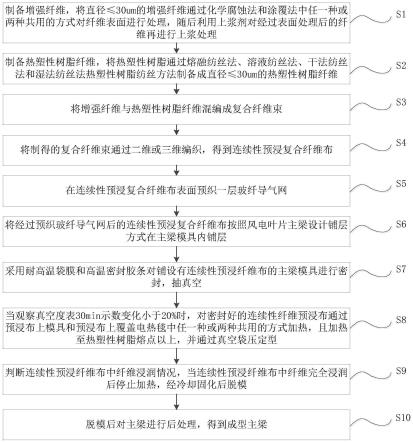
1.本发明涉及风力发电机技术领域,具体涉及热塑性风电叶片主梁成型方法。
背景技术:2.风能被全世界认为是目前可获得的最清洁、最具商业潜力和最具活力的可再生能源之一,复合材料风机叶片是风力发电机组捕获风能的核心部件,但是现有技术中,大型复合材料梁帽结构件的成型工艺主要采用拉挤成型、真空灌注成型和预浸料真空吸附成型等工艺。
3.但是,前述这些成型方法所采用的复合材料为热固性树脂基复合材料,热固性复合材料生产的叶片,由于树脂的热固性能,报废叶片无法进行自然降解缓慢,同时回收较为困难、重复利用率较低,对环境带来了巨大的潜在隐患。
4.为此,本发明提供了热塑性风电叶片主梁成型方法。
技术实现要素:5.为解决上述技术问题,提供热塑性风电叶片主梁成型方法,本技术方案解决了上述背景技术中提出的现有成型方法采用热固性树脂基复合材料生产叶片时,由于树脂的热固性能,报废叶片无法进行自然降解缓慢,同时回收较为困难、重复利用率较低,对环境带来了巨大的潜在隐患的问题。
6.为了实现上述目的,本发明的技术方案如下:
7.热塑性风电叶片主梁成型方法,包括:
8.制备增强纤维,将直径≤30um的增强纤维通过化学腐蚀法和涂覆法中任一种或两种共用的方式对纤维表面进行处理,随后利用上浆剂对经过表面处理后的纤维再进行上浆处理;
9.制备热塑性树脂纤维,将热塑性树脂通过熔融纺丝法、溶液纺丝法、干法纺丝法和湿法纺丝法热塑性树脂纺丝方法制备成直径≤30um的热塑性树脂纤维;
10.将增强纤维与热塑性树脂纤维混编成复合纤维束,所述复合纤维束中热塑性树脂纤维和增强纤维的横截面积之比为35~55:45~65;
11.将制得的复合纤维束通过二维或三维编织,得到连续性预浸复合纤维布;
12.在连续性预浸复合纤维布表面预织一层玻纤导气网;
13.将经过预织玻纤导气网后的连续性预浸复合纤维布按照风电叶片主梁设计铺层方式在主梁模具内铺层,其中,主梁模具内先打脱模剂,先铺设脱模布,再铺设经过预织玻纤导气网后的连续性预浸复合纤维布,随后铺设脱模布,并在最后一层采用含胶量为30~100%的连续性预浸复合纤维布或采用相同热塑性基体树脂的薄膜/胶片/胶块进行铺设,再将抽真空口用vap单向透气膜封住;
14.采用耐高温袋膜和高温密封胶条对铺设有连续性预浸复合纤维布的主梁模具进行密封,抽真空;
15.当观察真空度表30min示数变化小于20%时,对密封好的连续性预浸复合纤维布通过预浸布上模具和预浸布上覆盖电热毯中任一种或两种共用的方式加热,且加热至热塑性树脂熔点以上,并通过真空袋压定型;
16.判断连续性预浸复合纤维布中纤维浸润情况,当连续性预浸纤维布中纤维完全浸润后停止加热,经冷却固化后脱模;
17.脱模后对主梁进行后处理,得到成型主梁。
18.作为本发明的一种优选技术方案,所述纤维表面处理中,纤维为碳纤维、玻璃纤维、kevlar纤维、玄武岩纤维、pbo纤维、芳纶纤维、聚乙烯纤维、聚丙烯纤维、涤纶、锦纶中的一种或多种混合。
19.作为本发明的一种优选技术方案,所述热塑性树脂为聚丙烯、聚乙烯、聚酰胺、热塑性聚酰亚胺、聚氨酯、聚乳酸、聚碳酸酯、聚醚醚酮、聚苯硫醚、聚醚砜、丙烯腈-丁二烯-苯乙烯的一种或多种。
20.作为本发明的一种优选技术方案,所述连续性预浸复合纤维布中纤维方向为单轴向/双轴向/三轴向。
21.作为本发明的一种优选技术方案,所述玻纤导气网由直径≤30um的纤维编织制成,网孔面积≤100mm2。
22.作为本发明的一种优选技术方案,所述判断连续性预浸纤维布中纤维浸润情况,包括:通过每隔一段距离开一个窗口观察浸润情况,当浸润的连续性预浸纤维布的透明度无明显区分时视为连续性预浸纤维布中纤维已经完全浸润。
23.本发明的有益效果为:
24.本发明涉及的热塑性风电叶片主梁成型方法,该方法将表面处理好的增强纤维与热塑性树脂纤维预制复合纤维束,再将热塑性预制复合纤维束编织成连续性热塑性预浸纤维布,最后用续性热塑性预浸纤维布生产的风电叶片主梁质量稳定可靠,且纤维体积含量均一可控。同时,叶片主梁成型生产工艺与常规热固性复合材料叶片主梁成型生产工艺相似,工艺装备精简,操作简便,极大的缩短了制造周期,降低了工艺成本。另外,若采用热塑性树脂制成的梁帽失效损坏后,便于回收循环使用,重复利用率较高,大大减少了对环境的破坏。
附图说明
25.图1为本发明热塑性风电叶片主梁成型方法的工艺流程图。
26.图2为本发明复合纤维束的部分结构示意图。
27.图3为本发明经过预织玻纤导气网后的连续性预浸复合纤维布的结构示意图。
具体实施方式
28.下面将结合本发明实施例中的附图,对本发明实施例中的技术方案进行清楚、完整地描述,显然,所描述的实施例仅是本发明的一部分实施例,而不是全部的实施例。基于本发明中的实施例,本领域普通技术人员在没有做出创造性劳动前提下所获得的所有其他实施例,都属于本发明保护的范围。
29.下面结合实施例对本发明进一步说明。
30.本实施例中提供的是热塑性风电叶片主梁成型方法,参考附图1所示,具体步骤如下:
31.s1、制备增强纤维,将直径≤30um的增强纤维通过化学腐蚀法和涂覆法中任一种或两种共用的方式对纤维表面进行处理,随后利用上浆剂对经过表面处理后的纤维再进行上浆处理。
32.在本实施例中,纤维选用碳纤维、玻璃纤维、kevlar纤维、玄武岩纤维、pbo纤维、芳纶纤维、聚乙烯纤维、聚丙烯纤维、涤纶、锦纶中的一种或多种混合。
33.在本实施例中,采用化学腐蚀法和涂覆法中任一种或两种共用的方式对纤维表面进行处理,再利用上浆剂对经过表面处理后的纤维再进行上浆处理,能够大大增加纤维的表面粗糙度与表面活性。
34.s2、制备热塑性树脂纤维,将热塑性树脂通过熔融纺丝法、溶液纺丝法、干法纺丝法和湿法纺丝法热塑性树脂纺丝方法制备成直径≤30um的热塑性树脂纤维。
35.在本实施例中,热塑性树脂为聚丙烯、聚乙烯、聚酰胺、热塑性聚酰亚胺、聚氨酯、聚乳酸、聚碳酸酯、聚醚醚酮、聚苯硫醚、聚醚砜、丙烯腈-丁二烯
‑ꢀ
苯乙烯的一种或多种。
36.在本实施例中,本发明包括但不限于熔融纺丝法、溶液纺丝法、干法纺丝法和湿法纺丝法制备热塑性树脂纤维,同时,本发明涉及的熔融纺丝法、溶液纺丝法、干法纺丝法和湿法纺丝法均为现有技术,在本示例中,例如:熔融纺丝法:先将热塑性树脂熔融,再将热塑性熔体通过定径喷丝孔挤出在经过冷却定型得热塑性树脂纤维;溶液纺丝法:先将热塑性树脂溶解,再将热塑性溶解液细流通过凝固浴或热空气或热惰性气体固化。
37.s3、将增强纤维与热塑性树脂纤维混编成复合纤维束。
38.在本实施例中,本发明涉及的复合纤维束中增强纤维和热塑性树脂纤维交错分布并相互粘连,包括但不限于参考附图2中所示的形式。
39.在本实施例中,复合纤维束中热塑性树脂纤维和增强纤维的横截面积之比为35~55:45~65;其中,复合纤维束中热塑性树脂纤维和增强纤维的横截面积之比优选为35:65和55:45。
40.s4、将制得的复合纤维束通过二维或三维编织,得到连续性预浸复合纤维布。
41.在本实施例中,连续性预浸复合纤维布中纤维方向可以为单轴向/双轴向/ 三轴向。
42.s5、参考附图3,在连续性预浸复合纤维布表面预织一层玻纤导气网。
43.在本实施例中,玻纤导气网由直径≤30um的纤维编织制成,网孔面积≤ 100mm2,具有导气导流的作用,该玻纤导气网也可以在使用过程中铺设。
44.s6、将经过预织玻纤导气网后的连续性预浸复合纤维布按照风电叶片主梁设计铺层方式在主梁模具内铺层。
45.在本实施例中,首先在主梁模具内先打脱模剂,先铺设脱模布,再铺设经过预织玻纤导气网后的连续性预浸复合纤维布,随后铺设脱模布,并在最后一层采用含胶量为30~100%的高含胶量连续性预浸复合纤维布或采用相同热塑性基体树脂的薄膜/胶片/胶块进行铺设,再将抽真空口用vap单向透气膜封住。
46.s7、采用耐高温袋膜和高温密封胶条对铺设有连续性预浸纤维布的主梁模具进行密封,抽真空。
47.在本实施例中,袋膜要求随温度变化无熔融、尺寸变化、漏气等影响密封性的现象,例如耐高温尼龙膜及其复合膜。
48.s8、当观察真空度表30min示数变化小于20%时,对密封好的连续性纤维预浸布通过预浸布上模具和预浸布上覆盖电热毯中任一种或两种共用的方式加热,且加热至热塑性树脂熔点以上,并通过真空袋压定型。
49.s9、判断连续性预浸纤维布中纤维浸润情况,当连续性预浸纤维布中纤维完全浸润后停止加热,经冷却固化后脱模。
50.在本实施例中,判断连续性预浸纤维布中纤维浸润情况,包括:通过每隔一段距离开一个窗口观察浸润情况,当浸润的连续性预浸纤维布的透明度无明显区分时视为连续性预浸纤维布中纤维已经完全浸润。
51.在本实施例中,冷却方式可采用模具冷循环和/或风机等方式散热。
52.s10、脱模后对主梁进行后处理,得到成型主梁。
53.在本实施例中,后处理包括切割、切边、打磨工艺。
54.在本实施例中,连续性预浸纤维布还可用于风电叶片叶根预制、防雨环等部位的成型制备。
55.最后说明的是,以上实施例仅用以说明本发明的技术方案而非限制,尽管参照较佳实施例对本发明进行了详细说明,本领域的普通技术人员应当理解,可以对本发明的技术方案进行修改或者等同替换,而不脱离本发明技术方案的宗旨和范围,其均应涵盖在本发明的权利要求范围当中。