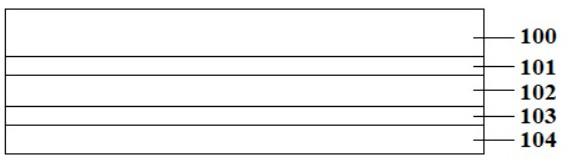
1.本发明涉及包装材料领域,具体涉及一种可回收包装材料及其制备方法。
背景技术:2.铝箔包装膜是食品包装、药品包装及电子零组件、光电产品等电子产品包装中的常用材料,具有阻光、恒温、无毒和成本低廉等特点,是一种性能良好的包装材料。
3.铝箔包装膜基本上属于一次性包装材料,但随着其使用量的增加,废弃的铝箔包装膜也越来越多,其废弃后大多数是混在生活垃圾中被丢弃,回收再利用率低。废弃后,一方面造成了巨大的资源浪费,大量铝箔和聚合物材料无法重新利用;另一方面,包装材料的堆积也易滋生细菌,污染环境和破坏城市面貌。
4.但是,常规的铝箔包装膜中,铝箔与塑性材料层粘接十分牢固,导致在回收时不能将铝箔与塑性材料层容易地分离并分类回收。铝箔包装膜的回收一般是将其浸泡在有机溶剂或者特定的溶解液中以溶解粘合剂,但该回收方法需要使用有机溶剂或者溶解液,对操作人员不友好,并且在回收过程中也会产生新的污染。鉴于此,现有技术也有使用聚乙烯醇等水溶性较好的材料作为剥离层以实现铝箔和塑性材料的分离。但聚乙烯醇对于铝箔的粘接强度较差,并且分解温度较低,在实际应用中受到较大限制。
5.因此,有必要开发更多能够容易地制备和回收的新型可回收包装材料。
技术实现要素:6.针对现有技术存在的问题,本发明提供了一种新型可回收包装材料及其制备方法,所述材料具有结合强度高、易回收等特点。
7.在本发明的一个实施方案中,所述可回收包装材料包含依次层合的:(1) 聚乙烯层;(2) 第一剥离层;(3) 铝箔层;所述第一剥离层包含:(a) 乙烯基吡咯烷酮
‑
丙烯酰胺共聚物,所述乙烯基吡咯烷酮
‑
丙烯酰胺共聚物中含有30~60mol%的源自丙烯酰胺的结构单元,含有40~70mol%的源自乙烯基吡咯烷酮的结构单元;(b) 聚丙烯酸钠;其中,乙烯基吡咯烷酮
‑
丙烯酰胺共聚物与聚丙烯酸钠的质量比为1:0.1~0.5。
8.在一个实施方案中,所述聚乙烯层的厚度为10~100μm,优选20~100μm,更优选30~60μm。构成聚乙烯层的聚乙烯没有特别限定,只要能满足使用需求和涂布要求即可。优选的,聚乙烯的熔体流动速率1~30g/10min,优选5~20g/10min。
9.在一个实施方案中,所述乙烯基吡咯烷酮
‑
丙烯酰胺共聚物含有40~55mol%的源自丙烯酰胺的结构单元,含有45~60mol%的源自乙烯基吡咯烷酮的结构单元;进一步优选
的,所述乙烯基吡咯烷酮
‑
丙烯酰胺共聚物含有45~50mol%的源自丙烯酰胺的结构单元,含有50~55mol%的源自乙烯基吡咯烷酮的结构单元。
10.优选的,所述乙烯基吡咯烷酮
‑
丙烯酰胺共聚物的数均分子量为5
×
104~30
×
10
4 g/mol。
11.在一个实施方案中,所述聚丙烯酸钠的数均分子量为0.8
×
104~8
×
10
4 g/mol,更优选1.5
×
104~4
×
10
4 g/mol。
12.在一个实施方案中,所述乙烯基吡咯烷酮
‑
丙烯酰胺共聚物与聚丙烯酸钠的质量比为1:0.2~0.4。
13.在一个实施方案中,所述第一剥离层的厚度为1~30μm,更优选1.5~20μm,进一步优选2~10μm或者3~8μm。当剥离层的厚度过低时,聚乙烯层与铝箔层的分离变得困难,甚至难以分离。当剥离层的厚度过高时,所述可回收包装材料的整体性能会受到影响。
14.在一个实施方案中,所述铝箔层的厚度为8~18μm,更优选10~16μm。
15.在本发明的一个实施方案中,所述可回收包装材料还可包含层合于铝箔层另一面的:(4) 第二剥离层,以及层合于第二剥离层的:(5) 保护层。
16.为此,在本发明的一个实施方案中,所述可回收包装材料包含依次层合的:(1) 聚乙烯层;(2) 第一剥离层;(3) 铝箔层;(4) 第二剥离层;(5) 保护层;所述第一剥离层包含:(a) 乙烯基吡咯烷酮
‑
丙烯酰胺共聚物,所述共聚物中含有30~60mol%的源自丙烯酰胺的结构单元,含有40~70mol%的源自乙烯基吡咯烷酮的结构单元;(b) 聚丙烯酸钠;其中,乙烯基吡咯烷酮
‑
丙烯酰胺共聚物与聚丙烯酸钠的质量比为1:0.1~0.5。
17.在一个实施方案中,所述第二剥离层可选自与第一剥离层相同的材料,也可选自与第一剥离层不同的材料。优选的,所述第二剥离层与第一剥离层选自相同的材料。优选的,所述第二剥离层的厚度为1~30μm,更优选1.5~20μm,进一步优选2~10μm。
18.优选的,所述保护层包含聚对苯二甲酸乙二醇酯、聚对苯二甲酸丙二醇酯、聚对苯二甲酸丁二醇酯的至少一种。构成保护层的聚对苯二甲酸乙二醇酯、聚对苯二甲酸丙二醇酯、聚对苯二甲酸丁二醇酯没有特别限定,只要能满足使用需求和涂布要求即可。优选的,所述聚对苯二甲酸乙二醇酯、聚对苯二甲酸丙二醇酯、聚对苯二甲酸丁二醇酯的熔体流动速率20~80g/10min,优选25~60g/10min。
19.优选的,所述保护层的厚度为10~30μm,更优选15~25μm。
20.在一个实施方案中,所述可回收包装材料具有如下所示结构中的一种:聚乙烯层/第一剥离层/铝箔层;聚乙烯层/第一剥离层/铝箔层/第二剥离层/聚对苯二甲酸乙二醇酯层;聚乙烯层/第一剥离层/铝箔层/第二剥离层/聚对苯二甲酸丙二醇酯层;聚乙烯层/第一剥离层/铝箔层/第二剥离层/聚对苯二甲酸丁二醇酯层。
21.在本发明的另一个实施方案中,本发明还涉及所述可回收包装材料的制备方法,其包括:a. 按比例称取乙烯基吡咯烷酮
‑
丙烯酰胺共聚物和聚丙烯酸钠,溶于适量的水中形成水溶液;b. 将所述水溶液涂布于铝箔层的一面上,干燥形成第一剥离层;c. 通过挤出涂布将聚乙烯涂布于第一剥离层上形成聚乙烯层。
22.以及可选地,d. 在铝箔层的另一面上形成第二剥离层;e. 通过挤出涂布将构成保护层的聚合物涂布于第二剥离层上形成保护层。
23.优选的,步骤a的水溶液中乙烯基吡咯烷酮
‑
丙烯酰胺共聚物和聚丙烯酸钠的总质量百分比为10~30%,优选15~20%。
24.优选的,步骤c中挤出涂布的操作温度为200~350℃,优选280~320℃。
25.在本发明的另一个实施方案中,本发明还涉及所述乙烯基吡咯烷酮
‑
丙烯酰胺共聚物的制备方法,其包括:将乙烯基吡咯烷酮、丙烯酰胺置于水中,用惰性气体吹扫后缓慢加入引发剂,升温至30~50℃进行反应;将反应产物用甲醇或乙醇沉淀,然后洗涤、干燥得到乙烯基吡咯烷酮
‑
丙烯酰胺共聚物。
26.优选的,所述乙烯基吡咯烷酮、丙烯酰胺的摩尔比为30~60:40~70,优选40~55: 45~60,更优选45~50:50~55,最优选50:50。
27.优选的,所述引发剂选自硝酸铈铵、偶氮二异丁腈、偶氮二异丁酸二甲酯、偶氮二异丙基咪唑啉盐酸盐、过硫酸钾、过硫酸铵中的至少一种。引发剂的用量为乙烯基吡咯烷酮、丙烯酰胺总量的0.05~4mol
‰
,优选0.1~2mol
‰
。
28.优选的,所述反应的温度为40~45℃。
29.优选的,所述反应视需要还可以加入助溶剂、链转移剂、稳定剂等。
30.在本发明的另一个实施方案中,本发明还涉及所述可回收包装材料的回收方法,包括:将所述可回收包装材料浸泡于至少80℃的热水中,搅拌一段时间,待铝箔层与聚乙烯层/保护层分离后,分别回收铝箔层和聚乙烯层/保护层。
31.优选的,将聚乙烯层/第一剥离层/铝箔层构成的可回收包装材料浸泡于至少80℃的热水中,搅拌一段时间,待铝箔层与聚乙烯层分离后,分别回收铝箔层和聚乙烯层。
32.优选的,热水的温度为至少85℃,或者至少90℃。
33.有益效果:本发明涉及一种新型可回收包装材料,所述包装材料可通过热水浸泡处理容易地将铝箔层与聚乙烯层或保护层分离,从而能够分类回收有用的铝箔与聚合物。本发明的可回收包装材料铝箔与聚合物层之间具有较大的剥离强度,在使用过程中不易发生层间剥离的情形。此外,所述可回收包装材料的制备工艺简单,材料安全无毒、阻隔性好,特别适用于作为食品、药品、电子元件类产品的软包装材料。
附图说明
34.图1为三层结构的可回收包装材料的截面示意图。
35.图2为五层结构的可回收包装材料的截面示意图。
36.附图标记说明:100
‑
聚乙烯层;101
‑
第一剥离层;102
‑
铝箔层;103
‑
第二剥离层;104
‑
保护层。
具体实施方式
37.以下将对发明的优选实例进行详细描述。所举实例是为了更好地对发明内容进行,并不是发明内容仅限于实例。根据发明内容对实施方案的非本质的改进和调整,仍属于发明范畴。
38.制备例1:取1mol乙烯基吡咯烷酮、1mol丙烯酰胺加入1l去离子水中,混合物在氮气吹扫下搅拌一小时,然后在2小时内向体系中加入2.2g硝酸铈铵、4ml的1n hno3于90ml水中的引发剂溶液,升温至40℃进行聚合反应,10小时后将所得到的聚合物凝胶加入到甲醇中进行沉淀,分离固体产物并用甲醇洗涤,然后干燥,得到乙烯基吡咯烷酮
‑
丙烯酰胺共聚物173g,通过分析确定乙烯基吡咯烷酮
‑
丙烯酰胺共聚物中包含47mol%的源自丙烯酰胺的单元,53mol%的源自乙烯基吡咯烷酮的单元,共聚物的数均分子量为7.5
×
10
4 g/mol。
39.实施例1:将15g制备例1的乙烯基吡咯烷酮
‑
丙烯酰胺共聚物、3g聚丙烯酸钠(数均分子量2.2
×
10
4 g/mol,下同)加热溶于82g水中形成水溶液,将其涂布于15μm厚的铝箔层102上,在90℃下干燥,从而在铝箔层102上形成3μm厚的第一剥离层101。然后,使用狭缝挤出型涂布机(深圳市科晶智达科技有限公司,msk
‑
afa
‑
mc400,下同)在300℃的加工温度下将35μm厚的聚乙烯层100(熔体流动速率16g/10min,下同)挤出涂布在第一剥离层101上以制备三层结构的铝箔包装膜。所述三层结构的铝箔包装膜如图1所示。
40.实施例2:将15g制备例1的乙烯基吡咯烷酮
‑
丙烯酰胺共聚物、5g聚丙烯酸钠加热溶于80g水中形成水溶液,将其涂布于15μm厚的铝箔层102上,在90℃下干燥,从而在铝箔层102上形成3μm厚的第一剥离层101。然后,使用狭缝挤出型涂布机在300℃的加工温度下将35μm厚的聚乙烯层100挤出涂布在第一剥离层101上以制备三层结构的铝箔包装膜。
41.实施例3:将15g制备例1的乙烯基吡咯烷酮
‑
丙烯酰胺共聚物、3g聚丙烯酸钠加热溶于82g水中形成水溶液,将其涂布于15μm厚的铝箔层102上,在90℃下干燥,从而在铝箔层102上形成8μm厚的第一剥离层101。然后,使用狭缝挤出型涂布机在300℃的加工温度下将35μm厚的聚乙烯层100挤出涂布在第一剥离层101上以制备三层结构的铝箔包装膜。
42.对比例1:将15g的1750型聚乙烯醇加热溶于85g水中形成水溶液,将其涂布于15μm厚的铝箔层102上,在90℃下干燥,从而在铝箔层102上形成3μm厚的剥离层。然后,使用狭缝挤出型涂布机在300℃的加工温度下将35μm厚的聚乙烯层100挤出涂布在所述剥离层上以制备三层结构的铝箔包装膜。
43.对比例2:将15g制备例1的乙烯基吡咯烷酮
‑
丙烯酰胺共聚物加热溶于85g水中形成水溶液,将其涂布于15μm厚的铝箔层102上,在90℃下干燥,从而在铝箔层102上形成3μm厚的第一剥离层101。然后,使用狭缝挤出型涂布机在300℃的加工温度下将35μm厚的聚乙烯层100挤出涂布在第一剥离层101上以制备三层结构的铝箔包装膜。
44.对比例3:使用狭缝挤出型涂布机在300℃的加工温度下将35μm厚的聚乙烯层挤出涂布在15μm厚的铝箔上以制备二层结构的铝箔包装膜。
45.性能测试:1、剥离强度测试参见国家标准gb/t 8808
‑
1988测试剥离强度,样品裁成15
×
200mm的试样条,结果如下表1所示:表1:2、分离性测试将样品切成2
×
20mm的小条,浸泡于90℃的水中并在搅拌下保持5
‑
30分钟,通过目测观察铝箔层与聚乙烯层的分离程度。结果如下表2所示:表2:
实施例4:在实施例1的三层结构的铝箔包装膜上,将实施例1的水溶液涂布于铝箔层102的另一面上,在90℃下干燥,从而在铝箔层102的另一面上形成3μm厚的第二剥离层103。然后,使用狭缝挤出型涂布机在270℃的加工温度下将15μm厚的保护层104(聚对苯二甲酸乙二醇酯)挤出涂布在第二剥离层103上以制备五层结构的铝箔包装膜。所述五层结构的铝箔包装膜如图2所示。
46.最后说明的是,以上优选实施例仅用于说明本发明的技术方案而非限制,尽管通过上述优选实施例已经对本发明进行了详细的描述,但本领域技术人员应当理解,可以在形式上和细节上对其作出各种各样的改变,而不偏离本发明权利要求书所限定的范围。