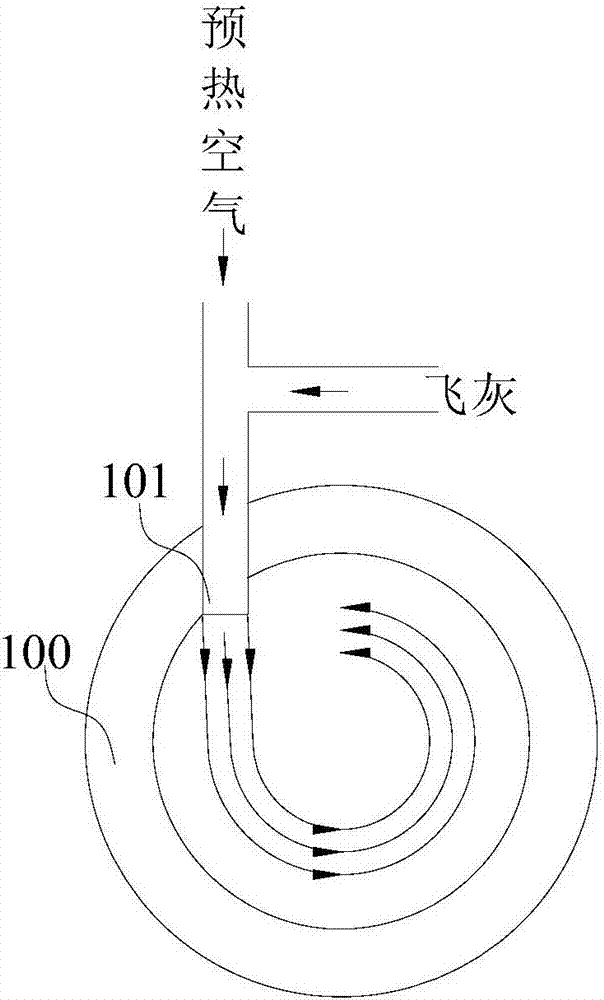
本实用新型属于固体废弃物资源化处理
技术领域:
,具体而言,本实用新型涉及一种蓄热式飞灰气化熔融炉。
背景技术:
:随着经济的发展、人口的不断增多以及人民生活水平的日益提高,城市垃圾的产生量也日渐增多。垃圾焚烧处理由于具有“无害化、减量化、资源化”程度高的特点,近年来在我国得到广泛的推广。在西方发达国家,垃圾焚烧技术的应用已经有将近130年的历史,而且目前仍被认为是最有效、经济的垃圾处理技术之一。垃圾焚烧飞灰的主要化学成分是SiO2、CaO、Al2O3和Fe2O3,以及大量的Cl-、SO3和碱等。垃圾焚烧飞灰还含有较高浓度的能被水浸出的可溶性Cd、Pb、Cu、Zn、Cr等多种有害重金属物质。此外,二噁英和呋喃等有机污染物也将在飞灰载体中富集存在。重金属的危害在于它不能被微生物分解且能在生物体内富集或形成其它毒性更强的化合物,通过食物链它们会最终对人体造成危害。二噁英类污染物是一类具有强烈致癌、致畸、致突变(三致作用)的有毒物质,它的毒性是氰化物的130倍、砒霜的900倍,有“世纪之毒”之称。可通过空气、水和迁徙物种及产品传输并沉积在远离其排放地点的地区,可长期在生态系统中累积,可引发癌症、损害中枢和外围神经系统,引发免疫系统疾病、生殖紊乱以及干扰婴幼儿的正常发育,直接威胁人类生存繁衍和可持续发展。这些有毒有害污染物的存在对地下水体、周围生态环境和人体健康构成了潜在的生态与健康风险。国家《生活垃圾焚烧污染控制标准》和《危险废物污染防治技术政策》中明确规定,生活垃圾焚烧产生的飞灰,需按危险废物进行管理和处置。飞灰的固化处理方式主要有熔融固化、水泥固化、沥青固化、化学稳定化处理、酸或其他溶剂洗涤法等。熔融技术是近年来新兴的飞灰处理技术,与水泥固化等方法相比,熔融处理技术的无害化程度彻底、产品稳定性高、运行费用适中、减量显著,并可以将飞灰转变为无毒、稳定的熔渣作为路基和混泥土等建筑材料使用。然而,目前的熔融固化技术均存在熔融效果差且能耗高的问题。因此,现有的飞灰处理技术有待进一步改进。技术实现要素:本实用新型旨在至少在一定程度上解决相关技术中的技术问题之一。为此,本实用新型的一个目的在于提出一种蓄热式飞灰气化熔融炉,采用该熔融炉可以实现垃圾飞灰的连续化熔融处理,并且稳定性高、能耗低。在本实用新型的一个方面,本实用新型提出了一种蓄热式飞灰气化熔融炉。根据本实用新型的实施例,所述熔融炉包括:炉膛,所述炉膛内自上而下限定出熔融区和排渣区,所述熔融区设置有第一开口和第二开口,并且所述第一开口和所述第二开口中均布置有烟气过滤器;第一蓄热室,所述第一蓄热室内设置有第一蓄热体,并且所述第一蓄热室通过所述第一开口与所述熔融区相连通;第二蓄热室,所述第二蓄热室内设置有第二蓄热体,并且所述第二蓄热室通过所述第二开口与所述熔融区相连通;第一烧嘴,所述第一烧嘴从所述第一蓄热室内经所述第一开口伸入到所述熔融区;第二烧嘴,所述第二烧嘴从所述第二蓄热室内经所述第二开口伸入到所述熔融区;燃气供给装置,所述燃气供给装置具有第一管道和第二管道,所述第一管道上布置有第一阀门,所述第二管道上布置有第二阀门,所述第一管道的至少一部分嵌入所述第一蓄热室内且与所述第一烧嘴相连,所述第二管道的至少一部分嵌入所述第二蓄热室内且与所述第二烧嘴相连;飞灰入口,所述飞灰入口布置在所述炉膛的侧壁上,且在高度方向上,所述飞灰入口低于所述第一开口和所述第二开口;U型出渣口,所述U型出渣口设置在所述排渣区的下端;熔渣池,所述熔渣池包括彼此间隔的熔渣室和换热室,所述熔渣室具有熔融渣入口和玻璃态熔渣出口,所述熔融渣入口与所述U型出渣口相连通,所述换热室具有常温空气入口和预热空气出口,所述预热空气出口与所述飞灰入口相连,并且所述预热空气出口通过换向阀与所述第一蓄热室和所述第二蓄热室相连通。由此,根据本实用新型实施例的蓄热式飞灰气化熔融炉通过在炉膛外面布置第一蓄热室和第二蓄热室,使得炉膛内烟气的余热可以被回收用于对助燃空气进行预热,从而可以充分利用烟气中的热量,并且可以显著降低炉膛内能耗,同时通过在连通蓄热室和炉膛的开口内布置烟气过滤器,蓄热室在处于蓄热状态时,即烟气在进入蓄热室时其中的灰尘被拦截,而当蓄热室处于放热状态时,预热后的空气又会将该部分灰尘吹入到炉膛中继续参与熔融处理,从而可以避免烟气过滤器中灰尘的大量聚集,进而真正意义上实现烟气中灰尘的减量化,其次本申请中在炉膛下端布置U型出渣口,可以实现熔融渣的连续排料,从而在提高飞灰处理效率的同时避免开启炉膛所带来的热能消耗,另外本申请在熔融渣出料过程中采用空气替代以往的冷却水对熔融渣进行冷却处理,不仅能够减少污水的排放量,而且可以将换热后的热空气用于飞灰的入炉动力以及作为蓄热室中的待预热空气使用,从而进一步节约了整体能耗。由此,通过采用本申请的熔融炉可实现飞灰的连续入料以及熔融渣的连续出料,并且可以充分分解飞灰中的二噁英等有害物质,将重金属固定于熔融渣中,并且炉体内物料分布均匀、受热性好、产物与烟气分离效果好,同时采用蓄热式燃烧技术和熔渣冷却空气回用,极大节约了能耗,具备良好的经济性。另外,根据本实用新型上述实施例的蓄热式飞灰气化熔融炉还可以具有如下附加的技术特征:任选的,所述换向阀具有空气进口、第一出口和第二出口和烟气出口,当所述第一蓄热室处于蓄热状态,所述第二蓄热室处于放热状态,所述第一蓄热室通过所述第一出口与所述烟气出口相连通,所述第二蓄热室通过所述第二出口与所述空气进口相连通。任选的,当所述第一蓄热室处于放热状态,所述第二蓄热室处于蓄热状态,所述第一蓄热室通过所述第一出口与所述空气进口相连通,所述第二蓄热室通过所述第二出口与所述烟气出口相连通。任选的,所述熔融区呈圆筒状,所述排渣区呈圆锥状。由此,可以便于熔融渣的排出。任选的,所述第一蓄热体和所述第二蓄热体分别独立地为陶瓷蓄热体。由此,可以充分回收烟气中的余热。任选的,经所述飞灰入口的喷入的物料在所述熔融区形成旋流。由此,可以实现飞灰物料在炉膛中均匀化分布,并且使得熔融后的小颗粒在离心力的条件下附着于炉壁,高温条件下附着于炉壁熔渣呈现良好的流动性,从而便于熔渣的及时分离,进而保证系统运行更加稳定。任选的,所述第一蓄热室和所述第二蓄热室对称布置在所述炉膛的两侧。任选的,所述熔融渣入口靠近所述预热空气出口设置,所述玻璃态熔渣出口靠近所述常温空气入口设置。由此,可以实现熔融渣热量的充分利用。本实用新型的附加方面和优点将在下面的描述中部分给出,部分将从下面的描述中变得明显,或通过本实用新型的实践了解到。附图说明本实用新型的上述和/或附加的方面和优点从结合下面附图对实施例的描述中将变得明显和容易理解,其中:图1是根据本实用新型一个实施例的蓄热式飞灰气化熔融炉的结构示意图;图2是根据本实用新型再一个实施例的蓄热式飞灰气化熔融炉中的飞灰入炉的示意图。具体实施方式下面详细描述本实用新型的实施例,所述实施例的示例在附图中示出,其中自始至终相同或类似的标号表示相同或类似的元件或具有相同或类似功能的元件。下面通过参考附图描述的实施例是示例性的,旨在用于解释本实用新型,而不能理解为对本实用新型的限制。在本实用新型的描述中,需要理解的是,术语“中心”、“纵向”、“横向”、“长度”、“宽度”、“厚度”、“上”、“下”、“前”、“后”、“左”、“右”、“竖直”、“水平”、“顶”、“底”、“内”、“外”、“顺时针”、“逆时针”、“轴向”、“径向”、“周向”等指示的方位或位置关系为基于附图所示的方位或位置关系,仅是为了便于描述本实用新型和简化描述,而不是指示或暗示所指的装置或元件必须具有特定的方位、以特定的方位构造和操作,因此不能理解为对本实用新型的限制。此外,术语“第一”、“第二”仅用于描述目的,而不能理解为指示或暗示相对重要性或者隐含指明所指示的技术特征的数量。由此,限定有“第一”、“第二”的特征可以明示或者隐含地包括至少一个该特征。在本实用新型的描述中,“多个”的含义是至少两个,例如两个,三个等,除非另有明确具体的限定。在本实用新型中,除非另有明确的规定和限定,术语“安装”、“相连”、“连接”、“固定”等术语应做广义理解,例如,可以是固定连接,也可以是可拆卸连接,或成一体;可以是机械连接,也可以是电连接;可以是直接相连,也可以通过中间媒介间接相连,可以是两个元件内部的连通或两个元件的相互作用关系,除非另有明确的限定。对于本领域的普通技术人员而言,可以根据具体情况理解上述术语在本实用新型中的具体含义。在本实用新型中,除非另有明确的规定和限定,第一特征在第二特征“上”或“下”可以是第一和第二特征直接接触,或第一和第二特征通过中间媒介间接接触。而且,第一特征在第二特征“之上”、“上方”和“上面”可是第一特征在第二特征正上方或斜上方,或仅仅表示第一特征水平高度高于第二特征。第一特征在第二特征“之下”、“下方”和“下面”可以是第一特征在第二特征正下方或斜下方,或仅仅表示第一特征水平高度小于第二特征。在本实用新型的一个方面,本实用新型提出了一种蓄热式飞灰气化熔融炉。根据本实用新型的实施例,参考图1,该熔融炉包括:炉膛100、第一蓄热室200、第二蓄热室300、第一烧嘴400、第二烧嘴500、燃气供给装置600、熔渣池700以及飞灰入口101和U型出渣口102。根据本实用新型的实施例,炉膛100内自上而下限定出熔融区11和排渣区12,熔融区11设置有第一开口103和第二开口104,并且第一开口103和第二开口104中均布置有烟气过滤器13。由此,通过在连通蓄热室和炉膛的开口内布置烟气过滤器,蓄热室在处于蓄热状态时,即烟气在进入蓄热室时其中的灰尘被拦截,而当蓄热室处于放热状态时,预热后的空气又会将该部分灰尘吹入到炉膛中继续参与熔融处理,从而可以避免烟气过滤器中灰尘的大量聚集,进而真正意义上实现烟气中灰尘的减量化。根据本实用新型的一个具体实施例,参考图1,熔融区11可以呈圆筒状,排渣区12可以呈圆锥状。由此,可以方便炉膛内产生熔融渣的及时排出。具体的,整个熔融炉炉膛均采用高温耐热材料制成。根据本实用新型的实施例,第一蓄热室200内设置有第一蓄热体21,并且第一蓄热室200通过第一开口103与熔融区11相连通。根据本实用新型的一个具体实施例,第一蓄热体21可以为陶瓷蓄热体。由此,可以显著提高烟气的余热回收率。根据本实用新型的实施例,第二蓄热室300内设置有第二蓄热体31,并且第二蓄热室300通过第二开口104与熔融区11相连通。根据本实用新型的一个具体实施例,第二蓄热体31可以为陶瓷蓄热体。由此,可以进一步提高烟气的余热回收率。根据本实用新型的一个具体实施例,第一蓄热室200和第二蓄热室300对称布置在炉膛100的两侧。具体的,当第一蓄热室处于蓄热状态时,第二蓄热室处于放热状态,炉膛内的烟气经第一开口进入到第一蓄热室中将热量传递给第一蓄热体后进行排放,而空气进入到第二蓄热室中被其中的第二蓄热体预热后经第二开口供给至炉膛中作为助燃空气参与燃烧,并且通过控制烟气流量和空气流量,使得蓄热室蓄热和蓄热室放热时间相同,即第一蓄热室蓄热完全后,则第二蓄热室刚好完成放热,二者状态交换,此时第一蓄热室处于放热状态,第二蓄热室处于蓄热状态,然后二者状态一直交替进行。根据本实用新型的实施例,第一烧嘴400从第一蓄热室200内经第一开口103伸入到熔融区11,从而在第一蓄热室处于放热状态时,通过第一烧嘴向炉膛中供给燃料参与燃烧为炉膛提供熔融热量。根据本实用新型的实施例,第二烧嘴500从第二蓄热室300内经第二开口104伸入到熔融区11,从而在第二蓄热室处于放热状态时,通过第二烧嘴向炉膛中供给燃料参与燃烧为炉膛提供熔融热量。根据本实用新型的一个具体实施例,第一烧嘴400和第二烧嘴500的喷焰方向分别与炉膛的径向方向呈向下45度角倾斜。由此,可以使得火焰尽可能喷向物料实现飞灰的快速熔融。根据本实用新型的实施例,燃气供给装置600具有第一管道61和第二管道62,第一管道61上布置有第一阀门63,第二管道上布置有第二阀门64,第一管道61的至少一部分嵌入第一蓄热室200内且与第一烧嘴400相连,第二管道62的至少一部分嵌入第二蓄热室300内且与第二烧嘴500相连。具体的,第一蓄热室处于放热状态时,第二蓄热室处于蓄热状态,打开第一管道上的第一阀门,关闭第二管道上的第二阀门,使得燃气经第一管道后再经第一烧嘴供给至炉膛内,而当第二蓄热室蓄热完全,第一蓄热室放热完全,第一蓄热室和第二蓄热室交换工作状态,即此时第一蓄热室处于蓄热状态,第二蓄热室处于放热状态,打开第二管道上的第二阀门,关闭第一管道上的第一阀门,使得燃气经第二管道后再经第二烧嘴供给至炉膛内,待第一蓄热室蓄热完全,第二蓄热室放热完全,第一蓄热室和第二蓄热室交替工作状态。根据本实用新型的实施例,飞灰入口101布置在炉膛100的侧壁上,且在高度方向上,飞灰入口101低于第一开口103和第二开口104,飞灰入口101适于将飞灰物料供给至炉膛中。具体的,飞灰入口距离第一开口和第二开口应具有一定距离,从而可以防止入炉飞灰随烟气而被带走。根据本实用新型的具体实施例,参考图2,经飞灰入口101的喷入的物料在熔融区11形成旋流。发明人发现,通过采用采用旋风入料的方式,可以实现物料的均匀化分布,并且使得熔融后的小颗粒在离心力的条件下附着于炉壁,高温条件下附着于炉壁熔渣呈现良好的流动性,从而便于熔渣的及时分离,进而保证系统运行更加稳定。需要说明的是,本领域技术人员可以根据实际需要对飞灰入口出料方向进行调整,只要能够实现经飞灰入口喷入的物料在熔融区中形成旋流即可。根据本实用新型的实施例,U型出渣口102设置在排渣区12的下端,且适于将炉膛中产生的熔融渣排出排渣区。由此,通过在炉膛下端布置U型出渣口,可以实现炉膛内的反应密闭且防止烟气泄露,同时可以实现熔融渣的连续排料,从而在提高飞灰处理效率的同时避免开启炉膛所带来的热能消耗。根据本实用新型的实施例,熔渣池700包括彼此间隔的熔渣室71和换热室72,熔渣室71具有熔融渣入口701和玻璃态熔渣出口702,熔融渣入口701与U型出渣口102相连通,换热室72具有常温空气入口703和预热空气出口704,预热空气出口704与飞灰入口101相连,并且预热空气出口704通过换向阀73与第一蓄热室200和第二蓄热室300相连通,且适于使得从排渣区得到的熔融渣与常温空气进行换热,从而得到玻璃态熔渣和预热空气,并将预热空气的一部分供给至飞灰入口为入炉飞灰喷吹提供动力,将预热空气的另一部分通过换向阀供给至第一蓄热室或第二蓄热室作为助燃空气使用。发明人发现,在熔融渣出料过程中采用空气替代以往的冷却水对熔融渣进行冷却处理,不仅能够减少污水的排放量,而且可以将换热后的热空气用于飞灰的入炉动力以及作为蓄热室中的待预热空气使用,从而显著节约了整体能耗。根据本实用新型的一个具体实施例,参考图1,熔融渣入口701靠近预热空气出口704设置,玻璃态熔渣出口702靠近常温空气入口703设置,从而使得常温空气与熔融渣在熔渣池中进行逆流换热,从而可以提高二者的换热效率。根据本实用新型的再一个具体实施例,参考图1,换向阀73具有空气进口705、第一出口706和第二出口707和烟气出口708,当第一蓄热室200处于蓄热状态,第二蓄热室300处于放热状态,第一蓄热室200通过第一出口706与烟气出口708相连通,第二蓄热室300通过第二出口707与空气进口705相连通,即当第一蓄热室处于蓄热状态,第二蓄热室处于放热状态时,炉膛中产生的烟气经第一蓄热室回收预热后经换向阀的第一出口和烟气出口而排出系统,而在熔渣池中与熔融渣换热后的空气经换向阀的空气进口和第二出口后供给至第二蓄热室中被第二蓄热体预热后供给至炉膛中作为助燃空气使用;而当第一蓄热室200处于放热状态,第二蓄热室300处于蓄热状态,第一蓄热室200通过第一出口706与空气进口705相连通,第二蓄热室300通过第二出口707与烟气出口708相连通,即当第一蓄热室处于放热状态,第二蓄热室处于蓄热状态时,炉膛中产生的烟气经第二蓄热室回收预热后经换向阀的第二出口和烟气出口而排出系统,而在熔渣池中与熔融渣换热后的空气经换向阀的空气进口和第一出口后供给至第一蓄热室中被第一蓄热体预热后供给至炉膛中作为助燃空气使用。下面对采用该蓄热室飞灰气化熔融炉对飞灰的处理过程进行详细描述:垃圾焚烧后产生的飞灰比炉渣含有更多的汞、铅、镉等多种易挥发重金属以及二恶英等剧毒有机成分,并且由于重金属具有高浸出特性,若直接加以填埋会溶出污染生活环境,危及人体健康,必须要进行特殊处理,而本申请中通过采用喷吹的方式将飞灰以旋流的方式供给至炉膛中,并且开启第一管道上的第一阀门使得燃气经第一烧嘴供给至炉膛,同时控制换气阀使得空气进口与第一出口相连通,使得空气经第一蓄热室供给至炉膛中作为助燃气使用,燃料在炉膛中燃烧为炉膛供热,控制炉膛内温度在1200℃~1700℃,使飞灰在高温下迅速熔化,并且由于二噁英的分解温度为800℃以上,而在熔融炉内温度在1200℃~1700℃左右,因此熔融炉内高温产生的热量,打断苯环,使二噁英分解为CO2、HCl和H2O等物质,使得经熔融处理后二噁英的浓度显著降低(飞灰中二噁英去除率达99.9%以上),同时炉膛内采用富燃料燃烧,控制空气过剩系数在一定的范围内,一方面飞灰中重金属在还原性气氛下被还原为金属可回收利用,另一方面可大幅度降低氮氧化物浓度,此外,还原性气氛有利于降低灰熔点50~100℃,提高灰渣流动性,高温下飞灰中的有机物发生热分解、气化、燃烧形成烟气,而无机物飞灰则熔融成小颗粒,熔融后的颗粒在离心力条件下被炉壁捕集,高温条件下熔渣呈现良好的流动性,并在炉体表面形成具有保护作用的绝缘体层,在锥形排渣区下部不断汇聚由U型排渣口排出,而烟气上升由布置在炉膛上的第二出口内布置的烟气过滤器过滤后进入第二蓄热室中进行余热回收,换热后的烟气(温度降低200摄氏度以下)经换向阀的第四出口和烟气出口而排出,而当第二蓄热室蓄热完全,关闭第一管道上的第一阀门,并且开启第二管道上的第二阀门,调整控制阀使得空气进口与第二出口连通,第一出口与烟气出口连通,使得燃气经第二烧嘴供给至炉膛中,而助燃空气经第二蓄热室供给至炉膛中,并且附着在第二出口烟气过滤器上的灰尘也被一起吹入到炉膛中继续参与熔融处理,燃气燃烧为炉膛供热,而产生的烟气经布置在炉膛上的第一出口进入第一蓄热室进行蓄热,换热后的烟气经第一出口和烟气出口排出,通过控制烟气流量和空气流量,使得蓄热室蓄热和蓄热室放热时间相同,即第一蓄热室蓄热完全后,则第二蓄热室刚好完成放热,二者状态交换,此时第一蓄热室处于放热状态,第二蓄热室处于蓄热状态,然后二者状态一直交替进行,同时通过U型排渣口排出的熔融渣进入到熔渣池中的熔渣室与换热室供给的常温空气进行换热,得到玻璃态熔渣和预热空气,而预热空气一部分供给至飞灰入口为飞灰入炉提供喷吹动力,并且可以补充炉膛内燃烧所需的风量,而预热空气的另一部分经换向阀上的空气进口供给至第一蓄热室或第二蓄热室中进行再次蓄热后供给至炉膛中作为助燃空气使用。需要说明的是,本领域技术人员可以根据实际需要对炉膛内空气过剩系数进行选择。根据本实用新型实施例的蓄热式飞灰气化熔融炉通过在炉膛外面布置第一蓄热室和第二蓄热室,使得炉膛内烟气的余热可以被回收用于对助燃空气进行预热,从而可以充分利用烟气中的热量,并且可以显著降低炉膛内能耗,同时通过在连通蓄热室和炉膛的开口内布置烟气过滤器,蓄热室在处于蓄热状态时,即烟气在进入蓄热室时其中的灰尘被拦截,而当蓄热室处于放热状态时,预热后的空气又会将该部分灰尘吹入到炉膛中继续参与熔融处理,从而可以避免烟气过滤器中灰尘的大量聚集,进而真正意义上实现烟气中灰尘的减量化,其次本申请中在炉膛下端布置U型出渣口,可以实现熔融渣的连续排料,从而在提高飞灰处理效率的同时避免开启炉膛所带来的热能消耗,另外本申请在熔融渣出料过程中采用空气替代以往的冷却水对熔融渣进行冷却处理,不仅能够减少污水的排放量,而且可以将换热后的热空气用于飞灰的入炉动力以及作为蓄热室中的待预热空气使用,从而进一步节约了整体能耗。由此,通过采用本申请的熔融炉可实现飞灰的连续入料以及熔融渣的连续出料,并且可以充分分解飞灰中的二噁英等有害物质,将重金属固定于熔融渣中,并且炉体内物料分布均匀、受热性好、产物与烟气分离效果好,同时采用蓄热式燃烧技术和熔渣冷却空气回用,极大节约了能耗,具备良好的经济性。下面参考具体实施例,对本实用新型进行描述,需要说明的是,这些实施例仅仅是描述性的,而不以任何方式限制本实用新型。实施例1流化床焚烧炉产生的飞灰中二恶英的毒性当量(I-TEQ)为3.7ng/g,采用本申请的蓄热室飞灰气化熔融炉对飞灰进行处理,控制炉膛内熔融温度为1400摄氏度,然后对排出熔融炉烟气中的二噁英等指标进行检测(参考表1),二噁英的含量去除率超过99%,远远低于排放标准,不会对环境造成负面影响。表1飞灰处理前以及处理后熔渣中二噁英的变化项目飞灰熔渣二噁英(ng/g)3200.012二噁英毒性当量(ng-TEQ/g)3.70.00049由表2可知,熔融处理过程中,重金属Cr和Zn的固定率较高,而挥发性重金属Cu、Pb和Cd的固定率较低。熔融渣浸出毒性远低于国家危险废物浸出毒性鉴别标准限值,因此熔融渣可被认为是非危险废物。表2飞灰经熔融后熔融渣中重金属含量及TCLP重金属浸出量结论:采用本申请的蓄热室飞灰气化熔融炉所得熔渣具有不易浸出重金属、基本不含二噁英和稳定性好等优点,具备作为良好建材原料的资源化利用条件,主要利用途径是做水泥或混凝土的替代骨料。实施例2流化床焚烧炉产生的飞灰中二恶英的毒性当量(I-TEQ)为6.7ng/g,采用本申请的蓄热室飞灰气化熔融炉对飞灰进行处理,控制炉膛内熔融温度为1700摄氏度,然后对排出熔融炉烟气中的二噁英等指标进行检测(参考表3),二噁英的含量去除率超过99%,远远低于排放标准,不会对环境造成负面影响。表3飞灰处理前以及处理后熔渣中二噁英的变化项目飞灰熔渣二噁英(ng/g)6400.004二噁英毒性当量(ng-TEQ/g)6.70.00066由表4可知,所得熔融渣的主要成分是CaO、Al2O3和SiO2,其含量占总质量的99%左右。而原灰中含量较高的SO3、K2O、Na2O和Cl在熔融过程中几乎完全挥发。表4熔渣成分及其含量成分Al2O3Fe2O3TiO2MgOCaOKNaSiO2质量百分比(%)10.952.520.151.3244.020.010.1340.90结论:采用本申请的蓄热室飞灰气化熔融炉所得熔渣具有不易浸出重金属、基本不含二噁英和稳定性好等优点,具备作为良好建材原料的资源化利用条件,利用途径是用于填料厂的覆盖材料。在本说明书的描述中,参考术语“一个实施例”、“一些实施例”、“示例”、“具体示例”、或“一些示例”等的描述意指结合该实施例或示例描述的具体特征、结构、材料或者特点包含于本实用新型的至少一个实施例或示例中。在本说明书中,对上述术语的示意性表述不必须针对的是相同的实施例或示例。而且,描述的具体特征、结构、材料或者特点可以在任一个或多个实施例或示例中以合适的方式结合。此外,在不相互矛盾的情况下,本领域的技术人员可以将本说明书中描述的不同实施例或示例以及不同实施例或示例的特征进行结合和组合。尽管上面已经示出和描述了本实用新型的实施例,可以理解的是,上述实施例是示例性的,不能理解为对本实用新型的限制,本领域的普通技术人员在本实用新型的范围内可以对上述实施例进行变化、修改、替换和变型。当前第1页1 2 3