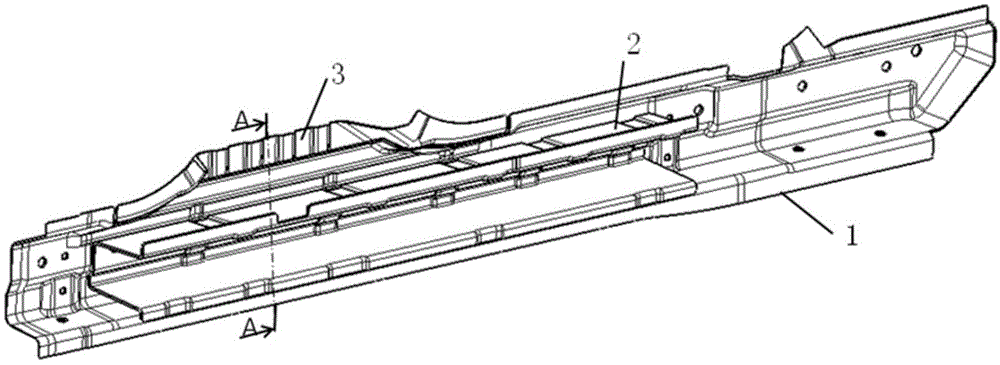
本发明属于汽车
技术领域:
,具体涉及一种汽车门槛总成结构及其成型方法。
背景技术:
:随着环保问题和能源问题越来越突出,汽车轻量化已经变得越来越重要。汽车轻量化设计可以提高车辆动力性、经济性、环保性、舒适性。整车重量下降10%,燃油经济性提高6-8%;整车每减重100kg,可降低百公里油耗0.3-0.6l,可减少co2排放量5g/km。碳纤维复合材料由于其轻质高强、耐腐蚀、抗疲劳、可设计性强等特点,已成为汽车轻量化的关键材料,所以采用碳纤维复合材料来合理设计以及如何通过合理的铺设及成型工艺来制造相应的汽车门槛总成结构,是所需解决的技术问题。技术实现要素:本发明旨在解决现有技术中存在的技术问题。为此,本发明提供一种汽车门槛总成结构及其成型方法,目的是实现门槛总成在减重的同时有更好的性能。为了实现上述目的,本发明采取的技术方案为:一种汽车门槛总成结构,包括门槛外板、分别设于门槛外板内外两侧的门槛加强梁和门槛外板加强板,所述门槛外板和门槛加强梁均采用碳纤维复合材料制成,所述门槛外板加强板采用钢板热压成型制成。所述门槛加强梁和门槛外板加强板均通过结构胶与门槛外板胶接连接。所述碳纤维复合材料采用多个碳纤维层依次堆叠后,经过热压罐成型工艺分别制成门槛外板和门槛加强梁。相邻碳纤维层中的碳纤维延伸方向呈交叉设置。本发明还提供所述汽车门槛总成结构的成型方法,包括如下步骤:步骤一、制作门槛外板及门槛加强梁所需的碳纤维层;步骤二、将多个碳纤维层分别依次堆叠形成用于成型门槛外板的第一碳纤维组和用于成型门槛加强梁的第二碳纤维组;步骤三、第一碳纤维组和第二碳纤维组分别经过热压罐成型工艺制成门槛外板及门槛加强梁;步骤四、采用钢板热压成型制成门槛外板加强板;步骤五、将门槛加强梁和门槛外板加强板通过结构胶与门槛外板胶接连接。所述步骤二中碳纤维层在工作平台上平铺,相邻碳纤维层中的碳纤维延伸方向呈交叉分布。所述第一碳纤维组包括第一上碳纤维组和第一下碳纤维组,所述第一上碳纤维组和第一下碳纤维组对称设置;所述第二碳纤维组包括第二上碳纤维组和第二下碳纤维组,所述第二上碳纤维组和第二下碳纤维组对称设置。以内部碳纤维延伸方向与工作平面相平行的碳纤维层作为基准碳纤维层,所述第一上碳纤维组包括基准碳纤维层、碳纤维延伸方向与基准碳纤维层中碳纤维延伸方向的夹角为30°~60°的碳纤维层i、碳纤维延伸方向与基准碳纤维层中碳纤维延伸方向的夹角为-30°~-60°的碳纤维层ii和碳纤维延伸方向与基准碳纤维层中碳纤维延伸方向的夹角为75°~105°的碳纤维层iii。第二上碳纤维组包括基准碳纤维层、碳纤维延伸方向与基准碳纤维层中碳纤维延伸方向的夹角为30°~60°的碳纤维层i、碳纤维延伸方向与基准碳纤维层中碳纤维延伸方向的夹角为-30°~-60°的碳纤维层ii和碳纤维延伸方向与基准碳纤维层中碳纤维延伸方向的夹角为75°~105°的碳纤维层iii。所述碳纤维层i和碳纤维层ii的数量相同。所述基准碳纤维层的数量占总碳纤维层数量的10%~60%;碳纤维层i占总碳纤维层数量的10%~60%;碳纤维层ii的数量占总碳纤维层数量的10%~60%;碳纤维层iii的数量占总碳纤维层数量的10%~60%。本发明的有益效果:本发明采用碳纤维层结构制成汽车门槛外板和门槛加强梁,具有重量轻,强度高,耐腐蚀,减振性好等优点;同时采用热压罐成型工艺,得到了更高质量和性能的碳纤维产品。本发明为采用热成型钢门槛外板加强板补强碳纤维门槛外板的混合材料门槛总成,实现总成在减重的同时有更好的性能。附图说明本说明书包括以下附图,所示内容分别是:图1是本发明汽车门槛总成结构的结构示意图;图2是图1中的a-a剖视图;图3是本发明的门槛外板的铺层分布的局部爆炸图;图4是本发明的门槛加强梁的铺层分布的局部爆炸图;图5是本发明的门槛外板和门槛加强梁的成型工艺流程图。图中标记为:1、门槛外板,2、门槛加强梁,3、门槛外板加强板,4、结构胶,5、基准碳纤维层,6、碳纤维层i,7、碳纤维层ii,8、碳纤维层iii。具体实施方式下面对照附图,通过对实施例的描述,对本发明的具体实施方式作进一步详细的说明,目的是帮助本领域的技术人员对本发明的构思、技术方案有更完整、准确和深入的理解,并有助于其实施。如图1至图4所示,一种汽车门槛总成结构,包括门槛外板1、分别设于门槛外板内外两侧的门槛加强梁2和门槛外板加强板3,门槛外板1和门槛加强梁2均采用碳纤维复合材料制成,门槛外板加强板3采用钢板热压成型制成。采用热成型钢门槛外板加强板补强碳纤维门槛外板的混合材料门槛总成,实现总成在减重的同时有更好的性能。具体实施时,碳纤维复合材料采用多个碳纤维层依次堆叠后,经过热压罐成型工艺分别制成门槛外板和门槛加强梁,具有重量轻,强度高,耐腐蚀,耐疲劳等优点。门槛加强梁和门槛外板加强板均通过结构胶与门槛外板胶接连接,保证连接的牢固性,且具有耐老化、耐疲劳和耐腐蚀的特性。上述汽车门槛总成结构的成型方法,包括如下步骤:步骤一、制作门槛外板及门槛加强梁所需的碳纤维层;步骤二、将多个碳纤维层分别依次堆叠形成用于成型门槛外板的第一碳纤维组和用于成型门槛加强梁的第二碳纤维组;步骤三、第一碳纤维组和第二碳纤维组分别经过热压罐成型工艺制成门槛外板及门槛加强梁;步骤四、采用钢板热压成型制成门槛外板加强板;步骤五、将门槛加强梁和门槛外板加强板通过结构胶与门槛外板胶接连接。具体而言,如图5所示,该成型方法是先采用热熔法制成碳纤维预浸料,即碳纤维层,并采用自动下料机裁料,制成单一碳纤维层,再进行手工铺层,最后采用热压罐成型工艺进行门槛外板1的制作,同时本发明中碳纤维层铺设时以零件外表面为贴模面进行铺覆,以零件最外边界作为工程边界,为了铺设更为精确,在零件表面建出坐标系原点,选用零件轴向作为0°,再进行后续的铺设,总体来说是用热熔法制成碳纤维层后采用自动下料机裁料,裁剪成需要的尺寸,上述操作完成后,进行各纤维层的手工铺层操作,把按要求铺设完成的各碳纤维层放入热压罐中,进行热压罐成型工艺操作,本发明采用热压罐成型工艺,是因为热压罐成型工艺采用高温、高压力场成型,使得产品质量及性能更高;在整个热压罐成型工艺的固化期间,记录每个热电偶的测量温度时间间隔不超过10分钟;通过该以上操作步骤生产的门槛外板1与传统钣金的门槛外板相比,具有重量轻,强度高、车身轻量化效果明显等优点。作为优选的,步骤二中碳纤维层在工作平台上平铺,各个碳纤维层中的碳纤维延伸方向间错位分布,这里的错位分布是指各个碳纤维层中碳纤维延伸走向按照设计约定的角度交叉分布,避免碳纤维层单一走向,使得由碳纤维层制成的门槛外板在不同方向上都能承受较大的力,能够很好的解决传统纤维单方向承受力较小的缺陷;当然,相邻碳纤维层间可以是平行分布也可以是垂直分布,也可以使得相邻碳纤维层间具有一定的夹角,具体铺设方向根据需要进行确定;上述各碳纤维层之间是相互堆叠的,本发明全文中的角度都是从贴模面方向进行观察的。作为优选的,第一碳纤维组包括第一上碳纤维组和第一下碳纤维组,第一上碳纤维组和第一下碳纤维组对称设置;第二碳纤维组包括第二上碳纤维组和第二下碳纤维组,第二上碳纤维组和第二下碳纤维组对称设置。通过这样的设置使得最后形成的门槛外板1两侧能够承受的外力相同,使得门槛外板1成型后的变形量减小,不会造成门槛外板1的尺寸因成型后的变形不满足尺寸要求;门槛加强梁同样能达到上述效果。同时上碳纤维组和下碳纤维组对称设置,是指,上碳纤维组与下碳纤维组关于中心对称,这里就会出现两种对称结构,如果总碳纤维层数为偶数,上碳纤维组和下碳纤维组关于两者相连接的平面中心对称;如果总碳纤维层数为奇数,上碳纤维组和下碳纤维组关于碳纤维层中心碳纤维层中心对称;并且通过这样的设置,使得碳纤维组铺覆时只需要铺覆上碳纤维组或者下碳纤维组即可,后续具体使用时,再把两个上碳纤维组或者两个下碳纤维组对称分布即可。提高了工作效率,也避免碳纤维组铺设的出错率。作为进一步的优选方式,以内部碳纤维延伸方向与工作平面相平行的碳纤维层作为基准碳纤维层5,选取上碳纤维组中的任意一个碳纤维层作为整体标定基准的基准碳纤维层,此基准碳纤维层中的碳纤维延伸方向与工作平台相平行,第一上碳纤维组包括基准碳纤维层、碳纤维延伸方向与基准碳纤维层中碳纤维延伸方向的夹角(在顺时针方向上的夹角)为30°~60°的碳纤维层i、碳纤维延伸方向与基准碳纤维层中碳纤维延伸方向的夹角(在逆时针方向的夹角)为-30°~-60°的碳纤维层ii和碳纤维延伸方向与基准碳纤维层中碳纤维延伸方向的夹角(在顺时针方向的夹角)为75°~105°的碳纤维层iii。碳纤维层在上文中说明了成交叉分布,作为进一步的改进,交叉分布的碳纤维层是具有一定规律的,又因为上碳纤维层和下碳纤维层是对称分布的,所以本文中着重介绍了上碳纤维组结构,在上碳纤维组中至少包括一个碳纤维层,也就是设定的0°,也就是基准碳纤维层,在基准碳纤维层上设有多个其它方向的碳纤维层,同时这里的方向指碳纤维层中纤维的延伸方向,从贴模面来看,在基准碳纤维层上设有与基准碳纤维层夹角呈30°~60°的碳纤维层,也有呈-30°~60°的碳纤维层,通过以上结构分布的各个碳纤维层,使得由碳纤维层组成的门槛外板具有较大的刚度,极大的提高了门槛外板的结构强度;作为更进一步的改进,同时使得碳纤维复合材料门槛外板刚度更大,上述与基准碳纤维层夹角呈30°~60°的碳纤维层铺设优选沿与基准碳纤维层夹角呈45°的方向铺设,与基准碳纤维层夹角呈-30°~-60°的碳纤维层铺设沿与基准碳纤维层夹角呈-45°的方向铺设,与基准碳纤维层夹角呈75°~105°的碳纤维层铺设优选沿与基准碳纤维层夹角呈90°的方向铺设,采用以上铺设角度进行铺设的碳纤维组,具有更好的结构强度,极大的提高了门槛外板的结构强度。作为优选的,上碳纤维层组中与基准碳纤维层夹角呈30°~60°的碳纤维层i数量和上碳纤维层组中与基准碳纤维层夹角呈-30°~60°的碳纤维层ii数量相同;这样的设置使得分布在基准碳纤维层两侧的碳纤维层数量相同,有利于优化整体的碳纤维组结构,使得整体碳纤维组结构更为优化,使得纤维分布方向更为均匀,同时避免各碳纤维中纤维同向。作为优选的,基准碳纤维层数量占总碳纤维层数量的10%~60%;碳纤维层i数量占总碳纤维层数量的10%~60%;碳纤维层ii数量占总碳纤维层数量的10%~60%;碳纤维层iii数量占总碳纤维层数量的10%~60%;总体来说,各个方向的碳纤维层数量不超过碳纤维层总量的60%,目的避免单一方向碳纤维层数量过多,影响整体强度。下面通过具体的优选铺设实施例进行详细说明:门槛外板1整体铺覆32层碳纤维层,碳纤维预浸料单层厚度为:0.145mm;0°方向铺覆16层,以上0°方向也就是上文中基准碳纤维层的铺设方向,占总铺层:50%;45°方向铺覆4层,占总铺层:12.5%;-45°方向铺覆4层,占总铺层:12.5%;90°方向铺覆8层,占总铺层:25%,铺覆总厚度为4.64mm,具体铺层分布如下表1;总体来说门槛外板1各纤维层整体铺覆遵循对称原则,进而保证门槛外板1两侧承受力相同;同时上述步骤完成后,把上述铺设完成的碳纤维层组封装,放入热压罐中,采用热压罐成型工艺,利用热压罐高温、高压力场把需要的门槛外板1成型,这样得到的产品质量及性能更高。门槛外板中碳纤维层的铺层分布表1同样的,门槛加强梁2采用的成型工艺及成型步骤与门槛外板1的成型工艺及成型步骤一致。优选的门槛加强梁2整体铺覆24层碳纤维层,碳纤维预浸料单层厚度为:0.145mm;0°方向铺覆8层,以上0°方向也就是上文中基准碳纤维层6的铺设方向,占总铺层:33.3%;45°方向铺覆4层,占总铺层:16.7%;-45°方向铺覆4层,占总铺层:16.7%;90°方向铺覆8层,占总铺层:33.3%,铺覆总厚度为3.48mm,具体铺层分布如下表2;总体来说,门槛加强梁2各纤维层整体铺覆遵循对称原则,进而保证门槛加强梁2两侧承受力相同;同时上述步骤完成后,把上述铺设完成的碳纤维层组封装,放入热压罐中,采用热压罐成型工艺,利用热压罐高温、高压力场把需要的门槛加强梁2成型,这样得到的产品质量及性能更高。门槛加强梁中碳纤维层的铺层分布表2层数层厚碳纤维延伸角度101454520.145030.145-4540.1459050.145060.1459070.1454580.1459090.1450100.145-45110.14590120.1450130.1450140.14590150.145-45160.1450170.14590180.14545190.14590200.1450210.14590220.145-45230.1450240.14545本实施例中碳纤维复合材料门槛总成结构由门槛外板1、门槛加强梁2和门槛外板加强板3三部分组成,且门槛外板加强板3由钢板冲压热成型制成,门槛外板加强板3的位置与汽车b柱结构相连,实现总成减重的同时满足汽车侧面碰撞的强度要求,更好的保护行人安全。门槛外板1、门槛加强梁2和门槛外板加强板3采用结构胶4胶接连接成门槛总成有更好的连接可靠性和耐久性。以上结合附图对本发明进行了示例性描述。显然,本发明具体实现并不受上述方式的限制。只要是采用了本发明的方法构思和技术方案进行的各种非实质性的改进;或未经改进,将本发明的上述构思和技术方案直接应用于其它场合的,均在本发明的保护范围之内。当前第1页12