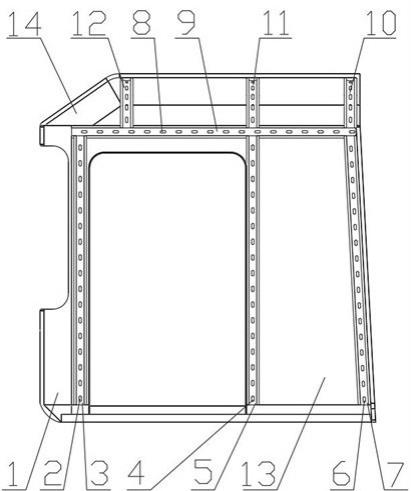
1.本实用新型属于工程机械技术领域,具体涉及一种侧围加强的驾驶室。
背景技术:2.目前驾驶室侧围采用外板加加强梁焊接成侧围的框架式结构。现有驾驶室框架式侧围工艺性较差,在碰撞受力的情况下易发生变形,对驾驶员造成威胁。在车辆行驶过程中,为了保证驾驶室满足可靠性和承载性的要求,驾驶室侧围需要提高强度,从而保证车身不会因为局部受到应力集中而导致变形及开裂。为了提高安全性,安装在汽车上的驾驶室侧围均是采用一体式,但是整体的侧围在使用时容易出现变形的现象,同时侧围内板与立柱及与上梁连接处的受力度较低,导致车身受到撞击时连接处容易变形及断裂。
3.中国专利授权公告号为:cn206797502u、授权公告日为2017年12月26日的实用新型专利公开了一种驾驶室侧围及后围连接位置结构,包括侧围外钣金、侧围内钣金、侧围内饰板、后围钣金和后围内饰板,后围钣金的端部、侧围外钣金的端部、侧围内钣金的端部和侧围内饰板的端部顺次贴合且固定连接,侧围外钣金远离后围钣金的一端和侧围内钣金远离后围钣金的一端贴合且固定连接,本实用新型通过将侧围外钣金、侧围内钣金、侧围内饰板、后围钣金和后围内饰板设置为部分贴合并且固定连接的结构,以及将侧围内饰板和后围内饰板与其他钣金进行固接的方式,该设计虽然大大提高了驾驶室侧围及后尾连接位置处的结构强度,保证结构的侧围及后围连接的可靠性,防止侧围内饰板和后围内饰板的脱落,但是结构复杂,驾驶室侧围强度依旧不高。
技术实现要素:4.本实用新型的目的在于克服现有技术中驾驶室侧围结构复杂、安全保护性能低的不足与缺陷,提出了一种侧围加强的驾驶室,使驾驶室整体性强,结构强度高,降低驾驶室侧围制造成本,能够满足防滚翻、防撞击变形要求,安全可靠。
5.为解决上述技术问题,本实用新型的技术解决方案是:一种侧围加强的驾驶室,所述驾驶室侧围包括驾驶室前围、a柱、b柱、c柱、上梁内板、侧围内板和侧顶盖,其特征在于:
6.设有立柱加强梁,所述立柱加强梁制造材料为超高强钢,形状为长方管状,包括a柱加强梁、b柱加强梁和c柱加强梁,分别插入至a柱、b柱和c柱之中,采用点焊的方式与驾驶室侧围内板焊接在一起,立柱加强梁的长度和大小与a柱、b柱、c柱的尺寸和形状相匹配;
7.设有上梁加强梁,所述上梁加强梁制造材料为超高强钢,形状为长方管状,所述上梁加强梁有两根,分别插入至左、右侧的上梁内板之中,采用点焊的方式与驾驶室侧围内板焊接在一起,立柱加强梁一端搭接在上梁加强梁上,采用激光焊的方式焊接成形,上梁加强梁的长度和大小与上梁内板的尺寸和形状相匹配;
8.设有侧顶盖加强梁,所述侧顶盖加强梁包括依次排列的侧顶盖前加强梁、侧顶盖中加强梁、侧顶盖后加强梁,所述侧顶盖加强梁制造材料为超高强钢,采用点焊的方式焊接在侧顶盖上,侧顶盖加强梁的长度和形状与侧顶盖的尺寸和形状匹配。
9.本实用新型产生的有益效果是:
10.1、在驾驶室侧围安装加强梁可以有效提高侧围强度,提高安全系数,避免车身受到撞击而导致开裂,降低安全隐患。为了顺应汽车轻量化发展要求,一些生产厂家利用高强度材料制造侧围加强装置。但驾驶室侧围立柱及横梁等部件形状复杂,用高强度材料制造困难,工艺繁琐,生产成本较高。相比于直接利用高强度材料制造立柱及横梁,本方法既满足车身强度要求,满足轻量化制造要求,同时制造成本低,制作过程简单,提高生产效率。
11.2、驾驶室侧围受到撞击时,立柱和横梁与侧围内板的连接点往往由于受力度较弱,而发生断裂,进而威胁驾驶人员安全。加强梁采用点焊的方式与侧围内板焊接成形,避免焊缝过长而导致的车身重量增加。经过实验验证,高强度材料与车身普通制造材料点焊后的强度有较大提升,可以避免连接处发生断裂。
附图说明
12.图1是本实用新型的结构示意图;
13.图2是本实用新型的总体结构示意图;
14.图3是本实用新型的立柱和上梁加强梁的结构示意图;
15.图4是本实用新型的侧顶盖加强梁的结构示意图。
16.图中:驾驶室前围1,a柱加强梁2,a柱3,b柱加强梁4,b柱5,c柱加强梁6,c柱7,上梁加强梁8,上梁内板9,侧顶盖后加强梁10,侧顶盖中加强梁11,侧顶盖前加强梁12,侧围内板13,侧顶盖14。
具体实施方式
17.以下结合附图说明和具体实施方式对本实用新型作进一步详细的说明。
18.参见图1至图4,一种侧围加强的驾驶室,所述驾驶室侧围包括驾驶室前围1、a柱3、b柱5、c柱7、上梁内板9、侧围内板13和侧顶盖14,其特征在于:
19.设有立柱加强梁,所述立柱加强梁制造材料为超高强钢,形状为长方管状,包括a柱加强梁2、b柱加强梁4和c柱加强梁6,分别插入至a柱3、b柱5和c柱7之中,采用点焊的方式与驾驶室的侧围内板13焊接在一起,立柱加强梁的长度和大小与a柱3、b柱5、c柱7的尺寸和形状相匹配;
20.设有上梁加强梁8,所述上梁加强梁8制造材料为超高强钢,形状为长方管状,所述上梁加强梁8有两根,分别插入至左、右侧的上梁内板9之中,采用点焊的方式与驾驶室的侧围内板13焊接在一起,立柱加强梁一端搭接在上梁加强梁8上,采用激光焊的方式焊接成形,上梁加强梁8的长度和大小与上梁内板9的尺寸和形状相匹配;
21.设有侧顶盖加强梁,所述侧顶盖加强梁包括依次排列的侧顶盖前加强梁12、侧顶盖中加强梁11、侧顶盖后加强梁10,所述侧顶盖加强梁制造材料为超高强钢,采用点焊的方式焊接在侧顶盖14上,侧顶盖加强梁的长度和形状与侧顶盖14的尺寸和形状匹配。
22.本设计中,立柱加强梁包括左右两侧的a柱加强梁2、b柱加强梁4和c柱加强梁6,所述立柱加强梁分别插入至a柱3、b柱5和c柱7之中,采用点焊的方式与驾驶室侧围内板13焊接在一起。所述立柱加强梁的长度和大小应根据a柱、b柱、c柱的尺寸和形状进行调整,满足装配要求,更好地提高立柱的强度。
23.所述上梁加强梁8同样包括左右两侧,分别插入至左、右上梁内板9之中,采用点焊的方式与驾驶室侧围内板13焊接在一起,所述立柱加强梁一端搭接在所述上梁加强梁8上,采用激光焊的方式焊接成形。经实验验证,采用激光熔丝焊对超高强钢进行焊接,其焊缝强度高于母材,因此可以有效避免焊缝处发生断裂,提高整体强度。所述上梁加强梁8的长度和大小应根据上梁9的尺寸和形状进行调整,满足装配要求,更好地提高上梁内板9的强度。
24.所述侧顶盖加强梁包括左右两侧的侧顶盖前加强梁12、侧顶盖中加强梁11、侧顶盖后加强梁10,所述侧顶盖加强梁制造材料为高强钢,采用点焊的方式焊接在侧顶盖14上。所述侧顶盖加强梁下端与所述上梁内板9搭接,上端与顶盖加强梁搭接焊接。所述侧顶盖中加强梁11与b柱加强梁4保持在同一直线上。所述侧顶盖加强梁的长度和形状应根据侧顶盖14的尺寸和形状进行调整,满足装配要求,更好地提高侧顶盖14的强度。
25.以上所述,仅仅是对本实用新型的具体描述,并不代表本实用新型所实施的所有方式,在本实用新型目的及技术方案的基础上所做的等同变化及修饰,均在本实用新型的专利保护范围内。