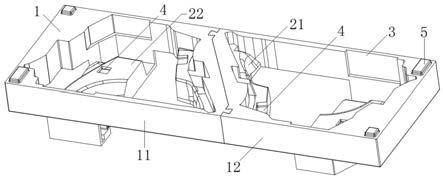
一种用于汽车内c柱下护板的eps包装箱
技术领域
1.本实用新型涉及一种用于汽车内c柱下护板的eps包装箱,属于包装箱技术领域。
背景技术:2.在汽车产业分工精细化快速发展的今天,汽车零部件通常由分散于不同地区的汽车零配件生产厂家根据设计图纸生产制造,再各自运输至车企总装部门统一装配。在汽车零配件出厂、储存、运输、装配过程中,科学选择汽车零部件包装箱,有利于最大限度地减少运输损耗、降低运输成本、提高运载效率。
3.c柱下护板属于汽车侧围护板总成的一个部件,布置在后行李箱两侧,通常起到遮挡钣金及其它附属部件的装饰功能。为适应其它附属部件的形状,汽车内c柱下护板通常需要设计为连续不规则曲面的特定形状,尤其是为适配汽车轮胎形状,导致汽车内c柱下护板的曲面高度差极大。这就给汽车内c柱下护板带来不便,由于汽车内c柱下护板无法承力,利用纸质、木质等传统包装箱进行储运时,不仅装载率不高,还极易造成损坏。
技术实现要素:4.针对现有技术的不足,本实用新型的目的在于提供一种用于汽车内c柱下护板的eps包装箱,以解决现有技术中由于汽车内c柱下护板的曲面高度差极大且无法承力,对其进行储运装载率不高、容易造成损坏的技术问题。
5.为解决上述技术问题,本实用新型所采用的技术方案是:
6.一种用于汽车内c柱下护板的eps包装箱,所述包装箱包括第一本体或/和第二本体,第一本体或/和第二本体的顶面向下凹陷形成有与汽车内c柱下护板的外缘轮廓相适配的型腔,所述型腔向下凹陷形成有第一支撑面和第二支撑面,第二支撑面相对于顶面的深度深于第一支撑面相对于顶面的深度;第一本体或/和第二本体的底面向外凸起形成有与第二支撑面相对应的压合面。
7.进一步地,所述型腔向下镂空形成有减料窗。
8.进一步地,第一支撑面或/和第二支撑面的侧面向内凹陷形成有取件槽。
9.进一步地,第一支撑面或/和第二支撑面向内凹陷形成有护板限位槽。
10.进一步地,底面或/和压合面向内凹陷形成有减料槽。
11.进一步地,第一本体或/和第二本体的顶面向上凸起形成有堆垛限位柱,第一本体或/和第二本体的底面向内凹陷形成有与堆垛限位柱相适配的堆垛限位槽。
12.进一步地,第一本体与第二本体卡接且彼此呈中心对称分布。
13.进一步地,第一本体和第二本体的侧面向外凸起形成有卡凸、向内凹陷形成有卡槽,第一本体的卡凸与第二本体的卡槽相适配,第一本体的卡槽与第二本体的卡凸相适配。
14.与现有技术相比,本实用新型所达到的有益效果:将包装箱设计为第一本体与第二本体卡接的组合式结构,有利于包装箱的生产和储运。第一本体和第二本体的顶面向下凹陷形成有型腔,利用型腔收容汽车内c柱下护板并对其横向限位;型腔向下凹陷形成有深
度不同的第一支撑面和第二支撑面,以适应高度差极大的汽车内c柱下护板曲面形状,延展第一本体和第二本体的底面的纵向尺寸从而形成压合面,当多个包装箱堆垛放置时,上层包装箱的压合面伸入下层包装箱型腔中的富余空间,有利于压缩包装箱高度并提高装载率。利用彼此对应的堆垛限位槽和堆垛限位柱对上下堆垛放置的包装箱进行横向限位,增强堆垛的稳定性,避免发生倾倒。
附图说明
15.图1是本实用新型实施例的正面结构示意图;
16.图2是本实用新型实施例的背面结构示意图;
17.图3是本实用新型实施例的俯视图;
18.图4是本实用新型实施例的仰视图;
19.图5是本实用新型实施例的前视图。
20.图中:1、顶面;11、第一本体;12、第二本体;21、第一支撑面;22、第二支撑面;3、取件槽;4、护板限位槽;5、堆垛限位柱;6、底面;61、堆垛限位槽;7、压合面;81、减料槽;82、减料窗;91、卡凸;92、卡槽。
具体实施方式
21.下面结合附图对本实用新型作进一步描述。以下实施例仅用于更加清楚地说明本实用新型的技术方案,而不能以此来限制本实用新型的保护范围。
22.需要说明的是,在本实用新型的描述中,术语“前”、“后”、“左”、“右”、“上”、“下”、“内”、“外”等指示的方位或位置关系为基于附图中所示的方位或位置关系,仅是为了便于描述本实用新型而不是要求本实用新型必须以特定的方位构造和操作,因此不能理解为对本实用新型的限制。本实用新型描述中使用的术语“前”、“后”、“左”、“右”、“上”、“下”指的是附图中的方向,术语“内”、“外”分别指的是朝向或远离特定部件几何中心的方向。
23.本实用新型具体实施方式提供了一种用于汽车内c柱下护板的eps包装箱,如图1和图2所示,分别是本实用新型实施例的正面和背面结构示意图,所述包装箱由第一本体11与第二本体12相互卡接而成,第一本体11与第二本体12的形状特征完全相同,卡接成包装箱后,第一本体11与第二本体12呈中心对称分布。第一本体11和第二本体12的顶面1各向下凹陷形成有一个型腔,该型腔的外缘轮廓与汽车内c柱下护板的外缘轮廓相吻合,每个型腔用于收容一个汽车内c柱下护板,通过型腔可对汽车内c柱下护板起到横向限位的作用。所述型腔的底面包括第一支撑面21和第二支撑面22,第二支撑面22相对于顶面1的深度显著深于第一支撑面21相对于顶面1的深度。第一支撑面21和第二支撑面22均与汽车内c柱下护板的连续不规则曲面接触,从而起到纵向支撑作用。之所以设计深度不同的两个支撑面,其目的在于,由于汽车内c柱下护板的曲面高度差极大,若支撑面的深度基本相同,那么会导致单个包装箱高度过高,不利于提高装载率。本实施例中,深度较浅第一支撑面21与汽车内c柱下护板高度较低的不规则曲面接触,深度较深的第二支撑面22与汽车内c柱下护板高度较高的不规则曲面接触,该高度较高的不规则曲面通常用于适配汽车轮胎,该曲面位置相较于其他位置的高度差往往能达到20公分以上。同时,要适当延展与第二支撑面22相对应的第一本体11和第二本体12的底面6的纵向尺寸,即:第一本体11和第二本体12的底面6向
外凸起形成有压合面7,该压合面7正好位于第二支撑面22的背面,从而确保了一个包装箱能够完整收容两个汽车内c柱下护板。
24.更具体地,如图3至图5所示,分别是本实用新型实施例的俯视图、仰视图、前视图,所述型腔的底面还向下镂空形成有减料窗82,底面6和压合面7向内凹陷形成有若干减料槽81,均起到节省eps原材料以及减轻重量的作用。本实施例中,每个型腔设有两个减料窗82。
25.更具体地,第一支撑面21和第二支撑面22的侧面均向内凹陷形成有取件槽3,以方便操作人员将手伸入取件槽3内,迅速便捷地将汽车内c柱下护板从型腔内取出。第一支撑面21和第二支撑面22向内凹陷形成有护板限位槽4,汽车内c柱下护板的不规则曲面上的凸起部位卡入该护板限位槽4,起到进一步横向限位的作用。
26.更具体地,第一本体11和第二本体12的顶面1向上凸起形成有堆垛限位柱5,第一本体11和第二本体12的底面6向内凹陷形成有与堆垛限位柱5相适配的堆垛限位槽61。当多个包装箱堆垛放置时,下层包装箱的堆垛限位柱5卡入上层包装箱的堆垛限位槽61内,同时上层包装箱的压合面7伸入下层包装箱的型腔,抵紧下层包装箱型腔内的汽车内c柱下护板,不仅对于汽车内c柱下护板起到纵向限位的作用,同时充分利用了下层包装箱型腔内富裕空间,有利于提高包装箱的装载率。
27.更具体地,第一本体11和第二本体12的侧面向外凸起形成有卡凸91、向内凹陷形成有卡槽92,第一本体11的卡凸91与第二本体12的卡槽92相适配,第一本体11与第二本体12之间通过前述卡凸91和卡槽92进行卡接。包装箱在生产出来后,平时不用时可不对第一本体11与第二本体12进行卡接,只有当使用时才进行卡接,避免卡接后包装箱因尺寸过大不利于储运。因此,设计为第一本体11与第二本体12卡接的组合式结构,在提高包装箱的生产和储运效率上更有优势。
28.以上所述仅是本实用新型的优选实施方式,应当指出,对于本技术领域的普通技术人员来说,在不脱离本实用新型技术原理的前提下,还可以做出若干改进和变形,这些改进和变形也应视为本实用新型的保护范围。