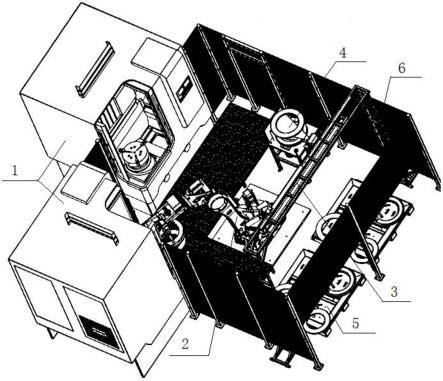
1.本实用新型涉及一种对焊法兰零件机床加工的自动上下料搬运装置,属于自动上下料技术领域。
背景技术:2.在对焊法兰零件机床加工行业,目前大多数都是靠人工给机床上下料,其次就是通过行车或一些自动化程度较低的设备进行辅助上下料,这种上料料结构存在以下缺点:
3.1、由于零件重量0-50kg,操作人员机械式动作,劳动强度大。
4.2、对焊法兰零件在给机床上料时,零件的焊疤位置需避开机床夹具,对操作人员的依赖性大,一般的辅助设备不能完成。
技术实现要素:5.本实用新型提供一种对焊法兰零件机床加工的自动上下料搬运装置,解决目前的对焊法兰零件上下料自动化程度较低,劳动强度较大,并且机床夹具不能避开零件的焊疤位置的问题。
6.本实用新型涉及一种对焊法兰零件机床加工的自动上下料搬运装置,包括存放对焊法兰零件的托盘,托盘的上方设有3d视觉拆码垛系统,搬运机械手一侧设有2d视觉疤痕检测系统;机床旁设有可以把托盘上的零件搬运到2d视觉疤痕检测系统上检测,然后把检测完的零件搬运到机床上加工,最后在把机床加工完的零件搬运到托盘上的搬运机械手。
7.优选的,搬运机械手包括关节机器人,关节机器人的上端固定有旋转电机,旋转电机固定连接有支撑板,支撑板两端安装有卡盘。双工位设计,节省了给机床上下料的时间,整个搬运动作流畅。
8.优选的,3d视觉拆码垛系统包括设置在托盘上方的架体,架体上安装有直线模组,直线模组的移动滑块固定安装有相机安装架,相机安装架底部固定有相机安装板,相机安装板上安装有3d相机。通过3d视觉判断工件的位置坐标进行拆垛抓取,码垛时通过3d视觉判断工件的码垛位置。3d视觉拆码垛系统解决了来料不整齐,托盘摆放有偏差的问题。
9.优选的,架体顶部固定有拖链槽,拖链槽内设有拖链,拖链一端与相机安装架固定。
10.优选的,2d视觉疤痕检测系统包括工作台,工作台上转动安装有转盘,转盘连接有驱动电机,转盘上方一侧的工作台上设有2d相机,2d相机的对面设有固定在工作台上的遮光板。2d视觉检测系统负责检测工件的焊疤位置,工件给机床装夹时有效让卡盘的夹爪避开焊疤位置,提高加工过程中的稳定性。
11.优选的,转盘的顶部固定有多块支承垫块,设置支承垫块,可以把零件垫高,防止机械手抓取零件时碰到转盘,并且防止法兰掉落的碎屑落到转盘上,造成下次放置支承不稳定,转盘一侧的工作台上固定有安装杆,安装杆上设有位置传感器。位置传感器检测支承垫块上是否有工件放上,当有工件放上后,驱动电机启动,可以带着转盘旋转一圈,对法兰
外壁进行焊疤检测。
12.优选的,所述装置还包括集成控制系统,集成控制系统包括plc控制器,plc控制器连接2d相机、3d相机、直线模组、关节机器人、旋转电机、驱动电机、位置传感器和卡盘。
13.托盘、2d视觉疤痕检测系统和搬运机械手外侧设有围挡。进行防护。机床为两个,设置在搬运机械手的两侧,分别负责法兰零件的孔和外园的加工,将两台机床合并到一条自动线,减少了人工干预,降低了劳动强度。
14.本实用新型,具有以下有益效果:
15.1、可以自动实现对焊法兰件的自动上下料搬运,减少了人工干预,降低了劳动强度。
16.2、提高了生产效率,搬运机械手双工位设计,节省了给机床上下料的时间,整个搬运动作流畅。
17.3、通过3d视觉和2d视觉系统实现了对工件的精准定位,提高了产品质量稳定性。
附图说明
18.图1为本实用新型的立体结构示意图;
19.图2为本实用新型的俯视结构示意图;
20.图3为搬运机械手的结构示意图;
21.图4为2d视觉疤痕检测系统的结构示意图;
22.图5为3d视觉拆码垛系统的结构示意图;
23.图中:1、机床,2、搬运机械手,201、旋转电机,202、关节机器人,203、卡盘,204、支撑板,3、3d视觉拆码垛系统,301、架体,302、直线模组,303、拖链槽,304、相机安装板,305、拖链,306、相机安装架,4、2d视觉疤痕检测系统,401、驱动电机,402、安装杆,403、工作台,404、2d相机,405、位置传感器,406、支承垫块,407、转盘,408、遮光板,5、托盘,6、围挡。
具体实施方式
24.下面结合实施例对本实用新型作进一步的说明。
25.实施例1,如图1和2所示,本实用新型为对焊法兰零件机床加工的自动上下料搬运装置,包括存放对焊法兰零件的托盘5,托盘5的上方设有3d视觉拆码垛系统3,搬运机械手2一侧设有2d视觉疤痕检测系统4;机床1旁设有可以把托盘5上的零件搬运到2d视觉疤痕检测系统4上检测,然后把检测完的零件搬运到机床1上加工,最后在把机床1加工完的零件搬运到托盘5上的搬运机械手2。
26.工作时,将工件摆放至托盘5上4摞20层,共80个零件,叉车将托盘5叉放至上料工位,搬运机械手2通过3d视觉拆码垛系统3判断工件的位置坐标进行抓取,然后把工件搬运到2d视觉疤痕检测系统4上,判断焊疤位置,然后机床1需要进行上料时,搬运机械手2移动到2d视觉疤痕检测系统4处,夹取工件,并且夹取时工件避开工件焊疤位置,然后搬运机械手2把工件转移到机床1上,并且装夹时,机床1夹具避开焊疤位置,机床1进行加工,机床1加工完,搬运机械手2把工件搬运到托盘5上。
27.实施例2,如图1至5所示,搬运机械手2包括关节机器人202,关节机器人202的上端固定有旋转电机201,旋转电机201固定连接有支撑板204,支撑板204两端安装有卡盘203。
28.3d视觉拆码垛系统3包括设置在托盘5上方的架体301,架体301上安装有直线模组302,直线模组302的移动滑块固定安装有相机安装架306,相机安装架306底部固定有相机安装板304,相机安装板304上安装有3d相机。
29.架体301顶部固定有拖链槽303,拖链槽303内设有拖链305,拖链305一端与相机安装架306固定。
30.2d视觉疤痕检测系统4包括工作台403,工作台403上转动安装有转盘407,转盘407连接有驱动电机401,转盘407上方一侧的工作台403上设有2d相机404,2d相机404的对面设有固定在工作台403上的遮光板408。
31.转盘407的顶部固定有多块支承垫块406,转盘407一侧的工作台403上固定有安装杆402,安装杆402上设有位置传感器405。机床有主轴定向再加上2d相机可以识别焊疤位置。
32.所述装置还包括集成控制系统,集成控制系统包括plc控制器和工控机,plc控制器连接2d相机404、3d相机、直线模组302、关节机器人202、旋转电机201、工控机、驱动电机401、位置传感器405和卡盘203。关节机器人202型号:埃斯顿re170-2650,直线模组302型号:堇力b13h-l45-s2000-l-p40-d3,2d相机404型号:海康mv-cs050-10gm+mvl-mf1228m-8mp,3d相机型号:埃尔森at-s1000-01a-s1,工控机型号为mv-ipc4794-256g-0206。工控机需要和关节机器人202的控制柜、集成电柜用网线通讯。机床和集成电柜用网线通讯。
33.托盘5、2d视觉疤痕检测系统4和搬运机械手2外侧设有围挡6。
34.操作时,人工将来料毛坯托盘放到毛坯上料工位,将成品空托盘放至成品下料工位;plc控制器给直线模组302的伺服电机发送指令,使3d相机移动到下料托盘处记录成品空托盘的位置;3d相机在移动至毛坯托盘处等待;关节机器人202给3d相机发送拍照扫描指令进行拍照,拍照完成后相机工控机运算工件坐标值,运算完成后工控机将坐标值发送给关节机器人202;关节机器人202根据坐标值抓取工件;关节机器人202双手爪设计,关节机器人202一个夹爪将上一次检测完的工件取走,然后另一夹爪将未检测的工件放至2d视觉旋转盘407上,旋转平台上设有有料检测开关,确认有料后,关节机器人202给plc控制器发送指令,使旋转电机开始工作;当焊疤出现在2d相机视野范围内时,工控机给plc控制器发送指令,使旋转平台停止旋转;关节机器人202手爪避开焊疤位置抓取毛坯件到op10立车一侧等待给机床1上下料;op10立车上一零件加工完成,给关节机器人202发出上料请求信号,关节机器人202给机床1上下料;关节机器人202抓取半成品工件移至op20立车一侧等待给机床上下料;op20立车加工完成,给关节机器人202发出上料请求信号,关节机器人202给机床上下料;关节机器人202根据刚开始确认的下料托盘位置进行码垛;自动线依次循环。op20为第二台机床,op10为第一台机床。
35.综上所述,本实用新型可以自动实现对焊法兰件的自动上下料搬运,减少了人工干预,降低了劳动强度。提高了生产效率,搬运机械手双工位设计,节省了给机床上下料的时间,整个搬运动作流畅。通过3d视觉和2d视觉系统实现了对工件的精准定位,提高了产品质量稳定性。
36.此外,应当理解,虽然本说明书按照实施方式加以描述,但并非每个实施方式仅包含一个独立的技术方案,说明书的这种叙述方式仅仅是为清楚起见,本领域技术人员应当将说明书作为一个整体,各实施例中的技术方案也可以经适当组合,形成本领域技术人员
可以理解的其他实施方式。
37.本实用新型的技术方案也可以针对现有技术解决方案过于单一的技术问题,提供了显著不同于现有技术的解决方案。
38.在本实用新型的描述中,术语“内”、“外”、“纵向”、“横向”、“上”、“下”、“顶”、“底”等指示的方位或位置关系为基于附图所示的方位或位置关系,仅是为了便于描述本实用新型而不是要求本实用新型必须以特定的方位构造和操作,因此不能理解为对本实用新型的限制。