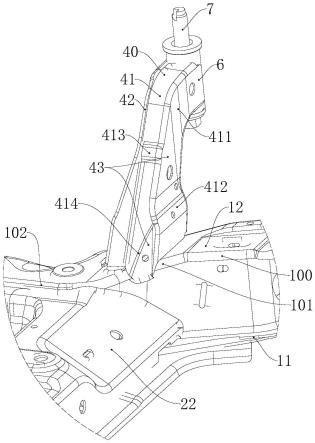
1.本实用新型涉及车架结构技术领域,特别涉及一种副车架与车身的连接结构。另外,本实用新型还涉及一种车辆。
背景技术:2.随着人民生活水平的不断提高,车辆已经不再是仅仅满足代步需要的工具,人们对汽车品质的要求不断提升,对于车辆的噪声、振动等舒适度方面的要求也愈加关注,因此,对车辆噪音和减振方面的性能优化成为本行业持续关注的研发课题。
3.对于前置驱动的车辆,其动力总成产生的振动通过前副车架传递至车身,进而引起整车的振动噪声问题,如何提升前副车架的强度,降低动力总成通过其传递至整车的振动噪声程度,是nvh(noise、vibration、harshness,噪声、振动与声振粗糙度)控制的重要项目。
4.现有技术中,前副车架与车身相连接的部位,其结构设计从整体架构到局部结构布局上都存在一些不足,导致该安装部位的振动传递灵敏度高,结构性能较弱,动力总成产生的振动噪声通过前副车架与车身相连接的安装部位传递至车内,导致整车振动噪声问题明显,降低了车辆乘坐舒适度和整车品质,不利于产品的用户体验。
技术实现要素:5.有鉴于此,本实用新型旨在提出一种副车架与车身的连接结构,以降低前副车架与车身相连接部位的振动传递灵敏度。
6.为达到上述目的,本实用新型的技术方案是这样实现的:
7.一种副车架与车身的连接结构,所述连接结构包括设于副车架上的连接臂,以及用于连接所述车身的连接件;
8.所述连接臂设于所述副车架的顶部,并沿车辆高度方向向上延伸设置,且所述连接臂的顶部设有安装套管,所述连接件穿设于所述安装套管内;所述连接臂采用盒体结构,且所述连接臂的板体上成型有外凸的拱起部。
9.进一步的,所述连接臂由前扣板和后扣板扣合而成,所述前扣板位于所述连接臂的面向车辆前方的一侧,所述后扣板位于所述连接臂的面向车辆后方的一侧。
10.进一步的,所述连接臂向着所述副车架的外侧倾斜设置,且所述连接臂的顶部成型有弯折成水平姿态的弯折段;所述安装套管以竖直姿态焊接于所述弯折段上。
11.进一步的,沿所述连接臂的延伸方向,所述连接臂在车辆宽度方向上的尺寸减小设置。
12.进一步的,所述连接臂设于所述副车架的纵梁上,所述纵梁包括扣合相连的纵梁下板和纵梁上板,所述连接臂与所述纵梁上板固连;所述纵梁内设有位于所述连接臂下方的加强板,所述加强板支撑于所述纵梁下板和所述纵梁上板之间。
13.进一步的,所述加强板包括横截面均呈“几”字形的第一加强板和第二加强板;所
述第一加强板和所述第二加强板相抵接,且所述第一加强板沿所述纵梁的宽度方向布置,所述第二加强板沿所述纵梁的长度方向布置。
14.进一步的,所述拱起部包括位于所述前扣板顶部的第一拱起部、位于所述前扣板底部的第二拱起部、位于所述后扣板顶部的第三拱起部、位于所述后扣板下部的第四拱起部和位于所述前扣板侧部的第五拱起部中的至少一个。
15.进一步的,所述前扣板的板体和所述后扣板的板体上均形成有多个三角形板面;其中,在所述前扣板的板体上,至少一个所述三角形板面位于所述第一拱起部与所述第二拱起部之间,至少一个所述三角形板面位于所述前扣板的板体左侧或右侧;在所述后扣板的板体上,至少一个所述三角形板面位于所述第三拱起部和所述第四拱起部之间,至少一个所述三角形板面位于所述第四拱起部的下方。
16.进一步的,所述后扣板的板体上还形成有梯形板面,所述梯形板面位于所述第三拱起部与距离所述第三拱起部最近的所述三角形板面之间。
17.相对于现有技术,本实用新型具有以下优势:
18.本实用新型的副车架与车身的连接结构,通过在副车架上设置盒体结构的连接臂,同时在连接臂的板体上设置外凸的拱起部,当来自轮毂总成的振动通过连接臂向车身传递时,盒体结构以及拱起部会一定程度地吸收振动的能量,从而削弱振动的传递强度,有利于降低前副车架与车身相连接部位的振动传递灵敏度。
19.此外,将连接臂设计为分体的扣板结构,便于连接臂的构造加工以及盒体结构的成型;前扣板和后扣板分别面向车辆的前后方向设置,使连接臂的厚度方向与车辆的前后方向一致,连接臂的宽度方向和车辆宽度方向一致,更有利于连接臂吸收来自宽度方向上的轮毂总成的振动。
20.而且,连接臂的宽度尺寸由下至上减小设置,较宽的根部优选和纵梁的纵梁底板焊接相连,来自轮毂总成的振动率先被连接臂的根部吸收削弱,随着振动沿连接臂的延伸方向传递,振动的能量逐步被消减,连接臂的宽度尺寸也相应缩小,使连接臂的整体结构外形和缓解振动的要求相适应,可以达到良好地降低振动传递灵敏度的要求。
21.本实用新型的另一目的在于提出一种车辆,所述车辆采用本实用新型所述的副车架与车身的连接结构。本实用新型的车辆具有上述的副车架与车身的连接结构所具备的技术优势。
附图说明
22.构成本实用新型的一部分的附图,是用来提供对本实用新型的进一步理解,本实用新型的示意性实施例及其说明是用于解释本实用新型,其中涉及到的前后、上下等方位词语仅用于表示相对的位置关系,均不构成对本实用新型的不当限定。在附图中:
23.图1为本实用新型实施例一所述的副车架的整体结构示意图;
24.图2为图1所示的副车架在去除轮毂总成和减震器后的俯视图;
25.图3为本实用新型实施例一所述的副车架上连接臂所在部位的局部结构示意图;
26.图4为图3所示部件另一视角下的结构示意图;
27.图5为图3所示部件(安装螺栓已隐去)上方视角下的结构示意图;
28.图6为图5所示部件在去除连接臂和纵梁顶板后的结构示意图;
29.图7为图6所示部件另一视角下的结构示意图;
30.图8为图6所示部件(第二加强板已隐去)下方视角下的结构示意图。
31.附图标记说明:
32.1、纵梁;100、前段;101、中段;102、后段;11、纵梁下板;110、焊接窗口;12、纵梁上板;
33.21、前部横梁;22、中部横梁;23、后部横梁;
34.3、轮毂总成;30、轮毂连接板;31、减震器;
35.4、连接臂;40、弯折段;41、前扣板;411、第一拱起部;412、第二拱起部;413、第五拱起部;414、第一弯折棱;42、后扣板;421、第三拱起部;422、第四拱起部;423、第二弯折棱;43、三角形板面;44、梯形板面;
36.500、减重孔;51、第一加强板;510、顶板;511、侧板;512、底板;513、翻边;52、第二加强板;
37.6、安装套管;7、连接件。
具体实施方式
38.需要说明的是,在不冲突的情况下,本实用新型中的实施例及实施例中的特征可以相互组合。
39.在本实用新型的描述中,需要说明的是,若出现“上”、“下”、“内”、“背”等指示方位或位置关系的术语,其为基于附图所示的方位或位置关系,仅是为了便于描述本实用新型和简化描述,而不是指示或暗示所指的装置或元件必须具有特定的方位、以特定的方位构造和操作,因此不能理解为对本实用新型的限制;若出现“第一”、“第二”等术语,其也仅用于描述目的,而不能理解为指示或暗示相对重要性。
40.此外,在本实用新型的描述中,除非另有明确的限定,术语“安装”、“相连”、“连接”、“连接件”应做广义理解。例如,连接可以是固定连接,也可以是可拆卸连接,或一体地连接;可以是机械连接,也可以是电连接;可以是直接相连,也可以通过中间媒介间接相连,亦或是两个元件内部的连通。对于本领域的普通技术人员而言,可以结合具体情况理解上述术语在本实用新型中的具体含义。
41.下面将参考附图并结合实施例来详细说明本实用新型。
42.实施例一
43.本实施例涉及一种副车架与车身的连接结构,可以降低前副车架与车身相连接部位的振动传递灵敏度;其一种示例性结构如图1、图2和图3所示。
44.整体而言,该副车架与车身的连接结构包括设于副车架上的连接臂4、以及用于连接车身的连接件7。其中,连接臂4设于副车架的顶部,并在车辆的高度方向上向着上方延伸设置,而且,连接臂4的顶部设有安装套管6,连接件7穿设于安装套管6内。同时,连接臂4采用盒体结构,且连接臂4的板体上成型有外凸的拱起部。
45.一般而言,副车架具有在车辆的宽度方向上间隔设置的两个纵梁1、以及连接于两纵梁1之间的多个横梁。在本实施例中,横梁包括沿车辆的前部向着车辆后方依次设置的前部横梁21、中部横梁22和后部横梁23。优选地,连接臂4采用满焊方式固连于纵梁1上和中部横梁22相连的部位。纵梁1的外侧设有轮毂连接板30,轮毂总成3安装在轮毂连接板30上;同
时轮毂总成3上安装由减震器31,减震器31顶部与车身骨架相连。
46.上述车辆的高度方向即车辆的上下方向,车辆的宽度方向即车辆的左右方向,可参考图1、图2中所示的方向理解本实施例。
47.仍如图3并结合图4、图5所示,在本实施例中,连接臂4由前扣板41和后扣板42扣合而成,前扣板41位于连接臂4的面向车辆前方的一侧,后扣板42位于连接臂4的面向车辆后方的一侧。将连接臂4设计为分体的扣板结构,便于连接臂4的构造加工以及盒体结构的成型;前扣板41和后扣板42分别面向车辆的前后方向设置,使连接臂4的厚度方向与车辆的前后方向一致,连接臂4的宽度方向和车辆宽度方向一致,更有利于连接臂4吸收来自宽度方向上的轮毂总成3的振动。
48.对于连接臂4的形状和姿态,优选采用如下的形式。连接臂4由纵梁上板12的顶部向着上方延伸,并向着纵梁1的外侧倾斜设置;并且,在连接臂4的顶部成型有弯折成水平姿态的弯折段40;安装套管6以竖直姿态焊接于弯折段40上;本实施例的连接件7为穿设于安装套管6并螺接到车身上的安装螺栓。同时,沿连接臂4的延伸方向,连接臂4在车辆的宽度方向上的尺寸减小设置。
49.连接臂4外倾设置,同时将连接臂4的弯折段40弯折呈水平姿态,利于将安装套管6竖直地焊接在弯折段40上,便于连接件7的穿设以及与车身的连接安装。连接臂4的宽度尺寸由下至上减小设置,较宽的根部优选和纵梁1的纵梁上板12焊接相连,来自轮毂总成3的振动率先被连接臂4的根部吸收削弱,随着振动沿连接臂4的延伸方向传递,振动的能量逐步被消减,连接臂4的宽度尺寸也相应缩小,使连接臂4的整体结构外形和缓解振动的要求相适应,可以达到良好地降低振动传递灵敏度的要求。
50.如上所述,连接臂4设于副车架的纵梁1上,纵梁1包括上下扣合为一体的纵梁下板11和纵梁上板12,连接臂4与纵梁上板12满焊固连。纵梁1采用纵梁下板11和纵梁上板12扣合的形式,便于加工构造。同时,优选地,纵梁1的中部采用“s”形成的弯曲形状,包括中部横梁22连接部位的中段101、位于中段101前侧的前段100、以及位于中段101后侧的后段102。连接臂4设置在中段101部位。该连接臂4的安装点设计在副车架的纵梁1与中部横梁22相连接的节点位置,利用纵梁1和中部横梁22处的连接强度提升对连接臂4的支撑强度,设计s型结构,则利用s型具有双重拱形的特点,提升该安装部位的强度,从而为连接臂4的设置提供了良好的强度基础。
51.此外,如图6、图7并图8所示,基于纵梁1的内部形成有型腔的情况,在纵梁1内的型腔中设有位于连接臂4下方的加强板,而且加强板支撑于纵梁下板11和纵梁上板12之间。在纵梁1的型腔内设置对应连接臂4的加强板,可形成对纵梁上板12上焊接有连接臂4的部位的支撑,有利于提升连接臂4和纵梁1之间的连接强度,并提升该位置的强度及振动传递面积。
52.加强板的具体数量和结构形式可以灵活设计,在本实施例中,加强板包括横截面均呈“几”字形的第一加强板51和第二加强板52;而且,第一加强板51和第二加强板52相抵接。以垂直于加强板自身的横截面的方向为加强板的布置方向,优选将第一加强板51和第二加强板52垂直布置,其中,第一加强板51沿纵梁1的宽度方向布置,第二加强板52沿纵梁1的长度方向布置,两者的布置方向相互垂直。
53.加强板的横截面采用“几”字形结构,不仅使加强板具有良好的支撑性能,而且加
强板本身也能起到一定的振动缓解效果。第一加强板51和第二加强板52两者抵接在一起且布置方向垂直,具有能缓解多个方向上的振动和冲击的作用,利于进一步提升纵梁1和连接臂4连接部位的结构强度。
54.其中,第一加强板51包括和纵梁上板12抵接相连的顶板510,位于顶板510两侧的侧板511,以及弯折成型于侧板511底部的底板512,底板512抵接在纵梁下板11上,侧板511则支撑在底板512和顶板510之间。同时,可以在侧板511的侧部设置翻边513,进一步提升第一加强板51的自身结构强度和支撑性能。第一加强板51和第二加强板52上均可在结构强度要求不高的部位设置减重孔500,以减轻加强板的自身重量。
55.如图7所示,第二加强板52采用沿其自身长度方向宽度尺寸渐变的形状;由其抵接第一加强板51的一端向着其另一端,第二加强板52的宽度尺寸逐渐增大,并在接近其尾端是再渐变缩小;这种渐变的外形结构不仅与第二加强板52所在的纵梁1的型腔内部空间相适应,且利于提升第二加强板52自身的结构强度。而且,在第二加强板52的横截面上,第一加强板51本身的“几”字形结构同样具有拱形的效果,利用上述结构具有强度大的特点,可提升连接臂4安装位置的强度,同时在第二加强板52上设计拱形凹坑结构可进一步提升该加强板的强度,降低该部位的振动传递灵敏度。
56.上述的加强板的顶部和底部均优选分别和纵梁上板12、纵梁下板11焊接相连,为增加焊接的面积,可在加强板的周边设计20-35mm翻边结构,提升加强板与纵梁1之间的焊接面积及强度。同时,在纵梁下板11上对应底板512的位置,可开设焊接窗口110,该焊接窗口110在降低纵梁下板11重量的同时,可以增加纵梁下板11和第一加强板51的焊接面积及连接强度。为进一步提升该位置的强度,还可在纵梁1连接加强板的位置设计多个凹坑结构,以进一步提升该位置的结构强度,并降低该部位对振动的响应灵敏度。
57.对于连接臂4上拱起部的具体设置位置和数量,同样有多种选择。在本实施例中,如图3、图4、图5所示,拱起部包括位于前扣板41顶部的第一拱起部411,位于前扣板41底部的第二拱起部412,位于于后扣板42顶部的第三拱起部421,位于后扣板42下部的第四拱起部422,以及位于前扣板41侧部的第五拱起部413。而且,在前扣板41和/或后扣板42的板体上,由于板体的弯折造型,在板体的表面成型有弯折棱;位于弯折棱一侧的板体相对于弯折棱另一侧的板体而言,是向着连接臂4的内部方向弯折,因此,弯折棱凸显于连接臂4的外表面。具体来说,本实施例的连接臂4上具有位于前扣板41的侧部的第一弯折棱414,以及位于后扣板42上的第二弯折棱423。
58.通过上述拱起部和弯折棱的设置,可以在前扣板41的板体和后扣板42的板体上划分出多个三角形板面43和梯形板面44的区域。在本实施例中,前扣板41的板体上,至少一个三角形板面43位于第一拱起部411与第二拱起部412之间,至少一个三角形板面43位于前扣板41的板体左侧或右侧。
59.在后扣板42的板体上,至少一个三角形板面43位于第三拱起部421和第四拱起部422之间,至少一个三角形板面43位于第四拱起部422的下方。此外,后扣板42的板体上还形成有梯形板面44,梯形板面位于第三拱起部421与距离第三拱起部421最近的三角形板面43之间。
60.除了上述的三角形板面43形成的三角形区域、以及梯形板面44形成的梯形区域外,在前扣板41的板体上,第五拱起部413位于连接臂4侧部的中部位置,由于第二拱起部
412和第四拱起部422的设置,在第五拱起部413下方的连接臂4的侧板上,还形成有呈纺坠形的区域。
61.在前扣板41的主体部分的顶部、底部以及前扣板41的侧部等尾部位置多个拱起部,可以显著增强前扣板41的结构强度和振动缓解性能;同样地,后扣板42上多个拱起部的设置,同样可达到良好的振动缓解和结构加强作用。前扣板41和后扣板42上多个拱起部的配合设置,可显著提升连接臂4的自身连接强度,并降低连接臂4对振动的敏感度。通过对前扣板41或者后扣板42的板体进行轻微的弯折,从而形成弯折棱,可以起到结构强化的作用;同时,由弯折棱或者拱起部在连接臂4的板体上划分出的多个特定形状的区域,可有效增强连接臂4的结构稳定性。
62.并且,本实施例的连接臂4采用前扣板41和后扣板42扣合而成,外形采用由其顶部向着底部尺寸渐大的设计,为闭合的盒子状加强结构。其中,优选地,前扣板41的板件厚度为1.6mm,后扣板42的板件厚度为1.4mm;第五拱起部413直接成型于前扣板41上,利用拱形强度大特点提升前扣板41侧部中间薄弱位置的强度。该第五拱起部413下方的纺坠形区域下沿至纵梁1上的“s”外形的中段101处,与纵梁1上的三角形凹坑结构衔接。通过上述的设计,利用三角形和纺坠形结构强度稳定的特点可提升连接臂4与纵梁1连接位置的结构稳定性,并降低该连接位置对振动的响应灵敏度。
63.综上所述,本实施例的副车架与车身的连接结构,通过在副车架上设置连接臂4为盒体结构的连接臂4,同时在连接臂4的板体上设置外凸的拱起部,当来自轮毂总成3的振动通过连接臂4向车身传递时,盒体结构以及拱起部会一定程度地吸收振动的能量,从而削弱振动的传递强度,有利于降低前副车架与车身相连接部位的振动传递灵敏度。
64.实施例二
65.本实施例涉及一种车辆,该车辆采用实施例一提供的副车架与车身的连接结构。
66.通过采用实施例一的副车架与车身的连接结构,不仅可提升副车架和车身框架之间的连接强度和结构稳定性,而且有助于降低连接部位对振动传递的灵敏度,可有效衰减动力总成的振动噪声所传递的能量,达到降低车内振动噪声的目的,从而为用户打造舒适的驾乘体验,并有利于提高车辆的耐久性。
67.以上所述仅为本实用新型的较佳实施例而已,并不用以限制本实用新型,凡在本实用新型的精神和原则之内,所作的任何修改、等同替换、改进等,均应包含在本实用新型的保护范围之内。