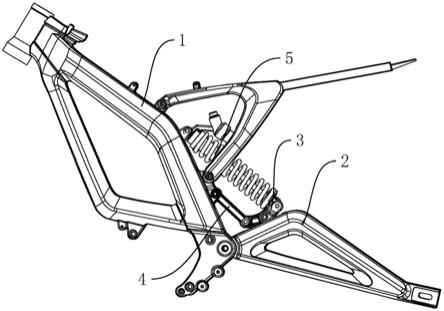
1.本技术涉及摇臂结构的技术领域,更具体地说,它涉及一种后减震器摇臂结构。
背景技术:2.摩托车后悬架是摩托车的重要组成之一,它直接影响摩托车的行驶平顺性,稳定性,燃料经济性等性能.摩托车后悬架整体布置的好坏,是衡量摩托车设计水平的重要指标.
3.如专利公告号为cn214296293u的中国实用新型专利,一种车架总成和两轮车,车架总成包括车架主体、后摇臂和减震器,车架主体包括左侧主梁、右侧主梁和后摇臂连接部件,左侧主梁和右侧主梁之间具有预定的间距,后摇臂连接部件设置于左侧主梁和右侧主梁之间,且后摇臂连接部件设置在左侧主梁和右侧主梁的下方;后摇臂具有车架连接结构,车架连接结构通过后摇臂连接部件与车架主体转动连接,后摇臂的后端具有后轮连接结构;减震器的一端与车架主体连接,另一端与后摇臂连接。
4.针对上述中的相关技术,由于减震器的两端分别与车架主体以及后摇臂直接连接,减震器调校的较软,路面稍有起伏便会产生较为明显的晃动,易导致驾乘人员的眩晕;减震器调校的较硬,遇颠簸路面时,冲击力便大部分会传递至车架主体,造成驾乘者的产生较强的颠簸感,影响驾乘体验。因此,现有的后减震器摇臂结构存在舒适性较差的缺陷,有待改善。
技术实现要素:5.为了提高舒适性,本技术提供一种后减震器摇臂结构。
6.本技术提供的一种后减震器摇臂结构,采用如下的技术方案:
7.一种后减震器摇臂结构,包括车架主体以及后摇臂,所述后摇臂转动连接于车架主体,所述后摇臂转动连接有第一转动架,所述第一转动架和后摇臂的转动轴线平行于所述车架主体和后摇臂的转动轴线;
8.所述第一转动架远离车架主体和后摇臂连接点的一端转动连接有减震器,所述减震器远离第一转动架的一端转动连接于车架主体;
9.所述第一转动架远离减震器的一端转动连接有第二转动架,所述第一转动架和第二转动架的转动轴线平行于第一转动架和后摇臂的转动轴线;
10.所述第二转动架远离第一转动架的一端转动连接于车架主体,所述第二转动和车架主体的转动轴线平行于第二转动架和第一转动架的转动轴线。
11.通过上述技术方案,设置第一转动架和第二转动架,减震器通过第一转动架与后摇臂实现间接连接;通过受力分析,减震器和第一转动架的连接点到后摇臂与车架主体的连接点处的力臂,要大于后摇臂与第一转动架的连接点到后摇臂与车架主体的连接点处的力臂,在后摇臂受到的地面冲击力不变的情况下,相比于减震器与后摇臂直连的结构,增大了减震器到车架主体和后摇臂连接点处的力臂,降低了减震器受到的作用力,进而降低了
通过减震器传递至车架主体的作用力,提高了舒适性。
12.可选的,所述第一转动架呈拱形,且第一转动架的两端朝向车架主体弯曲。
13.通过上述技术方案,设置第一转动架呈拱形,在第一转动架受到来自下摇臂的冲击力时,第一转动架拱形的设置能够较好的分散冲击力,提高第一转动架的结构稳定性。
14.可选的,所述后摇臂包括左半臂、右半臂以及连接左半臂和右半臂的第一连接臂以及第二连接臂,所述第一连接臂用于与第二转动架连接;
15.所述右半臂朝向左半臂的端面设有第一压凹槽;
16.所述左半臂朝向右半臂的端面设有第二压凹槽。
17.通过上述技术方案,设置第一压凹槽以及第二压凹槽,减少左半臂和右半臂所用的材料,减轻左半臂和右半臂的重量,提高整体的轻量化水平。
18.可选的,所述第一压凹槽的槽底设有若干个第一加强筋;
19.所述第二压凹槽的槽底设有若干个第二加强筋。
20.通过上述技术方案,设置第一加强筋和第二加强筋,提高了左半臂和右半臂的结构强度。
21.可选的,所述右半臂背离左半臂的端面开设有第一通槽,所述左半臂背离右半臂的端面开设有第二通槽。
22.通过上述技术方案,设置第一通槽和第二通槽,减少左半臂和右半臂的用料,减轻左半臂和右半臂的重量,提高整体的轻量化水平。
23.可选的,所述第一通槽和第二通槽的槽型均呈三棱锥型。
24.通过上述技术方案,设置第一通槽和第二通槽的槽型均呈三棱锥型,使得第一通槽的侧壁之间以及第二通槽的侧壁之间具有良好的结构稳定性,提高左半臂和右半臂的结构强度。
25.可选的,所述第一连接臂背离第一转动架的端面设有第三压凹槽。
26.通过上述技术方案,设置第三压凹槽,减少第一连接臂上的材料,减少第一连接臂的重量,提高整体的轻量化水平。
27.可选的,所述第三压凹槽中设有第三加强筋,所述第三加强筋沿第一连接臂远离第一转动架的方向正对于第一连接臂和第一转动架的连接点设置。
28.通过上述技术方案,设置第三加强筋,加强第一连接臂的强度,进而强化后摇臂受冲击时第一连接臂和第一转动架连接点处的结构强度,提高整体使用过程中的稳定性。
29.可选的,所述后摇臂的材质为6061-t6材质。
30.通过上述技术方案,设置后摇臂的材质为6061-t6材质,由于6061-t6具有较高的强度,且同时具备良好的加工性能,氧化效果佳,加工过程中不易产生沙眼气孔,平整度较好,能够提高加工效率,降低材料成本。
31.可选的,所述后摇臂通过锻造成型。
32.通过上述技术方案,通过锻造加工后摇臂的方式,能消除后摇臂在冶炼过程中产生的铸态疏松等缺陷,优化微观组织结构,且能够较为完整的保存金属流线,使得锻造成型的后摇臂机械性能要优于铸造成型的后摇臂的机械性能,提高整体的结构强度。
33.综上所述,本技术包括以下至少一种有益技术效果:
34.(1)通过设置第一转动架和第二转动架,减震器通过第一转动架与后摇臂实现间
接连接;通过受力分析,减震器和第一转动架的连接点到后摇臂与车架主体的连接点处的力臂,要大于后摇臂与第一转动架的连接点到后摇臂与车架主体的连接点处的力臂,在后摇臂受到的地面冲击力不变的情况下,相比于减震器与后摇臂直连的结构,增大了减震器到车架主体和后摇臂连接点处的力臂,降低了减震器受到的作用力,进而降低了通过减震器传递至车架主体的作用力,提高了舒适性;
35.(2)通过设置第一压凹槽以及第二压凹槽,减少左半臂和右半臂所用的材料,减轻左半臂和右半臂的重量,提高整体的轻量化水平;
36.(3)通过设置第一加强筋和第二加强筋,提高了左半臂和右半臂的结构强度。
附图说明
37.图1为本实施例的整体结构示意图。
38.图2为本实施例的整体结构示意图,用于展示第一压凹槽的结构。
39.图3为本实施例的整体结构示意图,用于展示第二压凹槽的结构。
40.图4为本实施例的整体结构示意图,用于展示第三压凹槽的结构。
41.附图标记:1、车架主体;2、后摇臂;201、右半臂;202、左半臂;203、第一连接臂;204、第二连接臂;3、第一转动架;4、第二转动架;5、减震器;6、第一压凹槽;7、第一加强筋;8、第二压凹槽;9、第二加强筋;10、第一通槽;11、第二通槽;12、第三压凹槽;13、第三加强筋。
具体实施方式
42.以下结合附图1-4对本技术作进一步详细说明。
43.本技术实施例公开一种后减震器摇臂结构。
44.参照图1和图2,包括车架主体1以及后摇臂2,后摇臂2包括右半臂201、左半臂202、第一连接臂203以及第二连接臂204。左半臂202以及右半臂201分别与车架主体1宽度方向的两侧壁转动连接,且左半臂202以及右半臂201相互平行。第一连接臂203长度方向的两端分别连接于左半臂202和右半臂201相对的两个端面,第二连接臂204长度方向的两端分别连接于左半臂202和右半臂201相对的两个端面,第一连接臂203的长度方向和第二连接臂204的长度方向平行。
45.第一连接臂203转动连接有第一转动架3,第一转动架3和第一连接臂203的转动轴线方向平行于第一连接臂203的长度方向。第一转动架3整体呈拱形,第一转动架3的两端朝远离第一连接臂203的方向弯曲。
46.第一转动架3靠近车架主体1的一端转动连接有第二转动架4,第二转动架4和第一转动架3转动轴线的方向平行于第一连接臂203的长度方向。第二转动架4远离第一转动架3的一端与车架主体1转动连接,且第二转动架4和车架主体1转动轴线的方向平行于第一连接臂203的长度方向。
47.第一转动架3远离车架主体1的一端转动连接有减震器5,第一转动架3和减震器5的转动轴线平行于第一连接臂203的长度方向。减震器5远离第一转动架3的一端与车架主体1转动连接,且减震器5与车架主体1的转动轴线平行于第一连接臂203的长度方向。
48.实际使用过程中,当后摇臂2受到地面冲击时,地面的冲击力通过左半臂202和右
半臂201传递至第一连接臂203,第一连接臂203再将冲击力传递至第一转动架3,第一转动架3将冲击力通过减震器5以及第二转动架4传递至车架主体1。
49.设置第一转动架3和第一连接臂203的转动连接点为第一受力点,减震器5远离车架主体1的一端与第一转动架3的转动连接点为第二受力点,后摇臂2和车架主体1的转动连接点为主受力点。后摇臂2在受到地面冲击的过程中,减震器5远离车架主体1的一端、第一转动架3以及后摇臂2都绕车架主体1做相对转动。由于第二受力点到主受力点的力臂要大于第一受力点到主受力点的力臂,在受到地面冲击力不变的情况下,减震器5受到的作用力要小于传统减震器直连于后摇臂的结构,降低了减震器5对于车架主体1于作用力上的反馈,使得车架主体1在驾乘过程中整体的抖动更小,提高了舒适性。
50.参照图2和图3,右半臂201朝向左半臂202的端面开设有第一压凹槽6,第一压凹槽6的槽底固定有若干个第一加强筋7。
51.左半臂202朝向右半臂201的端面开设有第二压凹槽8,第二压凹槽8的槽底固定有若干个第二加强筋9。通过设置第一压凹槽6、第二压凹槽8减轻左半臂202以及右半臂201的整体质量,提高轻量化水平,且设置了第一加强筋7和第二加强筋9,在开设第一压凹槽6和第二压凹槽8的同时保证了左半臂202和右半臂201的结构强度。
52.右半臂201背离左半臂202的端面开设有第一通槽10,第一通槽10的槽型呈三棱锥形,且第一通槽10靠近左半臂202的槽口小于第一通槽10远离左半臂202的槽口。左半臂202背离右半臂201的端面开设有第二通槽11,第二通槽11的槽型呈三棱锥型,且第二通槽11靠近右半臂201的槽口小于第二通槽11远离右半臂201的槽口。通过在右半臂201上开设第一通槽10,在左半臂202上开设第二通槽11,减少右半臂201和左半臂202的用料,减轻左半臂202和右半臂201的整体质量,进一步提高整体的轻量化程度,且通过三角形具有稳定性的原理,设置第一通槽10和第二通槽11的槽型均呈三棱锥型,保留了右半臂201和左半臂202的结构强度。
53.参照图4,第一连接臂203背离第一转动架3的端面开设有第三压凹槽12,第三压凹槽12的槽底固定有第三加强筋13,第三加强筋13沿第一连接臂203远离第一转动架3的方向正对于第一连接臂203和第一转动架3的转动连接点。通过在第一连接臂203上开设第三压凹槽12,进一步提高整体的轻量化水平,通过设置第三加强筋13,提高整体的结构强度。
54.参照图1,后摇臂2、第一转动架3以及第二转动架4的材质均为6061-t6材质,6061-t6具有较高的强度,且同时具备良好的加工性能,氧化效果佳,加工过程中不易产生沙眼气孔,平整度较好,能够提高加工效率,降低材料成本。
55.后摇臂2、第一转动架3以及第二转动架4均为锻造成型,通过锻造的方式能消除冶炼过程中产生的铸态疏松等缺陷,优化微观组织结构,且能够较为完整的保存金属流线,使得锻造成型的后摇臂2、第一转动架3以及第二转动架4的机械性能要优于铸造成型的机械性能,提高整体的结构强度。
56.本实施例的工作原理是:后摇臂2受到冲击时,后摇臂2将冲击力通过第一转动架3传递至第二转动架4和减震器5,减震器5以及第二转动件再将冲击力传递至车架主体1;通过增大减震器5到后摇臂2和车架主体1转动连接点的力臂,减少减震器5受到冲击力对车架主体1的反馈。
57.以上均为本技术的较佳实施例,并非依此限制本技术的保护范围,故:凡依本技术
的结构、形状、原理所做的等效变化,均应涵盖于本技术的保护范围之内。