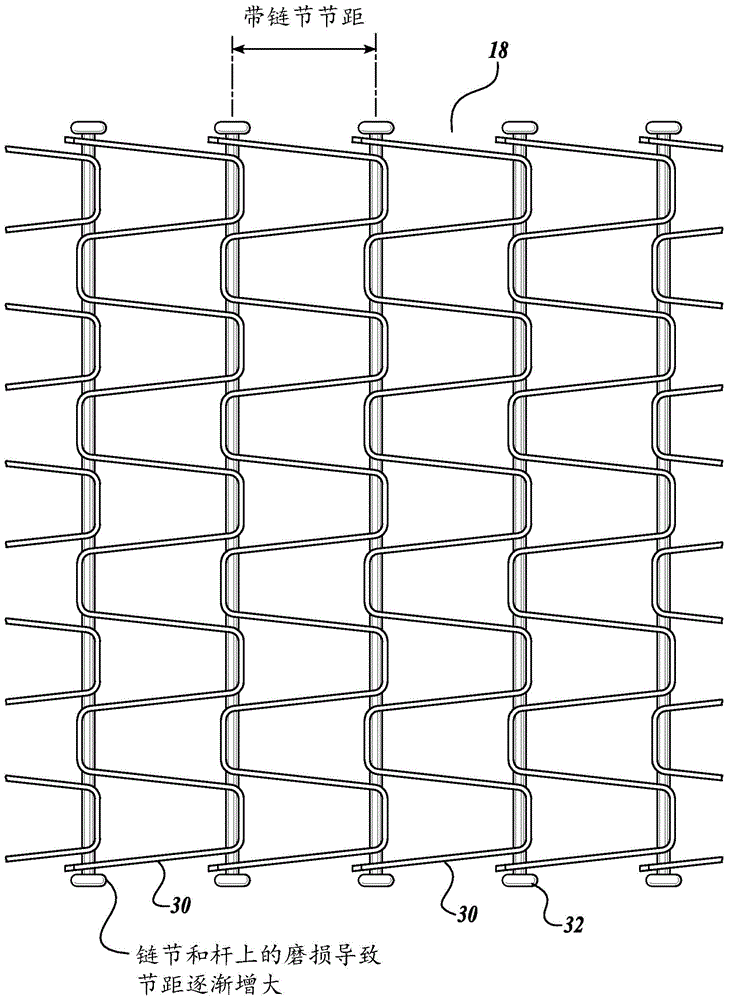
输送带速度/位置的确定和校正对相关申请的交叉引用本申请要求于2012年4月13日提交的美国临时申请号61/624170的权益,其公开内容在此通过引用并入本文。
背景技术:包括食品在内的工件根据客户需要被加工装置切割或以其他方式分割成较小的部分。还有,多余的肥肉、骨头和其它无关的或不希望的材料通常从食品中剔除。通常希望的是,将工件分割和/或修整成均匀的尺寸,例如以便制成餐馆中提供的肉排或制成用于冷冻食品或鸡肉汉堡中的鸡肉片。目前工件特别是食品的分割/修整中的多数都是通过使用高速分割机器实施的。当食品在运动的输送器上前进时,这些机器使用各种扫描技术以确定食品的尺寸、重量和形状。在计算机辅助下分析该信息以便确定如何最高效地将食品分割成最佳尺寸。例如,客户可能想要两种不同重量尺寸、但是没有脂肪或有可接受的有限量脂肪的鸡胸肉部分。鸡胸肉在其在进给输送带上运动时被扫描,并且通过使用计算机确定如何最佳地将鸡胸肉分割和/或修整成客户希望的重量和客户可接受的脂肪含量水平,从而最高效地利用鸡胸肉。前述类型的分割机器在本领域中是已知的。这种分割机器或其构件在之前的专利中公开,例如美国专利号4,962,568和5,868,056,其通过引用并入本文。通常,分割机器包括进给输送器,其具有在支撑结构上滑动的活动实心带。进给输送带被驱动马达以选定的速度驱动。驱动马达可以由变速马达构成,从而调整进给带的速度。工件首先由进给输送器运载经过扫描站,在此工件例如被光学扫描器扫描,以便确定选定的物理参数,例如其尺寸和形状,然后通常通过采用工件的假定密度来确定其重量。此外,可能的是,定位出在工件内或在其上的不连续点(包括空隙)、无关材料和不希望的材料,例如肉部分中的骨头或肥肉。在扫描站处测量/收集到的数据和信息被传递至优选在分割设备上的计算机,该计算机记录工件在进给输送器上的位置以及工件的形状和其它参数。借助该信息,计算机确定如何在分割站处最佳地切割、分割和/或修整工件。一旦 工件经过扫描,则其可以被转送至通常由金属网材料构成的切割输送器。分割可以通过各种类型的切割/分割装置实施。切割装置依靠在扫描站处确定的工件在带上的位置得知由计算机确定的切割在何处进行。因而,重要的是,进给输送器和切割输送器8的速度被精确控制,并且理想地两个输送器均以相同的均匀速度运行。如果(多个)输送器的速度不同,那么工件相对于切割/分割装置的实际位置将不会对应于由计算机计算出的位置。如上所述,根据扫描数据和产品具体情况计算得出切割路径以便进行希望的分割。扫描站和切割/分割站通常以大约3米的距离隔开。为了实现希望的切割效果,加工品在切割输送器上的运输须是相对于其预计位置极其精确的。加工品在输送器上的甚至1毫米(mm)的位置误差将造成不可接受的不精确的加工品切割。切割带通常由安装在驱动轴上的链轮驱动。链轮齿接合带的链节或链的链节,所述链连接至所述带。带的驱动轴的角位置从监测驱动轴角位置的编码器提供的数字信号中知晓。如果带的链节节距在带各处总是恒定的,那么将驱动轴位置转换成带位置将是容易的。然而,因制造误差或随时间推移产生的磨损和损坏,带节距经常不是非常一致的。金属带链节通常在金属横杆上旋转。参见例如本文的图3中的链节30和横杆32。杆与链节中的孔之间的配合必须是松的,当发生磨损时,孔被延长以形成槽,并且带链节的节距改变。如果带的一些部分被损坏并且被更换为新的带,那么将会在系统中存在两种不同的带节距。在链节节距为14mm的一段3米带中的1mm位置误差可以由仅每链节4.7微米(一万八千分之一英寸)的磨损造成。作为参考,(比如自行车上的)辊链在更换之前大体上允许磨损至每链节125微米;所以在输送带上均匀的带节距的假设将造成工件在输送带上的假定位置方面非常大的误差。克服这一问题的一种方法是使用抵靠带表面转动的、编码的摩擦辊测量带位置。在这一方面,参见美国专利号7,025,196,其通过引用并入本文。编码器信号要么直接用于切割器正时,要么其可以用作对驱动轴的反馈以使该驱动轴保持恒定的速度。这种方案具有明显的缺点,包括在没有过多的带张力和在带上存在污染物比如鸡肉、鸡肉脂肪和水的情况下维持摩擦辊和带之间的摩擦方面的困难。使带路径部分地包绕编码的摩擦辊将减小打滑的问题,但不会必然将其消除。本发明试图满足精确和可靠地知晓工件在输送器上的位置的需要。
技术实现要素:本部分被提供用来介绍选取的一些呈简化形式的概念,该概念将在以下具体实施方式部分被进一步描述。本部分并不意图指明了要求保护的主题的关键特征,其也不意图用于辅助确定要求保护的主题的范围。用于基于工件相对于加工器具的位置来控制加工器具在食品或其它类型工件上的操作的控制系统包括用于将工件运载至加工器具的输送器,该输送器包含由相继的部段构成的带。安装在旋转轴上的轮包括从轮的周边延伸的突起以接合带部段。工件相对于加工器具的位置可以通过旋转轴的角位置和带部段在旋转轴处的瞬时节距来确定。在本发明的另一方面,第二轮在沿输送器与第一旋转轴隔开的位置处安装在第二旋转轴上。第二轮包括从第二轮的周边延伸的突起以接合输送带的部段。输送带在第一旋转轴处的瞬时节距通过测量第一和第二旋转轴之间的相对旋转差量来确定。在本发明的另一方面中,输送带是链带,并且第一和第二轮是与链带的链节接合的链轮。在本发明的另一方面中,传动链沿输送带延伸,并且第一和第二轮包括与传动链接合的链轮。在本发明的另一方面中,用于在食品或其它工件上进行操作的系统包括用于在工件上进行操作的工具。用于在工件被操作的同时运载和支撑工件的输送器包括由相继的部段构成的带。传感器检测带部段的瞬时节距和每单位时间沿输送器经过固定位置的带节距的数量以计算出运动的输送器的速度,由此确定工件相对于加工器具的位置。根据本发明的另一方面,输送带的节距通过在两个沿输送带隔开的位置处检测在带部段上的对应位置来确定。根据本发明的另一方面,输送带节距通过在沿输送带隔开的位置处光学感应在带部段上的对应位置而检测出。根据本发明的另一方面,使用处理器而基于检测到的带节距来生成合成编码器的计数,以用于计算运动的输送器的速度,然后校正该合成输送器计数,使之与在两个沿输送带隔开的位置之间的输送带距离成比例。根据本发明的另一方面,提供一种系统用于定位输送物体例如在输送器上被运载的食品,以及用于跟踪输送物体的位置。用于输送所述输送物体的输送器具有基于沿输送器的长度重复的物理特征。传感器检测输送器的物理特征之 间的瞬时节距,以及每单位时间沿输送器经过固定位置的物理特征的数量,由此计算运动的输送器的速度。由该信息确定输送物体的位置。根据本发明的另一方面,输送器节距通过在沿输送器隔开的位置处光学感应出这些沿输送器的物理特征而测定。用于监测在运动的、由相继的带部段构成的输送带上的具体位置的系统包括被配置成围绕第一旋转轴旋转的第一轮。第一轮包括接合带部段的、围绕其周缘的众突起。第一传感器检测第一旋转轴的角位置。第二轮被配置成围绕第二旋转轴旋转,该第二旋转轴位于相对于输送器与第一旋转轴隔开的位置。第二轮包括接合带部段的、围绕其周缘的众突起。第二传感器检测第二旋转轴的角位置。子系统接收检测到的第一和第二旋转轴的角位置并且确定在第一和第二旋转轴之间的角位置方面的相对旋转差量,并且将该信息转换成在第一或第二旋转轴处的带部段的瞬时节距。该信息用于确定监测到的在输送器上的位置。根据本发明的另一方面,用于分割食品或其它类型的加工品的分割系统被装载在输送器上,该输送器具有基于沿输送器的长度重复的物理特征。扫描器扫描由输送器运载的加工品,有切割器用于切割在输送器上被运载的加工品。监测系统监测输送器在扫描器和切割器之间运动过的距离。监测系统因此检测输送器的重复的物理特征之间的瞬时节距,以及检测每单位时间沿输送器经过固定位置的物理特征的数量。该信息用于计算运动的输送器的速度和输送器将加工品从扫描器朝向切割器移动的距离。根据本发明的另一方面,输送器包含由相继的部段构成的带。提供传感器用于检测带部段的瞬时节距,以及检测每单位时间沿输送器经过固定位置的带节距的数量,由此计算出运动的输送器的速度。该信息用于确定加工品从扫描器朝向切割器运动的距离。附图说明图1是根据本发明的呈分割系统形式的加工站的示意图;图2是根据本发明的输送器的出口端的放大图;图3是输送带的部段的放大平面图;图4是另一输送带的部段的放大平面图;以及图5是本发明的另一实施例的示意图。具体实施方式本发明提供这样的系统和方法,其试图通过(除其它方法外)在带的驱动链轮附近测量带节距且合适地调整来自驱动链轮的编码器信号以根据带节距的差量进行校正而精确地确定工件在输送带上的位置。图1示意性示出适合于实施本发明的实施例的系统10。系统10包括输送器20,其用于运载将被分割、修整、切割或以其它方式操作的加工品11。尽管示出了一个输送器20,系统10可以使用多于一个的输送器,例如使用装载输送器、加工输送器和卸载输送器。在扫描方面,系统10包括用于扫描加工品11的扫描器12。在分割方面,系统10包括切割器14和16,其用于将加工品切割成一个或多个具有希望的尺寸或其它物理参数的块。系统10的分割方面还可以包括切片器(未示出),其可以插入在扫描器和切割器之间或者位于切割器的下游。输送器20和扫描器12联结至处理器或具有CPU48和存储器50的计算机46并且由该处理器或具有CPU48和存储器50的计算机46控制。切割器14和16被示出为联结至同一计算机46,但可以改为联结至不同的计算机(未示出)。如图所示,计算机包括界面52,其可以由例如呈键盘、鼠标等形式的一个或多个输入装置以及例如呈显示器、打印机等形式的一个或多个输出装置构成。切割输送器20由金属带18构建而成、由位于下方的支架21支撑并且由安装在驱动轴24上的链轮22驱动。如图4所示,链轮22的齿26接合沿带18的侧边延伸、由成形的平线缆构成的链28的链节34。或者,所述带可以设计成没有链28;而是,链轮22接合带18的最外侧的链节30。带链节30通过金属横杆32相互连接,其接合在链节30中形成的通孔,参见图3。这种类型的输送带驱动引入了在带18被驱动的速度方面的显著的可变性。在链轮22的每个齿26接合和脱离带18的情况下,带的速度因平线缆型带链节30或所述链的链节34的节距变化而增大和减小。计算机46联结至集成到输送器20中的编码器54。编码器以固定间隔产生信号或脉冲,该固定间隔对应于联结至链轮22的驱动轴24的转动。在系统10的操作中,扫描器12扫描加工品11以产生代表加工品的扫描信息并且将扫描信息传递至处理器/计算机46。处理器/计算机46使用扫描产品程序分析扫描数据以确定加工品的形状和生成经扫描的加工品的厚度曲线。处理器/计算机还生成经扫描的加工品的体积分布区域。然后处理器/计算机可以为加工品建模以确定加工品如何被划分成由具有特定物理条件包括例如重量、形状、厚度、长度或宽度的一个或多个终端产品构成的终端产品组。因此,计算机考虑到加工品的面积和形状,以及考虑到加工品的厚度可能在加工品被切割器14 和16分割之前或之后被改变。此外,计算机考虑到在扫描过程中发现的加工品中的缺陷这一因素,并且确定如何经由切割器14和16移除这些缺陷。计算机利用扫描程序和/或分割程序确定加工品如何被修整和/或被分割成一个或多个终端产品。然后,计算机通过使用分割软件而控制切割器14和16以根据选定的终端产品组来修整和/或分割加工品。扫描器12可以是本领域已知的各种类型。这些扫描器在美国专利号7,715,935中描述,其通过引用并入本文。还有,可以使用各种类型的切割器14和16来修整和切割加工品11。切割装置的实例包括高速水射流器、激光器、盘锯、弓锯、铡刀和带锯。高速水射流系统的实例由美国专利号5,365,816和5,868,056公开,其通过引用并入本文。编码的带有链轮的轴精度轮比如图1-3中示出的用于驱动链28或金属带18的链轮22大致被加工成形。链轮极其精确的方面是其具有整数数量的齿26,而链轮的加工可以只是比较精确的。换言之,即使加工操作相当差,如果足以使带和链轮仍然能够啮合,那么在链轮22的每转中有设定数量的齿26经过,随之拉动相同数量的在带18中的链节30。链轮驱动轴24的每转的编码器计数的数量以及因而每齿的编码器计数的数量容易通过根据具体情况计算或通过试验而确定。因而,任何具有链轮的编码的轴,不论是被驱动的还是惰性的,均可以在本发明中用作齿或带链节行程的精确计量器。如上所述,这并不意味着精确地已知带18的行进距离,因为每个链节30大体上具有略微不同的节距。两根带有链轮的轴在带驱动链轮比如链轮22附近测量带节距的一个方法是在距驱动轴链轮24短距离处设置有惰性链轮42的、第二编码的链轮轴40。两个相邻轴24和40的链轮齿经过时间之间的差量可以用于计算两个轴之间的平均带节距。计算机46还联结至集成到输送器20中的编码器44。第二编码器以固定间隔生成信号或脉冲,该固定间隔对应于联结至惰性链轮42的惰性轴40的旋转。两个编码的链轮轴24和40布置成短距离地隔开,例如中心至中心相距300毫米(mm)。得知在整个带长度(可在带上测出)上的平均带节距为15mm,所以轴之间的距离是带18的20个链节。轴之间的平均链节的数量不必须是整数。在带18运行了刚好带的整个长度的一个行程(或者许多行程,如果整个带长度未知的话)之后,在两个轴上的齿行程之间的平均相位可以被确定并且通过加上相位常数而设定为零。如果两个链轮是相同的,那么平均相位是零。但是, 由于情况不太可能是这样,所以在每链轮齿行程的两根轴的旋转角度之间会有一些差异。接着,在两个轴24和40上的齿26和42之间的瞬时相位由编码器计数已知,其被测量为一个齿节距的分数,例如,如果在给定的时刻驱动轴24相比惰性轴40(其位于驱动轴的上游)提前了0.04个齿节距。因而,现在在300mm中存在20–0.04=19.96个齿节距,所以瞬时带链节长度已知为300/19.96=15.03mm。如果平均节距是15mm,那么存在节距小于15mm的带18的其它区域。驱动轴齿行程率乘以瞬时带节距是瞬时带速度。那么对应于瞬时带速度的计算机生成的编码器计数然后可以促动切割器14和16何时和何地需要切割工件11的计算。不是必须明确地根据齿行程来执行计算。齿行程是描述轴之间相位的一种方便的方式,而实际的计算可以使用轴24和40的旋转角度或整体保持在编码器计数的范围内。还有,加工站的实际物理设置例如分割系统10可能具有不同于驱动轴24的用于惰性轴40的编码器分辨率,并且在两个轴上的链轮22和40可以具有不同数量的齿26和42。尽管如此,以上描述的基本原理仍适用。噪声问题就旋转角度而言,编码器信号相较于两个轴24和40的编码器信号之间的差量是非常大的。在任何一个链节/齿的接合中,可能由于链节/齿的实际接合方式、在链节和齿之间的产品碎屑、加工误差、磨损等造成显著的变化。在任何一个链节/齿的接合中的误差相较于产品相对于切割器的位置是轻微的,并且迅速由下一齿或接下来多个齿平衡。然而,当使用本系统在短的长度上检测带节距时,这些小的变化可以导致非常不平稳的和不希望的结果。因此,可以实施过滤来减小这些齿与齿之间的变化量。一种过滤技术是简单地在轴之间的距离上均摊齿相位差(通过节距值计算出)。在探测齿相位差的轴之间的距离越长,任何一个链节变化的影响越小。当然,增大轴之间的距离还降低了系统对于带节距的实际变化的响应能力。可以通过平均在多个相邻的带链节上计算出的带链节节距值来完成额外的过滤。更复杂的方案可以使用数字过滤技术,其中超过一定阈值的频率成分被忽略。假定和校准平均带节距的假定值或直接测得的值与本发明的方法结合使用。因为带12磨损,平均节距会增大(例如增大达1%),并且操作者可能没有输入新的值。然而,在典型的分割机器上有某些校准程序,该校准程序被定期地执行以减小对 于设定假定的担忧。平均带节距中的小误差导致带速度方面的小误差。速度方面的小误差的主要后果是扫描出的体积将与速度误差成比例地发生偏离,切割器的位置将与速度误差乘以扫描至切割的距离的值成比例地发生偏离,并且由切割器产生的切割形状将在长度上与速度误差成比例地发生偏离。由于自动分割器的尺寸和加工方法,所以希望经常且大体上每周一次地校准从扫描器至第一切割器的距离、从第一切割器至第二切割器的距离、从第二切割器至第三切割器的距离等。由于实际加工品例如鸡肉的密度的变化、鸡肉的半透明度的变化以及因此由扫描器探测到的表观厚度等的变化等,所以希望通过输入达到想要的切割重量的密度值来校准切割鸡肉的密度。这一程序基本上每天进行一次。扫描至切割的距离和切割至切割的距离的频繁校准有助于补偿由不正确的平均节距假定值造成的产品位置方面的误差。频繁的密度校准补偿由不正确的平均节距假定值造成的扫描体积方面的微小误差并且还补偿切割体积方面的微小误差。这些补偿对于由于约为0.5%的节距中期值变化而产生的小差量而言是非常合理的。合成编码器信号/速度控制自动分割器控制装置的一种结构是使用带编码器信号而非时间信号,以促动大多数其它工作过程,比如切割器/切片器位置。在这种情况下,希望在控制计算机或其它处理器中生成合成编码器信号,其按时间间隔变化以补偿带速度方面的变化。该合成编码器信号要么可以由刮擦生成,要么其可以是对于来自编码的带有链轮的轴中之一的信号的校正值。自动分割器控制装置的另一种可能的结构是使用时间信号而非带编码器信号,以促动大多数其它工作过程,比如切割器位置。在这种情况下,希望利用在带节距变化方面的信息来致使驱动马达的控制器连续地改变驱动马达速度以维持稳定的带速度。其它组合是可能的,比如生成稳定的合成编码器计数和校正马达速度以实现稳定的带速度。还有,可以使用其它带和机器控制装置的方案,其中带速度被假定为一常数或一斜率值直到其被重新限定成不同的常数或斜率值,来代替编码器信号方案(类似于像素图像和矢量图像表示法之间的区别)。在这种情况下,速度将根据瞬时带节距来校正。启动方法当分割机器例如在一天的起初(假设之前已经进行了所有的校准和输入工作) 开启时,不能马上知道带有链轮的轴24和40位于带18上的什么位置,比如位于低于平均带节距的区域或高于平均带节距的区域。对相位常数作出初始假定,从而机器可以运行并开始节距校正过程。对于相位常数初始值的合理的起始猜测被选取为使得齿初始地同相(等于初始相位差的负值)。随着带18的运行,由于相位常数被更新以使平均值同相,所估计的相位平均值变得越来越精确。在带18运行的几圈内,相位常数变得稳定,并且带节距感应系统精确地确定带速度。"更快速地启动"的方法是,从之前的运行,记录在何处平均齿相位是从最小齿相位开始的齿相位范围的百分数。在带18的一圈之内将遇到最小和最大齿相位。然后,假定的平均相位由目前在运行中遇到的最小和最大值计算出。这种方案由于需要被确定、存储和周期性地更新的值增加了复杂性,但是缩短了实现精确的带链节节距校正的时间。公开范围本发明关于在自动分割器尤其是用于食品分割器中的切割器或切片器进行描述。本方法和技术可以用于控制在其它机器中的除了切割器或切片器以外的加工器具、装备和加工装置,或者用于控制这样的设备,这些设备中两个分离的工作过程(比如扫描和切割)的位置控制相隔很远而有积累带节距误差。这些在食品加工领域中的其它加工器具、装备和加工装置可以包括例如打糊机、面包机、煎炸机、冷冻机、炊具、烤箱、压延机、去肠机、去鳞机等。因而,在使用了切割器或切片器这些词语的任何地方,同样可以适用更宽泛的术语"加工器具"。还有,本发明可以应用于除食品加工以外的许多领域。一些实例包括用于打印、涂装、注射填充、加工操作(例如钻削、铣削或拉削)、焊接或众多其它操作的加工器具。本发明还可以应用于对于工件的自动化操作,或者用于通过自动化装置或其它装置从输送器上卸载工件的时候。还有,任何带,不论是由链轮还是由其它装置驱动,并且不论是由金属、塑料还是由弹性体构成,或者甚至是用于纸的牵引器驱动,均可以利用本发明。前述公开内容讨论了使用两个用于检测带节距的带有链轮的编码的轴24和40,其中之一(24)被驱动,其中另一(40)是惰性的。替代地,可以改为使用两个惰性轴或两根被驱动的轴。还有,两个带有链轮的编码的轴的位置不必须在位于输送器20输出端的末端辊处。两根轴可以在沿输送器20的几乎任何位置处,尽管它们需要非常接近到一起,并且在两根轴之间或在轴与扫描或切割站之间 不能存在收卷机构。两根轴可以位于扫描站12和切割站14、16之前或者甚至在这些站之间。另外,链轮22和40中任一个要么切向地接合带18,要么被带18包绕地接合带18,或者链轮要么位于带上方,要么位于带下方。轴和链轮还可以位于另一轴上,比如接合带18的边缘而非带的底部或顶部。还有,链轮可以呈其它接合带18的旋转装置的形式,比如轮、盘、辐条圈等。还有,与该带的接合可以通过沿这种轮、盘、圈的周边或周缘隔开的齿、突起、凸出来实现,并且可以相对于轮、盘、圈等径向地、横向地或在其间成角度地突出或延伸。轴编码装置可以是许多不同类型的,并且甚至可以呈来自马达控制器的位置反馈装置的形式。另外,如图5所示,为了确定瞬时带速度,链轮122和142中的一个或二者以及关联的编码器的使用可以由使用一个或多个扫描器60或其它光学或近距感应装置来代替,该感应装置检测带链节30、横杆32或输送带118的其它替代(多个)特征或(多个)方面的位置和行程,或者检测在输送带118上的其它(多个)位置。这种特征或方面可以被有目的地设计到带中用作结合本系统和方法的标记,或这种物理特征可以由于其它功能性原因或结构性原因而被设计到带中。因此,与扫描器或者光学或近距传感器一起使用的(多个)带的类型不必须是典型的丝网或链带,而是实际上可以具有任何构造,包括扁平带、塑料带、由多层不同材料构建的带、由高抗拉强度材料或其它类型材料增强的多层带等等。如图5所示,扫描器或者光学或近距传感器可以位于与分割器10隔开的位置。替代地,带的扫描可以使用与用于初始确定工件的物理特征的扫描站相同的扫描站12来实施,见图1。自动分割器和其它加工或产品系统经常使用两个相继的带,其具有从第一带至第二带的平滑的转送装置。第一带用于装载和扫描并且可以具有比如光滑表面的特性。第二带比如上述的带18用于切割或其它操作以及卸载,并且需要具有足够的结构完整性以承受加工器具的操作,例如,通过高压水射流切割器进行的切割操作。因而,第二带18通常呈上文公开类型的带有链轮的金属链带的形式。第一带可以由摩擦驱动系统驱动并且因此在其运动方面非常精确。而且,通常反映从扫描至切割的大部分距离的第二带可以从本发明的方法和技术中极大地获益。在这种情况下,在以上本发明中描述语言是从"扫描至切割"的地方,其可以改成从"转换点至切割"或"转换点至工件操作"。再者,尽管本发明可以有利地用在现代的高精度输送器系统中,但是本发明还可以有利地用在较老式的或精度较低的输送器中,尤其是由连续的链节构 成的输送器,无论其是否具有关联的由链轮或类似的驱动机构驱动的传动链。通常,如果与驱动轴一起使用单一编码器来确定带速度,那么这种输送器将是固有地不精确的。在带经受快速劣化并且必须非常频繁地更换的情形下尤其如此;例如,当用于输送用高速水射流切割的加工品的时候。总体上,本发明的系统和方法可以用于使产品或工件在输送带或类似的输送装置或系统上精确地定位,或者用于监控特定的带或输送装置部段或监控沿运动的输送带或输送装置的具体位置。还可以理解,本发明的系统和方法可以用于扫描或检测所有类型的食品,以及所有类型的制造产品,不论是电子产品、包装还是机械部件等。因此,本系统和方法的使用可以从具有更精确的编码器或关于加工品的位置信息中获益,特别是在随加工品获取扫描器图像的情况下。在一个简单的实例中,本系统和方法可以有利地用于精确地测量较长产品或者用于精确地知晓沿产品长度被扫描的特定特征存在的位置。因此,可以沿运载加工品的输送带每隔一段固定距离进行一次产品扫描,而不是通常采取的以固定的时间间隔进行扫描。尽管已经示出和描述了本发明的示例性实施例,但是应理解,可以在其中作出各种改变而不背离本发明的精神和范围。