),制动踏板(312)将制动信号通过摆臂(313)推动推杆(314)移动,速度传感器和位移传感器通过采集推杆(314)的动作信号,传输到转换器(32)中,转换器(32)再将制动动作信号转换为数字信号,然后发送至整车控制器(2)中,整车控制器(2)再分别向制动电机(431)和第二电磁体(444)发送电信号,制动电机(431)转动通过减速箱(432)将动力传输到移动座(433),带动移动座(433)靠近制动液压缸(42)一侧移动,制动液压缸(42)的活塞杆随移动座(433)移动,将制动液压缸(42)的制动液通过管道推动制动器(12)动作;同时,第二电磁体(444)带电后,吸引第二永磁体(443)靠近第二电磁体(444)移动,第二永磁体(443)将第二液压缸(442)内的制动液推进第一液压缸(441)内,第一液压缸(441)内的液压升高,推动制动液压杆的活塞杆移动,辅助制动液压缸(42)的制动液通过管道推动制动器(12)动作,制动器(12)夹紧制动盘(11)形成制动摩擦,制动摩擦产生的热量通过半导体温差电偶(13)进行能量回收,半导体温差电偶(13)将热能转化为电能后传输至制动力再生系统(5),通过制动力再生系统(5)处理后储存至动力电池中,在整个制动过程中,制动操纵到制动执行过程是实时进行的,因此制动非常及时,可靠性高。在整个制动过程中,可以通过整车控制器(2)向第一电磁体(317)发送电信号,通过调节电信号的大小来调节第一电磁体(317)的磁性大小,从而调节踏板机构(31)的反馈力,实现不同驾驶模式的切换。由于本实施例的制动装置在制动盘(11)和制动器(12)上均设置半导体温差电偶(13)进行制动能量回收,安装后需要与制动力再生系统(5)进行连接,半导体温差电偶(13)直接嵌入制动盘(11)和制动器(12)的制动片内进行安装形成一整体,半导体温差电偶(13)嵌入安装后无法再次分离回收,而由于新能源汽车的制动装置对制动能量的回收要求较高,因此对半导体温差电偶(13)的能量回收转化率要求也相应较高,半导体温差电偶(13)的价格也较高,而制动盘(11)和制动片作为制动磨损件,使用一段时间后,磨损到一定程度就需要更换,更换时,半导体温差电偶(13)也同时成了废弃物,因此这种制动盘(11)和制动片的更换成本非常高,因此本申请人同时对制动盘(11)和制动片的制造工艺进行技术研发,研发出了一种新型制造工艺,该新型制造工艺制造的制动盘(11)和制动片具有耐磨耐高温且使用寿命长的特点。在本实施例中,所述制动盘(11)和制动片均采用三层结构设计,制动盘(11)包括中间的导热层(7)和平铺在导热层(7)两侧的耐磨层(8),而制动片包括中间的导热层(7)和平铺在导热层(7)两侧的耐磨层(8)、防高温氧化层(9),耐磨层(8)铺设在导热层(7)面向制动盘(11)的一侧,防高温氧化层(9)铺设在导热层(7)背向制动盘(11)的一侧,耐磨层(8)与导热层(7)之间设有y型结构的金属连接件进行连接,金属连接件的一端伸入耐磨层(8)内固定,另一端固定在导热层(7)内,半导体温差电偶(13)的前端固定在耐磨层(8)内,后端固定在导热层(7)内,金属连接件与半导体温差电偶(13)呈交错阵列分布。1、导热层(7)采用石墨烯导热片。2、耐磨层(8)由以下原料制成:石墨粉30~40份、mn18cr2粉末20~25份、聚醚醚酮10~12份、al2o3粉末30~40份、al2sio5粉末10~15份、sic粉末3~5份、融合剂40~50份、si3n4粉末10~15份、y2o3粉末2~4份,bao-tio2-sio2粉末5~8份;耐磨层(8)的制备工艺如下:步骤一、以导热层(7)为浇注基体,对导热层(7)的表面进行打磨,使导热层(7)的表面粗糙度在6.30≤ra≤12.5范围内;步骤二、将金属连接件和半导体温差电偶(13)以交错阵列分布的方式固定在导热层(7)上;步骤三、粉末球磨,石墨粉30~40份、mn18cr2粉末20~25份、聚醚醚酮10~12份、al2o3粉末30~40份、al2sio5粉末10~15份、sic粉末3~5份、si3n4粉末10~15份、y2o3粉末2~4份,bao-tio2-sio2粉末5~8份,使各组分的颗粒度为300~400目;步骤四、制备浇注熔体,将步骤三中球磨得到的混合粉末放入浇注容器中,加入融合剂40~50份充分搅拌均匀,采用变频分散机以1000转/分钟的转速搅拌3小时,在搅拌过程中施加振动频率为25khz的超声振动;步骤五、将步骤二得到的导热层(7)放入浇注模具内,再向浇注模具内注入步骤四得到的浇注熔体,加压20~30mpa,在100℃下烘干处理10小时、在1000℃下烧结处理2小时,得到耐磨层(8)毛坯件;步骤六、将步骤五得到的耐磨层(8)毛坯件进行机械加工,得到符合设计要求的耐磨层(8)结构。其中融合剂为浓度40%的羧甲基纤维素水溶液和浓度为50%的硅熔胶溶液与适量水经均匀混合制成。3、防高温氧化层(9)由以下原料制成:al2o3粉末25~30份、sic粉末20~25份、cr2o3粉末3~5份、稀土1~3份、kbf4粉末1~3份、粘结剂30~40份;步骤一、对导热层(7)的表面进行抛光处理,采用1500#以上砂纸抛光,使导热层(7)表面粗糙度达到ra≤0.05mm;步骤二、粉末球磨,将al2o3粉末25~30份、sic粉末20~25份、cr2o3粉末3~5份、稀土1~3份,kbf4粉末1~3份进行球磨1~5h,使各组分的粒度为500~600目;步骤三、制备喷涂料,在步骤二中球磨得到混合粉末中加入粘结剂30~40份,在温度为400~500℃的反应池中混合均匀,混合时间为1~1.5h;步骤四、涂料喷涂,在步骤三中得到的混合涂料在保温350~400℃环境下均匀喷涂在步骤一抛光后的导热层(7)中;步骤五、喷涂层冷却,将步骤四中得到的工件在氮气环境下冷却至室温;步骤六、涂层电解氧化,将步骤五中得到的工件放置于电解液中进行电解氧化,工件作为阳极,铝棒作为阴极,使涂层直接转化为防高温氧化层(9);步骤七、取出步骤六中得到的工件并用水清洗表面。通过上述步骤,使导热层(7)的外壁覆盖有一层防高温氧化层(9),制动片与制动盘(11)接触实施制动动作时,产生的热量通过耐磨层(8)传递到导热层(7),在此过程中,半导体温差电偶(13)在其中进行热量回收,且在制动片的背部设置防高温氧化层(9)进行制动片高温防护和热量流失防护,进一步提高制动片的使用寿命和制动能量回收效率。作为优选的实施方式,所述粘结剂的制备方法如下:将50~60份酞菁树脂聚合物,25~35份sio2,1~3份二甲苯,1~3份3-氨基丙基三乙氧基硅烷混合均匀,加热至200~400℃,保温4~6h,再升温至400~500℃,保温2~4h,再升温至500~600℃,保温1~2h,自然冷却后即得复合粘结剂。作为优选的实施方式,所述步骤六中的电解液制备方法如下:将10~20g/l氢氧化钠、10~20g/l硅酸钠、20~25g/l偏铝酸钠中的任意二种按1:1的比例混合,混合试剂溶于去离子水中,充分溶解;作为优选的实施方式,所述电解液中加载高压脉冲电压,电压范围为1000~1500v,电解时间为2~5h。实施例1:本实施例制动盘(11)的制造工艺如下:步骤一、选择石墨烯导热片作为导热层(7);步骤二、以导热层(7)为浇注基体,对导热层(7)的表面进行打磨,使导热层(7)的表面粗糙度在6.30≤ra≤12.5范围内;步骤三、将金属连接件和半导体温差电偶(13)以交错阵列分布的方式固定在导热层(7)上;步骤四、粉末球磨,石墨粉30份、mn18cr2粉末20份、聚醚醚酮10份、al2o3粉末30份、al2sio5粉末10份、sic粉末3份、si3n4粉末10份、y2o3粉末2份,bao-tio2-sio2粉末5份,使各组分的颗粒度为300目;步骤五、制备浇注熔体,将步骤四中球磨得到的混合粉末放入浇注容器中,加入融合剂40份充分搅拌均匀,采用变频分散机以1000转/分钟的转速搅拌3小时,在搅拌过程中施加振动频率为25khz的超声振动;步骤六、第一面耐磨层(8)浇注,将步骤三得到的导热层(7)放入浇注模具内,再向浇注模具内注入步骤五得到的浇注熔体,加压20mpa,在100℃下烘干处理10小时、在1000℃下烧结处理2小时;步骤七、另一面耐磨层(8)浇注,将步骤六得到的工件反面放入浇注模具内,再向浇注模具内注入步骤五得到的浇注熔体,加压20mpa,在100℃下烘干处理10小时、在1000℃下烧结处理2小时,得到耐磨层(8)毛坯体;步骤八、将步骤七得到的耐磨层(8)毛坯件进行机械加工,得到符合设计要求的耐磨层(8)结构。其中融合剂为浓度40%的羧甲基纤维素水溶液和浓度为50%的硅熔胶溶液与适量水经均匀混合制成。本实施例制动片的制造工艺如下:步骤一、选择石墨烯导热片作为导热层(7);步骤二、以导热层(7)为浇注基体,对导热层(7)的表面进行打磨,使导热层(7)的表面粗糙度在6.30≤ra≤12.5范围内;步骤三、将金属连接件和半导体温差电偶(13)以交错阵列分布的方式固定在导热层(7)上;步骤四、粉末球磨,石墨粉30份、mn18cr2粉末20份、聚醚醚酮10份、al2o3粉末30份、al2sio5粉末10份、sic粉末3份、si3n4粉末10份、y2o3粉末2份,bao-tio2-sio2粉末5份,使各组分的颗粒度为300目;步骤五、制备浇注熔体,将步骤四中球磨得到的混合粉末放入浇注容器中,加入融合剂40份充分搅拌均匀,采用变频分散机以1000转/分钟的转速搅拌3小时,在搅拌过程中施加振动频率为25khz的超声振动;步骤六、第一面耐磨层(8)浇注,将步骤三得到的导热层(7)放入浇注模具内,再向浇注模具内注入步骤五得到的浇注熔体,加压20mpa,在100℃下烘干处理10小时、在1000℃下烧结处理2小时;步骤七、另一面防高温氧化层(9)制备,对导热层(7)的表面进行抛光处理,采用1500#以上砂纸抛光,使导热层(7)表面粗糙度达到ra≤0.05mm;步骤八、粉末球磨,将al2o3粉末25份、sic粉末20份、cr2o3粉末3份、稀土1份,kbf4粉末1份进行球磨1h,使各组分的粒度为500目;步骤九、制备喷涂料,在步骤八中球磨得到混合粉末中加入粘结剂30份,在温度为400℃的反应池中混合均匀,混合时间为1h;步骤十、涂料喷涂,在步骤九中得到的混合涂料在保温350℃环境下均匀喷涂在步骤七抛光后的导热层(7)中;步骤十一、喷涂层冷却,将步骤十中得到的工件在氮气环境下冷却至室温;步骤十二、涂层电解氧化,将步骤十一中得到的工件放置于电解液中进行电解氧化,工件作为阳极,铝棒作为阴极,使涂层直接转化为防高温氧化层(9);步骤十三、取出步骤十二中得到的工件并用水清洗表面,得到制动片。其中,所述粘结剂的制备方法如下:将50份酞菁树脂聚合物,25份sio2,1份二甲苯,1份3-氨基丙基三乙氧基硅烷混合均匀,加热至200℃,保温4h,再升温至400℃,保温2h,再升温至500℃,保温1h,自然冷却后即得复合粘结剂。所述步骤十二中的电解液制备方法如下:将10g/l氢氧化钠、10g/l硅酸钠、20g/l偏铝酸钠中的任意二种按1:1的比例混合,混合试剂溶于去离子水中,充分溶解;所述电解液中加载高压脉冲电压,电压范围为1000v,电解时间为2h。实施例2:本实施例制动盘(11)的制造工艺如下:步骤一、选择石墨烯导热片作为导热层(7);步骤二、以导热层(7)为浇注基体,对导热层(7)的表面进行打磨,使导热层(7)的表面粗糙度在6.30≤ra≤12.5范围内;步骤三、将金属连接件和半导体温差电偶(13)以交错阵列分布的方式固定在导热层(7)上;步骤四、石墨粉35份、mn18cr2粉末23份、聚醚醚酮11份、al2o3粉末35份、al2sio5粉末13份、sic粉末4份、si3n4粉末13份、y2o3粉末3份,bao-tio2-sio2粉末7份,使各组分的颗粒度为350目;步骤五、制备浇注熔体,将步骤四中球磨得到的混合粉末放入浇注容器中,加入融合剂45份充分搅拌均匀,采用变频分散机以1000转/分钟的转速搅拌3小时,在搅拌过程中施加振动频率为25khz的超声振动;步骤六、第一面耐磨层(8)浇注,将步骤三得到的导热层(7)放入浇注模具内,再向浇注模具内注入步骤五得到的浇注熔体,加压25mpa,在100℃下烘干处理10小时、在1000℃下烧结处理2小时;步骤七、另一面耐磨层(8)浇注,将步骤六得到的工件反面放入浇注模具内,再向浇注模具内注入步骤五得到的浇注熔体,加压30mpa,在100℃下烘干处理10小时、在1000℃下烧结处理2小时,得到耐磨层(8)毛坯体;步骤八、将步骤七得到的耐磨层(8)毛坯件进行机械加工,得到符合设计要求的耐磨层(8)结构。其中融合剂为浓度40%的羧甲基纤维素水溶液和浓度为50%的硅熔胶溶液与适量水经均匀混合制成。本实施例制动片的制造工艺如下:步骤一、选择石墨烯导热片作为导热层(7);步骤二、以导热层(7)为浇注基体,对导热层(7)的表面进行打磨,使导热层(7)的表面粗糙度在6.30≤ra≤12.5范围内;步骤三、将金属连接件和半导体温差电偶(13)以交错阵列分布的方式固定在导热层(7)上;步骤四、石墨粉35份、mn18cr2粉末13份、聚醚醚酮11份、al2o3粉末35份、al2sio5粉末13份、sic粉末4份、si3n4粉末13份、y2o3粉末3份,bao-tio2-sio2粉末7份,使各组分的颗粒度为350目;步骤五、制备浇注熔体,将步骤四中球磨得到的混合粉末放入浇注容器中,加入融合剂45份充分搅拌均匀,采用变频分散机以1000转/分钟的转速搅拌3小时,在搅拌过程中施加振动频率为25khz的超声振动;步骤六、第一面耐磨层(8)浇注,将步骤三得到的导热层(7)放入浇注模具内,再向浇注模具内注入步骤五得到的浇注熔体,加压25mpa,在100℃下烘干处理10小时、在1000℃下烧结处理2小时;步骤七、另一面防高温氧化层(9)制备,对导热层(7)的表面进行抛光处理,采用1500#以上砂纸抛光,使导热层(7)表面粗糙度达到ra≤0.05mm;步骤八、将al2o3粉末28份、sic粉末23份、cr2o3粉末4份、稀土2份,kbf4粉末2份进行球磨3h,使各组分的粒度为550目;步骤九、制备喷涂料,在步骤八中球磨得到混合粉末中加入粘结剂35份,在温度为450℃的反应池中混合均匀,混合时间为1.3h;步骤十、涂料喷涂,在步骤九中得到的混合涂料在保温375℃环境下均匀喷涂在步骤七抛光后的导热层(7)中;步骤十一、喷涂层冷却,将步骤十中得到的工件在氮气环境下冷却至室温;步骤十二、涂层电解氧化,将步骤十一中得到的工件放置于电解液中进行电解氧化,工件作为阳极,铝棒作为阴极,使涂层直接转化为防高温氧化层(9);步骤十三、取出步骤十二中得到的工件并用水清洗表面,得到制动片。其中,所述粘结剂的制备方法如下:将55份酞菁树脂聚合物,30份sio2,2份二甲苯,2份3-氨基丙基三乙氧基硅烷混合均匀,加热至300℃,保温5h,再升温至450℃,保温3h,再升温至550℃,保温1.5h,自然冷却后即得复合粘结剂。所述步骤十二中的电解液制备方法如下:将15g/l氢氧化钠、15g/l硅酸钠、23g/l偏铝酸钠中的任意二种按1:1的比例混合,混合试剂溶于去离子水中,充分溶解;所述电解液中加载高压脉冲电压,电压范围为1250v,电解时间为3.5h。实施例3:本实施例制动盘(11)的制造工艺如下:步骤一、选择石墨烯导热片作为导热层(7);步骤二、以导热层(7)为浇注基体,对导热层(7)的表面进行打磨,使导热层(7)的表面粗糙度在6.30≤ra≤12.5范围内;步骤三、将金属连接件和半导体温差电偶(13)以交错阵列分布的方式固定在导热层(7)上;步骤四、石墨粉40份、mn18cr2粉末25份、聚醚醚酮12份、al2o3粉末40份、al2sio5粉末15份、sic粉末5份、si3n4粉末15份、y2o3粉末4份,bao-tio2-sio2粉末8份,使各组分的颗粒度为400目;步骤五、制备浇注熔体,将步骤四中球磨得到的混合粉末放入浇注容器中,加入融合剂50份充分搅拌均匀,采用变频分散机以1000转/分钟的转速搅拌3小时,在搅拌过程中施加振动频率为25khz的超声振动;步骤六、第一面耐磨层(8)浇注,将步骤三得到的导热层(7)放入浇注模具内,再向浇注模具内注入步骤五得到的浇注熔体,加压30mpa,在100℃下烘干处理10小时、在1000℃下烧结处理2小时;步骤七、另一面耐磨层(8)浇注,将步骤六得到的工件反面放入浇注模具内,再向浇注模具内注入步骤五得到的浇注熔体,加压30mpa,在100℃下烘干处理10小时、在1000℃下烧结处理2小时,得到耐磨层(8)毛坯体;步骤八、将步骤七得到的耐磨层(8)毛坯件进行机械加工,得到符合设计要求的耐磨层(8)结构。其中融合剂为浓度40%的羧甲基纤维素水溶液和浓度为50%的硅熔胶溶液与适量水经均匀混合制成。本实施例制动片的制造工艺如下:步骤一、选择石墨烯导热片作为导热层(7);步骤二、以导热层(7)为浇注基体,对导热层(7)的表面进行打磨,使导热层(7)的表面粗糙度在6.30≤ra≤12.5范围内;步骤三、将金属连接件和半导体温差电偶(13)以交错阵列分布的方式固定在导热层(7)上;步骤四、石墨粉40份、mn18cr2粉末25份、聚醚醚酮12份、al2o3粉末40份、al2sio5粉末15份、sic粉末5份、si3n4粉末15份、y2o3粉末4份,bao-tio2-sio2粉末8份,使各组分的颗粒度为400目;步骤五、制备浇注熔体,将步骤四中球磨得到的混合粉末放入浇注容器中,加入融合剂50份充分搅拌均匀,采用变频分散机以1000转/分钟的转速搅拌3小时,在搅拌过程中施加振动频率为25khz的超声振动;步骤六、第一面耐磨层(8)浇注,将步骤三得到的导热层(7)放入浇注模具内,再向浇注模具内注入步骤五得到的浇注熔体,加压30mpa,在100℃下烘干处理10小时、在1000℃下烧结处理2小时;步骤七、另一面防高温氧化层(9)制备,对导热层(7)的表面进行抛光处理,采用1500#以上砂纸抛光,使导热层(7)表面粗糙度达到ra≤0.05mm;步骤八、将al2o3粉末30份、sic粉末25份、cr2o3粉末5份、稀土3份,kbf4粉末3份进行球磨5h,使各组分的粒度为600目;步骤九、制备喷涂料,在步骤八中球磨得到混合粉末中加入粘结剂40份,在温度为500℃的反应池中混合均匀,混合时间为1.5h;步骤十、涂料喷涂,在步骤九中得到的混合涂料在保温400℃环境下均匀喷涂在步骤七抛光后的导热层(7)中;步骤十一、喷涂层冷却,将步骤十中得到的工件在氮气环境下冷却至室温;步骤十二、涂层电解氧化,将步骤十一中得到的工件放置于电解液中进行电解氧化,工件作为阳极,铝棒作为阴极,使涂层直接转化为防高温氧化层(9);步骤十三、取出步骤十二中得到的工件并用水清洗表面,得到制动片。其中,所述粘结剂的制备方法如下:将60份酞菁树脂聚合物,35份sio2,3份二甲苯,3份3-氨基丙基三乙氧基硅烷混合均匀,加热至400℃,保温6h,再升温至500℃,保温4h,再升温至600℃,保温2h,自然冷却后即得复合粘结剂。所述步骤十二中的电解液制备方法如下:将20g/l氢氧化钠、20g/l硅酸钠、25g/l偏铝酸钠中的任意二种按1:1的比例混合,混合试剂溶于去离子水中,充分溶解;所述电解液中加载高压脉冲电压,电压范围为1500v,电解时间为5h。将实施例1-3得到的成套制动盘和制动片按照gb/t5763标准进行物理性能测试,结果如下表所示:为考察制动装置的摩擦性能和磨损性能,按照《saej2522》测试制动盘和制动片效能标准要求进行了台架试验,试验结果如下表所示:1、耐磨性能测试结果如下表:2、耐高温性能测试结果如下表:实施例1实施例2实施例3耐受温度(℃)6136376553、磨损试验检测结果如下表:实施例1实施例2实施例3制动盘磨损0.0010.0010.001制动片磨损0.0010.0010.001因此,通过上述试验结果可以知道,本发明研发的制动盘和制动片具有耐磨耐高温的特点,且使用时磨损非常小,从而延长制动装置的使用寿命。以上所述仅为本发明的优选实施方式,只要以基本相同手段实现本发明目的的技术方案都属于本发明的保护范围之内。当前第1页12