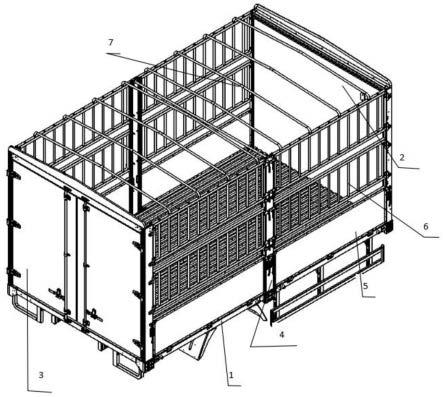
1.本发明涉及仓栏车厢结构技术领域,尤其涉及一种模块化、低碳化、轻量化的仓栏车厢结构。
背景技术:2.目前由于环保和节能的需要,汽车的轻量化已经成为世界汽车发展的潮流。然而目前主要的仓栏车箱大多是钢质车箱,自身重量大,承载能力低,易脱漆生锈,且绝大部分是通过焊接和一些螺接装配而成,装配复杂、困难,维修不便。车箱的尺寸以及车箱与车架连接的硬点位置相对固定,无法应对不同类型的车架,通用性不好。
3.普通钢质车箱多采用焊接方式连接,焊接时焊接变形量大,装配困难,且其在运输过程中焊接处容易开裂,变形,导致车箱寿命降低。一些铝制车箱,为保证性能,其立柱以及立柱与边梁、前后横梁的关键接头位置仍然采用钢质零件,减重效果有限。或有些全铝合金车箱的地板及边板为满足性能而采用较厚实的铝板或铝型材,减重效果不明显反而成本大增。且与钢质车箱一样,存在通用性问题。
4.专利号“cn110239635”提出的模块化装配式轻量化车厢,总成与总成之间仍然焊接用的较多,不利于后期维修和平台化。地板采用的带腔体的铝型材,相比钢板类型的底板减重量小,反而较大的增加了成本。
5.专利号“cn206243281”提出车箱下纵梁和地板下横梁之间焊接而成,无法调节地板下纵梁之间的间距,无法兼容不同的车架,平台化程度低,地板选用了厚实的铝板,减重效果一般。
技术实现要素:6.本发明的目的是为了解决现有技术中存在的缺点,而提出的一种模块化、低碳化、轻量化的仓栏车厢结构。
7.为了实现上述目的,本发明采用了如下技术方案:
8.一种模块化、低碳化、轻量化的仓栏车厢结构,包括底板总成、前围总成、后围总成、中立柱总成、边板总成、花栏总成和顶部总成,所述底板总成的底端设置有六个基座,六个基座分别为左前立柱基座、右前立柱基座、两个中立柱基座、左后立柱基座和右后立柱基座,六个基座将底板总成和前围总成、后围总成、中立柱总成连接固定,前围总成的底端设置有左前立柱和右前立柱,左前立柱和右前立柱插入对应的左前立柱基座和右前立柱基座的腔体内,中立柱总成插入中立柱基座腔体内,后围总成的底端设置有左后立柱和右后立柱,左后立柱和右后立柱插入对应的左后立柱基座和右后立柱基座的腔体内。
9.优选的,所述左前立柱和右前立柱插入对应的左前立柱基座和右前立柱基座的腔体内,并通过螺栓固定。
10.优选的,所述左前立柱基座和右前立柱基座为两通结构,第一接口通过铆钉与左侧或右侧边梁连接,第二接口通过螺栓与前围总成连接。
11.优选的,所述中立柱总成插入中立柱基座腔体内,并通过螺栓固定。
12.优选的,所述中立柱基座为t型三通结构,第一接口和第二接口通过铆钉与左侧或右侧边梁连接,第三接口与中间立柱总成通过螺栓连接。
13.优选的,所述左后立柱和右后立柱插入对应的左后立柱基座和右后立柱基座的腔体内,并通过螺栓固定。
14.优选的,所述左后立柱基座和右后立柱基座为两通结构,第一接口通过铆钉与左侧或右侧边梁连接,第二接口通过螺栓与左后立柱和右后立柱连接。
15.优选的,所述边板总成的四块边板分总成上的上合页分别与底板总成的下合页对齐,插入销轴,装配好开口销,锁紧上翻锁扣。
16.优选的,所述花栏总成的八块花栏分总成上的合页销轴与前围总成、后围总成上的合页对齐,将销轴从上往下插入合页内锁紧栓杆和栓板。
17.本发明的有益效果是:
18.本仓栏车厢采用模块化、低碳化的制造和装配工艺,有效的解决了传统仓栏车厢制造、装配中的各种问题,实现了零件制造和总装生产的柔性化,通过螺接和铆接工艺的运用,实现了车厢生产的革命性变化,尽最大可能减少了焊接工艺,采用模块化生产,提升了涂装工艺的通过性,降低了物流成本,减少了碳排放,提升了产品核心竞争力。
附图说明
19.图1为本发明提出的一种模块化、低碳化、轻量化的仓栏车厢结构的结构示意图;
20.图2为本发明提出的一种模块化、低碳化、轻量化的仓栏车厢结构的中立柱总成的结构示意图;
21.图3为本发明提出的一种模块化、低碳化、轻量化的仓栏车厢结构的底板总成的结构示意图;
22.图4为本发明提出的一种模块化、低碳化、轻量化的仓栏车厢结构的前围总成的结构示意图;
23.图5为本发明提出的一种模块化、低碳化、轻量化的仓栏车厢结构的后围总成的结构示意图;
24.图6为本发明提出的一种模块化、低碳化、轻量化的仓栏车厢结构的边板总成和花栏总成的结构示意图。
25.图中:底板总成1、前围总成2、后围总成3、中立柱总成4、边板总成5、花栏总成6、顶部总成7、左前立柱基座8、右前立柱基座9、中立柱基座10、左后立柱基座11、右后立柱基座12、左前立柱13、右前立柱14、左后立柱15、右后立柱16。
具体实施方式
26.下面将结合本发明实施例中的附图,对本发明实施例中的技术方案进行清楚、完整地描述,显然,所描述的实施例仅仅是本发明一部分实施例,而不是全部的实施例。
27.参照图1-6,一种模块化、低碳化、轻量化的仓栏车厢结构,包括底板总成1、前围总成2、后围总成3、中立柱总成4、边板总成5、花栏总成6、顶部总成7。
28.底板总成1中六个基座分别是左前立柱基座8和右前立柱基座9、中立柱基座10、左
后立柱基座11和右后立柱基座12,本发明专利产品立柱基座采用的是压铸工艺,也可采用组焊工艺。这六个基座是连接底板总成1和前围总成2、后围总成3、中立柱总成4的关键零部件,通过将前围总成2的左前立柱13和右前立柱14插入左前立柱基座8和右前立柱基座9的腔体内,用螺栓紧固,即可实现前围总成2的可靠装配。通过将中立柱总成4插入中立柱基座10腔体内,用螺栓紧固,即可实现中立柱4的可靠安装。通过将后围总成3的左后立柱15和右后立柱16插入左后立柱基座11和右后立柱基座12的腔体内,用螺栓紧固,即可现实后围总成3的可靠装配。
29.将边板总成5的四块边板分总成上的上合页分别与底板总成1的下合页对齐,插入销轴,装配好开口销,锁紧上翻锁扣,即可实现边板总成5的可靠装配。
30.将花栏总成6的八块花栏分总成上的合页销轴与前围总成2、后围总成3上的合页对齐,将销轴从上往下插入合页,锁紧栓杆和栓板,即可实现花栏总成6的可靠装配。
31.底板的中立柱基座10为t型三通结构,接口1和接口2通过铆钉与左侧或右侧边梁连接,接口3与中间立柱总成4通过螺栓连接。底板的左前立柱基座8和右前立柱基座9为两通结构,接口1通过铆钉与左侧或右侧边梁连接,接口2通过螺栓与前围总成2连接。底板的左后立柱基座11和右后立柱基座12为两通结构,接口1通过铆钉与左侧或右侧边梁连接,接口2通过螺栓与左后立柱15和右后立柱16连接。
32.底板的六个连接基座承受一部分横梁和立柱传递来的载荷,需要有足够的刚度、强度和良好的疲劳耐久性能。为了满足上述要求,需要在铸铝件上布设加强筋,通过形貌优化得到加强筋的合理位置,通过尺寸优化得到加强筋的最优尺寸。铸铝上螺栓孔处布设了凸台和传力筋,提高安装孔局部刚度,并降低孔周边应力,防止连接处开裂。
33.六个连接基座的使用,将仓栏车厢底板与侧围的连接方式由传统的焊接改为螺接,实现了上下车体的可分离,从而使上、下车体成为各自独立的子模块,便于参数化设计,模块化制造、低碳化排放、标准化生产、低成本运输、高效率响应。
34.本发明的仓栏车厢结构,采用模块化设计,分为前围总成、后围总成、边板总成、花栏总成、顶部总成、底板总成六大模块,前围总成和后围总成与车厢的高度和宽度相关,边板总成和花栏总成与车厢的长度和高度相关,顶部总成和底板总成与车厢的长度和宽度相关。这些分总成均采用参数化设计,根据客户对车厢规格的不同需求同步实现各分总成的设计,大大提高了产品的设计效率,通过数控锯床、数控折弯机、数控加工中心、激光切割机、数控机械手柔性化设备的运用,实现零件的批量制造,确保零件装配精度,保证后续分总成拼装的顺利进行。
35.因为模块化的设计,保证了分总成及零件的一致性,六大分总成的拼装主要采用螺接、铆接和插接的工艺,极少采用焊接工艺,最大程度的消除了分总成的焊接变形,减少了因焊接烟尘造成的环境污染,提升了分总成的装配精度。
36.因为模块化设计,仓栏车厢的涂装工艺得以优化,六大分总成在合装前分片进行涂装,分片涂装大大节省了涂装线的线体宽度和高度,减少了投资,节约了能源,减少了碳排放,同时杜绝了因整厢电泳形成的电场屏蔽,大大提升了涂装质量。
37.因为模块化设计,仓栏车厢的合厢装配工艺在涂装工艺之后,涂装完成后,无需再有任何焊接和涂胶工序,不损伤油漆,不对环境造成污染,只需采用螺接和插接的方式就可完成仓栏车厢的合厢工艺。
38.因为模块化设计,分总成及零件一致性和精度得以保证,六大分总成采用螺接和插接方式进行连接,防呆设计,无需任何保证合厢精度的夹具和辅具,只需把安装孔对齐,贯穿螺栓即可连接,本发明仓栏车厢装配简便,连接牢固,经权威检测机构标载路试,检验合格,符合国家各项标准。
39.因为模块化设计,使得本发明专利的仓栏车厢可实现异地装配。终端客户对上装的差异化需求,各地经销商需要储备大量整车方能最大限度满足市场需求,占用大量资金,这已成为市场一大痛点。仓栏车厢的异地上装让困扰经销商的这一问题得以缓解,经销商只需储备少量通用底盘和厢体即可,客户需要什么样的上装,可以使用库存厢体及时给予满足,减少客户提车待时间。因为模块化厢体物流成本经济,可根据厢体库存情况,适时补充厢体,大大缩短交付周期,减少资金占用,提高周转率和资金利用效率。
40.因为模块化设计,使得本发明专利仓栏车厢的单台物流成本大幅下降。模块化设计,可以实现仓栏车厢的分片包装运输,物流效率可提高4倍以上,大大降低物流成本,为企业创造效益,为社会节约资源。
41.因为模块化设计,使得本发明专利的仓栏车厢的维修简单便捷。终端用户使用中的造成了车厢的损坏,只需拆卸连接螺栓即可实现对零件及分总成的更换,无需切割及焊接,并保持维修后车辆外观与原来相同,减少车辆年检外观不一致的麻烦。
42.因为模块化设计,可以在不改变现有工艺的前提下,实现仓栏车厢规格尺寸的快速扩展。在标准长度的基础上,通过零件与底板基座的连接,无需任何夹具和模具的投入,快速实现车厢宽度高度的变化及长度的延长,实现车厢规格尺寸的全面覆盖,满足客户差异化的需求。
43.因为模块化设计,使得本发明专利仓栏车厢的制造效率实现了5倍以上的提升,无论是零件、分总成制造环节,还是合厢装配环节,大大缩短了生产节拍,减少了因错焊漏焊、错装漏装造成的返工时间,自动化、标准化生产得以推广和运用。
44.以上所述,仅为本发明较佳的具体实施方式,但本发明的保护范围并不局限于此,任何熟悉本技术领域的技术人员在本发明揭露的技术范围内,根据本发明的技术方案及其发明构思加以等同替换或改变,都应涵盖在本发明的保护范围之内。