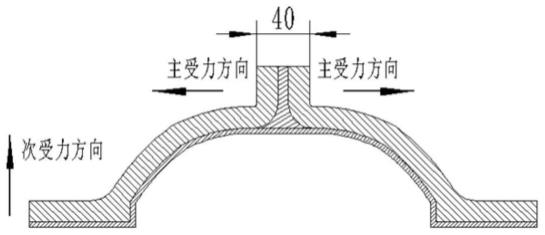
1.本发明涉及复合材料牵引座,特别是一种纤维增强复合材料牵引座及其制备方法、模具。
背景技术:2.悬浮架是磁悬浮列车的核心部件,牵引座则是安装在悬浮架纵梁上的重要传力部件,为磁浮列车传递牵引力和制动力。现有的牵引座为铝合金材质,铸造坯体后焊接在悬浮架的纵梁上,再采用大型数控机床与悬浮架一体机加工成型,密度大、强度低、工艺复杂。随着轨道交通领域对车辆轻量化要求越来越高,传统的铝合金材质已经无法满足现有需求,采用轻质高强的碳纤维复合材料进行替代具有很大的减重空间。
3.铝合金的强度通常在120mpa~300mpa,密度约2.75g/cm3,强度仅200mpa,原磁悬浮列车牵引座为铝合金材质,通过铸造、焊接、机加工等多道工序成型,存在密度大、工艺复杂、强度低、难维护等不足。因此现有技术存在密度高、强度低的缺点,而且工艺复杂。
4.碳纤维密度仅1.65g/cm3,而沿纤维方向的拉伸强度可达到500~800mpa,可见碳纤维的密度更低,而强度更高。但是碳纤维复合材料是一种二维材料,层间的剪切强度仅30~80mpa,因此如何铺层设计和成型工艺设计从而充分发挥出碳纤维复合材料的轻质高强特性是本技术的关键。
技术实现要素:5.本发明所要解决的技术问题是,针对现有技术不足,提供一种纤维增强复合材料牵引座及其制备方法、模具,充分发挥碳纤维的高强度、低密度优势,拉伸强度达到产品性能要求。
6.本发明公开了一种纤维增强复合材料牵引座的模具,包括第一模具、第二模具和第三模具,所述第一模具包括平台和设于所述平台上表面的弧形凸起部,所述第二模具包括第一凹陷部和第一直角部,所述第三模具包括第二凹陷部和第一直角部。
7.由于牵引座的主受力方向近似于对称,因此本技术设计了左右模块对称铺层结构,本技术中模具设计的特点是:用第一模具定位,保证了牵引座与纵梁的装配精度,第二模具和第三模具保证了牵引座与牵引杆的装配精度。
8.本发明涉及一种连续碳纤维牵引座,整体厚度20mm,根据传力方向设计纤维方向(如图1),水平方向左右牵引力力大小近乎一致,因此在分模块时将第二模具和第三模具分型为对称结构,在中间部位(40mm处)合模引用了复合材料典型结构t型梁(如图2),该结构制造简单,工艺性好,充分发挥碳纤维的高强度、低密度优势,同时本发明不仅成型工艺简单,成型周期短,而且拆卸方便,降低维护成本。
9.本发明还公开了一种纤维增强复合材料牵引座的制备方法,包括以下步骤:
10.准备第一模具,在所述平台和所述弧形凸起部上表面进行第一次碳纤维预浸料铺层;
11.准备第二模具,在所述第一凹陷部和所述第一直角部表面进行第二次碳纤维预浸料铺层;
12.将第一模具和第二模具进行合模,使第二模具上的第二次碳纤维预浸料铺层铺于第一模具上的第一次碳纤维预浸料铺层左侧上表面;
13.在所述第一直角部表面的第二次碳纤维预浸料铺层上进行第三次碳纤维预浸料铺层;
14.准备第三模具,在所述第二凹陷部和所述第一直角部表面进行第四次碳纤维预浸料铺层;
15.将第三模具和第一模具进行合模,使第三模具上的第四次碳纤维预浸料铺层铺于第一模具上的第一次碳纤维预浸料铺层右侧上表面,得到铺层后的整体模具;
16.将铺层后的整体模具进行固化成型后形成毛坯,并机加工制得纤维增强复合材料牵引座。
17.本发明根据牵引座的传力方向设计了纤维方向,充分发挥碳纤维高强度优势,极大地降低牵引座重量。由于牵引座的主受力方向为水平方向(如图1),为保证牵引座在受力方向上的纤维连续性,铺层时各个模块的纤维是连续的,纤维铺层截面如图4。纤维铺层方向全部是沿模具面,成型时压力更均匀。铺层时每层需贴合紧实,让预浸料层间更加紧实。
18.第一次碳纤维预浸料铺层的厚度为3-5mm,第二次碳纤维预浸料铺层和第四次碳纤维预浸料铺层的厚度为14-17mm,第三次碳纤维预浸料铺层的厚度为7-10mm。
19.本技术中的铺层厚度是结合受力分析和实验研究的优化结果,底部第一模具铺层太薄牵引座受力时导致底部加强层整体分层出现层间剥离(如图19);底部第一模具加强层铺层太厚导致第二模块和第三模块厚度减少,牵引座拱形结构的刚度不足,牵引座的最大承载力仅45kn,不能满足试验要求的50kn。
20.第一次碳纤维预浸料铺层、第二次碳纤维预浸料铺层、第三次碳纤维预浸料铺层和第四次碳纤维预浸料铺层的工艺均为每铺10~15层碳纤维预浸料进行袋压一次,每次保压时间≥30min。有效提高了层间结合力。
21.制作时,根据三维及模具尺寸设计三个模块的下料图,用裁布机进行预浸料的裁剪以保证尺寸精准度;铺层时每层需贴合紧实,每10~15层进行袋压一次让预浸料层间更加紧实,每次保压时间≥30min。单层碳纤维的厚度仅0.4mm,而牵引座最厚尺寸达到40mm,即碳纤维层数需达到100层,本技术虽然通过模块划分优化了铺层方案,但单个模块铺敷层数最多仍高达40层,若采用一次性铺完,直接袋压固化的方式,则碳纤维层间的气泡被挤压在内部很难排出,固化后就会变成气泡或脱层,为了降低这种工艺缺陷风险,本技术通过实验研究得出每10~15层需袋压一次,让层间充分压实。在满足力学性能要求的前提下,袋压成型工艺相比热压罐、模压,袋压成型工艺制作周期短,模具成本与耗能更低。
22.第一次碳纤维预浸料铺层、第二次碳纤维预浸料铺层、第三次碳纤维预浸料铺层和第四次碳纤维预浸料铺层均采用平纹/斜纹交替铺层。平纹/斜纹交替铺层有效提高了层间结合力。
23.将第一模具和第二模具进行合模后,进行袋压,保压0.5-2h。
24.待第一模具和第二模具单独铺层完成后,将两个模块进行组合,袋压保压1h使两个模块贴合紧实无缝隙。
25.铺层后的整体模具固化成型的温度为80-100℃保温1-2h,100-150℃再保温0.5-2h。
26.第一次碳纤维预浸料铺层、第二次碳纤维预浸料铺层、第三次碳纤维预浸料铺层和第四次碳纤维预浸料铺层均采用连续的碳纤维预浸料。
27.第一次碳纤维预浸料铺层、第二次碳纤维预浸料铺层、第三次碳纤维预浸料铺层和第四次碳纤维预浸料铺层均沿同一个方向进行铺贴。
28.从工艺设计方面考虑,为保证牵引座外观尺寸与表面平整度,将模具设计成对模(如图3);碳纤维环氧预浸料沿同一个方向进行铺贴,保证层间结合力强度。
29.本发明还公开了一种所述的纤维增强复合材料牵引座的制备方法制得的纤维增强复合材料牵引座。
30.本技术的关键是通过铺层设计,使主承力方向为纤维连续方向,次承力方向为层间剪切方向,从而充分发挥出碳纤维复合材料的轻质高强特性。近年来,碳纤维复合材料在各行业应用逐渐深入,而本技术与其他碳纤维制件的区别主要体现在铺层设计和成型工艺设计。
31.本发明关键点是设计了铺层方案、成型方案和连接方案,保护点是纤维增强复合材料牵引座铺层方案、成型工艺技术和连接技术。
32.与现有技术相比,本发明所具有的有益效果为:本发明相比现有的铝合金方案,本发明提高了牵引座的承载能力,同时重量降低40%以上。牵引座的最大承载力满足试验要求的50kn。
附图说明
33.图1为本发明一实施例的受力分析图。
34.图2为本发明一实施例中t型梁铺层示意图(其中铺层组2和铺层组4中的铺层组3未画出)。
35.图3为本发明一实施例的模具结构示意图。
36.图4为本发明一实施例中牵引座铺层截面图。
37.图5为本发明一实施例中制备方法步骤一、准备第一模具。
38.图6为本发明一实施例中制备方法步骤二、在第一模具上铺层。
39.图7为本发明一实施例中制备方法步骤三、准备第二模具。
40.图8为本发明一实施例中制备方法步骤四、在第二模具上铺层。
41.图9为本发明一实施例中制备方法步骤五、将第一模具和第二模具合模。
42.图10为本发明一实施例中制备方法步骤六、准备第三模具。
43.图11为本发明一实施例中制备方法步骤七、在第三模具上铺层。
44.图12为本发明一实施例中制备方法步骤八、将第三模具与和第一模具、第二模具合模。
45.图13为本发明一实施例中制备方法步骤九、固化后毛坯。
46.图14为本发明一实施例中制备方法步骤十、机加后的牵引座。
47.图15为本发明对比例中的单面整体模具。
48.图16为本发明一实施例中牵引座俯视图。
49.图17为本发明一实施例中牵引座侧视图。
50.图18为本发明一实施例中牵引座重量。
51.图19为本发明对比例中出现的断裂与层间剥离。
52.图20为本发明一实施例中的力学性能测试照片。
具体实施方式
53.如图3所示,一种纤维增强复合材料牵引座的模具,包括第一模具1、第二模具2和第三模具3,所述第一模具1包括平台11和设于所述平台11上表面的弧形凸起部12,所述第二模具2包括第一凹陷部21和第一直角部22,所述第三模具3包括第二凹陷部31和第一直角部32。
54.如图5-14所示,一种纤维增强复合材料牵引座的制备方法,包括以下步骤:
55.如图5-6所示,准备第一模具1,在所述平台11和所述弧形凸起部12上表面进行第一次碳纤维预浸料铺层,得到铺层组1;
56.如图7-8所示,准备第二模具2,在所述第一凹陷部21和所述第一直角部22表面进行第二次碳纤维预浸料铺层,得到铺层组2;
57.如图9所示,将第一模具1和第二模具进行合模,使第二模具2上的第二次碳纤维预浸料铺层铺于第一模具上的第一次碳纤维预浸料铺层左侧上表面;
58.如图9所示,在所述第一直角部22表面的第二次碳纤维预浸料铺层上进行第三次碳纤维预浸料铺层,得到铺层组3;
59.如图10-11所示,准备第三模具3,在所述第二凹陷部31和所述第一直角部32表面进行第四次碳纤维预浸料铺层,得到铺层组4;
60.如图12所示,将第三模具3和第一模具1进行合模,使第三模具3上的第四次碳纤维预浸料铺层铺于第一模具1上的第一次碳纤维预浸料铺层右侧上表面,得到铺层后的整体模具;
61.如图13所示,将铺层后的整体模具进行固化成型后形成毛坯,如图14所示,并机加工制得纤维增强复合材料牵引座。
62.第一次碳纤维预浸料铺层的厚度为3-5mm,第二次碳纤维预浸料铺层和第四次碳纤维预浸料铺层的厚度为14-17mm,第三次碳纤维预浸料铺层的厚度为7-10mm。
63.第一次碳纤维预浸料铺层、第二次碳纤维预浸料铺层、第三次碳纤维预浸料铺层和第四次碳纤维预浸料铺层的工艺均为每铺10~15层碳纤维预浸料进行袋压一次,每次保压时间≥30min。
64.第一次碳纤维预浸料铺层、第二次碳纤维预浸料铺层、第三次碳纤维预浸料铺层和第四次碳纤维预浸料铺层均采用平纹/斜纹交替铺层。
65.将第一模具1和第二模具2进行合模后,进行袋压,保压0.5-2h。
66.铺层后的整体模具固化成型的温度为80-100℃保温1-2h,100-150℃再保温0.5-2h。
67.第一次碳纤维预浸料铺层、第二次碳纤维预浸料铺层、第三次碳纤维预浸料铺层和第四次碳纤维预浸料铺层均采用连续的碳纤维预浸料。
68.实施例
69.本发明根据牵引座的传力方向设计了纤维方向,充分发挥碳纤维高强度优势,极大地降低牵引座重量。由于牵引座的主受力方向为水平方向(如图1),为保证牵引座在受力方向上的纤维连续性,铺层时各个模块的纤维是连续的,纤维铺层截面如图4。
70.制作时,根据三维及模具尺寸设计三个模块的下料图,用裁布机进行预浸料的裁剪以保证尺寸精准度;铺层时每层需贴合紧实,每10~15层进行袋压一次让预浸料层间更加紧实,每次保压时间≥30min。单层碳纤维的厚度仅0.4mm,而牵引座最厚尺寸达到40mm,即碳纤维层数需达到100层,本技术虽然通过模块划分优化了铺层方案,但单个模块铺敷层数最多仍高达40层,若采用一次性铺完,直接袋压固化的方式,则碳纤维层间的气泡被挤压在内部很难排出,固化后就会变成气泡或脱层,为了降低这种工艺缺陷风险,本技术通过实验研究得出每10~15层需袋压一次,让层间充分压实。在满足力学性能要求的前提下,袋压成型工艺相比热压罐、模压,袋压成型工艺制作周期短,模具成本与耗能更低。
71.1)从工艺设计方面考虑,为保证牵引座外观尺寸与表面平整度,将模具设计成对模(如图3);碳纤维环氧预浸料沿同一个方向进行铺贴,保证层间结合力强度。由于牵引座的主受力方向近似于对称,因此本技术设计了左右模块对称铺层结构,本技术中模具设计的特点是:1、用第一模具定位,保证了牵引座与纵梁的装配精度,第二模具和第三模具保证了牵引座与牵引杆的装配精度;2、优化了铺层操作,将原来的单个模块最厚142层通过工艺优化为57层,从而也减少了袋压次数;3、纤维铺层方向全部是沿模具面,成型时压力更均匀。
72.2)从选材方面,从牵引座外形考虑,需具有良好的成型及加工要求;从结构考虑,牵引座为承载件,需满足牵引座力学性能试验要求。
73.3)成型工艺上,通过多次工艺验证及试验测试,得到最优方案为第一模具底部加强层铺层4mm,第二模块和第三模块为对称结构,均铺层16mm(如图3)。本技术中的铺层厚度是结合受力分析和实验研究的优化结果,底部第一模具铺层太薄牵引座受力时导致底部加强层整体分层出现层间剥离(如图19);底部第一模具加强层铺层太厚导致第二模块和第三模块厚度减少,牵引座拱形结构的刚度不足,牵引座的最大承载力仅45kn,不能满足试验要求的50kn。
74.铺层过程中严格按照工艺要求进行操作,最终达到满足产品一体化成型要求。铺层时先铺底部加强层4mm(平纹7层,斜纹7层)如图6;左右弧形模块为对称结构,均为16mm(平纹28层,斜纹29层)如图8、图11,左右模块进行单独铺层;三个模块单独进行铺层后将模块1和2(或3)进行组合,再铺中间40mm厚的填充层(8mm)如图9,最后组合3(或2)如图12;为保证装配精准度,待固化成型后将装配圆孔与中间镂空减重位置进行机加;严格按照计算的理论层数要求以及铺层方向,每层布料铺放完成之后用刮板刮平压实,排除气泡;铺层过程中每10层袋压一次保证层间无缝隙、气泡,每次保压时间≥30min。碳纤维环氧预浸料采用中航的cw240(斜纹编织布)和cw200t(平纹编织布),平纹/斜纹交替铺层有效提高了层间结合力;固化温度:90℃/1.5h+130℃/1h。
75.待模块1和2单独铺层完成后,将两个模块进行组合,袋压保压1h使两个模块贴合紧实无缝隙。然后铺中间填充层8mm(如图9);铺完填充层后组合第三模块(如图12)。
76.图3示出了该发明的一种实施例,将产品结构分成3个模块,先将其先独立铺层成型,后组合一体固化成型。通过从工艺设计、材料选择、合理的成型工艺方案,最终实现牵引
座一体化成型。
77.如图16-18、20所示,本发明产品经过以下实验测试
78.(1)阻燃/烟毒测试,阻燃等级达到en 45545-hl2级、
79.(2)环保测试,满足tb/t 3139-2021标准
80.(3)常规力学性能测试,通过了50kn牵引力考核
81.(4)通过了湿热老化试验
82.本发明借助有限元仿真软件分析了应力云图、模态、振动仿真,证明方案可行。
83.本技术优化了铺层操作,将原来的单个模块最厚142层通过工艺优化为57层,从而也减少了袋压次数。
84.对比例1
85.对比例与实施例的区别在于采用单面模整体模具,单面模整体模具(如图15)操作困难且不能做到牵引座上下两个面都光滑。整体开模在中间位置(40mm处)铺层操作难,拐角处难以铺层到位,造成产品层间有缝隙、积胶等缺陷。
86.对比例2
87.对比例与实施例的区别在于模具铺层厚度不一样。前期厚度分型为底部第一模具铺层10mm,第二模具和第三模具铺层10mm,为对称结构,经过牵引力极限试验发现该铺层结构不能满足力学性能要求,牵引座在最大应力集中部位(中间40mm处的r角)出现断裂;后期进行多次制件、试验,第一模具与第二模具和3尝试6mm+14mm,4mm+16mm,2mm+18mm等铺层厚度,试验发现:底部第一模具铺层太薄牵引座受力时导致底部层整体分层出现层间剥离(如图19);底部第一模具铺层太厚导致第二模具和3厚度减少,其强度不能满足最大牵引力,在最大应力集中处出现断裂。根据力学试验结果证明4mm+16mm为最优铺层方案。